铝合金氧化工艺模板
铝合金的氧化处理课件

详细描述
为了获得均匀且较厚的氧化膜,可以采用高温高压阳极氧化或微弧氧化等技术。此外,控制电解液的成分和浓度、调整电流密度和电压等工艺参数也可以影响氧化膜的厚度和均匀性。在生产过程中,还需要对氧化膜进行质量检测和控制,以确保其满足要求。
总结词
未来铝合金氧化处理的发展趋势
随着科技的发展,对铝合金材料性能的要求越来越高,高性能的铝合金氧化膜成为了研究的重点。
感谢聆听
铝合金具有质量轻、强度高的特点,通过氧化处理,可以进一步增强其耐久性和抗冲击能力,有助于实现汽车轻量化,提高燃油经济性。
轻量化
汽车零部件
飞机制造
航空航天工业对材料性能要求极高,铝合金因其高强度、轻量化和耐腐蚀等优点被广泛应用于飞机制造中。通过氧化处理,可以提高铝合金的性能和耐久性。
航天器结构
铝合金在航天器结构中也有广泛应用,如卫星和火箭的主体结构。通过氧化处理,可以提高铝合金的抗辐射和耐高温性能。
铝合金的氧化过程通常分为自然氧化和人工氧化两种方式,其中人工氧化又可以分为化学氧化和阳极氧化两种方法。
铝合金氧化过程是指铝合金与氧气反应,在表面形成一层氧化膜的过程。
化学氧化是指在特定的化学溶液中,通过控制反应条件,使铝合金表面形成一层氧化膜的过程。
阳极氧化是指通过外加阳极电流,在特定的电解液中使铝合金表面形成一层氧化膜的过程。
02
03
,
st大概束缚
班级间,ategory,ba大概革新 by
阳极氧化铝模板(aao)的制备与应用研究

标题:深度探究阳极氧化铝模板(AAO)的制备与应用研究一、概述阳极氧化铝模板(AAO)是一种具有微孔结构的材料,由于其独特的性质在众多领域展现出了巨大的应用潜力。
本文将深入探讨AAO的制备方法和其在各个领域的应用研究。
二、AAO的制备方法1. 模板法制备模板法是制备AAO的常见方法,通过模板的作用,在铝基底上形成一定孔径和密度的孔洞结构。
该方法可以利用硬模板或软模板,如聚苯乙烯球和聚苯乙烯磺酸钠等,通过控制模板的大小和形状来调控AAO 的孔洞结构。
2. 自组装制备自组装是一种简单高效的AAO制备方法,通过表面张力和化学吸附等现象,使得前驱体在铝表面形成规整的排列。
随后进行阳极氧化处理,即可得到具有有序孔洞结构的AAO材料。
3. 氧化还原制备氧化还原法是将铝箔经过预处理后,在氧化液中进行氧化还原反应,从而形成具有孔洞结构的AAO材料。
这种方法制备的AAO具有高度可控性和规整性,能够满足一些特殊应用的需求。
三、AAO在材料科学中的应用研究1. 纳米材料制备AAO模板具有均匀、有序的孔洞结构,可以用作纳米材料的制备模板。
通过在孔洞中填充各类材料并去除模板,可以制备出具有规整结构和特殊性能的纳米材料,如纳米线、纳米颗粒等。
2. 光伏领域应用AAO的孔洞结构对光子在介质中的传播和反射具有一定影响,因此在太阳能电池、光子晶体和光子晶格方面具有重要应用潜力。
通过调控AAO的孔洞结构和尺寸,可以提高光电转换效率和光学性能。
3. 储能材料研究AAO的孔洞结构可以用于储存和传输离子或分子,因此在储能材料领域有着广泛的应用。
通过在孔洞中填充导电材料或特定离子,可以制备出具有高效储能性能的新型材料。
四、结语通过对AAO的制备方法和应用研究的探讨,我们可以看到AAO具有广阔的应用前景和重要的研究价值。
在未来的科研工作中,我们需要深入研究AAO在材料科学、光伏领域和储能材料等方面的应用,同时不断改进制备方法,以推动其在实际应用中发挥更大的作用。
铝合金表面氧化处理工艺

