零件数控加工的走刀路线设计
数控加工中工艺路线设计原则及方法
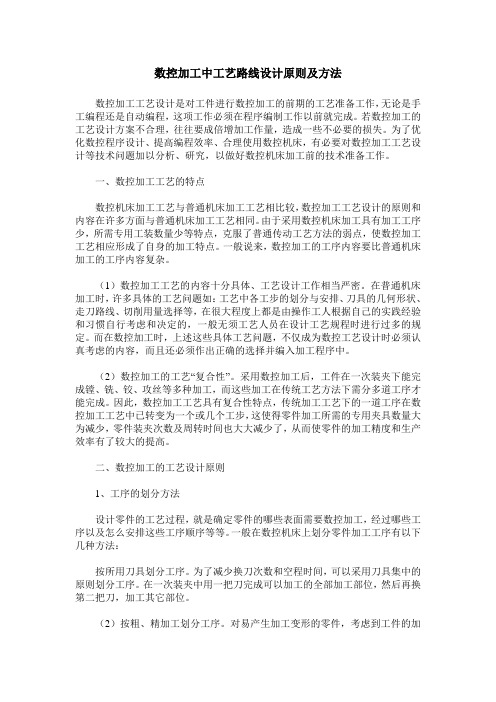
数控加工中工艺路线设计原则及方法数控加工工艺设计是对工件进行数控加工的前期的工艺准备工作,无论是手工编程还是自动编程,这项工作必须在程序编制工作以前就完成。
若数控加工的工艺设计方案不合理,往往要成倍增加工作量,造成一些不必要的损失。
为了优化数控程序设计、提高编程效率、合理使用数控机床,有必要对数控加工工艺设计等技术问题加以分析、研究,以做好数控机床加工前的技术准备工作。
一、数控加工工艺的特点数控机床加工工艺与普通机床加工工艺相比较,数控加工工艺设计的原则和内容在许多方面与普通机床加工工艺相同。
由于采用数控机床加工具有加工工序少,所需专用工装数量少等特点,克服了普通传动工艺方法的弱点,使数控加工工艺相应形成了自身的加工特点。
一般说来,数控加工的工序内容要比普通机床加工的工序内容复杂。
(1)数控加工工艺的内容十分具体、工艺设计工作相当严密。
在普通机床加工时,许多具体的工艺问题如:工艺中各工步的划分与安排、刀具的几何形状、走刀路线、切削用量选择等,在很大程度上都是由操作工人根据自己的实践经验和习惯自行考虑和决定的,一般无须工艺人员在设计工艺规程时进行过多的规定。
而在数控加工时,上述这些具体工艺问题,不仅成为数控工艺设计时必须认真考虑的内容,而且还必须作出正确的选择并编入加工程序中。
(2)数控加工的工艺“复合性”。
采用数控加工后,工件在一次装夹下能完成镗、铣、铰、攻丝等多种加工,而这些加工在传统工艺方法下需分多道工序才能完成。
因此,数控加工工艺具有复合性特点,传统加工工艺下的一道工序在数控加工工艺中已转变为一个或几个工步,这使得零件加工所需的专用夹具数量大为减少,零件装夹次数及周转时间也大大减少了,从而使零件的加工精度和生产效率有了较大的提高。
二、数控加工的工艺设计原则1、工序的划分方法设计零件的工艺过程,就是确定零件的哪些表面需要数控加工,经过哪些工序以及怎么安排这些工序顺序等等。
一般在数控机床上划分零件加工工序有以下几种方法:按所用刀具划分工序。
数控车削加工刀具轨迹自动生成的算法

数控车削加工刀具轨迹自动生成的算法本文针对数控车削加工的特点,结合被加工零件的特征,提出了数控车削加工刀具轨迹自动生成的算法。
该算法在实际应用中,取得了理想的效果。
1 零件图的预处理根据数控车削加工的特点,零件的加工工艺分为:孔加工(包括打中心孔),外(内)表面加工、退刀槽及螺纹加工,根据表面质量的要求,又分为粗加工、半精加工和精加工等工艺。
数控车削加工刀具轨迹的规划,重点外(内)表面粗加工时刀具轨迹的规划处理。
对退刀槽、螺纹样的零件特征在进行表面粗加工时将其用表面代替,如图1。
数控加工中为减少多次安装带来的安装误差,一般采用一次装夹,对那些需要调头加工的部位则采取右偏刀反向走刀切削。
此外,对端面的加工有时选取向下的切削方向。
因此加工时的切削方向分为向左、向右和向下的切削方向。
图1对于倒角和倒圆角等工艺的处理在算法上将其作为表面处理。
