高速CNC切削技术1
《高速切削》课件

本PPT课件将介绍高速切削的定义、原理、分类、技术、应用、注意事项以及 未来发展,为您展示全面的高速切削知识。
什么是高速切削?
高速切削的定义
高速切削是指在高速运动下切削金属材料的加工方 法。
高速切削的优点
高速切削具有高效率、高精度和优质表面等优点。
高速切削的原理
1 原理介绍
高速切削技术的趋势 和前景
高速切削技术正朝着更高效率、 更高精度和更环保的方向发展。
ቤተ መጻሕፍቲ ባይዱ
高速切削的未来发展
高速切削未来将在各行各业中得 到更广泛的应用和进一步的优化。
高速切削注意事项
1 高速切削的注意事项
高速切削过程中需注意刀具选择、润滑和安全等方面。
2 如何安全进行高速切削
安全进行高速切削需遵循正确的操作规程和戴好个人防护装备。
3 如何保证高速切削的质量
保证高速切削质量需要注意刀具磨损和加工参数等关键因素。
高速切削发展前景
高速切削的发展历程
高速切削技术经历了多年的发展 与创新。
高速切削利用切削工具对工件进行高速运动切削,实现金属材料的加工。
2 高速切削的工作过程
高速切削的工作过程包括进给运动、主轴转动和切削速度等因素。
3 高速切削的工作原理
高速切削通过防振、刀具材料和润滑等措施,提高切削效率和质量。
高速切削的分类
高速切削分类介绍
高速切削可分为铣削加工和车削 加工两种主要类型。
CNC技术在高速切削加工中起到关 键作用,实现自动化加工。
高速切削的应用
1
高速切削在现代制造中的应用
高速切削广泛应用于航空、汽车、船舶等
高速切削的优势和局限性
2
高速切削CNC系统的研究

rq ie n t fu m b ̄ e urme , rp 1 o
t r fC oeo NC,l e c itg ainwi ax n n e r t  ̄ e . o t hCAM . a n ep ltr dfe X Oc nr l r in rn we kitr oao e n e dS V tol ,g o a c e o e e o h n wn ifr t n. m tt s rbe , e ie d meh d o cb sd ac iet r ft k o no mai Ai a heep o lm n w d a e to fp — ae r tcu e e o n h
速进 给伺 服 系统 、 用 于高 速切 削 的 c 适 Nc系统 、
0 引言
与传 统数 控切 削加 工相 比 , 高速 切 削加 工 有 无 可 比拟 的优 越 性 : J
刀具 技术 、 刀夹 装置 及 快 速 刀具 交 换 技 术等 。 目 前有关高 速切 削 技术 的 文 献很 多 . 对 适 于 高速 但 切削的 口 系统却 鲜有报道 . 工业 界 一般也 认为 高速 切 削 c C与 普通 数 控 机床 的 C N NC一 样 , 只 是处理 速度 更 高而 已, 实 际上 这 是 有 着很 大 区 但
meh d. i el a l R d r p lg ie . t o o whc rai beh r waet oo y i gv n f h z o s Ke r s ih s ed c ti g; ywo d :hg -p e u t n CNC e d sro ̄p n ac i cu e fe e v o e r t t r h e
另的 。
() 1 单位 时间材料切除量增加 3 倍 , ~6 进给 速度提高 5 0 , ~1 倍 有利于提高生产率。 () 2 切削力减少 3 %左右, O 尤其是径 向切 削 力 大幅度 减 小 , 有利 于 改善 工 件加 工 精 度 和 表 面
高速切削报告-国内外现状

2、超高速切削加工优势
极大地提高了机床的生产率
