刀具磨损监测技术的研究现状及发展趋势
刀具磨损监测技术的研究现状及发展趋势

刀具磨损监测技术的研究现状及发展趋势
一、研究现状
截止目前,刀具磨损监测技术已经发展了很长一段时间,从传统试剂盒和一般机械手检测刀具磨损至今,近几十年来出现了很多新技术,从机械方面到电子,从传感器到传感器封装、信号处理,从视觉技术到先进信号处理等,均有重大进展。
近年来,越来越多的研究者将技术运用到刀具磨损的测量上,使得刀具磨损监测技术不仅成为一个研究热点,而且取得了许多飞跃式的进步。
主要包括以下几方面:
(1)传感器技术的发展。
传感器已经发展到可以获得更精确、更稳定、更鲁棒的测量结果,检测刀具磨损程度的精度也越来越高。
例如,电容式传感器、磁性传感器、光电力学传感器等,能有效地测量刀具磨损程度的变化,从而可以更好地确定刀具的磨损程度。
(2)信号处理技术的发展。
由于刀具磨损的过程比较复杂,传感器所采集的原始信号需要进一步加工处理。
传统的数字信号处理技术只能通过低通滤波器、滤波器等方式进行简单的处理,得到的结果不够准确。
近年来,智能信号处理技术,如模糊控制、神经网络等,能够更好地滤除噪声,获得更准确的信号,从而更准确地检测刀具磨损程度。
刀具磨损监测及在线补偿控制技术研究
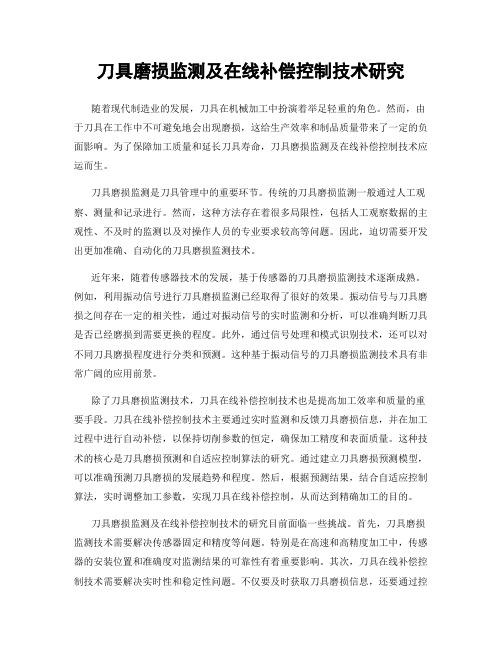
刀具磨损监测及在线补偿控制技术研究随着现代制造业的发展,刀具在机械加工中扮演着举足轻重的角色。
然而,由于刀具在工作中不可避免地会出现磨损,这给生产效率和制品质量带来了一定的负面影响。
为了保障加工质量和延长刀具寿命,刀具磨损监测及在线补偿控制技术应运而生。
刀具磨损监测是刀具管理中的重要环节。
传统的刀具磨损监测一般通过人工观察、测量和记录进行。
然而,这种方法存在着很多局限性,包括人工观察数据的主观性、不及时的监测以及对操作人员的专业要求较高等问题。
因此,迫切需要开发出更加准确、自动化的刀具磨损监测技术。
近年来,随着传感器技术的发展,基于传感器的刀具磨损监测技术逐渐成熟。
例如,利用振动信号进行刀具磨损监测已经取得了很好的效果。
振动信号与刀具磨损之间存在一定的相关性,通过对振动信号的实时监测和分析,可以准确判断刀具是否已经磨损到需要更换的程度。
此外,通过信号处理和模式识别技术,还可以对不同刀具磨损程度进行分类和预测。
这种基于振动信号的刀具磨损监测技术具有非常广阔的应用前景。
除了刀具磨损监测技术,刀具在线补偿控制技术也是提高加工效率和质量的重要手段。
刀具在线补偿控制技术主要通过实时监测和反馈刀具磨损信息,并在加工过程中进行自动补偿,以保持切削参数的恒定,确保加工精度和表面质量。
这种技术的核心是刀具磨损预测和自适应控制算法的研究。
通过建立刀具磨损预测模型,可以准确预测刀具磨损的发展趋势和程度。
然后,根据预测结果,结合自适应控制算法,实时调整加工参数,实现刀具在线补偿控制,从而达到精确加工的目的。
刀具磨损监测及在线补偿控制技术的研究目前面临一些挑战。
首先,刀具磨损监测技术需要解决传感器固定和精度等问题。
