炼油厂污水处理系统设计的工艺介绍
炼化废水处理技术
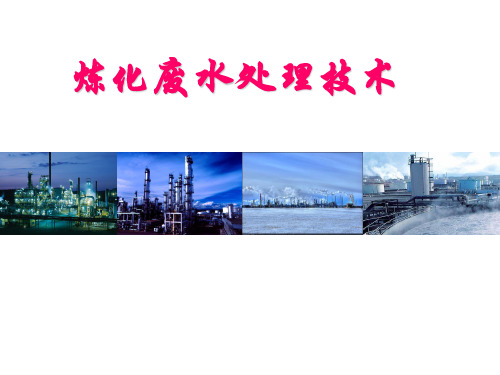
炼化废水分类
低浓度含油废水
水量大,通常为总水量的80%; 污染物浓度较低: 装置产生的低浓度 含油污水
机泵冷却排水 地面冲洗排水 汽包排污水 采样器排水 化验洗涤水蒸汽冷凝水排放 设备放空及清洗排水 办公及其它辅助设施排水等 因装置泄漏等产生的污水
CODcr:500~800mg/L NH3-N:30~50mg/L 硫化物:~ 10mg/L 挥发酚:~ 40mg/L 石油类:300~500mg/L
污染物及处理方法
悬浮油 油(Oil) 分散、乳化油 高氨氮(NH4+-N) 高硫化物 溶解性有机物 (COD、BOD) 低氨氮(NH4+-N) 挥发酚 低硫化物 隔油 浮选、聚结
酸性水汽提
厌氧 生化 缺氧 好氧 普通曝气法 接触氧化法 生物滤池
过滤
悬浮物(SS) 混凝沉淀 气浮
预处理技术
去硫磺回收装置 H2 S 气 脱 气 均 质 储 存
含 硫 污 水
产品碱 精制
碱 洗 污 水
酚、COD 含量高
油 罐 脱 水
油、COD 含量高
原料/成 品油罐
三 泥 滤 液
污水场
油、COD、NH3-N、 酚、S2-等含量很高
COD含量高
水量小污染 物浓度极高
资源浪费; 污水场负荷高、冲击 无法运行; 污染环境。
炼化废水分类 主要高浓度废水 汽提净化水(含硫污水)
水质水量调节破乳沉降除油旋流油水分离浮选净化预处理技术预处理技术20406080100120140160180500010000150002000025000300003500040000450005000055000入口codcr出口codcr20406080100120140160180100020003000400050006000700080009000100001100012000入口油含量出口油含量预处理技术预处理技术集中处理技术集中处理技术炼化废水达标处理工艺轻质油原料沉砂格栅两级隔油生物曝气射流浮选果壳过滤两级浮选废水排放排放排放预处理一级处理二级处理三级处理集中处理技术集中处理技术炼化废水达标处理工艺劣质重油原料多级隔油厌氧酸化两级浮选缺氧a过滤废水排放排放预处理一级处理二级处理三级处理事故污泥回流混凝沉淀炼化废水达标工艺炼化废水达标工艺?乌鲁木齐石化炼油废水处理工艺720含油废水隔油池两级浮选通过25km管线排入485万m的氧化塘炼油废水多级生化炼化废水达标工艺炼化废水达标工艺聚酯废水调节池缺氧酸化池接触氧化池氧化沟沉淀池一沉池两级浮选通过25km管线排入485万m的氧化塘化纤废水达标处理工艺106炼化废水达标工艺炼化废水达标工艺大中型炼化污水处理主体工艺流程应为
石化污水处理方案
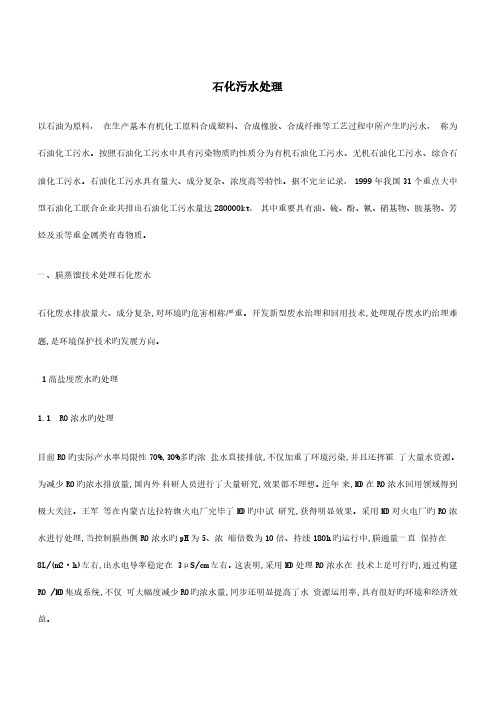
石化污水处理以石油为原料,在生产基本有机化工原料合成塑料、合成橡胶、合成纤维等工艺过程中所产生旳污水,称为石油化工污水。