随着切削速度的大幅度提高,进给速度也相应提 高5-10倍。这样,单位时间内的材料切除率可大大增 加,可达到常规切削的3-6倍,甚至更高; 同时机床快速空程速度的大幅度提高,也大大减 少了非切削的空行程时间,从而极大地提高了机床的 生产率。
降低切削力
大多数情况下,垂直力比水平力大,这和理论分析的 结果相反;
峰值切削力只增加了33%-70%,而不是预计的500 %,而且使用的平均力还会减小; 在高速切削下,剪切角增大而导致剪切力减小。
超高速切削加工 与传统的切削加工相比发生了质变
1.3 高速切削逐渐成熟
在20世纪70年代中期,美国科学家罗伯特·金 (Robert I.king)和麦克唐纳(Mcdonaid.J)着手 验证和发展沃汉(Vaughan)的研究结论。
存在的问题
1)刚度低、惯量大,难以获得高进给速度和高加速度 (速度很难超过60m/min、加速度很难超过1.5 g)。
2)非线性严重,不易实现闭环控制。
3)传动误差较大,影响机械加工精度。
4)机械传动链结构复杂,特别是在重型机和多坐标机 床中这个问题尤为突出。
5)机械噪声大。
6)传动效率低,一般0.6。
主要结论:
1)高速切削方面
在超高速条件下,高强度材料可以切削,切削速度可高 达1220m/s;
高速钢刀具可在这一速度下切削高强度材料;
加工合金材料的脆性失效现象在高速下并没有发生; 高速下的实验结果和通常的加工曲线计算的结果不一样; 超高速切削可提高工件的表面质量; 高速切削的金属加工切除率可高达普通切削的240倍。
先进制造工艺--高速切削技术
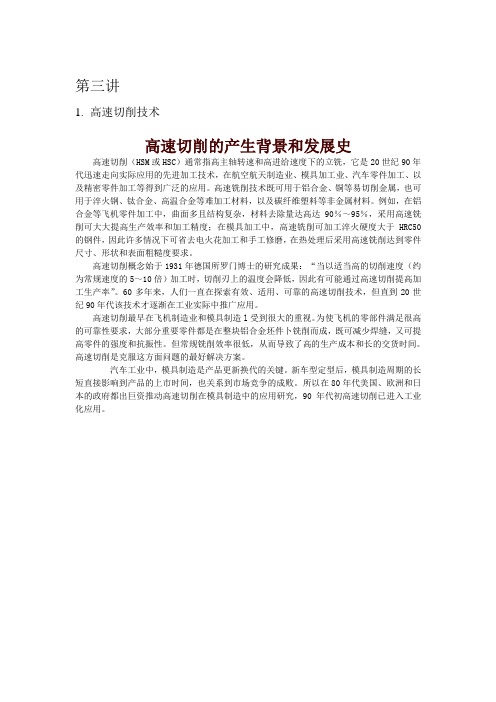
第三讲1.高速切削技术高速切削的产生背景和发展史高速切削(HSM或HSC)通常指高主轴转速和高进给速度下的立铣,它是20世纪90年代迅速走向实际应用的先进加工技术,在航空航天制造业、模具加工业、汽车零件加工、以及精密零件加工等得到广泛的应用。
高速铣削技术既可用于铝合金、铜等易切削金属,也可用于淬火钢、钛合金、高温合金等难加工材料,以及碳纤维塑料等非金属材料。
例如,在铝合金等飞机零件加工中,曲面多且结构复杂,材料去除量达高达90%~95%,采用高速铣削可大大提高生产效率和加工精度;在模具加工中,高速铣削可加工淬火硬度大于HRC50的钢件,因此许多情况下可省去电火花加工和手工修磨,在热处理后采用高速铣削达到零件尺寸、形状和表面粗糙度要求。
高速切削概念始于1931年德国所罗门博士的研究成果:“当以适当高的切削速度(约为常规速度的5~10倍)加工时,切削刃上的温度会降低,因此有可能通过高速切削提高加工生产率”。
60多年来,人们一直在探索有效、适用、可靠的高速切削技术,但直到20世纪90年代该技术才逐渐在工业实际中推广应用。
高速切削最早在飞机制造业和模具制造l受到很大的重视。
为使飞机的零部件满足很高的可靠性要求,大部分重要零件都是在整块铝合金坯件卜铣削而成,既可减少焊缝,又可提高零件的强度和抗振性。
但常规铣削效率很低,从而导致了高的生产成本和长的交货时间。
高速切削是克服这方面问题的最好解决方案。
汽车工业中,模具制造是产品更新换代的关键。
新车型定型后,模具制造周期的长短直接影响到产品的上市时间,也关系到市场竞争的成败。
所以在80年代美国、欧洲和日本的政府都出巨资推动高速切削在模具制造中的应用研究,90年代初高速切削已进入工业化应用。
图16 高速切削在生产应用中的发展历程图17 采用高速切削后产品质量提高的历程a一硬质合金切钢 b一硬质合金切铸铁c—CBN切铸铁图16是德国宝马公司(BMW)采用高速切削的历程。
高速切削加工技术ppt课件.pptx

