CO2腐蚀
油气生产中CO2腐蚀与防腐技术

分压MPa
温度
110℃ 8.4639 8.6012 9.948 7.9002 9.948
0.5 0.75 1 1.25 1.5
在T< 70℃ 时,N80钢的腐蚀速率随温度的升高而增加 在T=70℃时达到极大值 当T> 70 时,N80 钢的腐蚀速率随温度的升高反而减小 在90℃ 附近又出现了腐蚀极小值,当温度再升高时,腐蚀速率也随着加快 当温度大于60℃ 时,随着CO2分压的增加,N80钢片的腐蚀速率出现了线性增大的 趋势
当pH 值小于4时,N80 钢在饱和CO2的3%NaCl水溶液中的腐蚀速率随 着pH 值增大而减小 当pH 值在4-9之间时,腐蚀速率为一常数值 在碱性条件下,腐蚀速率随着pH 值增大而减小
15
二氧化碳腐蚀影响因素
3、温度的影响
图6、温度对腐蚀的影响
T<60 ℃
60 ℃ <T< l00℃
T >150℃
不腐蚀 可能腐蚀 发生腐蚀
0.02MPa
0.2MPa
即当温度一定时,CO2气体的分压愈大,材料的腐蚀就愈快。
14
二氧化碳腐蚀影响因素
2、pH 值的影响
表2 不同pH 值下N80钢的腐蚀速率 pH 值 腐蚀速率mm/a pH 值 腐蚀速率mm/a 1 19.97 7 8.51 2 17.46 8 9.98 3 10.1 9 8.35 4 8.24 10 4.13 5 10.95 11 3.7
(4)
(5) (6)
析氢反应可按如下历程进行(1)(2)(3)(6)或(1)(2)(4)(5) 阴极反应:
pH<4
2H 2e H 2
H+的扩散是控制步骤
4<pH<6 H2CO3(吸附) + e- =H (吸附)+ HCO3- (吸附)
二氧化碳的腐蚀与防治
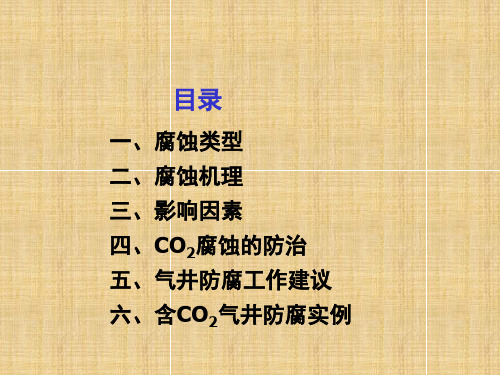
lgV=5.8-1710/T+0.67lgPc
三、影响因素
1、CO2分压的影响
CO2分压按下式计算:Pdc=Pt×Cc Pdc为CO2分压,MPa;Pt为气相总压力,MPa;Cc为气相中CO2体 积含量,%。(分压 < 0.2MPa,温度 < 60℃)。高于此范围则腐蚀速度 偏低,与腐蚀膜的生成有关。
研究表明,Cl-的存在大大降低了钝化膜形成的可能性,碳钢的腐蚀速度随Cl-含量 的增加而增加。
●钙、镁离子的影响
钙、镁离子的存在,导致溶液的导电性增强,介质易于结垢,因而会使腐蚀更加严 重。
三、影响因素
8、介质组成的影响
●H2S的影响
在CO2和H2S共存体系中H2S的作用表现为3种形式: (1)当H2S分压< 0.01psi(0.000067MPa)时,CO2是主要的腐蚀介质, 温度高于60℃时,腐蚀速率取决于FeCO3膜的保护性能,基本与H2S无关; (2)当H2S分压增加至PCO2/PH2S >200时,材料表面形成一层与系统温度 和pH值有关的较致密的FeCO3膜,导致腐蚀速率降低; (3)当PCO2/PH2S< 200时,系统中H2S为主导,其存在一般会使材料表面 优先生成一层FeS膜,此膜的形成会阻碍具有良好保护性的FeCO3膜的生成, 系统最终的腐蚀性取决于FeS和FeCO3膜的稳定性及其保护情况。
● 时间:4 ~144h
结论: ● 随着压力增加,腐蚀膜厚度的增长逐渐变缓 ● 压力>30MPa时,CO2腐蚀产物膜在8h内迅速 形成,且不再增厚, ● 与CO2分压1-2MPa下的腐蚀产物膜相比,高压 腐蚀膜的晶粒尺度小1-2个数量级,晶体组成为 FeCO3。
