氨回收工艺
各种回收氨方法比较
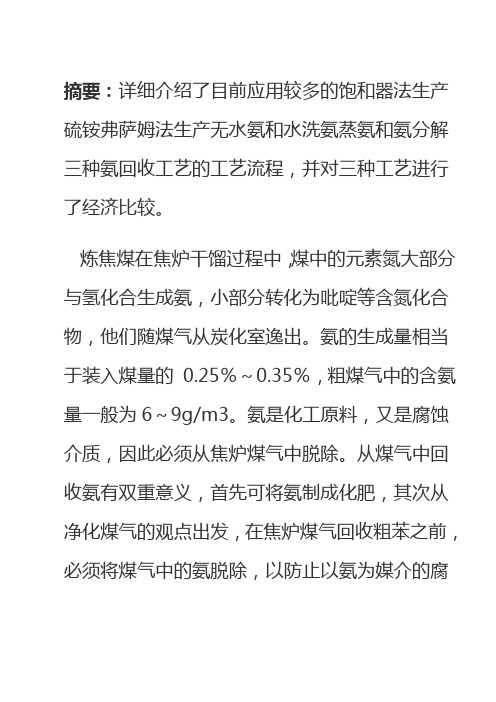
摘要:详细介绍了目前应用较多的饱和器法生产硫铵弗萨姆法生产无水氨和水洗氨蒸氨和氨分解三种氨回收工艺的工艺流程,并对三种工艺进行了经济比较。
炼焦煤在焦炉干馏过程中,煤中的元素氮大部分与氢化合生成氨,小部分转化为吡啶等含氮化合物,他们随煤气从炭化室逸出。
氨的生成量相当于装入煤量的 0.25%~0.35%,粗煤气中的含氨量一般为6~9g/m3。
氨是化工原料,又是腐蚀介质,因此必须从焦炉煤气中脱除。
从煤气中回收氨有双重意义,首先可将氨制成化肥,其次从净化煤气的观点出发,在焦炉煤气回收粗苯之前,必须将煤气中的氨脱除,以防止以氨为媒介的腐蚀性介质进入粗苯回收系统而造成设备的严重腐蚀。
对于氨的脱除,目前我国广泛采用的有三种不同类型的工艺,即生产硫铵、无水氨和氨分解等工艺。
硫铵工艺所得硫酸铵的国家标准见下表。
硫酸铵的国家标准名称指标一级品二级品三级品氮含量(以干基计),%≮21 ≮20.8≮20.6水分,%≯0.1≯1.0≯2.0游离酸(H2S4O) ,%≯0.05≯0.2≯0.3粒度(60目筛余量),%≮75 --颜色白色或微带颜色的结晶生产无水氨工艺所得的无水氨主要用于制造氮肥和复合肥料,还可用于制造硝酸、各种含氮无机盐及有机物中间体、磺胺药、聚氨酯、聚酰胺纤维和丁腈橡胶等。
此外,还常用作制冷剂。
氨分解工艺所产生的废气送入鼓风机前的吸煤气管道,但该工艺装臵无产品回收。
1 硫铵生产工艺生产硫铵是焦炉煤气净化工艺流程中回收氨的传统方法。
我国20世纪60年代以前建成的大中型焦化厂均采用半直接法鼓泡型饱和器生产硫铵,该工艺的主要缺点是设备腐蚀严重,硫铵质量差,煤气系统阻力大。
在宝钢一期工程的建设中,我们引进了酸洗法生产硫铵工艺,它是由酸洗、真空蒸发结晶以及硫铵离心、干燥、包装等三部分组成。
与饱和器法相比,由于实现了氨的吸收与硫铵结晶分离的操作,以获得优质大颗粒硫铵结晶。
酸洗塔结构为空喷塔,煤气系统阻力仅为饱和器的1/4,煤气鼓风机的电耗可大幅度下降。
弗萨姆法回收氨的基本原理

弗萨姆法回收氨的基本原理
弗萨姆法是一种回收氨的方法,其基本原理是通过将废水中的氨与硫酸反应生成硫酸铵沉淀,从而实现氨的回收。
具体步骤如下:
1. 将废水中的氨与硫酸进行反应,生成铵离子(NH4+)和硫酸根离子(SO4^-2)。
2NH3 + H2SO4 →(NH4)2SO4
2. 硫酸铵是一种沉淀,可以通过沉淀法进行固液分离。
将产生的硫酸铵沉淀从废水中分离出来。
3. 硫酸铵沉淀可以进一步经过热解、结晶等工艺步骤进行后续处理,从而得到高纯度的氨。
通过弗萨姆法回收氨的优点是操作简便、成本较低,能够高效地回收废水中的氨并得到可再利用的硫酸铵产品。
这种方法在废水处理和化工生产过程中得到了广泛应用。
合成氨氨回收工艺技术改造

综上所述 , 次吹风气余热回收装置技术改 本
造 达到 了预期 目的 , 仅 全 部 回收 了 4台造 气 炉 不 的吹风 气气量 , 实现 了造气 生产 蒸汽 自给 , 明显 还
地 改善 了厂 区 生产 环境 , 现 了吹 风 气 余热 回收 实
装 置 的长周 期 、 安全稳 定运 行
实 际情 况 自行 设计 了 1套氨 回收 装置 。
合成氨 公 司铜 洗 再 生气 、 氨罐 弛放 气 的 回收 装 置 属于 2 0世 纪 7 0年代 小 氮 肥 企 业 的 传 统 回 收 技
