航空发动机叶片裂纹检测技术及应用分析
航空发动机维修中孔探技术的运用研究

航空发动机维修中孔探技术的运用研究航空发动机是飞机的心脏,对飞机的安全和性能至关重要。
因此,对于航空发动机的维修保养非常重要。
其中一个重要的维修方法就是孔探技术。
孔探技术是一种通过特殊的探伤设备在航空发动机表面钻孔后探测内部缺陷的方法。
孔探技术被广泛应用于航空发动机维修保养中,以检测并修补隐蔽的内部缺陷,确保发动机的安全和可靠性。
在航空发动机的维修保养过程中,孔探技术主要应用于以下几个方面:1. 检测裂纹和缺陷:航空发动机的高温、高压、高速工作环境对各种零部件的质量和耐久性提出了很高的要求。
发动机内部如叶片、转子等重要部件的损坏或缺陷可能会导致发动机性能严重下降甚至故障,危及飞行安全。
通过钻孔孔探技术可以检测到发动机内部的裂纹、夹杂和缺陷,及时进行修理和更换,降低故障率和延长使用寿命。
2. 沉积物探测:航空发动机在使用过程中,空气中的杂质、灰尘和涂层材料等会积聚在发动机叶片、轴承和飞行控制系统等重要部件表面。
这些沉积会导致气动效率下降,影响发动机的运行性能。
通过孔探技术检测发动机内部的沉积物,可以及时清理和保养,确保发动机的正常运转。
3. 薄弱部位探测:航空发动机结构复杂,各零部件之间的连接点和薄弱部位容易受到疲劳和损坏。
通过钻孔孔探技术检测这些薄弱部位是否存在裂纹和缺陷,可以及时进行修补和更换,提高发动机的安全性和可靠性。
在孔探技术的实际应用中,需要注意以下一些问题:1. 钻孔数量和位置:钻孔位置应该选择在被测件的最大应力区域,避免无用的钻孔、减少被测件的破坏。
2. 数据分析和解释:孔探技术得到的数据需要进行细致的分析和解释,评估被测件的状况,并制定恰当的维修措施。
总之,孔探技术是航空发动机维修保养中不可或缺的工具之一,能够保障飞机的飞行安全和性能。
随着科技的不断进步和发展,孔探技术也在不断更新和发展,为航空发动机的维修保养提供更加精确和高效的工具。
毕业设计论文:涡轮叶片断裂故障的分析与预防措施[管理资料]
![毕业设计论文:涡轮叶片断裂故障的分析与预防措施[管理资料]](https://img.taocdn.com/s3/m/b70f4ec7ee06eff9aff807bc.png)
Civil Aviation University of China 毕业设计(论文)专业:发动机动力工程学号:XXXXXXXX学生姓名:XXX所属学院:中国民航大学指导教师:XXX二〇一一年十月中国民航大学本科生毕业设计(论文)涡轮叶片断裂故障的分析与预防措施THE ANALYZING AND PREVENTIVE MEASURE OF TURBINE BLADE CRACKFAULT专业:发动机动力工程学生姓名:XXX学号:XXXXXXX学院:中国民航大学指导教师:XXXX2011年 10月创见性声明本人声明:所呈交的毕业论文是本人在指导教师的指导下进行的工作和取得的成果,论文中所引用的他人已经发表或撰写过的研究成果,均加以特别标注并在此表示致谢。
与我一同工作的同志对本论文所做的任何贡献也已在论文中作了明确的说明并表示谢意。
毕业论文作者签名:签字日期:年月日本科毕业设计(论文)版权使用授权书本毕业设计(论文)作者完全了解中国民航大学有关保留、使用毕业设计(论文)的规定。
特授权中国民航大学可以将毕业设计(论文)的全部或部分内容编入有关数据库进行检索,并采用影印、缩印或扫描等复制手段保存、汇编以供查阅和借阅。
同意学校向国家有关部门或机构送交毕业设计(论文)的复印件和磁盘。
(保密的毕业论文在解密后适用本授权说明)毕业论文作者签名:指导教师签名:签字日期:年月日签字日期:年月日涡轮叶片断裂故障的分析与预防措施XXX摘要:涡轮转子叶片是把高温燃气的能量转变为转子机械功的重要零件工作时,它不仅被经常变化着的高温燃气所包围并且还承受着高速旋转产生的巨大离心力气体和振动负荷等,此外还要经受高温燃气引起的腐蚀和侵蚀,因而涡轮转子叶片的工作条件是恶劣的,它是决定发动机寿命的主要零件之一,因此涡轮转子叶片的故障是不可忽视的。
涡轮叶片的断裂故障往往导致下面整个阶段的损失并且对涡轮机的可用性造成重大影响。
