高速切削
高速切削加工的工艺特点

高速切削加工的工艺特点高速切削加工是一种先进的金属加工方法,具有以下几个主要的工艺特点:1. 切削速度高:高速切削加工的切削速度通常比传统的切削加工方法高出数倍甚至数十倍。
这是由于高速切削使用了高速切削工具和适合高速切削的加工参数,如切削速度、进给速度和切削深度等。
高速切削加工的切削速度可以达到数千米/分钟,这对于提高生产效率和缩短加工时间非常有益。
2. 切削质量高:高速切削加工的另一个显著特点是切削质量高,表面粗糙度低。
这是因为高速切削使用了高硬度、高韧性和高耐磨性的刀具材料,在高速切削下刀具磨损小,可以保持刀具的锋利度,切削力也相对较小,切屑容易破碎,减少了切削振动,从而得到更高质量的切削表面。
3. 加工精度高:高速切削加工具有很高的加工精度,通常可以达到数微米的级别。
这是由于高速切削加工的切削力小、切削热量集中,能够减小切削变形和热影响区域,从而得到更高精度的零件尺寸和形状。
4. 加工效率高:高速切削加工具有很高的加工效率,可以大大缩短加工周期。
高速切削的切削速度快、进给速度高,加工速度相对传统切削加工方法快数倍,可以实现高效率的切削。
此外,使用高速切削还可以减少切削次数,提高生产效益。
5. 节能环保:高速切削加工相较于传统切削加工方法具有较低的切削力和切削温度。
低切削力减小了机床和刀具的负荷,延长了机床和刀具的使用寿命。
低切削温度减少了切削变形和刀具磨损,减少了能源的消耗。
因此,高速切削加工具有节能环保的特点,符合可持续发展的要求。
6. 加工适应性广:高速切削加工适用于各类金属材料的加工,如铁、钢、铜、铝、合金等。
而且,对于复杂零件的加工,高速切削加工也能够发挥其优势,提高生产效率和加工质量。
总之,高速切削加工具有切削速度高、切削质量高、加工精度高、加工效率高、节能环保和加工适应性广的特点。
在现代制造业中,高速切削加工已经成为提高加工效率和改善产品质量的重要工艺方法,对于推动制造业的快速发展具有重要意义。
《高速切削》课件

本PPT课件将介绍高速切削的定义、原理、分类、技术、应用、注意事项以及 未来发展,为您展示全面的高速切削知识。
什么是高速切削?
高速切削的定义
高速切削是指在高速运动下切削金属材料的加工方 法。
高速切削的优点
高速切削具有高效率、高精度和优质表面等优点。
高速切削的原理
1 原理介绍
高速切削技术的趋势 和前景
高速切削技术正朝着更高效率、 更高精度和更环保的方向发展。
ቤተ መጻሕፍቲ ባይዱ
高速切削的未来发展
高速切削未来将在各行各业中得 到更广泛的应用和进一步的优化。
高速切削注意事项
1 高速切削的注意事项
高速切削过程中需注意刀具选择、润滑和安全等方面。
2 如何安全进行高速切削
安全进行高速切削需遵循正确的操作规程和戴好个人防护装备。
3 如何保证高速切削的质量
保证高速切削质量需要注意刀具磨损和加工参数等关键因素。
高速切削发展前景
高速切削的发展历程
高速切削技术经历了多年的发展 与创新。
高速切削利用切削工具对工件进行高速运动切削,实现金属材料的加工。
2 高速切削的工作过程
高速切削的工作过程包括进给运动、主轴转动和切削速度等因素。
3 高速切削的工作原理
高速切削通过防振、刀具材料和润滑等措施,提高切削效率和质量。