特别是在高速和高精度加工中,传感器的安装位置和准确度对监测结果的可靠性有着重要影响。
其次,刀具在线补偿控制技术需要解决实时性和稳定性问题。
不仅要及时获取刀具磨损信息,还要通过控制算法实现切削参数的实时调整,这对算法的复杂度和硬件系统的稳定性提出了更高的要求。
CNC机床加工中的刀具磨损监测与预警技术

CNC机床加工中的刀具磨损监测与预警技术CNC机床是一种应用广泛的数控机床,在工业生产中具有重要的地位。
而刀具磨损是CNC机床加工过程中常见的问题之一,对于保证加工质量和提高生产效率具有直接影响。
因此,刀具磨损监测与预警技术的发展变得至关重要。
一、背景介绍CNC机床是利用计算机数控系统实现精密加工的机床,具有高速、高精度、高自动化等特点。
在CNC机床的加工过程中,刀具是直接与工件接触的部件,承受着巨大的切削力和摩擦力,因此刀具容易出现磨损和断裂的问题。
二、刀具磨损对加工的影响刀具磨损会直接影响加工质量和生产效率。
首先,刀具磨损会导致加工尺寸的偏差,影响工件的精度。
其次,刀具磨损会增加加工过程中的摩擦力和切削力,导致加工温度升高,进而影响加工表面的质量。
此外,刀具磨损还会缩短刀具的使用寿命,增加更换刀具的频率和成本。
三、刀具磨损监测技术的发展为了及时掌握刀具磨损情况,避免因磨损过度而导致的加工质量下降和生产效率降低,刀具磨损监测技术应运而生。
随着传感技术和数据处理技术的不断进步,刀具磨损监测技术也取得了长足的发展。
1. 分析刀具振动信号刀具在加工过程中会产生振动信号,通过分析刀具振动信号的频谱特征,可以获得刀具磨损情况的信息。
一般情况下,刀具磨损会导致切削力的增加,进而引起刀具振动的变化,因此可以通过监测刀具振动信号来判断刀具磨损情况。
2. 利用红外热像技术红外热像技术是一种无接触的测量方法,可以实时监测刀具表面温度的变化。
由于刀具磨损会产生大量的热量,使刀具表面温度升高,通过红外热像技术可以准确地监测到刀具磨损的程度。
3. 应用机器学习算法机器学习是一种人工智能领域的重要技术,可以通过对大量刀具使用数据的分析,建立刀具磨损模型。
利用机器学习算法可以对刀具磨损状态进行监测和预测,提前采取相应的措施。
四、刀具磨损预警技术的应用刀具磨损预警技术可以实时监测刀具磨损情况,并提前预警,以便及时更换刀具或采取修磨等措施,从而避免因刀具磨损引起的加工质量下降和生产效率降低。
刀具磨损的研究现状及发展 论文 曹庆
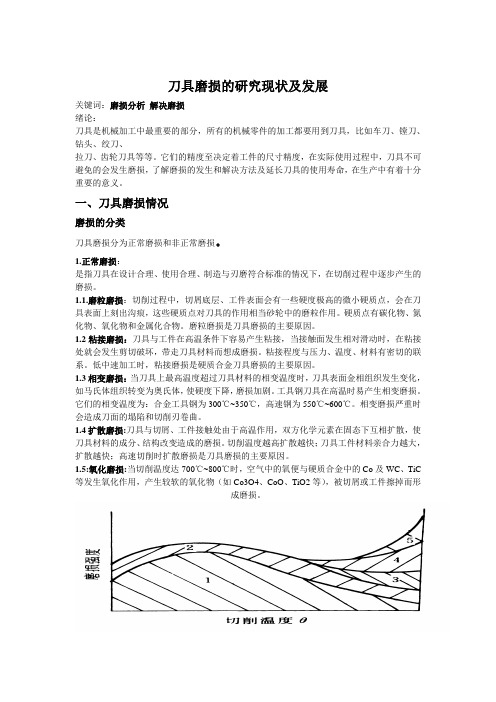
刀具磨损的研究现状及发展关键词:磨损分析解决磨损绪论:刀具是机械加工中最重要的部分,所有的机械零件的加工都要用到刀具,比如车刀、镗刀、钻头、绞刀、拉刀、齿轮刀具等等。
它们的精度至决定着工件的尺寸精度,在实际使用过程中,刀具不可避免的会发生磨损,了解磨损的发生和解决方法及延长刀具的使用寿命,在生产中有着十分重要的意义。
一、刀具磨损情况磨损的分类刀具磨损分为正常磨损和非正常磨损。
1.正常磨损:是指刀具在设计合理、使用合理、制造与刃磨符合标准的情况下,在切削过程中逐步产生的磨损。