涡轮叶片断裂故障的研究分析对于涡轮机耐用性的有效管理是非常必要的。
无损检测技术的应用案例分析与讨论

无损检测技术的应用案例分析与讨论无损检测技术是一种在不破坏或损伤被测试物体的情况下,通过对其进行各种分析和测试手段的综合应用,以确定材料的性质、缺陷和损伤程度的技术手段。
这项技术广泛应用于各个领域,包括航空航天、铁路、核工业、工程结构等领域,因其能够提供可靠、快速、准确的检测结果而备受青睐。
本文将以几个典型的案例来分析无损检测技术的应用,并探讨其优势和局限性。
第一个案例是在航空航天领域的应用。
在航空航天工业中,无损检测技术被广泛应用于飞机的材料和结构检测中。
例如,检测飞机发动机叶片中的裂纹和疲劳损伤,使用超声波检测技术可以非常准确地发现这些隐蔽的缺陷,确保飞机发动机的安全运行。
此外,利用磁粉检测技术可以有效地检测飞机机身中的金属缺陷,如腐蚀、裂纹等,以及飞机螺杆和紧固件中的松动情况。
这些无损检测技术在航空航天领域的应用,不仅可以确保航空器的安全性和可靠性,还可以减少因可见性不足而导致的不必要损耗。
第二个案例是在核工业领域的应用。
在核工业中,无损检测技术被用于核设施和核材料的安全检测。
例如,利用红外热像仪可以对核反应堆的冷却系统进行监测,发现异常情况,如泄漏和堵塞等。
同时,通过利用钴60射线源进行伽马射线检测技术,可以对核燃料棒进行快速、准确的检测,以确定是否存在燃料损耗、腐蚀、烧蚀等情况。
这些无损检测技术的应用使得核工业更加安全可靠,提高了核能的利用效率。
第三个案例是在工程结构领域的应用。
无损检测技术在工程结构中起着至关重要的作用,可以确保建筑物和桥梁的结构安全。
例如,利用超声波检测技术,可以对钢结构中的焊缝进行质量评估,检测是否存在缺陷,如气孔、裂纹等。
同时,利用热红外成像技术,可以检测混凝土结构中的渗漏情况,发现潜在的水损伤和热效应。
这些无损检测技术的应用,可以保障工程结构的安全性,防止由于材料和结构缺陷造成的工程事故和损失。
虽然无损检测技术在各个领域的应用非常广泛且有效,但也存在一些局限性。
航空发动机涡轮叶片损伤分析与优化

航空发动机涡轮叶片损伤分析与优化航空发动机是飞机最基本的动力设备,而涡轮叶片则是发动机的关键部件之一。
它们负责将高温高压的气体转化为动力,为飞机提供推力。
但由于受到高温高压的磨损、疲劳等因素的影响,涡轮叶片容易出现损伤和磨损,降低了发动机的性能和寿命,甚至可能导致事故的发生。
因此,航空发动机涡轮叶片的损伤分析与优化是极为重要的。
一、涡轮叶片损伤形式涡轮叶片主要有以下几种损伤形式:1. 疲劳裂纹:叶片由于在高温高压环境中不断的膨胀和收缩,会导致疲劳裂纹的产生,长时间的使用容易形成大面积的疲劳损伤,严重影响发动机的性能和安全。
2. 磨损:叶轮进行高速旋转时,空气颗粒与叶片的碰撞和磨擦会导致叶片表面的磨损,造成叶片表面清平不良,影响涡轮叶片的气动性能。
磨损导致的叶片几何变形还会影响整个涡轮机的性能。
3. 烧蚀:热腐蚀主要是由于冷却不良引起的。
由于设计和加工因素影响,涡轮叶片冷却过程不良会导致结构内部高温区域产生严重的氧化和腐蚀现象,使叶片的热稳定性和寿命受到影响。
4. 叶片断裂:涡轮叶片由于在高速旋转过程中受到高温高压气流的冲击、振动和疲劳,易发生断裂,出现这种情况,需要及时更换叶片,否则可能导致严重的事故发生。
二、损伤分析针对涡轮叶片存在的各种损伤形式,需要对其进行详尽的分析和评估,以便找出问题的瓶颈并做出相应的建议,为涡轮叶片的使用和保养提供参考。
1. 损伤分析方法涡轮叶片的损伤分析方法主要有以下几种:①直接观察:利用肉眼和显微镜对涡轮叶片进行观察,得到表面和内部的损伤情况。
②无损检测:采用无损检测技术对涡轮叶片进行检测,如超声波、X射线、光学等方法,可检测出叶片内部的裂纹、缺陷等问题。
③仿真分析:利用计算机辅助工程软件对涡轮叶片进行流场仿真,可以模拟出各种工况下的应力分布和变形情况,得到叶片的结构强度和性能等参数。
2. 损伤评估标准对于涡轮叶片的损伤评估,一般需要参考以下标准:①疲劳裂纹的长度和分布情况。
航空发动机风扇静子叶片裂纹失效分析