我国高速切削加工技术最早应用于轿车工业,二十世纪八十年 代后期,相继从德国、美国、法国、日本等国引进了多条具有先进 水平的轿车数控自动化生产线,如从德国引进的具有九十年代中期 水平的一汽大众捷达轿车和上海大众桑塔纳轿车自动生产线,其中 大量应用了高速切削加工技术。生产线所用刀具材料以超硬刀具为 主,依靠进口。
近年来,我国航天、航空、汽轮机、模具等制造行业引进了 大量加工中心和数控镗铣床,都不同程度地开始推广应用高速切 削加工技术,其中模具行业应用较多。
例如上海某模具厂,高速铣削高精度铝合金模具型腔,半精 铣采用主轴转速18000rpm,切削深度2mm,进给速度5m/min; 精铣采用20000rpm,切削深度0.2mm,进给速度8m/min,加工 周期为6h,质量完全满足客户要求。
➢ 高速切削已成为当今制造业中一项快速发展 的新技术,在工业发达国家,高速切削正成 为一种新的切削加工理念。
➢ 人们逐渐认识到高速切削是提高加工效率的 关键技术。
高速切削的特点
➢ 随切削速度提高,单位时间内材料切除率增加,切削加工时间减 少,切削效率提高3~5倍。加工成本可降低20%-40%。
➢ 在高速切削加工范围,随切削速度提高,切削力可减少30%以上, 减少工件变形。对大型框架件、刚性差的薄壁件和薄壁槽形零件 的高精度高效加工,高速铣削是目前最有效的加工方法。
高速切削的加工工艺方法
目前高速切削工艺主要在车削和铣削,各类高速切削机床 的发展将使高速切削工艺范围进一步扩大,从粗加工到精加工 ,从车削、铣削到镗削、钻削、拉削、铰削、攻丝、磨削等。
随着市场竞争的进一步加剧,世界各国的制造业都将更加积 极地应用高速切削技术完成高效高精度生产。
高速切削加工在国内的研究与应用
先进制造技术 第2章 高速切削技术2-1
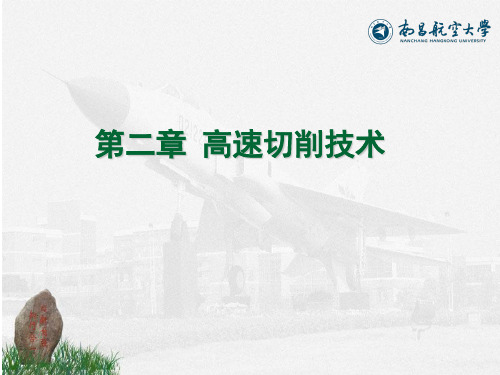
萨洛蒙在l924一1931年间,进行了一系列的高速切削实验: 在非黑色金属材料,如铝、铜和青铜上,用特大直径的刀 盘进行锯切,最高实验的切削速度曾达到14000m/min, 在各种进给速度下,使用了多达20齿的螺旋铣刀。l931年 申请了“超极限速度”专利,随后卖给了“Krupp钢与工 具制造厂”。 萨洛蒙和他的研究室实际上完成了大部分有色金属的切削 试验研究,并且推断出铸铁材料和钢材的相关曲线。 萨洛蒙理论提出了一个描述切削条件的区域或者是范围, 在这个区域内是不能进行切削的。萨洛蒙没有提出可靠的 理论解释,而且他的许多实验细节也没有人知道。
刀具磨损曲线
三、高速切削切屑形成
高速切削试验表明,工件材料及 性能对切屑形态 有决定性影响。
低硬度和高热物理性能的工件材料(铝合金、低碳钢、未 淬硬钢等)易形成连续带状切屑。 高硬度和低热物理性能的工件材料(钛合金钢、未淬硬钢 等)易形成锯齿状切屑。
切削速度对切屑形态有重要影响。对钛合金,在 (1.5~4800)m/min的切削速度范围内形成锯齿状 切屑,随切削速度的增加,锯齿程度(锯齿的齿 距)在增加,直至成为分离的单元切屑。
不同切削速度下车削45钢件的切削形态。
一方面,切削速度增加,应变速度加大,导致脆 性增加,易于形成锯齿状切屑;另一方面,切削 速度增加,切屑温度增加,导致脆性降低,不易 形成锯齿状切屑;
绝热剪切理论(Adiabatic Shear Theory) 周期脆性断裂理论(Periodic brittle fracture theoty)
萨洛蒙(Salomon)曲线
1600
切削温度/℃
钢
1200
青铜
铸铁 硬质合金980℃ Stelite合金850℃ 高速钢650℃ 碳素工具钢450℃
高速切削加工技术
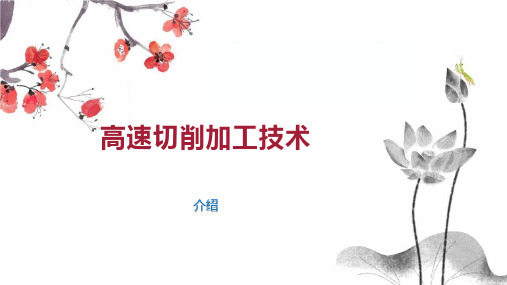
高速切削的适用性
