4x150万吨锅炉石灰石膏法脱硫方案
石灰石-石灰-石膏法工艺流程

脱硫后的烟气依次经过除雾器出去雾滴,在经过换热器或加热器升温后,由烟囱排入大气。由于吸收剂浆液通过循环泵反复循环与烟气接触,吸收剂利用率很高。
石灰/石灰石-石膏法烟气脱硫技术
工艺说明:
石灰/石灰石-,脱硫效率达95%以上等优点,已在意大利、捷克、泰国等许多国家得到应用,取得十分理想的烟气净化效果。目前,此技术在我国广泛应用,工艺已经成熟。
工艺流程:
烟气经除尘后,通过吸收塔入口区从浆液池上部进塔体,在吸收塔内,热烟气逆流向上与自上而下的浆液接触发生化学吸收反应,并被冷却。添加的石灰石浆液由石灰石浆液泵输送至吸收塔,与吸收塔内的浆液混合,混合浆液经循环泵向上输送由多喷嘴层喷出。浆液从烟气中吸收二氧化硫以及其它酸性物质,在液相中二氧化硫与碳酸钙反应,形成亚硫酸钙。
石灰石石膏湿法脱硫工艺流程

石灰石石膏湿法烟气脱硫技术1、石灰石/石膏湿法烟气脱硫技术特点:1).高速气流设计增强了物质传递能力,降低了系统的成本,标准设计烟气流速达到4.0m/s 。
2).技术成熟可靠,多于55,000 MWe的湿法脱硫安装业绩。
3) .最优的塔体尺寸,系统采用最优尺寸,平衡了SO2去除与压降的关系,使得资金投入和运行成本最低。
4).吸收塔液体再分配装置,有效避免烟气爬壁现象的产生,提高经济性,降低能耗。
从而达到:脱硫效率高达95%以上,有利于地区和电厂实行总量控制;技术成熟,设备运行可靠性高(系统可利用率达98%以上);xx处理烟气量大,SO2脱除量大;适用于任何含硫量的煤种的烟气脱硫;对锅炉负荷变化的适应性强(30%—100%BMCR);设备布置紧凑减少了场地需求;处理后的烟气含尘量大大减少;吸收剂(石灰石)资源丰富,价廉易得;脱硫副产物(石膏)便于综合利用,经济效益显著;2、系统基本工艺流程石灰石(石灰)/ 石膏湿法脱硫工艺系统主要有:烟气系统、吸收氧化系统、浆液制备系统、石膏脱水系统、排放系统组成。
其基本工艺流程如下:锅炉烟气经电除尘器除尘后,通过增压风机、GGH可选)降温后进入吸收塔。
在吸收塔内烟气向上流动且被向下流动的循环浆液以逆流方式洗涤。
循环浆液则通过喷浆层内设置的喷嘴喷射到吸收塔中,以便脱除SO2、SO3、HCL和HF,与此同时在强制氧化工艺”的处理下反应的副产物被导入的空气氧化为石膏(CaS042H2O,并消耗作为吸收剂的石灰石。
循环浆液通过浆液循环泵向上输送到喷淋层中,通过喷嘴进行雾化,可使气体和液体得以充分接触。
每个泵通常与其各自的喷淋层相连接,即通常采用单元制。
在吸收塔中,石灰石与二氧化硫反应生成石膏,这部分石膏浆液通过石膏浆液泵排出,进入石膏脱水系统。
脱水系统主要包括石膏水力旋流器(作为一级脱水设备)、浆液分配器和真空皮带脱水机。
经过净化处理的烟气流经两级除雾器除雾,在此处将清洁烟气中所携带的浆液雾滴去除。
石灰石石膏湿法烟气脱硫工艺

低 比湿磨约高10%
简单 简单 需防粉尘 适合多点供应 可间断运行
要求较高 较高 复杂
管道(需防腐防堵) 高
复杂 复杂 需防泄漏 适合单点供应 须连续运行
主要系统及设备介绍—石灰石浆液制备系统及设备
斗式提升机 地下受料斗
石灰石仓 皮带称量给料器
破碎机
MPS磨机 收尘器
石灰石料仓
后橡B a胶c k R衬u b套b e r L in e r B a c k S p lit C后a s盖in g
金属合金
叶MIemt apleAl l
llo er
y
轮
Front Rubber
前L i橡n e r胶衬套