对反向走刀切削时的刀具轨迹规划的算法与正向切削时类似,对内表面加工时刀具轨迹规划的算法与外表面切削时也相类似。
另外对精加工时的刀具轨迹规划,以及退刀槽和螺纹加工的刀具轨迹规划处理也较为容易。
一般,为减少刀具轨迹生成算法的复杂性,在刀具轨迹生成前对零件进行刀具干涉处理(刀具干涉处理的算法另文讨论)。
本文仅讨论正向切削外表面时粗加工刀具轨迹生成的算法。
2 刀具轨迹生成的算法图2由于粗加工刀具轨迹规划是从毛坯开始的,因此生成刀具轨迹时必须考虑毛坯的形状,并且随着工步的不同,其毛坯的形状也是不同的,此即工艺毛坯。
由于在轨迹生成前已经进行过刀具干涉的处理,所在刀具轨迹生成时主要考虑的是零件图形的特征。
经过零件图的预处理后,零件图形是由直线和圆弧所构成的连续表面,其中的关键是对图形中凹槽的识别和处理。
如图2所示,零件图形经过处理后,其粗加工的外表面轮廓为ABCDEPFGHIQJKM,经刀具切削方向为左时干涉处理后,其轮廊为ABCDPEFGHQJKM,其阴影部分为欠切削部分,在下一工步加工时,反向走刀切削时的刀具的起点分别为P点和Q点,通过反向向右走切切除其残留部分,从而形成所要求的零件轮廓QIH和PED。
数控机床加工路线的确定

科 之 学 友
Fnfie ar dd e ts e cc me o nA u S
27 0J 0 ̄7固 0 , E
数控机床加 工路线的确定
张士 印
( 台市技术学院 ,山东 烟 台 2 4 0 ) 烟 6 0 6 摘 要: 文章就数控加 工中加工路 线的最近确 定进行 了讨论 , 出了空行程路线如何最短 得
/
\
一 .
’ } ≥
・
Байду номын сангаас
点
:
b 路线 I 图 1最短走刀路线的设计
/
、 、
a 零件图样
C 路线 2
12 合理设置起刀点 . 特别是采用矩形循 环出车外 圆 ,起刀点应设置 在离毛坯较 近的位置 。 13 合理选择换刀点 . 要在保证换刀时不碰工件及机床其他部位 的前提下尽可能的
的时间。 确定进给 路线的工作重点 ,主要 在于确定粗加 工及空行程
后一次走刀 中连续加工出来 。 图 2中 a图所示为用行切方式加 见 工内腔的走刀路线 , 这种走刀方法 能切 除内腔中的全部余量 , 不 留死角 , 不伤轮廓 。但行切法将在两次走刀的起点和终点间 留下 残留高度而达不 到表面要 求的粗糙度 。所 以如采用 图 2中 b图
一
1 9—
维普资讯
科 之 学 友
Fnfie ar rd e ts i cc me eo nA u S
27 0 国 0 ̄ 7 0 月
起砼表 面的早期裂缝 。新浇筑早期拆模 , 在表面引起很大的拉应 力, 出现“ 温度 冲击” 现象 。在砼浇筑初期 , 由于水 化热的散发 , 表 面引起相 当大的拉应 力 , 时表面温度亦较气温为 高 , 此 如果拆 除 模板 , 表面温度骤 降 , 必然引起温 度梯 度 , 从而在 表面 附加一拉 应力, 与水化热应 力迭加 , 再加上 砼干缩 , 表面 的拉应力 达到很 大 的数值 , 就有导致裂缝 的危险。