航空发动机Aeroengine收稿日期:2019-07-21基金项目:航空动力基础研究项目资助作者简介:卜嘉利(1985),男,硕士,工程师,主要从事航空发动机故障零部件的失效分析工作;E-mail :。
引用格式:卜嘉利,高志坤,牛建坤,等.航空发动机风扇静子叶片裂纹失效分析[J].航空发动机,2021,47(6):91-95.BU Jiali ,GAO Zhikun ,NIU Ji⁃ankun ,et al.Crack failure analysis of a fan stator blade[J].Aeroengine ,2021,47(6):91-95.航空发动机风扇静子叶片裂纹失效分析卜嘉利,高志坤,牛建坤,曹勇(中国航发沈阳发动机研究所,沈阳110015)摘要:针对某型航空发动机风扇静子叶片前缘靠近上缘板部位在振动疲劳试验结束后发现的裂纹故障,运用荧光探伤检测、断口宏微观分析、叶片表面划痕来历分析、源区表面检查、材质分析及有限元应力模拟分析等技术手段,对该裂纹的性质及萌生原因进行细致分析。
分析结果表明:故障风扇静子叶片裂纹的性质为高周疲劳,裂纹断口疲劳起源于叶片叶盆侧前缘靠近上缘板基体表面划痕处,呈多源线性起始特征。
疲劳源区距前缘距离约为2.3mm ,疲劳源区表面未见明显冶金缺陷,疲劳裂纹的萌生与叶片表面划痕有关。
建议严格控制振动光饰机中磨粒棱边的圆滑度,不应存有锋利棱角,避免在振动光饰时磨粒划伤叶片表面,降低叶片表面完整性,在叶片划伤部位出现应力集中现象。
关键词:风扇静子叶片;振动疲劳试验;疲劳裂纹;振动光饰;有限元分析;失效分析;航空发动机中图分类号:V232.4文献标识码:Adoi :10.13477/ki.aeroengine.2021.06.016Crack Failure Analysis of a Fan Stator VaneBU Jia-li ,GAO Zhi-kun ,NIU Jian-kun ,CAO Yong(AECC Shenyang Engine Research Institute ,Shenyang 110015,China )Abstract :The crack initiation was found at the leading edge of the fan stator vane ,where was close to the upper edge plate ,after the vibration fatigue test finished.The crack property and emergence were identified by fluoroscopy ,fracture analysis ,surface inspection ,scratch analysis ,chemical composition analysis ,metallographic examination ,hardness inspection and finite element analysis.The results show that the property of the crack is high cycle fatigue fracture ,the fatigue of the crack fracture originates from the scratch on the front edge of the vane basin side close to the matrix surface of the upper edge plate ,the fatigue source region showed multi-source linear initialcharacteristics.The distance between the fatigue source area and the leading edge is about 2mm ,no obvious metallurgical defects arefound on the surface of the fatigue source area ,the initiation of the