1.1.磨粒磨损:切削过程中,切屑底层、工件表面会有一些硬度极高的微小硬质点,会在刀具表面上刻出沟痕,这些硬质点对刀具的作用相当砂轮中的磨粒作用。
硬质点有碳化物、氮化物、氧化物和金属化合物。
磨粒磨损是刀具磨损的主要原因。
1.2粘接磨损:刀具与工件在高温条件下容易产生粘接,当接触面发生相对滑动时,在粘接处就会发生剪切破坏,带走刀具材料而想成磨损。
粘接程度与压力、温度、材料有密切的联系。
低中速加工时,粘接磨损是硬质合金刀具磨损的主要原因。
1.3相变磨损:当刀具上最高温度超过刀具材料的相变温度时,刀具表面金相组织发生变化,如马氏体组织转变为奥氏体,使硬度下降,磨损加剧。
工具钢刀具在高温时易产生相变磨损。
它们的相变温度为:合金工具钢为300℃~350℃,高速钢为550℃~600℃。
相变磨损严重时会造成刀面的塌陷和切削刃卷曲。
1.4扩散磨损:刀具与切屑、工件接触处由于高温作用,双方化学元素在固态下互相扩散,使刀具材料的成分、结构改变造成的磨损。
切削温度越高扩散越快;刀具工件材料亲合力越大,扩散越快;高速切削时扩散磨损是刀具磨损的主要原因。
1.5:氧化磨损:当切削温度达700℃~800℃时,空气中的氧便与硬质合金中的Co及WC、TiC 等发生氧化作用,产生较软的氧化物(如Co3O4、CoO、TiO2等),被切屑或工件擦掉而形成磨损。
温度对磨损的影响1-粘结磨损2-磨粒磨损3-扩散磨损4-相变磨损5-氧化磨损刀具非正常磨损原因2.非正常磨损主要是由于机械冲击力或热效应作用造成的。
刀具磨损监测与预测技术研究

刀具磨损监测与预测技术研究刀具是现代工业生产中不可或缺的工具之一,其质量的好坏直接影响着加工效率和产品质量。
然而,刀具在长时间的使用过程中不可避免地会出现磨损现象,导致其性能下降甚至失效。
因此,刀具磨损监测与预测技术的研究显得尤为重要。
一、刀具磨损的类型与影响因素刀具的磨损主要表现为刀尖磨损和刀面磨损两种类型。
刀尖磨损主要是因为切削速度过高造成的高温烧伤,而刀面磨损主要是由于材料的磨削和冲击引起的。
刀具的磨损程度受到多种因素的影响,在实际加工中往往是多种因素综合作用的结果。
刀具材料的硬度、切削速度、切削力、切削液等都会对刀具磨损产生影响。
二、刀具磨损监测技术的研究现状目前,刀具磨损监测主要有离线和在线两种方式。
离线监测一般是通过拆卸刀具后对其进行人工观察和测量,再根据一定的标准来评估其磨损程度。
虽然这种方法可以在加工过程中搜集到大量的刀具磨损数据,但由于其需要停机检测,导致监测周期长,反应迟缓,部分磨损情况无法及时得到监测。
在线监测则是一种可以在切削过程中通过传感器实时监测刀具磨损情况的方法。
常见的在线监测技术有声发射、振动、电流和红外热像等。
声发射技术通过检测刀具的声波信号变化来判断刀具的磨损程度;振动监测则是通过检测刀具的振动信号来评估其磨损情况;电流监测是通过测量切削电流的变化来判断刀具磨损;红外热像技术则是通过热像仪测量刀具在加工过程中的温度分布来评估其磨损情况。
这些在线监测技术在不同的工况下具有一定的适用性,但仍然存在着监测结果受到外界环境干扰的问题。