但如果在拆除模板后及时在表 面覆盖一轻 型保 温材 料 , 沫海棉 等 , 于防止砼表面产生过 如泡 对 大 的拉应力 , 具有显著 的效果 。 加筋对大体积砼 的温度应力影响很小 ,因为大体 积砼 的含 筋率极低 , 只是对一般钢筋砼有影 响。在温度不太 高及应力低于 屈服极 限的条件 下 , 的各项性 能是稳定 的 , 与应力状 态 、 钢 而 时 间及温度无关 。钢 的线胀系数与砼线胀系数相差很小 , 在温度变 化时两者间 只发生很小 的内应 力。由于钢的弹性模量 为砼 弹性 模量的 7 1 倍 , 内 应力达到抗拉强度 而开裂时 , 的应 ~5 当 砼 钢筋 力将不超过 10k/ 20 g m , 0 g m ~ 0 / 因此 , 中想要利用钢筋 e kc 在砼 来防止细小裂缝的出现很 困难 。但 加筋 后结构 内的裂缝一般就 变得数 目多 、 间距小 、 宽度与 深度较小 了, 而且 如果钢 筋的直径 细而间距 密时 , 对提 高砼抗裂性的效果较好 。砼和钢筋 砼结构 的
数控铣削加工的走刀路线

数控铣削加工的刀路线反映了工序的加工过程,走刀路线合理与否,关系到工件的加工质量与生产效率。
尤其在数控铣削曲面零件过程中,应认真分析零件的加工要求及其结构特点,找出走刀路线中影响加工效率的因素,在保证零件加工精度和表面粗糙度要求的前提下,应尽量缩短加工路线,从而提高数控机床的加工效率,降低加工成本。
数控加工过程中刀具相对于工件的运动轨迹称为走刀路线。
走刀路线反映了工序的加工过程,确定合理的走刀路线是保证铣削加工精度和表面质量的重要工艺措施之一,也是确定数控编程的前提。
数控铣削加工中走刀路线对工件的加工精度和表面质量有直接的影响,走刀路线合理与否,还关系到加工的生产效率,因此每道工序走刀路线的确定都是非常重要的。
一、走刀路线的确定原则影响走刀路线的因素很多,有工艺方法、工件材料及状态、加工精度及表面粗糙度要求、工件刚度、加工余量、刀具的刚度及耐用度、机床类型和工件的轮廓形状等。
在确定走刀路线时,主要应遵循以下原则:(1)保证产品质量,应将保证工件的加工精度和表面粗糙度要求放在首位。
(2)在保证工件加工质量的前提下,应力求走刀路线最短,并尽量减少空行程时间,提高加工效率。
(3)在满足工件加工质量、生产效率等条件下,尽量简化数学处理的数值计算工作量,以简化编程工作。
此外,在确定走刀路线时,还要综合考虑工件、机床与刀具等多方面因素,确定一次走刀还是多次走刀,以及设计刀具的切入点与切出点,切入方向与切出方向。
在铣削加工中,还要确定是采用顺铣还是逆铣等。
二、铣削方式的选择铣削有顺铣和逆铣两种方式。
铣削加工中是采用顺铣还是逆铣,对工件表面粗糙度有较大的影响。
确定铣削方式应根据工件的加工要求,材料的性质、状态、使用机床及刀具等条件综合考虑。
由于采用顺铣方式,工件加工表面质量较好,刀齿磨损小,因此,一般情况下,尽可能采用顺铣,尤其是精铣内外轮廓、精铣铝镁合金、钛合金或耐热合金时,应尽量按顺铣方式安排走刀路线。
三、铣削曲面类零件走刀路线的确定铣削曲面类零件的走刀路线加工面为空间曲面的零件称为曲面类零件。
数控加工路线的确定