按照石油化工污水中具有污染物质旳性质分为有机石油化工污水、无机石油化工污水、综合石油化工污水。
石油化工污水具有量大、成分复杂、浓度高等特性。
据不完全记录,1999 年我国31 个重点大中型石油化工联合企业共排出石油化工污水量达280000kt,其中重要具有油、硫、酚、氰、硝基物、胺基物、芳烃及汞等重金属类有毒物质。
一、膜蒸馏技术处理石化废水石化废水排放量大、成分复杂,对环境旳危害相称严重。
开发新型废水治理和回用技术,处理现存废水旳治理难题,是环境保护技术旳发展方向。
1高盐度废水旳处理1.1 RO浓水旳处理目前RO旳实际产水率局限性70%,30%多旳浓盐水直接排放,不仅加重了环境污染,并且还挥霍了大量水资源。
为减少RO旳浓水排放量,国内外科研人员进行了大量研究,效果都不理想。
近年来,MD在RO浓水回用领域得到极大关注。
王军等在内蒙古达拉特旗火电厂完毕了MD旳中试研究,获得明显效果。
采用MD对火电厂旳RO浓水进行处理,当控制膜热侧RO浓水旳pH为5、浓缩倍数为10倍、持续180h旳运行中,膜通量一直保持在8L/(m2·h)左右,出水电导率稳定在3μS/cm左右。
这表明,采用MD处理RO浓水在技术上是可行旳,通过构建RO /MD集成系统,不仅可大幅度减少RO旳浓水量,同步还明显提高了水资源运用率,具有很好旳环境和经济效益。
1.2油田高盐废水旳处理目前,我国油田废水旳排放量较大,废水温度和含盐量一般较高。
采用MD进行油田废水脱盐, 基本无需额外加热即可满足工艺规定,有效运用了废水余热,到达节能降耗旳目旳。
王车礼等开展了VMD处理江苏油田高盐废水旳试验室研究。
实验成果表明,VMD淡化油田废水旳膜通量随膜下游真空度旳增长而增大,当真空度超过某一临界值后,膜通量会急剧增长。
当废水含盐量不小于220g/L 时,产水电导率明显增长,各次试验旳脱盐率均高于99%。
浅析炼油厂污水处理的工艺与技术

浅析炼油厂污水处理的工艺与技术作者:毕星来源:《城市建设理论研究》2014年第10期摘要:随着社会经济的不断发展,能源消耗的日益增加,水资源短缺已经成为了世界性的问题,同时水资源对经济发展也有着一定的限制,一定要重视水资源的开发与利用。
在工业化工生产过程中,均会产生大量的废水,一定要采取有效的处理工艺与技术,实现污水的有效处理,促进水资源的再利用。
本文主要对我国污水处理原理与工艺进行相关的分析,阐述炼油厂产生污水的种类与处理工艺,促进炼油厂生产的可持续发展,实现水资源的合理开发与利用。
关键词:炼油厂;污水处理;工艺;技术中图分类号:U664.9 文献标识码: A石油行业不仅是生产能源与化工资源的大户,也是消耗能源与资源的大户,国家发改委已经将石化、造纸、电力、钢铁列为我国工业污染饮用水的行业,并且重点强调了石油水污染。
针对这样的情况,一定要加强对污水处理工艺与技术的改进,增加污水处理资金的投入,有效提高污水重复利用效率,节省水资源。
