CO2腐蚀文献2
油气田CO2腐蚀的防护技术研究
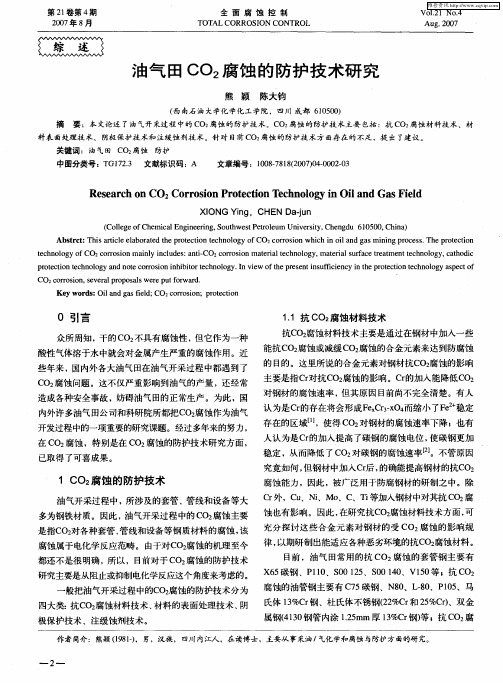
众所周知 , 干的 C 不具有腐蚀性 ,但它作为一种 O2
11 抗 CO 腐 蚀材 料技 术 . z
抗C 2 O 腐蚀材料技术主要是通过在钢材 中加入一些
能抗C 2 O 腐蚀或 减缓 C 2 O 腐蚀 的合金元素来达到防腐蚀
酸性 气体溶于水中就会对金属产生 严重的腐蚀作用 。近
些年来 , 国内外各大油气 田在油气开采过程中都遇到了 C2 O 腐蚀问题 。这不仅严重影响到油气的产量 ,还经常 造成各种安全事故 ,妨碍油气 田的正常生 产 。为此 ,国
C02 o r s n s v r l r p s l we ep t o wa d ro i . e e a o o as r u r r , c o p f Ke r s Oi a dg sf l ; y wo d : l n a i d CO2 o r so ;p oe to e r o i n r tc i n c
维普资讯
第 2 卷第 4 1 期
20 年 8月 07
全 面 腐 蚀 控 制
TOTA CORROS ON L I CONTROL
Vo . 1 1 NO 4 2 . Au . 0 7 g 2 0
油 气 田 Co2 蚀 的 防 护 技 术 研 究 腐
中图分类号 :T 7 . 文献标识码 :A G1 2 3
文章编号 :10 —8 820 )40 0 —3 0 87 l(0 70 —0 20
Re e r h o s a c n C02 r o i n Pr tc i nT c n l g l n sF ed Co r so o e to e h o o yi Oi a d Ga il n X ON ig I G Yn ,CH N D - n E aj u
某油田开发中二氧化碳腐蚀的危害性现状分析

某油田开发中二氧化碳腐蚀的危害性现状分析要想降低油气田开采中的二氧化碳腐蚀,必须对腐蚀机理以及类型基质影响因素这些进行分析和研究。
通过对腐蚀机理调研可以发现,二氧化碳会产生碳酸,进而产生电化学反应,最终造成钢材腐蚀。
在腐蚀种类上有均匀和冲刷以及坑点腐蚀,影响因素较多。
现在开发中防腐蚀措施也较多,现在主要对腐蚀的危害以及方式方式进行论述。
标签:二氧化碳;腐蚀机理;防腐方式前言:在油田开发中,二氧化碳腐蚀会造成巨大损失同时也会发生灾难性后果。
二氧化碳还石油和天然气开发中产生的常见气体。
在溶于水之后对金属会有加强的腐蚀性,这些对材料造成的破坏可以称之为二氧化碳腐蚀。
这些腐蚀会使得油井寿命大大低于设计寿命,也会使得设备腐蚀失效,现在掌握好腐蚀问题研究现状以及趋势,为减少损失提升效益提供借鉴。
1 二氧化碳腐蚀的机理二氧化碳腐蚀问题一直是人们关注的主要问题。
因为在二氧化碳溶于水之后PH 值升高,不断加速管材腐蚀,金属表面附着的H2C03中没有被电离的分子会被还原为H2分子,在电解质溶液中扩散到金属表面形成H2C03。
从此也可以看出碳酸造成的腐蚀要明显比电离要严重。
腐蚀学认为,坑腐蚀诱发主要是因为有台地腐蚀机制以及流动诱导机制等都会造成膜破损。
也有人通过腐蚀产物膜生产和发展过程,提出台地腐蚀机制:坑蚀最早出现在几个点,之后发展为一片,小孔腐蚀介质会破坏腐蚀产物膜,从而造成腐蚀。
2 二氧化碳腐蚀中的影响因素二氧化碳腐蚀是一个复杂的电化学过程,主要影响因素为PH 值以及二氧化碳分压、温度和流速、水量等各种因素。
2.1 PH 值。
溶液内PH 值会影响到H2C03在水中存在方式,在研究中可以发现PH﹤4 时,主要存在形式为H2C03;在4≤PH≤10 时,主要是以HC03 的形式出现,在PH>10 时,存在形式是CO2。
同时随着PH 值持续增加,H+增加而不断下降,腐蚀速率也会逐渐降低。
随着FeCO3 内的溶解度持续下降,更方便FeCO3 腐蚀膜的形成,这样也会降低腐蚀速率。
海上油气田CO2/H2S腐蚀控制

溶解的 ls H ・ l/(gL ) 2 -
图 1 H S的 不 同溶 解 度 对碳 钢 腐 蚀 的 影 响 :
12 2 溶解 氧 的影 响 ..
的溶解 盐类 。在质 量浓 度低 的情 况下 , 这些 盐类 不
油气 田采 出水 中含 有 的氧一 般 由注入水 携带 。
和海底集输管道腐蚀 , 造成泵漏 、 管漏、 杆管断脱和 井下 工具 密封失 效 等 事 故 , 生 产 带来 极 大 危 害 , 给
且造 成重 大经济 损失 。
1 海 上油气 田腐 蚀现 状分 析 1 1 溶解盐 类 的影响 .