三、影响因素
CO2腐蚀

CO2腐蚀的机理及介绍1.1 CO2的腐蚀特点:从CO2的腐蚀情况来看,腐蚀的形状各异,但从各种情况分析,除了外观和介质油差别外,所有的气田用钢材的CO2腐蚀都非常集中以蚀坑、沟槽或大小不同的腐蚀区的型式出现,所以腐蚀穿透率很高,一般都达数毫米/年,一般来说,底面平整边缘锐利,是典型的CO2腐蚀特征。
2.3CO2的腐蚀机理:钢铁在除O2水中CO2腐蚀机理,其阳极反应主要是Fe的溶解,可简写为:Fe →Fe2+ + 2e (1)对阴极过程观点不一,较占主导的观点认为,在环境温度下,裸钢在除O2水中的腐蚀是受氢析出动力学控制,而阴极析氢机制除了一般的电化学还原H3O+离子放电反应析氢外,既在低pH除了非催化的析氢机制:H3O+ + e →H + H2O (2)反应外,还可以通过下述表面吸附催化作用H+还原反应析氢机制进行:CO2 + H2O = H2CO3 (3)H2CO3 + e =H+ + HCO3- (4)HCO3- + H3O+ = H2CO3 + H2O (5)上述析氢机制得到的一些试验的支持,并由此可以得出(1)不同金属材料具有不同的催化活性,而影响腐蚀速率。
(2)在一定pH范围(4~6),pH对阴极反应速度没有明显影响。
然而实际中,钢铁表面总是被某些物质覆盖着,如扎皮、氧化膜或在含介质中的腐蚀产物膜等,这些覆盖物使析氢可能不是在裸钢表面而是在膜或覆盖物上进行,因此影响到腐蚀特性,而这些问题不是上述简单机制所能解决的,所以CO2腐蚀机理仍在研究中。
2.4影响CO2腐蚀的因素:由于介质中的成分比较复杂,各种成分的含量也各不同,因此在各种条件下,影响CO2腐蚀特性的因素很多,归纳起来可以分为以下几个因素:(1)温度的影响(2)CO2分压(Pco2)影响(3)腐蚀产物膜的影响(4)流速的影响(5)pH、Fe2+及介质组成的影响等,这些因素可能导致钢的多种腐蚀破坏,比如可能产生高的腐蚀速率、严重的局部腐蚀穿孔,甚至可能发生应力腐蚀开裂等。
油气田CO2腐蚀及防控技术
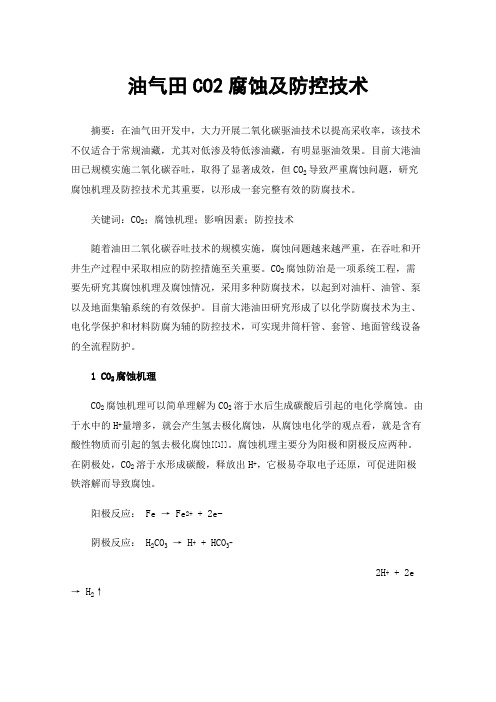
油气田CO2腐蚀及防控技术摘要:在油气田开发中,大力开展二氧化碳驱油技术以提高采收率,该技术不仅适合于常规油藏,尤其对低渗及特低渗油藏,有明显驱油效果。
目前大港油田已规模实施二氧化碳吞吐,取得了显著成效,但CO2导致严重腐蚀问题,研究腐蚀机理及防控技术尤其重要,以形成一套完整有效的防腐技术。
关键词:CO2;腐蚀机理;影响因素;防控技术随着油田二氧化碳吞吐技术的规模实施,腐蚀问题越来越严重,在吞吐和开井生产过程中采取相应的防控措施至关重要。
CO2腐蚀防治是一项系统工程,需要先研究其腐蚀机理及腐蚀情况,采用多种防腐技术,以起到对油杆、油管、泵以及地面集输系统的有效保护。
目前大港油田研究形成了以化学防腐技术为主、电化学保护和材料防腐为辅的防控技术,可实现井筒杆管、套管、地面管线设备的全流程防护。
1CO2腐蚀机理CO2腐蚀机理可以简单理解为CO2溶于水后生成碳酸后引起的电化学腐蚀。
由于水中的H+量增多,就会产生氢去极化腐蚀,从腐蚀电化学的观点看,就是含有酸性物质而引起的氢去极化腐蚀[[1]]。
腐蚀机理主要分为阳极和阴极反应两种。
在阴极处,CO2溶于水形成碳酸,释放出H+,它极易夺取电子还原,可促进阳极铁溶解而导致腐蚀。
