多面反射镜的超精密切削
超精密切削加工技术探析
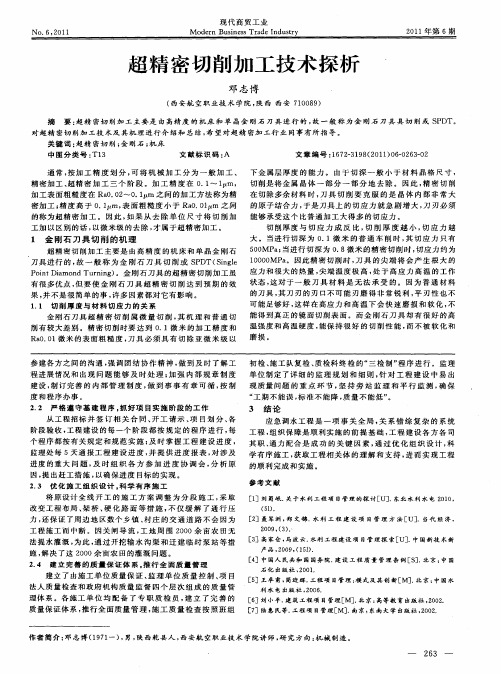
用 的 区 域 ) 是 加 工 单 位 , 工 单 位 的 大 小 和 材 料 缺 陷 分 布 切 削 刃钝 圆 圆 弧 上 某 一 质 点 A 的受 力 情 况 见 图 。该 点 有 切 就 加 的尺 寸 大 小 不 同 时 , 加 工 材 料 的 破 坏 方 式 就 不 同 。 被 向分 力 F 和 法 向 分 力 F , 力 为 F , 。切 向 分 力 使 质 点 z y合 yZ 向前 移 动 , 成 切 屑 ; 向 分 力 使 质 点 压 向 被 加 工 表 面 , 形 法 形 2 超精 : 精 密 切 削加 工 主 要 是 由 高精 度 的 机 床 和 单 晶 金 刚 石 刀 具 进 行 的 , 一 般 称 为金 刚 石 刀 具 具 切 削 或 S D 超 故 P T。
对 超 精 密 切 削加 工 技 术 及 其 机 理 进 行 介 绍 和 总 结 , 望 对 超 精 密加 工 行 业 同事 有 所 指 导 。 希
21 年第 6 01 期
1 2 材 料 缺 陷 及 其 对 超 精 密 切 削 的 影 响 .
2 2 金 刚 石 刀 具 超 精 密 车 削 的切 屑 形 成 . 金 刚 石 刀 具 超 精 密 车 削 是 一 种 原 子 、 子 级 加 工 单 位 分 金刚石 刀具超精密车削所 能切 除金 属层 的厚度 标志其 的去 除 ( 离 ) 工 方 法 , 从 工 件 上 去 除 材 料 , 要 相 当 大 加 工 水 平 。 当 前 , 小 切 削 深 度 可 达 0 1微 米 以 下 , 主 要 分 加 要 需 最 . 其 的能 量 , 种 能 量 可 用 临 界 加 工 能 量 密 度  ̄ J c ) 单 位 影 响 因素 是 刀 具 的锋 利 程 度 , 般 以 刀 具 的 切 削 刃 钝 圆 半 这 (/ m3 和 一
第2章超精密切削与金刚石刀具详解
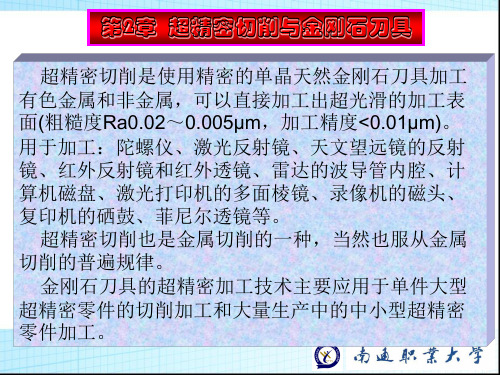
• 1)极高的硬度、极高的耐磨性和极高的弹性模量。 • 2)刃口能磨得极其锋锐,刃口半径值极小,能实现超薄切削厚度。 • 3)刀刃无缺陷,切削时刃形将复制在被加工表面上,从而得到超光滑的 镜面。 • 4)与工件材料的抗粘性好、化学亲和性小、摩擦系数低,以得到极好的 加工表面完整性。 • 不可替代的超精密切削刀具材料:单晶金刚石。
刃口半径为0.6μm、0.3μm
刃口锋锐度对加工表面有一 定的影响,相同条件下(背 吃刀量、进给量),更锋锐 的刀具切出的表面粗糙度更 小;速度的影响不是很大。
2.4 刀刃锋锐度对切削变形和加工表面质量的影响
二、刀刃锋锐度对切削变形和切削力的影响
锋锐车刀切削变形系数明显低于 较钝的车刀。 刀刃锋锐度不同,切削力明显不 同。刃口半径增大,切削力增大, 即切削变形大。背吃刀量很小时, 切削力显著增大。因为背吃刀量很 小时,刃口半径造成的附加切削变 形已占总切削变形的很大比例,刃 口的微小变化将使切削变形产生很 大的变化。所以在背吃刀量很小的 精切时,应采用刃口半径很小的锋 锐金刚石车刀。
