高速切削
高速切削知识
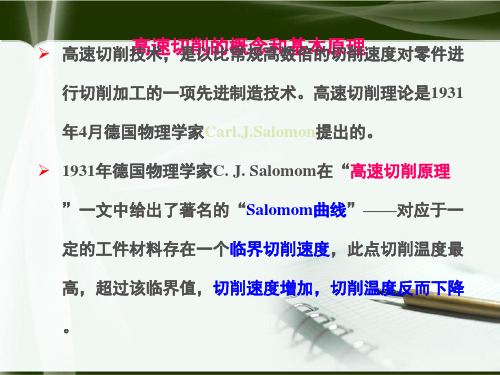
精度高: 对于同样的切削层参数,高速切削的单位切削力明显减小。这对减小振动和偏差 非常重要,也使工件在切削过程的受力变形显著减小。
质量高: 一方面,高速切削的力值及其变化幅度小,与主轴转速有关的激振频率远远高于切削工 艺系统的高阶固有频率。 另一方面,也是的传入工件的切削热的比例大幅度减少,加工表面受热时间短、切削温 度低,因此热影响区和热影响程度都较小。加工表面质量显著提高。
低能耗:高速切削时,单位功率所切削的切削曾材料体积显著增大。由于采用较小的背吃 刀量,刀具每刃的切削量很小,因而机床的主轴、导轨的受力就小,机床的精度寿命 长,同时刀具寿命也延长了。
高速加工机床振动小、噪声低、少用或不用切削液,也符合环保要求。
二 .高速加工切削的特点:(6个问题)
1.单位时间内材料切除率可大大增加,可达到常规切削的 3~6倍。极大提高了机床的生产率 2.切削力可降低30%,尤其是径向切削力大幅度减少, 特别有利于薄壁等刚性较差零件的加工,最小0.05mm 3.高速切削时95%~98%以上的切削热来不及传给工件, 工件基本处于冷态。特别适合加工易热变形的零件 4.高速切削时,机床的激振频率特别高,远高出机床系统的固 有频率,可加工出非常精密光滑的零件
5.高速加工可加工各种难加工材料 6.降低加工成本 单件加工时向缩短 一次安装完粗、半精、精
先进制造技术专题
高速切削技术
切削技术的新发展
目标 手段
提高柔性 提高加工质量
柔性制造系统
提高切削速度
切削加工 提高精度 扩大加工材料范围 提高生产率 降低加工成本 减少消耗
高速切削
精密与超精密加工
硬材料切削 干切削与微切削
高速切削范围: 按不同的加工工艺:车削:700 ~ 7000m/min (线速度) 铣削:300 ~ 6000m/min 钻削:200 ~ 1100m/min 磨削:150 ~ 360m/s 主轴转速:10000转/分以上(最少) 进给建度:30 ~ 90m/min 加减速度:1 ~ 8g (普通数控 0.1 ~ 0.3g)
《高速切削加工》课件

3
高速切削加工技术的新发展
高速切削加工技术的新发展是智能化、高效化、多功能化等方向的发展。
总结
1 高速切削加工的重要性
在现代先进制造业中,高速切削加工已成为最先进的加工工艺之一。
2 发展前景
高速切削加工将朝着更高精度、更稳定、更智能的方向发展。
刀具
高速切削加工用的刀具有硬质合金刀具和普通高速钢刀具。
2
夹具
用于夹紧加工件,保证加工件的位置和尺寸的准确度。
3
加工中心机床
高速切削加工的核心设备,一般配备自动换刀库,可实现多种工序的加工。
高速切削加工的原理
四角切削
四角切削是刀具在加工过程 中所受力的主要方向,也是 影响刀具切削稳定的主要因 素。
பைடு நூலகம்
机械制造
高速车削、高速铣削、高速钻削 等机械制造领域。
电子信息
如手机、笔记本电脑金属外壳、 DVD机零部件、各类光学仪器等。
高速切削加工的挑战与未来
1
超细加工
针对非金属的加工,要求精度更高,应考虑空气轴承、颤动反馈控制、非触变形 传感控制等。
2
超硬材料加工
超硬材料的加工,如石墨、硬质合金、陶瓷等,已成为高速切削加工的一个重要 领域。
精密加工
精密高速切削加工广泛应用 于航空航天、汽车、电子和 精密机械制造等领域,如模 具、光学部件、超声波探头 和燃烧室等零部件。
表面质量
