锅炉燃烧调整与各项指标的控制措施
供暖锅炉的燃烧调节与节能范本

供暖锅炉的燃烧调节与节能范本供暖锅炉是很多家庭和企事业单位的主要供暖设备,如何调节供暖锅炉的燃烧以实现节能是一个重要的课题。
本文将介绍供暖锅炉的燃烧调节与节能的一些范本和措施。
一、优化燃料选择优化燃料选择是实现供暖锅炉节能的第一步。
在选择燃料时,应选择高效、环保的燃料,如天然气、液化石油气等清洁燃料,避免使用高污染、低效的燃料,如煤炭等。
清洁燃料的燃烧过程中产生的废气减少,热能利用效率提高,从而节能减排。
二、优化燃烧调节优化燃烧调节是提高供暖锅炉热能利用效率的关键。
以下是一些燃烧调节的范本和措施:1. 燃烧空气预热:采用空气预热装置,将燃烧用的空气预先加热到一定温度,可以增加燃烧温度,提高燃烧效率,降低燃料消耗。
2. 过量空气系数控制:过量空气系数是指实际燃烧所需要的空气量与理论所需空气量之间的比值。
过量空气系数过大,会导致燃料浪费和燃烧不完全。
通过调节供暖锅炉的空气进入量,控制过量空气系数,可以实现燃烧的最优化。
3. 排烟温度控制:排烟温度是供暖锅炉燃烧的一个重要参数,也是衡量燃烧效率的一个指标。
燃烧过程中,如果排烟温度过高,说明热量未能充分吸收,意味着燃烧效率较低,热量浪费较多。
通过控制排烟温度,可以实现燃烧效率的提高。
4. 燃料喷射方式优化:供暖锅炉的燃料喷射方式会影响燃烧的均匀性和热量传输效果。
优化燃料喷射方式,可以改善燃烧气流的流动性和均匀性,提高热量传输效果,实现燃烧效率的提升。
5. 燃料比例控制:对于多燃料供暖锅炉,燃料的比例控制是非常重要的。
通过合理的燃料比例控制,可以实现各种燃料的最优利用,节约燃料消耗。
三、燃烧控制系统升级燃烧控制系统是供暖锅炉燃烧调节和控制的核心部分,升级燃烧控制系统可以改善燃烧效率,实现节能减排。
1. 火焰检测与监控技术:利用先进的火焰检测与监控技术,可以实时监测燃烧情况,掌握燃烧过程的动态数据,及时发现和调整燃烧异常情况,保证燃烧的稳定和高效。
2. 氧气含量监测:通过对燃烧过程中氧气含量的监测,可以实时调整燃烧空气进入量,控制燃烧过程的过量空气系数,以达到最佳燃烧效果。
锅炉燃烧器排烟量的控制与优化
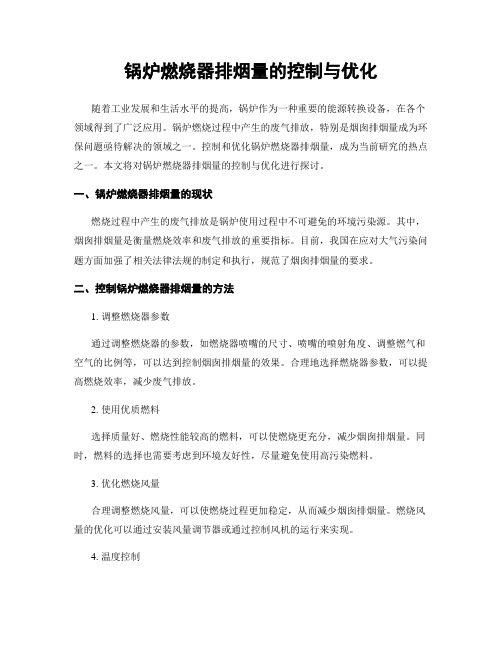
锅炉燃烧器排烟量的控制与优化随着工业发展和生活水平的提高,锅炉作为一种重要的能源转换设备,在各个领域得到了广泛应用。
锅炉燃烧过程中产生的废气排放,特别是烟囱排烟量成为环保问题亟待解决的领域之一。
控制和优化锅炉燃烧器排烟量,成为当前研究的热点之一。
本文将对锅炉燃烧器排烟量的控制与优化进行探讨。
一、锅炉燃烧器排烟量的现状燃烧过程中产生的废气排放是锅炉使用过程中不可避免的环境污染源。
其中,烟囱排烟量是衡量燃烧效率和废气排放的重要指标。
目前,我国在应对大气污染问题方面加强了相关法律法规的制定和执行,规范了烟囱排烟量的要求。
二、控制锅炉燃烧器排烟量的方法1. 调整燃烧器参数通过调整燃烧器的参数,如燃烧器喷嘴的尺寸、喷嘴的喷射角度、调整燃气和空气的比例等,可以达到控制烟囱排烟量的效果。
合理地选择燃烧器参数,可以提高燃烧效率,减少废气排放。
2. 使用优质燃料选择质量好、燃烧性能较高的燃料,可以使燃烧更充分,减少烟囱排烟量。
同时,燃料的选择也需要考虑到环境友好性,尽量避免使用高污染燃料。
3. 优化燃烧风量合理调整燃烧风量,可以使燃烧过程更加稳定,从而减少烟囱排烟量。
燃烧风量的优化可以通过安装风量调节器或通过控制风机的运行来实现。
4. 温度控制合理控制燃烧工艺中的温度,可以提高燃烧效率,减少废气排放。
通过控制燃烧温度,可以使燃烧更充分,减少烟囱排烟量。
三、锅炉燃烧器排烟量优化的挑战与解决1. 技术挑战锅炉燃烧器排烟量优化面临一系列技术挑战。
首先,不同类型的锅炉燃烧器的结构和工作原理各不相同,因此需要根据具体情况制定相应的烟囱排烟量优化方案。
