粉料压制成型
粉末成型压力机工作原理
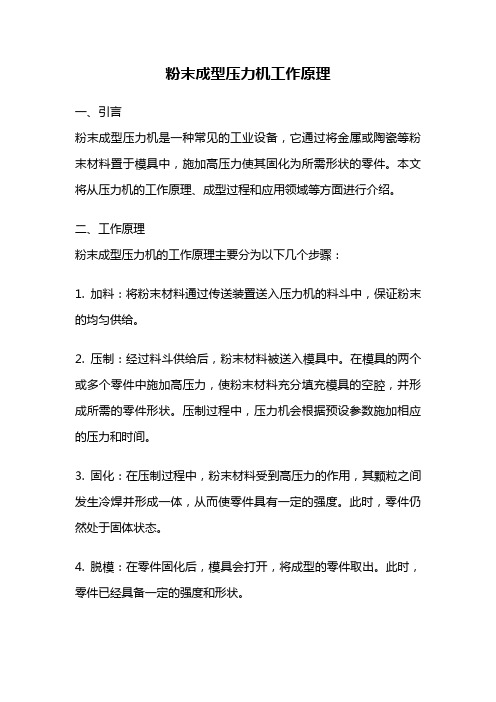
粉末成型压力机工作原理一、引言粉末成型压力机是一种常见的工业设备,它通过将金属或陶瓷等粉末材料置于模具中,施加高压力使其固化为所需形状的零件。
本文将从压力机的工作原理、成型过程和应用领域等方面进行介绍。
二、工作原理粉末成型压力机的工作原理主要分为以下几个步骤:1. 加料:将粉末材料通过传送装置送入压力机的料斗中,保证粉末的均匀供给。
2. 压制:经过料斗供给后,粉末材料被送入模具中。
在模具的两个或多个零件中施加高压力,使粉末材料充分填充模具的空腔,并形成所需的零件形状。
压制过程中,压力机会根据预设参数施加相应的压力和时间。
3. 固化:在压制过程中,粉末材料受到高压力的作用,其颗粒之间发生冷焊并形成一体,从而使零件具有一定的强度。
此时,零件仍然处于固体状态。
4. 脱模:在零件固化后,模具会打开,将成型的零件取出。
此时,零件已经具备一定的强度和形状。
5. 后处理:成型零件可能需要进行后续的烧结、热处理、机械加工等工艺,以进一步提高其性能和精度。
三、成型过程粉末成型压力机的成型过程是一个复杂的物理过程。
在压制过程中,粉末材料的颗粒之间不仅发生冷焊,还会发生变形和流动。
压制过程中的一些关键因素包括压力、温度、时间、粉末材料的性质和模具的设计等。
1. 压力:压力是控制成型过程中粉末材料变形和流动的关键因素。
适当的压力可以保证粉末材料充分填充模具的空腔,并获得所需的形状和密度。
2. 温度:温度对粉末成型过程中的冷焊和变形起着重要的影响。
适当的温度可以促进粉末颗粒之间的结合,并改善成型零件的强度和致密度。
3. 时间:时间是控制成型过程中压力施加的关键因素。
合理的时间可以确保粉末材料充分流动和变形,从而得到理想的成型效果。
4. 粉末材料的性质:不同的粉末材料具有不同的物理性质和成型特性。
在选择和设计粉末材料时,需要考虑其流动性、可压性和烧结性等因素。
5. 模具的设计:模具的设计直接影响到成型零件的形状和精度。
合理的模具设计可以保证粉末材料的充分填充和流动,从而得到高质量的成型零件。
18粉体成型的基本方法和过程

过程特点: ①随着压制力的继续增大,当压力达到和超过粉末颗粒的强度极限,粉末颗粒 将发生塑形变形(对于脆性粉末来说,不发生碎塑性变形而出现脆性断裂), 直到达到具有一定密度的坯块。 ②由于接近加压端面的部分压力最大,远离加压端面压力逐渐降低,这种压 力分布的不均匀性造成了压坯各个部分粉末致密化不均匀。
3、去除压力,施加脱模压力
现象: ①去除压力后,压坯仍会紧紧的固定在钢压膜内
②压坯中聚集的内应力使压坯产生弹性后效现象
三、影响粉体压制成形的因素
1、粉末本身的特性起关键性作用
