钢结构构件制作与预拼装分解
《钢结构预拼装》课件
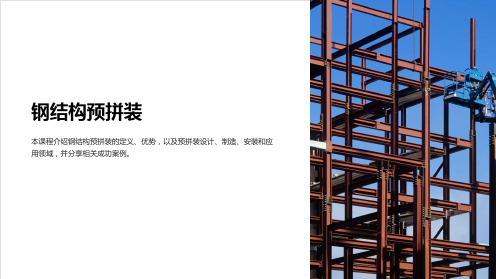
预拼装制造设备
介绍用于钢结构预拼装制造的自 动化设备和工具,提高生产效率 和质量。
预拼装制造技术
探讨钢结构预拼装中常用的焊接、 连接和拼装技术,确保构件的稳 固和安全性。
预拼装安装
1 预拼装构件的安装方 2 预拼装构件安装的注 3 预拼装安装案例分析
3 优势与挑战
总结钢结构预拼装的优势和面临的挑战,为业界提供启示和思考。
钢结构预拼装
本课程介绍钢结构预拼装的定义、优势,以及预拼装设计、制造、安装和应 用领域,并分享相关成功案例。
钢结构预拼装的定义
钢结构预拼装是一种将钢结构构件在工厂中预先拼装好,然后运输到现场进 行安装的建筑方法。它通过优化工序、提高质量和效率,成为现代建筑领域 的重要技术。
钢结构预拼装的优势
• 缩短工期,加快项目进展。 • 减少现场施工,降低劳动力成本。 • 确保质量和安全。 • 可重复使用,环保节能。
预拼装设计
1
预拼装设计流程
从结构设计到构件拼装顺序,通过协同设
拼装设计注意事项
2
计和优化,确保预拼装系统的完整性和稳 定性。
考虑现场施工条件和可能的运输限制,确
保钢结构构件的大小和重量满足要求。
3
预拼装设计案例分析
通过实际项目案例,展示成功的预拼装设 计方案,并分
式
意事项
分享成功的预拼装安装案
介绍常见的预拼装构件的
解释在安装过程中需考虑
例,并讨论其中的挑战和
安装方法,如吊装、拼接
的因素,如施工工艺、安
解决方案。
和连接。
全性要求和环境限制。
预拼装的应用
建筑结构
钢构件的组装及预拼装
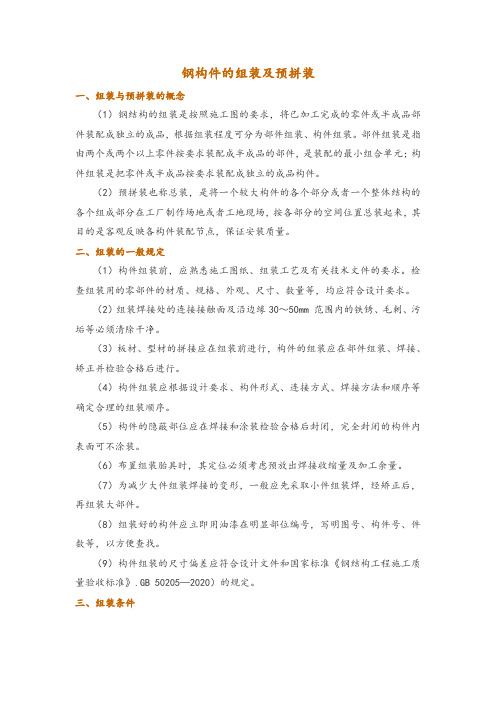
钢构件的组装及预拼装一、组装与预拼装的概念(1)钢结构的组装是按照施工图的要求,将已加工完成的零件或半成品部件装配成独立的成品,根据组装程度可分为部件组装、构件组装。
部件组装是指由两个或两个以上零件按要求装配成半成品的部件,是装配的最小组合单元;构件组装是把零件或半成品按要求装配成独立的成品构件。
(2)预拼装也称总装,是将一个较大构件的各个部分或者一个整体结构的各个组成部分在工厂制作场地或者工地现场,按各部分的空间位置总装起来,其目的是客观反映各构件装配节点,保证安装质量。
二、组装的一般规定(1)构件组装前,应熟悉施工图纸、组装工艺及有关技术文件的要求。
检查组装用的零部件的材质、规格、外观、尺寸、数量等,均应符合设计要求。
(2)组装焊接处的连接接触面及沿边缘30~50mm 范围内的铁锈、毛刺、污垢等必须清除干净。
(3)板材、型材的拼接应在组装前进行,构件的组装应在部件组装、焊接、矫正并检验合格后进行。
(4)构件组装应根据设计要求、构件形式、连接方式、焊接方法和顺序等确定合理的组装顺序。