化学腐蚀产生氢 , 氢原子向钢铁 内部渗透 , 从而导 致 氢损伤 , 在很 低 的 拉 应力 下 就 可 能发 生 破 裂 , 因 此在 H s 腐蚀严重地区, 抽油杆断裂会更频繁。
张 强 李家锋 孙爱平
( 中国海洋石油能 源发展股 份有 限公 司 , 广东 湛江 54 5 ) 20 7
摘要: 根据 中国海 洋石油 南海 西部各油 气田的 实际情 况 , 结合水质特 点分析 了采 油平 台、 输油管 道、 水处理 系统和生产 管汇腐蚀的原 因以及影响 因素。阐述 了海上油气田腐蚀 机理 , 出了海上油气 提
田 开 采 的 防腐 蚀 措 施 。
关键词 : 海上油气 田
水质
C2 o 腐蚀
C :H S O / : 腐蚀
影 响因素
防护方法
中图分类号 :G 7 . T 126
文献标识码: A
文章编号 :17- 1X[0 0 0 00 0 10 05 2 1 )2- 0 1— 6 3
随着海上 油气 田注水 开 发 的深 入 , 大部 分地 区 进 入高 含水开 发期 , 由于其 水 质 矿 化 度较 高 、 蚀 腐 介 质质量 浓度 大 和注 海 水均 会 导 致 油 井 井 下设 备
CO_2腐蚀产物的分析及其防腐技术研究

CO 2腐蚀产物的分析及其防腐技术研究X姚志霞1,陈相伟2,陈暗梅1(1.中原油田采油二厂注水大队;2.中原油田油气储运管理处,河南濮阳 457532) 摘 要:在论述CO 2的腐蚀机理的基础上,分析了影响腐蚀的各种因素,例如温度、压力等。
并重点对CO 2的腐蚀产物进行研究,从表面形态结构到影响膜厚和膜晶粒大小的因素进行阐述。
最后归纳了最近的防腐技术,并说明了如何确定合理的防腐技术。
关键词:CO 2腐蚀;腐蚀产物;防腐技术 中图分类号:T E98 文献标识码:A 文章编号:1006—7981(2012)14—0088—04 CO 2腐蚀是油套管腐蚀的重要类型之一。
研究表明,在含CO 2的油水体系或水溶液中,铁基金属表面会形成一层主要成分为FeCO 3的腐蚀产物膜。
而产物膜的物理性能又会影响CO 2的腐蚀。
分析腐蚀产物膜的结构及物性对如何防腐和腐蚀研究有重要的意义和作用。
1 腐蚀机理干燥的CO 2气体本身是没有腐蚀性。
但当CO 2溶解于水中时形成碳酸,会引发钢铁材料发生电化学腐蚀。
暴露于含CO 2的介质中钢铁材料,表面很容易沉积一层垢或腐蚀产物,如果结构致密,就会阻抑金属的腐蚀。
相反,不够致密时会使垢下的金属成为缺氧区,和周围的富氧部分形成一个氧浓差电池,垢下金属发生阳极溶解并进一步快速腐蚀[1]。
Ogundele 等人[2]认为主要的腐蚀过程可以概括为三个阴极反应和一个阳极反应,在pH 值为6时,阴极发生的主要过程为H 2CO 3和HCO 3-的减少:2H 2CO 3+2e -→H 2+2HCO 3-2HCO 3-+2e -→H 2+2CO 32-2H+2e -→H 2Fe →Fe 2++2e -经过上述反应,在碳钢的表面就会形成一层腐蚀膜。
有些资料认为碳酸铁(Fe-CO 3)对保护膜的形成有重要的影响,它的形成过程如下:Fe 2++CO 2-3→FeCO 3Fe 2++2HCO 3-→Fe (HCO 3)2Fe (HCO 3)2→FeCO 3↓+CO 2+H 2O同时Waar d 和Milliams 的研究表明[3],钢在酸中的阴极反应如下:2H →H 2或H ++e -→H 2然而Bockris,Drazic 和Despic 提出了不同的观点[4]F ++→F O +F O +→F ++O 从反应过程可知,由于涉及了OH -离子和H +离子,所以在固定电位下,阳极溶解与H +离子浓度成反比,因此腐蚀速率主要依赖于pH 值。
油气井中的二氧化碳腐蚀

(4)
式中 : Ic—腐蚀速率 , mm / a; T—温度 , °K; R —气体常
数 , cal. /mole0 K。
D e W aard等认为 [ 1 ] ,在 70 ℃~80℃时 , CO2 的
腐蚀速率存在一个最大值 ,此后随温度升高 ,腐蚀速
率降低 ,这是因为生成了 FeCO3 或 Fe3 O4 膜 。这种 膜并不是在所有条件下都具有保护性 ,只有在高温
1. CO2 分压的影响 在影响 CO2 腐蚀速率的各个因素中 , CO2 分压
起着决定性作用 ,从式 ( 1)和式 ( 2)便可以看出 CO2 的腐蚀速率和 CO2 分压之间的关系 。Lohodny等 [ 8 ] 的研究表明 : 在气井中 , 当 CO2 分压大于 206. 85 kPa时将发生腐蚀 ;当 CO2 分压在 20. 685~206. 85 kPa 之 间 时 , 腐 蚀 有 可 能 发 生 ; 当 CO2 分 压 小 于
壁的剪切应力联系起来考虑的 ,因为流动直接影响
物质扩散和力矩的传递 。
当流速小于 1 m / s时 ,可以认为是静止的 ,此时
腐蚀速率较大 。因为在静止的条件下 ,没有紊流来
保证液相与保护性的烃及缓蚀成分的混合 ,加剧了
缝隙腐蚀和垢下腐蚀 。
流速在 1~3 m / s之间时 ,通常是层流 。此时 ,
膜的性质发生变化以后才具有保护性 ,这个温度被
称作成膜温度 。此时金属表面局部的 Fe2 + 浓度和
pH 值保证保护性膜的形成 ,这个温度取决于流速 、
pH值和 CO2 的分压等条件 ,当流速和 pH 值增高 、 CO2 分压降低时 ,成膜温度升高 。
成膜温度可以由式 (5)计算
log ( Fscale ) = 2400 / T - 0. 6 log ( FCO2 ) - 6. 7 ( 5) 当 log ( Fscale ) = 0时的温度即是成膜温度 。 将温度的影响用修正因子来表示 。
川气东送天然气管道材料CO_(2)腐蚀机理研究
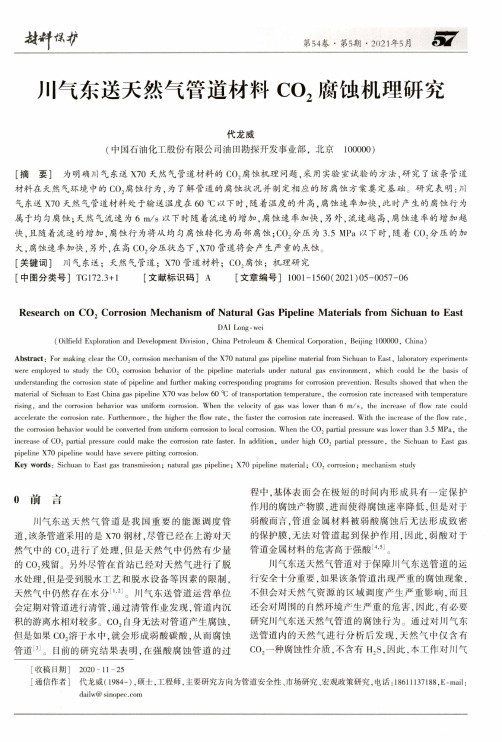
第54卷.第5期.2021年5月S7川气东送天然气管道材料c o2腐蚀机理研究代龙威(中国石油化工股份有限公司油田勘探开发事业部,北京100000)[摘要]为明确川气东送X7 0天然气管道材料的C02腐蚀机理问题,采用实验室试验的方法,研究了该条管道 材料在天然气环境中的(:02腐蚀行为,为了解管道的腐蚀状况并制定相应的防腐蚀方案奠定基础。
研究表明:川气东送X70天然气管道材料处于输送温度在60 T;以下时,随着温度的升高,腐蚀速率加快,此时产生的腐蚀行为 属于均勾腐蚀;天然气流速为6 m/s以下时随着流速的增加,腐蚀速率加快,另外,流速越高,腐蚀速率的增加越 快,且随着流速的增加,腐蚀行为将从均匀腐蚀转化为局部腐蚀;C02分压为3.5 M Pa以下时,随着(:02分压的加 大,腐蚀速率加快,另外,在高C02分压状态下,X70管道将会产生严重的点蚀。
[关键词]川气东送;天然气管道;X70管道材料;C02腐蚀;机理研究[中图分类号]TG172.3+1 [文献标识码]A[文章编号]1001-1560(2021)05-0057-06Research on C02Corrosion Mechanism of Natural Gas Pipeline Materials from Sichuan to EastDAI Long-wei(Oilfield Exploration and Development Division, China Petroleum & Chemical Corporation, Beijing 100000, China)A b stract:For making clear the C02 corrosion mechanism of the X70 natural gas pipeline material from Sichuan to East, laboratory experiments were employed to study the C02corrosion behavior of the pipeline materials under natural gas environment, which could be the basis of understanding the corrosion state of pipeline and further making corresponding programs for corrosion prevention. Results showed that when the material of Sichuan to East China gas pipeline X70 was below 60 of transportation temperature, the corrosion rate increased with temperature rising, and the corrosion behavior was uniform corrosion. When the velocity of gas was lower than 6m/s, the increase of flow rate could accelerate the corrosion rate. Furthermore, the higher the flow rate, the faster the corrosion rate increased. With the increase of the flow rate, the corrosion behavior would be converted from uniform corrosion to local corrosion. When the C02 partial pressure was lower than 3.5 MPa, the increase of C02partial pressure could make the corrosion rate faster. In addition, under high C02partial pressure, the Sichuan to East gas pipeline X70 pipeline would have severe pitting corrosion.Key w ords:Sichuan to East gas transmission;natural gas pipeline;X70 pipeline material;C02corrosion;mechanism study0前言川气东送天然气管道是我国重要的能源调度管 道,该条管道采用的是X70钢材,尽管已经在上游对天 然气中的c o2进行了处理,但是天然气中仍然有少量 的c o2残留。
油气田CO2腐蚀及防控技术
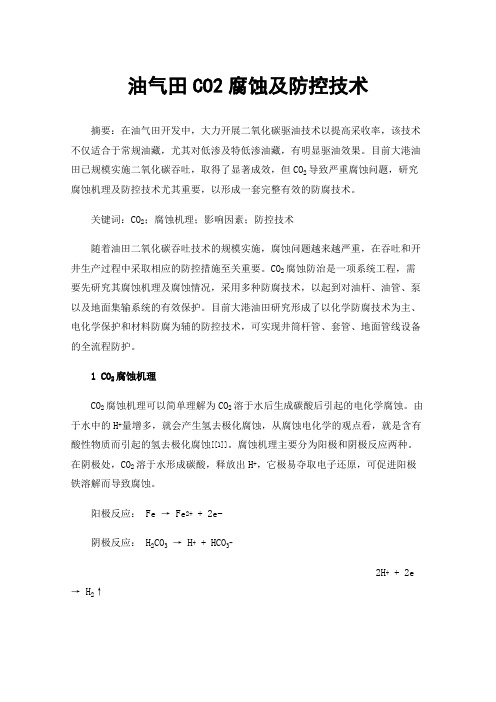
油气田CO2腐蚀及防控技术摘要:在油气田开发中,大力开展二氧化碳驱油技术以提高采收率,该技术不仅适合于常规油藏,尤其对低渗及特低渗油藏,有明显驱油效果。
目前大港油田已规模实施二氧化碳吞吐,取得了显著成效,但CO2导致严重腐蚀问题,研究腐蚀机理及防控技术尤其重要,以形成一套完整有效的防腐技术。
关键词:CO2;腐蚀机理;影响因素;防控技术随着油田二氧化碳吞吐技术的规模实施,腐蚀问题越来越严重,在吞吐和开井生产过程中采取相应的防控措施至关重要。
CO2腐蚀防治是一项系统工程,需要先研究其腐蚀机理及腐蚀情况,采用多种防腐技术,以起到对油杆、油管、泵以及地面集输系统的有效保护。
目前大港油田研究形成了以化学防腐技术为主、电化学保护和材料防腐为辅的防控技术,可实现井筒杆管、套管、地面管线设备的全流程防护。
1CO2腐蚀机理CO2腐蚀机理可以简单理解为CO2溶于水后生成碳酸后引起的电化学腐蚀。
由于水中的H+量增多,就会产生氢去极化腐蚀,从腐蚀电化学的观点看,就是含有酸性物质而引起的氢去极化腐蚀[[1]]。
腐蚀机理主要分为阳极和阴极反应两种。
在阴极处,CO2溶于水形成碳酸,释放出H+,它极易夺取电子还原,可促进阳极铁溶解而导致腐蚀。
阳极反应:Fe → Fe2+ + 2e-阴极反应: H2CO3→ H+ + HCO3-2H+ + 2e → H2↑碳酸比相同pH值下的可完全电离的酸腐蚀性更强,在腐蚀过程中,可形成全面腐蚀和局部腐蚀。