术 , 回收率低 ( 3 .7 ) 再 生气 回收 因结垢 氨 仅 74 % , 严重 , 成 回流塔 憋压而 频繁 放空 , 造 回收率 只能达
弛放 气 回收 采用 自冷 方式 , 冷凝 其 中大 部 分 的 氨 以减轻后 工 段 的负 荷 , 回收 的气 氨 送气 氨总 管, 多余 的液 氨送 合 成 氨 冷 器 。氨 自冷 工艺 流程 见图 2 。将 来 自液氨贮 罐 的弛放 气 经过 冷 热交 换 器冷 却降 温后 , 氨冷器进 一 步冷凝 , 送 多余 的液氨 送 合 成氨 冷器 , 回收的气 氨送 气 氨总管 , 冷凝除 去
度 ≥10 o 8 C。随着入 炉蒸汽 温 度 的提 高 和 吹风 阻
表 3 改造 前、 3 h燃煤锅炉运行数据对 比 后 5t /
力的降低 , 吹风 时间减 少 1— , 2s每班 白煤 消耗 下 降 一 。根据 生产 部 门统 计 的数据 , 造 后 余 热 2t 改 回收系统 比改造前 每年 增加 效益 l5万元 以上 5 ( )该 装置 投运 后 , 煤锅 炉负 荷大 幅下 降 , 2 燃 鼓 风机 电流 由原 来 的 30A降为 20A, 汽量 由 2 7 产 原 来的 4 / 2th降 为 3 h 吨氨 烟 煤 消耗 由原 来 3t , / 的 30k 2 g下降 为 20k。3 h锅炉 由原 来 的超 8 g 5t / 负荷运行 变为轻 负荷 运 行 , 锅 炉 长周 期 运 行 奠 为
冷库氨回收方案

冷库氨回收方案概述冷库氨回收方案是为了解决冷库中氨气的泄露问题,减少对环境和人体的危害,并达到节能和环保的目的。
本文档将介绍冷库氨回收方案的原理、设备和操作流程。
方案原理冷库氨回收方案的原理是通过氨气回收系统将冷库中泄露的氨气吸收并经过处理后重新利用。
具体的回收过程包括氨气吸收、氨气处理和氨气再利用三个步骤。
氨气吸收冷库中的泄露氨气通过整流器进入氨气吸收器,并与吸收剂发生吸收反应。
吸收剂通常是一种有机溶剂,能够与氨气发生物理或化学吸收反应,形成氨合物。
氨气处理吸收剂中的氨合物经过加热和真空蒸馏,使氨气从吸收剂中脱附出来。
同时,对吸收剂进行再生处理,将其中的杂质去除,恢复其吸收能力。
氨气再利用脱附出来的氨气经过冷凝和压缩,得到高纯度的氨气,可以重新用于冷库的冷却系统。
设备介绍冷库氨回收方案所涉及的主要设备有氨气吸收器、整流器、加热器、真空蒸馏器、冷凝器和压缩机等。
氨气吸收器氨气吸收器是冷库氨回收系统的关键设备,用于将冷库中的氨气吸收到吸收剂中。
吸收器通常由壳管式换热器组成,具有较大的换热面积和高效的氨气吸收性能。
整流器整流器用于调节冷库中泄露氨气的流量和压力,保持吸收器中氨气的稳定供应。
整流器通常由调节阀和过滤器组成。
加热器加热器用于对吸收剂和氨合物进行加热,使氨气从吸收剂中脱附出来。
加热器通常采用蒸汽或电加热的方式。
真空蒸馏器真空蒸馏器用于对吸收剂进行再生处理,将其中的杂质去除,恢复其吸收能力。
真空蒸馏器通常由加热器、冷却器和凝结器组成。
冷凝器和压缩机冷凝器用于将脱附出来的氨气冷凝成液体,压缩机用于将冷凝后的氨气压缩成高纯度的氨气。
冷凝器和压缩机通常组成一套封闭的循环系统。
操作流程冷库氨回收方案的操作流程包括氨气吸收、氨气处理和氨气再利用三个步骤。
1.氨气吸收–打开整流器,调节氨气的流量和压力。
–将冷库中的氨气引导到吸收器中,与吸收剂发生吸收反应。
–根据吸收效果,调节吸收剂的添加量和吸收器的温度和压力。
氨回收操作规程
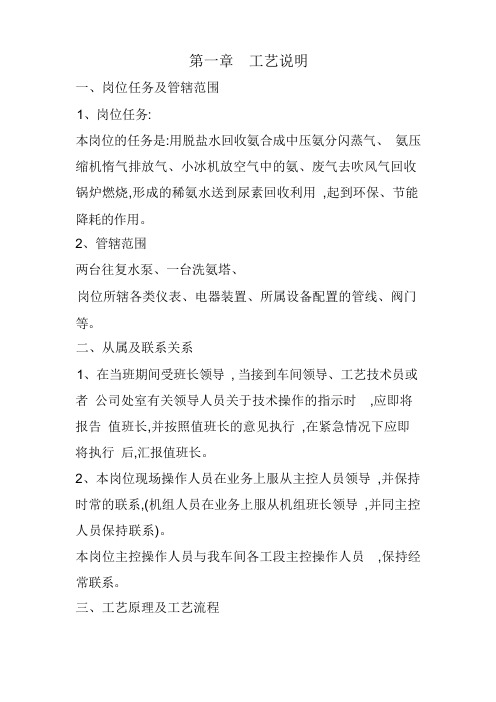