(5)构件的隐蔽部位应在焊接和涂装检验合格后封闭,完全封闭的构件内表面可不涂装。
(6)布置组装胎具时,其定位必须考虑预放出焊接收缩量及加工余量。
(7)为减少大件组装焊接的变形,一般应先采取小件组装焊,经矫正后,再组装大部件。
(8)组装好的构件应立即用油漆在明显部位编号,写明图号、构件号、件数等,以方便查找。
(9)构件组装的尺寸偏差应符合设计文件和国家标准《钢结构工程施工质量验收标准》.GB 50205—2020)的规定。
三、组装条件在进行部件或构件组装时,无论采取何种方法,都必须具备支撑、定位和夹紧三个基本条件,俗称组装三要素。
(1)支撑是解决工件放置位置的问题。
而实质上,支撑就是组装工作的基准面。
用何种基准面作为支撑,需根据工件的形状大小和技术要求,以及作业条件等因素确定。
图8-8所示为H形梁的组装平台,是以平台作为支撑的。
钢结构安装工程施工方案

钢结构安装工程施工方案一、施工前期准备施工图纸会审与技术交底:详细审查施工图纸,明确工程要求及细节。
组织技术交底会议,确保施工人员对图纸、工艺要求有深刻理解。
材料准备:根据设计图纸要求,提前采购和储备所需的钢材、焊接材料、紧固件等,确保材料质量满足国家相关标准。
现场准备:确保施工现场“三通一平”(水通、电通、路通、场地平整),搭设临时设施,如仓库、办公区、生活区等。
人员培训:对施工人员进行安全教育和技术培训,确保施工人员具备相应的操作技能和安全意识。
二、钢结构制作钢材加工:按照图纸要求,进行钢材的切割、矫正、预制等工作,确保尺寸准确、表面平整。
构件组装:按照设计要求进行构件的组装,确保各部件之间配合紧密,尺寸准确。
预拼装:在车间内对构件进行预拼装,检查构件间的连接、尺寸等是否满足设计要求。
三、钢结构安装基础验收:确认基础工程符合设计要求,无沉降、变形等问题。
构件吊装:选择合适的吊装设备,按照吊装方案进行构件的吊装。
高位拼装:在施工现场进行构件的高位拼装,确保各部件之间的连接准确、紧固。
四、焊接工艺焊接材料选择:根据钢材材质和焊接要求,选择适当的焊接材料和焊接方法。
焊工培训:确保焊工具备相应的操作技能和资格证书,焊接前进行试焊,确保焊接质量。
焊接过程控制:焊接过程中,严格控制焊接速度、温度、电流等参数,确保焊缝质量。
五、安全操作规程施工现场应设置明显的安全警示标志,确保施工人员遵守安全规定。
施工人员应佩戴安全防护用品,如安全帽、安全带、防护眼镜等。
高空作业应设置安全网、安全护栏等设施,确保施工人员安全。
施工现场应定期进行安全检查,及时发现和排除安全隐患。
六、质量控制措施建立健全质量管理体系,明确质量目标和责任分工。
对进场材料进行严格检查,确保材料质量满足国家相关标准。
施工过程中,进行定期的质量检查和验收,确保各道工序质量合格。
对不合格品进行标识、隔离和处理,防止不合格品流入下道工序。