三、刀具磨损预测技术的研究进展刀具磨损预测技术是指通过对刀具的历史使用数据进行分析和建模来预测其未来磨损情况的方法。
这种方法可以及时发现刀具的磨损趋势,提前进行刀具的更换或维修,从而保证加工过程的稳定性和效率。
刀具磨损预测技术主要包括基于规则的方法和基于模型的方法。
基于规则的方法主要是通过建立一系列的经验规则,将刀具的使用数据与磨损状态进行对应,利用这些规则来进行刀具磨损预测。
数控车床刀具磨损监测与预警系统研究
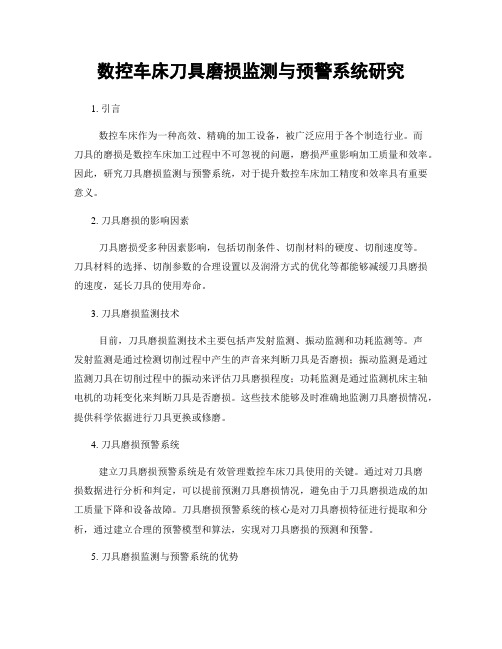
数控车床刀具磨损监测与预警系统研究1. 引言数控车床作为一种高效、精确的加工设备,被广泛应用于各个制造行业。
而刀具的磨损是数控车床加工过程中不可忽视的问题,磨损严重影响加工质量和效率。
因此,研究刀具磨损监测与预警系统,对于提升数控车床加工精度和效率具有重要意义。
2. 刀具磨损的影响因素刀具磨损受多种因素影响,包括切削条件、切削材料的硬度、切削速度等。
刀具材料的选择、切削参数的合理设置以及润滑方式的优化等都能够减缓刀具磨损的速度,延长刀具的使用寿命。
3. 刀具磨损监测技术目前,刀具磨损监测技术主要包括声发射监测、振动监测和功耗监测等。
声发射监测是通过检测切削过程中产生的声音来判断刀具是否磨损;振动监测是通过监测刀具在切削过程中的振动来评估刀具磨损程度;功耗监测是通过监测机床主轴电机的功耗变化来判断刀具是否磨损。
这些技术能够及时准确地监测刀具磨损情况,提供科学依据进行刀具更换或修磨。
4. 刀具磨损预警系统建立刀具磨损预警系统是有效管理数控车床刀具使用的关键。
通过对刀具磨损数据进行分析和判定,可以提前预测刀具磨损情况,避免由于刀具磨损造成的加工质量下降和设备故障。
刀具磨损预警系统的核心是对刀具磨损特征进行提取和分析,通过建立合理的预警模型和算法,实现对刀具磨损的预测和预警。
5. 刀具磨损监测与预警系统的优势数控车床刀具磨损监测与预警系统的应用能够带来诸多优势。
首先,可以减少刀具的过早更换,延长刀具的寿命,降低生产成本。
其次,可以提高加工质量和效率,减少废品率,增加生产效益。
最后,通过实时监测和预警,可以避免因刀具磨损引起的设备故障和生产事故,提高工作安全性。
6. 发展趋势与挑战随着工业自动化和智能化水平的不断提高,数控车床刀具磨损监测与预警系统正迎来新的发展机遇。
然而,仍面临一些挑战。
首先,监测和预警系统的精度需要进一步提高,以适应高精度加工的需求。
其次,系统应具备自适应能力,能够根据不同工况进行实时调整和优化。
CNC机床加工中的刀具磨损监测与诊断系统

CNC机床加工中的刀具磨损监测与诊断系统随着制造业的发展,CNC机床在加工领域的应用越来越广泛。
然而,随着时间的推移,CNC机床上的刀具会出现磨损,这不仅影响加工质量,还会增加生产成本。
因此,开发一种刀具磨损监测与诊断系统,成为解决这一问题的关键。
1. 引言在CNC机床加工中,刀具的磨损无法避免。
当刀具磨损到一定程度时,必须及时更换以保证加工质量。