F前r o n盖t S p lit
C asing
金M属et合a l A金llo护y 套
T h ro a tb u sh
((前fr o磨n t w损e a盘r )
p la te )
主要系统及设备介绍—浆液循环系统
循环浆泵实物图
主要系统及设备介绍—氧化系统
(三) 氧化系统
强制氧化在浆液槽底部通入空气,浆液中的HSO3-基本能够全部被氧化。
搅拌器和空气喷枪组合式(Agitator Air Lance Assemblies,ALS)强制氧化装置
(四)除雾器
除雾器由除雾器叶片、卡具、夹具、支架等按一定的结构形式组装而成。 除雾器布置形式通常有水平形、人字形、V字形、组合形等。多采用人字形、V字形 布置。
除雾器的工作原理都是利用烟气折向通过曲折的挡板,流向多次发生偏 转,烟气中携带的液滴由于惯性作用撞击在挡板上被捕集下来。
气流
小液滴 液膜
大液滴
输送机
4x150万吨锅炉石灰石膏法脱硫方案
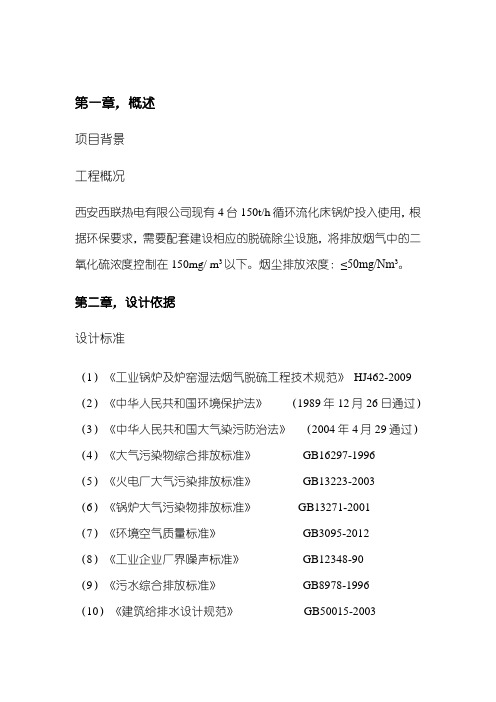
第一章,概述项目背景工程概况西安西联热电有限公司现有4台150t/h循环流化床锅炉投入使用,根据环保要求,需要配套建设相应的脱硫除尘设施,将排放烟气中的二氧化硫浓度控制在150mg/ m3以下。
烟尘排放浓度:≤50mg/Nm3。
第二章,设计依据设计标准(1)《工业锅炉及炉窑湿法烟气脱硫工程技术规范》HJ462-2009(2)《中华人民共和国环境保护法》(1989年12月26日通过)(3)《中华人民共和国大气染污防治法》(2004年4月29通过)(4)《大气污染物综合排放标准》GB16297-1996(5)《火电厂大气污染排放标准》GB13223-2003(6)《锅炉大气污染物排放标准》GB13271-2001(7)《环境空气质量标准》GB3095-2012(8)《工业企业厂界噪声标准》GB12348-90(9)《污水综合排放标准》GB8978-1996(10)《建筑给排水设计规范》GB50015-2003(11)《建筑地基基础设计规范》GB50007-2002(12)《混凝土结构设计规范》GB50010-2002(13)《花岗岩类湿式烟气脱硫除尘装置》HJT319-2006(14)《花岗岩建材检验标准》JC204-205-1996(15)《脱硫除尘专用建材检验标准》GB/(16)《湿式烟气脱硫除尘装置技术要求》HJ/T288-2006(17)《压力容器技术管理规定》YB9070—92(18)《钢制压力容器》GBl50—98设计原则(1)贯彻执行国家经济建设和新、改、扩建项目的一系列方针政策和规范,在工程设计中贯彻切合实际、技术先进、经济合理、安全适用原则,确保排放烟气达标并最大限度地提高工程的经济效益。
(2)选用先进可靠的脱硫技术工艺,确保脱硫效率高的前提下,强调系统的安全、稳定性能,并减少系统运行费用。
(3)充分结合厂方现有的客观条件,因地制宜,制定具有针对性的技术方案。
(4)系统平面布置要求紧凑、合理、美观,实现功能分区,方便运行管理。
石灰、石灰石-石膏法烟气脱硫

吸收塔外观
喷淋层的喷嘴
除雾器
脱硫机理及工艺流程
脱硫系统的工艺及设备
脱硫技术分析
四、石膏脱水系统
石膏脱水系统的作用 是将吸收塔底部抽出 的石膏浆液脱水成固 态的湿石膏。
石灰/石灰石烟—气石脱膏硫法技烟术气比脱选硫
脱硫机理及工艺流程
脱硫系统的工艺及设备
脱硫技术分析
五、工艺水、工业水和废水排放系统
能广泛应用各种规模 的多种行业,尤其适合 于脱硫要求严格的大 规模企业。
感谢观看!