七、工程验收与交付工程完成后,组织相关部门进行验收,确保工程质量和安全符合设计要求。
钢结构七大生产流程
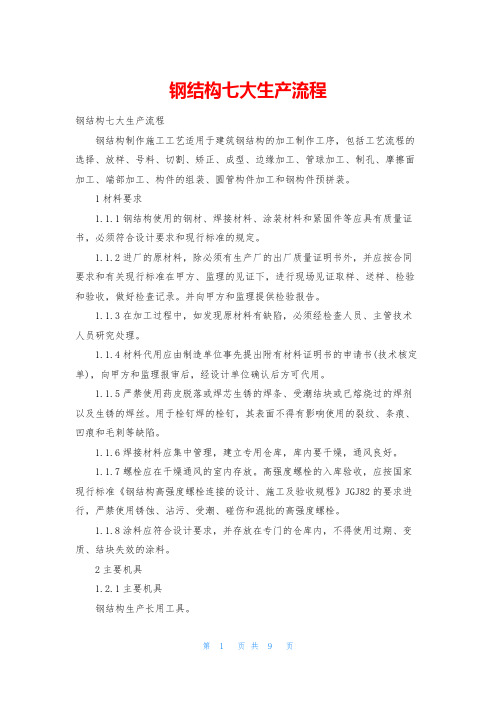
钢结构七大生产流程钢结构七大生产流程钢结构制作施工工艺适用于建筑钢结构的加工制作工序,包括工艺流程的选择、放样、号料、切割、矫正、成型、边缘加工、管球加工、制孔、摩擦面加工、端部加工、构件的组装、圆管构件加工和钢构件预拼装。
1材料要求1.1.1钢结构使用的钢材、焊接材料、涂装材料和紧固件等应具有质量证书,必须符合设计要求和现行标准的规定。
1.1.2进厂的原材料,除必须有生产厂的出厂质量证明书外,并应按合同要求和有关现行标准在甲方、监理的见证下,进行现场见证取样、送样、检验和验收,做好检查记录。
并向甲方和监理提供检验报告。
1.1.3在加工过程中,如发现原材料有缺陷,必须经检查人员、主管技术人员研究处理。
1.1.4材料代用应由制造单位事先提出附有材料证明书的申请书(技术核定单),向甲方和监理报审后,经设计单位确认后方可代用。
1.1.5严禁使用药皮脱落或焊芯生锈的焊条、受潮结块或已熔烧过的焊剂以及生锈的焊丝。
用于栓钉焊的栓钉,其表面不得有影响使用的裂纹、条痕、凹痕和毛刺等缺陷。
1.1.6焊接材料应集中管理,建立专用仓库,库内要干燥,通风良好。
1.1.7螺栓应在干燥通风的室内存放。
高强度螺栓的入库验收,应按国家现行标准《钢结构高强度螺栓连接的设计、施工及验收规程》JGJ82的要求进行,严禁使用锈蚀、沾污、受潮、碰伤和混批的高强度螺栓。
1.1.8涂料应符合设计要求,并存放在专门的仓库内,不得使用过期、变质、结块失效的涂料。
2主要机具1.2.1主要机具钢结构生产长用工具。
3作业条件1.3.1完成施工详图,并经原设计人员签字认可。
1.3.2施工组织设计、施工方案、作业指导书等各种技术准备工作已经准备就绪。
1.3.3各种工艺评定试验及工艺性能试验和材料采购计划已完成。
1.3.4主要材料已进厂。
1.3.5各种机械设备调试验收合格。
1.3.6所有生产工人都进行了施工前培训,取得相应资格的上岗证书。
4操作工艺1.4.1工艺流程1.4.2操作工艺1放样、号料1)熟悉施工图,发现有疑问之处,应与有关技术部门联系解决。
钢桁架结构构件预拼装施工工艺

1、构件拼装清单与胎架、场地的准备1.1 工厂拼装构件清单为了确定工厂拼装构件的类型和数量,必须对本工程构件和现场安装特点作一分析。
工厂制作的构件可能对现场安装带来最大的潜在影响和需考虑的因素有:各梁,特别是主梁和收边环梁牛腿空间位置不准确,导致现场安装不上。
复杂的铸钢件节点牛腿空间位置不准确,同样导致现场安装不上。
对于主桁架HJ-2在制作时,作为一个整体拼装,然后分开,故不进行二次拼装。
铸钢节点基本超长超宽,在现场进行预拼装比较合适。