2.7 刀具的要求及金刚石的性能和晶体结构
二、金刚石晶体的性能
• • • • 硬度最高,各向异性,不同晶向的物理性能相差很大。 优质天然单晶金刚石:多数为规整的8面体或菱形12面体,少数为6面立方体 或其他形状,浅色透明,无杂质、无缺陷。 大颗粒人造金刚石在超高压、高温下由子晶生长而成,并且要求很长的晶体 生长时间。 人造单晶金刚石已用于制造超精密切削的刀具。
2.3 切削参数变化对加工表面质量的影响
一、切削速度、进给量、修光刃和背吃刀量的影响
3、修光刃的影响
修光刃长度常取0.05~ 0.20mm。 修光刃的长度过长,对 加工表面粗糙度影响不 大。 修光刃有直线和圆弧两 种,加工时要精确对 刀,使修光刃和进给方 向一致。圆弧刃半径一般 取2~5mm。
精密和超精密加工技术复习思考题答案
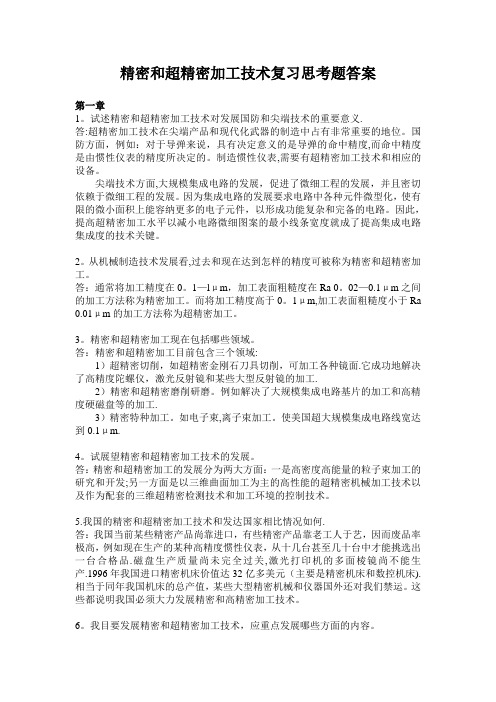
精密和超精密加工技术复习思考题答案第一章1。
试述精密和超精密加工技术对发展国防和尖端技术的重要意义.答:超精密加工技术在尖端产品和现代化武器的制造中占有非常重要的地位。
国防方面,例如:对于导弹来说,具有决定意义的是导弹的命中精度,而命中精度是由惯性仪表的精度所决定的。
制造惯性仪表,需要有超精密加工技术和相应的设备。
尖端技术方面,大规模集成电路的发展,促进了微细工程的发展,并且密切依赖于微细工程的发展。
因为集成电路的发展要求电路中各种元件微型化,使有限的微小面积上能容纳更多的电子元件,以形成功能复杂和完备的电路。
因此,提高超精密加工水平以减小电路微细图案的最小线条宽度就成了提高集成电路集成度的技术关键。
2。
从机械制造技术发展看,过去和现在达到怎样的精度可被称为精密和超精密加工。
答:通常将加工精度在0。
1—lμm,加工表面粗糙度在Ra 0。
02—0.1μm之间的加工方法称为精密加工。
而将加工精度高于0。
1μm,加工表面粗糙度小于Ra 0.01μm的加工方法称为超精密加工。
3。
精密和超精密加工现在包括哪些领域。
答:精密和超精密加工目前包含三个领域:1)超精密切削,如超精密金刚石刀具切削,可加工各种镜面.它成功地解决了高精度陀螺仪,激光反射镜和某些大型反射镜的加工.2)精密和超精密磨削研磨。
例如解决了大规模集成电路基片的加工和高精度硬磁盘等的加工.3)精密特种加工。
如电子束,离子束加工。
使美国超大规模集成电路线宽达到0.1μm.4。
试展望精密和超精密加工技术的发展。
答:精密和超精密加工的发展分为两大方面:一是高密度高能量的粒子束加工的研究和开发;另一方面是以三维曲面加工为主的高性能的超精密机械加工技术以及作为配套的三维超精密检测技术和加工环境的控制技术。
5.我国的精密和超精密加工技术和发达国家相比情况如何.答:我国当前某些精密产品尚靠进口,有些精密产品靠老工人于艺,因而废品率极高,例如现在生产的某种高精度惯性仪表,从十几台甚至几十台中才能挑选出一台合格品.磁盘生产质量尚未完全过关,激光打印机的多面棱镜尚不能生产.1996年我国进口精密机床价值达32亿多美元(主要是精密机床和数控机床).相当于同年我国机床的总产值,某些大型精密机械和仪器国外还对我们禁运。