第一章工艺说明一、岗位任务及管辖范围1、岗位任务:本岗位的任务是:用脱盐水回收氨合成中压氨分闪蒸气、氨压缩机惰气排放气、小冰机放空气中的氨、废气去吹风气回收锅炉燃烧,形成的稀氨水送到尿素回收利用,起到环保、节能降耗的作用。
2、管辖范围两台往复水泵、一台洗氨塔、岗位所辖各类仪表、电器装置、所属设备配置的管线、阀门等。
二、从属及联系关系1、在当班期间受班长领导, 当接到车间领导、工艺技术员或者公司处室有关领导人员关于技术操作的指示时,应即将报告值班长,并按照值班长的意见执行,在紧急情况下应即将执行后,汇报值班长。
2、本岗位现场操作人员在业务上服从主控人员领导,并保持时常的联系,(机组人员在业务上服从机组班长领导,并同主控人员保持联系)。
本岗位主控操作人员与我车间各工段主控操作人员,保持经常联系。
三、工艺原理及工艺流程1、气相流程:氨合成中压氨分闪蒸气减压后 1.6Mpa, 氨压缩机惰气排放气1.5Mpa 和小冰机放空气1.6Mpa 三股气体合并后,一同进入洗氨塔由下而上进入洗氨塔,,水洗后的废气经顶部调节阀减压到0.3Mpa 后送造气吹风气回收利用。
2、水流程由中压水泵将水箱中的脱盐水打到洗氨塔顶部, 自上而下洗涤气体中的氨, 吸收废气中的氨后形成稀氨水,送到尿素氨水槽回收利用。
四、工艺指标中压氨分闪蒸气: 减压前2.46Mpa 减压后1.5Mpa小冰机放空气: 1.5Mpa洗氨塔操作压力: 1.5Mpa( 由顶部减压阀来控制) 减压后压力: 0.3Mpa洗氨塔顶部操作温度: 小于45℃洗氨塔液位: 50% —80%水量: 2m3/h含量: <10ppm中压氨分出口气体NH3第二章设备说明往复泵(软水泵) 介质:脱盐水流量(正常)2.0t/h工作压力: 进口正常0.02Mpa(G)出口正常2. 1Mpa(G)扬程:213m 洗氨塔:工作压力:1.0- 1.5Mpa 第三章 一、原始开车工作温度:小于 45℃操作程序1、准备工作:(1)装置吹扫试漏、水洗完毕、全部合格。
第六节焦炉煤气氨的回收

第六节焦炉煤气回收氨炼焦煤料在焦炉中干馏时,煤中所含的一部分氮转化为含氮化合物进入粗煤气中,其中最主要的是氨。
粗煤气含氨量为69g/m3。
氨既是化工原料,又是腐蚀性介质,因此必须从粗煤气中回收氨。
焦炉煤气回收氨主要有水洗氨法、硫酸吸氨法和磷酸吸氨法3种。
一、水洗氨法水洗氨法以软水为吸收液回收煤气中的氨,同时使焦炉煤气得到净化。
回收的氨制成氮肥或进行分解。
这类方法有:制浓氨水法、间接法、联碱法和氨分解法。
水洗氨法回收氨的优点是,产品可按市场需要调整,适应性大;缺点是,流程长,设备多,占地面积大。
水洗氨法的主要设备有洗氨塔和蒸氨塔。
1.制浓氨水法制浓氨水法以软水为吸收液回收焦炉煤气中的氨,氨水经蒸馏得到浓氨水。
制浓氨水法的工艺流程如图5-33所示。
脱萘后的煤气依次经过3个串联的洗氨塔,每个塔分为两段。
3号塔的上段为净化段,在净化段内煤气用新鲜软水净化,使其含氨量降到0. lg/m3以下,再去洗苯塔。
净化段排出的水送生物脱酚装置处理。
从3号塔下段送入蒸氨废水,洗氨水与煤气逆流接触。
为了提高洗氨塔各段的喷淋密度,每段均设有单独的循环泵。
从1号塔下段排出的富氨水与剩余氨水一并送人原料氨水池,再由氨水池用泵送出与蒸氨废水换热,经预热器加热至85~90℃,送往分解器中部。
分解器底部设有加热器,原料氨水中的挥发氨盐在此被分解,分解出的CO2、H2S等气体从器顶逸出。
为了减少氨的损失,用冷回流泵将10%的原料氨水直接送入分解器顶部,以降低器顶温度,使顶部外排气体主要为二氧化碳和硫化氢,经分解器自流人蒸氨塔顶部的原料氨水被从塔底直接送入的蒸汽蒸出氨。