综合以下因素考虑,确定工厂拼装构件如下:1.2拼装胎架和拼装的准备对于本工程而言,预拼装主要是针对制作单元,因些胎架的准备基本相同,同时由于主梁及牛腿空间位置的不确定性,胎架需具有可调的特点,下图为拟使用的胎架。
图4.12-1 拼接胎架示意图通过对各制作单元的尺寸分析,其常规尺寸如下:上下可调式专用胎架上部挡块胎架一:可调式专用胎架,用于主梁的下部支胎架二:普通胎架,用于次梁的支撑调节机构调节螺杆胎架三:普通可调式胎架,用于次梁图4.12-2 制作单元尺寸示意图2、工厂预拼装和现场拼装方案2.1工厂预拼装流程图4.13-1 工厂预拼装流程图2.2具体拼装示意图从整体上分析,工厂拼装有两种方案;一种是先次梁→定位主梁→定位铸钢件节点,另一种是先定位铸钢件节点→主梁→定位次梁。
由于采用的是单元拼装,从尺寸的准确度上,采用第一种比较好一些,能够较准确判断铸钢件和主梁牛腿的准确度。
下面是现场安装第一榀的工厂预拼装示意图:第三步:从一侧依次拼装主梁第四步:从一侧依次拼装铸钢件第一步:根据第一榀的尺寸特点,在非牛腿处布置胎架第二步:从一侧依次拼装次梁图4.13-2 现场安装第一榀的工厂预拼装示意图第六步:利用采集的各特征点三坐标数据,计算机重构模型,相关原理详见“三坐标测量系统与模型计算机重构技术”应用实例: 国家体育场拼装场地,利用三坐标测量系统,拼装构件进行扫描第七步:利用测量系统分析软件,对各点与理论点坐标比较,然后进行调整第八步:对对接口作好对接标志,折除发运第五步: 利用三坐标测量系统,对构件进行扫描 应用实例: 国家体育场工程中,利用三坐标测量系统,对弯扭构件进行扫描鉴于工地现场拼装主要的工作是吊装件的拼装,因此现场拼装相关内容见钢结构吊装、安装方案。
钢结构预拼装
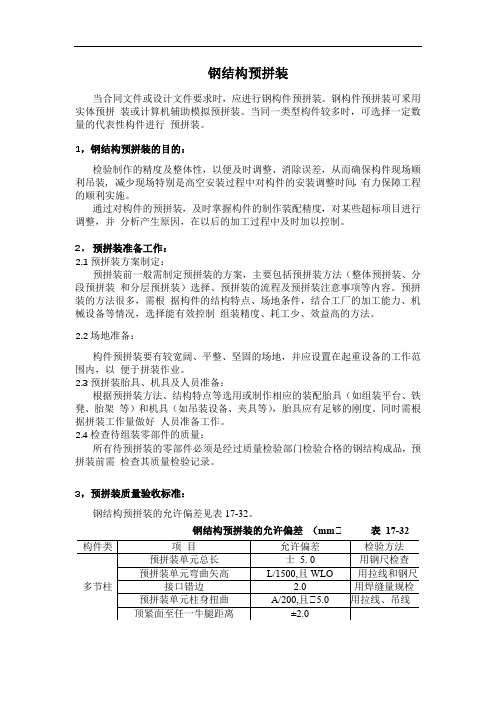
钢结构预拼装
当合同文件或设计文件要求时,应进行钢构件预拼装。
钢构件预拼装可釆用实体预拼装或计算机辅助模拟预拼装。
当同一类型构件较多时,可选择一定数量的代表性构件进行预拼装。
1,钢结构预拼装的目的:
检验制作的精度及整体性,以便及时调整、消除误差,从而确保构件现场顺利吊装, 减少现场特别是高空安装过程中对构件的安装调整时间,有力保障工程的顺利实施。
通过对构件的预拼装,及时掌握构件的制作装配精度,对某些超标项目进行调整,并分析产生原因,在以后的加工过程中及时加以控制。
2,预拼装准备工作:
2.1预拼装方案制定:
预拼装前一般需制定预拼装的方案,主要包括预拼装方法(整体预拼装、分段预拼装和分层预拼装)选择、预拼装的流程及预拼装注意事项等内容。
预拼装的方法很多,需根据构件的结构特点、场地条件,结合工厂的加工能力、机械设备等情况,选择能有效控制组装精度、耗工少、效益高的方法。
2.2场地准备:
构件预拼装要有较宽阔、平整、坚固的场地,并应设置在起重设备的工作范围内,以便于拼装作业。