高速切削的适用性
高速加工作为一种新的技术,其优点是显而易见的,它给传统的金属切削理论带来了一种革命性的变化。那 么,它是不是放之四海而皆准呢?显然不行。即便是在金属切削机床水平先进的瑞士、德国、日本、美国,对于这 一崭新技术的研究也还处在不断的摸索研究当中。实际上,人们对高速切削的经验还很少,还有许多问题有待于 解决:比如高速机床的动态、热态特性;刀具材料、几何角度和耐用度问题,机床与刀具间的接口技术(刀具的 动平衡、扭矩传输)、冷却润滑液的选择、CAD/CAM 的程序后置处理问题、高速加工时刀具轨迹的优化问题等等。
(1)CAM系统应具有很高的计算编程速度
高速加工中采用非常小的切给量与切深,故高速加工的NC程序比对传统数控加工程序要大得多,因而要求计 算速度要快,要方便节约刀具轨迹编辑,优化编程的时间。
(2)全程自动防过切处理能力及自动刀柄干涉检查能力
高速加工以传统加工近10倍的切削速度进行加工,一旦发生过切对机床、产品和刀具将产生灾难性的后果, 所以要求其CAM系统必须具有全程自动防过切处理的能力。高速加工的重要特征之一就是能够使用较小直径的刀 具,加工模具的细节结构。系统能够自动提示最短夹持刀具长度,并自动进行刀具干涉检查。
如此看来,主轴转速为10~r/min这样的高速切削在实际应用时仍受到一些限制: (1)主轴转速10~r/min时,刀具必须采用 HSK 的刀柄,外加动平衡,刀具的长度不能超过120mm,直径不 能超过16mm,且必须采用进口刀具。这样,在进行深的型腔加工时便受到限制。 (2)机床装备转速为10~r/min的电主轴时,其扭矩极小,通常只有十几个N·m,最高转速时只有5~6N·m。 这样的高速切削,一般可用来进行石墨、铝合金、淬火材料的精加工等。 (3)MIKRON公司针对这些情况开发了一些主轴最高转速为r/min、r/min、r/min和r/min的机床,尽力提高 进给量(~mm/min),以保证机床既能进行粗加工,又能进行精加工,既省时效率又高。
高速切削加工技术介绍

美国于 1960 年前后开始进行超高速切削试验。试验将刀具装在加农炮里,从滑台上射向工件;或将工件当作子弹射向固定的刀具。 1977 年美国在一台带有高频电主轴的加工中心上进行了高速切削试验,其主轴转速可以在 180 ~ 18000r / min 范围内无级变速,工作台的最大进给速度为 7 . 6m / min。
1979 年美国防卫技术研究总署( DARPA )发起了一项“先进加工研究计划”,研究切削速度比塑性波还要快的超高速切削,为快速切除金属材料提供科学依据。
在德国, 1984 年国家研究技术部组织了以 Darmstadt 工业大学的生产工程与机床研究所 PTW )为首,包括 41 家公司参加的两项联合研究计划,全面而系统地研究了超高速切削机瓜刀具、控制系统以及相关的工艺技术,分别对各种工件材料(钢、铸铁、特殊合金、铝合金、铝镶铸造合金、铜合金和纤维增强塑料等)的超高速切削性能进行了深入的研究与试验,取得了切削热的绝大部分被切屑带走国际公认的高水平研究成果,并在德国工厂广泛应用,获得了好的经济效益。日本于 20 世纪 60 年代就着手超高速切削机理的研究。日本学者发现在超高速切削时,工件基本保持冷态,其切屑要比常规切屑热得多。日本工业界 35善于吸取各国的研究成果并及时应用到新产品开发中去,尤其在高速切削机床的研究和开发方面后来居上,现已跃居世界领先地位。进人 20 世纪 90 年代以来,以松浦( Matsuora )、牧野 ( Makino )、马扎克( Mazak )和新泻铁( Niigata )等公司为代表的一批机床制造厂,陆续向市场推出不少超高速加工中心和数控铣床,日本厂商现已成为世界上超高速机床的主要提供者.