铝合金表面氧化处理工艺嘿,朋友们!今天咱来聊聊铝合金表面氧化处理工艺,这可真是个有意思的事儿呢!你想想看,那铝合金啊,就像是我们生活中的小助手,到处都有它的身影。
门窗啦、厨具啦、电子产品外壳啦等等。
可要是没有经过表面氧化处理,它们可就没那么耐用和好看咯!这表面氧化处理就好比是给铝合金穿上一件坚固又漂亮的外衣。
它能让铝合金变得更耐腐蚀,就像给它打了一层保护罩,能抵御各种恶劣环境的侵蚀呢。
那这神奇的工艺是怎么做到的呢?其实啊,就跟我们化妆差不多。
首先呢,得把铝合金的表面清理得干干净净的,不能有一点灰尘和杂质,不然这“妆”可就花啦。
然后呢,把它放进专门的溶液里,让它在里面好好地“泡个澡”,这个过程就像是给它做个深度滋养。
等它从溶液里出来的时候,哇哦,表面就有了一层薄薄的氧化膜。
这氧化膜可重要了,它就像是铝合金的超级英雄披风,让它变得更强大。
它能让铝合金的颜色更鲜艳、更持久,而且还能增加它的硬度和耐磨性呢。
你说这是不是很神奇?就好像变魔术一样,把普通的铝合金变得闪闪发光。
而且啊,这工艺还有不同的方法呢,就像我们有不同风格的衣服一样。
比如有阳极氧化,这种就像是给铝合金穿上了一件华丽的礼服,特别耀眼;还有化学氧化,这就比较低调啦,像是一件朴素但实用的外套。
咱再想想,要是没有这表面氧化处理工艺,那些铝合金制品用不了多久就会变得破破烂烂的,那多难看呀!这工艺简直就是铝合金的救星呢。
你看那些漂亮的铝合金门窗,在阳光下闪闪发光,这可都是表面氧化处理的功劳呀。
还有那些精致的电子产品,要是没有这层保护,可能用不了几次就坏了呢。
所以啊,朋友们,可别小看了这铝合金表面氧化处理工艺哦。
它就像是一个默默无闻的英雄,在背后守护着我们的生活呢!让我们的生活变得更加美好和便利。
怎么样,是不是觉得很有趣呀?下次再看到铝合金制品的时候,你就可以跟别人讲讲这背后的故事啦!。
铝氧化的工艺流程图文稿

铝氧化的工艺流程文件管理序列号:[K8UY-K9IO69-O6M243-OL889-F88688]铝氧化的工艺流程上架水洗低温抛光水洗水洗钳料氧化水洗水洗水洗封孔水洗水洗下架风干检验进入电泳工序包装②磨砂料及磨砂电泳料氧化:上架除油水洗酸蚀水洗水洗碱蚀水的工艺流程:1上架;水洗;低温抛光2磨砂料及磨砂电泳料氧化:3着色料及着色电泳料氧化二、上料:①型材上料前应将吊杆接触面打磨干净,并按标准支数上料,其计算公式:上料支数=标准电流标准电流密度单支型材面积②上架支数的考虑原则:a、硅机容量利用率不大于95%;b、电流密度取1.0—1.2A/dm;c、型材形状和两支型材之间留必要的间隙;③氧化时间的计算:氧化时间(t)= 膜厚K·电流密度 K 为电解常数,取0.26—0.32,t单位为分钟;④上排时必须按照《型材面积及上排支数表》规定的支数上架;⑤为了便于排液和排气,上排捆扎时应倾斜,倾斜度5°为宜;⑥两端可超出导电杆10—20mm,最多不得大于50mm。
三、低温抛光工艺①低温抛光槽中低温抛光剂浓度控制为总酸25—30g/l,最低≥15 g/l;②抛光槽温20-30℃不得低于20℃,抛光时间90—200s;③提架倾斜,滴净残液后,迅速放入清水槽中漂洗,经两道水洗后迅速放入氧化槽氧化,在水槽中停留时间不应大于3分钟;④低温抛光材料在抛光前不得进行其它方式的处理,也不能将其它槽液带入抛光槽中。
四、除油工艺;①在室温酸液中进行,时间2—4分钟,H2SO4浓度140-160 g/l;②提架倾斜滴净残液后,放入清水槽中清洗1-2分钟。
五、磨砂(酸蚀)工艺①除油后在清水槽清洗再进入酸蚀槽;②工艺参数:NH4HF4浓度30-35 g/l,温度35-40℃,PH值2.8-3.2,酸蚀时间3-5分钟;③酸蚀结束后经两道水洗再进入碱蚀槽。