2.3预拼装胎具、机具及人员准备:
根据预拼装方法、结构特点等选用或制作相应的装配胎具(如组装平台、铁凳、胎架等)和机具(如吊装设备、夹具等),胎具应有足够的刚度。
同时需根据拼装工作量做好人员准备工作。
2.4检查待组装零部件的质量:
所有待预拼装的零部件必须是经过质量检验部门检验合格的钢结构成品,预拼装前需检查其质量检验记录。
3,预拼装质量验收标准:
钢结构预拼装的允许偏差见表17-32。
钢结构预拼装的允许偏差(mm)表17-32。
钢结构预制与预拼装
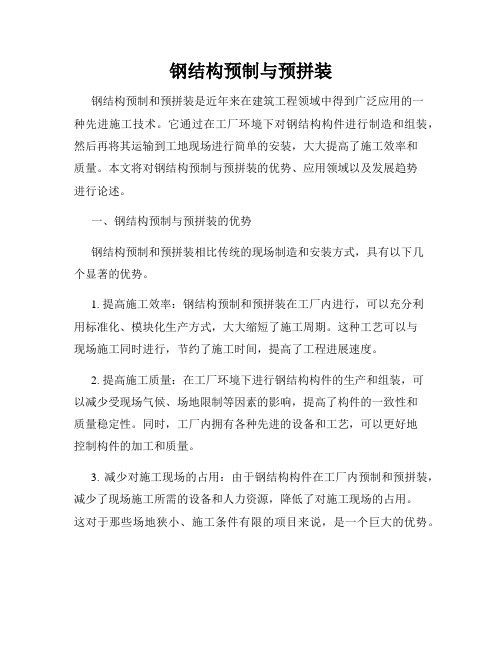
钢结构预制与预拼装钢结构预制和预拼装是近年来在建筑工程领域中得到广泛应用的一种先进施工技术。
它通过在工厂环境下对钢结构构件进行制造和组装,然后再将其运输到工地现场进行简单的安装,大大提高了施工效率和质量。
本文将对钢结构预制与预拼装的优势、应用领域以及发展趋势进行论述。
一、钢结构预制与预拼装的优势钢结构预制和预拼装相比传统的现场制造和安装方式,具有以下几个显著的优势。
1. 提高施工效率:钢结构预制和预拼装在工厂内进行,可以充分利用标准化、模块化生产方式,大大缩短了施工周期。
这种工艺可以与现场施工同时进行,节约了施工时间,提高了工程进展速度。
2. 提高施工质量:在工厂环境下进行钢结构构件的生产和组装,可以减少受现场气候、场地限制等因素的影响,提高了构件的一致性和质量稳定性。
同时,工厂内拥有各种先进的设备和工艺,可以更好地控制构件的加工和质量。
3. 减少对施工现场的占用:由于钢结构构件在工厂内预制和预拼装,减少了现场施工所需的设备和人力资源,降低了对施工现场的占用。
这对于那些场地狭小、施工条件有限的项目来说,是一个巨大的优势。
4. 节约材料:钢结构预制和预拼装可以通过优化设计和提高材料利用率,达到节约材料的效果。
在工厂环境下,材料浪费较少,能够最大限度地减少资源消耗。
二、钢结构预制与预拼装的应用领域钢结构预制与预拼装技术广泛应用于各个领域的建筑工程项目,包括但不限于以下几个方面。
1. 住宅建筑:钢结构预制与预拼装技术在住宅建筑领域得到广泛应用。
通过工厂生产和预制,可以快速组装出标准化的住宅构件,提高了施工效率,缩短了交房时间。
2. 商业建筑:商业建筑项目通常具有大跨度、复杂结构的特点,钢结构预制和预拼装技术可以灵活应用于各种商业建筑类型,如购物中心、办公楼等。
该技术能够提高施工速度,满足时间紧迫的项目要求。
3. 工业建筑:工业建筑常常需要大面积的空间,钢结构预制和预拼装技术可以有效应对这一需求。
通过工厂生产的构件,可以迅速组装成大跨度、大空间的工业建筑,提高了施工效率和质量。
单元6-钢构件组装和预拼装4ppt课件(全)

3. 选择装配基准