高速切削加工能够获得极高 的表面质量,如挤出铝合金 管、铜合金输入输出端子, 铜轴套、石英晶体等产品的 光洁度达到镜面级。
高速切削加工的应用
航空航天
航空航天零部件,如高压涡轮叶 片、大型钛合金零件等。
加工效率高
高速切削加工速度快,可以完成 较长时间处理不完的工作。
高速切削加工的工艺特点

高速切削加工的工艺特点高速切削加工是一种先进的金属加工方法,具有以下几个主要的工艺特点:1. 切削速度高:高速切削加工的切削速度通常比传统的切削加工方法高出数倍甚至数十倍。
这是由于高速切削使用了高速切削工具和适合高速切削的加工参数,如切削速度、进给速度和切削深度等。
高速切削加工的切削速度可以达到数千米/分钟,这对于提高生产效率和缩短加工时间非常有益。
2. 切削质量高:高速切削加工的另一个显著特点是切削质量高,表面粗糙度低。
这是因为高速切削使用了高硬度、高韧性和高耐磨性的刀具材料,在高速切削下刀具磨损小,可以保持刀具的锋利度,切削力也相对较小,切屑容易破碎,减少了切削振动,从而得到更高质量的切削表面。
3. 加工精度高:高速切削加工具有很高的加工精度,通常可以达到数微米的级别。
这是由于高速切削加工的切削力小、切削热量集中,能够减小切削变形和热影响区域,从而得到更高精度的零件尺寸和形状。
4. 加工效率高:高速切削加工具有很高的加工效率,可以大大缩短加工周期。
高速切削的切削速度快、进给速度高,加工速度相对传统切削加工方法快数倍,可以实现高效率的切削。
此外,使用高速切削还可以减少切削次数,提高生产效益。
5. 节能环保:高速切削加工相较于传统切削加工方法具有较低的切削力和切削温度。
低切削力减小了机床和刀具的负荷,延长了机床和刀具的使用寿命。
低切削温度减少了切削变形和刀具磨损,减少了能源的消耗。
因此,高速切削加工具有节能环保的特点,符合可持续发展的要求。
6. 加工适应性广:高速切削加工适用于各类金属材料的加工,如铁、钢、铜、铝、合金等。
而且,对于复杂零件的加工,高速切削加工也能够发挥其优势,提高生产效率和加工质量。
总之,高速切削加工具有切削速度高、切削质量高、加工精度高、加工效率高、节能环保和加工适应性广的特点。
在现代制造业中,高速切削加工已经成为提高加工效率和改善产品质量的重要工艺方法,对于推动制造业的快速发展具有重要意义。
《高速切削》课件

本PPT课件将介绍高速切削的定义、原理、分类、技术、应用、注意事项以及 未来发展,为您展示全面的高速切削知识。
什么是高速切削?
高速切削的定义
高速切削是指在高速运动下切削金属材料的加工方 法。
高速切削的优点
高速切削具有高效率、高精度和优质表面等优点。
高速切削的原理
1 原理介绍
高速切削技术的趋势 和前景
高速切削技术正朝着更高效率、 更高精度和更环保的方向发展。
ቤተ መጻሕፍቲ ባይዱ
高速切削的未来发展
高速切削未来将在各行各业中得 到更广泛的应用和进一步的优化。
高速切削注意事项
1 高速切削的注意事项
高速切削过程中需注意刀具选择、润滑和安全等方面。
2 如何安全进行高速切削
安全进行高速切削需遵循正确的操作规程和戴好个人防护装备。
3 如何保证高速切削的质量
保证高速切削质量需要注意刀具磨损和加工参数等关键因素。
高速切削发展前景
高速切削的发展历程
高速切削技术经历了多年的发展 与创新。
高速切削利用切削工具对工件进行高速运动切削,实现金属材料的加工。
2 高速切削的工作过程
高速切削的工作过程包括进给运动、主轴转动和切削速度等因素。
3 高速切削的工作原理