(1)加工路线的确定原则在数控加工中,刀具刀位点相对于工件运动的轨迹称为加工路线。
确定加工路线是编写程序前的重要步骤,加工路线的确定应遵循以下原则。
1.加工路线应保证被加工零件的精度和表面粗糙度,且效率较高。
2.使数值计算简单,以减少编程工作量。
3.应使加工路线最短,这样既可以减少程序段,又可以减少空刀时间。
此外,确定加工路线时,还要考虑工件的加工余量和机床、刀具的刚度等情况,确定是一次走刀,还是多次走刀来完成加工,以及在铣削加工中是采用顺铣还是逆铣等。
(2)辅助程序段的设计1.轮廓加工的进退刀路径设计在对零件的轮廓进行加工时,为了保证零件的加工精度和表面粗糙度符合要求,应合理地设计进退刀路径。
如图1所示,当铣削平面零件外轮廓时,一般采用立铣刀侧刃切削。
刀具切入工件时,应避免沿零件外廓的法向切入,而应沿外廓曲线延长线的切向切入,以避免在切入处产生刀具的刻痕而影响表面质量,保证零件外廓曲线平滑过渡。
同理,在切离工件时,也应避免在工件的轮廓处直接退刀,而应该沿零件轮廓延长线的切向逐渐切离工件。
图1 外轮廓加工刀具的切入切出图2 内轮廓加工刀具的切入和切出1铣削封闭的内轮廓表面时,若内轮廓曲线允许外延,则应沿切线方向切入切出。
若内轮廓曲线不允许外延(见图2),刀具只能沿内轮廓曲线的法向切入切出,此时刀具的切入切出点应尽量选在内轮廓曲线两几何元素的交点处。
当内部几何元素相切无交点时(见图3),为防止刀具在轮廓拐角处留下凹口,刀具切入切出点应远离拐角。
图3 内轮廓加工刀具的切入和切出2如图4所示,用圆弧插补方式铣削外整圆时,当整圆加工完毕时,不要在切点处直接退刀,而应让刀具沿切线方向多运动一段距离,以免取消刀补时,刀具与工件表面相碰,造成工件报废。
铣削内圆弧时也要遵循从切向切入的原则。
最好安排从圆弧过渡到圆弧的加工路线(见图5,这样可以提高内孔表面的加工精度和加工质量。
本篇文章来源于数控网|原文链接:2.孔加工时引伸距离的确定孔加工在确定轴向尺寸时,应考虑一些辅助尺寸,包括刀具的引入距离和超越距离。
数控加工中工艺路线设计原则及方法
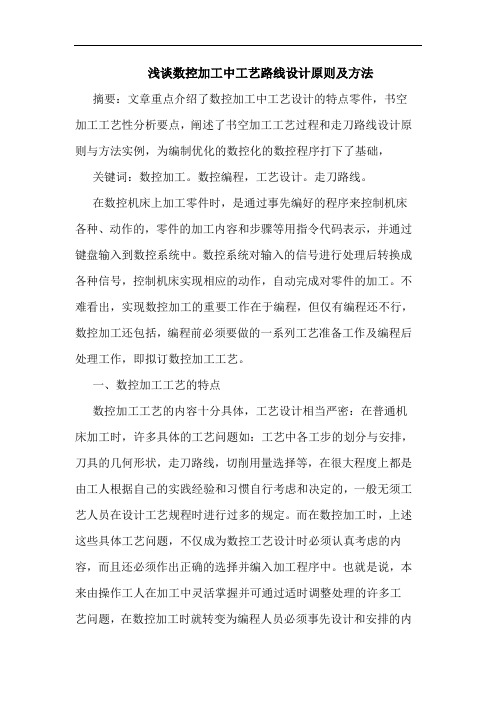
浅谈数控加工中工艺路线设计原则及方法摘要:文章重点介绍了数控加工中工艺设计的特点零件,书空加工工艺性分析要点,阐述了书空加工工艺过程和走刀路线设计原则与方法实例,为编制优化的数控化的数控程序打下了基础,关键词:数控加工。
数控编程,工艺设计。
走刀路线。
在数控机床上加工零件时,是通过事先编好的程序来控制机床各种、动作的,零件的加工内容和步骤等用指令代码表示,并通过键盘输入到数控系统中。
数控系统对输入的信号进行处理后转换成各种信号,控制机床实现相应的动作,自动完成对零件的加工。
不难看出,实现数控加工的重要工作在于编程,但仅有编程还不行,数控加工还包括,编程前必须要做的一系列工艺准备工作及编程后处理工作,即拟订数控加工工艺。
一、数控加工工艺的特点数控加工工艺的内容十分具体,工艺设计相当严密:在普通机床加工时,许多具体的工艺问题如:工艺中各工步的划分与安排,刀具的几何形状,走刀路线,切削用量选择等,在很大程度上都是由工人根据自己的实践经验和习惯自行考虑和决定的,一般无须工艺人员在设计工艺规程时进行过多的规定。