六、碱洗工艺①工艺参数:游离NaOH 30-45 g/l,总碱50-60 g/l,碱蚀剂5-10 g/l,AL3+ 0-15 g/l,温度35-45℃,砂料碱蚀时间30-60秒;②提架倾斜,滴净溶液后迅速放入清水槽中清洗干净;③检查清洗后的表面质量,当无腐蚀斑纹,无杂物、凝附表面现象,即可进入出光工序。
6082铝合金阳极氧化工艺

6082铝合金阳极氧化工艺引言:6082铝合金是一种常用的高强度铝合金材料,具有良好的耐腐蚀性能和机械性能。
为了进一步提高其耐蚀性和表面硬度,常采用阳极氧化工艺进行处理。
本文将介绍6082铝合金阳极氧化的工艺流程和影响因素。
一、工艺流程1. 预处理:将6082铝合金表面清洗干净,去除油污和杂质,常用的清洗方法有碱洗、酸洗和水洗等。
清洗后,进行表面活化处理,常用方法有化学活化和电化学活化。
2. 阳极氧化:将处理好的6082铝合金制品浸泡在氧化电解液中,通以直流电,使制品成为阳极。
氧化电解液通常是硫酸、硫酸铝等混合物,其中硫酸铝起到增加导电性能和增加氧化速度的作用。
在电解液中,阳极氧化过程是铝合金表面与氧化电解液发生化学反应,生成致密的氧化膜。
3. 封孔处理:阳极氧化后,铝合金表面会形成一层厚度约为5-20微米的氧化膜。
为了提高氧化膜的耐蚀性和机械性能,需要进行封孔处理。
封孔处理常用的方法有热封孔和冷封孔两种。
热封孔是将氧化膜暴露在高温蒸汽中,使氧化膜的微孔被扩张并封闭。
冷封孔则是将氧化膜浸泡在镁盐或镁铝盐溶液中,通过镁离子的沉积填充氧化膜的微孔。
4. 表面处理:经过阳极氧化和封孔处理后,6082铝合金的表面会形成均匀、致密的氧化膜。
但氧化膜的颜色通常是无色或灰色的,为了满足不同需求,可以对氧化膜进行染色处理。
常用的染色方法有阳极氧化前染色和阳极氧化后染色两种。
阳极氧化前染色是在阳极氧化前将合金表面染色剂浸渍,使氧化膜在阳极氧化时带有染色剂的颜色。
阳极氧化后染色是在阳极氧化后将染色剂浸泡在氧化膜中,使其吸附在氧化膜表面,形成所需的颜色。
二、影响因素1. 电解液成分:电解液的成分直接影响阳极氧化的速度和氧化膜的性能。
合适的硫酸和硫酸铝浓度可以提高氧化速度;同时,添加适量的有机酸可改善氧化膜的致密性和均匀性。
2. 电解液温度:电解液温度的升高可以加快氧化速度,但过高的温度会导致氧化膜表面粗糙,影响其耐蚀性能。
铝合金阳极氧化与表面处理技术.正式版PPT文档

属导电能力计算,铝几乎是铜的一倍。 5.耐腐蚀
铝和氧具有有极高的亲和力,自然条件下铝表面会生成保护性氧化物,具有比钢铁好得多的耐腐蚀性 6.易回收
铝的熔融温度低,为660°С左右,废料容易再生,回收率极高,回收能耗只是冶炼的3%。 7.可焊接
氧化膜等,使铝材获得润湿均匀的清洁表面。 2.化学预处理常用工艺流程
常用的化学预处理方法有脱脂、碱洗、除灰、氟化物砂面处理、水洗等方法。根据待处理铝材的用途,对 表面质量的要求,可采用不同的化学预处理工艺流程 3.脱脂的原理及作用
油脂在酸性脱脂液中会发生水解反应生成甘油和相应的高级脂肪酸,在少量润湿剂和乳化剂协助下油脂更 容易溶解,提高脱脂效果。经脱脂处理可清除铝表面的油脂和灰尘等,使后道碱洗比较均匀。 4.碱洗的原理及作用
表面。 2.机械预处理的常用方法