压制成形是一个十 分复杂的过程 Nhomakorabea2、 压制力起着决定性的作用
金属材料工程基础知识 一、粉体成型的原理 二、粉体成型的过程 三、影响粉体压制成形的因素
的预成形坯中,底部和顶部的密度有很大差异,这种密 度差随预成形高度的增加而增加,随直径的增大而减小。
解决方法:若使用润滑剂可以减少粉粉末批量与莫蒂之间的摩
擦力,也可以降低沿高度方向的密度不均匀程度
双向压制
浮动凹模压制
轧制成形
二、粉体成型的过程
1、将松散的粉末装在钢压膜内 2、对钢压模中粉末施加压力
金属材料工程第十八讲
胡燕燕
一、粉体成型的原理
粉体成型是指将粉末状的材料制成具有一定形状,尺寸,孔隙 率以及强度的预成形坯体的加工过程。
成型方法
不同材料因其物 理化学特性不同, 所采用的成型方 法与技术并不完 全相同
模压成形 钢模压制成形
等静压成形
单向压制 是指压力施加在粉末配料的上顶部
特点:粉末批料与凹模之间的摩擦,使得在经单向压制所得到
压制成型的工艺原理
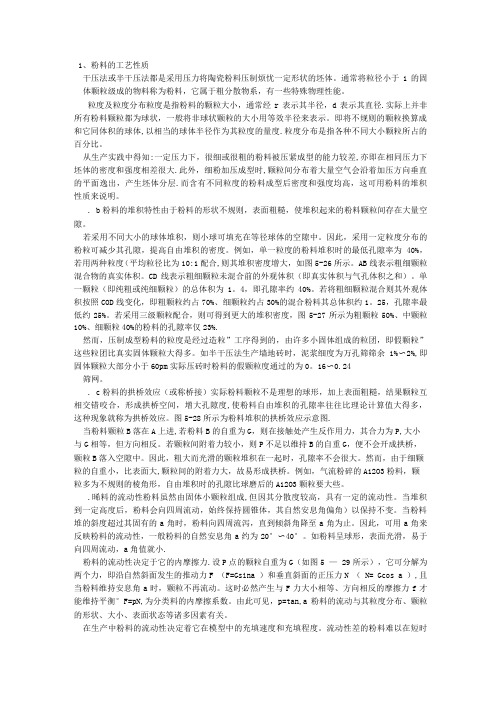
1、粉料的工艺性质干压法或半干压法都是采用压力将陶瓷粉料压制烦忧一定形状的坯体。
通常将粒径小于1的固体颗粒级成的物料称为粉料,它属于粗分散物系,有一些特殊物理性能。
粒度及粒度分布粒度是指粉料的颗粒大小,通常经r表示其半径,d表示其直径.实际上并非所有粉料颗粒都为球状,一般将非球状颗粒的大小用等效半径来表示。
即将不规则的颗粒换算成和它同体积的球体,以相当的球体半径作为其粒度的量度.粒度分布是指各种不同大小颗粒所占的百分比。
从生产实践中得知:一定压力下,很细或很粗的粉料被压紧成型的能力较差,亦即在相同压力下坯体的密度和强度相差很大.此外,细粉加压成型时,颗粒间分布着大量空气会沿着加压方向垂直的平面逸出,产生坯体分层.而含有不同粒度的粉料成型后密度和强度均高,这可用粉料的堆积性质来说明。
. b粉料的堆积特性由于粉料的形状不规则,表面粗糙,使堆积起来的粉料颗粒间存在大量空隙。
若采用不同大小的球体堆积,则小球可填充在等径球体的空隙中。
因此,采用一定粒度分布的粉粒可减少其孔隙,提高自由堆积的密度。
例如,单一粒度的粉料堆积时的最低孔隙率为40%,若用两种粒度(平均粒径比为10:1配合,则其堆积密度增大,如图5-26所示。
AB线表示粗细颗粒混合物的真实体积。
CD线表示粗细颗粒未混合前的外观体积(即真实体积与气孔体积之和)。
单一颗粒(即纯粗或纯细颗粒)的总体积为1。
4,即孔隙率约40%。
若将粗细颗粒混合则其外观体积按照COD线变化,即粗颗粒约占70%、细颗粒约占30%的混合粉料其总体积约1。
25,孔隙率最低约25%。
若采用三级颗粒配合,则可得到更大的堆积密度,图5-27所示为粗颗粒50%、中颗粒10%、细颗粒40%的粉料的孔隙率仅23%.然而,压制成型粉料的粒度是经过造粒”工序得到的,由许多小固体组成的粒团,即假颗粒”这些粒团比真实固体颗粒大得多。