Ⅰ
气态SO2与吸收浆液混合、溶解
Ⅱ SO2进行反应生成亚硫根
Ⅲ 亚硫根氧化生成硫酸根
Ⅳ
硫酸根与吸收剂反应生成硫酸盐
Ⅴ 硫酸盐从吸收剂中分离
脱硫机理及工艺流程
脱硫系统的工艺及设备
脱硫技术分析
石灰/石灰石—石膏法烟气脱硫
脱硫机理及工艺流程
脱硫系统的工艺及设备 脱硫技术分析
石灰/石灰石烟—气石脱膏硫法技烟术气比脱选硫
工艺水主要为循环水,为脱硫系统提供各生产
设备正常工作所需水量。
工业水主要为补充水,为脱硫系统的湿式球磨
机和真空皮带机提供正常的所需水量。 废水主要由石膏脱水系统产生,pH值范围4~6, 含有悬浮物及汞、铜、铅、镍、锌等金属污染物, 需要处理后才能排放。
石灰/石灰石烟—气石脱膏硫法技烟术气比脱选硫
工艺水的输送
脱硫技术分析
石灰/石灰石烟—气石脱膏硫法技烟术气比脱选硫
技 术
优势
劣势
适用工况
①技术成熟; 石 ②脱硫效率高 灰 (90%~98%); 石- ③脱硫剂来源广泛 石 且价格低廉; 膏 ④副产物脱硫石膏 法 可作为水泥添加剂
石灰石石膏法脱硫方程式

石灰石石膏法脱硫方程式
石灰石石膏法是一种常见的脱硫方法,它通过反应生成石膏来去除燃煤等工业过程中产生的硫化物。
石灰石石膏法脱硫的方程式如下:
1. 脱硫反应:
CaCO3 + SO2 + H2O → CaSO3 · 1/2H2O + CO2
这是最基本的反应方程式,石灰石(CaCO3)与二氧化硫(SO2)和水(H2O)反应生成硫酸钙(CaSO3 · 1/2H2O)和二氧化碳(CO2)。
2. 氧化反应:
2CaSO3 · 1/2H2O + O2 → 2CaSO4 · 2H2O
为了使脱硫剂再生,所生成的硫酸钙(CaSO3 · 1/2H2O)需要氧化为二水合硫酸钙(CaSO4 · 2H2O)。
这一氧化反应通常在除 SOx 设备之外的其他装置中进行。
以上是石灰石石膏法脱硫的基本反应方程式,实际过程中还存在其他辅助反应和中间产物的生成。
石灰石膏法脱硫技术介绍
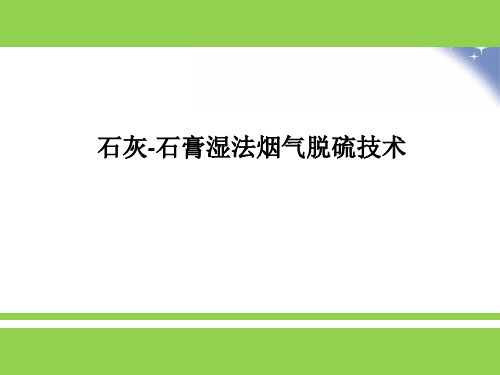
主要内容
1 石灰-石膏法工艺原理 2 工艺系统及主要设备介绍 3 我公司脱硫工艺的技术特征 4 系统性能指标
1. 工艺原理
石灰—石膏湿法烟气脱硫工艺
该工艺采用石灰作为脱硫吸收剂,粉状的生石灰与水混 合搅拌制成吸收浆液,在吸收塔内,吸收浆液与烟气接 触混合,烟气中的二氧化硫与浆液中的碱性物质以及鼓 入的氧化空气进行化学反应吸收脱除二氧化硫,最终产 物为石膏。脱硫后的洁净烟气通过除雾器除去雾滴经烟 囱排放。
,该混合物以缓冲液的性质存在,使吸收的pH值保持相对平稳。 在浆液循环槽,充入空气进行强制氧化,其反应如下: HSO3-+1/2O2→ SO42-+ H+ SO32-+1/2O2→ SO42-
石灰石-石膏法流程示意图
石灰-石膏法技术特点
(1) 脱硫效率高达96%以上,对煤种适用性强,可用于高中低 含硫煤种。
增压风机
一般选用静叶可调轴流风机,适用于风机风量大,压升低。
轴流风机模型图
挡板门
2.3 SO2吸收系统
空塔喷淋:内部结构简 单,具有负荷大、不易 堵塞、操作弹性宽。
塔内主要构件包括:
入口喷淋层 雾化喷淋层 二级除雾器
吸收塔配套设备有:
循环泵 氧化风机 搅拌器
吸 收 塔 示 意 图
SO2吸收系统 石膏脱水系统 工艺水系统