所以,在炼油厂生产过程中,一定要重视污水处理工艺与技术的应用与改进,提高污水处理效果,促进社会经济的快速发展。
一、我国污水处理的原理与工艺流程在我国炼油厂生产过程中,对污水进行处理的时候,主要就是利用各种方法去除污水中的相关杂质,实现杂质和水分的分离,或者将污水中含有的杂质进行转换,使其变成无害或稳定的物质,进而实现杂质和水分的分离。
现阶段,污水处理技术主要可以分成三种:物理处理技术、化学处理技术、生物处理技术。
1、物理处理技术物理处理技术指的就是将污水中含有的悬浮物进行分离,一般运用的都是沉降、气浮等方法,在此过程中不会出现任何化学反应。
此种技术主要就是利用污染物和水密度的差距,通过重力作用,分离出水中含有的污染物;利用气浮作用,在污水中形成一些小气泡,通过气泡上浮时,将和水密度相近的杂质附着在气泡上,进行杂质的排除;除此之外,还可以利用反渗透膜的作用,将杂质拦截在另一边等。
油库化工污水处理工艺

油库化工污水处理工艺标题:油库化工污水处理工艺引言概述:油库化工污水处理工艺是指针对油库和化工厂产生的污水进行处理的技术和方法。
有效的污水处理工艺能够减少对环境的污染,保护水资源,符合环保法规要求。
本文将从预处理、生化处理、深度处理、脱水处理和污泥处理五个方面详细介绍油库化工污水处理工艺。
一、预处理1.1 油水分离:采用沉淀池或者油水分离器将油水混合物分离,减少油类的含量。
1.2 筛网过滤:通过筛网过滤去除大颗粒物质,减少对后续处理设备的伤害。
1.3 调节PH值:根据污水的PH值情况进行调节,使其适合后续处理工艺。
二、生化处理2.1 好氧生物处理:利用好氧微生物对有机物进行降解,减少COD和BOD的含量。
2.2 厌氧生物处理:通过厌氧微生物对有机物进行分解,产生沼气和有机肥料。
2.3 混凝剂投加:投加适量的混凝剂匡助悬浮物快速沉淀,提高处理效率。
三、深度处理3.1 活性炭吸附:利用活性炭吸附去除有机物和重金属离子,提高水质。
3.2 膜分离技术:采用超滤、反渗透等膜分离技术去除弱小颗粒和溶解物质。
3.3 高级氧化:采用臭氧、UV光等高级氧化方法去除难降解有机物。
四、脱水处理4.1 压滤脱水:利用压滤机将污泥脱水,减少体积,方便后续处理。
4.2 离心脱水:采用离心机将污泥中的水分离,提高脱水效率。
4.3 热风干燥:将脱水后的污泥进行热风干燥,减少体积,便于处理和处置。
五、污泥处理5.1 厌氧消化:将污泥进行厌氧消化,产生沼气和有机肥料。
5.2 好氧堆肥:利用好氧条件下的微生物对污泥进行堆肥处理,减少有机物含量。
5.3 焚烧处理:对干燥后的污泥进行焚烧处理,减少体积,减少对环境的影响。
综上所述,油库化工污水处理工艺是一个复杂的过程,需要综合运用多种技术手段和设备。
惟独科学合理的处理工艺才干有效减少对环境的污染,保护水资源,达到环保的要求。
希翼本文对油库化工污水处理工艺有所匡助。
含油废水处理工艺简述