全面研究二氧化碳的腐蚀机理十分关键,2CO2腐蚀影响因素二氧化碳对金属材料的腐蚀受多种因素影响,有材质因素、压力、温度、流速、pH、介质中水和气体、有机酸、共存离子、细菌腐蚀等,本文主要介绍三种重要因素。
2.1 二氧化碳压力碳钢等金属的腐蚀速度随二氧化碳分压压力增大而加大,溶于水介质中CO2的含量增大,酸性增强,H+的还原反应就会加速,腐蚀性加大。
通过高温高压动态腐蚀评价来验证压力的影响,选取二氧化碳不同压力作为试验条件,对采出液在不同压力下评价腐蚀性。
一种环境响应型水泥石的抗CO2腐蚀性能
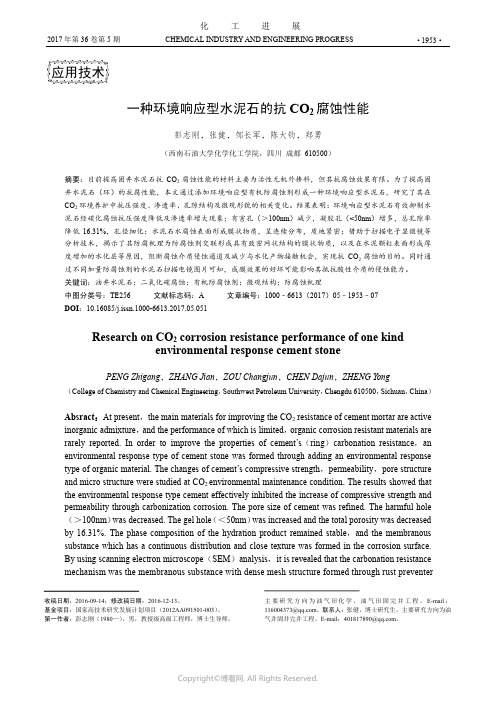
2017年第36卷第5期 CHEMICAL INDUSTRY AND ENGINEERING PROGRESS·1953·化 工 进展一种环境响应型水泥石的抗CO 2腐蚀性能彭志刚,张健,邹长军,陈大钧,郑勇(西南石油大学化学化工学院,四川 成都 610500)摘要:目前提高固井水泥石抗CO 2腐蚀性能的材料主要为活性无机外掺料,但其抗腐蚀效果有限。
为了提高固井水泥石(环)的抗腐性能,本文通过添加环境响应型有机防腐蚀剂形成一种环境响应型水泥石,研究了其在CO 2环境养护中抗压强度、渗透率、孔隙结构及微观形貌的相关变化。
结果表明:环境响应型水泥石有效抑制水泥石经碳化腐蚀抗压强度降低及渗透率增大现象;有害孔(>100nm )减少,凝胶孔(<50nm )增多,总孔隙率降低16.31%,孔径细化;水泥石水腐蚀表面形成膜状物质,呈连续分布,质地紧密;借助于扫描电子显微镜等分析技术,揭示了其防腐机理为防腐蚀剂交联形成具有致密网状结构的膜状物质,以及在水泥颗粒表面形成厚度增加的水化层等原因,阻断腐蚀介质侵蚀通道及减少与水化产物接触机会,实现抗CO 2腐蚀的目的。
同时通过不同加量防腐蚀剂的水泥石扫描电镜图片可知,成膜效果的好坏可能影响其抵抗酸性介质的侵蚀能力。
关键词:油井水泥石;二氧化碳腐蚀;有机防腐蚀剂;微观结构;防腐蚀机理中图分类号:TE256 文献标志码:A 文章编号:1000–6613(2017)05–1953–07 DOI :10.16085/j.issn.1000-6613.2017.05.051Research on CO 2 corrosion resistance performance of one kindenvironmental response cement stonePENG Zhigang ,ZHANG Jian ,ZOU Changjun ,CHEN Dajun ,ZHENG Yong(College of Chemistry and Chemical Engineering ,Southwest Petroleum University ,Chengdu 610500,Sichuan ,China )Absract :At present ,the main materials for improving the CO 2 resistance of cement mortar are active inorganic admixture ,and the performance of which is limited ,organic corrosion resistant materials are rarely reported. In order to improve the properties of cement’s (ring )carbonation resistance ,an environmental response type of cement stone was formed through adding an environmental response type of organic material. The changes of cement’s compressive strength ,permeability ,pore structure and micro structure were studied at CO 2 environmental maintenance condition. The results showed that the environmental response type cement effectively inhibited the increase of compressive strength and permeability through carbonization corrosion. The pore size of cement was refined. The harmful hole (>100nm )was decreased. The gel hole (<50nm )was increased and the total porosity was decreased by 16.31%. The phase composition of the hydration product remained stable ,and the membranous substance which has a continuous distribution and close texture was formed in the corrosion surface. By using scanning electron microscope (SEM )analysis ,it is revealed that the carbonation resistance mechanism was the membranous substance with dense mesh structure formed through rust preventer主要研究方向为油气田化学、油气田固完井工程。
- 1、下载文档前请自行甄别文档内容的完整性,平台不提供额外的编辑、内容补充、找答案等附加服务。
- 2、"仅部分预览"的文档,不可在线预览部分如存在完整性等问题,可反馈申请退款(可完整预览的文档不适用该条件!)。
- 3、如文档侵犯您的权益,请联系客服反馈,我们会尽快为您处理(人工客服工作时间:9:00-18:30)。
FUNDAMENTAL ASPECTS OF CO 2 METAL LOSS CORROSION – PART II: INFLUENCE OF DIFFERENT PARAMETERS ON CO 2 CORROSION MECHANISMSGuenter SchmittLaboratory of Corrosion ProtectionIserlohn University for Applied SciencesFrauenstuhlweg 31, D-58644 IserlohnGermanyMichaela HörstemeierInstitute for Technical and Macromolecular ChemistryAachen University of TechnologyWorringerweg 1, D-52074 AachenGermanyABSTRACTThe literature has been reviewed with respect to information gained in the recent 20 years on CO 2 corrosion of materials used in the oil and gas industry. The paper discusses the effect of materials-related, medium-related and interface-related parameters on general (uniform) and localized corrosion.INTRODUCTIONCarbon dioxide corrosion of steels is influenced by materials-related, medium-related and interphase-related parameters. The paper will address the present day knowledge on the effect of these parameters on the corrosion of steels with respect to general corrosion and localized corrosion including pitting, preferential weld corrosion, flow induced localized corrosion and stress cracking. The rate of general corrosion and the susceptibility to localized corrosion is mainly dependent on the formation of protective, semi-protective or non-protective corrosion product scales which are affected by temperature, CO 2 partial pressure, medium composition (iron ion concentration, presence of certain chemicals), pH, flow, alloy composition and mechanical stress.06112Paper No.©2006 NACE International. Requests for permission to publish this manuscript in any form, in part or in whole must be in writing to NACE International, Conferences Division, 1440 South Creek Drive, Houston, Texas 77084. The material presented and the views expressed in this paper are solely those of the author(s) and are not necessarily endorsed by the Association. Printed in the U.S.A.CopyrightExtensive studies have been performed during the last four decades on the mechanism of CO2 corrosion of steels and the understanding of parameter effects has increased considerably. However, quite a few mechanistic questions are still unsolved or are a matter of debate and require further research. The first general review on CO2 corrosion of steel was performed in 1983 and summarised by Burke [1] and Schmitt [2] in 1984. Recently the key parameters affecting the intensity of carbon dioxide corrosion have been addressed by Kermani et al. [3]. In the same