2.1 吸收剂制备系统
石灰品质要求:
CaO含量≥85% 原料粒径≤6mm 石灰活性要求:(T60) ≤4 min(DL/T 943-2005)符合在4分钟内熟
化反应温度从20℃升高到60℃ 石灰品质达不到上述要求一般不影响脱硫设备的运行,但会影响
性能。
4 实时调节增压风机电机转速,大大节省系统运行电耗。
锅炉脱硫工艺

针对于大中型锅炉的湿法烟气脱硫技术,是采用德国Babcock Borsig Power公司授权的石灰石--石膏湿法烟气脱硫工艺技术,完成了多项4×500MW机组烟气脱硫工程业绩。
该技术具有以下特点:脱硫效率高节省吸附剂/能耗低性能可靠,使用方便生成稳定的商用石膏在整个工程期间公司提供全方位的服务包括供货,安装,工程管理,现场调试和投产服务石灰石--石膏湿法烟气脱硫工艺流程图1、吸收剂槽2、吸收带3、除雾器4、氧化鼓风机5、吸附剂仓6、新配制的洗涤悬吊槽7、石膏浆旋流器站8、真空皮带过滤器9、真空泵10、废水旋流器站11、循环水槽1、石灰石-石膏法脱硫工艺(Gypsum Recovery Process)石灰石-石膏法脱硫工艺流程图工艺特点:有机酸隔离,SO2吸收率高,在烟气流量及SO2容量变化范围大的情况下也能稳定运行;能够在低PH值(4-5)条件下吸收,在吸收塔里很易氧化,所以不要强制的氧化槽也不要强制的氧化硫酸,吸收剂利用率高;制造商业用石膏(用于石膏、木板、水泥等)2、放流法脱硫工艺(MgSO4 Purge Process)放流法脱硫工艺流程图工艺特点:SO2吸收率高;操作适应性高;吸收塔压力损失小;避免结垢系统;运转低成本;使排放的废水量达到最小。
3、半干法脱硫工艺(Semi-dry Process)半干法脱硫工艺流程图工艺特点:运转低成本;无废液产生;操作及维护简便;无须白烟气防止系统。
4、干法脱硫工艺(Dry Process)5、芒硝法脱硫工艺(Na2SO4 Recovery System)干法脱硫工艺流程图工艺特点:运转低成本;无废液产生;操作及维护简便;无须白烟气防止系统。
芒硝法脱硫工艺流程图工艺特点:SO2吸收率高;制成高纯度芒硝;结晶器采用了MVR系统,所以能量消耗低;结晶器避免结垢故障。
6、亚硫酸钠法脱硫工艺(Na2SO3 Recovery System)亚硫酸钠法脱硫工艺流程图工艺特点:SO2吸收率高;运转低成本;操作适应性高;吸收塔压力损失小;通过增加结晶系统可得到Na2SO4结晶。
- 1、下载文档前请自行甄别文档内容的完整性,平台不提供额外的编辑、内容补充、找答案等附加服务。
- 2、"仅部分预览"的文档,不可在线预览部分如存在完整性等问题,可反馈申请退款(可完整预览的文档不适用该条件!)。
- 3、如文档侵犯您的权益,请联系客服反馈,我们会尽快为您处理(人工客服工作时间:9:00-18:30)。
第一章,概述1.1项目背景1.2工程概况西安西联热电有限公司现有4台150t/h循环流化床锅炉投入使用,根据环保要求,需要配套建设相应的脱硫除尘设施,将排放烟气中的二氧化硫浓度控制在150mg/ m3以下。
烟尘排放浓度:≤50mg/Nm3。