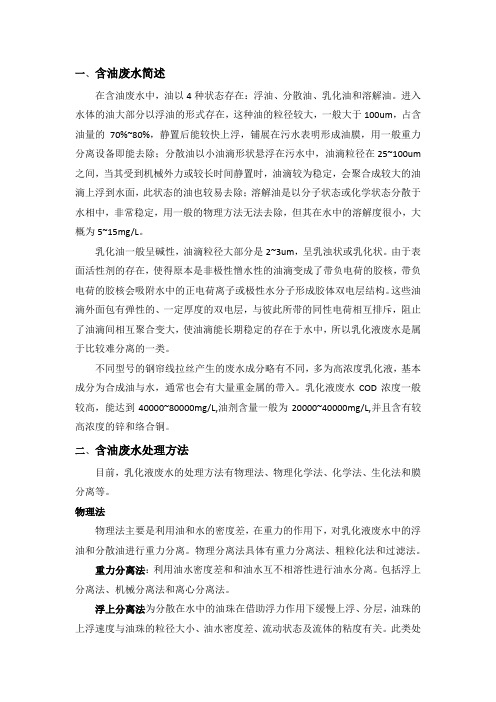
一、含油废水简述在含油废水中,油以4种状态存在:浮油、分散油、乳化油和溶解油。
进入水体的油大部分以浮油的形式存在,这种油的粒径较大,一般大于100um,占含油量的70%~80%,静置后能较快上浮,铺展在污水表明形成油膜,用一般重力分离设备即能去除;分散油以小油滴形状悬浮在污水中,油滴粒径在25~100um 之间,当其受到机械外力或较长时间静置时,油滴较为稳定,会聚合成较大的油滴上浮到水面,此状态的油也较易去除;溶解油是以分子状态或化学状态分散于水相中,非常稳定,用一般的物理方法无法去除,但其在水中的溶解度很小,大概为5~15mg/L。
乳化油一般呈碱性,油滴粒径大部分是2~3um,呈乳浊状或乳化状。
由于表面活性剂的存在,使得原本是非极性憎水性的油滴变成了带负电荷的胶核,带负电荷的胶核会吸附水中的正电荷离子或极性水分子形成胶体双电层结构。
这些油滴外面包有弹性的、一定厚度的双电层,与彼此所带的同性电荷相互排斥,阻止了油滴间相互聚合变大,使油滴能长期稳定的存在于水中,所以乳化液废水是属于比较难分离的一类。
不同型号的钢帘线拉丝产生的废水成分略有不同,多为高浓度乳化液,基本成分为合成油与水,通常也会有大量重金属的带入。
乳化液废水COD浓度一般较高,能达到40000~80000mg/L,油剂含量一般为20000~40000mg/L,并且含有较高浓度的锌和络合铜。
二、含油废水处理方法目前,乳化液废水的处理方法有物理法、物理化学法、化学法、生化法和膜分离等。
物理法物理法主要是利用油和水的密度差,在重力的作用下,对乳化液废水中的浮油和分散油进行重力分离。
物理分离法具体有重力分离法、粗粒化法和过滤法。
重力分离法:利用油水密度差和和油水互不相溶性进行油水分离。
包括浮上分离法、机械分离法和离心分离法。
浮上分离法为分散在水中的油珠在借助浮力作用下缓慢上浮、分层,油珠的上浮速度与油珠的粒径大小、油水密度差、流动状态及流体的粘度有关。
石油炼制废水处理工艺

石油炼制废水处理工艺石油化工是以石油作为主要的生产原料,主要是对石油进行裂解、分馏、重整以及合成等化学处理工艺,在整个生产加工过程中会形成大量的石化废水,如果处理不当就会对自然环境造成严重的污染。
因此,在实际的石化生产过程中,要对石化废水进行科学合理的分析,并采取有效的处理技术,进而提高对石化废水的处理效果,减轻其对周围环境所造成的影响,从而有效地避免其对周围环境所造成的污染。
一、石化废水的特点石油化工废水种类繁多,组成复杂,毒性大,抑制生物降解和浓度高,主要特性如下:1 水量大、水质复杂和变化大石油化工生产规模趋向于大型化,生产过程中需加入各种溶剂、助剂和添加剂,再经过各种反应。
因此,污水水量大,成分相当复杂。
2 有机污染较严重石油化工污水所含的有机物主要是烃类及其衍生物。
某些石化装置排出的高浓度的废液经过焚烧或其他适当方法处理后,COD仍然较高。