然而,传统的刀具检查方法需要停机、拆卸和实地观察,效率低且影响生产进度。
因此,开发一种能够实时监测和诊断刀具磨损的系统非常重要。
2. 刀具磨损监测系统的原理及功能2.1 原理刀具磨损监测系统通过安装传感器,实时监测刀具的运行状态和磨损程度。
传感器可以测量刀具的振动、力和温度等参数,将数据传输给监测设备进行分析。
2.2 功能刀具磨损监测系统主要具有以下功能:1) 实时监测刀具的运行状态和磨损程度;2) 提供刀具的寿命预测和更换建议;3) 分析刀具磨损的规律和原因,优化切削参数;4) 提供报警和故障诊断功能,防止刀具磨损导致的生产事故;5) 数据记录和分析,为生产管理和决策提供支持。
3. 刀具磨损监测系统的开发和应用3.1 传感器选择刀具磨损监测系统的核心是传感器,因此在开发过程中,需要选择合适的传感器。
根据刀具特点及加工需求,常用的传感器包括加速度传感器、力传感器和温度传感器等。
根据具体情况,可以选择单一传感器或组合使用。
3.2 数据采集与分析刀具磨损监测系统通过采集传感器数据并进行分析,实现对刀具磨损情况的监测和诊断。
数据采集可以通过有线或无线方式实现,将数据传输给监测设备进行处理。
分析方法可以采用机器学习、模式识别等技术,建立磨损预测模型和故障诊断模型。
3.3 应用实例刀具磨损监测系统已在许多企业中得到应用。
例如,在汽车制造业中,采用该系统能够随时监测车床上的车刀磨损情况,及时更换刀具,从而确保汽车零件的加工质量。
在航天航空领域,刀具磨损监测系统能够提高航空发动机零件的加工精度与效率。
刀具磨损监测与实时补偿控制技术研究

刀具磨损监测与实时补偿控制技术研究刀具磨损监测与实时补偿控制技术研究引言刀具在加工过程中由于摩擦和冲击等作用,会逐渐磨损,进而影响加工质量和效率。
为了保持加工过程的稳定性,需要对刀具的磨损进行监测,并实时进行补偿控制。
本文旨在对刀具磨损监测与实时补偿控制技术进行研究,提出一种可行的解决方案。
一、刀具磨损监测技术1. 监测指标刀具磨损的程度可以通过测量不同参数来评估。
常见的监测指标包括切削力、振动、温度和声音等。
其中,切削力是最常用的监测指标之一,可以通过力传感器进行测量。
振动也是一种常见的监测指标,可以通过加速度传感器进行测量。
温度的变化可以反映刀具的摩擦情况,可以通过红外测温仪或热电偶进行测量。
声音的变化可以反映刀具与工件的摩擦情况,可以通过麦克风进行测量。
2. 监测方法刀具磨损的监测方法多种多样,根据监测指标的不同,可以选择不同的方法。
对于切削力的监测,可以通过牵引力传感器或剪切力传感器进行测量。
对于振动的监测,可以通过加速度传感器或振动传感器进行测量。
对于温度的监测,可以通过红外测温仪或热电偶进行测量。
对于声音的监测,可以通过麦克风进行测量。
此外,还可以使用非接触式的监测方法,如红外摄像头、激光测距仪等。
二、刀具磨损实时补偿控制技术1. 补偿方法刀具磨损的实时补偿方法有多种,根据补偿的原理和方式的不同,可以选择不同的方法。
常见的补偿方法包括刀具半径补偿、刀具长度补偿和刀具补偿。
刀具半径补偿是指根据刀具磨损的情况,自动调整加工程序中的半径值,以保持加工精度。
