螺纹脱模
注塑模具设计结构篇--注塑模脱模系统的设计培训

29
30
31
4.推块脱模机构 对于端面平直的无孔塑件,或仅带有小孔的塑件,为保证塑件在模具打开 时能留到动模一侧,一般都把型腔安排在动模一侧,如果塑件表面不希望留下 推杆痕迹,必须采用推块机构推推塑件,如图4-86所示。对于齿轮类或一些带 有凸缘的制品,如果采用推杆推出容易变形或者是采用推板推出容易使制品粘 附模具时,也需采用推块作为推出零件。推动推块的推杆如果用螺纹连接在推 块上,则复位杆可以与推杆安装在同一块固定板上,如图4-86(a)所示。如果 推块与推杆无螺纹连接,必须采用图4-86(b)所示的复位方法。推块实际上成 为型腔底板或构成形腔底面大部分,推件运动的配合间隙既要小于溢料间隙, 又不产生过大的摩擦磨损,这就对配合面间的加工,特别是非圆形推块的配合 面提出很高要求,常常要在装配时研磨。
一次推出机构 塑件在推出零件的作用下,通过一次推出动作,就能将塑件全部脱出。 这种类型的脱模机构即为一次推出机构,也称为简单脱模机构。它是最常见 的,也是应用最广的一种脱模机构。一般有以下几种形式。
8
1.推杆脱模机构 (1) 机构组成和动作原理 推杆脱模是最典型的一次推出机构,它结构简单,制造容易且维修方便, 其机构组成和动作原理如图4-76所示。它是由推杆1、推杆固定板2、推板导套 3、推板导柱4、推杆垫板5、拉料杆6、复位杆7和限位钉8等所组成的。推杆、 拉料杆、复位杆都装在推杆固定板2上,然后用螺钉将推杆固定板和推杆垫板 连接固定成一个整体,当模具打开并达到一定距离后,注塑机上的机床推杆将 模具的推出机构挡住,使其停止随动模一起的移动,而动模部分还在继续移动 后退,于是塑件连同浇注系统一起从动模中脱出。合模时,复位杆首先与定模 分型面相接触,使推出机构与动模产生相反方向的相对移动。模具完全闭合后, 推出机构便回复到了初始的位置(由限位钉8保证最终停止位置)。
模具n种顶出结构解说
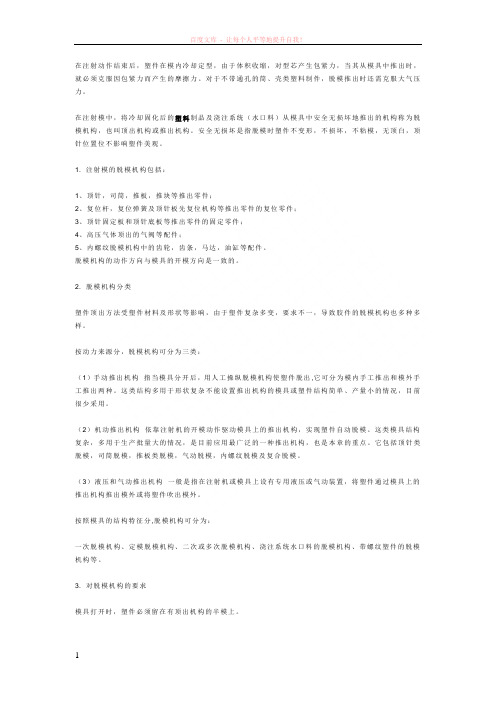
在注射动作结束后,塑件在模内冷却定型,由于体积收缩,对型芯产生包紧力,当其从模具中推出时,就必须克服因包紧力而产生的摩擦力。
对于不带通孔的筒、壳类塑料制件,脱模推出时还需克服大气压力。
在注射模中,将冷却固化后的塑料制品及浇注系统(水口料)从模具中安全无损坏地推出的机构称为脱模机构,也叫顶出机构或推出机构。
安全无损坏是指脱模时塑件不变形,不损坏,不粘模,无顶白,顶针位置位不影响塑件美观。
1. 注射模的脱模机构包括:1、顶针,司筒,推板,推块等推出零件;2、复位杆,复位弹簧及顶针板先复位机构等推出零件的复位零件;3、顶针固定板和顶针底板等推出零件的固定零件;4、高压气体顶出的气阀等配件;5、内螺纹脱模机构中的齿轮,齿条,马达,油缸等配件。
脱模机构的动作方向与模具的开模方向是一致的。
2. 脱模机构分类塑件顶出方法受塑件材料及形状等影响,由于塑件复杂多变,要求不一,导致胶件的脱模机构也多种多样。