装配基准的选择直接关系到装配的全部工艺过程。正确地选择装配基准能使夹具的 结构简单,工件定位比较容易,夹紧牢靠,操作方便。 对各种结构都要作具体分析,选择的基准不同其装配方法也不一样。以构件的底面 为基准采用的是正装,以顶面为基准的可进行反装,以侧面为基准则需作倒装。即 使是同一构件,由于装配基准不同,装配方法变化也很大。
6.1.8 钢构件组装质量检验
1. 构件焊接质量允许偏差 ⑴ 构件焊缝坡口的允许偏差应符合表 6-4 的规格。 ⑵ 焊接 H 型钢的翼缘板和腹板拼接缝的间距应不小于 200 ㎜.翼缘板拼接长度应不 小于 2 倍板宽,腹板拼接宽度应不小于 300 ㎜,长度应不小于 600 ㎜。 ⑶ 焊接 H 型钢的允许偏差应符合《钢结构工程施工质量验收规范》 (GB 50205-2001) 附录 C 中表 C.0.1 的规定。 ⑶ 端部铣平的允许偏差应符合表 6-5 的规定。外露铣平面应防锈保护。 ⑷ 焊接连接组装的允许偏差应符合《钢结构工程施工质量验。顶紧接触面应有 75﹪以上的面积紧贴。 (5)桁架结构杆件轴线交点错位的允许偏差不得大于 3.0 ㎜。 2. 钢构件外形尺寸允许偏差 ⑴ 钢构件外形尺寸主控项目的允许偏差应符合表 6-6 的规定。 ⑵ 钢构件外形尺寸一般项目的允许偏差应符合《钢结构工程施工质量验收规范》(GB 50205-2001)附录 C 中表 C.0.3~表 C.0.9 的规定。
6.1.2 装配条件
1. 支承 支承是解决工件放置何处装配的问题。而实质上,支承就是装配工作的基准面。用 何种基准面作为支承,要根据工件的形状大小和技术要求,以及作业条件等因素确 定。图 6-1 所示为工字形梁的装配,是以平台 6 作支承的。 2. 定位 定位就是确定零件在空间的位置或零件间的相对位置。只有在所有零件都达到确定 位置时,整体结构才能满足设计上的各种要求。图 6-1 所示,工字形梁的两翼板的 相对位置由腹板与挡板来定位,而腹板的高低位置是由垫块来定位的。 3. 夹紧 夹紧是定位的保障,它以借助外力将定位后的零件固定为目的。这种外力即为夹紧 力。 夹紧力通常由刚性夹具来实现,也可以利用气压力或液压力进行。图 6-1 中翼板与 腹板间的夹紧力是由调节螺杆产生的。
- 1、下载文档前请自行甄别文档内容的完整性,平台不提供额外的编辑、内容补充、找答案等附加服务。
- 2、"仅部分预览"的文档,不可在线预览部分如存在完整性等问题,可反馈申请退款(可完整预览的文档不适用该条件!)。
- 3、如文档侵犯您的权益,请联系客服反馈,我们会尽快为您处理(人工客服工作时间:9:00-18:30)。
加工边直线度
l/3000 ,且
不应大于2.0
加工面表面粗糙 度
相邻两边夹角
±6′
注: t构件厚度
➢制孔
1.钻孔
2.冲孔
3.扩孔 4.锪孔
5.制孔精度
6.孔距要求
螺栓孔距范围
≤500
同一组内任意两孔间距离
±1.0
相邻两组的端孔间距离
±1.5