蒸出的氨进入分凝器。
将分凝器出口温度控制在88~92℃,即可得到含氨18%~20%昀氨气。
氨气经冷凝器冷凝,得到浓氨水。
蒸氨塔底排出的废水,经换热器降温后送往洗氨塔洗氨,多余的废水送生物脱酚装置处理。
2.间接法间接法以软水为吸收液回收焦炉煤气中的氨,氨再经蒸氨制取硫酸铵。
氨回收分离工艺简介
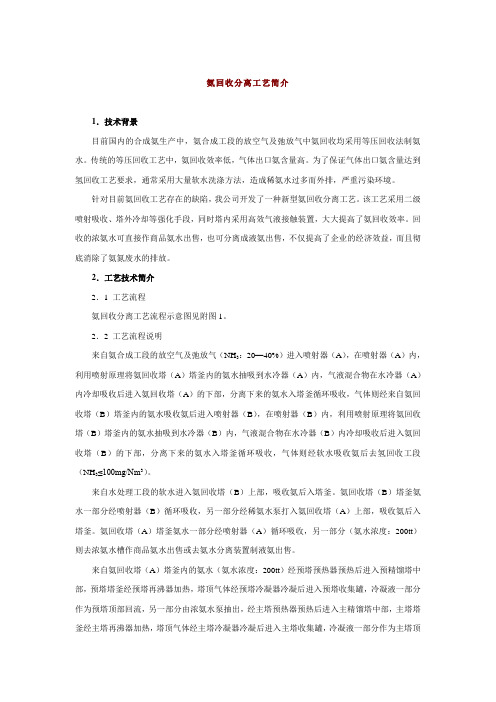
氨回收分离工艺简介1.技术背景目前国内的合成氨生产中,氨合成工段的放空气及弛放气中氨回收均采用等压回收法制氨水。
传统的等压回收工艺中,氨回收效率低,气体出口氨含量高。
为了保证气体出口氨含量达到氢回收工艺要求,通常采用大量软水洗涤方法,造成稀氨水过多而外排,严重污染环境。
针对目前氨回收工艺存在的缺陷,我公司开发了一种新型氨回收分离工艺。
该工艺采用二级喷射吸收、塔外冷却等强化手段,同时塔内采用高效气液接触装置,大大提高了氨回收效率。
回收的浓氨水可直接作商品氨水出售,也可分离成液氨出售,不仅提高了企业的经济效益,而且彻底消除了氨氮废水的排放。
2.工艺技术简介2.1 工艺流程氨回收分离工艺流程示意图见附图1。
2.2 工艺流程说明来自氨合成工段的放空气及弛放气(NH3:20—40%)进入喷射器(A),在喷射器(A)内,利用喷射原理将氨回收塔(A)塔釜内的氨水抽吸到水冷器(A)内,气液混合物在水冷器(A)内冷却吸收后进入氨回收塔(A)的下部,分离下来的氨水入塔釜循环吸收,气体则经来自氨回收塔(B)塔釜内的氨水吸收氨后进入喷射器(B),在喷射器(B)内,利用喷射原理将氨回收塔(B)塔釜内的氨水抽吸到水冷器(B)内,气液混合物在水冷器(B)内冷却吸收后进入氨回收塔(B)的下部,分离下来的氨水入塔釜循环吸收,气体则经软水吸收氨后去氢回收工段(NH3≤100mg/Nm3)。
来自水处理工段的软水进入氨回收塔(B)上部,吸收氨后入塔釜。
氨回收塔(B)塔釜氨水一部分经喷射器(B)循环吸收,另一部分经稀氨水泵打入氨回收塔(A)上部,吸收氨后入塔釜。
氨回收塔(A)塔釜氨水一部分经喷射器(A)循环吸收,另一部分(氨水浓度:200tt)则去浓氨水槽作商品氨水出售或去氨水分离装置制液氨出售。
来自氨回收塔(A)塔釜内的氨水(氨水浓度:200tt)经预塔预热器预热后进入预精馏塔中部,预塔塔釜经预塔再沸器加热,塔顶气体经预塔冷凝器冷凝后进入预塔收集罐,冷凝液一部分作为预塔顶部回流,另一部分由浓氨水泵抽出,经主塔预热器预热后进入主精馏塔中部,主塔塔釜经主塔再沸器加热,塔顶气体经主塔冷凝器冷凝后进入主塔收集罐,冷凝液一部分作为主塔顶部回流,另一部分则去液氨贮槽作商品液氨出售。
饱和器法生产硫酸铵回收氨全解
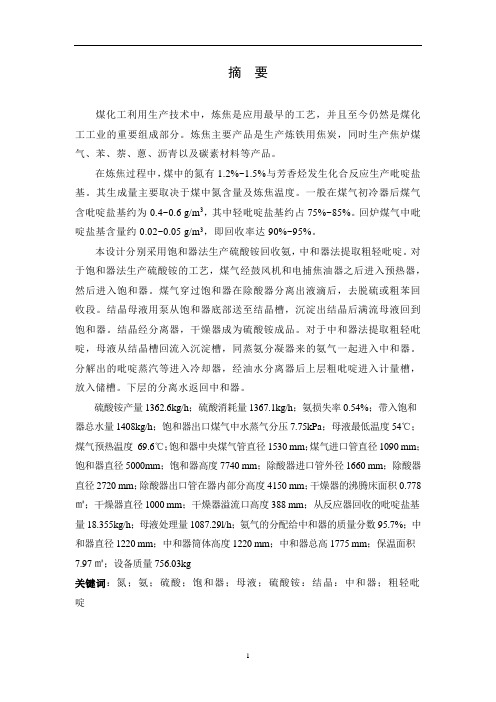
摘要煤化工利用生产技术中,炼焦是应用最早的工艺,并且至今仍然是煤化工工业的重要组成部分。
炼焦主要产品是生产炼铁用焦炭,同时生产焦炉煤气、苯、萘、蒽、沥青以及碳素材料等产品。
在炼焦过程中,煤中的氮有1.2%~1.5%与芳香烃发生化合反应生产吡啶盐基。
其生成量主要取决于煤中氮含量及炼焦温度。
一般在煤气初冷器后煤气含吡啶盐基约为0.4~0.6 g/m3,其中轻吡啶盐基约占75%~85%。
回炉煤气中吡啶盐基含量约0.02~0.05 g/m3,即回收率达90%~95%。
本设计分别采用饱和器法生产硫酸铵回收氨,中和器法提取粗轻吡啶。
对于饱和器法生产硫酸铵的工艺,煤气经鼓风机和电捕焦油器之后进入预热器,然后进入饱和器。