高速切削的分类
高速切削分类介绍
高速切削可分为铣削加工和车削 加工两种主要类型。
CNC技术在高速切削加工中起到关 键作用,实现自动化加工。
高速切削的应用
1
高速切削在现代制造中的应用
高速切削广泛应用于航空、汽车、船舶等
高速切削的优势和局限性
2
高速切削简介

2020/4/3
金属切削原理 影响刀具耐用度的主要因素
泰勒公式 vT m A
T
Cv
11
1
vm f nap p
T
Cv
v5
f
2 .25
a
0 .75 p
2020/4/3
高速切削的概念和基本原理
➢ 高速切削技术,是以比常规高数倍的切削速度对零件进 行切削加工的一项先进制造技术。高速切削理论是1931 年4月德国物理学家Carl.J.Salomon提出的。
2020/4/3
2020/4/3
高速钻孔
表面和内侧倒棱
高速加工中心 1台1轴1工序(3万件/月) 柔性(零件、孔数、孔径、孔型可变)
汽车轮毂螺栓孔高速加工实例
电极制造
1毛坯 → 2粗铣 → 3半精铣 → 4热处理 →5电火花加工→6精铣 →7手工磨修 a)传统模具加工的过程
1硬化毛坯→ 2粗铣 → 3半精铣 → 4精铣 →5手工磨修 b)高速模具加工的过程
➢ 1931年德国物理学家C. J. Salomom在“高速切削原理 ”一文中给出了著名的“Salomom曲线”——对应于一 定的工件材料存在一个临界切削速度,此点切削温度最 高,超过该临界值,切削速度增加,切削温度反而下降 。
2020/4/3
➢ Salomom的理论与实验结果,引发了人们极大的兴趣, 并由此产生了“高速切削(HSC)”的概念。
2020/4/3
高速切削的特点
通常切削速度下
M A
I
Ⅱ O
I 剪切滑移 II 前刀面挤压摩擦 III 后刀面挤压摩擦
Ⅲ
2020/4/3
金属切削过程中的滑移线和流线示意图
高速切削的特点
高速切削技术研究
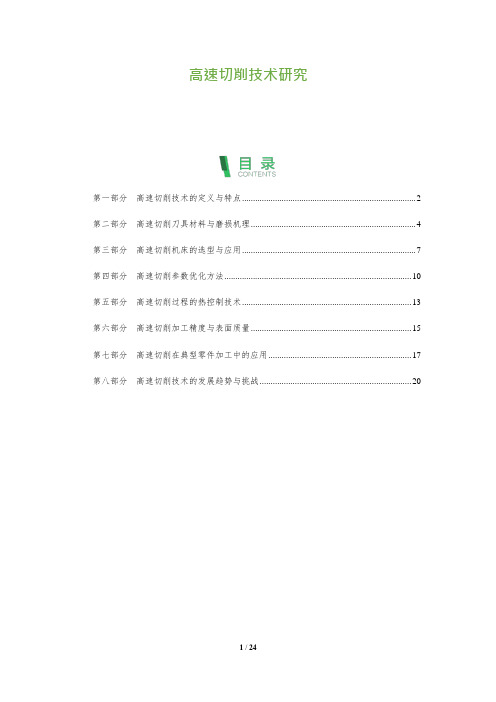
高速切削技术研究第一部分高速切削技术的定义与特点 (2)第二部分高速切削刀具材料与磨损机理 (4)第三部分高速切削机床的选型与应用 (7)第四部分高速切削参数优化方法 (10)第五部分高速切削过程的热控制技术 (13)第六部分高速切削加工精度与表面质量 (15)第七部分高速切削在典型零件加工中的应用 (17)第八部分高速切削技术的发展趋势与挑战 (20)第一部分高速切削技术的定义与特点高速切削技术是一种先进的制造工艺,它通过使用高转速的刀具和优化的切削参数来提高材料去除率、加工精度和表面质量。
该技术的核心在于实现高效率、高质量和高精度的加工过程。
在高速切削过程中,刀具以极高的速度旋转(通常超过每分钟数千转),同时进给速度也相应提高。
这种高速旋转产生的离心力有助于减小切削力和切削热,从而延长刀具寿命并减少工件的热变形。
此外,由于切削力的降低,高速切削还可以减少振动,进一步提高加工精度。
高速切削技术的优势主要体现在以下几个方面:1.高效率:与传统切削相比,高速切削可以显著提高材料去除率,缩短加工时间。
研究表明,高速切削可以提高生产效率达 30%至50%。
2.高精度:高速切削过程中的低切削力可以减少工件的振动,从而提高加工精度。