第二章,设计依据2.1设计标准(1)《工业锅炉及炉窑湿法烟气脱硫工程技术规范》HJ462-2009(2)《中华人民共和国环境保护法》(1989年12月26日通过)(3)《中华人民共和国大气染污防治法》(2004年4月29通过)(4)《大气污染物综合排放标准》GB16297-1996(5)《火电厂大气污染排放标准》GB13223-2003(6)《锅炉大气污染物排放标准》GB13271-2001(7)《环境空气质量标准》GB3095-2012(8)《工业企业厂界噪声标准》GB12348-90(9)《污水综合排放标准》GB8978-1996(10)《建筑给排水设计规范》GB50015-2003(11)《建筑地基基础设计规范》GB50007-2002(12)《混凝土结构设计规范》GB50010-2002(13)《花岗岩类湿式烟气脱硫除尘装置》HJT319-2006(14)《花岗岩建材检验标准》JC204-205-1996(15)《脱硫除尘专用建材检验标准》GB/T4100.1-1999(16)《湿式烟气脱硫除尘装置技术要求》HJ/T288-2006(17)《压力容器技术管理规定》YB9070—92 (18)《钢制压力容器》GBl50—982.2设计原则(1)贯彻执行国家经济建设和新、改、扩建项目的一系列方针政策和规范,在工程设计中贯彻切合实际、技术先进、经济合理、安全适用原则,确保排放烟气达标并最大限度地提高工程的经济效益。
(2)选用先进可靠的脱硫技术工艺,确保脱硫效率高的前提下,强调系统的安全、稳定性能,并减少系统运行费用。
(3)充分结合厂方现有的客观条件,因地制宜,制定具有针对性的技术方案。
(4)系统平面布置要求紧凑、合理、美观,实现功能分区,方便运行管理。
(5)操作简单、维护方便、可靠性高、噪音小、运行稳定,无二次污染。
2.3设计范围本设计范围包括烟气脱硫系统工艺、系统结构、电气等专业的设计,工程设计范围:从锅炉出口至烟囱进口前水平烟道接口之间的脱硫装置和相应配套的附属设施。
包括:(1)脱硫剂制备系统(2)烟气系统(3)SO2吸收系统(4)石膏脱水处理系统(5)工艺水系统(6)电气控制系统2.4设计参数2.4.1原始参数:1)锅炉原始参数2)煤质资料2.4.2 排放标准除尘+脱硫总除尘效率:98%除尘脱硫后粉尘排放浓度:50mg/ Nm3脱硫效率:≥96%脱硫后SO2排放浓度:≤150mg/ Nm3装置可用率:≥98%净烟气排放温度:≯50℃;第三章,工艺选择及说明3.1脱硫技术现状煤炭脱硫一般分为燃烧前的煤炭洗选脱硫;燃烧中掺烧石灰石脱硫以及燃烧后的烟气脱硫技术,目前国内外应用最广泛的方法是烟气脱硫。
烟气脱硫技术(FGD)主要利用各种碱性的吸收剂或吸附剂捕集烟气中的二氧化硫,将之转化为较为稳定且易机械分离的硫的化合物或单质硫,从而达到脱硫的目的。
FGD的方法按脱硫剂和脱硫产物含水量的多少可分为两类:①湿法,即采用液体吸收剂如水或碱性溶液(或浆液)等洗涤以除去二氧化硫。
②干法,用粉状或粒状吸收剂、吸附剂或催化剂以除去二氧化硫。
按脱硫产物是否回用可分为回收法和抛弃法。
按照吸收二氧化硫后吸收剂的处理方式可分为再生法和非再生法(抛弃法)。
国外烟气脱硫研究始于1850年,经过多年的发展,至今为止,世界上已有2500多套FGD装置,总能力已达200,000MW(以电厂的发电能力计),处理烟气量700Mm3/h,一年可脱二氧化硫近10Mt,这些装置的90%在美国、日本和德国。
尽管各国开发的FGD方法很多,但真正进行工业应用的方法仅是有限的十几种。