如半干压法生产墙地砖时,泥浆细度为万孔筛筛余1%〜2%,即固体颗粒大部分小于60pm实际压砖时粉料的假颗粒度通过的为0。
粉末材料的主要成型方法

粉末材料的主要成型方法引言粉末材料是一种常见的材料形式,具有独特的性质和广泛的应用领域。
成型是将粉末材料转变为所需形状和尺寸的关键步骤之一。
本文将介绍粉末材料的主要成型方法,包括压制成型、注塑成型、烧结成型和3D打印等。
压制成型压制成型是最常见的粉末材料成型方法之一。
它通过将粉末材料放入模具中,施加高压使其变形并形成所需形状。
压制成型可以分为冷压成型和热压成型两种方式。
冷压成型冷压成型是将粉末材料在常温下进行成型的方法。
它适用于一些易于压制的材料,如金属粉末和陶瓷粉末。
冷压成型的步骤包括:1.将粉末材料放入模具中。
2.施加压力使粉末材料变形。
3.移除模具并得到成型件。
冷压成型的优点是成本低、工艺简单,但其成型密度较低,需要进一步处理以提高密度和强度。
热压成型热压成型是将粉末材料在高温下进行成型的方法。
它适用于一些高熔点材料和复杂形状的零件。
热压成型的步骤包括:1.将粉末材料放入模具中。
2.加热模具使粉末材料熔化或软化。
3.施加压力使粉末材料变形。
4.冷却模具并得到成型件。
热压成型的优点是成型密度高、强度好,但其成本较高,工艺复杂。
注塑成型注塑成型是将粉末材料通过注塑机进行成型的方法。
它适用于一些塑料粉末和橡胶粉末等可熔融的材料。
注塑成型的步骤包括:1.将粉末材料放入注塑机的料斗中。
2.通过螺杆将粉末材料加热熔化。
3.将熔化的材料注入模具中。
4.冷却模具并得到成型件。
注塑成型的优点是成型速度快、成型精度高,但其设备和模具成本较高。
烧结成型烧结成型是将粉末材料通过烧结过程进行成型的方法。
烧结是指将粉末材料加热至接近熔点的温度,使其颗粒之间发生结合,形成固体材料的过程。
烧结成型的步骤包括:1.将粉末材料放入模具中。
2.加热模具使粉末材料烧结。
3.冷却模具并得到成型件。
烧结成型的优点是成型密度高、强度好,适用于一些难以通过其他成型方法获得高密度材料的情况。
3D打印3D打印是一种近年来发展迅速的粉末材料成型方法。
碳酸钙压制成型的原理

碳酸钙压制成型的原理
碳酸钙压制成型的原理是在一定温度、压力下,使碳酸钙粉末附着在一起形成块状体。
在这个过程中,粉末在热胀冷缩的作用下逐渐凝结成一定形状的块状体,其原理与土壤固结相似。
具体来说,碳酸钙压制成型需要将碳酸钙粉末填充到模具中,然后通过加热和压力使其凝结成块状体。
压制时,粉末粒子之间的内聚力会增加,这使得粉末凝结成块状体的能力增强。
同时,通过提高温度和施加压力,可以加速碳酸钙粉末的热胀冷缩过程,使得块状体的增长速度更快。