煤气穿过饱和器在除酸器分离出液滴后,去脱硫或粗苯回收段。
结晶母液用泵从饱和器底部送至结晶槽,沉淀出结晶后满流母液回到饱和器。
结晶经分离器,干燥器成为硫酸铵成品。
对于中和器法提取粗轻吡啶,母液从结晶槽回流入沉淀槽,同蒸氨分凝器来的氨气一起进入中和器。
分解出的吡啶蒸汽等进入冷却器,经油水分离器后上层粗吡啶进入计量槽,放入储槽。
下层的分离水返回中和器。
硫酸铵产量1362.6kg/h;硫酸消耗量1367.1kg/h;氨损失率0.54%;带入饱和器总水量1408kg/h;饱和器出口煤气中水蒸气分压7.75kPa;母液最低温度54℃;煤气预热温度69.6℃;饱和器中央煤气管直径1530 mm;煤气进口管直径1090 mm;饱和器直径5000mm;饱和器高度7740 mm;除酸器进口管外径1660 mm;除酸器直径2720 mm;除酸器出口管在器内部分高度4150 mm;干燥器的沸腾床面积0.778㎡;干燥器直径1000 mm;干燥器溢流口高度388 mm;从反应器回收的吡啶盐基量18.355kg/h;母液处理量1087.29l/h;氨气的分配给中和器的质量分数95.7%;中和器直径1220 mm;中和器筒体高度1220 mm;中和器总高1775 mm;保温面积7.97㎡;设备质量756.03kg关键词:氮;氨;硫酸;饱和器;母液;硫酸铵:结晶:中和器;粗轻吡啶目录第一章总论 (6)1.1 概述 (6)1.2 文献综述 (6)1.2.1 用硫酸回收氨的生产工艺原理 (7)1.2.2 从硫酸铵母液中制取粗轻吡啶工艺原理 (8)1.3 设计条件及要求 (10)1.4 工艺流程的确定 (11)第二章回收氨的工艺流程 (12)第三章硫酸铵生产的影响因素及其控制 (14)3.1 母液酸度 (14)3.2 母液温度 (15)3.3 母液搅拌 (16)3.4 离心分离和水洗 (16)3.5 杂质 (18)3.6 晶比 (19)第四章回收氨时物料平衡和热量平衡的计算 (20)4.1 物料衡算 (20)4.1.1氨的平衡及硫酸用量的计算和硫酸铵产量的计算 (20)4.1.2 水平衡及母液温度的确定 (21)4.2 热量衡算 (23)4.2.1输入热量 (23)4.2.2 输出热量 (26)第五章硫酸铵生产的主设备计算 (28)5.1 饱和器 (28)5.2 除酸器 (30)5.3 干燥器 (32)5.4 结晶槽 (37)第六章中和器法提取粗轻吡啶工艺流程 (39)第七章影响粗轻吡啶生产的因素及其控制 (41)7.1 吸收阶段 (41)7.2 中和及粗轻吡啶分离阶段 (42)第八章中和器的物料平衡工艺计算 (43)8.1 母液处理量 (43)8.2 分凝器后氨气分配给中和器的质量分数 (44)第九章回收粗轻吡啶的主要设备计算 (45)9.1 中和器 (45)9.2 冷凝冷却器 (46)9.3 沉淀槽 (46)第十章设计一览表 (47)参考文献 (48)设计体会与收获 (49)致谢 (50)第一章总论1.1概述炼焦化学产品在国民经济中占有重要的地位,炼焦化学工业是国民经济的一个重要部门,是钢铁联合企业的主要组成部分之一,是煤炭的综合利用工业。
- 1、下载文档前请自行甄别文档内容的完整性,平台不提供额外的编辑、内容补充、找答案等附加服务。
- 2、"仅部分预览"的文档,不可在线预览部分如存在完整性等问题,可反馈申请退款(可完整预览的文档不适用该条件!)。
- 3、如文档侵犯您的权益,请联系客服反馈,我们会尽快为您处理(人工客服工作时间:9:00-18:30)。