year Lopez et al. reviewed the influence of microstructure and chemical composition of steels on CO2 corrosion with respect to the influence of these parameters on the efficiency of corrosion inhibitors [5]. Several prediction models for carbon dioxide corrosion of oil and gas pipelines have been developed [5-13] and Nyborg [14] presented a complete overview of all relevant modelling approaches.FACTORS INFLUENCING CO2 CORROSIONThe properties of solid corrosion product layers formed on metal surfaces during corrosion reactions control the corrosion rate. This holds as well for the corrosion of steel in CO2 environments. Depending on the formation and the characteristics of iron carbonate scales, CO2 corrosion can be classified into general corrosion and localized corrosion. At low temperature ranges (< ca. 60°C) no protective films are formed on the surface due to the high solubility of iron carbonate and, therefore, general corrosion dominates. At temperatures at and above ca. 80°C the solubility of FeCO3 decreases considerably and high supersaturation leads to FeCO3 precipitation and very dense and protective iron carbonate films can form [14]. When discussing the protectivity of iron carbonate scales also the kinetics of iron carbonate precipitation has to be considered. At sites of nonuniform formation or localized destruction of carbonate films or scales severe localized corrosion can occur.General and localized CO2 corrosion is influenced by a number of factors which can be divided into interface-related, materials-related and medium-related parameters. Interface-related parameters include temperature, flow rate, condensation, and presence of scales. Materials-related parameters are alloy composition, microstructure and heat treatment. The influences of pH, CO2 partial pressure, solution chemistry, and presence of oxygen belong to medium-related parameters. All parameters are interdependent and influence the CO2 corrosion in different ways. The aim of the present work is to give an overview of the present day knowledge on the effect of these parameters on CO2 corrosion.GENERAL CORROSIONInfluence of surface filmsCO2 environments the main end product of carbon steel corrosion is iron carbonate which Informs on the steel surfaces if the supersaturation of FeCO3 in the near-surface solution is sufficiently high [14,15]. FeCO3 precipitates when Fe2+ ions react with carbonate (CO32-) and bicarbonate (HCO3-) ions in the solution. Therefore a high supersaturation of Fe2+ and CO32-/HCO3- is necessary for the formation of protective films. Once the film is formed, it will remain protective at a much lower supersaturation [14]. To get a successful protection, the film must be adherent and cover the whole surface. Localized corrosion can occur if parts of the scale break down and cannot re-form. Nesic et al. described two mechanisms on the protective role of passive surface films [16]. They represent a physical barrier which retards the diffusive transfer of corrosive species and prevent further metal dissolution of the blocked steel surface.The protective properties of the surface scale depend on the characteristics of the material (metal composition, heat treatment/microstructure) and the environmental conditions (temperature, CO2 partial pressure, pH). The morphology and adherence of the corrosion product film has been often related to the presence of carbides. It is suggested that in case of ferritic-pearlitic microstructures the iron carbide phase strengthens the film and anchors it to the steel substrate [17]. This is in agreement with the fact that on carbon steels with a normalized (ferritic-pearlitic) microstructure the iron carbonate scale is better adherent to the metal surface than on quenched-and-tempered steels (martensitic-bainitic microstructure) [17-19]. Thus, the shape and distribution of the carbides plays a very important role.It is well recognized that the temperature strongly influences the conditions needed to form protective iron carbonate layers. At lower temperatures (ca. < 60 °C) the solubility of FeCO3 is high and the precipitation rate is slow and protective films will not form unless the pH is increased [15,20]. In this temperature range the corrosion rate increases with temperatures up to an intermediate range of ca. 60 – 80 °C. Above 60°C the protectiveness of the iron carbonate layer increases with temperature due to the decrease of iron carbonate solubility and, thus, the corrosion rate is reduced (Fig.1). At temperatures above 110°C magnetite (Fe3O4) may form through direct reaction between steel and water (Schikorr Reaction) [2] and at 130°C the steels are passivated [2]. On ferritic-pearlitic steels surface scales formed below 40°C mainly consist of iron carbide (Fe3C) with some FeCO3 and carbonates of alloying elements of the steel [20-21]. Fe3C is part of the original steel microstructure and it is suggested that iron carbides may become sites of the cathodic reaction [20]. In case of martensitic microstructure this model cannot be applied because the cementite is nearly homogenously dispersed and the grain size is very small. Furthermore, in-situ measurement