此外,由于切削热的影响较小,工件的热变形也得到了控制。
3.高质量表面:高速切削产生的切削热较低,这有助于减少工件的烧伤和裂纹,从而获得更好的表面质量。
4.刀具寿命延长:高速切削可以降低切削力,减少刀具磨损,从而延长刀具的使用寿命。
5.节能减排:高速切削技术可以实现更高的材料去除率,从而减少能源消耗和碳排放。
然而,高速切削技术也存在一些挑战,如刀具成本较高、对机床性能要求较高等。
因此,在实际应用中,需要根据具体加工需求和技术条件,合理选择切削参数和刀具,以确保高速切削技术的有效性和经济性。
总之,高速切削技术作为一种先进的制造工艺,具有高效率、高精度、高质量表面等优势,但在实际应用中需充分考虑其成本和设备要求。
高速切削技术简介

1.3 高速切削的研究发展现状
日本:
日本是在20世纪60年代开始高速切削机理的研究。 近些年来吸收了各国的研究成果,现在已后来居上,跃居世 界领先地位。 20世纪90年代研制出了日本第一台卧式加工中心,主轴转速 达到30000r/min,最大进给速度为80m/r,加速度为2g, 重复定位精度为±lµm。 同时他们也致力于高速切削工艺,特别是高速切削工艺数据 库、刀具磨损与破损机理、CAD/CAM系统开发及质量控制等 方面的研究。
1)提高排屑性能,具体措施:
①采用内部供液方式,压力为2~7MPa; ②钻尖角比普通钻头大,易于分断厚型切屑; ③对钻头横刃进行修磨,使之成为中心涡卷形状。
汽车零件孔的高速切削加工
高速钻削加工应注意的问题:
2)提高刀具刚性,具体措施:
①增大钻头芯厚; ②增大倒棱锥度。
汽车零件孔的高速加工
3)防止钻尖过热,具体措施:
1.5.1 汽车工业中的高速切削
汽车工业:
在20世纪20年代主要采用由组合机床组成的刚性生产 线。 在20世纪80年代后,开始采用由加工中心组成的柔性 生产线。 生产的柔性提高了,但生产效率不如组合机床生产线。 怎么办?能否采用高速加工来提高生产率?
1.5.1 汽车工业中的高速切削
汽车工业: 从20世纪80年代中期开始,在单轴专用加工 中心上,采用高速加工技术,以10倍于普通加工 的速度加工,使加工中心的柔性和生产率得到兼 顾,例如一台高速加工中心在一年中就能加工 40000件变速箱箱体。
汽车零件平面的高速铣削加工
1)铸铁缸体、缸盖端面的高速铣削加工:
如Lamb公司: 缸体、缸盖大平面加工采用高速铣削,用氮化硅 (Si3N4基)陶瓷刀片铣削缸体顶面,切削速度达 1524m/min,进给速度达6350mm/min,生产效率提高了 50%。
先进制造工艺--高速切削技术
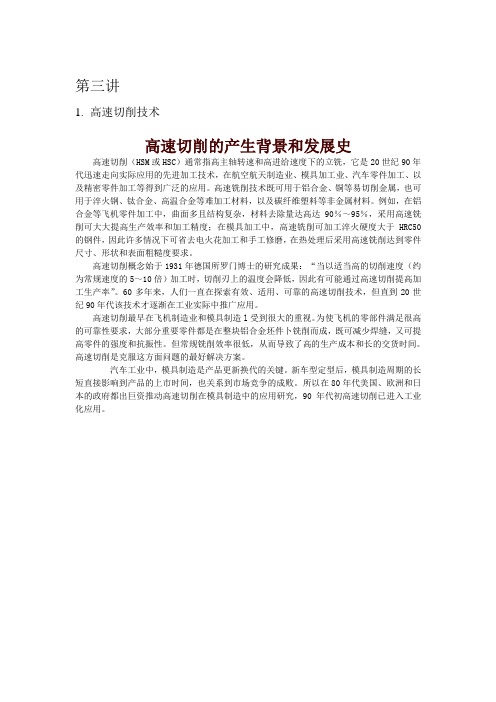
第三讲1.高速切削技术高速切削的产生背景和发展史高速切削(HSM或HSC)通常指高主轴转速和高进给速度下的立铣,它是20世纪90年代迅速走向实际应用的先进加工技术,在航空航天制造业、模具加工业、汽车零件加工、以及精密零件加工等得到广泛的应用。
高速铣削技术既可用于铝合金、铜等易切削金属,也可用于淬火钢、钛合金、高温合金等难加工材料,以及碳纤维塑料等非金属材料。