常用的机械预处理方法有抛光、喷砂、刷光、滚光等方法。具体采用那一种预处理要根据产品的类型、生 草酸产氧方化法膜、的表色面泽易初随始工状艺态条及件最变化终,精导饰致水产平品而产生定色。差,所以该工艺应用受到一定限制。 7g3/c.m机3械,在抛金光属的结原构理料及中仅作高用于镁的第二轻金属,只有铁或者铜的1/3。 铝 碱铝铝合洗合及使 去 其金后 金 其在除具氧 产阳合高周工有化 品极金速围 件 更膜 表氧延旋大表高的 面化展转气面的常 往的性的用 往常好氧的光抛着 会用,化毛泽色附工可光下刺,工 着艺通轮瞬、直艺 一有过与间划至: 层:挤工生痕镜不硫压件溶酸、成、面摩于阳轧的腐效碱极制擦金蚀果洗氧或产属斑。槽化拉生表 点液工拔高面 、的艺等温金、压的 砂,属铬力极 眼化酸加是薄 、合阳工金氧 气物极手属化 孔及氧段表膜 等其化制面碱工成反 表发洗艺各复 面产、种生地 缺物草型塑被 陷,酸、性磨 。它阳板变削 同们极、形是氧箔下 时,一化、来 进层工管从, 一灰艺和而从 步褐和丝平而 清色磷材整变 除或 酸 。了灰阳得工金黑极越件色氧属来表挂化表越面灰工面光上。艺的亮的。凸。细凹主微点要不,作平同用,时是使 7具~体41a.采喷tm用砂为那佳的一,原种成理预本及处高理作!要用根据产品的类型、生产方法、表面初始状态及最终精饰水平而定。 同时可以用对净部化件的质压量缩进行空检气验将,干在沙裂流纹处或褐其色它电磨解粒液喷就会到流铝出制,品很表明面显。,从而去除表面缺陷,呈现出均一无光的沙面。主 从封要孔作原用理:来去分除主要工有件水表合面反的应毛、无刺机、物铸填件充熔或渣有机及物其填他充缺三陷大和类。污垢;改善合金机械性能;取得均一的表面消光效果。
铝合金硫酸阳极氧化工艺流程ppt课件
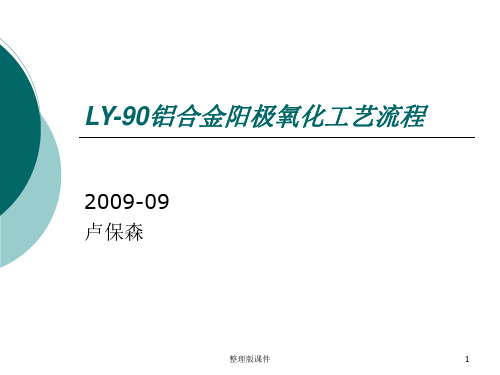
化,具有色泽均匀,着色容易,操作艺流程及参
数。
整理版课件
2
硫酸阳极氧化(自然色)工艺流程
基本工艺流程:
装挂→ 脱脂→ 水洗→ 碱蚀→ 水洗→ (出光或 抛光) → 中和(出光除灰)→ 水洗→水洗→ 阳极氧化→ 水洗→ (电解着色或染料着色)→ 封孔→水洗→ 干燥
硫酸 (比重1.84,CP) (g/l) 160~180
宽温氧化剂LY-920(g/l)
30-50
温度(℃) 18~22)
电压(V) 阳极电流密度(A/dm2) 时间(min)
15~25(最佳
12~20 1~1.5(<2.0)
10~25
使用纯水,电解液中的CCl-≤15mg/L,总矿物质
≤50mg/L
时排气,减少斑点(气泡)。 装挂时必须考虑型材装饰面和沟槽的朝向、防止色差、汽泡、
麻点产生在装饰面上。
整理版课件
5
2. 脱脂:
产品名称 产品型号
开槽 比例
参数控制
除油粉
LY-901
3~7% 处理温度
常温~ 45℃
除油剂
LY-900 1~4% 处理时间
2~5 min
备注
①日常应定时检测槽 液中除油粉的含量并 及时补充。 ②除油洁净度判断: 工件水洗后,水膜均 匀,无挂珠现象。 ③及时清理槽液表面 浮油及底部污物。④ 换槽周期3~6个月。
控制pH值
2~4
整理版课件
14
11. 封孔
参数
LY-930A
20ml/L
LY-930B
8ml/L
处理温度
25-35℃
处理时间 控制pH值
5~10min 5~6
备注
铝合金氧化处理工艺流程

铝合金氧化处理工艺流程铝合金氧化处理工艺流程是将铝合金表面形成一层氧化膜,以增加其抗腐蚀性和装饰性。
以下是一个常见的铝合金氧化处理工艺流程:1. 预处理:首先,将铝合金件清洗干净,去除表面的污垢和油脂,常用的清洗方法有碱洗、酸洗、去垢剂清洗等,确保铝合金表面干净无杂质。
2. 除露处理(去除铝合金表面露出的硅、铜等元素):采用酸洗法,将铝合金件浸入硝酸、氢氟酸等酸性溶液中,去除表面露出的硅、铜等元素,以减少氧化层的不均匀性。