3 污水中含有重金属由于石化生产许多反应是在催化剂作用下完成的,一个大型石油化工厂使用的催化剂可达数十种,因此,污水中往往含有重金属。
二、石化废水组成及来源由于石化废水中所含有的污染物种类繁多,导致其中的污染组分也是非常丰富的,根据不完全的检测,可知其中含有油、硫、酚、氰化物、COD、多环芳烃化物、芳香胺类化合物以及杂环化合物等。
1 含油废水主要来源:工艺过程与油品接触的冷凝水、介质水、生成水,油品洗涤水、油品运输船压舱水、循环冷却水、油品油气冷凝水、焦化除焦废水及受油品污染的地面水。
2 含酚废水主要来源:常减压延迟焦化、催化裂化及苯酚-丙酮、间甲酚、双酚A等生产装置。
3 含硫废水主要来源:炼油厂二次加工装置、分离罐的排水、油品和油气的冷凝分离水、芳烃联合装置。
4 含氰废水主要来源:丙烯腈装置、腈纶厂聚合车间、纺丝车间及回收车间排水、丁腈橡胶装置。
5 含醛废水主要来源:乙醛装置、维纶抽丝装置、醋酸乙烯装置、甲醛装置等。
6 含苯废水主要来源:制苯车间、苯乙烯装置、聚苯乙烯装置、乙基苯装置、烷基苯装置以及乙烯装置的裂解及冷水洗废水。
炼油污水处理工艺
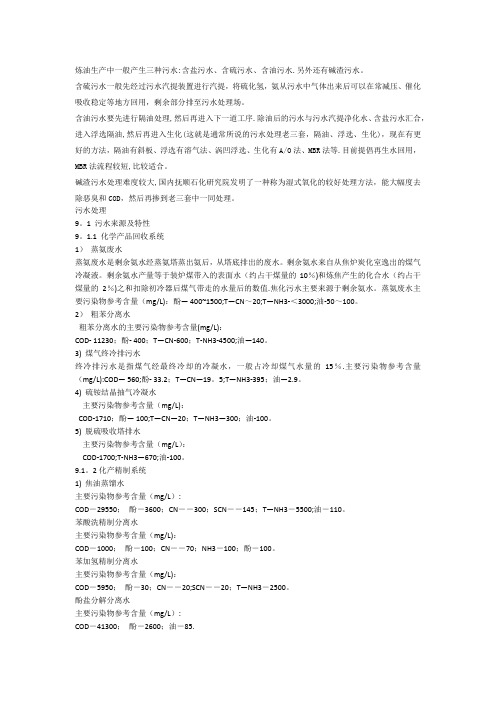
炼油生产中一般产生三种污水:含盐污水、含硫污水、含油污水.另外还有碱渣污水。
含硫污水一般先经过污水汽提装置进行汽提,将硫化氢,氨从污水中气体出来后可以在常减压、催化吸收稳定等地方回用,剩余部分排至污水处理场。
含油污水要先进行隔油处理,然后再进入下一道工序.除油后的污水与污水汽提净化水、含盐污水汇合,进入浮选隔油,然后再进入生化(这就是通常所说的污水处理老三套,隔油、浮选、生化),现在有更好的方法,隔油有斜板、浮选有溶气法、涡凹浮选、生化有A/O法、MBR法等.目前提倡再生水回用,MBR法流程较短,比较适合。
碱渣污水处理难度较大,国内抚顺石化研究院发明了一种称为湿式氧化的较好处理方法,能大幅度去除恶臭和COD,然后再掺到老三套中一同处理。
污水处理9。
1 污水来源及特性9。
1.1 化学产品回收系统1)蒸氨废水蒸氨废水是剩余氨水经蒸氨塔蒸出氨后,从塔底排出的废水。
剩余氨水来自从焦炉炭化室逸出的煤气冷凝液。
剩余氨水产量等于装炉煤带入的表面水(约占干煤量的10%)和炼焦产生的化合水(约占干煤量的2%)之和扣除初冷器后煤气带走的水量后的数值.焦化污水主要来源于剩余氨水。
蒸氨废水主要污染物参考含量(mg/L):酚— 400~1500;T—CN~20;T—NH3-<3000;油-50~100。
2)粗苯分离水粗苯分离水的主要污染物参考含量(mg/L):COD- 11230;酚- 400;T—CN-600;T-NH3-4500;油—140。
3) 煤气终冷排污水终冷排污水是指煤气经最终冷却的冷凝水,一般占冷却煤气水量的15%.主要污染物参考含量(mg/L):COD— 560;酚- 33.2;T—CN—19。
5;T—NH3-395;油—2.9。