而在数控加工时,上述这些具体工艺问题,不仅成为数控工艺设计时必须认真考虑的内容,而且还必须作出正确的选择并编入加工程序中。
也就是说,本来由操作工人在加工中灵活掌握并可通过适时调整处理的许多工艺问题,在数控加工时就转变为编程人员必须事先设计和安排的内容。
二、零件数控加工的工艺分析要点数控加工前,必须首先对图纸进行仔细的数控加工工艺性分析,应重点从数控加工的方便性与可能性两个角度进行审查和分析。
例如:(一)首先分析零件图纸中的尺寸数据的给出是否符合编程方便的原则1、零件图纸中的尺寸标注方法是否适应数控加工的特点;2、够成零件轮廊的几何元素的条件是否充分。
因为在手工编程时,要计算够成零件轮廊的所有集合元素进行定义,如果某一条件不充分,则无法计算零件轮廊的基点坐标,无法表达零件轮廊的几何元素,导致无法进行编程,因此在分析零件图时,要分析几何元素的给定田间是否充分。
数控加工走刀路线图介绍

14.4 数控加工走刀路线图
数控加工走刀路线图零件图号工序号 2 工步号 2 程序号O0002 机床型号KV650 程序段号加工内容铣心型轮廓共 6 页第 2 页
编程
校对
审批
符号
含义抬刀下刀编程原点起刀点
走刀
方向
走刀线
相交
爬斜坡铰孔行切数控加工走刀路线图零件图号工序号 3 工步号 3 程序号O0003 机床型号KV650 程序段号加工内容挖槽共 6 页第 3 页
编程
校对
审批符号
含义抬刀下刀编程原点起刀点走刀
方向
走刀线
相交
爬斜坡铰孔行切
数控加工走刀路线图零件图号工序号 5 工步号5-8 程序号O0005
钻孔
编程
校对
审批符号
含义抬刀下刀编程原点起刀点走刀
方向
走刀线
相交
爬斜坡铰孔行切
数控加工走刀路线图零件图号工序号 6 工步号13 程序号O0006 机床型号KV650 程序段号加工内容加工内球面共 6 页第 6 页
编程
校对
审批。
数控加工工艺路线设计
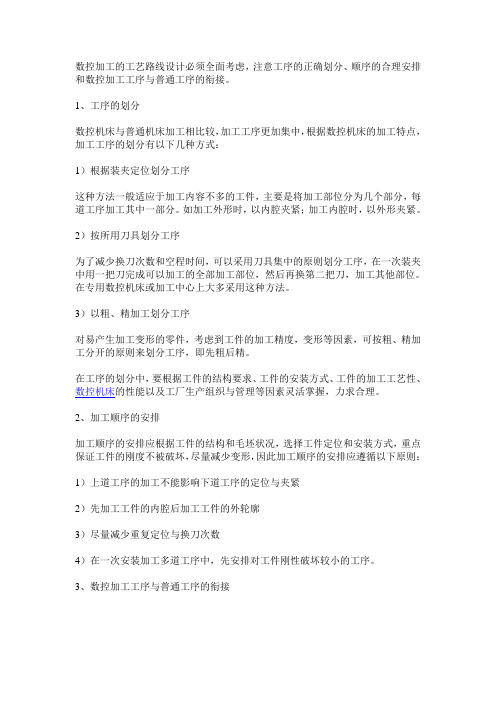
数控加工的工艺路线设计必须全面考虑,注意工序的正确划分、顺序的合理安排和数控加工工序与普通工序的衔接。
1、工序的划分数控机床与普通机床加工相比较,加工工序更加集中,根据数控机床的加工特点,加工工序的划分有以下几种方式:1)根据装夹定位划分工序这种方法一般适应于加工内容不多的工件,主要是将加工部位分为几个部分,每道工序加工其中一部分。
如加工外形时,以内腔夹紧;加工内腔时,以外形夹紧。
2)按所用刀具划分工序为了减少换刀次数和空程时间,可以采用刀具集中的原则划分工序,在一次装夹中用一把刀完成可以加工的全部加工部位,然后再换第二把刀,加工其他部位。
在专用数控机床或加工中心上大多采用这种方法。
3)以粗、精加工划分工序对易产生加工变形的零件,考虑到工件的加工精度,变形等因素,可按粗、精加工分开的原则来划分工序,即先粗后精。
在工序的划分中,要根据工件的结构要求、工件的安装方式、工件的加工工艺性、数控机床的性能以及工厂生产组织与管理等因素灵活掌握,力求合理。