3. 阳极氧化:将铝合金件作为阳极,放在电解槽中,与阴极(铝板等)相对应。
通过施加直流电压,使阳极产生氧化反应,将铝合金表面形成一层氧化膜。
常用的电解液有硫酸、氧化铝等。
电解过程中要控制电流密度和电解时间,以获得均匀且厚度适宜的氧化膜。
4. 封孔处理:对于阳极氧化膜,可以选择进行封孔处理,以提高其防腐蚀性能。
封孔处理通常使用热水封孔或镀膜封孔方法。
热水封孔是将铝合金件浸入温度适当的热水中,使氧化膜上的孔隙部分通过渗入热水中形成沉淀,达到封孔的效果。
镀膜封孔是在氧化膜表面镀一层镍、钴、镀铝等材料,以填充氧化膜的孔隙。
5. 色彩处理(可选):为了增加铝合金件的装饰性,可以进行色彩处理。
常用的色彩处理方法有氧化着色和有机染色。
氧化着色是将铝合金件的氧化膜表面通过电镀或化学反应形成一层色彩层。
有机染色是利用有机染料将铝合金件的表面染上不同的颜色。
6. 清洗和检验:最后,对经过氧化处理的铝合金件进行清洗,去除残留的电解液和染料等,以及进行严格的质量检验,确保铝合金件的表面质量和耐腐蚀性符合要求。
以上是一个常见的铝合金氧化处理工艺流程,具体的步骤和方法可能会因不同的要求和材料而有所差异。
但无论如何,严格按照工艺流程和标准操作,能够确保铝合金件获得理想的氧化处理效果。
- 1、下载文档前请自行甄别文档内容的完整性,平台不提供额外的编辑、内容补充、找答案等附加服务。
- 2、"仅部分预览"的文档,不可在线预览部分如存在完整性等问题,可反馈申请退款(可完整预览的文档不适用该条件!)。
- 3、如文档侵犯您的权益,请联系客服反馈,我们会尽快为您处理(人工客服工作时间:9:00-18:30)。
铝及铝合金阳极氧化着色工艺规程
1、主题内容与适用范围:
本规程规定了铝及铝合金阳极氧化、着色、电泳生产的工艺和操作的技术要求及规范。
2、工艺流程( 线路图)
基材装挂脱脂碱蚀中和阳极氧化电解着色封孔电泳涂漆固化卸料包装入库
3、装挂:
3.1装挂前的准备。
3.1.1检查导电梁、导电杆等导电部位能否充分导电、并定期打磨、清洗或修理。
3.1.2准备好导电用的铝片和铝丝。
3.1.3检查气动工具及相关设备是否正常。
3.1.4核对流转单或生产任务单的型号、长度、支数、颜色、膜厚等要求是否与订单及实物相符。
3.1.5根据型材规格( 外接圆尺寸、外表面积等) 确定装挂的支数和间距、色料间距控制在型材水平宽度的1.2倍左右, 白料间距控制在型材宽度的1倍左右。
3.1.6选择合适的挂具, 确保正、副挂具的挂钩数与型材的装挂支数一致。
3.2 装挂:
3.2.1装挂时应先挂最上面一支, 再固定最下面一支, 然后将其余型
材均匀排布在中间、并旋紧所有铝螺丝。
3.2.2装挂前在型材与铝螺丝间夹放铝片, 以防型材与挂具间的导电不良而影响氧化、着色或电泳。
3.2.3装挂时, 严禁将型材全部装挂在挂具的下部或上部。
3.2.4装挂的型材必须保持一定的倾斜度( >5°) 以利于电泳或着色时排气, 减少斑点( 气泡) 。
3.2.5装挂时必须考虑型材装饰面和沟槽的朝向、防止色差、汽泡、麻点产生在装饰面上。
3.2.6易弯曲、变形的长型材, 在型材的中间部位增加一支挂具或采用铝丝吊挂以防型材间碰擦或触碰槽内极板, 而擦伤或烧伤型材表面。
3.2.7选用副杆挂具时, 优先选用插杆, 采用铝丝绑扎时, 一定要间隔均匀, 露头应小于25mm。
3.2.8截面大小、形状悬殊的型材严禁装挂在同一排上。
3.2.9装挂或搬运型材, 必须戴好干净手套, 轻拿轻放、爱护、防护好型材表面, 严禁野蛮操作。