其次,废气排放涉及到燃烧过程中涉及的多个参数,如燃料、燃气与空气的比例、燃烧温度等,需要进行复杂的计算和调整。
2. 环境限制为了减少锅炉燃烧器排烟量,需要合理控制燃烧参数和优化燃烧工艺,但在实际操作中需要考虑到环保要求和排放标准的限制。
因此,烟囱排烟量的控制与优化需要根据不同地区和不同行业的排放标准来确定。
锅炉各项小指标控制措施及注意事项
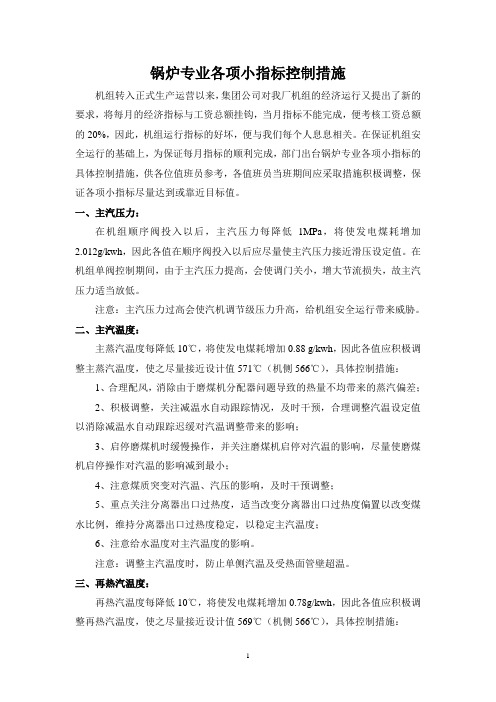
锅炉专业各项小指标控制措施机组转入正式生产运营以来,集团公司对我厂机组的经济运行又提出了新的要求,将每月的经济指标与工资总额挂钩,当月指标不能完成,便考核工资总额的20%,因此,机组运行指标的好坏,便与我们每个人息息相关。
在保证机组安全运行的基础上,为保证每月指标的顺利完成,部门出台锅炉专业各项小指标的具体控制措施,供各位值班员参考,各值班员当班期间应采取措施积极调整,保证各项小指标尽量达到或靠近目标值。
一、主汽压力:在机组顺序阀投入以后,主汽压力每降低1MPa,将使发电煤耗增加2.012g/kwh,因此各值在顺序阀投入以后应尽量使主汽压力接近滑压设定值。
在机组单阀控制期间,由于主汽压力提高,会使调门关小,增大节流损失,故主汽压力适当放低。
注意:主汽压力过高会使汽机调节级压力升高,给机组安全运行带来威胁。
二、主汽温度:主蒸汽温度每降低10℃,将使发电煤耗增加0.88 g/kwh,因此各值应积极调整主蒸汽温度,使之尽量接近设计值571℃(机侧566℃),具体控制措施:1、合理配风,消除由于磨煤机分配器问题导致的热量不均带来的蒸汽偏差;2、积极调整,关注减温水自动跟踪情况,及时干预,合理调整汽温设定值以消除减温水自动跟踪迟缓对汽温调整带来的影响;3、启停磨煤机时缓慢操作,并关注磨煤机启停对汽温的影响,尽量使磨煤机启停操作对汽温的影响减到最小;4、注意煤质突变对汽温、汽压的影响,及时干预调整;5、重点关注分离器出口过热度,适当改变分离器出口过热度偏置以改变煤水比例,维持分离器出口过热度稳定,以稳定主汽温度;6、注意给水温度对主汽温度的影响。
注意:调整主汽温度时,防止单侧汽温及受热面管壁超温。
三、再热汽温度:再热汽温度每降低10℃,将使发电煤耗增加0.78g/kwh,因此各值应积极调整再热汽温度,使之尽量接近设计值569℃(机侧566℃),具体控制措施:1、保持燃烧稳定,积极调整烟气挡板开度,注意再热汽温的变化趋势,做到超前调节;2、合理利用燃尽风;3、启停磨煤机时缓慢操作,并关注磨煤机启停对再热汽温的影响,尽量使磨煤机启停操作对再热汽温的影响减到最小;4、注意给煤量突变及一次风压改变对再热汽温的影响;5、改变煤粉细度,提高火焰中心有利于提高再热汽温。
锅炉燃烧优化调整技术

2)掺冷风量对排烟温度影响
②运行控制磨煤机出口温度偏低 按照《电站磨煤机及制粉系统选型导则》(DL/T 466-
2004)规定的磨煤机出口温度,见表1。 锅炉设计时热风温度的选择主要取决于燃烧的需要; 所选定的热风温度往往高于所要求的磨煤机入口的干
燥剂温度,因此要求在磨煤机入口前掺入一部分温度 较低的介质; 运行中磨煤机出口温度控制的越低,则冷一次风占的 比例越大,即流过空预器的风量流量降低,这样引起 排烟温度升高。
➢ 排烟热损失主要取决于排烟温度与排烟氧量 (过剩空气系数)
➢ 排烟热损失是锅炉各项热损失中最大的 (5%~7%);
➢ 排烟温度每升高10℃.排烟损失约增加0.5%~ 0.7%);机组发电煤耗升高约1.7 ~2.2 g/kWh。
➢ 过高的排烟温度,对锅炉后电除尘及脱硫设备 的安全运行也构成威胁。
烟气余热利于系统图
~180
贫煤 130 烟煤、褐煤 70
褐煤 90 烟煤 120
烟煤 70~75 褐煤 70 Vdaf≤15%的煤 100
当Vdaf<40%时,tM2=[(82-Vdaf)×5/3±5] 当Vdaf≥40%时,tM2<70
高热值烟煤<82,低热质烟煤<77,次烟煤、褐煤 <66