煤化工工艺大作业氨回收工段工艺论证院系:资源与环境学院班级:化工09—4班姓名:小孩学号:14指导老师:大海氨回收工段工艺论证作者:摘要:炼焦煤在焦炉干馏过程中,煤中的元素氮大部分与氢化合生成氨,小部分转化为吡啶等含氮化合物,氨的生成量相当于装入煤量的 0.25%~0.35%,粗煤气中的含氨量一般为6~9g/m3。
关键词:氨的回收饱和器无饱和器冷却器一、硫铵生产工艺生产硫铵是焦炉煤气净化工艺流程中回收氨的传统方法。
我国20世纪60年代以前建成的大中型焦化厂均采用半直接法鼓泡型饱和器生产硫铵,该工艺的主要缺点是设备腐蚀严重,硫铵质量差,煤气系统阻力大。
在宝钢一期工程的建设中,我们引进了酸洗法生产硫铵工艺,它是由酸洗、真空蒸发结晶以及硫铵离心、干燥、包装等三部分组成。
与饱和器法相比,由于实现了氨的吸收与硫铵结晶分离的操作,以获得优质大颗粒硫铵结晶。
酸洗塔结构为空喷塔,煤气系统阻力仅为饱和器的1/4,煤气鼓风机的电耗可大幅度下降。
采用干燥冷却机将干燥后的硫铵进一步冷却,防止结块,有利于自动包装。
鞍山焦耐院将此工艺经改进后用于天津煤气二厂,装置投产后已通过了技术鉴定。
在宣钢和北焦的建设中,我们引进了间接法饱和器生产硫铵工艺,该工艺是从酸性气体中回收氨,其硫铵的质量比饱和器法好,但因在较高温度(100℃左右)下操作,对设备和管道材质的要求高,加之饱和器尺寸并不比半直接法小,因此投资高于半直接法。
在杭钢焦化厂,我们将此工艺用于蒸氨塔后氨汽生产硫铵,并已正常投产。
除上述方法外,鞍钢二回收从法国引进的二手设备喷淋式饱和器,以代替半直接法的鼓泡型饱和器。
喷淋式饱和器的特点是煤气系统阻力较小,设备尺寸可相对减小,硫铵质量有所提高。
国内已有不少厂家用其代替老式的鼓泡型饱和器。
但是,不管采用那种生产硫铵的工艺,从经济观点分析,其共同的致命缺点是硫铵的收入远远不够支付其生产费用。
下面重点介绍一下酸洗法和喷淋式饱和器生产硫铵的工艺。
1、酸洗法生产硫铵工艺酸洗法硫铵生产工艺由氨的回收、蒸发结晶与分离干燥等3部分组成。
煤气自下而上经过酸洗塔,在酸洗塔分上下两段,均用含游离酸2%~3%的硫铵母液进行喷洒,煤气中的氨即与硫酸结合生成硫铵,从酸洗塔顶逸出煤气经除酸器分离出酸雾后送入煤气总管。
用泵将母液循环槽中的硫铵母液抽送至结晶槽,结晶槽的母液用循环泵抽出,经母液加热器加热后送入真空蒸发器,蒸发器在(绝压)11kPa压力和48℃下工作,母液因真空蒸发而浓缩,浓缩后的过饱和溶液经中心管自流至结晶槽底部。
含有小颗粒结晶的母液在结晶槽中部经循环泵抽出大量循环,使结晶不断长大,几乎不含结晶的母液在结晶槽上部溢流至满流槽,再用泵送回母液循环槽。
大颗粒结晶沉积在结晶槽底部用浆液泵送往供料槽。
蒸发器的真空是用二级蒸汽喷射造成的,蒸汽喷射器使用0.7MPa的中压蒸汽。
从蒸发器上部出来的汽体经第一凝缩器与第二凝缩器冷凝后排往热井。
含有大颗粒结晶的硫铵母液在供料槽内进行沉降分离,上部清液溢流回结晶槽,底部含有50%结晶的母液进入离心机,滤液经滤液槽后再返回结晶槽。
硫铵结晶采用带冷风的干燥冷却器进行干燥、冷却。
酸洗法硫铵与老式饱和器硫铵工艺相比,有以下优点:酸洗法工艺采用空喷塔,煤气系统阻力小,约为饱和器法的1/4~1/5,使风机电耗可以大大降低;酸洗法工艺在酸洗塔内母液始终控制在不饱和状态,结晶颗粒是在真空蒸发结晶系统内形成,由于采用了大流量的母液循环,控制了晶核的形式,并使结晶有足够的成长时间,因而,可以获得大颗粒的优质硫铵结晶。
酸洗法硫铵的设备与管道均采用了超低碳不锈钢(OOCrl7Nil4Mo2),较好地解决了稀硫酸的腐蚀问题,酸洗塔可不设备品,大大减少了设备的维修工作量。