阳极反应:Fe → Fe2+ + 2e-阴极反应: H2CO3→ H+ + HCO3-2H+ + 2e → H2↑碳酸比相同pH值下的可完全电离的酸腐蚀性更强,在腐蚀过程中,可形成全面腐蚀和局部腐蚀。
全面研究二氧化碳的腐蚀机理十分关键,2CO2腐蚀影响因素二氧化碳对金属材料的腐蚀受多种因素影响,有材质因素、压力、温度、流速、pH、介质中水和气体、有机酸、共存离子、细菌腐蚀等,本文主要介绍三种重要因素。
2.1 二氧化碳压力碳钢等金属的腐蚀速度随二氧化碳分压压力增大而加大,溶于水介质中CO2的含量增大,酸性增强,H+的还原反应就会加速,腐蚀性加大。
通过高温高压动态腐蚀评价来验证压力的影响,选取二氧化碳不同压力作为试验条件,对采出液在不同压力下评价腐蚀性。
CO2腐蚀油井水泥石的深度及其对性能的影响

CO2腐蚀油井水泥石的深度及其对性能的影响随着以石油工业为代表的工业领域的不断发展,大量的二氧化碳被排放在大气中,进一步加剧了全球气候变暖、气候灾害等问题。
同时,这些排放物也对环境产生了不可逆转的影响。
近年来,人们不断探索新的环保技术和工艺,以应对大气污染问题。
然而,除了寻求新的解决方案之外,我们也需要寻找其后果并加以控制和减少。
其中之一就是CO2对油井水泥石的腐蚀,本文旨在介绍 CO2 腐蚀油井水泥石深度及其对性能的影响的相关信息。
CO2腐蚀(carbonate corrosion)是指CO2在一定条件下与油井水泥石中的钙源反应,形成碳酸钙。
其反应具有一定的速度,在一定温度、压力、深度及CO2浓度等多重因素的共同作用下,CO2能够产生较为显著的腐蚀影响,导致水泥石的力学性能、渗透性能和耐化学性能等方面的下降。
CO2腐蚀的深度通常取决于CO2暴露的时间、CO2浓度、水泥石的质量和钙源,常常采用酸性溶液注入方法和高压瓶实验方法来模拟CO2腐蚀作用。
研究表明,CO2腐蚀深度与暴露时间和CO2浓度成正比关系,在同等环境条件下,腐蚀深度与钙源含量质量密切相关,钙源含量越高,腐蚀深度越浅。
这是因为钙源在水泥石中的存在能够与CO2形成碳酸类物质,形成一层保护膜,从而减缓或阻止CO2腐蚀水泥石的程度。
CO2腐蚀还会对水泥石的力学性能、渗透性能和耐化学性能产生重大影响。
在力学性能方面,由于CO2腐蚀加剧了水泥石内部的裂缝、孔洞和剥落等症状,导致抗压强度、抗拉强度、全弹性模量、裂缝扩展性等方面的性能均下降。
在渗透性能方面,CO2腐蚀会导致水泥石内部的孔径加大,孔洞增多,渗透性大幅度提高,从而使油井周边的水气体进入油管,降低油井的采收率。
在耐化学性能方面,CO2腐蚀也会使水泥石表面产生酸洞,并迅速降低水泥石的耐化学性能,导致水泥石更容易被化学物质侵蚀、溶解、剥落和破坏。
总的来说,CO2腐蚀是一种严重的水泥石腐蚀现象。
针对二氧化碳的腐蚀与防护

金属材料的抗二氧化碳腐蚀原理及如何防护经过挂片法及电腐蚀法的实验表明,当二氧化碳溶于水后对部分金属材料有极强的腐蚀性,二氧化碳腐蚀又可称为甜蚀,在相同的PH条件下,二氧化碳水溶液的腐蚀性比盐酸还要强。
以下是二氧化碳腐蚀影响的因素。
1、温度的影响。
研究表明,温度是影响二氧化碳腐蚀的重要因素,而且温度对腐蚀速率的影响较为复杂,在一定的温度范围内,碳钢在二氧化碳水溶液中的腐蚀速度随温度的升高而增大,当碳钢表面形成致密的腐蚀产物膜时,碳钢的溶解度随温度的升高而降低,前者加剧腐蚀,后者则有利于保护膜的形成以减缓腐蚀。