备注:燃用混煤的,可允许tM2较低的相应煤种取值;无烟煤只受设备允许 温度的限制
W火焰燃烧方式
➢ 无烟煤这种反应特性极低的煤种 (可燃基挥发分低于10%),
➢ 采用“W”火焰的燃烧方式,通过 提高炉膛的热负荷,延长火焰行程 等手段来获得满意的燃烧效果。
左侧墙
右侧墙
燃尽风口
燃烧器
➢ ➢
前后墙对冲燃烧方式 ➢
沿炉膛宽度方向热负荷分布均匀 过热器、再热器区炉宽方向的烟温 分布更加均匀 燃烧器具有自稳燃能力
燃气锅炉的燃烧控制及其方法

燃气锅炉的燃烧控制及其方法燃气锅炉是一种常见的供暖系统,它通过燃烧燃气来产生热量,从而为居住空间提供温暖。
然而,关于燃气锅炉的燃烧控制问题,很多人并不是很清楚。
本文将对燃气锅炉的燃烧控制及其方法进行探讨。
一、燃气锅炉的燃烧控制燃气锅炉的燃烧控制是指通过控制燃气的供应量、气体混合比、燃气流量、气体压力等参数,确保锅炉在燃烧过程中达到最佳状态,从而提高能源利用效率,减少能源浪费,延长设备寿命,降低排放浓度,保护环境等目的。
燃气锅炉燃烧控制主要包括三个方面:点火控制、燃烧控制和安全控制。
点火控制:燃气锅炉在启动前需要进行点火操作,即将燃气与空气混合后进行点火。
点火控制的目的是确保燃气与空气的混合比例正确,点火过程安全可靠。
燃烧控制:燃气锅炉的燃烧控制是指通过调节燃气与空气混合比例、燃气流量、进气压力、燃气预热温度等参数来调整锅炉的燃烧效率和排放浓度。
例如,燃气与空气的混合比例过高,会导致燃烧不完全,浪费能源;混合比例过低,则会导致燃烧不稳定,影响锅炉的使用寿命。
安全控制:燃气锅炉的安全控制包括燃气泄漏报警、氧气浓度检测、水位保护、过热保护等措施。
这些控制措施能够及时发现和解决可能存在的安全隐患,保障设备和人员的安全。
二、燃气锅炉的燃烧优化方法除了上述控制措施外,还有一些燃烧优化方法可以帮助提高燃气锅炉的能源利用效率。
1、氧气浓度控制:在锅炉燃烧过程中,通过控制氧气浓度来调整燃气和空气的混合比例。
在保证燃烧效率的同时,能够减少废气排放量达20%以上。
2、锅炉辅助设施优化:燃气锅炉还需要配套一些辅助设施,如送风机、废气处理装置等。
这些设施的优化能够减少能源浪费和环境污染程度。
3、锅炉清洗:锅炉内部容易积累灰尘等污物,影响热能传递。
定期对锅炉进行清洗和维护,能够提高燃烧效率,降低能源消耗。
4、锅炉负荷控制:通过调整锅炉的负荷来控制燃烧效率。
如果锅炉负荷过低,则会造成燃气浪费;如果负荷过高,则会影响锅炉寿命。
锅炉燃烧调整与各项指标的控制措施
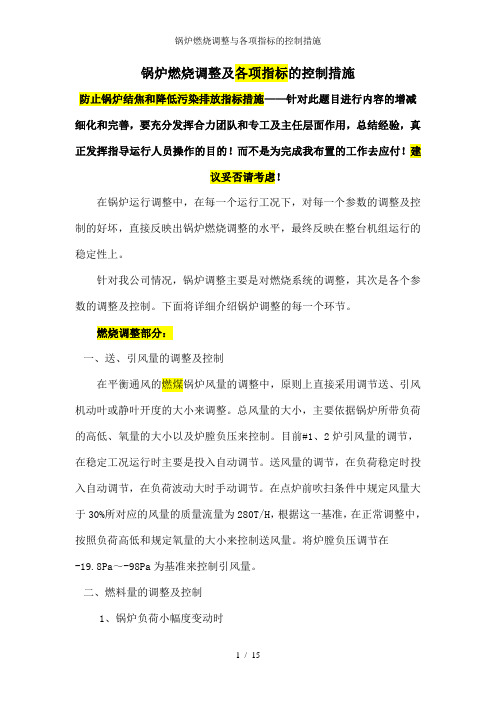
锅炉燃烧调整及各项指标的控制措施防止锅炉结焦和降低污染排放指标措施——针对此题目进行内容的增减细化和完善,要充分发挥合力团队和专工及主任层面作用,总结经验,真正发挥指导运行人员操作的目的!而不是为完成我布置的工作去应付!建议妥否请考虑!在锅炉运行调整中,在每一个运行工况下,对每一个参数的调整及控制的好坏,直接反映出锅炉燃烧调整的水平,最终反映在整台机组运行的稳定性上。
针对我公司情况,锅炉调整主要是对燃烧系统的调整,其次是各个参数的调整及控制。
下面将详细介绍锅炉调整的每一个环节。
燃烧调整部分:一、送、引风量的调整及控制在平衡通风的燃煤锅炉风量的调整中,原则上直接采用调节送、引风机动叶或静叶开度的大小来调整。
总风量的大小,主要依据锅炉所带负荷的高低、氧量的大小以及炉膛负压来控制。
目前#1、2炉引风量的调节,在稳定工况运行时主要是投入自动调节。
送风量的调节,在负荷稳定时投入自动调节,在负荷波动大时手动调节。
在点炉前吹扫条件中规定风量大于30%所对应的风量的质量流量为280T/H,根据这一基准,在正常调整中,按照负荷高低和规定氧量的大小来控制送风量。
将炉膛负压调节在-19.8Pa~-98Pa为基准来控制引风量。
二、燃料量的调整及控制1、锅炉负荷小幅度变动时调节原则:通过调节运行着的制粉系统的出力来进行。