2、加工顺序的安排加工顺序的安排应根据工件的结构和毛坯状况,选择工件定位和安装方式,重点保证工件的刚度不被破坏,尽量减少变形,因此加工顺序的安排应遵循以下原则:1)上道工序的加工不能影响下道工序的定位与夹紧2)先加工工件的内腔后加工工件的外轮廓3)尽量减少重复定位与换刀次数4)在一次安装加工多道工序中,先安排对工件刚性破坏较小的工序。
3、数控加工工序与普通工序的衔接由于数控加工工序穿插在工件加工的整个工艺过程之中,各道工序需要相互建立状态要求,如加工余量的预留,定位面与孔的精度和形位公差要求,矫形工序的技术要求,毛坯的热处理等要求,各道工序必须前后兼顾综合考虑。
4、数控机床加工工序和加工路线的设计数控机床加工工序设计的主要任务:确定工序的具体加工内容、切削用量、工艺装备、定位安装方式及刀具运动轨迹,为编制程序作好准备。
其中加工路线的设定是很重要的环节,加工路线是刀具在切削加工过程中刀位点相对于工件的运动轨迹,它不仅包括加工工序的内容,也反映加工顺序的安排,因而加工路线是编写加工程序的重要依据。
- 1、下载文档前请自行甄别文档内容的完整性,平台不提供额外的编辑、内容补充、找答案等附加服务。
- 2、"仅部分预览"的文档,不可在线预览部分如存在完整性等问题,可反馈申请退款(可完整预览的文档不适用该条件!)。
- 3、如文档侵犯您的权益,请联系客服反馈,我们会尽快为您处理(人工客服工作时间:9:00-18:30)。
零件数控加工的走刀路线设计
摘要:走刀路线是指切削加工过程中刀具相对于被加工零件的运动轨迹和运动方向,即指刀具从对刀点开始运动起,直至返回该点并结束加工程序所经过的路径,包括切削加工的路径及刀具引入、返回等非切削空行程。
走刀路线是编制程序的依据之一。
关键词:数控加工;走刀路线
1.确定走刀路线设计原则
(1)走刀路线应保证被加工工件的精度和表面粗糙度。
(2)应尽量使加工路线最短,减少空行程时间,以提高加工效率;(3)合理选用铣削加工中的顺铣或逆铣方式。
(4)选择工件加工变形小的加工路线。
(5)使数值计算最简单和减少程序段,以减少编程工作量。
(6)根据工件情况,确定循环加工次数。
(7)合理设计刀具的切入与切出的方向。
2铣削加工中加工路线的选择要点
2.1在数控铣床上铣削外轮廓零件时,为了保证轮廓表面质量的要求,应设计合理的刀具切入和切出时的进、退刀位置。
2.2铣削封闭内轮廓表面零件时也要注意刀具切入和切出时的运动轨迹。
为了提高加工精度和减少表面粗糙度,在铣削封闭的内轮廓时,因刀具切入、切出不允许外延,此时刀具的切入和切出点尽量选在内轮廓曲线两几何元素的交点处或者以圆弧切向进刀。
用行切法加工凹槽,其加工路线最短,但表面租糙度差,适用于对表面粗糙度要求不太高的粗加工或半精加工。
用环切法加工凹槽,其表面粗糙度最好,但加工路线最长。
用综合法加工凹槽,即先采用行切法粗加工,最终轮廓用环切法再沿轮廓切削一周进行精加工,使凹槽轮廓表面光整,易保证凹槽侧面达到所要求的表面质量。
见图2.1。
图2.1综合法