按动力来源分,脱模机构可分为三类:(1)手动推出机构指当模具分开后,用人工操纵脱模机构使塑件脱出,它可分为模内手工推出和模外手工推出两种。
这类结构多用于形状复杂不能设置推出机构的模具或塑件结构简单、产量小的情况,目前很少采用。
(2)机动推出机构依靠注射机的开模动作驱动模具上的推出机构,实现塑件自动脱模。
这类模具结构复杂,多用于生产批量大的情况,是目前应用最广泛的一种推出机构,也是本章的重点。
它包括顶针类脱模,司筒脱模,推板类脱模,气动脱模,内螺纹脱模及复合脱模。
(3)液压和气动推出机构一般是指在注射机或模具上设有专用液压或气动装置,将塑件通过模具上的推出机构推出模外或将塑件吹出模外。
按照模具的结构特征分,脱模机构可分为:一次脱模机构、定模脱模机构、二次或多次脱模机构、浇注系统水口料的脱模机构、带螺纹塑件的脱模机构等。
3. 对脱模机构的要求模具打开时,塑件必须留在有顶出机构的半模上。
由于注射机的推杆在安装后模的一侧,所以注射模的顶出机构一般在后模。
螺纹塑件的成型

内容
1 螺纹设计 2 螺纹型芯与螺纹型环尺寸的计算 3 螺纹型芯或螺纹型环的结构设计 4 螺纹塑件的非旋转脱模 5 螺纹塑件旋转脱模
10.1 螺 纹 设 计
10.1.1 螺纹形状与尺寸精度
塑件上的螺纹可以在模塑时直接成型,也可 以用后加工的办法机械切削,在经常装拆和受力 较大的地方则应该采用金属的螺纹嵌件。塑件上 的螺纹应选用可参考表10-1,原则上螺牙尺寸应 选较大者,螺纹直径较小时就不宜采用细牙螺纹, 特别是用纤维或布基作填料的塑料成型的螺纹, 其螺牙尖端部分常常被强度不高的纯树脂所充填, 如螺牙过细将会影响使用强度。
返回
在注塑模具中,若嵌件无通孔,并且受塑料 的冲击力不大时,可直接将嵌件插在固定于模具 上的光杆型芯上,如图f所示。小直径的螺纹嵌 件(如M3.5毫米以下),螺纹牙沟槽很细小,即 使是通孔的嵌件也可以采取这种简单的装固方法, 在适当的工艺条件下,塑料仅能挤入一小段,但 并不妨碍使用。这样就省去了模外卸螺纹型芯的 操作,但使用不当时嵌件易移动或脱落。上述各 种固定螺纹型芯的办法,多用于立式注塑机的下 模或卧式注塑机的定模。对于上模或合模时冲击 振动较大的卧式注塑机模具动模边,当型芯插入 时应有弹性连接装置,以免合模时型芯落下或移 位造成制品报废、模具损伤。
返回
模制的螺纹达不到高精度,一般低于GB 3级, 螺纹外径不能小于2毫米。如果模具的螺纹牙距 未加上收缩值,则塑料螺纹与金属螺纹的配合长 度就不能太长,—般不大于螺纹直径的1.5倍, 否则会因收缩值不同互相干涉造成附加内应力, 使联接强度降低。螺纹成型方法有以下几种:(1) 采用成型杆或成型环在成型之后从制品上拧下来; (2)外螺纹采用辨合模成型,这时工效高,但精 度较差,还可能带有不易除尽的飞边;(3)要求 不高的内螺纹(如瓶盖螺纹)用软塑料成型时,可 强制脱模,而不必从型芯拧下,这时螺牙断面最 好设计得浅一些,且呈圆形或梯形断面,如图 10-1所示。
没有顶针顶出的模具是如何设计的呢?