高速切削通过防振、刀具材料和润滑等措施,提高切削效率和质量。
高速切削的分类
高速切削分类介绍
高速切削可分为铣削加工和车削 加工两种主要类型。
CNC技术在高速切削加工中起到关 键作用,实现自动化加工。
高速切削的应用
1
高速切削在现代制造中的应用
高速切削广泛应用于航空、汽车、船舶等
高速切削的优势和局限性
2
高速切削技术研究
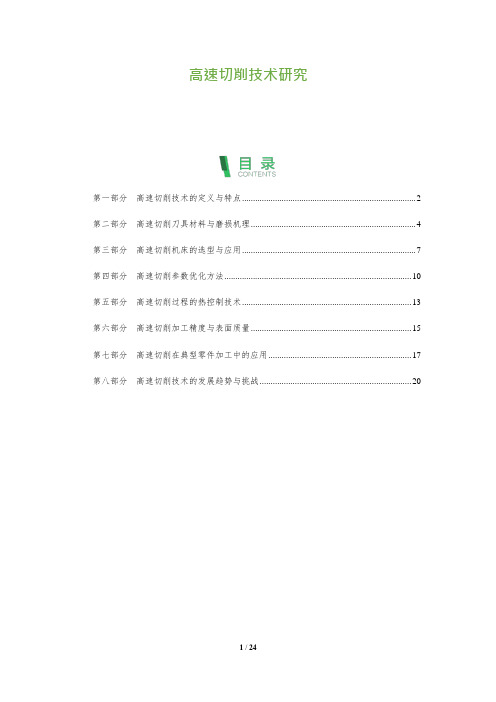
高速切削技术研究第一部分高速切削技术的定义与特点 (2)第二部分高速切削刀具材料与磨损机理 (4)第三部分高速切削机床的选型与应用 (7)第四部分高速切削参数优化方法 (10)第五部分高速切削过程的热控制技术 (13)第六部分高速切削加工精度与表面质量 (15)第七部分高速切削在典型零件加工中的应用 (17)第八部分高速切削技术的发展趋势与挑战 (20)第一部分高速切削技术的定义与特点高速切削技术是一种先进的制造工艺,它通过使用高转速的刀具和优化的切削参数来提高材料去除率、加工精度和表面质量。
该技术的核心在于实现高效率、高质量和高精度的加工过程。
在高速切削过程中,刀具以极高的速度旋转(通常超过每分钟数千转),同时进给速度也相应提高。
这种高速旋转产生的离心力有助于减小切削力和切削热,从而延长刀具寿命并减少工件的热变形。
此外,由于切削力的降低,高速切削还可以减少振动,进一步提高加工精度。
高速切削技术的优势主要体现在以下几个方面:1.高效率:与传统切削相比,高速切削可以显著提高材料去除率,缩短加工时间。
研究表明,高速切削可以提高生产效率达 30%至50%。
2.高精度:高速切削过程中的低切削力可以减少工件的振动,从而提高加工精度。
此外,由于切削热的影响较小,工件的热变形也得到了控制。
3.高质量表面:高速切削产生的切削热较低,这有助于减少工件的烧伤和裂纹,从而获得更好的表面质量。
4.刀具寿命延长:高速切削可以降低切削力,减少刀具磨损,从而延长刀具的使用寿命。
5.节能减排:高速切削技术可以实现更高的材料去除率,从而减少能源消耗和碳排放。
然而,高速切削技术也存在一些挑战,如刀具成本较高、对机床性能要求较高等。
因此,在实际应用中,需要根据具体加工需求和技术条件,合理选择切削参数和刀具,以确保高速切削技术的有效性和经济性。
总之,高速切削技术作为一种先进的制造工艺,具有高效率、高精度、高质量表面等优势,但在实际应用中需充分考虑其成本和设备要求。
数控机床加工中的高速切削技巧分享

数控机床加工中的高速切削技巧分享数控机床加工作为制造业领域的重要环节,对于提高生产效率和降低成本起着至关重要的作用。
在数控机床加工过程中,高速切削作为一种重要的切削技巧,可以进一步提高切削效率和加工质量。
本文将分享一些数控机床加工中的高速切削技巧,帮助读者更好地进行切削加工。
首先,在进行高速切削前,我们需要选择合适的刀具。
刀具的选择直接影响切削效率和加工质量。
对于高速切削,我们可以选择具有高硬度和刚度的刀具。
例如,碳化钨刀具、多刃刀具以及高速钢刀具等都可以满足高速切削的要求。
此外,刀具的切削刃角和刀尖圆度也需要注意,切削刃角的选取应根据具体的加工材料和切削工艺进行选择。
其次,在切削参数的选择上,我们需要考虑切削速度、进给速度和切削深度等因素。
对于高速切削来说,切削速度是一个重要的参数。
通常情况下,高速切削的切削速度要高于常规切削。
在选择切削速度时,应综合考虑材料的硬度、刀具材料和刚度等因素进行合理选择。