国外超精密数控机床概述

国外超精密数控机床概述20世纪50年代后期,美国首先开始进行超精密加工机床方面的研究,当时因开发激光核聚变实验装置和红外线实验装置需要大型金属反射镜,急需反射镜的超精密加工技术和超精密加工机床。
人们通过使用当时精度较高的精密机床,采用单点金刚石车刀对铝合金和无氧化铜进行镜面切削,以此为起点,超精密加工作为一种崭新的机械加工工艺得到了迅速发展。
1962年,Union Carbide公司首先开发出的利用多孔质石墨空气轴承的超精密半球面车床,成功地实现了超精密镜面车削,尺寸精度达到士0.6 um,表面粗糙度为Ra0.025um,从而迈出了亚微米加工的第一步。
但是,金刚石超精密车削比较适合一些较软的金属材料,而在航空航天、天文、军事等应用领域的卫星摄像头方面,最为常用的却是如玻璃、陶瓷等脆性材料的非金属器件。
用金刚石刀具对这些材料进行切削加工,则会使己加工表面产生裂纹。
而超精密磨削则更有利于脆性材料的加工。
Union Carbide公司的另一代表性产品是其在1972年研制成功的R-0方式的非球面创成加工机床。
这是一台具有位置反馈的双坐标数控车床,可实时改变刀座导轨的转角0和半径R,实现非球面的镜面加工。
加工直径达380mm,工件的形状精度为士0.63um,表面粗糙度为Ra0.025 um。
摩尔公司(Mood Special Tool)于1968年研制出带空气主轴的Moori型超精密镜面车床,但为了实现脆性材料的超精密加工,该公司又于1980年在世界上首次开发出三坐标控制的M-18AG型超精密非球面金刚石刀具车削、金刚石砂轮磨削机床。
该机床采用空气主轴,回转精度径向为0.075pm;采用Allen-Braley 7320数控系统;X,Z 轴行程分别为410mm和230mm,其导轨的平直度在全长行程范围内均在0.5um以内,B轴的定位精度在3600范围内是0.38um;采用金刚石砂轮可加工最大直径为356mm的各种非球面的金属反射镜。
金属反射镜超精密加工研究进展

摘 要:金属反射镜已经成为光学系统主反射镜的发展方向和趋势ꎬ金属反射镜的超精密加工已经成为当代科技前 沿的关键支撑技术ꎮ 主要对国内外金属反射镜超精密加工研究进展进行综合评述ꎮ 评述了单点金刚石车削、光学冷 加工、复制法对面形精度和光学性能的影响ꎬ从材料方面研究了材料物理特性、工件表面镀层和快速冷凝制造合金对 超精密加工表面质量和光学性能的影响ꎮ 最后对这些加工方法分析对比优缺点ꎬ并对金属反射镜超精密加工的技术 发展愿景进行了展望ꎮ 关键词:金属反射镜ꎻ超精密加工ꎻ研究进展 中图分类号:TH74 文献标志码:A 文章编号:1007-4414(2018)01-0159-05
0 引 言