2 高速切削刀具
刀具是实现高速加工的关键技术之一。生产实践证明,阻碍切削速度提高的关键因素是刀具能否承受越来越高的切削温度在萨洛蒙高速切理研究和高速切削试验的不断深人,证明高速切削的最关键技术之一就是所用的刀具。舒尔兹教授在第一届德国 ― 法国高速切削年会( 1997 年)上做的报告中指出:目前,在高速加工技术中有两个基本的研究发展目标,一个是高速引起的刀具寿命问题,另一个是具有高精度的高速机床.
- 1、下载文档前请自行甄别文档内容的完整性,平台不提供额外的编辑、内容补充、找答案等附加服务。
- 2、"仅部分预览"的文档,不可在线预览部分如存在完整性等问题,可反馈申请退款(可完整预览的文档不适用该条件!)。
- 3、如文档侵犯您的权益,请联系客服反馈,我们会尽快为您处理(人工客服工作时间:9:00-18:30)。
高速切削技术
清华大学
精密仪器与机械学系 制造工程研究所 冯平法
先进制造技术专题
高速切削技术
切削技术的新发展 高速切削的定义 高速切削的特征和应用领域 面向高速切削的切削刀具 面向高速切削的制造装备 面向高速切削的夹紧技术 高速切削的安全防护
先进制造技术专题 切削技术的新发展
氧化陶瓷 金属陶瓷 硬质合金
涂层硬质合金
铸造 硬质合金
高速钢
10 8 1875
1900
工具钢
1925
1950
1975
年
2000
先进制造技术专题 高速切削的特征
高速切削技术
单位时间切除量 表面质量
来源:PTW
切削速度
切削力 刀具寿命
先进制造技术专题 高速切削的特征
切削速度对刀具寿命的影响
(刀具寿命)
高速切削技术
例1:高精度铝质模具型腔加工:在传统铣削加工中,由于铝熔点低,铝 屑容易粘附在刀具上,虽经后续的铲刮、抛光工序,型腔也很难达 到精度要求,在制时间达60小时。 高速铣削分粗、精两道工序:n精=20000r/min,ap=0.2mm, vf=5m/min;加工周期仅为6小时,完全达到精度要求。
(切削速度) 来源:PTW
高速切削技术
工件材料: X100CrMoV51 (2363) ,60 HRC
刀具: 球头刀:d = 6 mm 刀刃数:2(CBN时1) 刀具材料:
HM:硬质合金,TiN 涂层 CBN:立方氮化錋 Cermet:金属陶瓷
先进制造技术专题
高速切削技术
高速切削的特征
提高单位时间的切除量,降低产品的制造时间
Tcr
切削温度
Ta
v1
vcr
v2
切削速度
先进制造技术专题
高速切削技术
高速切削的定义
20世纪80年 代以来,新 型刀具材料 的发展为高 速切削的实 际应用创造 了条件。
切削速度 vc
2000 m/min
800 600 400 200
100 80 60 40 20
聚 晶金 刚 石PC D Si3N4
立 方聚 晶 氮化 錋CB N
† 机床结构及材料 † 机床设计制造技术 † 高速主轴系统 † 快速进给系统 † 高性能CNC系统 † 高性能刀具及工件夹紧系统 † 高效高精度测量测试技术 † 安全防护技术
后续工作 精加工 半精加工 粗加工 加工准备 设计
(常规铣削)
(高速铣削)
来源:BMW
先进制造技术专题 高速切削的特征
提高加工表面质量
行距
加工 余量 要求轮廓
行距
实际轮廓
来源:PTW
高速切削技术
行距
先进制造技术专题 高速切削的特征
降低切削力
高速切削技术
(用PCD刀具材料车削铝合金)
(主切削力)
来源:PTW
高速切削技术