进给速度也是一个关键参数,过低的进给速度可能导致切削不稳定或刀具容易磨损,而过高的进给速度则可能导致切屑堆积、加工表面质量变差等问题。
切削深度的选择也需要慎重考虑,过大的切削深度可能导致切削力过大、热量集中等问题。
同时,在数控机床加工的过程中,冷却润滑剂的使用也是至关重要的。
冷却润滑剂可以降低切削温度,减少切削力,提高切削质量。
对于高速切削而言,冷却润滑剂的选择和使用需要根据材料和切削工艺选择适当的类型和喷洒方式。
常见的冷却润滑剂有液压油、切削液等。
在使用冷却润滑剂时,还需要注意及时更换和合理设置喷洒方式,以确保其正常使用的效果。
此外,切削过程中的切削力和切削温度的控制也是关键。
高速切削时,切削力会变大,对切削系统和刀具都会产生一定的影响。
对于切削力的控制,可以采用后退式切削、控制进给速度和切削深度等方式。
切削温度的控制主要通过冷却润滑剂的使用、合理选择切削参数等来实现。
切削力和切削温度的控制可以有效提高切削加工的精度和质量。
高速切削加工工艺参数与刀具磨损机理

高速切削加工工艺参数与刀具磨损机理高速切削加工工艺参数与刀具磨损机理是现代制造业中的关键研究领域,它们直接影响到加工效率、产品质量以及生产成本。
本文将探讨高速切削加工工艺参数的优化以及刀具磨损机理的分析,以期为制造业提供理论指导和实践参考。
一、高速切削加工工艺参数概述高速切削加工技术是一种先进的金属切削技术,它通过提高切削速度来实现高效率和高质量的加工。
这种技术在汽车、航空、模具制造等行业中得到了广泛应用。
高速切削加工工艺参数的优化是实现高效加工的关键,包括切削速度、进给速度、切削深度、刀具材料选择等。
1.1 高速切削加工的优势高速切削加工技术具有以下优势:- 提高生产效率:由于切削速度的提高,单位时间内可以去除更多的材料,从而缩短加工时间。
- 改善加工表面质量:高速切削可以减少切削力和切削温度,从而减少加工表面的毛刺和烧伤。
- 提高加工精度:高速切削过程中的振动较小,有利于提高加工精度。
- 减少刀具磨损:高速切削可以减少刀具与工件的接触时间,从而降低刀具磨损。
1.2 高速切削加工工艺参数高速切削加工工艺参数主要包括以下几个方面:- 切削速度:切削速度是影响高速切削效率和质量的关键参数,需要根据材料特性和刀具材料进行合理选择。
- 进给速度:进给速度影响切削的连续性和表面粗糙度,需要与切削速度相匹配。
- 切削深度:切削深度影响切削力和刀具的耐用度,需要根据工件材料和刀具强度进行选择。
- 刀具材料:刀具材料的选择直接影响切削性能和刀具寿命,常见的刀具材料有硬质合金、陶瓷、石等。
二、刀具磨损机理分析刀具磨损是高速切削加工中不可避免的现象,它会影响加工质量、生产效率和刀具成本。
研究刀具磨损机理对于延长刀具寿命、提高加工效率具有重要意义。
2.1 刀具磨损的类型刀具磨损主要包括以下几种类型:- 磨料磨损:由于切削过程中工件材料中的硬质点与刀具表面接触,导致刀具表面逐渐磨损。
- 热磨损:高速切削过程中产生的高温会使刀具材料发生热软化,从而加速磨损。
先进制造工艺--高速切削技术
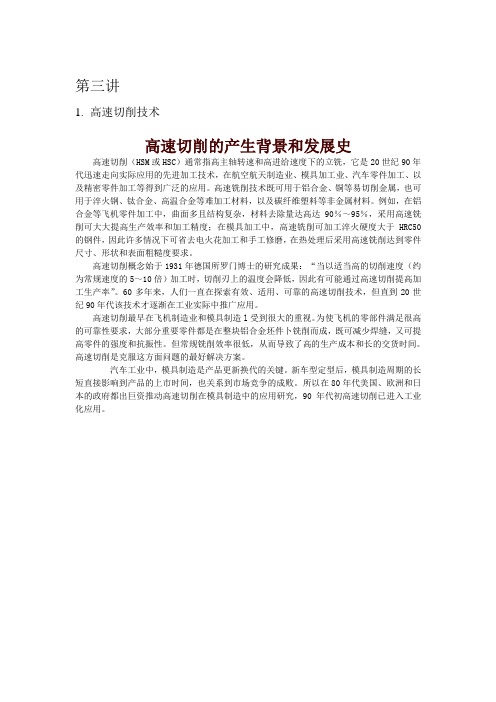
第三讲1.高速切削技术高速切削的产生背景和发展史高速切削(HSM或HSC)通常指高主轴转速和高进给速度下的立铣,它是20世纪90年代迅速走向实际应用的先进加工技术,在航空航天制造业、模具加工业、汽车零件加工、以及精密零件加工等得到广泛的应用。
高速铣削技术既可用于铝合金、铜等易切削金属,也可用于淬火钢、钛合金、高温合金等难加工材料,以及碳纤维塑料等非金属材料。