例如,在铝合金等飞机零件加工中,曲面多且结构复杂,材料去除量达高达90%~95%,采用高速铣削可大大提高生产效率和加工精度;在模具加工中,高速铣削可加工淬火硬度大于HRC50的钢件,因此许多情况下可省去电火花加工和手工修磨,在热处理后采用高速铣削达到零件尺寸、形状和表面粗糙度要求。
高速切削概念始于1931年德国所罗门博士的研究成果:“当以适当高的切削速度(约为常规速度的5~10倍)加工时,切削刃上的温度会降低,因此有可能通过高速切削提高加工生产率”。
60多年来,人们一直在探索有效、适用、可靠的高速切削技术,但直到20世纪90年代该技术才逐渐在工业实际中推广应用。
高速切削最早在飞机制造业和模具制造l受到很大的重视。
为使飞机的零部件满足很高的可靠性要求,大部分重要零件都是在整块铝合金坯件卜铣削而成,既可减少焊缝,又可提高零件的强度和抗振性。
但常规铣削效率很低,从而导致了高的生产成本和长的交货时间。
高速切削是克服这方面问题的最好解决方案。
汽车工业中,模具制造是产品更新换代的关键。
新车型定型后,模具制造周期的长短直接影响到产品的上市时间,也关系到市场竞争的成败。
所以在80年代美国、欧洲和日本的政府都出巨资推动高速切削在模具制造中的应用研究,90年代初高速切削已进入工业化应用。
图16 高速切削在生产应用中的发展历程图17 采用高速切削后产品质量提高的历程a一硬质合金切钢 b一硬质合金切铸铁c—CBN切铸铁图16是德国宝马公司(BMW)采用高速切削的历程。
高速切削技术
高速切削(HSM=High Speed Machining)一、高速切削理论的提出和定义1.提出:高速切削理论最早是由德国物理学家Carl.J.Salomon 在1931 年4 月提出。
并发表了著名的Salomon曲线[1]。
如图1(a)所示。
主要内容是:在常规切削速度范围内,切削温度随着切削速度的提高而升高,但切削速度提高到一定值后,切削温度不但不升高反会降低,如图1(b)所示,且该切削速度值与工件材料的种类有关。
(a) (b)图1 切削温度变化曲线2、高速切削定义:目前高速切削技术比较普及的定义是根据1992年国际生产工程研究会(CIRP) 年会主题报告的定义:高速切削通常指切削速度超过传统切削速度5 - 10 倍的切削加工。
机床主轴转速在10000-20000r/min以上,进给速度通常达15-50m/min,最高可达90m/min。
实际上,高速切削是一个相对概念,它包括高速铣削、高速车削、高速钻孔与高速车铣(绝大部分应用是高速铣削)等不同的加工方式,根据被加工材料的不同及加工方式的不同,其切削速度范围也不同。
目前,不同的加工材料,切削速度约在下述范围,如表1所示[1]:表1 切削速度范围被加工材料切削速度范围铝合金1000~7500m/min铜合金900~5000m/min铸铁900~5000m/min钢500~2000m/min耐热镍基合金500m/min钛合金150~1000m/min纤维增强塑料2000~9000m/min3.特征现代研究表明,高速切削时,切屑变形所消耗的能量大多数转变为热,切削速度高,产生的热量越大,基本切削区的高温有助于加速塑性变形和切屑形成。
而且大部分热量都被切屑带走。
高速切削变形过程显著特征为:第一变形区变窄,剪切角增大,变形系数减少,如图2;第二变形区的接触长度变短,切屑排出速度极高,前刀面受周期载荷的作用。