crack is related to the scratch of the vane surface.It is suggested that the smoothness of the abrasive grinding edges in vibration finishing machine should avoid scratching the vane surface by abrasive particles during vibration finishing ,reduce the integrity of the vane surface ,and stress concentration occurs at the scratched part of vane.Key words :fan stator vane ;vibration fatigue test ;fatigue crack ;vibration finishing ;finite element analysis ;failure analysis ;aero⁃engine第47卷第6期2021年12月Vol.47No.6Dec.20210引言随着中国对航空发动机动力要求的不断提升,压气机部件气动负荷和性能指标也不断提高。
无损检测技术在航空维修中的实际应用案例分享
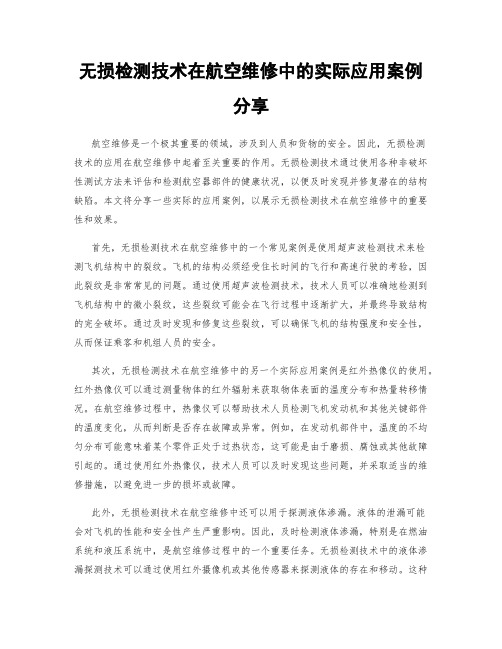
无损检测技术在航空维修中的实际应用案例分享航空维修是一个极其重要的领域,涉及到人员和货物的安全。
因此,无损检测技术的应用在航空维修中起着至关重要的作用。
无损检测技术通过使用各种非破坏性测试方法来评估和检测航空器部件的健康状况,以便及时发现并修复潜在的结构缺陷。
本文将分享一些实际的应用案例,以展示无损检测技术在航空维修中的重要性和效果。
首先,无损检测技术在航空维修中的一个常见案例是使用超声波检测技术来检测飞机结构中的裂纹。
飞机的结构必须经受住长时间的飞行和高速行驶的考验,因此裂纹是非常常见的问题。
通过使用超声波检测技术,技术人员可以准确地检测到飞机结构中的微小裂纹,这些裂纹可能会在飞行过程中逐渐扩大,并最终导致结构的完全破坏。
通过及时发现和修复这些裂纹,可以确保飞机的结构强度和安全性,从而保证乘客和机组人员的安全。
其次,无损检测技术在航空维修中的另一个实际应用案例是红外热像仪的使用。
红外热像仪可以通过测量物体的红外辐射来获取物体表面的温度分布和热量转移情况。
在航空维修过程中,热像仪可以帮助技术人员检测飞机发动机和其他关键部件的温度变化,从而判断是否存在故障或异常。
例如,在发动机部件中,温度的不均匀分布可能意味着某个零件正处于过热状态,这可能是由于磨损、腐蚀或其他故障引起的。
通过使用红外热像仪,技术人员可以及时发现这些问题,并采取适当的维修措施,以避免进一步的损坏或故障。
此外,无损检测技术在航空维修中还可以用于探测液体渗漏。
液体的泄漏可能会对飞机的性能和安全性产生严重影响。
因此,及时检测液体渗漏,特别是在燃油系统和液压系统中,是航空维修过程中的一个重要任务。
无损检测技术中的液体渗漏探测技术可以通过使用红外摄像机或其他传感器来探测液体的存在和移动。
这种技术能够将液体渗漏的位置和严重程度清楚地显示出来,从而帮助技术人员快速定位和修复问题,以确保飞机的正常运行和安全性。
最后,无损检测技术在航空维修中的一个关键应用案例是使用X射线或γ射线检测技术来评估金属结构的完整性和质量。
航空发动机叶片检测验收技术

叶片材料性能检测
硬度检测
通过硬度计测量叶片材料的硬度,评估材料的机械性能和耐 磨性。
拉伸检测
通过拉伸试验机测量叶片材料的拉伸强度、延伸率等力学性 能参数,评估材料的力学性能和可靠性。
03
验收标准与流程
叶片外观验收标准
叶片表面应光滑、无 划痕、无裂纹、无气 孔等缺陷。
叶片的涂层应均匀, 无明显色差或剥落现 象。
叶片维修过程中的检测应用
叶片损伤评估
通过目视检查、敲击检测和振动 分析等方法,对叶片的损伤程度 进行评估,确定是否需要维修或
更换。
叶片修复质量检测