of the conductivity of iron carbonate films revealed that iron carbonate films exhibit a very low electronic conductivity and act as an insulator [22]. Therefore, carbonate films as such cannot act as cathodic sites, e.g. they are not comparable with iron sulfides which exhibit electronic conductivity. This is also true when cementite is dispersed in the carbonate film.The precipitation rate of FeCO3 has been described as a slow and temperature dependent process and even under supersaturated conditions, high corrosion rates can maintain for weeks until protective iron carbonate layers are formed, specifically at low temperatures [23]. Furthermore, in flow systems corrosion films obviously can grow for months without giving protection unless the steel is exposed to stagnant or “wet” conditions [14]. During a few days stagnation, corrosion products can accumulate on the steel surface and form protective films [14]. Thus, the kinetics of FeCO3 precipitation seems to be a controlling factor for the protectiveness of the corrosion product layer. At higher temperatures the FeCO3 solubility is reduced and the precipitation rate is much faster, thus allowing the formation of iron carbonate films [20]. Protective carbonate scales can be recognized already by its morphology and crystallinity. At temperatures ≥ 90°C the scale is composed of well-defined and well-packed cubes, while at lower temperatures a flat grain-type appearance is found [24]. However, the morphology of iron carbonate scales strongly depends not only on the temperature, but on the pH and the CO2 partial pressure, as well. At higher pH values (e.g. 6.5), protective iron carbonate films can also form at room temperature [23-26,27].Effect of TemperatureThe temperature strongly influences the CO2 corrosion due to its effect on the rate of scale formation. As mentioned above, at low temperatures, corrosion rates increase because of high solubility of the FeCO3 film. As temperatures increase (around 60-80 °C) the iron carbonate layer becomes more adherent to the metal surface and more protective in nature resulting in a decrease of the corrosion rate[15,20,28-29]. This correlation between temperature and corrosion rate was reported by many researchers and Ueda et al. attribute the maximum corrosion rate to a critical temperature T max encountered both in carbon and chromium steels, however, differing in T max [30].Effect of FlowFlow affects the metal dissolution rate in different ways [31,32]. Below a critical flow intensity (Fig. 2) the corrosion rate increases only gradually with increasing flow intensity [29,33]. Above the critical flow intensity the interaction between the fluid and the wall becomes so intense that protective films or scales are destructed by near-wall turbulence elements which also prevent re-formation of the protective film [31,32]. In this case the dissolution of the unprotected (bare) metal surface is transport controlled. The typical apperance of flow-shaped surfaces with shallow pits and grooves is the result of chaotic actions of near-wall turbulences. The situation of a "bare" metal surface is encountered in CO2 corrosion of steel also under conditions leading to nonprotective films. Under such conditions the metal dissolution rate is transport controlled, as well, however, is significantly lower.In the presence of protective CO2 corrosion product films the flow intensity can influence to a certain extent the transport of cathodic species towards the steel surface yielding an increase of metal dissolution rates at high flow velocities [29,33]. At the same time flow may stimulate the removal of Fe2+ ions from the steel surface at the bottom of pores and may cause lower surface supersaturation and slower precipitation rates. This in turn yields less protective films and, hence, higher corrosion rates [29, 33,34]. At elevated temperatures critical flow intensities for destruction of protective films and initiation of flow-induced localized corrosion (FILC) are generally higher because films with higher protectivity are formed above certain temperature ranges discussed above. The influence of flow on localized corrosion will be discussed later in more detail.Influence of alloy compositionThe influence of alloy composition of low alloy steel has been investigated intensely in recent years. According to the reviews made in 1983/84 [1,2] the highest effect is encountered with additions of chromium. The corrosion rate is significantly decreased with increasing Cr content [1,2,15,28,30,35-40]. In recent years the interest in low alloy steels with increased Cr content in the order of 3 to 5% Cr has increased due to the pressure to reduce CAPEX and OPEX in oil and gas production. An intermediate alloyed steel between API 5CT grade L80 and 13Cr steel would be of interest which offers improved corrosion resistance but stays with its costs close to API 5CT grade. This prompted a number of investigations which were not only devoted to the chromium content but also to the influence of microalloying elements (V, Ti, Nb, Mo, Cu, Si) [18,35-44]. The idea behind this work was to avoid that chromium is tied up in carbides