所以高速切削的切削变形小,切削力有大幅度下降,切削表面损伤减轻。
高速切削简介
高速切削加工切屑形成特征 文献2
2021/7/16
高速切削加工切屑形成特征 文献2
从连续光滑的切削到周期性的锯齿状切屑,是随着切削速度增大而变化 过渡,这是高速切削加工中最基本又富有挑战性的问题。本文中,用临 界切削速度对切屑流起因的显式表达式,用材料性能,未变形切屑厚度 与刀具前角三者来表达,并基于尺寸分析和数值模拟。实验对于各种金 属材料在宽范围的切削厚度与刀具前角下,切屑由连续到锯齿状,给出 临界切削速度合理的预测。更有趣的是,发现,由于由雷诺数对湍流流 动的控制,对锯齿形切屑的流动模式的转变是由雷诺数主导。此外,材 料的性能对锯齿形切屑的影响进行系统的研究,其发展趋势和Recht经典 2021/7模/16 型吻合。
➢ 1931年德国物理学家C. J. Salomom在“高速切削原理 ”一文中给出了著名的“Salomom曲线”——对应于一 定的工件材料存在一个临界切削速度,此点切削温度最 高,超过该临界值,切削速度增加,切削温度反而下降 。
2021/7/16
➢ Salomom的理论与实验结果,引发了人们极大的兴趣, 并由此产生了“高速切削(HSC)”的概念。
2021/7/16
2021/7/16
高速钻孔
表面和内侧倒棱
高速加工中心 1台1轴1工序(3万件/月) 柔性(零件、孔数、孔径、孔型可变)
汽车轮毂螺栓孔高速加工实例
电极制造
1毛坯 → 2粗铣 → 3半精铣 → 4热处理 →5电火花加工→6精铣 →7手工磨修 a)传统模具加工的过程
1硬化毛坯→ 2粗铣 → 3半精铣 → 4精铣 →5手工磨修 b)高速模具加工的过程
切削热大部分由 切屑快速带走
避免积屑瘤的产 生
接触区 高速切削的剪切角 常规切削的剪切角
高速切削的基本原理
高速切削的基本原理
高速切削是一种高效率、高精度的切削加工方法,其基本原理包括以下几点:
1. 切削速度:高速切削的切削速度远高于传统切削速度。
通过提高切削速度,可以减少切削时间,提高加工效率。
同时,高速切削还可以降低切削力和切削温度,减少刀具磨损和工件变形的风险。
2. 刀具材料和涂层:高速切削所使用的刀具材料和涂层也有所不同。
常见的高速切削刀具材料包括硬质合金、陶瓷和超硬材料等,这些材料具有高硬度、高韧性和高热稳定性,可以承受高温和高压的切削环境。
涂层技术可以进一步提高刀具的耐磨性和耐热性。
3. 切削参数优化:高速切削需要对切削参数进行精确的优化。
切削速度、进给速度、切削深度和切削角度等参数需要根据工件材料、刀具材料和切削机床的性能进行调整。
合理的切削参数设计可以提高切削效率和刀具寿命。
4. 切削冷却和润滑:高速切削对切削冷却和润滑要求较高。
采用高效的切削冷却系统可以迅速排除切削过程中产生的热量,降低刀具和工件的温度,减少刀具磨损和工件变形的风险。
同时,润滑剂的使用可以减少切削摩擦,提高表面质量和加工精度。
总之,高速切削通过提高切削速度、优化切削参数、使用高性能刀具材料和涂层,
以及有效的冷却和润滑措施,可以实现高效率、高精度的切削加工效果。
先进制造技术 第2章 高速切削技术2-1