调节过程(以少量加负荷为例)1)在给煤量不变的情况下,首先将A磨煤机的调整做为燃烧稳定的基础,然后通过适当开B、C磨煤机容量风门开度来调整负荷,调整时不要大幅度开容量风门,根据负荷情况,可单侧或双侧调整,调整幅度控制在2%开度左右,调整后,密切注意汽包压力或主汽压力以及氧量的变化趋势,如果压力上升快,可适当对单侧容量风门回调来进行控制。
2)在各台磨煤机容量风门开至40-45%时,此时应根据磨煤机料位及电流情况,来增加给煤量,根据长时间观察,每台磨煤机给煤量最稳定工况出力在54-56T/H之间,在掺烧劣质煤(如金生小窑煤)时,出力在48-50T/H之间。
电厂锅炉的燃烧优化和运行调整分析
电厂锅炉的燃烧优化和运行调整分析在锅炉的运行中,时常发生锅炉偏离最佳工况的现象,所以须根据实际情况讨论锅炉燃烧系统的优化控制运行问题.。
电厂锅炉运行时要保证满足外界负荷对锅炉蒸发量和蒸汽参数的要求,同时保护锅炉本体及附属设备不受损坏.。
因此,加强电厂锅炉设备运行与维护管理,不断对锅炉的燃烧进行优化,有利于提高电厂的生产效率,降低电厂的生产成本,从而提高电厂的经济效益.。
本文主要通过讨论燃烧优化的目的和意义,从而指出其存在的问题,并提出锅炉燃料量控制调整,锅炉燃烧送风量的调整,引风控制系统优化,以及燃用劣质烟煤的调整等优化和运行调整的方法.。
关键词:燃烧优化;火电厂;锅炉;运行调整当前我国经济开始向集约型方向发展,这也对电厂锅炉燃烧的安全性、经济性和环保性提出了更高的要求.。
锅炉燃烧过程中,燃料在炉膛中燃烧会释放大量的热能,这些热能经过金属壁面传热使锅炉中的水转化为过热蒸汽,这些蒸汽被送入到汽轮机中,从而驱动汽轮机进行发电.。
通过对锅炉燃烧运行进行优化,可以有效的提高锅炉燃烧的效率,降低锅炉燃烧过程中所带来的污染,实现节能减排的目标.。
1 燃烧优化的目的和意义煤粉燃烧在我国大型电厂锅炉上的应用十分广泛.。
燃烧优化实际上就是在满足安全运行和外界负荷要求的前提,提高燃燒效率、减少锅炉热损失,同时减少污染物的排放.。
锅炉通过燃烧和传热将燃料的化学能转化为蒸汽的热能.。
锅炉效率是其能量转换的重要经济性指标,一般来说,对于大型火力发电机组,锅炉效率每提高1%,整套机组的效率可以提高0.3-0.4%,供电煤耗可以降低0.7-1%.。
而锅炉效率又与炉内的燃烧工况密切相关,组织好炉内的燃烧,可以有效地提高锅炉效率,实现机组的高效运行.。
锅炉燃烧优化控制系统的最终目的是在保持锅炉自身设备运行参数的情况下,使锅炉燃烧处于最佳运行工况,降低热量损失,提高热能效率,并通过运行人员在线实时的调整各项参数,来降低含碳量和再热器超温问题.。
19.9.24 防止锅炉炉膛温度低的燃烧调整措施
防止锅炉炉膛温度低的燃烧调整措施一、防止垃圾干燥不够、风量使用不配平,造成炉排主料区堆料、燃烧不良低温。
(一)正常调整。
1、干燥风量、燃I段风量、燃II-1风量与通过炉排上的垃圾量应配平,即有多少垃圾、要配有多少的风量,同时平时保证燃II-1足够风量、以燃II-1为主燃区,保持其总体相对较高的风量,防止燃II-1垃圾过多或堆料。
2、控制垃圾品质:垃圾吊、锅炉主操、值长平时加强沟通,了解垃圾状况,及时配料。
(二)遇到垃圾换区、底部垃圾、垃圾较湿情况,提前预控。
1、首先适时控制合理偏薄的料厚(稍薄有助于炉排片、料层本身风量穿透),便于风量穿透性相对较好、达到良好干燥:换区、底部垃圾或料垃圾湿度大的情况,干燥段、燃I段周期与推料器的比率应控制:1#炉(0.28~0.33、0.28~0.34)、2#炉(0.24-0.26、0.24-0.27)进行调整,尽量往下限靠;若给料器一个周期内推的垃圾量(即给料器推一把的量)明显增加,则比率应往下限靠,防止干燥段、燃I段越来越多、越来越厚。
2、其次尽快、尽量提高风温,干燥段、燃I段周期改变后,适时根据进料情况及时、尽量提高风温,及时调整干燥段、燃I段风量,但风量不宜过大也不宜过小,要保证足够的干燥能力和适当提高干燥段、燃I段燃烧份额以防止堆料。