另一种成型方法是碳酸钙粉干压成型,这种方法是将碳酸钙粉料与粘合剂混合后,通过加压使粉粒在模具内相互靠近并结合,形成一定形状的坯体。
这种方法常用于制备具有一定形状和强度要求的碳酸钙坯体。
以上信息仅供参考,如有需要,建议咨询专业技术人员。
大颗粒球形粉体材料的成型与压制工艺

大颗粒球形粉体材料的成型与压制工艺引言大颗粒球形粉体材料的成型与压制工艺广泛应用于各个领域。
这种工艺能够通过控制颗粒的形状和尺寸,使得材料具有更好的物理性能和机械性能。
本文将详细介绍大颗粒球形粉体材料的成型与压制工艺的原理、方法和优势。
一、工艺原理大颗粒球形粉体材料的成型与压制工艺的原理基于粉末冶金技术。
首先,粉末材料被制备成为球形颗粒。
然后,通过力的作用将这些颗粒聚集在一起形成所需的形状,最后通过适当的温度和压力进行烧结,使得颗粒之间结合成为固体材料。
二、工艺步骤1. 球形颗粒制备:首先,选取合适的原料,经过混合、球磨、筛分等步骤,使得原料粉末成为均匀的、具有一定粒径分布的粉末。
然后,将粉末投入球形颗粒制备设备中,通过旋转、喷雾、滚动等方式使得粉末逐渐形成球形颗粒。
2. 成型:将球形颗粒制备好的材料倒入成型模具中,施加足够的压力进行成型。
一般情况下,成型压力会根据原料的特性和所需的形状进行调整,以确保成型后的材料具有良好的致密性和机械性能。
3. 烧结:成型后的材料还需要进行烧结,以进一步增加其结晶度和力学性能。
烧结过程中,材料通常会经历高温处理,使得颗粒之间发生结合,形成固体材料。
烧结温度和时间的选择与原料的成分和特性相关,需要经过试验和实际操作来确定。
三、工艺优势大颗粒球形粉体材料的成型与压制工艺具有许多优势,使得它被广泛应用于各个领域。
1. 较好的致密性:通过粉末的成型与压制工艺,材料的颗粒之间实现了更好的贴合和结合,使得成型后的材料具有较高的致密性。
这样可以提高材料的强度和硬度,使其在应力和环境变化下更加稳定。
2. 良好的机械性能:大颗粒球形粉体材料的成型与压制工艺能够使材料的颗粒在成型过程中达到更好的排列和排布状态,从而提高了材料的力学性能。
材料在压缩、弯曲和拉伸等加载条件下表现出更好的弹性和韧性。
3. 粒径控制能力强:通过粉末制备和成型过程中的工艺调控,可以精确地控制颗粒的大小和分布。
粉末冶金工艺的基本工序(三篇)
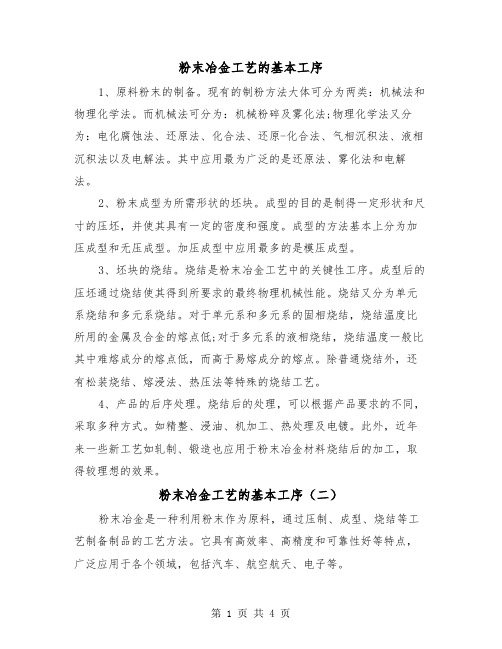
粉末冶金工艺的基本工序1、原料粉末的制备。
现有的制粉方法大体可分为两类:机械法和物理化学法。
而机械法可分为:机械粉碎及雾化法;物理化学法又分为:电化腐蚀法、还原法、化合法、还原-化合法、气相沉积法、液相沉积法以及电解法。
其中应用最为广泛的是还原法、雾化法和电解法。
2、粉末成型为所需形状的坯块。
成型的目的是制得一定形状和尺寸的压坯,并使其具有一定的密度和强度。