刀具长度补偿是指根据刀具磨损的情况,自动调整加工程序中的长度值,以保持加工精度。
刀具补偿是指根据刀具磨损的情况,自动调整加工程序中的刀具参数,以保持加工精度。
2. 控制方法刀具磨损的实时补偿控制方法有多种,根据控制的原理和方式的不同,可以选择不同的方法。
常见的控制方法包括开环控制和闭环控制。
开环控制是指根据预先设定的规则或模型,对刀具磨损进行补偿。
- 1、下载文档前请自行甄别文档内容的完整性,平台不提供额外的编辑、内容补充、找答案等附加服务。
- 2、"仅部分预览"的文档,不可在线预览部分如存在完整性等问题,可反馈申请退款(可完整预览的文档不适用该条件!)。
- 3、如文档侵犯您的权益,请联系客服反馈,我们会尽快为您处理(人工客服工作时间:9:00-18:30)。
76
研究与探索Research and Exploration ·监测与诊断
中国设备工程 2019.01 (下)
在制造业中,数控机床发挥着举足轻重的作用。
近年来,随着零件品质要求不断提高,越来越多的零部件需要进行高精密的加工,尤其是在航空航天、汽车、手机等领域,数控机床的发展已成为提高产品质量的关键性因素。
对于数控机床来讲,刀具系统是其最重要的组成部分,它与加工工件的质量有着紧密联系,而刀具的磨损是导致工件质量差,废品率高的直接原因。
有研究指出,五分之一的机床停机是由于刀具系统破损造成的,采用准确可靠的刀具磨损在线监测技术可使机床利用率提高1.5倍,最高提升切削速度50%,并节约30%左右的总加工成本。
因此,对刀具磨损状态的实时监测有助于提高加工环境的稳定性和工件的质量,保障机床及加工人员安全,同时还能提高企业的生产效率、降低企业的生产成本。
因此,发展刀具磨损监测技术有重要的作用。
1 刀具磨损状态监测技术的研究现状
现阶段的刀具磨损监测方法主要分为直接法和间接法。
直接法主要是通过监测刀具磨损面反光强度、刀刃位移情况、切削面放射性、接触电阻及工件尺寸的变化来判断刀具的磨损情况。
而间接法主要是通过监测切削过程中某些与刀具磨损构成映射关系的参数,例如工件温度、超声信号、切削过程的振动信号、切削力、扭矩、电机功率或电流的变化来间接反映刀具的磨损情况。
以下是几种主要的监测方法。
1.1 直接法
(1)光学图谱法:光学图谱法是通过利用光学仪器记录刀具后刀面磨损处的反光强度变化或进行图像处理得到刀具磨损信息的方法。
这类方法的优点是其结果较为明确直观,方便技术人员分析;缺点是在实际生产过程中伴有切削液等切削条件的干扰,很难实现实时监测。
(2)接触法:接触法是通过探头磁间隙传感器检测切削刃的位置参数来得到刀具磨损信息的方法。
这类方法的优点是简便易操作,缺点是其易受切削温度影响。
(3)放电性技术:放电性技术是通过在刀具原材料中加入放射性物质,随着磨损程度的加大,刀具放射
性逐渐加大,从而达到监测目的。
这类方法的优点是其不受加工环境的影响,缺点是其实时性差,应用于实际生产还需考虑防护性问题。
(4)工件尺寸测量法:这类方法通过传感器检测工件的尺寸,根据检测结果与实际工件尺寸误差的大小来判断刀具磨损情况。