例如,在铝合金等飞机零件加工中,曲面多且结构复杂,材料去除量达高达90%~95%,采用高速铣削可大大提高生产效率和加工精度;在模具加工中,高速铣削可加工淬火硬度大于HRC50的钢件,因此许多情况下可省去电火花加工和手工修磨,在热处理后采用高速铣削达到零件尺寸、形状和表面粗糙度要求。
高速切削概念始于1931年德国所罗门博士的研究成果:“当以适当高的切削速度(约为常规速度的5~10倍)加工时,切削刃上的温度会降低,因此有可能通过高速切削提高加工生产率”。
60多年来,人们一直在探索有效、适用、可靠的高速切削技术,但直到20世纪90年代该技术才逐渐在工业实际中推广应用。
高速切削最早在飞机制造业和模具制造l受到很大的重视。
为使飞机的零部件满足很高的可靠性要求,大部分重要零件都是在整块铝合金坯件卜铣削而成,既可减少焊缝,又可提高零件的强度和抗振性。
但常规铣削效率很低,从而导致了高的生产成本和长的交货时间。
高速切削是克服这方面问题的最好解决方案。
汽车工业中,模具制造是产品更新换代的关键。
新车型定型后,模具制造周期的长短直接影响到产品的上市时间,也关系到市场竞争的成败。
所以在80年代美国、欧洲和日本的政府都出巨资推动高速切削在模具制造中的应用研究,90年代初高速切削已进入工业化应用。
图16 高速切削在生产应用中的发展历程图17 采用高速切削后产品质量提高的历程a一硬质合金切钢 b一硬质合金切铸铁c—CBN切铸铁图16是德国宝马公司(BMW)采用高速切削的历程。
- 1、下载文档前请自行甄别文档内容的完整性,平台不提供额外的编辑、内容补充、找答案等附加服务。
- 2、"仅部分预览"的文档,不可在线预览部分如存在完整性等问题,可反馈申请退款(可完整预览的文档不适用该条件!)。
- 3、如文档侵犯您的权益,请联系客服反馈,我们会尽快为您处理(人工客服工作时间:9:00-18:30)。
普通切削
铝 合金
青铜, 黄铜
过渡区 高速切削
铸铁
钢
钛 合金 镍 基合 金 10 100 1000 m/min 10000
切削速度 vc(铣削)
来源:PTW
8
高速切削的定义
高速范围与加工方法密切相关
车削:700~7000 m/min; 铣削:300~6000 m/min; 钻削:200~1100 m/min; 磨削:150m/s以上。
v=200m/mim vf =50mm/min a p= 0.5mm v=110m/min f =0.08mm/r a p= 0.3mm
钛合金Ti6Al4V 柴油机机体主轴 承孔(表面热喷 涂镍基合金)
HV330
铣削
HRC50
镗孔
20
高速切削的应用
干切系指不使用冷却液的切削技术
准干切则指使用最少量冷却液的切削技术
HRA90 HRA93 HV10000 HV7500 0.3GPa 146.5 惰性小 2.8GPa 100-120 600-800 ℃ 惰性小
抗弯强度 2.4GPa 导热系数 40-50 热稳定性 350℃ 化学惰性
1000 ℃ 1400 ℃ 800 ℃
耐磨性
加工质量
低
低
较高 高 一般精度 Ra≤0.8 Ra≤0.8 IT7-8 IT7-8
4
高速切削定义
高速切削是一个相对概念,是相对常规切削而言,用
较高的切削速度对工件进行切削。一般认为应是常规切削
速度的5~10倍。 高速切削的速度范围与加工方法和工件 材料密切相关。
术语:
HSC
HSM HSM HSD
=
= = =
High-Speed-Cutting