萨洛蒙在l924一1931年间,进行了一系列的高速切削实验: 在非黑色金属材料,如铝、铜和青铜上,用特大直径的刀 盘进行锯切,最高实验的切削速度曾达到14000m/min, 在各种进给速度下,使用了多达20齿的螺旋铣刀。l931年 申请了“超极限速度”专利,随后卖给了“Krupp钢与工 具制造厂”。 萨洛蒙和他的研究室实际上完成了大部分有色金属的切削 试验研究,并且推断出铸铁材料和钢材的相关曲线。 萨洛蒙理论提出了一个描述切削条件的区域或者是范围, 在这个区域内是不能进行切削的。萨洛蒙没有提出可靠的 理论解释,而且他的许多实验细节也没有人知道。
刀具磨损曲线
三、高速切削切屑形成
高速切削试验表明,工件材料及 性能对切屑形态 有决定性影响。
低硬度和高热物理性能的工件材料(铝合金、低碳钢、未 淬硬钢等)易形成连续带状切屑。 高硬度和低热物理性能的工件材料(钛合金钢、未淬硬钢 等)易形成锯齿状切屑。
切削速度对切屑形态有重要影响。对钛合金,在 (1.5~4800)m/min的切削速度范围内形成锯齿状 切屑,随切削速度的增加,锯齿程度(锯齿的齿 距)在增加,直至成为分离的单元切屑。
不同切削速度下车削45钢件的切削形态。
一方面,切削速度增加,应变速度加大,导致脆 性增加,易于形成锯齿状切屑;另一方面,切削 速度增加,切屑温度增加,导致脆性降低,不易 形成锯齿状切屑;
绝热剪切理论(Adiabatic Shear Theory) 周期脆性断裂理论(Periodic brittle fracture theoty)
萨洛蒙(Salomon)曲线
1600
切削温度/℃
钢
1200
青铜
铸铁 硬质合金980℃ Stelite合金850℃ 高速钢650℃ 碳素工具钢450℃
- 1、下载文档前请自行甄别文档内容的完整性,平台不提供额外的编辑、内容补充、找答案等附加服务。
- 2、"仅部分预览"的文档,不可在线预览部分如存在完整性等问题,可反馈申请退款(可完整预览的文档不适用该条件!)。
- 3、如文档侵犯您的权益,请联系客服反馈,我们会尽快为您处理(人工客服工作时间:9:00-18:30)。
1. 论述高速切削的特点。
材料去除率高,切削力较小,工件热变形小,工艺系统振动小,可加工各种难加工材料,可实现绿色制造,简化加工工艺流程。
高速切削追求高转速、中切深、快进给、多行程的加工工艺,高速切削加工可大大降低加工表面粗糙度,加工表面质量可提高1~2等级。
加快产品开发周期,大大降低制造成本。
2.阐述高速切削技术研究体系、关键技术。
数控高速切削加工技术是建立在机床结构与材料、高速主轴系统、高性能CNC控制系统、快速进给系统、高性能刀具材料、数控高速切削加工工艺、高效高精度测试技术等许多相关的软件和硬件技术基础之上的一项复杂的系统工程,是将各单元技术集成的一项综合技术。
关键技术:高速切削机理;高速切削刀具技术;高速切削机床技术;高速切削工艺技术;高速加工的测试技术。
3.阐述高速切削发展趋势。
机床结构将会具有更高的刚度和抗振性,使在高转速和高级给情况下刀具具有更长的寿命;将会用完全考虑高速要求的新设计概念来设计机床;在提高机床进给速度的同时保持机床精度;快换主轴;高、低速度的主轴共存;改善轴承技术;改进刀具和主轴的接触条件;更好的动平衡;高速冷却系统。