and then no more available for forming chromium oxide enriched "passive" layers. This should be achieved by reducing the carbon content [28,45] and adding elements that form more stable carbides (V, Ti, Nb, Mo).It appeared that microalloying influences the corrosion performance of 3% Cr steels significantly. Specifically microalloying with vanadium yielded excellent results. The corrosion resistance increases with increasing temperature. Compared to L80 steel the corrosion rate of 3% Cr is decreased by factors of 3 to 40 depending on the temperature (Fig. 3) and microalloying element. The effect of microalloying on the CO2 corrosion rate of steel is summarized in Fig. 4 [36,38]. However, for the effect of Cu in carbon steels controversial results were obtained by Kimura et al. [46] which indicated that increased Cu and Ni contents may accelerate mesa attack and additionally increase the general corrosion rate. Similar results were reported by Dugstad et al. in earlier investigation [47].Microalloyed 3% Cr steels have been announced as a new generation of low alloy steels meeting all requirements for downhole application. However, the benefit can only be used in those cases where corrosion rates are low enough that inhibition ist not necessary. Furthermore, in case of inhibition appropriate inhibitors have to be selected, because inhibitors that work perfectly at L80 steels may not necessarily perform well on surfaces enriched with chromium.Increasing the chromium content up to 5% Cr generally reduces the corrosion resistance of steel to uniform corrosion but localized corrosion like pitting or SSC could occur. In a study with 3 and 5% Cr steels the corrosion rate of the Cr steels was reduced by a factor of two or more compared to chromium free carbon steel, but 5% chromium steel suffered deeper localized attack than 3% chromium steels [35]. Different results were reported earlier in a 5 months field test exposure where 5% chromium steels showed superior corrosion resistance to general and localized corrosion than steels with 0.2- 3%Cr [48].Chromium steels with more than 12 % Cr are very resistant in severe sweet and mildly sour production conditions and have been used for effective corrosion control [40,49]. But it is also widely recognized that stainless steel exhibit less resistance to localized corrosion at elevated temperature and may be susceptible to stress corrosion cracking [40,49,50]. The influence of alloying elements on localized corrosion will be discussed later.Microstructure and Heat TreatmentThe microstructure plays an important role in corrosion of carbon steel in CO2-containing environments. Several authors have studied the influence of steel microstructure on the corrosion process in aqueous solutions containing CO2, although there is no general agreement on this issue [17, 19,30,44,51-54]. The majority of the investigations show that carbon steels with ferritic-pearlitic microstructure exhibit a better corrosion resistance than compared with martensitic or martensitic-bainitic microstructured steels [17,19, 44,53] but also the opposite has been reported [51,52].The effect of microstructures is attributed to different roles of different phases in acting as anodic or cathodic sites. The cementite (Fe3C) phase is generally thought to act cathodically and to enhance the corrosion of ferrite galvanically [30,54]. This, however, holds only for ferritic-pearlitic steels. Furthermore, lamellar pearlite seems to provide better grip for protective scales than particulate pearlite due to the cementite lamellae [17,19,30]. In this context, the influence of heat treatment on the shape and distribution of the cementite gains importance [51]. It appears as kind of a rule that the more uniform the distribution and the smaller the ferrite grain size, the lower the corrosion rate [55].Palacios and Shadley [19]postulated that the structural characteristics of iron carbonate corrosion-product (e.g. the adherence or thickness) depend on the microstructure of the material. It is claimed that iron carbonate is less tenacious and less crystalline on quenched-and-tempered (QT-) steels with martensitic microstructure, and that the corrosion product scale forms more dense and larger crystals on normalised steel with ferritic-pearlitic microstructure [19].This agrees with observations by Ueda et al. [51] who compared the morphology of the corrosion product films of three different carbon steels. Ferritic-pearlitic steel yielded homogeneous FeCO3 films, while carbon steels with martensitic-bainitic microstructure gave porous iron carbonate films [51]. Thus, the better corrosion resistance of ferritic-pearlitic C-Mn steels could be attributed to differences in the morphology of corrosion products. This is explained in more detail in [17] and [19]. It was also reported that in the initial state J55 C-Mn steel with ferritic-pearlitic microstructure showed higher mass loss rate than N80 with martensiticmicrostructure [53, 125]. The rapid initial mass loss of J55 indicates that the film formation occurs earlier and thus corrosion protective films form faster on J55 than on N80 steel. Therefore, J55 