High-Speed-Machining High-Speed-Milling High-Speed-Drilling
小时就完全达到了工艺要求。
18
高速切削的应用
PCD刀具切削铝、铜合金实例
加工对象 车辆汽缸体 AlSi17Cu4Mg 合金 照相机机身 13%硅铝合金 活塞环槽 LM24铝合金 活塞式阀门 LM24铝合金 整流子 CDA105铜合 金 油泵喷射内孔 GdAlSi12Cu 硅铝合金 加工方式 工艺参数 v = 800m/mim fz = 0.08mm/齿 a p= 0.5mm v = 2900m/mim fz = 0.018mm/齿 a p= 0.5mm v = 590m/mim f = 0.2mm/r a p= 10mm v = 132m/mim vf = 380mm/min v = 350m/mim f = 0.05mm/r a p= 0.25mm, 干切 v = 173m/mim f = 0.02mm/r a p= 0.2mm 刀具参数 12mm方形刀片 齿数z = 12 α0=12° 齿数z = 4 γ0=10° α0=12° γ0=10° α0=12° α0’=2° 麻花钻 γ0=0° α0 = 7 ° rε=0.5mm 阶梯镗刀 加工效果 Ra=0.8μm,可连续加工500件 (使用WC基硬质合金只能加 工25件) Ra=0.8~0.4μm,可连续加工 20000件(使用WC基硬质合金 只能加工250件) 可连续加工2500件,无颤振 可连续加工5000件,取代硬质 合金钻头定中心、钻孔、铰孔 可连续加工2500件(使用WC 基硬质合金只能加工50件) Ra=0.35μm,每把刀可加工 150000件
HST
=
High-Speed-Turning
High-Speed-Turn-Milling
5
HSTM =
高速切削定义
20世纪20年代德国物理学家Carl.J.Salomon 提出高速加 工的理论
Tcr
切削 温度
Ta
v1 vcr
切削 速度
6
v2
高速切削定义
切削温度/℃
1600
钢
1200
பைடு நூலகம்
青铜
铸铁
硬质合金980℃
高速加工技术
High Speed Machining Technology
内容提要
高速加工概述
切削技术的发展 高速切削定义 高速切削的特征 高速切削的应用
相关的技术
高速加工刀具 高速切削机床
高速加工路径规划
2
切削技术的发展
目标 手段
柔性制造系统
提高柔性
提高加工质量
提高切削速度
前刀面 刀具
后刀面 工件
切削热大部分由 切屑快速带走
避免积屑瘤的产 生
15
高速切削的优点
高单位时间切除率,进给率较常规切削提高5-10倍,材料去
除率可提高3-6倍
高加工表面质量,精度,刀具激振频率远离工艺系统固有
频率,不易产生振动;又切削力小、热变形小、残余应力小,易 于保证加工精度和表面质量
• 天然金刚石耐热性为 700-800℃,高于此温度,碳原子 转化为石墨结构,硬度丧失。 • 天然金刚石价格昂贵,刃磨困难,主要用于加工精度和 表面粗糙度要求极高的零件,如激光反射镜、感光鼓、多 面镜、磁盘等。
25
高速加工刀具
聚晶金刚石 • 人造金刚石是在高温高压条件下,借助于某些合金触媒的 作用,由石墨转化而成。 • 在高温高压下,金刚石粉经二次压制形成聚晶金刚石 • 聚晶金刚石硬度略低于天然金刚石,为HV6500-8000 。 • 聚晶金刚石价格便宜,焊接方便,可磨性好,应用广泛, 可在大部分场合代替天然金刚石。 • 用等离子CVD(化学气相沉积)可将聚晶金刚石作成涂层, 用途和聚晶金刚石刀具相同。 • 金刚石刀具不适于加工铁族材料,因为金刚石中的碳元 素与铁元素有很强的亲和力,碳元素极易向含铁的工件扩 散,使金刚石刀具很快磨损。