超精密加工技术在国防建设与国民经济发展中 具有不可替代的作用ꎬ它是现代高技术战争的重要支 撑技术ꎬ也是现代基础科学技术发展的重要保障ꎬ从 某种意义上说ꎬ超精密加工技术是衡量一个国家科技 实力的重要标志之一[1] ꎮ 单点金刚石车削 ( SPDTꎬ single point diamond turning) 技术作为超精密加工技 术的一个典型代表ꎬ具有良好的可控性ꎬ不仅可以获 得亚微米级的形状精度ꎬ还可以获得纳米级的表面粗 糙度ꎬ因而成为加工精密光学元器件最重要的方法之 一ꎮ 目前ꎬ大口径反射镜已成为光学系统主反射镜的 发展方向和趋势ꎬ并广泛应用于空间光学、天文观察、 高功率激光技术等领域ꎮ 因此ꎬ大口径反射镜的制造 已经成为当代科技前沿的关键支撑技术ꎮ 随着口径
加大ꎬ对制造工艺提出了更大挑战ꎮ 单点金刚石超精 密车削大口径金属反射镜时ꎬ由于多方面因素交互作 用ꎬ使得已加工表面非常容易出现缺陷( 例如划伤、 麻点、波纹等) ꎬ 导 致 无 法 完 全 满 足 光 学 系 统 的 性 能 要求ꎮ 如果被加工表面缺陷能够得到有效控制ꎬ则对 未来超大口径反射式光学系统的发展具有重要军事 意义、经济意义和社会意义ꎮ
超精密切削加工技术介绍

超精密切削加工技术介绍
超精密加工技术是适应现代高科技的需要而发展起来的先进制造技术, 是高科技尖端产品开发中不可或缺的关键技术, 是一个国家制造业水平重要标志, 是先进制造技术基础和关键, 也是装备现代化不可缺少的关键技术之一, 在军用和民用工业中有着十分广阔的应用前景。
金刚石超精密切削技术, 是超精密加工技术发展最早的、应用最为广泛的技术之一。
超精密切削加工技术
1、超精密切削的历史
60年代初,由于宇航用的陀螺,计算机用的磁鼓、磁盘,光学扫描用的多面棱镜,大功率激光核聚变装置用的大直径非圆曲面镜,以及各种复杂形状的红外光用的立体镜等等,各种反射镜和多面棱镜精度要求极高,使用磨削、研磨、抛光等方法进行加工,不但加工成本很高,而且很难满足精度和表面粗糙度的要求。
为此,研究、开发了使用高精度、高刚度的机床和金刚石刀具进行切削加工的方法加工。
2、超精密切削加工的应用
(1)平面镜的切削
平面度
金刚石刀具
1、金刚石刀具特点
金刚石刀具拥有很高的高温强度和硬度,而且材质细密,经过精细研磨,切削刃可磨得极为锋利,表面粗糙度值很小,因此可进行镜面切削。
金刚石刀具超精密切削主要用于加工铜、铝等有色金属,如高密度硬磁盘的铝合金基片、激光器的反射镜、复印机的硒鼓、光学平面镜,凹凸镜、抛物面镜等。
超精切削刀具材料有天然金刚石,人造单晶金刚石。
金刚石刀具磨损的常见形式为机械磨损和破损。
机械磨损——机械摩擦、非常微小;破损。
国外超精密数控机床概述

国外超精密数控机床概述20世纪50年代后期,美国首先开始进行超精密加工机床方面的研究,当时因开发激光核聚变实验装置和红外线实验装置需要大型金属反射镜,急需反射镜的超精密加工技术和超精密加工机床。
人们通过使用当时精度较高的精密机床,采用单点金刚石车刀对铝合金和无氧化铜进行镜面切削,以此为起点,超精密加工作为一种崭新的机械加工工艺得到了迅速发展。