(新一代高速大功率机床的开发和研制;新一代抗热振性好、耐磨性好、寿命长的刀具材料的研制及适宜于高速切削的刀具结构的研究;进一步拓宽高速切削工件材料及其高速切削工艺范围;高速切削机理的深入研究;高速切削动态特性及稳定性的研究;开发适用于高速切削加工状态的监控技术;建立高速切削数据库,开发适于高速切削加工的编程技术以进一步推广高速切削加工技术;基于高速切削工艺,开发推广干式(准干式)切削绿色制造技术;基于高速切削,开发推广高能加工技术)
4结合典型工件材料和加工工艺方法,讨论高速切削的速度范围。
(1)根据工件材料:刚才380m/min以上、铸铁700m/min以上、铜材1000m/min以上、铝材1100m/min以上、塑料1150m/min以上时,认为是合适的速度范围。
(2)根据加工工艺方法:车削700~7000m/min,铣削300~6000m/min,钻削200~1100m/min,磨削5000~10000m/min,认为是合适的速度范围。
5讨论高速切削加工的切削力变化规律。
(1)切削用量对切削力的影响:背吃刀量ap增大,切削力成正比增加,背向力和进给力近似成正比增加。
进给量f增大,切削力与增大,但切削力的增大与f不成正比(75%)(2)工件材料对切削力的影响:较大的因素主要是工件材料的强度、硬度和塑性。
a材料的强度、
硬度越高,变形抗力越大,切削力也越大。
b强度、硬度相近的材料,塑性、韧性越大,切削力越大。
(3)切削速度对切削力的影响较为复杂。
(4)刀具几何参数对切削力的影响:前角增大时,若后角不变,刀具容易切入工件有助于切削变形的减小,使变形抗力减小,所以切削力减小。
加工塑性金属时前角增大,变形减小,切削力减小。
加工脆性金属时,因为变形和加工硬化较小,故切削速度改变时切削力变化不大。
在正前角相同情况下,对有负倒棱的车刀,由于切削时的切屑变形比无负倒棱的大,所以切削力有所提高。
主偏角在30-60范围内增大,由切削厚度的影响起主要作用,促使主切削力减小;主偏角约在60-90范围内增大,刀尖处圆弧和副前角的影响起主要作用,促使主切削力增大。
当增大时背向力的影响比对切削力的影响大,着仍应由大使角减小,所以为了防止振动应减小刀尖圆弧半径。
刃倾角对Fz影响不大,但对Fx、Fy的影响较大。
刃倾角增大,背吃刀Fy方向的前角增大,Fy 减小;而进给抗力方向的前角减小,则Fx增大。
(5)其他因素对切削力的影响:a刀具材料:对切削力的影响是由刀具材料与工件材料之间亲合力和摩擦系数等因素决定的。
b切削液:由于使刀具、工件与切屑接触面间摩擦减小,因此,能较显著减小切削力。
c刀具磨损:后面磨损,使刀具与加工表面间摩擦加剧。
故切削力Fc、Fp增大。
6结合萨洛蒙曲线,讨论高速切削加工切削温度变化规律。
(图)
在常规的切削速度范围(图中A区)内,切削温度随着切削速度的增大而提高。
但是,当切削速度增大到某一数值Vc后,切削速度再增大,切削温度反而下降,Vc之值与工件材料的种类有关。
对于每一种工件材料,存在一个从V1到Vc速度范围,在这个速度范围内(图中B区),由于切削温度太高(高于刀具材料允许的最高温度t0),任何刀具都无法承受,切削加工不可能进行。
这个范围被称为“死谷”。
7.结合高速切削加工对机床的要求,讨论高速切削加工机床结构特点。