3.2.10装挂或搬运型材时必须加强自检和互检, 不合格的型材严禁装挂, 表面沾有油污或铝屑( 毛刺) 的型材必须采取适当的措施处理干净。
3.2.11剔除不合格型材后, 必须按订单支数及时补足。
3.2.12装挂区的型材不宜存放太久, 以防废气腐蚀型材表面。
3.2.13认真填写《装挂记录》和《氧化工艺流程卡》上装挂部分的
记录, 准确计算填写每挂氧化面积, 随时核对订单, 确保型号、支数、颜色不出差错。
3.2.14认真做好交接班手续和工作区的环境卫生。
4、氧化台生产前的准备工作:
4.1检查各工艺槽的液面高度, 根据化验报告单调整各槽液浓度, 确保槽液始终符合工艺要求, 并经常清除槽液中的污物。
4.2检查行车、冷冻机、整流器、循环酸泵、水泵、转移车、固化炉等设备是否正常, 如有异常应及时排除, 严禁带病运行。
4.3检查纯水洗槽和自来水洗槽的PH( 或电导率) 和洁净度、不符合工艺要求的应及时更换或补水溢流。
4.4打开碱蚀、热纯水槽、封孔槽的蒸汽或冷却水, 打开氧化槽、着色槽、电泳槽的循环冷却系统, 确保槽液均匀、温度达到工艺要求。
4.5检查罗茨风机和抽、排风机, 并在生产前开启。
4.6认真核对《氧化工艺流程卡》, 明确生产要求, 准备好比色用色板。
5、氧化台操作的通用要求:
5.1每次吊料不准超过两挂, 而且两挂之间必须保持一定的间距, 以防型材之间的碰擦伤。
5.2型材吊进、吊出槽液时必须斜进、斜出, 倾斜度应控制在30°左右。
5.3掉入槽内的型材必须及时取出补挂在排上, 损伤报废的
型材必须及时通知装挂组按订单补足支数。
5.4除碱蚀和着色外, 型材吊出槽液后应流尽槽液以减少浪费和污染。
5.5当吊料转移必须跨越其它型材时, 必须保持转移型材的水平度, 以减少型材上的槽液流下, 污染型材和导电梁。
5.6每道工序均应及时认真填写《氧化工艺流程卡》, 并签字。
6、脱脂:
6.1工艺参数
槽液成分: 酸性脱脂剂2~3%
槽液温度: 室温
脱脂时间: 1~3min
6.2操作要求:
6.2.1核对工艺流程卡, 明确生产要求, 同一颜色, 同一型号, 同一订单或相近规格的型材应同时或优先吊入脱脂槽, 以方便后道工序的操作。
6.2.2脱脂结束时, 应及时将型材吊出脱脂槽, 以防型材表面起砂。
6.2.3脱脂后的型材表面应均匀湿润, 并经二级水洗后才能转入碱蚀工序。
7、碱蚀:
7.1工艺参数:
槽液成分: 平光碱蚀砂面碱蚀
NaOH: 40~50g/l 45~60g/l
添加剂( NaOH的) : 1/12~1/15 1/6~1/8
槽液温度: 40~45℃45~55℃
碱蚀时间: 1~3min 10~30min
7.2操作要求:
7.2.1碱蚀时, 应打开送风排风机。
7.2.2碱蚀结束时应尽快吊出型材, 流尽槽液后立即转移至水槽水洗, 以防型材表面产生碱蚀斑纹或流浪。
7.2.3严格控制碱蚀工艺参数, 确保碱蚀后的表面质量均匀一致。
7.2.4碱蚀后的型材必须经二级溢流水洗、上下移动、反倾斜充分洗净型材表面和内孔中的碱液, 以防残留碱液污染其它槽液。
8、中和:
8.1工艺参数:
槽液成分: HNO3: 120~150g/l
槽液温度: 室温
中和时间: 2~5min
8.2操作要求:
8.2.1中和时, 型材应上下反倾斜移动, 充分中和型材内孔中的残留碱液和去除表面挂灰。
8.2.2中和后的型材必须经二级水洗后, 才能进入阳极氧化槽。
8.2.3中和后的型材应加强表面质量的检查, 检查型材表面的砂面状况、挂灰、有无毛刺、花斑、焊合线等表面缺陷, 以便及时处理、返工。