成型的方法基本上分为加压成型和无压成型。
加压成型中应用最多的是模压成型。
3、坯块的烧结。
烧结是粉末冶金工艺中的关键性工序。
成型后的压坯通过烧结使其得到所要求的最终物理机械性能。
烧结又分为单元系烧结和多元系烧结。
对于单元系和多元系的固相烧结,烧结温度比所用的金属及合金的熔点低;对于多元系的液相烧结,烧结温度一般比其中难熔成分的熔点低,而高于易熔成分的熔点。
除普通烧结外,还有松装烧结、熔浸法、热压法等特殊的烧结工艺。
4、产品的后序处理。
烧结后的处理,可以根据产品要求的不同,采取多种方式。
如精整、浸油、机加工、热处理及电镀。
此外,近年来一些新工艺如轧制、锻造也应用于粉末冶金材料烧结后的加工,取得较理想的效果。
粉末冶金工艺的基本工序(二)粉末冶金是一种利用粉末作为原料,通过压制、成型、烧结等工艺制备制品的工艺方法。
它具有高效率、高精度和可靠性好等特点,广泛应用于各个领域,包括汽车、航空航天、电子等。
粉末冶金工艺的基本工序包括粉末选料、混合、成型、烧结等。
首先是粉末选料。
粉末冶金工艺中所用的粉末要求颗粒细小、纯度高、形状均匀。
常见的粉末材料包括金属、陶瓷和合金等。
粉末选料的过程中需要考虑到材料的物理化学性质,并进行相应的测试和分析。
接下来是粉末的混合。
混合是将不同种类的粉末按一定比例混合在一起,以获得所需的材料性能。
混合可以通过机械混合、化学方法和物理方法等进行。
在混合过程中,需要控制混合时间和混合速度,以保证混合的均匀性。
然后是成型。
成型是将混合好的粉末放入模具中进行压制或注塑成型。
新型无机材料:无机材料成型技术
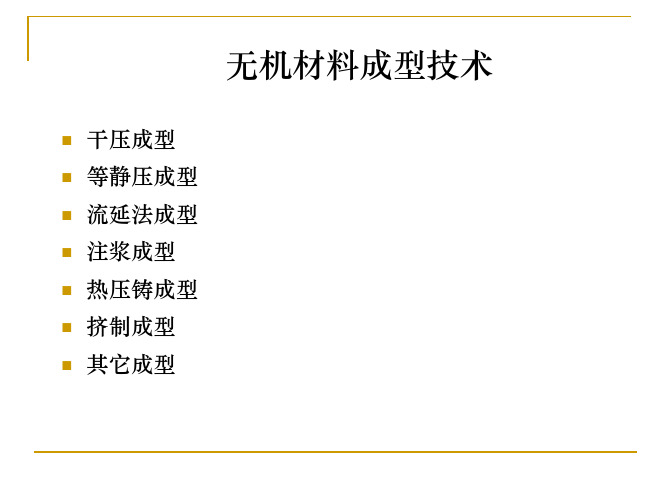
粉料本征特性
堆集方式 最大填充率为面心立方密堆或六方密堆(74.05%) 简立方堆集 (52.36%) 振动: 可提高堆积密度
粒径配比 大小球搭配, 可能的填充率越高
流动性
粒形圆润,流动性好,可获得较大填充密度
加压方式
单向加压 一端加压, 受压面密度大, 未加压端密度小
双向加压:坯体两边受压,两端密度大,中间密度小 改进的双向加压:
乙烯醇单体不存在,PVA由聚醋酸 乙烯(PVAc)皂化而成。 含大量亲水性羟基,是水溶性物质
(成本1~1.2万元/吨)
皂化PVAc, 生成粉状PVA, PVA溶于乙 醇或甲醇中, 加入酸催化剂和丁醛, 进行缩聚反应而成。
含羟基、乙酰基和羧基 可溶于极性和非极性溶剂中。
(成本9.5万元/吨)
纤维素基团:n×C6H10O5 含有大量羟基,大多数水溶性
和粒径。一般制备的晶粒具有严重的团聚现象 粉体处理(搅拌磨、振动磨、滚动磨)
打开颗粒团聚体,获得窄颗粒尺寸分布的粉料
硬团聚的ZrO2粉末颗粒的电子显微照片
浆料制备