3、维持主燃区足够风量,干燥段、燃I段周期比例往下限靠后,垃圾总体往后铺长,故燃II-1的风量也要适当提高以保证及时燃掉,防止燃II-1越堆越多。
4、合理料位,换区、底部垃圾、料垃圾湿度大的垃圾,垃圾斗料位应控制稍偏低些,建议在2.0~3.5米之间即可,以保证给料器每次推料量稳定且偏少一些。
二、异常情况下的处理措施(一)高风温:及时开大或全开一次蒸预器进汽门、尽力提高一次风温,越高越好。
1、当炉膛二次风截面四个温度平均低于980℃或中部任一低至890℃或中上部任低于880℃并有下降趋势,一次风温应控制在165℃以上。
2、当炉膛二次风截面四个温度平均低于970℃或中部任一低至880℃或中上部任低于870℃并有下降趋势,一次风温应控制在185℃以上,否则全开一、二级一次风蒸预器进汽调门并检查疏水畅通。
锅炉燃烧调整与控制
锅炉燃烧调整与控制摘要:自备电厂自投产以来,三台锅炉均不同程度的频繁出现煤粉管道堵塞、渣量大、灰渣含碳量高、制粉系统出力降低等现象,直接导致的结果是煤耗偏高,尤其是在2011年年底和2012年年初,均未完成厂部下达的煤耗指标。
为此,发电运行部针对上述现象,专门组织人员进行燃烧调整和分析,以彻底查清问题产生的原因,并提出解决措施,提高锅炉运行的经济性。
关键词:燃烧;调整;措施中图分类号:tm73 文献标识码:a文章编号:1009—0118(2012)10—0244—01一、主要问题描述三台锅炉及制粉系统在运行过程中主要存在以下问题:(一)炉底渣量较大,含碳量高,炉渣中含大颗粒原煤;(二)分离器调节叶片被杂物堵塞,回粉管堵塞杂物较多,锁气器频繁动作或不动作;(三)煤粉管道堵塞严重;(四)分离器出口压力偏高;(五)制粉系统出力降低;(六)发电标煤耗较高。
二、调整目的针对三台炉出现的共性问题,通过对锅炉及制粉系统调整和设备治理,达到以下目的:(一)查找锅炉渣量大、灰渣含碳量高的原因;(二)通过查看分离器调节叶片堵塞情况、锁气器动作频率、制粉系统运行周期,确定分离器需要清理时的出口压力高值;(三)明确防止煤粉管道堵塞的措施;(四)查找制粉系统处理降低的原因;(五)总结出制粉系统出力降低时表现出来特征;(六)总结出磨煤机旁路风开大、关小对磨煤机出力的影响。
三、原因分析及治理措施(一)原因分析为达到上述目的,根据锅炉运行、制粉系统设备定期清理工作和运行人员反映的情况,经过发电运行部分析,认为产生主要原因有以下几点:1、原煤中杂物较多,堵塞分离器调节叶片,回粉量增大,导致回粉管堵塞或常开,同时磨煤机处理降低。
2、为提高磨煤机出力,运行人员增大一次风量或旁路风量,分离器出口压力增高,煤粉细度增大,同时携带大颗粒原煤进入煤粉管道,导致管道堵塞、燃烧不完全、灰渣含碳量增大。
3、在煤质较差的情况下,磨煤机出力大于50吨时,为了增加或稳定机组负荷,继续增大磨煤机出力,使分离器出口压力增高、管道堵塞。
锅炉飞灰、炉渣残碳控制指标及调整
锅炉飞灰、炉渣残碳控制指标及调整1.引言1.1 概述概述部分的内容可以按照以下方式来撰写:锅炉是一种广泛应用于工业生产和居民生活的热能设备,其燃烧产生的飞灰和炉渣残碳是锅炉运行过程中的常见问题。
锅炉飞灰和炉渣残碳的控制对于提高锅炉燃烧效率、减少污染物排放以及延长锅炉使用寿命具有重要意义。
锅炉飞灰是指燃烧过程中由于燃料不完全燃烧或物料质量问题而未燃尽的颗粒状物质。
它们经过锅炉烟道系统排出后,常常会对环境造成污染。
另外,飞灰还会附着在锅炉热交换器表面上,形成结渣,影响热传递效率,降低锅炉的工作效率。
因此,控制锅炉飞灰含量对于提高能源利用效率和保护环境具有重要意义。
炉渣残碳是锅炉燃烧过程中产生的固体残渣,一般由燃料中的矿物质在高温条件下反应生成。
炉渣残碳会附着在锅炉炉膛和烟道系统内,增加了烟道系统的阻力,降低了热传递效率,同时还会导致炉渣层的剥落和腐蚀,进一步影响锅炉的安全和经济运行。
因此,炉渣残碳的控制对于提高锅炉燃烧效率和延长锅炉寿命非常重要。