2.3用圆弧插补铣削整圆时,当整圆加工完毕后,要让刀具最好沿切线方向多运动一段距离,以免取消刀具补偿时,刀具与工件表面发生碰撞,造成工件报废。
2.4在铣削零件时,要根据工件的材料等因素考虑铣削方式,顺铣效率高节能性好,但当工件表面有硬皮时,应采用逆铣的加工路线进行加工。
2.5在铣削圆弧与直线的连接处,应选用直径较小的刀具,采用补加工的方式消除欠切现象。
3钻削加工加工路线的选择要点
对加工精度要求较高的孔系时,安排的镗孔路线一定要注意各孔的定位方向要一致,以避免传动系统或检测系统的误差对定位精度的影响。
4其它情况的选择要点
(1)在表面加工时,应尽量避免加工停顿现象。
(2)在确定加工路线时,同时也要兼顾工序集中原则,尽量在一次装夹中,尽可能使用同一把刀具完成较多的加工表面。
(3)在安排加工路线过程中,通过合理的选择起刀点、换刀点来合理安排空行程的路线提高生产效率。
(4)应尽量采用子程序、镜像功能、宏程序的调用、固定循环的使用等,以达到减少编程的工作量。
5刀具的选择
5.1数控加工常用刀具的种类及性能
数控加工刀具必须适应数控机床高速、高效和自动化程度高的特点。
数控刀具的分类有多种方法。
根据刀具结构可分为:①整体式,②镶嵌式。
根据制造刀具所用的材料可分为;①高速钢刀具;②硬质合金刀具;③金刚石刀具;
④陶瓷刀具等。
从切削工艺上可分为;①车削刀具;②钻削刀具;③镗削刀具:④铣削刀具等。
刀具材料应具备的性能:
(1)高硬度刀具材料的硬度应高于工件的硬度,常温硬度应在HRC68以上;(2)足够的韧性承受切削力、振动和冲击:(3)高耐磨性;(4)良好的工艺性。
5.2选择数控刀具的原则
刀具选择总的原则是:安装调整方便,刚性好,耐用度和精度高。
在满足加工要求的前提下,尽量选择较短的刀柄,以提高刀具加工的刚性。
选取刀具时,要使刀具的尺寸与被加工工件的表面尺寸相适应。
平面轮廓的
加工,常采用立铣刀;铣削平面时,应选镶硬质合金刀片面铣刀:加工毛坯表面或粗加工孔时,可选取镶硬质合金刀片的铣刀;对一些立体型面和变斜角轮廓外形的加工,常采用球头铣刀、环形铣刀、锥形铣刀和梯形铣刀等。
在进行曲面加工时只要在保证精度的前提下,无论是曲面的粗加工还是精加工,都应优先选择平头刀。
在数控加工中,铣削平面零件内外轮廓及铣削平面常用平底立铣刀,该刀具有关参数的经验数据如下:(1)铣刀半径RD约为零件内轮廓面的最小曲率半径的0.8-0.9倍;(2)零件的加工高度H≤(1/4-1/6)RD;(3)刀具的排列顺序应遵循以下原则:
①尽量减少刀具数量;②一把刀具装夹后,应完成其所能进行的所有加工部位;③粗精加工的刀具应分开使用;④先面后孔;⑤先进行曲面精加工,后进行二维轮廓精加工;⑥应尽可能利用数控机床的自动换刀功能,以提高生产效率。
结论
正确地选择对刀点和换刀点的位置、零件安装方法的确定、刀具及其切削用量的选择、工艺文件的编写以及数控加工工序与普通工序的衔接等等有明确的认识,应尽量做到工序集中,工艺路线最短,机床辅助时间最少。
参考文献
[1]周济,周艳红.数控加工技术.北京:国防工业出版社,2002:l~70.
[2]杨皖苏,严鸿和.机械科学与技术,1997,26(4):l~6.。