腐蚀产物碳酸亚铁溶解度具有负的温度系数,溶解度随温度的升高而降低,即反常溶解现象。
Ikeda等人的研究结果表明较低温度下,在碳钢表面生成少量松软且不致密的氧化亚铁膜,此时材料表面光滑,腐蚀为均匀腐蚀。
2、二氧化碳分压的影响许多学者认为二氧化碳分压是控制腐蚀的主要因素之一。
Cor和marsh对此作了估计,结果为:当二氧化碳分压低于0.021Mpa时,腐蚀可以护绿:当二氧化碳分压为0.021--0.21Mpa 时腐蚀有可能发生;当二氧化碳分压大于0.21Mpa时通常表示将发生腐蚀。
对于碳钢、低合金钢的裸钢。
最早的腐蚀速率可以用De warrd 和millians的经验公式(温度低于60°C,CO2分压小于0.2Mpa)计算:lgv c=0.67lgP(CO2)+C式中:Vc——腐蚀速率,mm/a;P(CO2)——CO2分压,MPaC——温度校正系数。
此公式最初是在大气环境中,将试件置于搅拌溶液里,以实验室得到的腐蚀数据为基础建立起来的,重点考察了CO2浓度对腐蚀速率的影响而没有考虑其他影响因素,所以有一定的局限性。
3、PH值的影响K.videm等人向正在进行试验的溶液中加入NaHCO3,使溶液的PH值升高,观察到腐蚀速率迅速发生变化。
在温度为70°C、铁离子浓度很低(1-2mg/L)时,加入12mmol/L碳酸氢钠,随着PH值由4.1升到6.2,腐蚀速率几乎降低了一倍。
浅谈热水锅炉和管网的氧腐蚀及二氧化碳腐蚀

浅谈热水锅炉和管网的氧腐蚀及二氧化碳腐蚀【摘要】锅炉和管网使用一段时间后会有不同程度的锈蚀,会对锅炉及管网产生很大的影响,本文分析了锈蚀的原因,提出大多数锅炉和管网普遍存在的问题,给出了预防锈蚀的建议。
【关键词】氧腐蚀、二氧化碳腐蚀、热水锅炉、PH前言    热水锅炉及其采暖系统经过一段时间的运行后,各部位都存在不同程度的腐蚀现象。
腐蚀分全面腐蚀和局部腐蚀两种,即二氧化碳腐蚀和氧腐蚀。
无论哪种腐蚀危害都很大:全面腐蚀会大大缩短锅炉和管网的使用寿命,造成原材物料和资金的浪费;而局部腐蚀的危害更加严重,不仅恶化锅炉及管网工作状况,而且可造成锅炉及管网局部破裂,甚至引起爆炸,是设备不能使用,或造成人员伤亡,后果不堪设想。
因此,杜绝腐蚀现象的发生,解决锅炉和管网的腐蚀是当前至关重要的问题之一。
从以下几个方面简单论述。
    一、热水锅炉和管网的氧腐蚀及二氧化碳腐蚀的原因:    热水锅炉和管网的常见腐蚀主要有两种,即氧腐蚀及二氧化碳腐蚀。
一般氧腐蚀发生后,腐蚀面成溃疡状,而二氧化碳腐蚀则为均匀腐蚀。
如果锅炉给水中含有溶解氧,则氧气与金属内壁在水溶液的作用下发生反应,生成氢氧化亚铁Fe[OH]2。
如果这时水溶液呈碱性(PH=9.5-10),则生成的氢氧化亚将稳定于锅炉和管网内壁,形成覆膜,阻止亚铁离子进一步被氧化进入水溶液,即阻止了腐蚀的进一步发生。
如果水溶液中仍然有氧存在,则氢氧化亚铁继续被氧化成氢氧化铁沉淀。
如果水溶液碱度被破坏,即水中有二氧化碳存在,PH值降低。
给水中虽没有溶解氧存在,但均匀的酸性腐蚀仍很强烈。
这是因为PH值降低会使氧化物保护膜变得松软,易被水冲走,锅炉金属面被暴漏出来,使腐蚀继续进行。
腐蚀产物被冲走,这样锅炉出水大量带铁,在管网中会生成很危险的渣垢,造成的危害是相互关联的。