没有顶针顶出的模具是如何设计的呢?
没有顶针顶出的模具是如何设计的
题主的问题应该是涉足于塑胶模具,塑胶产品在注塑时从模具中脱落,离不开脱模装置,没有顶针,那么还应该有其它的产品脱模装置。
1例如:纯净水瓶盖产品内部是看不到顶针的,内部是螺纹,这种带螺纹的产品,脱模的方式一般有两种:
1-1 二级缩呵标准件装置,这是一种比较特殊的标准件,螺纹产品在一边顶出时,标准件会一边向内缩呵而脱离内螺纹;
1-2 是利用齿轮齿条的带动,旋转内模件而使产品脱离模具;
2例如:生活中用到的水桶,洗脸盆之类的这类产品也是不需要顶针顶出的,而它一般需要气顶,因为产品的内模在注塑后形成的真空状,这时需要气顶使产品和内模脱离,再用手动取出产品,或者利用机械手取出产品。
3 有些产品为了美观,会用到推块、推板类的顶出,需要具体产品具体对待。
4 还有更加特殊的产品,比如产品在滑块上,将整个滑块系统顶出模具后,利用滑块抽出后,产品自动脱模。
当然,还有其它的很多顶出方式,整个模具设计过程中,需要不断的去积累知识,相信你也会设计出这类不需要顶针顶出的模具的。
4.9 脱模机构设计

(4) 推杆的固定与配合形式
1)推杆的固定形式
a.常用形式 b.采用垫块或垫圈代 替固定板上的沉孔 c.螺钉顶紧推杆 d.推杆固定端无推板 时使用 e.螺钉紧固,用于粗 大推杆 f. 铆钉的形式,用于 直径小的推杆
2)圆形横截面推杆的配合形式
推杆端面应和塑件成型表面在同一平面或高出0.05~0.1mm 推杆与推杆孔有一段配合长度为推杆直径3~5倍的间隙配 合 (H8/f8或H9/f9),其余部分为扩孔。 扩孔直径比推杆大0.5mm。
(1)利用推杆拉断点浇口Байду номын сангаас料 (2)利用拉料杆拉断点浇口凝料
(3)利用侧凹拉断点浇口凝料
(4)利用定模推板拉断点浇口凝料
3.潜伏式浇口凝料的脱出结构
其脱模装置必须分别设置塑件和流道凝料的推出机构, 在推出过程中,浇口被拉断,塑件与浇注系统凝料各自脱 落。 (1)利用脱模板切断浇口凝料
(2)利用差动式推杆切断浇口凝料 (3)
3)摆块拉板式脱模机构 利用活动摆块推动型腔板完成一次脱模,由推杆完成二 次脱模。
4)滑块式
2. 双推板二次脱模机构
这种类型的脱模结构有两组推出装置,利用两组推板的 先后动作完成二次脱模。 1)八字摆杆式脱模机构
① 开模时,当注射机顶杆推动 一次推板时,连接推杆与脱 模板一起以同样速度移动, 使塑件和型腔一起运动而脱 离动模型芯,完成一次推出 动作。
3)定距导柱顺序脱模结构 4)尼龙拉钩式顺序脱模结构
七、浇注系统凝料的脱出机构
1.普通浇注系统凝料的脱出结构
通常采用侧浇口、直接浇口及中心浇口类型的模具,其 浇注系统凝料一般与塑件连在一起。塑件脱出时,先用拉 料杆拉住冷料,使浇注系统凝料留在动模一侧,然后用推 杆或拉料杆推出,靠其自重而脱落。
材料成型及控制工程专业考试辅导

哈工大华德学院 年 季学期塑料成型工艺及模具设计模拟试题(Ⅱ)考试时间:120 分 考试形式:闭 卷 适用班级:一、填空1.为使推出机构简单、可靠,开模时应使塑件留于(动模上),以利用注射机移动部分的(顶杆)或液压缸的活塞推出塑件。