其中湿式洗涤法(含抛弃法及石膏法)占总装置数的73.4%,喷雾干燥法占总装置数的17.7%,其它方法占9.3%。
美国的FGD系统中,抛弃法占大多数。
在湿法中,石灰/石灰石法占90%以上。
可见,湿式石灰/石灰石法在当今FGD系统中占主导地位。
尽管各国在FGD方面都取得了很大的进步,但运行费用相当惊人,而且各种方法均有其局限性,因此,至今许多研究者仍在不断研究开发更先进、更经济的FGD技术。
目前工业化的主要技术有:1,湿式石灰/石灰石—石膏法该法用石灰或石灰石的浆液吸收烟气中的SO2,生成半水亚硫酸钙或再氧化成石膏。
其技术成熟程度高,脱硫效率稳定,达90%以上,是目前国内外的主要方法。
2,喷雾干燥法该法是采用石灰乳作为吸收剂喷入脱硫塔内,经脱硫及干燥后为粉状脱硫渣排出,属半干法脱硫,脱硫效率85%左右,投资比湿式石灰石-石膏法低,但脱硫效率不高。
目前主要应用在美国。
3,炉内喷钙—增湿活化脱硫法该法是一种将粉状钙质脱硫剂(石灰石)直接喷入燃烧锅炉炉膛的脱硫技术,适用于中、低硫煤锅炉,脱硫效率约85%。
4,吸收再生法主要有氨法、氧化镁法、双碱法。
脱硫效率可达95%左右,技术较成熟。
①氨法:氨法采用氨水作为SO2的吸收剂,SO2与NH3反应可产生亚硫酸氨、亚硫酸氨与鼓入空气中的氧气反应而生成硫酸氨。
氨法主要特点是脱硫效率高,副产物可作为农业肥料,但该肥料属酸性肥料,长期使用易造成土壤板结,在农业上的应用受到限制。
该法脱硫剂氨水的来源,运输,储存和使用要求均较为繁杂,操作管理要求高。
否则,会造成氨的挥发,污染大气。
该方法适合有废氨水的烟气脱硫。
②镁法:氢氧化镁或氧化镁与SO2反应得到亚硫酸镁与硫酸镁,它们通过煅烧可重新分解出氧化镁,使吸收剂得到再生,同时可回收较纯净的SO2气体,脱硫剂可循环使用。
由于氧化镁活性比石灰水高,脱硫效率也较石灰法稍高。
它的缺点是氧化镁回收过程需结晶、分离、蒸发、煅烧等工序,工艺较复杂;但若直接采用抛弃法,大量可溶性镁盐会进入水体导致二次污染,总体运行费用也较高。
另外该系统的管路易结垢,特别是当水质硬度较高时管路结晶堵塞更加严重。
一般适用于氧化镁产地及沿海地区。
③双碱法:钠钙双碱法(Na2CO3/Ca(OH)2)结合石灰法和钠碱法优点,利用钠盐易溶于水反应活性高的特点,在吸收塔内部采用钠碱吸收SO2,吸收后的脱硫液在再生槽内利用较廉价的石灰进行再生,从而使得钠离子循环吸收利用。
该工艺综合石灰法与钠碱法的特点,解决了石灰法的塔内易结垢的问题,又具备钠碱法吸收效率高的优点。
与氧化镁法相比,钙盐不具污染性,因此不产生废渣二次污染。
适合于小烟气量脱硫。
我国废气脱硫技术早在1950年就在硫酸工业和有色冶金工业中进行,对电厂锅炉燃烧产生烟气二氧化硫的脱除技术在二十世纪70年代开始起步并在国家“六五”至“九五”期间有了长足的进步。
先后有60多个高校、科研和生产单位对多种脱硫工艺进行了试验研究。
尽管我国对FGD系统的研究开始得很早,涉及的面也很宽,但大部分技术只停留在小试或中试阶段,远未达到大面积工业化应用的程度。
而投入巨资引进的示范工程虽然设备先进、运行稳定,但投资巨大,运行费用也相当高。
因此加快对国外先进技术的消化吸收,使其国产化、低成本化,是当前重要而艰巨的任务。
3.2湿式石灰—石膏法石灰—石膏法用石灰或石灰石的浆液吸收烟气中的SO2,生成半水亚硫酸钙再氧化成石膏,是目前国内外的主要方法。