   以下是腐蚀原理的化学方程式:   氧腐蚀的化学方程式:O2+2Fe+2H2O=2Fe(OH)2                      4Fe(OH)2+O2+2H2O=4Fe(OH)3   二氧化碳腐蚀的化学方程式:CO2+2H2O=H2CO3=H++HCO3-                             CO2+Fe(OH)2=Fe(HCO3)2    当水中同时又有氧存在时,则发生如下反应:                            4 Fe(HCO3)+2O2+2H2O=4Fe(OH)3+8CO2    这样反应中生成的CO2又能与氢氧化亚铁作用,生成重碳酸铁,是上述反应循环进行,直至消耗完毕。
CO2腐蚀环境下油套管防腐技术

CO2腐蚀环境下油套管防腐技术摘要:CO2气体溶于水中形成碳酸后引起电化学腐蚀,如不及时采取有效措施,将导致油套管的严重破坏甚至油井报废。
CO2对油、套管的腐蚀是油田开发的一个亟待解决的重要课题。
本文研究了CO2对油管的腐蚀机理、特征及影响因素,并提出了使用耐蚀合金管材、涂镀层管材、注入缓蚀剂、阴极保护和使用普通碳钢等五类防腐技术,可有效延缓气体对油套管的腐蚀、预防套管漏失的发生。
关键词:CO2腐蚀电化学腐蚀影响因素防腐蚀技术1、CO2的腐蚀机理CO2对金属的腐蚀主要表现为电化学腐蚀,即CO2溶解于水生成碳酸后引起的电化学腐蚀,其化学反应式主要为:CO2+H2O H2CO3;Fe+ H2CO3 FeCO3+H2;水中溶解了CO2使pH值降低,呈酸性,碳酸对钢材发生极化腐蚀。
随着碳酸的增多,溶液酸性增加,加快了钢铁的腐蚀速度。
CO2对碳钢的腐蚀为管内腐蚀,表现为3种腐蚀形式:均匀腐蚀、冲刷腐蚀和坑蚀,其产物为FeCO3和Fe3CO4。
在一定条件下,水汽凝结在管面形成水膜,CO2溶解并吸附在管面,使金属发生均匀的极化腐蚀。
管柱内的高速气流冲刷带走腐蚀物,使得金属表面不断裸露,腐蚀加速。
腐蚀产物FeCO3和Fe3CO4在金属表面形成保护膜,但这种膜生成的很不均匀,易破损,出现典型的坑点腐蚀,蚀坑常为半球形深坑。
CO2生产井的腐蚀部位主要集中在管串的上部位置及内壁,这是因为井筒的中上部位压力低、井温低,凝析水易产出,与CO2作用生成腐蚀介质H2CO3的浓度高,随着气体流动,酸液以液滴形式附着在管内壁上形成局部的严重蚀坑蚀洞,造成了油套管的腐蚀现象。
2、影响因素2.1CO2分压在影响CO2腐蚀速率的各个因素中,CO2分压起着决定性的作用,它直接影响CO2在腐蚀介质中的溶解度和溶液的酸度,即溶液的酸度和腐蚀速度皆随CO2分压的增大而增加。
在气井中,当CO2的分压大于0.2MPa时,将发生腐蚀,分压小于0.021MPa时,腐蚀可以忽略不计。
- 1、下载文档前请自行甄别文档内容的完整性,平台不提供额外的编辑、内容补充、找答案等附加服务。
- 2、"仅部分预览"的文档,不可在线预览部分如存在完整性等问题,可反馈申请退款(可完整预览的文档不适用该条件!)。
- 3、如文档侵犯您的权益,请联系客服反馈,我们会尽快为您处理(人工客服工作时间:9:00-18:30)。
CO2腐蚀的机理及介绍1.1 CO2的腐蚀特点:从CO2的腐蚀情况来看,腐蚀的形状各异,但从各种情况分析,除了外观和介质油差别外,所有的气田用钢材的CO2腐蚀都非常集中以蚀坑、沟槽或大小不同的腐蚀区的型式出现,所以腐蚀穿透率很高,一般都达数毫米/年,一般来说,底面平整边缘锐利,是典型的CO2腐蚀特征。