exhibits a better corrosion resistance than N80 steel [53].Attempts to profit from both Cr addition (1% Cr) and ferritic-pearlitic microstructure were not successful [48]. It appeared (Fig.5) that the corrosion rate of Cr bearing steel with martensitic microstructure was lower than the corrosion rate of the steel with ferritic-pearlitic microstructure. Furthermore, the corrosion resistance of Cr bearing steel with martensitic microstructure was superior to the corrosion rate of a C-Mn steel with martensitic microstructure. According to Mishra et al [55] the microstructural effect due to different heat treatment becomes vanishingly small at temperatures above 60°C. At the end, the microstructure of materials has to be selected according to the needs of the technical application. If no acceptable compromise is possible with low alloy steel, high alloy steels like 9Cr1Mo or 13Cr should be looked at.Influence of CO2 partial pressureThe CO2 partial pressure plays an important role in CO2 corrosion both for film-free conditions (formation of non-protective films) and for film-forming conditions. In most publications the authors established a relationship between CO2 partial pressure and corrosion rate [29, 56-60]. However, higher CO2 partial pressure means not necessarily also higher corrosion rates. This is a matter of environmental conditions.Generally, under film-free conditions higher CO2 partial pressures results in higher corrosion rates [28,56,58,60] by reducing the pH [61] and by increasing the rate of carbonic acid reduction [62]. This agrees with the finding [63] that the anodic reaction is practically unaffected when the CO2 partial pressure is increased from 3 to 20 bar while the cathodic limiting current density is strongly increased due to a higher reservoir of carbonic acid. This again indicates that in CO2 corrosion the pH is only an orientating parameter for assessing the corrosivity. What really matters is the availability of carbonic acid and the surface sites for its reduction.Under conditions favourable for protective film formation (high supersaturation at the interface with subsequent carbonate precipitation) high CO2 partial pressure can also reduce the corrosion attack due to a lower availability of cathodic sites. It falls within this picture that increasing the CO2 partial pressure from 4 to 18 bars under film-free conditions in a horizontal wet gas flow yields an increase of the corrosion rate from about 3 mm/y to about 8 mm/y [56]. On the other hand, an increase of the CO2 partial pressure in the same flow system from 3.8 to 10.6 bar reduces the max. corrosion rates from about 15 to 0.2 mm/y (Fig. 6) [56] under conditions when semiprotective films are formed, e.g. in the pH range below pH 5.2. In another case, an increase of the CO2 partial pressure from 1 to 30 bar in an unbuffered 0.1 % NaCl solution yielded an increase of the corrosion rate of rotated low alloy steel probes (average flow rate at the probes: 1m/s) from 2 mm/y to 4 mm/y at 40°C and from 1.5 mm/y to 2.5 mm/y at 90°C, respectively [28]. Thus, the correlation between the corrosion rate of low alloy steels and the CO2 partial pressure is quite complicated and by no means linear. So far there is no model which can predict this correlation satisfactorily. What model would e.g. predict that in 1% unbuffered NaCl at 40 °C an increase of the CO2 pressure from 10 to 95 bar would decrease the corrosion rate of low alloy steels from about 5.5 (10 bar) to 0.5 mm/y (95 bar) [64]. It appears that at high CO2 partial pressures (e.g. >20 bar) the protectivity of iron carbonate films is considerably higher than expected from existing models. This was also found in a series of pH-static experiments with CO2 pressures up to 50 bar [27].Effect of pHThe pH affects the CO2 corrosion of carbon steels by different mechanism. Increased pH values generally lead to a reduction of the corrosion rate by influencing the electrochemical mechanisms and the formation of protective iron carbonate films [29,47,17,56,65]. By an increase of pH the cathodic reduction of H+ is slowed down which decreases the anodic dissolution rate of iron. Furthermore at very high pH values protective carbonate scales are formed on the surface that reduces the corrosion rate significantly [25-26,29]. This is due to the effect of decreasing the solubility of iron carbonate in the solution [29]. In flow loop tests with carbon steels protective scales could only be observed for pH’s greater than 5.0 [26]. In another study it was found that at lower temperatures protective scales are only formed when the pH is increased to values of at least 6 while above 80°C protective scales are easily formed [25]. In multi-phase flow conditions the increase of pH leads to a significant decrease of the corrosion rate of carbon steel due to the formation of protective corrosion product films above pH 6.2 [56]. Another study revealed a decrease in corrosion rate by a factor of 3 with an increase of pH from 3.5 to 5.5 depending on the flow velocity (Fig.7) [29].Brine composition and ion concentrationThe iron content in the corrosive medium is dependent on the anodic reaction