1962年,Union Carbide公司首先开发出的利用多孔质石墨空气轴承的超精密半球面车床,成功地实现了超精密镜面车削,尺寸精度达到士0.6 um,表面粗糙度为Ra0.025um,从而迈出了亚微米加工的第一步。
但是,金刚石超精密车削比较适合一些较软的金属材料,而在航空航天、天文、军事等应用领域的卫星摄像头方面,最为常用的却是如玻璃、陶瓷等脆性材料的非金属器件。
用金刚石刀具对这些材料进行切削加工,则会使己加工表面产生裂纹。
而超精密磨削则更有利于脆性材料的加工。
Union Carbide公司的另一代表性产品是其在1972年研制成功的R-0方式的非球面创成加工机床。
这是一台具有位置反馈的双坐标数控车床,可实时改变刀座导轨的转角0和半径R,实现非球面的镜面加工。
加工直径达380mm,工件的形状精度为士0.63um,表面粗糙度为Ra0.025 um。
摩尔公司(Mood Special Tool)于1968年研制出带空气主轴的Moori型超精密镜面车床,但为了实现脆性材料的超精密加工,该公司又于1980年在世界上首次开发出三坐标控制的M-18AG型超精密非球面金刚石刀具车削、金刚石砂轮磨削机床。
该机床采用空气主轴,回转精度径向为0.075pm;采用Allen-Braley 7320数控系统;X,Z 轴行程分别为410mm和230mm,其导轨的平直度在全长行程范围内均在0.5um以内,B轴的定位精度在3600范围内是0.38um;采用金刚石砂轮可加工最大直径为356mm的各种非球面的金属反射镜。
答案精密加工课后习题—黄

.
.
液压喷砂法,用高压泵打出流量为20L/min、压力为150Pa的冷却液,进入喷嘴的漩涡室时,形成低压,从
边孔中吸入碳化硅或刚玉等磨粒及空气,与冷却液形成混合液,并以高速喷嘴喷射到转动的砂轮上。
晶面。
网面最小单元不同,100是正方形,110为矩形,111为三角形,网面密度100:110:111为1:1.414:2.308
网面距不同:100与110为均匀分布,分别为D/4=0.089mm,sqrt(2)D/4=0.126mm,111为宽窄交替宽为
sqrt(3)D/4=0.154mm,窄为sqrt(3)D/12=0.1051mm
光刃的长度对表面加工质量效果不大,对刀不易
圆弧刃容易对刀,半径可取R=2~5mm。可加工高质量的超光滑表面,缺点是刀具制造复杂
2-19试述金刚石刀具的前面应选哪个晶面
选用100面,111面硬度高,而微观破损强度并不高,研磨加工困难。
选用100面的原因:
1)100面耐磨性高于110面,刀具使用寿命长
2)100面微观破损强度高于110面,产生崩刃的机会小
解理现象:111面的面网宽面距比100和110都大,最易解理。
好磨难磨方向可用图表示:
.
.
好磨方向
难磨方向
100磨削率:111磨削率:110磨削率=5.8:1:12.8
2-15金刚石晶体有哪些定向方法?
1)人工目测定向2)X射线定向3)激光定向
2-16试述金刚石晶体的激光定向原理和方法。
利用金刚石在不同晶面方向上,晶体结构不同,对激光反射形成的衍射图像不同而进行。
小后面与加工表面间的摩擦
2-10工件材料的晶体方向对切削变形和加工表面质量的影响如何?