对经过修复的叶片,采用与生产过 程中类似的检测方法,对修复质量 进行检测,确保叶片能够恢复到原 始性能。
叶片性能测试
在维修后,对叶片进行性能测试, 包括耐久性、稳定性和冷却性能等 ,确保叶片满足使用要求。
叶片检测的重要性
确保叶片的质量和可靠性,防止因叶 片故障导致的航空事故。
通过检测验收,可及时发现并处理叶 片生产中的质量问题,提高生产效率 和产品质量。
02
叶片检测技术
无损检测技术
超声检测
利用超声波在叶片材料中的传播特性 ,检测叶片内部和表面的缺陷,具有 非破坏性、高精度和灵敏度高的特点 。
磁粉检测
3
叶片材料的机械性能,如抗拉强度、冲击韧性等 应满足使用要求。
叶片功能性验收
叶片在发动机上的安装应牢固,无松 动现象。
叶片的冷却性能、气动性能等应符合 设计要求。
叶片的动平衡性能应良好,无明显振 动或异常声音。
04
叶片检测设备与工具
无损检测设备
超声波检测仪
利用超声波在物体中的传播和反射,检测叶片内 部和表面的缺陷。
基于模态分析的航空发动机压气机工作叶片结构裂纹检测

1 模态 分析 理论基础
物 体结构振动 问题由激励 、 动结构 和响应三部分组成“ 振 如图1 示 。 所
将 问 题 简 单 处 理 , 设 这 个 振 动 系统 是 无 阻尼 的 自 由振 动 系 统 , 假 那
取 得 了相 当 的 成 果 。
根 据 不 同 的 研 究 目的 可 将 一 般 振 动 问 题 分 为 以 下 基 本 类 型 : 已知 激 励和 振 动 结 构 , 求结 构 响 应 ; 已知 激 励 和 响 应 , 求结 构 参 数 ; 已知 结 构 和 响 应 , 激 励 。 中 , 求 其 已知 激 励 和 响应 , 结 构 参 数 , 求 就 是 结 构 辨识 问题 。 用模 态 固有 频 率 和模 态 矢 量 ( 型) 采 振 为特 征 参 数 的 数学 模 型 可 以完 整 描 述 振 动 系 统 , 以模 态 参 数 模 型 为基 础 , 模 以 态 参 数为 目标 的 系 统 识 别 方 法 , 态 参 数 能 从 总 体 上 反应 系 统 的 模 动 态 固 有特 性 , 重 要 的是 需 要 的 参 数 还 很 少 , 最 因此 模 态 参 数辨 识 能 够 进 行 , 模 态 参数 辨识 正 是 模 态 分 析 的 主 要 任 务 。 而 模 态分 析 方 法就 是 以 各 阶 主 振 型所 对 应 的模 态 坐 标 来 代 替 物 理 坐 标 , 微 分 方程 解 藕 , 成 彼 此 独 立 的 微 分 方程 。 使 变 系 统 结 构 的 模 态 分 析 案 例 【: 何 结 构 系 统 的 运 动 , 可 表 示 2任 】 均 为 内 力 、 力 和 惯 性 力的 平 衡 方 程 组 : 外
- 1、下载文档前请自行甄别文档内容的完整性,平台不提供额外的编辑、内容补充、找答案等附加服务。
- 2、"仅部分预览"的文档,不可在线预览部分如存在完整性等问题,可反馈申请退款(可完整预览的文档不适用该条件!)。
- 3、如文档侵犯您的权益,请联系客服反馈,我们会尽快为您处理(人工客服工作时间:9:00-18:30)。
航空发动机叶片裂纹检测技术及应用分析
航空发动机作为飞机动力的核心,是体现飞机性能的标准之一。
大多采用复杂型面叶片,在运行过程中因为会受到应力、离心力已于弯矩应力的影响,所以容易生成疲劳裂纹、层间分离等损伤。
这种损伤会降低航空发动机的性能,给装备带来安全隐患,甚至会引发灾难。
因此发展、使用高效的检测技术是解决这类问题的关键。
大部分应用于航空发动机叶片检测的方法主要有孔探法以及常规的检测方法如磁粉、射线、涡流电磁法,其中孔探法是发动机外场检测应用最多的一种技术,这种技术检测时间长,对人力的要求很高,并且操作过程较为复杂且必须十分谨慎。
常规的检测方法对复杂曲面结构缺陷的检测存在这一定的局限性。
近年来已出现一些高效的无损检测方法如声波/超声波检测、电磁超声非线性检测、相控阵检测等已经逐步应用于发动机叶片的探伤。
红外热成像技术亦是较为先进的无损检测技术之一,它主要是通过对被测结构件表面的温度变化进行捕捉,利用红外热成像仪采集表面因温度变化而产生的红外信号检测的。