本文通过对锅炉飞灰和炉渣残碳的控制指标进行研究和分析,旨在为锅炉运行和维护人员提供相关的理论和技术支持。
在实践中,通过合理调整锅炉的燃烧参数和操作方式,采取适当的措施来控制飞灰和炉渣残碳的生成和排放,以提高锅炉的燃烧效率、保护环境和延长设备使用寿命。
随着环保意识的提高和能源资源的稀缺,锅炉飞灰和炉渣残碳的控制问题越来越受到重视。
通过对飞灰和炉渣残碳的研究,能够为锅炉的运行管理提供依据,进一步促进锅炉技术的进步和能源利用的提高。
接下来的章节将会详细介绍锅炉飞灰控制指标和炉渣残碳控制指标的研究现状、影响因素和调整方法,以及对未来的展望和建议。
通过深入研究和探讨,相信能够为锅炉飞灰、炉渣残碳的控制提供有益的参考和指导,为锅炉的安全、高效运行做出贡献。
1.2 文章结构文章结构在本篇文章中,我们将重点讨论锅炉飞灰和炉渣残碳的控制指标以及相应的调整方法。
文章分为三个主要部分:引言、正文和结论。
- 1、下载文档前请自行甄别文档内容的完整性,平台不提供额外的编辑、内容补充、找答案等附加服务。
- 2、"仅部分预览"的文档,不可在线预览部分如存在完整性等问题,可反馈申请退款(可完整预览的文档不适用该条件!)。
- 3、如文档侵犯您的权益,请联系客服反馈,我们会尽快为您处理(人工客服工作时间:9:00-18:30)。
锅炉燃烧调整与各项指标的控制措施防止锅炉结焦和降低污染排放指标措施——针对此题目进行内容的增减细化和完善,要充分发挥合力团队和专工及主任层面作用,总结经验,真正发挥指导运行人员操作的目的!而不是为完成我布置的工作去应付!建议妥否请考虑!在锅炉运行调整中,在每一个运行工况下,对每一个参数的调整与控制的好坏,直接反映出锅炉燃烧调整的水平,最终反映在整台机组运行的稳定性上。
针对我公司情况,锅炉调整主要是对燃烧系统的调整,其次是各个参数的调整与控制。
下面将详细介绍锅炉调整的每一个环节。
燃烧调整部分:一、送、引风量的调整与控制在平衡通风的燃煤锅炉风量的调整中,原则上直接采用调节送、引风机动叶或静叶开度的大小来调整。
总风量的大小,主要依据锅炉所带负荷的高低、氧量的大小以及炉膛负压来控制。
目前#1、2炉引风量的调节,在稳定工况运行时主要是投入自动调节。
送风量的调节,在负荷稳定时投入自动调节,在负荷波动大时手动调节。
在点炉前吹扫条件中规定风量大于30%所对应的风量的质量流量为280T/H,根据这一基准,在正常调整中,按照负荷高低和规定氧量的大小来控制送风量。
将炉膛负压调节在-19.8Pa~-98Pa为基准来控制引风量。
二、燃料量的调整与控制1、锅炉负荷小幅度变动时调节原则:通过调节运行着的制粉系统的出力来进行。
调节过程(以少量加负荷为例)1)在给煤量不变的情况下,首先将A磨煤机的调整做为燃烧稳定的基础,然后通过适当开B、C磨煤机容量风门开度来调整负荷,调整时不要大幅度开容量风门,根据负荷情况,可单侧或双侧调整,调整幅度控制在2%开度左右,调整后,密切注意汽包压力或主汽压力以及氧量的变化趋势,如果压力上升快,可适当对单侧容量风门回调来进行控制。
2)在各台磨煤机容量风门开至40-45%时,此时应根据磨煤机料位及电流情况,来增加给煤量,根据长时间观察,每台磨煤机给煤量最稳定工况出力在54-56T/H之间,在掺烧劣质煤(如金生小窑煤)时,出力在48-50T/H之间。
此时可适当提高一次风压来调整负荷。
3)在煤质差,顶压困难时,采取以上方法无法提高或维持负荷时,可采取调大大矿煤比例来提高入炉煤综合发热量,此时应特别监视和调整给煤量较少或给煤机停运侧的分离器出口温度,不得超过85℃。
2、锅炉负荷大幅度变动时调节原则:通过启、停一套层制粉系统来进行调节。
最低允许出力:取决于制粉的经济性和燃烧的稳定性。
当负荷低于一定程度时,应停掉一套运一层制粉系统,将它的出力分摊给其余运行着的制粉系统。
最大允许出力:取决其碾磨能力以及所要求的煤粉细度。