- 1、下载文档前请自行甄别文档内容的完整性,平台不提供额外的编辑、内容补充、找答案等附加服务。
- 2、"仅部分预览"的文档,不可在线预览部分如存在完整性等问题,可反馈申请退款(可完整预览的文档不适用该条件!)。
- 3、如文档侵犯您的权益,请联系客服反馈,我们会尽快为您处理(人工客服工作时间:9:00-18:30)。
多面反射镜的超精密切削一、多面反射镜过去多面反射镜只用作测量角度的标准光学元件,在一般情况下,是用它作为测量回转工作台分度精度的角度标准。
随着科学技术的发展,多面反射镜的用途也在不断地扩大,目前广泛地用于激光扫描的装置中,即让多面反射镜高速回转,使照射在多面反射镜上的激光束进行扫描。
利用多面反射镜制作的激光扫描装置用途很广,例如在激光打印机上使激光通过多面反射镜在感光鼓筒上进行扫描,而实现高速印刷。
除此之外,还在检查轧制钢板的表面缺陷及检查胶片等的缺陷,零件、物品等的识别,用a岛激光淬火、焊接等装置上都要使用多面反射镜。
在上述的各种用途中,以用在激光打印机上的多面反射镜精度最高、最有代表性。
图7-20所示是激光打印机的原理图。
多面反射镜是构成激光打印机的核心零件,只有多面反射镜的精度高,反射率高,打印机才能有高的析像度,像汉字、画像这样复杂的图像才能高速地印刷。
因此要求多面反射镜的几何形状精度高,反射镜面的粗糙度R。
值低。
图7—21所示是激光打印机用多面反射镜的技术要求。
从图中225可以看出,镜体的平行度和平面度精度均为0.5f,tm,镜面的角度误差在1“~y,而镜面所要求的粗糙度为R,0.01,ttm,平面度要求为A/5~2/10(Ne—Ni激光A=0.682 8『』m)c在一般情况下,作为激光反射镜必须满足的加工精度是:形状精度(平面度)低于0.1“m,表面粗糙度R。
0.01弘m,表面反射率大于85%,而且没有散乱光和衍射光。
过去因多面反射镜形状复杂,对几何形状精度和表面粗糙度的要求很高,故多采用研磨的方法进行加工。
图7—22为其工艺路线,因为加工工艺复杂,效率较低,所以成本很高。
近来由于多面反射镜用途的不断扩大,用研臃方法进行加工已远远满足不了要求,因而开发了丹j 铜及铜铝系合金等软金属以及塑料等材料,采用金刚石刀具超精密切削加工出多面反射镜的技术,其工艺路线见图7-23。
加工多面反射镜采用超精密切削与采用研磨相比,可以看出:采用超精密切削,工艺路线大大地l一感光滚筒:2一激比发振器;3~数字信号:4一电fi十算机;5一变调器;6-一激光束放大器;7一多【酊反射镜;8一壤焦透镜。
缩短,减少了热处理、电镀等工序;不会在被加工表面上残留有磨料,也不会出现研磨时常有的塌边现象;可以批量生产,因而成本低。
近年来通过大量的试验研究,采用金刚石刀具的超精密切削方法,不仅可以加工像多面反射镜这样较小的反射镜面,而且还可以加工各种平面镜、球面镜、非球面镜和透镜等大直径的镜面。
尽管采用金刚石刀具切削加工镜面有许多优点,但因这还是个新技术,无论是在加工机床、金刚石刀具的形状角度、被加工材料的可加工性、切削方法、切削条件、镜面的评价方法等方面,还存在许多问题需进一步深入地研究和探讨.二、多面反射镜加工机床及其特点切削加工是基于机床的复映原则进行的。
要得到镜面和必要的几何形状精度,就必须有相应高的机床精度和性能。
多面反射镜的加工机床是按第二章第六节所介绍的各种超精密加工用的各部件组合而成的。
回转主轴与直线运动导轨均采用空气静压轴承支承。
国外有一种金刚石刀具切削力U_-L多面反射镜用的机床,它有两个正变并单独驱动的高精度空气静压回转主轴。
左边的主轴为装夹工件(多面镜)用,它可以按多面镜的分度要求进行精确分度。