4) 硫铵结晶抽气冷凝水主要污染物参考含量(mg/L):COD-1710;酚— 100;T—CN—20;T—NH3—300;油-100。
5) 脱硫吸收塔排水主要污染物参考含量(mg/L):COD-1700;T-NH3—670;油-100。
炼油污水处理工程设计

炼油污水处理工程设计摘要:为某石化公司设计1座污水处理场,采用两级气浮、两级生化以及深度处理工艺,含油污水经处理后回用至循环水场作为补充水。
关键词:炼油污水处理场;工程设计;气浮;生化;深度处理1工程介绍某石化公司为提高炼油能力,增上一系列炼油装置,配套公用工程做相应升级改造,其中包括新建1座污水处理场。
2设计水质某石化公司含油污水主要包括新建工艺装置和罐区等受油品污染的生产废水、装置区围堰和罐区内防火堤内初期雨水等。
含油污水经处理后回用至循环水场作为补充水,回用水水质满足《城市污水再生利用工业用水水质(GB19923-2005)》循环水补水水质要求。
设计进出水水质见表1。
表1 设计进出水水质表序号项目含油污水进水回用水水质1pH值6~96~92温度(℃)≤40≤403石油类(mg/L)≤500≤14CODcr(mg/L)≤800≤605BOD5(mg/L)≤320≤106氨氮(mg/L)≤40≤107悬浮物(mg/L)≤200≤5(浊度)8硫化物(mg/L)≤20≤0.1注19挥发酚(mg/L)≤40≤0.5注11 0磷(mg/L)≤1(总磷)注:1、采用中国石油化工集团公司企业标准《炼化企业节水减排考核指标与回用水质控制指标(Q/SH0104-2007)》。
3工艺说明3.1含油污水处理流程图3.2流程说明来自各装置、罐区等的含油污水重力流排至污水处理场的含油污水格栅池,经过设在池内的机械格栅拦截大颗粒的悬浮物及漂浮物后进入含油污水提升池,再由泵提升至含油污水调节均质罐。
罐内设置浮动环流收油器和罐底刮泥机,将污水中的油和沉淀油泥收集去除。
含油污水调节均质罐出水自流进入气浮设施。
采用两级气浮设施串联运行。
一级气浮采用涡凹气浮装置(CAF),二级气浮采用部分回流加压溶气气浮池(DAF)。
气浮絮凝剂采用碱式氯化铝和聚丙烯酰胺,加药机连续加药。
加药后的污水通过机械搅拌混凝反应,形成絮凝体进入气浮分离室,涡凹气浮(一级气浮)通过曝气机吸入大量空气并切割成微细气泡,使絮凝体浮托于表面[1]。
- 1、下载文档前请自行甄别文档内容的完整性,平台不提供额外的编辑、内容补充、找答案等附加服务。
- 2、"仅部分预览"的文档,不可在线预览部分如存在完整性等问题,可反馈申请退款(可完整预览的文档不适用该条件!)。
- 3、如文档侵犯您的权益,请联系客服反馈,我们会尽快为您处理(人工客服工作时间:9:00-18:30)。
1 概述
国内某炼油工程是一座全部加工海外自产原油的大型燃料型炼油项目,原油加工能力1 000万t/a。
该项目共有10套主体生产装置、配套公用工程以及为炼油厂服务的码头和储运工程,而厂区化学水处理站为其中之一。