红外热成像技术是用超声波对工件表面积局部进行激励进而进行加热,通过热成像仪捕捉裂纹区域的局部红外图像。
由于在固体器件中超声波传播速度快,所以从发出激励信号到采集到反馈信号是极短时间的过程,又因为深度、裂纹大小不同,红外信号传播到试件表面并得到反馈是随着时间、裂纹规模变化的,最后经过图像处理可以对试件的裂纹进行识别与定位。
1 检测原理及方法概述
1.1 检测原理概述
超声红外热成像检测技术的原理是先将低频高能的超声波注入被测零件,被测零件会产生小幅的机械振动,如果存在裂纹,那么由于裂纹两侧因震动频率不同(即出现相位差)而出现部分热效应(即
摩擦生热),导致局部的温度升高表面产生的热辐射也不同。
之后利用热成像仪对被测件表面温度进行捕捉生成零件表面的温度分布图,最后通过对温度分布图中的异常信号进行分析从而得到裂纹的位置及尺寸。
相比于其他成像技术,超声红外热成像技术可以只对表面或者裂纹区域进行加热,对正常的结构区域不加热,这种方法可以增加裂纹检测的可靠性,更有利于分析与判定,其检测原理如图1所示。
红外热成像检测的原理采集就是因不同材料表面热传导不同而出现温度差异的图像并对其进行甄别,因此我们可以通过热传导方程对其做出解释,热传导方程如下:
由此可知,试件受到激励之后会表面会发生温度变化,在时间相同的情况下,试件表面的温度T与待测件厚度(或者是裂纹的深度)成反比,即厚度(深度)越大,表面的温度越低。
为了达到可以完全显现裂纹的目的,激励的时间应该越长,因此为了使裂纹处温差会达到最大便于观察,应该给予一定时间的激励。
从原理上分析可以通过激励被测试件并采集试件表面温度的变化来识别裂纹及缺陷。
1.2 检测仪器介绍
本系统主要由数据采集处理、激励发生器组成。
目前完成的检测系统包括计算机、红外热成像仪、超声波发生器组成。
其中计算机主要用于采集红外热成像图并作为后期对结果处理的装置,超声波发生器主要包括超声波激励电源、激励触头等。
本实验采用红外热成像仪为德国InfraTecVarioCHD head 高清便携式红外热成像仪,此设备可以高效率、精确的测量并分析被测试件表面的温度变化。
由于仪器设备不同,因此最后得到的检测结果也会随着红外摄像仪的精度有所变化。
数据采集与处理使用的是计算机与红外软件IRBIS3plus,可以在其控制界面改变参数改变采集的模式。
2 实验检测及结果
由于不具备发动机叶片作为检测对象,因此选用其他替代试件作为待测件,最终通过分析结果判断超声红外热成像技术是否适用于发动机叶片裂纹的检测。
根据热传导定律可知,当材料表面温度分布不均匀时,材料表面热辐射不均匀,因此最终采集到的热温度图可以清晰显示裂纹形状及位置。
本次实验采用3mm与4mm厚CFRP(碳纤维板)板作为待测材料,为了验证是否可行,需要对CFRP板进行人为(破坏)。
实验中,设置采集的频率为30Hz,采集帧数的热图为1000帧。
激励时长分别为3s和4s,最后采集热图像序列。
经过实验发现,裂纹热成像出现的过程为逐渐变小,即大部分缺陷最先出现且最容易出现,少部分逐渐出现并且缺陷逐渐完整化。
缺陷热成像图见图2和图3。
图2、图3中显示的是首次能够清晰观察到全部的裂纹缺陷之后的帧数图,出现的时间分别为:第124帧时3mm厚试件可以全部显示;第197帧时4mm厚试件可以全部显示。
从图2、图3中可以清晰发现裂纹、缺陷所在位置,并且在4mm厚裂纹热像图中,可以观察到裂纹缺陷因深度不同而出现的深色区域颜色不同的现象。
之后经过Blob提取统计二值图中的像素值并计算面积,可以得到缺陷区域的大小及其产生的热效应。
具体见表1。
从最后的检测结果可以看出,超声红外热成像检测应用于表面结构缺陷、裂纹探测是可行的,尽管具体的面积提取仍然存在一定的误差,但是对于定量检测叶片裂纹大小或者识别叶片是否有损伤依旧具有一定的参考价值。
3 结语
部分航空发动机由于具有多级叶片,在检测叶片是否受损时难度较高、精确性要求较高,因此传统的叶片检测对于航空发动机叶片裂纹与缺陷的检测存在一定的局限性。
本文通过应用超声红外热成像技术检测特殊材料表面热像图验证该方法是否具备检测航空发动机复杂叶片结构的能力并最終通过分析结果确定该方法可以应用于发动机叶片的检测。