但工件的尺寸受机床运动精度和热膨胀的影响,可靠性较低。
1.2 间接测量法
(1)切削温度测量法:切削温度与刀具磨损有着直接联系,因此可通过监测工件与刀具之间的热电偶或用红外检测仪监测切削部位温度变化来实现磨损状态的识别,但这种方法不适用于添加冷却液的加工过程。
(2)声发射监测法:声发射是刀具或被加工器件在加工过程中因裂缝扩展、塑性变形、相变等引起应变能快速释放而产生应力波的现象。
这种方法能在不影响刀具和工件的情况下检测到刀具磨损的特征信号,这些信号频率较高,受环境干扰较小,其缺点是传播过程中信号衰减很快,传感器需安置在接近切削处的位置,且信号处理方式复杂,效率低下。
(3)振动监测法:其通常用加速度计来监测切削过程中振动信号的变化来判断刀具磨损情况,对刀具磨损敏感度高,但其信号易受到机床的自激振动和噪声干扰,给后期判断增加了难度。
(4)切削力监测法:切削力对刀具磨损灵敏度高且作为加工过程中刀具状态变化最直接的表现之一,其信号特征能准确反应刀具的磨损情况。
其缺点是传感器需要与工件有特定的安装位置,信号采集困难,设备昂贵。
2 研究难点及可能的解决方案
从现有刀具磨损监测技术来看,直接法操作性强,能够得到直观数据,避免了复杂的数据分析,但采集数据时容易受到环境干扰,采集数据不可靠,测量精度不高。
而间接法虽然可以采集相对准确的数据,但它并不能直观反映刀具的磨损状态,需建立复杂的数学模型对磨损特征进行提取,过程复杂。
刀具磨损监测技术的研究现状及发展趋势
任泽宇
(浙江 杭州 311200)
摘要:刀具磨损的在线监测有助于提升刀具系统的稳定性和提高工件的加工质量,降低数控机床的故障率,减少故障时间,提高生产效率,对高精度的机械自动化加工有着重要意义。
本文综述了现有的研究现状,并分析了现有技术的研究难点,提出了可能的解决方案,并展望了未来的发展趋势,为刀具磨损监测技术的发展提供了方向和拓展性思路。
关键词:刀具磨损;数控机床;在线监测
中图分类号:TG54;TP311.13 文献标识码:A 文章编号:1671-0711(2019)01(下)-0076-02
77
中国设备
工程
Engineer ing hina C P l ant
中国设备工程 2019.01 (下)
数控机床作为一种高精尖端的加工设备,应用于许多关键性零件的加工,但如果故障发现不及时,会导致工件的报废,人员的人身安全受到威胁,同时降低企业的生产效率,增加企业生产成本。
因此,研究并发展数控机床故障诊断技术不仅对我国数控机床核心技术领域有着重要意义,同时对制造业也有很大的帮助。
1 数控机床故障诊断技术的研究现状
数控机床故障诊断主要面临着以下几个问题:故障位置不明显且难以发现,容易出现误诊;加工环境复杂,获得故障信息繁复,机床发生故障概率高;现阶段机床故障诊断知识不完备等。
目前主要的故障诊断方法
数控机床故障诊断技术的
研究现状及未来的发展趋势
张瑞浠
(四川 成都 610200)
摘要:数控机床在整个制造业中有着举足轻重的地位,同时也是自动化加工产业的重要组成部分。