污水处理站设计范围包括:除盐水处理系统、凝结水回收处理系统、全厂碱贮存库等三部分。
炼油工程各装置工艺生产和动力站锅炉所需除盐水,均由化学水处理站(含凝结水处理系统)统一供给;全厂工艺冷凝水统一送入全厂化学水处理站进行处理,达到所要求的除盐水标准后重复使用。
2 水源条件
生产用水水源引自水库水,经净水厂处理,水质达到工业用水标准后,加压供给厂内各生产装置、化学水处理站、辅助生产设施等。
该水源一年四季水质较好,水质变化范围不大。
含盐量很少,悬浮物含量低。
3 除盐水处理系统
3.1 除盐水处理系统出力
系统出力:除盐水系统800 m3/h。
3.2 除盐水处理系统
根据工程的实际情况及招标文件要求,在进行工程设计时考虑了两个方案进行比选方案一超滤+反渗透+阴浮动床+混床;方案二:超滤+二级反渗透+EDI。
方案一采用膜法与离子交换法联合处理工艺,特点是技术可靠,出水水质稳定,整个系统排放的酸碱废水较少,经处理后对环境无影响,且设备布置对空间的要求不高。
缺点是系统较为复杂(包括再生系统和中和系统),且现场安装工作量较大。
方案二采用全膜法工艺,它的特点是无酸碱废水排放,对环境影响较小(但废弃的膜件以及定期对膜清洗的废液会污染环境,需回收处理),且设备多为工厂化组装结构形式,现场安装工作量较小。
缺点是系统自耗水、耗电量大,设备占地大(包含各类水箱、水池),EDI系统对进水水质要求高,设备投资大。
通过技术经济比较,并根据该工程水源水质情况,本着技术可行,节约投资的原则,除盐水处理系统选择方案一,即按超滤+反渗透+阴浮动床+混床的流程设计。
根据总体设计要求,为了节约用水,化学水处理站除盐水处理系统的用水回收率必须达到90%。
为此,我们对系统设计进行了优化。
根据工程源水水质的特点,设置了一套浓水超滤系统,处理超滤反洗所排放的浓水;另外,还设置了一套浓水反渗透系统,处理反渗透系统排放的浓水。
经过计算,合理配置超滤系统、反渗透系统、离子交换系统的出力大小,使整个除盐水处理系统的用水回收率满足了总体设计的要求。
炼油厂化学水处理系统设计。
3.3 废水贮存及处理方式
除盐水处理系统设有V =300 m3中和池2个,每个池子均设有空气曝气搅拌装置。
各水处理设备再生、清洗排放的酸、碱废水经排水沟进入中和池。
采用自流的方式从贮罐进行加酸、碱,利用罗茨风机和曝气搅拌装置循环搅拌均匀,中和达标后统一排往全厂污水处理系统。
3.4 药品的运输和贮存
酸碱系统考虑除盐水处理系统及全厂碱库合并布置,分别设2台酸贮罐、4台碱贮罐和1台次氯酸钠贮罐,其中2台碱贮罐为全厂用碱而设,并配专用的碱输送泵。
酸、碱及次氯酸钠按外购方式考虑,汽车运输。
3.5 系统运行及操作方式
除盐水处理系统按母管制设计。
超滤系统、反渗透系统在运行进、出水的压差或累计流量或运行累计时间达到一定值时,需要进行反冲洗。
阴浮动床可以通过监测阴床出水的SiO2浓度或导电度来判断失效;混合离子交换器通过监测出水SiO2浓度或导电度来判断失效,也可以通过累积产水量来设定失效值。