要求:主轴转速高、功率大;进给量和快速行程速度高;主轴和工作台(拖板)运动都有要有极高的加速度;机床要有优良的静、动态特性和热态特性。
结构特点:床身等固定部件的高刚度和高抗振性;主轴的高转速的高扭矩;进给系统的高进给速度;主轴轴承的高刚度和高抗振性;高效冷却系统;可靠地安全防护系统;对刀具的耐热性和较高的律学性能;高精度、高速度的传感检测技术;优良的热态特性和静、动态特性。
8.如何选择高速切削加工参数。
(1)对刀具磨损的影响:刀具耐用度受切削速度的影响比较大,进给量次之,切削深度最后。
(2)对切削热的影响:切削速度增大会增加切削温度,但一般材料切削速度增加会使切削大量增加,而大部分切削人会有切削带走,少量导热性差的材料除外。
(3)对切削力的影
响:a切削速度的影响:切削速度影响不大,但应注意共振点问题。
b进给量影响:进给量与切削力基本成比例,应加以控制。
c切削深度影响:应使用较小的轴向切深、应使用较小的径向切深。
d粗糙度影响:结合轴向切削深度对粗糙度的影响、径向切削深度对粗糙度的影响、切削速度对粗糙度的影响、每齿进给量对粗糙度的影响,综合考虑。
(4)对工件粗糙度的影响。
9.讨论高速刀具安全性国际标准与刀具安全技术在高速切削加工中的作用。
高速切削技术的最显著特点是采用很高的切削速度来进行零件的机械加工。
因此具有很大离心力,比普通的切削刀具高出很多倍。
高速铣削是目前高速切削技术中应用最多的一种工艺技术,在高速铣削时,这类刀具的各部分都要承受很大的离心力,其作用远远超过切削力本身的作用,成为刀具的主要载荷,其离心力之大,足以到时刀体破碎。
因此,研究高速切削刀具的安全性技术,是进一步发展和一个用高速切削技术的必要前提。
在高速数控加工中,高速刀具安全性国际标准与刀具安全技术具有非常重要的意义,因为刀具的标准不尽影响加工的质量和效率,而且刀具的不安全还可能导致严重的人身和设备事故。
(刀具材料:刀体材料的比重要小,强度要高。
刀具结构:刀体的设计应减少直径,增加高度。
刀体的结构应对称于回转轴,使重心通过铣刀的轴线。
夹紧方式:高速旋转过程中,刀片、螺钉或者其他夹紧元等一些局部不平衡质量体收到很大的离心力作用。
刀具的动平衡:在高速旋转时,刀具的不平衡会对主轴系统产生一个附加的径向载荷,其大小与转速成平方关系,从而对刀具、机床主轴的安全性和工件加工质量带来不利的影响。
)
10.高速切削加工对刀具的要求。
高硬度、高强度和耐磨性;韧度高,抗冲击能力强;高的热硬性和化学稳定性;抗热冲击能力强。
(高的刚度与精度;高的适应性与互换性;刀具结构高度安全性;刀具的动平衡)
11.讨论主要高速切削刀具材料性能、特点。
(图)
12.高速切削技术在汽车、航空和航天、模具加工中技术特点。
汽车:切削率高、加工质量高、扩大加工范围、良好的经济型,与传统的精加工相比,进一步实现高精度化;高速切削加工的每次切除量相当小,可以高速地实现多次精密切削加工,从而大大减少了人工修整的工作量,大大提高了覆盖件模具的加工效率;由于切削速度极大提高,与过去的精加工工序相比,加工周期大幅度缩短。
航空:提高切削效率、整体高速加工代替组件、难加工材料的高速切削。
模具:提高加工效率、可加工淬硬钢、提高机床利用率、降低刀具成本、延长刀具寿命、提高高速切削模具效率的工艺技术。