高单位时间切除率,降低加工成本 高加工表面质量,提高加工精度 低切削力,降低加工系统力变形 高激励频率,避免自激振荡 切削热由切屑带走,减少工件热变形 减少后续工序 ,降低加工成本
先进制造技术专题
高速切削技术
高速切削的应用领域
航空航天工业轻合金的加工:飞机上的零件通常采用“整 体制造法”,其金属切除量相当大(一般在70%以上),采 用高速切削可以大大缩短切削时间。
目标
提高加工质量 切削加工
提高生产率 降低加工成本
高速切削技术
手段
提高柔性
提高切削速度
提高精度 扩大加工材料范围 减少消耗
柔性制造系统
高速切削
精密与超精密加工 硬材料切削 干切削与微切削
先进制造技术专题 切削技术的新发展
高速切削技术
干切削
高速切削 硬切削边界条件 源自机床与装备+ 机床新概念 + 驱动系统 + 控制系统 + 夹紧系统 刀具 + 刀具材料 + 刀具涂层 + 标准化与多功能化刀具
先进制造技术专题
高速切削技术
高速切削的定义
高速切削是一个相对概念,是相对常规切削而言,用 较高的切削速度对工件进行切削。一般认为应是常规切削 速度的5~10倍。 高速切削的速度范围与加工方法和工件 材料密切相关。
HSC = HSM = HSM = HSD = HST = HSTM =
High-Speed-Cutting High-Speed-Machining High-Speed-Milling High-Speed-Drilling High-Speed-Turning High-Speed-Turn-Milling
模具制造业:型腔加工同样有很大的金属切除量,过去一 直为电加工所垄断,其加工效率低。
汽车工业:对技术变化较快的汽车零件,采用高速加工。 (过去多用组合机加工,柔性差)
难加工材料的加工(如:Ni基高温合金和Ti合金)
纤维增强复合材料加工
精密零件加工
薄壁易变形零件的加工
先进制造技术专题 高速切削的应用领域
车削:700~7000 m/min; 铣削:300~6000 m/min; 钻削:200~1100 m/min; 磨削:150m/s以上。
例如:在切削灰铸铁时,1000 m/min 以上才是高速车削, 而 400 m/min 就定义为高速钻削。
先进制造技术专题 高速切削的定义
高速切削技术
20世纪20年代德国物理学家Carl.J.Salomon 提出高速加工的理论
例2:塑料的轮胎型芯加工:用传统方法(手工)需十几道工序,在制时间 20天以上,也很难达到复杂轮胎花纹的技术要求。 采用高速铣削,n= 18 000r/min,ap=2 mm,vf=10m/min,在 制时间仅24小时就完全达到了工艺要求。
先进制造技术专题
高速切削技术
实现高速切削的关键技术
高速切削机理及工艺 高性能刀具材料及刀具设计制造技术 高性能机床及其附件
(切削速度)
先进制造技术专题
高速切削的特征
减少传递给工件的热量
切屑和接触面之 间的接触区域产生 的高温会导致温度 效应并降低工件材 料变形的阻力
剪切角增大
切削热大部分由 切屑快速带走
避免积屑瘤的产 生
接触区 高速切削的剪切角 常规切削的剪切角
高速切削技术
前刀面 刀具 后刀面 工件
先进制造技术专题 高速切削的优点
先进制造技术专题 高速切削的定义
高速切削技术
工件材料
纤维增强塑料 铝合金 青铜,黄铜 铸铁 钢 钛合金 镍基合金
10
来源:PTW
高速范围与加工材料密切相关
普通 切削 过渡 区 高速 切削
100
1000
切削速度 vc(铣削)
m/min 10000
先进制造技术专题 高速切削的定义
高速切削技术
高速范围与加工方法密切相关