我国自行设计的酸洗法硫铵生产装置,将酸洗塔由一台两段改为二台各一段的空喷塔,这样,两台可以互为备用,便于连续、稳定生产。
2、喷淋式饱和器法硫铵工艺喷淋式饱和器硫铵生产工艺与鼓泡式饱和器流程基本一样,只是将喷淋式饱和器代替鼓泡式饱和器。
喷淋式饱和器是将饱和器和结晶器连为一体,流程更为简化。
在此流程中采用母液加热器,从结晶槽顶部一部分母液通过加热器加热,再循环返回饱和器喷淋。
在饱和器底部控制一定的母液液位,母液从满流管流入满流槽。
在满流槽中除去焦油的母液流入母液贮槽。
母液循环泵从结晶槽上部抽出母液,送到喷淋室的环形分配箱进行喷洒,母液循环量为15L/m3。
吸收氨后的母液通过中心降液管向下流到结晶槽底部。
饱和器内母液酸度控制20%~30%,结晶段的结晶体积百分比上限为35%~40%,下限为4%。
晶比达到25%时,启动结晶泵抽取结晶,送往结晶槽提取硫铵。
在保证饱和器水平衡的条件下,一般饱和器母液温度保持在50~55℃,煤气出口温度44~48℃。
喷淋式饱和器的阻力一般为1000~2000Pa,为旧式鼓泡型饱和器的1/5~1/4。
饱和器后的煤气含氨可达到30~50mg/m3。
喷淋式饱和器的结构有如下特点:①喷淋室由本体、外套筒和内套筒组成,煤气进入本体后向下在本体与外套筒的环形室内流动,然后由上出喷淋室,再沿切线方向进入外套筒与内套筒间旋转向下进入内套筒,由顶部出去。
外套筒与内套筒间形成旋风分离作用,以除去煤气夹带的液滴,起到除酸器的作用。
②在喷淋室的下部设置母液满流管,控制喷淋室下部的液面,促使煤气由入口向出口在环形室内流动。
③在煤气入口和煤气出口间分隔成两个弧形分配箱,在弧形分配箱配置多组喷嘴,喷嘴方向朝向煤气流,形成良好的气液接触面。
④喷淋室的下部为结晶槽,用降液管与结晶槽连通,循环母液通过降液管从结晶槽的底部向上返,不断生成的硫铵晶核,穿过向上运动的悬浮硫铵母液,促使晶体长大,并引起颗粒分级,小颗粒升向顶部,从上部出口接到循环泵,结晶从下部抽出。
⑤在煤气出口配置有母液喷洒装置。
煤气入口和出口均设有温水喷洒装置,可以较彻底清洗喷淋室。
⑥饱和器材质,国外引进的设备其材质均采用耐酸不锈钢制造,所用材料牌号为URANUS 50(法国牌号);我国引进的酸洗法酸洗塔材质为SUS316L,目前国内采用的喷淋式饱和器和母液加热器均采用SUS316L,它可使用于接触介质硫酸酸度在10%以下的设备。
综上所述,喷淋式饱和器工艺综合了旧式饱和器法流程简单,酸洗法有大流量母液循环搅拌,结晶颗粒大的优点,又解决了旧式饱和器法煤气系统阻力大,酸洗法工艺流程长,设备多的缺点。
其工艺流程和操作条件与现有的鼓泡型饱和器相接近,易于掌握,设备材料国内能够解决。
不但可以在新建厂采用,而且更适于老厂的大修改造。
3、鼓泡式饱和器法由鼓风机来的焦炉煤气,经电捕焦油器后进入煤气预热器。
在预热器内用间接蒸汽加热煤气到60~70℃或更高的温度,目的是为了使煤气进入鼓泡式饱和器蒸发饱和器内多余的水分,保持饱和器内的水平衡。
预热后的煤气沿饱和器中央煤气管进入饱和器,经泡沸伞从酸性母液中鼓泡而出,同时煤气中的氨被硫酸所吸收。
煤气出饱和器后进入除酸器,捕集其夹带的酸雾后,被送往粗苯工段。
鼓泡式饱和器后煤气含氨一般小于0.03g/m3。
冷凝工段的剩余氨水经蒸氨后得到的氨气,在不生产吡啶时,直接进入饱和器;当生产吡啶时将此氨气通入吡啶中和器。
氨在中和器内与母液中的游离酸及硫酸吡啶作用,生成硫酸铵,又随中和器回流母液返回饱和器。