右边的主轴用于安装金刚石刀具,它具有精确的进给和走刀机构。
用这种机床切削加工的庐40mm,厚度8mm的八面体铝合金反射镜。
面积为15.3ram×8rnm的各镜面的平面度均可低于0.2”m,粗糙度值低于R。
0.02,urn。
所用的时间仅为用研磨加工的数十分之一。
另一种超精密切削多面反射镜专用机床的回转主轴采用超精密球面空气轴承支承。
导轨为超精密直线运动空气静压支承导轨。
它是加工激光打印机用多面反射镜的专用加工机床,以铣削方式进行加工。
其铸铁床身具有很高的结构刚度,在其上安装具有双V型导轨的床鞍。
由床鞍进行吃刀进给和定位。
安装工件的工作台可以直线运动,采用空气静压支承。
工件的走刀、进给通过介于驱动装置之间的空气静压联轴器来实现。
工件装在特制的多齿盘分度:【作台上,其分度精度为l”。
刀具安装在刀具主轴的刀盘上。
主轴采用球面空气静压主轴,刀盘上装有两个金刚石刀具,它可以精确地调整刀尖高度,使一个刀具进行粗加工,另一个刀具进行精加工,即粗、精加工同时进行。
机床的全部操作均集中在操作台上。
此外,还有切削用的喷雾装置和切屑、尘雾的收集装置等。
在此机床上可以加工内切圆及庐30~4,200mm的多面反射镜。
反射镜的面数可以由多齿分度盘确定,面数不限,可以自由选择。
为了能成批、稳定地切削加工出合格的多面反射镜,不仅机床本身要有足够的精度,足够的刚度、热稳定性和排除机床内部的振动装置,而且对环境也有严格的要求。
为了得到长时间的热稳定性,必须把机床设置在恒温间里。
要用空气弹簧隔断外部的振源,同时也要求供给空气静压轴承和导轨的空气温度和压力稳定。
三、金刚石刀具及其调整镜面加工用的金刚石刀具,不仅要仔细地选择制作刀具的金刚石原料及其结晶方位,而且刀具的切削刃要锋利,不允许有缺损。
刀具前刀面和后刀面均不允许有研磨的条痕。
切削反射镜面的金刚石刀具有两种:用于粗加工的刀具刀尖半径小,通常为5~lOmm;用于精加工的刀具刀尖半径大,刀尖半径大于760ram或为直线切削刃刀具。
刀尖半径小(5~lOmm)的刀具调整容易,由于挤光量小和切削力小,所以因切削而产生的残留应力也小,可以得到高平面度的表面。
另外在刀具磨损的情况下,可以使刀具的切削点错开,从而延长刀具的使用寿命。
但是因为刀尖半径小,要想得到没有切削条痕、没有衍射和散乱光的表面,将是很困难的。
刀尖半径大或直线切削刃刀具,如果刀具的位置调整得适当,由于挤光效应,可以得到没有切削条痕的良好镜面。
但要正确地调整刀具的位置,使其处于良好的切削状态是很棘手的问题,必须有丰富的切削经验才能很好地掌握它。
刀具半径大或直线切削刃刀具,切削力大,工具的调整状态和切削刃的锋利性,将影响切削表面的平面度。
而且由于挤压而产生的残留应力,也将使平面度变坏。
综上所述,镜面切削所用的刀具在很大程度上决定了被切削表面状态。
为了得到没有衍射光和散乱光的镜面,夹持刀具的夹具应具有很好的微调机构。
根据经验,在刀具的调整范围内,在走刀的方向上使刀具稍微向前倾斜,可以得到较好的切削效果。
为了使被切削的表面没有切削条痕,不要使用刚经过刃磨的新刀具,采用已经用过一段时间并具有初期磨损状态的刀具较好。
究竟什么样的初期磨损状态为好,目前还不能定量地确定。
按经验对于新刀具最好先用10~30tzm大的吃刀深度进行一段时间切削,以促进刀具的初期磨损,然后再正式使用。
这样可以在较短的时间内获得良好的镜面。
随着切削的进行,将在刀具的刀口上附着如图7-24(口)所示的熔着物,看上去好像产生了磨损,实际上不是磨损,它对切削没有影响。
用4096的氢氧化钠(NaOH)溶液可以很容易地将其清洗掉。