2.对黏度较高、(温度较低)的塑料熔体;尺寸较大、(形状复杂)、(薄壁)塑件,一般宜用(较大)的注射压力。
3.塑料管材挤出成型时,口模用于成型塑料制件的(外表面);芯棒用于成型制件的(内表面)。
4.当塑料原材料、注射机和模具结构确定之后,注射成型工艺参数:(温度), (压力)和(时间)的选择与控制,是决定塑件(成型质量)的主要因素。
5.对大型模具的成型零部件尺寸设计计算时,主要是(刚度)问题,应防止模具产生过大的(弹性变形)。
在刚度和强度计算时,应先用(刚度条件)计算公式进行壁厚和垫板厚度的设计计算,再用(强度条件)计算公式进行校核。
6.注射模导向机构主要用于保证(定模)和(动模)两大部分的准确对合;可保证(凸凹模)的配合间隙;还可使垂直分型拼块在闭合时(准确定位)等。
7.注射模单推出板二次脱模机构的动作顺序是 : 一次脱模时将(型腔)推出 ,使(塑件)脱离型芯;二次脱模时通过(推杆)将(塑件)从型腔中推出。
8.注射机普通流道浇注系统一般由(主流道)、(分流道)、(浇口)和(冷料穴)组成。
二、名词解释1.塑化能力答:注射机在单位时间内能够塑化的物料重量或体积。
2.均化答:物料经过塑化之后,使熔体内组分均匀、密度均匀、黏度均匀和温度分布均匀,称为均化。
3.塑料挤出成型答:在挤出机上使塑料受热呈熔融状态,在一定压力下通过挤出成型机头而获得连续型材。
4.分型面答:模具上用于取出塑件和浇注系统凝料的可分离的接触表面通称为分型面。
5.内径定径答:在定径套内通冷却水管,并在管材外部设置冷风冷却,使管材冷却贴在定径套上。
三、简答1.在成型零部件的工作尺寸计算中,影响塑件尺寸精度的主要因素有哪些?答:⑴成型零部件的制造误差;⑵成型零部件的磨损;⑶塑件的收缩率波动;⑷配合间隙引起的误差。
《模具技术》8

第八章注射模脱模机构8-1概述1,概念:将胶件安全无损坏地推离模具.2 分类:顶针(重点),司筒(重点),推板(重点),气动,内螺纹脱模(了解)及复合脱模(了解),二次脱模。
8-2 顶针脱模:8-2-1 圆顶针:(见图一)1、优点:1)制造加工方便;2)阻力小;3)维修方便。
2、缺点:顶出位置有一定的局限性。
3、设计要点:1)直身圆顶针:直径3/64”—1”;常用顶针直径在1.6mm(或1/16”)至8mm(或5/16”)之间,对于小于2.5MM(或7/64”)顶针宜加托位。
2)顶针可以顶骨,顶边,顶Boss柱。
3)顶针与后模镶件的配合长度一般在12—20mm之间。
8-2-2 扁顶针:(见图二)常用于顶边或深骨部位。
1、优点:顶出力大。
2、缺点:加工困难,易磨损,以及成本高。
8-3 司筒顶出:(见右图)常用于细长螺丝柱,圆筒形零件的顶出。
1、优点:顶出力较大且均匀,不会留下明显痕迹。
2、缺点:制造和装配麻烦,易磨损,出披锋,成本高。
3、设计要点:1)柱高小于15mm或螺丝柱壁厚小于0.8mm的,尽量不用司筒,而在其附近对称加兩枝頂針;司筒壁在1mm以下或司筒壁径比≤0.1的要做有托司筒。
顶针上端面要高于内模镶件3丝∽5丝,因为低下来易多胶,可能会影响装配。