501~1200 ±1.5 ±2.0
6~14 0.1~0.3
15~30 0.4~0.5
30~40 0.5~0.6
➢ 冲裁下料
(a)倾斜式; (b)非倾斜式 两种不同圆盘剪切的装置
(a)
冲裁
(b)
1—凸模;2—板料;3—凹模;4—冲床工作台
➢ 气割下料
(1)气割条件 (2)手工气割操作要点
1)气割前的准备 2)气割操作
(a)预热
(b)上提 (c)吹渣 图 手工气割
7 弯曲样板 各种压型件及制作胎模零件的检查标准
➢覆盖和过样
样板、样杆制作尺寸的允许偏差
项目
长度
样板
宽度
两对角线长度差
样杆
长度 两最外排孔中心线距离
同组内相邻两孔中心线距离
相邻两组端孔间中心线距离
加工样板的角度
(单位:mm)
容许偏差 0 -0.5 5.0-0.5 1.0 1.0 1.0 0.5 1.0 20′
(d)切割
矫正和成型
➢1.型钢机械矫正
(a)
(b)
(a)撑直机矫直角钢; (b) 撑直机(或压力机)矫直工字钢
机械矫正型钢
1、2—支承;3—推撑;4—型钢;5—平台
(a)
(b)
(a) 扳弯器矫直工字钢 (b) 手扳压力机示意图 手动机械矫直型钢
➢2.型钢半自动机械矫正 扳弯器矫正型钢 手扳压力机械矫正型钢 千斤顶矫正型钢 ➢3.型钢手工矫正
切割面平面度示意图
切割面割纹深度示意图
机械剪切面的边缘缺棱示意图
剪切面的垂直度示意
➢ 剪切下料
➢ (1)在斜口剪床上剪切 ➢ (2)在龙门剪床上剪切 ➢ (3)在圆盘管剪切机上剪切 ➢ (4)剪切对钢材质量的影响
斜口剪床上、下刀片之间的间隙 (单位:mm)
钢板厚度 刀片间隙
<5 0.08~0.09
➢ 辅助材料的检验:钢结构用辅助材料包括螺栓、电焊条、焊 剂、焊丝等,均应对其化学成分、力学性能及外观进行检验, 并应符合国家有关标准。
➢ 堆放:检验合格的钢材应按品种、牌号、规格分类堆放,其 底部应垫平、垫高,防止积水。钢材堆放不得造成地基下陷
和钢材永久变形。
放样和下料
➢ 加工余量 : (1)自动气割切断的加工余量为3mm;手工气割切断的加工余量 为4mm;气割后需铣端或刨边者,其加工余量为4~5mm。 (2)剪切后无需铣端或刨边的加工余量为零。 (3)对焊接结构零件的样板,除放出上述加工余量外,还须考虑 焊接零件的收缩量,一般沿焊缝长度纵向收缩率为0.03%~0.2%; 沿焊缝宽度横向收缩,每条焊缝为:0.03~0.75mm;加强肋的 焊缝引起的构件纵向收缩,每肋每条焊缝为0.25mm。
钢结构构件制作与预拼装
主要内容:
➢ 熟悉钢结构制作过程;熟悉钢结构构件放样 下料过程;
➢ 掌握钢结构矫正成型以及边缘加工过程; ➢ 熟悉钢结构构件预拼装施工过程。
学习目标:
➢ 通过理论教学,熟悉钢结构构件放样和下料的 基本内容;掌握钢结构构件矫正成型和钢结构 构件边缘加工过程,熟悉钢结构构件预拼装施 工过程。