mechanisms in CO2 corrosion of steel [66] and the solubility varies with the CO2 concentration, temperature, pH and the concentration of other ions in the solution [67]. The Fe2+ concentration has a large influence on the corrosion rate in CO2 environment given high corrosion rates at low Fe2+ levels [7,65,67]. An increase in iron ion concentration results in higher supersaturation which leads to the precipitation of protective corrosion passive films [34]. In a study at 70°C, 50 ppm Fe2+ could reduce the corrosion rate of carbon steels from 5 mm/y to 2 mm/y at pH 4 by the formation of more protective corrosion films [65].Cations such as Ca2+ and Mg2+ react with carbonic acid and deposit calcium and magnesium carbonates. This codeposition of earth alkali and iron carbonates enhances the scale formation and, hence, reduces the corrosion rates [17]. Ueda et al. found that the corrosion rates of carbon steels in CaCl2 solutions were smaller than those in 5% NaCl + 2,5meq/l NaHCO3 solution with same pH, but the steels showed higher localized attack [17]. Thus, it is not only the pH that commands the protectivity of scales but also its composition. Earlier investigations in the author's lab had shown, that even minor concentrations (e.g. 10-2 mole/L) of earthalkali salts or salts of Zn, Cd, Sn, Pb, and other heavy metal ions would be found accumulated in the corrosion product scale [68].The formation and stability of protective corrosion layers depend heavily on the supersaturation of the bulk solution and hence, any variation in this level of supersaturation could affect the severity of the corrosion [3]. High supersaturation of anions and cations leads to precipitation of a corrosion layer which would reduce the corrosion rate through several kinds of effects [3].Effect of oxygenOxygen in CO2 systems exhibits a strong effect on the corrosion rate and facilitates the formation of localized attack. While this is known for some time only a few papers have been devoted to this problem [69-71]. Martin studied the corrosion consequences of oxygen entry into both sweet and sour systems [71]. He found that the corrosion rate in CO2 system is accelerated in the presence of oxygen by 0.5 mm/y per ppm of oxygen at medium velocity and ambient temperature (Fig. 8). He suggested that the mechanism is consistent with a change in surface corrosion product, which accelerates H2CO3reduction. Investigations of Lyle and Schutt revealed the same relationship between the concentration of O 2 and the general corrosion rate while also pitting was observed [70].Effect of H 2SThe effect of H 2S in CO 2 systems is particularly important because low concentrations of H 2S may arise in otherwise sweet environments, e.g. by microbial influenced reservoir souring. Depending on the concentration, hydrogen sulfide significantly affects CO 2 corrosion by influencing the type and properties of the corrosion film or acting as a promoter of anodic dissolution through sulfide adsorption. At high concentrations H 2S may also affect the pH [3].Below the NACE sour limit of 3 mbar H 2S [72] the composition of the corrosion films depends on the CO 2 /H 2S ratio, the corrosion rates and the temperature [73]. Dunlop et al. [74] suggested ratios which for room temperature allow the estimation of the carbonate and sulfide regime. According to this suggestion the carbonate regime exists when the ratio of the partial pressure of CO 2 and H 2S is above 500, while the sulfide regime is reached when this ratio of partial pressures is below 500. New investigations from Smith and Pacheo [75] resulted in a more precise equation for the calculation of critical constants assuming coexistence of FeCO 3 and all forms of Fe X S Y (Equ. 1 and 2).()()Svap H Svap H aq CO H vap CO vap CO aq CO O H FeCO FeS a K K a K a K 223222223//⋅⋅⋅⋅= (1) Svap H vap CO FeCO FeS a a C K 223/⋅= (2)In Equ. 1 the a values stand for activities or fugacities of the various species in the aqueous or vapor phase (the fugacities often equal corresponding partial pressures) and the K values for equilibrium constants. Equ. 2 is a simplification of Equ. 1 by combining the equilibrium constants into a single constant and making the simplifying assumption that the activity of water is equal to 1.0, to produce an equation that is very similar to the one reported by Dunlop [74].Calculations based on solubility data lead to theoretical CO 2 /H 2S ratios for the transition between FeS and FeCO 3 formation in the range of 105 -107 [73]. Observed CO 2 /H 2S ratios of 1000-5000 have been reported in literature [73,76,77].For worst case calculation of the corrosion rate (CR) of low alloy steel in slightly sour conditions the following Equ. 3 was suggested [75]:17925510848.510]/[⋅⋅⋅=−−pH T e y mm CR (3)The actual corrosion rates will be lower than the rate calculated from Equ. 3 because the equation assumes infinite flow rates. At the transition point between sweet and slightly sour corrosion, the corrosion rate drops as the mechanism shifts from the CO 2-controlled to the slightly sour corrosion mechanism. This has been verified experimentally by Smith and Pacheco when testing the steel。