顶针配合位长度:一般取顶针直径的3倍左右,当然,最短不小于12MM,最长不大于20MM顶针孔在加工镶件顶面前加工,运水在试模后再加工斜面上上顶针要加管位顶边最小4MM顶针硬度HRC55 扁顶针与镶件的配合长度是其宽度的10倍以上圆筒形外径小于12.7MM的可以使用司筒顶出,否则用推板顶出如果Boos柱高度≥15以上,用司筒顶出。
<15,且旁边可以加顶时用顶针,否则还用司筒。
一、司筒规格书写方法如下:∅1/8"*∅3/16"*250 MM∅1/8":司筒针直径∅3/16":司筒针直径250MM:司筒长度(注:司筒针的长度比司筒的长度长50MM 以上时司筒针长度要注明)二、司筒规格书写方法如下:司筒:∅3/16"*250MM 司筒针:∅1/8"*350MM 流动性好的塑料避免用司筒,司筒易磨损,所以易走披峰,更换频繁。
注射模脱螺纹机构类型分析

1 引言
低 。大批量生产时就需要 自动脱螺纹模具 。 自动脱
共有 3 种类型 : ①马 在 瓶盖行业 中, 有很 多瓶盖塑件 都有螺纹 , 而螺 螺纹机构按照动力传动方式来分 , ② 螺纹传动 ; ③齿轮齿条传动 。本文将着重 纹 的脱模方法有两种 : 一种是在材料允许 的情况下 , 达传动 ; 种螺纹旋脱机构的模具结构特点 。 利用材料 的弹性 变形通 过卸料板将 塑件强行从 型芯 介绍以上 3 . 2 旋脱 类模具 结构 上顶 出, 称为强制脱模法 , 简称强脱 ; 另一类是对螺纹 3
. 2 . 1 马达 式 较深 , 材料强度较高 、 螺纹精度要求高的塑件 , 必须采 3
用旋转脱模 的方法 , 简称旋脱 , 这种方 法需要 利用齿
马达有电机和液压马达 。电动机 由于转速过快 ,
较少采用 ; 液压马达由于转速相对较慢 , 轮、 齿条 、 丝杠等 , 把开模时动模的直线运动或电机的 动作不平稳 , 动作平稳 , 安全可靠 , 因此被广泛采用 。使用马达传 转动等动力来源转变成螺纹型芯的转动。
必须 有另外 两个与之互相 结合 的附件 , 即链轮 和链
条 。马 达 、 链轮 、 链条 3 个 最 重 要 的部 件 缺 一 不 可 , 方
可实现 马达传动。
l 处 放 大
能采用螺纹强脱 , 只能采用螺纹旋脱 , 如图 1 所示。
3 模 具 结构 分 析 3 . 1 强脱 类模具 结构
了 自动 脱 螺纹 机构 在模 具设 计 中的应 用 。
关 键词 : 瓶盖; 螺 纹;自动 脱 螺纹机 构
中图分 类 号 : T Q 3 2 0 . 6 6
文 献标 识码 : B
An a l y s i s o f T h r e a d De - Mo l d i n g Me c h a n i s m f o r t h e I n j e c t i o n Mo l d
- 1、下载文档前请自行甄别文档内容的完整性,平台不提供额外的编辑、内容补充、找答案等附加服务。
- 2、"仅部分预览"的文档,不可在线预览部分如存在完整性等问题,可反馈申请退款(可完整预览的文档不适用该条件!)。
- 3、如文档侵犯您的权益,请联系客服反馈,我们会尽快为您处理(人工客服工作时间:9:00-18:30)。