流延浆料配制是流延成型技术的关键: (1) 合适的流动性, (2) 分散特性, (3) 良好的干燥特性, (4) 易加工性
分散剂
浆
增塑剂
流延设备
流延机是流延成型主要设备ቤተ መጻሕፍቲ ባይዱ其结构示意图如下
实验流延机
流延厚度
研究发现,流延干坯片的厚度D与各种流延参数的关系为:
D h (1 h2P ) 2 6 v0 L
其中α为湿坯干燥时厚度的收缩系数,h和L分别是刮刀刀刃间 隙的高度和长度,η为浆料粘度,△P为料斗中的压力,而v0为载 体线速度 厚 膜: 刮刀口间隙↑料浆液面↑载体线速↓料浆粘度↓ 薄膜:相反
- 1、下载文档前请自行甄别文档内容的完整性,平台不提供额外的编辑、内容补充、找答案等附加服务。
- 2、"仅部分预览"的文档,不可在线预览部分如存在完整性等问题,可反馈申请退款(可完整预览的文档不适用该条件!)。
- 3、如文档侵犯您的权益,请联系客服反馈,我们会尽快为您处理(人工客服工作时间:9:00-18:30)。
组员:杜高杰 程树林 刘唯俊 梅自寒 吴羿 吕萱萱 刘思佳
压制成型
• 压制成型 是将粉状的坯料在钢模中压成致密坯体(具有一 定形状、尺寸)的一种成型方法。 • 优点 压制成型工艺简单,生产效率高,缺陷少,便于连续 化、机械化和自动化生产。
成型工艺原理
• 将分散的固体颗粒通过外力使其最大限度地靠近,并通过 含有一定水分和其他粘结剂的表面,使物料颗粒间能形成 一定的键合(分子键、氢键),从而成为具有一定强度的 弹性体。
• 压制成型中坯体的密度变化和强度变化是两个核心问题。
密度的变化
强度的变化
压制成型只要问题是坯体中压力分布不均匀
产生的原因 颗粒移动重新排列时,颗粒之间产生内摩擦力, 颗粒与模壁之间产生外摩擦力,摩擦力妨碍着压力的传递。 (最均匀的加压方式) 等静压成型 粉料的各个方面同时均匀受压的一种加压方式。 压制出的坯体密度大且均匀。
压制成型对粉料的要求
• • • • ①体积密度 ②流度,以降低其压缩比。从两个方面进 行: • ①造粒 • 轮碾造粒:体积密度 0.90~1.10g/cm • 喷雾干燥:体积密度 0.75~0.90g/cm • ②调整颗粒级配 • 单一粒度的粉料堆积时最低孔隙率为40% • 三级颗粒配合,可降低孔隙率,获得更大的堆积密度。(如粗 颗粒50%,中颗粒10%,细颗粒40%,孔隙率仅23%)
压制设备
等静压设备
谢谢
流动性
• 粉料流动性好,颗粒间的内摩擦力小,重排致密化时也容 易滑移。 • 喷雾干燥 后的颗粒是圆形,流动性好。 • 烘干泥饼打碎 后的颗粒是多角形的,流动性差,很难致密 化。
含水率
粉料的含水率控制合适,可以获得极小的孔隙率。 粉料含水率 影响坯体的密度和收缩率 粉料水分分布的均匀程度 对坯体质量也有一定的影响,局 部过干或过湿都会使压制过程出现困难,随后的干燥和烧成 中容易产生开裂或变形。