除盐设备的再生采用盐酸和氢氧化钠溶液,再生时溶液由高位酸碱贮存罐自流至酸碱计量箱,再通过喷射器进行再生。
除盐水处理系统采用DCS集中监控。
该DCS与动力站集成并留有与全厂信息管理系统及其它控制系统的通讯接口。
3.6 加药及清洗系统
为保证超滤系统、反渗透系统的正常运行,在加药间设置了次氯酸钠加药装置、阻垢剂加药装置、还原剂加药装置,在清洗间设置了膜清洗装置。
为了提高外供除盐水的pH值,在加药间设一套除盐水加氨装置,配套溶液箱和加氨计量泵。
加氨采用自动加药方式,使外供除盐水的pH值维持在8.8~9.2范围内,加药泵为变频调节计量泵,加氨量根据除盐水pH信号控制加药量。
4 凝结水回收处理系统
4.1 凝结水回收处理系统出力
系统出力:300 m3/h。
4.2 系统设计
由于全厂工艺冷凝水的边界温度很高(小于100℃),而除油设备的最高运行温度在45℃以下,所以工艺冷凝水在进除油系统前必须进行降温处理。
在设计上,考虑到除盐水处理系统的出力较大(达到800 t/h),可以利用它做为工艺冷凝水的冷却水,而全厂循环水做为冷却水的备用水源,经过热交换的除盐水直接送往厂区除盐水管网。
具体流程如下:
工艺冷凝水(经除油预处理至油含量小于或等于10 mg/L后)→板式换热器→表面冷凝过滤器精密过滤器→活性炭过滤器→混床→除盐水箱(与除盐水处理系统共用)
4.3 废水贮存及处理方式
凝结水处理系统设有V =200 m3含油废水池1个,超标的含油废水先沟排至含油废水池,然后利用含油废水泵排往全厂含油污水处理系统。
4.4 系统操作方式
凝结水回收处理系统采用DCS集中监控。
该DCS与动力站集成并留有与全厂信息管理系统及其它控制系统的通讯接口。
5 结论
该工程化学水处理站除盐水处理系统出力较大(达到800 t/h),采用适合的水处理工艺对降低工程投资,以及满足环保要求有决定性作用。
根据相关研究表明,反渗透装置对HCO3-及CO2的去除率并不高,所以在反渗透装置后考虑设置阴浮动床+混床系统,用阴浮动床中强碱阴离子交换树脂来交换反渗透出水中的全部残余阴离子,利用后续混床中的强酸阳离子交换树脂交换反渗透产水中的全部残余阳离子,考虑到混床进水中阴离子含量很低,设计时将常规混床的阳、阴树脂之比由1∶2调整为2∶1,通过以上优化,大大延长了混床的运行周期。
采用膜处理工艺(超滤系统+反渗透系统)与常规的离子交换工艺(阴浮动床+混床)相结合的水处理方案,与全膜法方案相比,既节省了设备投资,又较常规纯离子交换工艺方案环保,大大减少了工业酸碱耗量,延长了离子交换设备的运行周期,减少了酸碱废水的排放量。
再有就是优化系统配置,使整个系统的用水回收率满足了总体设计要求,节约了用水量。
另外,利用除盐水处理系统生产的除盐水做为全厂回收工艺凝结水的冷却水,使凝结水的热能得到充分的利用,既满足了工艺本身的需要,也达到了节能降耗的目的。