具有以下优势:(1)适用于燃料范围大,脱硫效率高。
该工艺脱硫率高达95%以上,脱硫后的烟气不但SO2浓度很低,而且烟气含尘量也大大减少。
大机组采用湿法脱硫工艺,SO2去除量大,有利于地区和电厂实行总量控制。
(2)技术成熟,运行可靠性好。
在世界脱硫市场上占有的份额达85%以上。
适用范围广,不受燃煤含硫量与机组容量的限制,单塔处理烟气量大,可达每小时3106m3,所以对高硫煤、大机组的烟气脱硫更有特殊的意义。
(3)对煤种变化的适应性强。
该工艺适用于任何含硫量的煤种的烟气脱硫,无论是含硫量大于3%的高硫煤,还是含硫量低于1%的低硫煤。
(4)紧凑的吸收塔设计(吸收塔集吸收、氧化、结晶于一体),节约投资和空间。
(5)吸收剂消耗接近化学理论计算值并且吸收剂的资源丰富,价格便宜作为该工艺吸收剂的石灰石在我国分布很广,资源丰富,品位也很好,碳酸钙含量多在90%以上,优者可达95%以上。
在脱硫工艺的各种吸收剂中,石灰石价格最便宜,破碎磨细较简单,钙利用率较高。
(6)脱硫副产物石膏可作为水泥缓凝剂或加工成建材产品。
不仅可以增加电厂效益、降低运行费用,而且可以减少脱硫副产物处置费用,延长灰场使用年限。
(7)技术进步快。
近年来国外对工艺进行了深入的研究与不断改进,如吸收装置由原来的冷却、吸收、氧化三塔合为一塔,塔内流速大幅度提高,喷嘴性能进一步改善等。
通过技术进步和创新,可望使该工艺占地面积较大、造价较高的问题逐步得到解决。
石灰石(石灰)—石膏湿法脱硫是目前世界上技术最为成熟、应用最多的脱硫工艺,特别在美国、德国和日本,应用该工艺的机组容量约占电站脱硫装机总容量的80%以上,应用的单机容量已达1000MW及以上。
因此,本工程采用湿式石灰—石膏法。
3.3工艺流程湿式石灰—石膏法工艺流程如下所示:石灰-石膏法烟气脱硫工艺的反应机理为:在脱硫吸收塔内烟气中SO2首先被浆液中的水吸收与浆液中的CaO反应生成CaSO3,CaSO3被鼓入氧化空气中的O2氧化最终生成石膏晶体CaSO4·2H2O。
其主要化学反应式为:吸收过程:SO2(g)→SO2 (l)+H2O→H++HSO3-→H++SO32-溶解过程:CaO+H2O=Ca(OH)2Ca (OH)2→Ca2++2OH-氧化:HSO3-+1/2O2→HSO42-→H++SO42-结晶:Ca2++SO32-+1/2H2O→CaSO3·1/2H2O (s)Ca2++SO42-+2H2O→CaSO4·2H2O (s)烟气从烟道引出后经增压风机增压,进入GGH烟气冷却器冷却后从下部进入吸收塔。
与上面喷淋下来的的石灰浆液逆向接触,吸收烟气中的SO2。
洁净烟气从吸收塔顶部经过两级除雾后排出脱硫塔,再经GGH烟气加热器加热后经烟道排出。
在吸收塔内浆液吸收SO2后生成亚硫酸钙并沉降下来,在强制鼓风氧化作用下亚硫酸钙生成硫酸钙晶体,然后通过石膏排出泵输送到水力旋流器,经旋流分离(浓缩)、真空脱水后生成石膏回收利用。
旋流器上层清夜输送到滤液池,滤液大部分用泵送回脱硫系统循环使用,当浆液经过多次循环利用后富集重金属元素和Cl-等时,再用泵将浆液输送到污水处理系统进行处理。
3.4 石灰石—石膏湿法脱硫工艺系统描述湿式石灰烟气脱硫工艺流程,主要由石灰浆液制备系统、SO2吸收,氧化系统、烟气系统和石膏脱水系统组成。