当负荷升高到一定程度时,应重新启动一套制粉系统,以分散各磨煤机的出力,同时分散炉内热负荷。
调节过程(以大量加负荷为例)1)当单台给水泵运行,运行磨煤机出力达到最大或负荷加至220MW以上时,首先启动一台给水泵,然后启动备用磨煤机运行,同时适当降低另两台磨煤机出力,以分散炉膛内过高的局部热负荷。
2)当两台给水泵运行时,直接启动备用磨煤机运行。
三汽压的调整与控制1、汽压调整的原则1)当外界负荷变化引起主汽压力变化时,通过增减燃烧工况的方法进行调节。
2)若由于锅炉燃烧原因引起的主汽压力波动,应立即查明原因,稳定锅炉燃烧;3)主汽压力超压后,应及时降低燃料量;当汽压继续升高达到PCV整定值时(18.13MPa),PCV打开泄压。
当压力达到安全门动作压力而安全门拒动时,应立即手动MFT停炉,严防锅炉超压。
2、汽压的调整是以改变锅炉蒸发量作为基本的调节手段,只有当锅炉蒸发量超出允许值或其他特殊情况发生时,采用增减汽轮机负荷的方法来调节汽压。
对于汽包锅炉,锅炉蒸发量的改变可以通过对燃烧工况的调节来实现。
四汽温的调整与控制1、正确使用减温水系统:在正常运行监视和调整的过程中,减温水系统应投入自动方式。
在监盘过程中随时监视过热器一、二级减温器前、后蒸汽温度的变化趋势,正常时一级减温器前的温度在391℃左右,减温器后温度在450℃左右。
二级减温器前温度在508℃左右。
如果这几个温度出现快速或不正常变化,此时应及时采用改变自动偏置或切手动来进行调节一、二级减温水流量的大小,以控制进入分隔屏过热器和高温过热器的蒸汽温度不至于过高,以使主汽温度能控制在额定范围。
2、燃烧器摆角的使用:原则上采用燃烧器摆角来主要调整再热汽温,但在实际运行中,摆角摆动过大或频繁摆动,对炉内燃烧动力工况影响很大。
因为,在做冷态动力场试验时,假想切圆的位置和大小的确定是在燃烧器摆角处在水平位置时调整的各层风速。
在热态运行时,随意大幅度或频繁改变摆角角度,直接影响炉内燃烧工况,极易造成烟气气流的无规律变化,使得汽温发生大幅度波动。
所以在运行中尽量保持摆角在水平位,再热汽温过高时,尽量小幅度向下摆动,然后采取别的办法来调节。
3、运行中出现异常情况:汽温超标时一定要果断处理,当即立断采取必要的手段,调整幅度可大,尽力减小汽温超限幅度保证机组运行安全。
当汽温超过540℃时一定要超前进行操作,及时果断采取一切必要手段进行调节,如一、二级减温水调门全开。
其它手段均采取后炉侧汽温高至550℃,且仍有上升趋势时,立即停止C2层粉或停止C磨运行且及时降低风量,加强燃烧调整,在此过程中一定要以汽温为重严禁存在侥幸心理而延误时机。
五:磨煤机的启、停操作1、启动磨煤机的操作1)在一台或两台磨煤机运行的情况下,需要启动另一台或两台磨煤机时,在检查过程中,燃烧调整值班员进行操作,逐一满足磨煤机启动条件,在“开启一次风总风门”和“分离器出口挡板开”这两条件时,严密监视和调整一次风总风压保持基本稳定,以防止风压突然变化对运行磨煤机造成过大的影响。
根据负荷及烟温情况,先调整好各层二次风。
根据氧量情况,调整送风量。
调整汽温的值班员有意识调整汽温有缓慢下降趋势。
2)在启动条件全部满足后(喷燃器最好对角开启),及时启动磨煤机。
3)磨煤机启动后,根据加负荷情况启动单侧或双侧给煤机并建立料位。
然后开启热风门至20-30%,开启投粉侧旁路门至30%,容量风门至5%左右,未投粉侧旁路风开至5%,保证分离器出口风压及一次风速。
4)根据压力和汽温变化情况,逐步单个投入另外的同层喷燃器。
及时调整热风门开度至50%,根据分离器出口温度调整冷风门。
然后根据压力上升情况及时调整运行磨煤机的给煤量和容量风门。
5)根据汽温情况,单个投入另一层喷燃器,并及时调整旁路风门至30%,容量风门至5%。
直至全部投入喷燃器。
6)开大热风门至70%,调整冷风门和旁路风门,以满足通风量和分离器出口温度及一次风速合适,然后缓慢开启两侧容量风门。
7)根据负荷和压力情况,调整各台磨煤机出力,以达到各台磨煤机出力基本平衡。