图7—24(b)示出经清洗后去掉熔着物的切削刃,可以看出切削刃仍良好无损。
四、多面反射镜的材质与镜面加工1.反射镜的材料因多面反射镜在使用中要进行高速回转,制造多面反射镜的材料要有足够的强度,可以承受高速回转所产生的离心力,且可用金刚石刀具超精密切削加工成镜面。
此类材_jls以铝合金最为合适。
但经试验证明,并不是所有的铝合金均可以/jn-r成镜面,即使是同一牌号的铝合金,因生产厂家不同,加工效果也不同,有的甚至不能加工出镜面。
从光学镑面的观点出发,对材料中的夹杂物的大小和数量都要有要求。
一般情况下不经切削试裂是很难判断出是否可以加工出镜面来的。
目前,多面反射镜多用AI—Mg合金,硬度为58HB,这种材料的夹杂物,结晶颗粒和晶界状况都较好。
但是由于材料的硬度差和结晶方位的各向异性的影响,在被切削的表面上将产生加工段差或产生切削痕。
图7-25所示是铝合金在镜面切削时因结晶的各向男性和硬度差所产生的加工段差和切削痕迹。
对铝合金来说,加工段差的高度可以说是递种材料的表面粗糙度的加工极限。
目前激光打印机的光源已从He—Ne激光变为半导体激光,从而使打印机小型化,躏低了成本。
但是铝合金的多面反射镜对二者的反射率却有一定的差别。
对He—Ne激井(波长A=0.623 8tan)的反射率可达90%,而对半导体激光(波长A=0.780-0.80胂)雕反射率则只有85%--87%。
因此在使用半导体激光的打印机中,所使用的多面反射镜茑是在铝合金的反射镜面上,真空镀上一层金膜,或是使用无氧铜的多面反射镜。
但是镀盒膜将使成本提高。
而用无氧铜的反射镜,因其密度比铝合金重3倍多,这将使轴承的负布增大,这不但增加了设计高速回转轴承部分的困难,而且也影响使用寿命。
除上述材料外,也有在铝合金上镀上一层非电解镍,然后再经金刚石刀具超精密蔹削。
但是因为镀层的质量不均匀,再加上成本高,与切削铝合金相比,刀具的寿命低等缺点,故使用不多。
目前正在对没有夹杂物和结晶晶界、密度又很小的丙烯酸酯、聚碳酸酯等树脂材料进行试验,制作多面反射镜。
2.镜面的加工多面镜镜面部分的加工是多面镜加工的最后一道工序。
将其部分已加工好,镜面部分也经过粗加:【的工件,安装在夹其中,然后在机床的多齿分度盘上经定心后夹紧。
根据:工件的材质,尺寸大小和多面镜的面数,确定加工条件。
若是全自动专用机床,只要将加工条件输入给控制系统,然后开动机床,便可以全部自动地完成所有镜面的加工。
如果不是多面镜的专用机床,则需每加工完一面后,根据要求用多齿分度盘分度后再加工下一个镜面。
为了提高生产效率,可将数个多面镜装夹在一个心轴上进行多件加工。
切削镜面时,在刀具主轴的刀盘上装有两把金刚石刀具,其中一把是刀尖半径为R5ntm的烧结金刚石刀具,用它进行粗加工;另一把是刀尖半径大或直线切削刃的:疋然单晶金刚石刀具,用它进行超精密加工。
这两把刀具在刀盘上安装时,在刀盘的径向E两把刀具要互相错开。
在轴向上精加:【二用的刀具应比粗加工用的刀具高出一精加工余量,这样在一次走刀中便可以同时完成粗、精加工。
粗加工的余量不能取得太大,如果粗加工余量太大,在被切削表面的四周将产生毛刺,为此粗加工的吃刀深度一般取0.05~0.1 ITllTI为宜。
根据所要求的表面粗糙度和刀具调整的状态,采用不同的切削加工条件。
表7—7列出铝镁合金多面反射镜的切削加工条件,如果粗、精加工在一次走刀中同时进行时,则应按精加工选取切削加工条件。
目前,切削速度与金刚石刀具寿命之间的关系尚不明确。
所以在选择切削速度时,主要考虑要避开机械的共振区,也要提高加工效率。
一般刀盘的转速在1500~2500r/min (切削速度500~900m/min)时较合适。