无齿锯
切割速度快,可切割不同形状、不同对的各类型钢、钢管和钢板,切口不 光洁,噪声大,适于锯切精度要求较低的构件或下料留有余量最后尚需精 加工的构件
砂轮锯
切口光滑、生刺较薄易清除、噪声大,粉尘多,适于切割薄壁型钢及小型 钢管,切割材料的厚度不宜超过4mm
锯床
功割精度高,适于切割各类型钢及粱、柱等型钢构件
钢结构的制作
钢结构制作的特点
➢ 钢结构制作的特点:件优、标准严、精度好、效 率高。
➢ 钢结构制作的依据:设计图和国家规范 。
钢材的准备
➢ 钢材材质的检验 :结构用钢的力学性能中屈服点、抗拉强 度、延伸率、冷弯试验、低温冲击韧性试验值等指标应符合 规范的要求 。
➢ 钢材外形的检验 :对于钢板、型钢、圆钢、钢管,其外形 尺寸与理论尺寸的偏差必须在允许范围内。
(a)大小面上下弯曲的矫正;(b)大小面侧向弯曲矫正 千斤顶矫正槽钢
(a)大于90°的矫正 (b) 小于90°的矫正 手工矫正角钢角度变形
➢4.型钢火焰矫正法
火焰加热的点状加热方式 (a)点状加热布局;(b)用点状加热矫正吊车梁腹板变形
1—点状加热点;2—梅花形布局
火焰加热的线状加热方式
火焰加热的三角形加热方式
除机械加工方法外,对要求不高的坡口亦可采用气 割或等离子弧切割方法。用自动或半自动气割机切割。 对于允许以碳弧气刨方法加工焊接坡口或焊缝背面清 根时,在保证气刨槽平直深度均匀的前提下可采用半 自动碳弧气刨。
边缘加工的允许偏差 (单位:mm)
项目 零件宽度、长度
允许偏差 ±1.0
项目 加工面垂直度
允许偏差
(a)线状加热方式;(b)用线状加热矫正板变形; (a)(b)角钢钢板的三角形加热方式;(c)(d)用
(c)用单加热带矫正H型钢梁翼缘角变形;
三角形加热矫正H型梁拱变形和旁弯曲变形
(d) 用双加热带矫正H型钢梁翼缘角变形;
t—板材厚度
边缘加工和制孔
边缘加工
边缘加工方法有:采用刨边机(或刨床)刨边、端面 铣床铣边、电弧气刨刨边、型钢切割机切边、半自动 机自动气割机切边、等离子弧纠割边、砂轮机磨边以 及风铲铲边等焊接坡口加工形式和尺寸应根据图样和 构件的焊接工艺进行。
切割
切割
➢ 一般规定
加工余量 锯切
切割缝
刨边 铣平
2~3 3~4
剪切
1 2~3 2~3
手工切割
半自动切 割
精密切割
4~5
3~4
2~3
3~4 4~5
1 2~3
1 2~3
各种切削方法分类比较
类别 机械切割
使用设备
特点及适用范围
剪板机 切割速度快、切口整齐、效率高,适用薄钢板,压型钢板、冷弯钢管的切 型钢冲剪机 削
顺序 样板名称
用途
1 平面样板 在板料及型钢平面进行划下料
2 弧形样板 检查各种圆弧及圆的曲率大小 3 切口样板 各种角钢、槽钢切口弯曲的划线标准 4 展开样板 各种板料及型材展开零件的实际长及形状
5 覆盖样板 按照放样图上(或实物上)图形用覆盖方法零件的孔心位置