饱和器母液中不断有硫酸铵生成,在硫酸铵含量高于其溶解度时,就析出结晶,并沉淀于饱和器底部。
其底部结晶被抽送到结晶槽,在结晶槽内使结晶长大并沉淀于底部。
结晶槽底部硫酸铵结晶放到离心机内进行离心分离,滤除母液,并用热水洗涤结晶,以减少硫酸铵表面上的游离酸和杂质。
离心分离的母液与结晶槽满流出的母液一同自流回饱和器中。
从离心机分离出的硫酸铵结晶经螺旋输送机,送入沸腾干燥器内,用热空气干燥后送入硫酸氨储斗,经称量包装入成品库。
为了使饱和器内煤气与母液接触充分,必须使煤气泡沸伞在母液中有一定的液封高度,并保证饱和器内液面稳定,为此在饱和器上还设有满流口,从满流口溢出的母液经插入液封内的满流管流入满流槽,以防止煤气逸出。
满流槽下部与循环泵链接,将母液不断地抽送到饱和器底部的喷射器。
因而一定的喷射速度,故饱和器内母液被不断循环搅动,以改善结晶过程。
煤气带入饱和器的煤焦油雾,在饱和器内与硫酸作用生成所谓的酸煤焦油,泡沫状酸煤焦油漂浮在母液面上,并与母液一起流入满流槽。
漂浮于满流槽液面上的酸煤焦油应及时捞出,或引入一分离处理装置与母液分离,以回收母液。
饱和器内所需补充的硫酸,由硫酸仓库送至高置槽,再自流入饱和器,正常生产时,应保持母液酸度为4%~6%,硫酸加入量为中氨的需要量;当不生产粗轻吡啶时,硫酸加入量要大一些,还要中和随氨气进入饱和器的氨。
饱和器在操作一定时间后,由于结晶的沉积将使其阻力增加,严重时会造成饱和器的堵塞。
所以操作中必须定期进行酸洗和水洗。
当定期大加酸、补水、用水冲洗饱和器及除酸器时,所形成的大量母液有漫流槽满流至母液储槽。
在正常生产时又将这些母液抽回饱和器以作补充。
饱和器是周期性连续操作设备,为了防止结晶堵塞,定期大加酸和水洗,从而破坏了结晶生成的正常条件,加之结晶在饱和器底部停留时间短,因而结晶颗粒较小,平均直径在0.5mm。
这些都是鼓泡式饱和器存在的缺点。
二、无饱和器法生产硫酸铵用饱和器法生产硫酸铵的方法存在着阻力大、硫酸铵结晶颗粒小、易堵塞设备等缺点。
所以,近年来无饱和器法生产硫酸铵的方法得到了迅速发展。
此法特点就是喷洒酸洗塔内用不饱和的酸性母液作为吸收剂,吸收煤气中氨,所得硫酸铵的结晶过程在单独的蒸发器内进行。
一些焦化厂采用后收到了明显的效果。
1无饱和器法生产硫酸铵的工艺流程煤气与蒸氨工段来的一部分氨气一起进入酸洗塔下段,煤气入口处及下段用酸度为2%~3%的循环母液喷洒,煤气与氨蒸气中大部分氨在此被吸收下来,此段得到的是硫酸铵浓度约40%的不饱和硫酸铵母液,上段喷洒的母液酸度为4%~5%,以吸收煤气和氨蒸气中剩余的氨及轻吡啶盐基,酸洗塔后煤气中含氨低于0.1g/m3。
由酸洗塔顶出来的煤气经旋风除酸器脱除酸雾后去脱苯工段。
酸洗塔的两段都有独立的母液循环系统。
下段来的部分母液先进入酸焦油分离槽,经分离后去澄清槽。
另一部分母液满流进入母液循环槽,由此用泵送往酸洗塔下段循环喷洒,母液循环量一般为 3.5 m3/km3煤气。
由酸洗塔上段引出的母液经循环槽用于上段喷洒,其循环喷洒量约为2.6 m3/km3煤气。
循环母液中需要补充的酸由酸高置槽补充。
澄清槽内的母液用结晶泵送至加热器,连同由结晶槽来的母液一起加热至60℃左右,然后进入真空蒸发器。
蒸发器内由两级蒸汽喷射器造成的87kPa的真空度,母液沸点降至55~60℃。
在此,母液因水分蒸发而得到浓缩,浓缩后的过饱和硫酸铵母液流入结晶槽,结晶长大并沉到结晶槽下部,仅含少量细小结晶的母液用循环泵送至加热器进行循环加热,而由结晶槽顶溢流的母液则经满流槽泵回循环母液槽。