2.3CO2的腐蚀机理:钢铁在除O2水中CO2腐蚀机理,其阳极反应主要是Fe的溶解,可简写为:Fe →Fe2+ + 2e (1)对阴极过程观点不一,较占主导的观点认为,在环境温度下,裸钢在除O2水中的腐蚀是受氢析出动力学控制,而阴极析氢机制除了一般的电化学还原H3O+离子放电反应析氢外,既在低pH除了非催化的析氢机制:H3O+ + e →H + H2O (2)反应外,还可以通过下述表面吸附催化作用H+还原反应析氢机制进行:CO2 + H2O = H2CO3 (3)H2CO3 + e =H+ + HCO3- (4)HCO3- + H3O+ = H2CO3 + H2O (5)上述析氢机制得到的一些试验的支持,并由此可以得出(1)不同金属材料具有不同的催化活性,而影响腐蚀速率。
(2)在一定pH范围(4~6),pH对阴极反应速度没有明显影响。
然而实际中,钢铁表面总是被某些物质覆盖着,如扎皮、氧化膜或在含介质中的腐蚀产物膜等,这些覆盖物使析氢可能不是在裸钢表面而是在膜或覆盖物上进行,因此影响到腐蚀特性,而这些问题不是上述简单机制所能解决的,所以CO2腐蚀机理仍在研究中。
2.4影响CO2腐蚀的因素:由于介质中的成分比较复杂,各种成分的含量也各不同,因此在各种条件下,影响CO2腐蚀特性的因素很多,归纳起来可以分为以下几个因素:(1)温度的影响(2)CO2分压(Pco2)影响(3)腐蚀产物膜的影响(4)流速的影响(5)pH、Fe2+及介质组成的影响等,这些因素可能导致钢的多种腐蚀破坏,比如可能产生高的腐蚀速率、严重的局部腐蚀穿孔,甚至可能发生应力腐蚀开裂等。
2.4.1温度的影响:大量的研究结果显示温度是CO2腐蚀的重要影响参数,较多的结果表明在60℃附近CO2腐蚀在动力学上有质的变化。
由于碳酸亚铁的溶解度具有负的温度系数,随着温度的升高而降低,因此在60℃~110℃之间,钢表面可生成具有一定保护性的腐蚀产物膜层,是腐蚀腐蚀速率出现过渡区,该温区内局部腐蚀较突出。
而低于60℃时不能形成保护性膜层,钢的腐蚀速率在此区出现极大值(含Mn钢在40℃附近、含Cr钢在60℃附近)。
在110℃或更高的温度范围内,由于可能发生下列反应:3Fe + 4H2O = Fe3O4 + 4H2因而在110℃附近显示出钢的第二个腐蚀速率极大值,表面产物膜层也由FeCO3变成杂有Fe3O4和FeCO3膜并随温度升高,Fe3O4量增加,达到更高温下成为Fe3O4在膜中占主导地位。
由上述表明,温度是通过化学反应和腐蚀产物膜特性影响钢的腐蚀特性,因此具体的钢种和环境介质、状态参数的差异会得到不同温度规律。
根据温度对CO2腐蚀特性的影响,CO2对钢的腐蚀可以粗略的划分为三类:(1)温度小于60℃时腐蚀产物为FeCO3,由于FeCO3软而无附着力,金属表面光滑,是均匀腐蚀。
(2)100℃附近,具有高的腐蚀速率和严重的局部腐蚀(深孔),腐蚀产物层厚而松,为粗晶粒的FeCO3。
(3)150℃以上腐蚀产物层是细致、紧密、附着力强的FeCO3和Fe3O4,腐蚀速率降低。
2.4.2 CO2分压(P co2)影响:CO2分压(Pco2)对碳钢、低合金钢腐蚀速率的影响,在温度小于60℃时,裸钢未形成保护性腐蚀产物膜情况下有重要影响,可用下列经验公式表达:lgCR = 0.67lg Pco2+ C式中:CR —腐蚀速率Pco2 —CO2分压C —与温度有关的常数由于腐蚀产物的影响,该式计算结果往往高于实测值,因此该式只能用来估算没有膜的裸钢(最坏的情况)的腐蚀速率,然而该式不能反映出流动状态下合金元素等对腐蚀速率有重要影响,从而限制了实际应用。