如果机床因故障而停止运转,将会降低企业生产效率并给企业带来巨大的损失,而研究数控机床故障诊断技术可对机床运转状态进行实时监测,并对机床故障进行及时预判,挽回企业损失,提高产品加工质量。
本文综述了现有数控机床故障诊断技术的研究现状,分析了他们的研究难点及可能的解决方案,并对其未来发展方向进行展望,为数控机床故障诊断技术提供新的研究思路。
关键词:数控机床;故障诊断;综述
中图分类号:TG659 文献标识码:A 文章编号:1671-0711(2019)01(下)-0077-02
目前刀具磨损监测的主流方法还是以间接测量法为主,而其中以振动监测法,声发射监测法和切削力监测法最为流行。
但是针对单一的传感器监测并不能全面和准确的反映刀具磨损的特征信息,因此不能同时兼有高敏感性、高容错性和高可靠性的优点,无法适应实际加工环境。
对此问题,可通过多传感器监测来协调单独传感器失灵或由于某些噪声干扰造成传感器的误判,最后综合多来源刀具磨损信息使刀具磨损状态识别可靠准确。
其次,传感器安装位置需尽可能靠近工件,但由于受加工环境以及刀具的干涉,传感器的安装往往不能安装在刀具较靠近工件的位置,因此,可将传感器集成在刀体或夹具上,以提高采集数据的准确性。
3 未来的发展趋势
未来是工业自动化的时代,数控加工是未来制造
业的重中之重,而刀具磨损的在线监测是整个加工链实现自动化的关键环节,但刀具磨损监测技术目前的研究还只是偏重于理论,局限于小样本的试验和小规模的加工,同时也只适用于简单的加工工艺和简单的走刀路线,并不适合复杂的曲面加工,也不能普遍运用于整个加工产业链。
因此,未来的刀具磨损在线监测应从以下几方面着手。
(1)发展多传感器融合技术,使之更能准确的采
集可靠磨损信息。
(2)发展智能刀体,将传感器、驱动装置、控制装置、微型计算机等集成在刀体或刀头上,以提高采集磨损数据的准确性和高效性,并通过高性能处理器及时分析磨损特征,识别磨损状态,以达到对刀具磨损状态的实时监测。
(3)可以将传感器和整个机床融为一体,例如可将传感器制作成夹具,使其兼有采集数据和装夹工件的功能,这样对于任意的加工工艺,都可以监测刀具的磨损信息。
参考文献:
[1]王国峰,李志猛,懂毅.刀具状态智能监测研究进展[J].航空制造技术,2018,61(6):16-23.
[2]王燕山,胡飞,张海菊,刘德峰,黄漫国,刘伟.智能制造中的在线监测技术[J].测控技术,2018,37(5):4-5.[3]KURADAS,BRADLEYC.Areviewofmachinevisionsensorsfortoolc onditionmonitoring[J].ComputersinIndustry,1997,34(1):55-72.[4]崔云先,张博文,刘义,祁洋.智能切削刀具发展现状综述[J].大连交通大学学报,2016,37(6);10-13.
[5]汤为.基于声发射法的铣刀磨损状态识别研究[D].上海交通大学,2009,(2):2-5.
[6]揭景耀.智能刀具状态监测系统研究与进展,中国机械工程[J].中国机械工程,1997,8(6):60-62.。