1) 对塑件的要求:由于螺纹表面有沟槽,所以,内螺纹必须 对塑件的要求:由于螺纹表面有沟槽,所以, 由螺纹型芯, 外螺纹必须由螺纹型环成型,而脱模时必 由螺纹型芯, 外螺纹必须由螺纹型环成型, 须从螺纹型芯或螺纹型环上脱出, 须从螺纹型芯或螺纹型环上脱出,两者之间必须作相对转 因此,塑件的外形或端面须有防止转动的花纹或图案, 动,因此,塑件的外形或端面须有防止转动的花纹或图案, 否则难以脱出。 否则难以脱出。 2) 对模具的要求:塑件不能转动,模具应有相应的防转措施 对模具的要求:塑件不能转动, 给予保证。当塑件型腔和螺纹型芯同在动模上时, 给予保证。当塑件型腔和螺纹型芯同在动模上时,型腔可 以保证不使塑件转动。但当型芯和型腔分别处在动、 以保证不使塑件转动。但当型芯和型腔分别处在动、定模 上时,开模后,塑件就离开定模型腔,此时, 上时,开模后,塑件就离开定模型腔,此时,即使塑件外 形有防转花纹也不起作用, 形有防转花纹也不起作用,塑件会留在动模型芯上和它一 起转动而无法脱模,因此在模具上要另设止转机构。 起转动而无法脱模,因此在模具上要另设止转机构。
螺 纹 脱 模
浙江工商职业技术学院
塑件螺纹
很多塑件上带有螺纹, 很多塑件上带有螺纹,螺紋的种类主 要有两大类:内螺纹和外螺纹。 要有两大类:内螺纹和外螺纹。螺纹表面 均带沟槽, 均带沟槽,因此脱模的方式与一般塑件不 它需要有特殊的脱模机构。 同。它需要有特殊的脱模机构。
设计螺纹脱模机构的注意点
设计带螺纹塑件的脱模机构应注意的问题
螺纹脱模方式
带螺纹塑件的脱模方式
对带螺纹塑件的脱模方式主要有以下几种。 对带螺纹塑件的脱模方式主要有以下几种。 1) 手动脱螺纹,这是在塑件成型、开模后,用 手动脱螺纹,这是在塑件成型、开模后, 手工或简单工具将型芯或型环从塑件上旋出。这 手工或简单工具将型芯或型环从塑件上旋出。 类模具的结构简单,易于制造,但劳动强度大, 类模具的结构简单,易于制造,但劳动强度大, 生产效率低。 生产效率低。 2) 强制脱螺纹,这是利用塑件的弹性或型芯的 强制脱螺纹, 弹性,使塑件或型芯与螺纹产生轴向移动, 弹性,使塑件或型芯与螺纹产生轴向移动,强行 将型芯或塑件拉离螺纹而脱模。这类模具结构也 将型芯或塑件拉离螺纹而脱模。 较简单,主要用于螺纹精度要求不高, 较简单,主要用于螺纹精度要求不高,螺紋形状 比较容易脱出的塑件。 比较容易脱出的塑件。
带螺纹塑件的脱模
强制脱螺纹
带螺纹塑件的脱模 内侧抽脱螺纹
带螺纹塑件的脱模 螺纹止动
带螺纹塑件的脱模
模内旋转脱螺纹
带螺纹塑件的脱模
模内旋转脱螺塑件, 螺纹的塑件,为了能 自动卸螺纹在模具内 设有能转动的螺纹型 芯或螺纹型环。 芯或螺纹型环。
螺纹脱模方式
3) 机动脱螺纹,这是利用开模时的直线运动, 机动脱螺纹,这是利用开模时的直线运动, 通过齿条齿轮或丝杠的传动, 通过齿条齿轮或丝杠的传动, 带动螺纹型芯作旋 转运动而使螺纹脱模。这种模具结构较复杂, 转运动而使螺纹脱模。这种模具结构较复杂,但 省力、效率咼、质量好。 省力、效率咼、质量好。 4) 瓣合模脱螺纹,这是采用瓣合型芯或瓣合型 瓣合模脱螺纹, 环来脱螺纹。这种脱模方式, 制造简单, 环来脱螺纹。这种脱模方式, 制造简单,但在螺 纹部分有分型线,且容易产生飞边,清除较难, 纹部分有分型线,且容易产生飞边,清除较难, 螺纹精度不高。 螺纹精度不高。