8)在启动和调整磨煤机过程中,及时监视和调整一次风压力保持基本稳定,在磨煤机启动正常后,根据煤质及负荷、脱硫效率情况适当调整各台给煤机给煤量及一次风总风压。
2、停止磨煤机的操作在正常情况下的操作:1)减小单侧或双侧给煤机给煤量至最小(6T/H),关闭给煤机上闸板。
2)给煤机皮带上原煤走空后,停止给煤机运行。
3)在磨煤机抽粉过程中,根据分离器出口温度,缓慢关闭热风门,开启冷风门。
4)根据负荷及压力情况,适当调整运行磨煤机出力。
5)待停磨煤机抽粉15-25分钟(根据料位情况)存粉抽完后,缓慢关闭冷风门至10%,停止待停磨煤机。
同时调整一次风总风压,保证负荷及压力基本稳定。
6)磨煤机停止后,开启一个或两个分离器出口挡板(停止前可以先挂禁操),用以泄去磨煤机和分离器内风压。
7)磨煤机停止后,根据氧量调整风量,调整二次风门至合适位置。
8)磨煤机停止后,继续监视其油系统运行情况及各部温度变化情况,发现不正常时及时采取措施进行处理。
紧急情况下的操作:1)某台磨煤机发生故障时,直接采取“紧急停止磨煤机”按钮对磨煤机进行停止。
并及时对其进行冲惰,以防止磨煤机因存粉而发生自燃或爆炸。
2)在燃烧调整稳定后,必须对停止磨煤机各一次风管进行彻底吹扫,防止一次风管内自燃。
掺配煤及控制炉内结焦部分:公司#1、2机组投产以来,锅炉结焦问题一直困扰着每一位领导及员工的心,公司及运行部领导针对这一情况,专门成立了热试小组进行掺配煤和燃烧调整。
对煤场制定了管理制度。
在燃料供应紧张,入厂煤来煤复杂的实际情况下,通过近一年的努力和摸索试验,通过对设备的不断调试,收集数据,总结经验,目前基本掌握了掺配煤的方式和掺烧比例,炉内结焦问题得到了有效地改善。
入厂煤情况:大矿煤以新疆煤为主,主要有望布#1、#3、柳沟北山、柳沟北塔山、柳沟三道岭、准东、小黄山#1、#7、低窝铺、鄯善、柳树泉和鹏远煤等,各个矿点大矿煤煤质含硫份、发热量、灰熔点等有很大差别。
小窑煤主要是右旗、金生、华隆和煤泥。
存煤分区堆放根据煤场存煤,经过长时间的配煤掺烧以及炉内燃烧工况的调整与观察,总结出适合入炉煤掺烧方式如下:1) 望布#1+准东+煤泥2)望布#1+煤泥+金生3)望布#1+唐家沟+煤泥4)小黄山#7+唐家沟+煤泥5)柳沟北山+唐家沟+煤泥6)柳沟北塔山+望布#1+唐家沟+煤泥7)柳沟三道岭+煤泥8)柳沟三道岭+准东+煤泥+金生9)鹏远+小黄山#1+煤泥10)鹏远+唐家沟+金生+小黄山#1在每日配煤计划单中掺烧方式中,每一种煤的参考掺烧比例很重要,每一种掺烧煤量的多少均是通过计算和实践经验而得来。
如果在调整中偏离太大,会造成炉膛内结焦以及脱硫效率降低。
这是因为在配煤时,对煤质指标进行了综合考虑和计算后得到的给煤量。
如燃煤加权平均收到基硫(St,ar)在1.25%以下时,脱硫塔入口烟气含硫量可以控制在2826Mg/Nm³以下,脱硫效率控制在90%以上。
灰熔点(ST)在1200 ℃以上时,炉内结焦可能性大大降低。
综合发热量在17.2-18.5MJ/KG时,炉膛整体温度可以控制在1320-1380℃左右,机组带负荷能力强。
掺配比例及煤粉细度方面通过实际掺烧情况,总结出不适合掺烧煤种有望布#3、小黄山#1和柳沟北塔山,尤其是小黄山煤种不易入炉燃烧。
小窑煤中,华隆和金生掺烧时,脱硫效率难以控制。
排放量的调整与控制部分NOx、CO、SO2超标排放将收取排污费,为实现环保型、节约针对目前环保要求,NOx SO2型电力生产,根据近期调整试验情况,确保锅炉的安全、稳定、低NOx、CO、SO2运行,总结出如下调整与控制措施。
一、NOx的成分及形成机理:NO x包括N2O、NO、N2O3、NO2、N2O4、N2O5,大气中NO x主要以NO、NO2的形式存在,氮氧化物(NOX)种类很多,造成大气污染的主要是一氧化氮(NO)和二氧化氮(NO2),因此环境学中的氮氧化物一般就指这二者的总称。
在氮氧化物中,NO占有90%-95%,二氧化氮占5%-10%。