一般情况下可以认为CO2分压高于0.21MPa时通常要出现腐蚀,在0.021 MPa~0.21 MPa之间可能出现腐蚀,低于0.021 MPa时腐蚀不严重。
2.4.3腐蚀产物膜的影响:腐蚀产物表面膜对钢的CO2腐蚀具有显著的影响,在含CO2介质中,钢表面腐蚀产物膜的组成、结构、形态及特性会受介质组成、Pco2、温度、pH值和钢的组成的影响,膜的稳定性、渗透性等会影响钢的腐蚀特性,完整、致密、附着力强的稳定性膜可减少均匀腐蚀速率,而膜的缺陷、膜脱落可以诱发局部腐蚀,配合其它因素而形成孔蚀、台地状侵蚀、涡状腐蚀、冲刷腐蚀及应力腐蚀开裂等。
对腐蚀产物膜的研究,尤其是如何形成保护膜、改善膜保护性以及快速评定或监测保护性能的技术等在生产中都具有重要意义。
2.4.4流速的影响:在实际经验和实验室研究中,都发现流速对钢的CO2腐蚀有重要影响,腐蚀速率随流速增加有很大的增加,可能导致严重局部腐蚀,在充分的试验数据基础上,得出腐蚀率随流速增大的经验公式:CR = B·V 0.8式中:CR —腐蚀速率V—流速B —常数由于油、气工业中流动情况很复杂,从静止到高速湍流状态都存在,所以在各种流动状态下的腐蚀特性还有待于研究。
2.4.5 pH、Fe2+及介质组成的影响:裸钢在含CO2的除O2水中,pH值低于3.8以下范围内,腐蚀速率随pH值降低而增大,但pH值不仅是Pco2和T的函数,与CO2含量有关,也与水中Fe2+和其它离子浓度有关,除O2纯水中,若无Fe2+等离子,CO2溶于水可使pH显著降低,造成很强的腐蚀性。
而在同样Pco2、T条件下,Fe2+增加30ppm,就使水的pH值从3.9增加到5.1,这个作用相当于变化Pco2几个大气压的效果。
pH值升高影响FeCO3溶解度,在局部高pH值下,接近钢表面的Fe2+便沉积为FeCO3膜,从而影响到腐蚀速率。
2.5解决CO2腐蚀问题的方法:由于四川设计院所接触的气田都是含有H2S和CO2,没有单独含CO2介质的气田,因此四川设计院采取的措施一般都是主要用于来针对H2S 的介质腐蚀,对于H2S和CO2腐蚀问题采取的解决方法主要有以下四种:(1)加注缓蚀剂(2)内部刷防腐涂料(3)在选材方面考虑(4)进行腐蚀情况监测等。
2.5.1流程中增加注缓蚀剂装置:缓蚀剂又称腐蚀抑制剂,是指一些用于腐蚀环境中抑制金属腐蚀的化学添加剂,对于一定的金属和腐蚀介质体系,只要在其中加入少量的缓蚀剂就能有效地降低该金属的腐蚀速率,由于缓蚀剂使用量较少,介质环境的性质基本上不会改变,也不需要太多的辅助设备,因此加注缓蚀剂是减缓酸性气田井下及地面管道、设备电化学腐蚀、延长使用寿命的主要技术措施之一。
加缓蚀剂防腐的机理是用缓蚀剂膜将钢材表面与腐蚀介质隔离开来,防止腐蚀介质对钢材表面产生电化学腐蚀。
一般的来说缓蚀剂可根据在不同介质中起作用分为液相型、气相型和气液相混合型三种,缓蚀剂的覆盖率都能够达到90%以上,但由于操作介质的组成不同,在某一个环境条件下,使用效果好的缓蚀剂,在其它条件下就不一定适用,因此我们在选择缓蚀剂时就必须根据不同的适用环境来选用。
四川设计院推荐的缓蚀剂:CZ3—1型适用于液相介质,CZ3—3型适用于气相介质,CZ3—1E适用于气、液两相介质(新型)。
液相型和气相型缓蚀剂可以配合使用也可以达到气液两相缓蚀的作用。