后续工作 精加工 半精加工 粗加工 加工准备 设计
(常规铣削)
(高速铣削)
来源:BMW
13
高速切削的特征
降低切削力
(用PCD刀具材料车削铝合金)
(主切削力)
(切削速度) 来源:PTW
14
高速切削的特征
减少传递给工件的热量 切屑和接触面之 接触区 间的接触区域产生 的高温会导致温度 高速切削的剪切角 效应并降低工件材 料变形的阻力 常规切削的剪切角 剪切角增大
† 机床结构及材料 † 机床设计制造技术 † 高速主轴系统
† 快速进给系统
† 高性能CNC系统 † 高性能刀具及工件夹紧系统 † 高效高精度测量测试技术 † 安全防护技术
23
高速加工刀具
普通刀具材料与超硬刀具材料性能与用途对比
刀具材料种类 材料性能 硬度 合金 高速钢 硬质合金 陶瓷 工具钢 W18Cr4V YG6 Si3N4 HRC65 HRC66 3.2GPa 20-30 620 ℃ 1.45GPa 0.8GPa 70-100 低 30-40 惰性大 天然 聚晶金刚石 金刚石 PCD 聚晶立方氮 化硼 PCBN HV4000 1.5GPa 40-100 >1000 ℃ 惰性大
切削加工 提高精度 扩大加工材料范围 提高生产率 降低加工成本 减少消耗
高速切削
精密与超精密加工 高硬材料切削(HRC60以 上) 干切削与微切削
3
切削技术的发展
条件
高速切削
机床与装备 + 机床新概念
+ 驱动系统 + 控制系统 + 夹紧系统
刀具 + 刀具材料
干切削
硬切削
+ 刀具涂层 + 标准化与多功能 化刀具
一般钢 材、铸 铁粗、 精加工 高硬度 钢材精 加工
最高 最高 高精度 Ra=0.1-0.05 IT5-6
硬质合金、铜、 铝有色金属及 其合金、陶瓷 等高硬度材料
很高 Ra=0.4-0.2 IT5-6 可替代磨削
淬火钢、冷硬 铸铁、高温合 金等难加工材 料
低速加 加工对象 工一般 钢材、 铸铁
一般钢 材、铸 铁粗、 精加工
(刀具寿命) 工件材料: X100CrMoV51 (2363) ,60 HRC
刀具: 球头刀:d = 6 mm 刀刃数:2(CBN时1) 刀具材料: HM:硬质合金,TiN 涂层 (切削速度)
CBN:立方氮化錋
Cermet:金属陶瓷
来源:PTW
12
高速切削的特征
提高单位时间的切除量,降低产品的制造时间
19
精铣
精铣
车削 钻孔 精车
精镗
高速切削的应用
PCBN刀具在高速切削中的应用实例
加工对象 冷挤压模YG15 硬度 HRA87 加工方式 镗孔 工艺参数 加工效果 工效较电火花加工提高30倍, Ra=0.8~0.4μm Ra=1.6~0.8μm 行程达13000m, Ra=1.6~0.8μm
v=50m/mim f = 0.1mm/r a p= 0.1mm
Stelite合金850℃
800 高速钢650℃ 碳素工具钢450℃ 400
软铝
非铁金属
切削不 切削适应区 适应区
0
600
1200
1800
2400
3000
切削适应区
切削速度v/(m/min)
图2 Salomon切削温度与切削速度曲线
7
高速切削的定义
高速范围与加工材料密切相关
工件材料
纤 维增 强 塑料
例如:在切削灰铸铁时,1000 m/min 以上才是高速车削,