四川设计院所接触的缓蚀剂大多是对H2S和CO2同时存在介质有效果的缓蚀剂,对单独含有H2S或CO2介质的效果也不错。
2.5.2管道内部刷防腐涂料:在金属设备的表面涂防腐涂料是防止和控制金属腐蚀的最常见手段之一,现在人们把能在物体表面形成有机涂层的化学物质材料统称为涂料,把涂敷涂料的过程称为涂装。
由四川设计院应用技术研究所研制的AC—1型卤水管道内壁防腐涂料,经威远气田现场使用达8年时间,涂层抗硫化氢、卤水介质,性能优良,AC—1型涂料分底漆、面漆和固化剂组成,可以现场采用喷涂、刷涂、挤涂的方法进行施工。
防腐涂料对金属的保护主要是由于它在金属表面是上形成的在腐蚀介质与金属间的漆膜的屏蔽作用,因此涂料本身的性能和有关漆膜形成过程中的参数(包括金属表面处理、涂敷工艺、干燥固化过程等)都直接影响涂层的防腐效果。
而且对于设备来说,进行涂料防腐有一定的局限性,比如对于公称直径较小的设备、内部构件较为复杂的设备或设备上公称直径很小的接管等都不能保证全部涂敷到,因此这些部位产生腐蚀的可能性较大。
2.5.3选材方面:从设备的安全角度来讲,材料的选择是最重要的一环,如果从材料方面能够解决的腐蚀问题,在设备造价允许的情况下,设备应首先选用优良的材料来进行设计。
据四川设计院有关专家介绍,我国目前还没有单独防止CO2腐蚀的材料,但可以根据一定的原则来进行选材并在制造上采取一定有效措施:(1)应选用比较软的材料,比如:Q235—A、20R等,一般不轻易使用16Mn材料。
(2)设备制造完毕后,应进行整体热处理。
(3)焊接方面应焊接一次成功,避免焊缝不合格时进行补焊,因为补焊的部位易产生腐蚀。
(4)一般的情况下选取腐蚀裕量为4mm。
(5)降低焊缝及其热影响区的硬度HB200以下。
2.5.4进行腐蚀情况监测:在现实生产,往往是当设备出现问题时,我们才能去进行检修,而在生产运行过程中,我们却并不了解设备的腐蚀状况。
如果能够在线监测设备内部的腐蚀情况,使我们能够正确掌握设备内部的腐蚀趋势,就可以考虑采取适当的防腐措施,及时更换腐蚀严重的设备,有效地避免各种事故的发生。
同时可以积累经验,为今后的设计提供依据。
腐蚀监测是指对设备的腐蚀或破坏进行系统测量,其目的在于搞清腐蚀过程、了解腐蚀控制的应用情况和控制效果。
通过腐蚀监测,可以获得腐蚀过程和操作参数之间相互联系的有关信息,以便对问题进行判断,改善腐蚀控制,使设备更有效地运行。
某设计院推荐了一套腐蚀监测系统CMA—1000型,该系统使一套监测设备内部腐蚀状况的仪器,通过电阻(ER)腐蚀探针、线性极化电阻(LPR)腐蚀探针监测设备内部的电化学腐蚀程度、氢脆趋势、评价缓蚀剂效果,并分析介质压力、流速、温度等工艺参数对腐蚀的影响。
CMA—1000型腐蚀监测系统适用于石油天然气工业中采油、采气井口装置、油气输送管道、污水输送管道、输油输气站,化学工业中各种化工厂的输送管道、容器、塔等具有腐蚀的环境。
2.6 存在的问题:通过调研,了解到一定的关于H2S、CO2腐蚀的情况,以及防止H2S、CO2腐蚀的手段,但对于单独CO2的腐蚀情况四川设计院也没有具体经验,四川设计院的专家认为能够防止H2S、CO2腐蚀的方法,对单独CO2的腐蚀也起作用,没有具体的试验或实测数据,因此对于CO2腐蚀问题还存在以下问题:(1)缓蚀剂的选型问题,因为介质的组分和生产过程的前期、后期的情况不同,缓蚀剂的选取也不同。