模切常见质量问题分析及处理 - 副本 - 副本
模切问题点【范本模板】

一、模切机常见问题与解决方案输纸部分1. 走纸不稳,需经常调节该故障主要是针对国产模切机而言的,由于国产模切机多数没有采用带吸气的传送带,容易导致走纸不稳,纸张定位精度不高,输纸导轮、输纸带、压纸毛轮、前规挡块.侧规挡块等容易磨损.在走纸之前对纸张进行敲纸、打边并在走纸过程中加以调节可有效解决此问题。
2。
输纸不顺畅引起输纸不顺畅的原因有多种,主要为纸张变形、印刷品表面过于光滑或由其他机械故障引起。
(1)由纸张变形引起的输纸不顺畅由于模切加工是整个印刷加工最末端的一道工序,纸张经过若干工序加工后容易产生变形,特别是经过高温、高压的上光.覆膜后的纸张变形更加严重,这时飞达往往不能 J 顷利地送纸。
(2)由印刷品表面过于光滑引起的输纸不顺畅上光覆膜后的产品由于其表面过于光滑,也会给输纸造成一定的困难.对于以上两种情况,有经验的操作人员会在上纸之前做好前期准备工作,比如:装纸时,在纸张中加入一些木楔子或纸卷使纸张保持平整,在上纸时预先进行打边、敲纸工作或把模切机的速度适当降低,一般可以避免此问题的发生。
(3)机械故障引起的输纸困难飞达吸嘴吸力不够、距离纸堆上平面的位置不合适、规矩的定位不准确等机械原因会造成输纸过程中出现斜张,双张、空张等故障。
只要平时做好模切机保养工作和机械部位的调节就会避免由于机械故障产生的输纸困难二、模切机模切部分常见问题与解决方案。
A。
压力不均匀模切压痕过程中压力不均匀,一般有两种情况:1。
如果压力有轻微的不均匀,可能是由于模切刀、线(钢刀、钢线)分布不均,造成动平台在模切时受力歪斜所致,此时应在模切版上加装平衡刀线,使平台受力均匀。
2. 如果平台前后成四角处出现比较严重的压力不均匀现象,则主要是支撑动平台的四个连杆摆杆高度不一致造成的,此时应打开模切底座的护罩,检查摆杆是否磨损,如磨损严重则需更换,否则需要调整四个压力调整斜铁,直到压力一致为止.B。
模切精度不高模切的精度是衡量模切质量最为重要的标准之一,是生产出合格产品的重要保证,在实际生产过程中,常常出现模切精度达不到设计要求的情况。
六种常见模切故障讲解
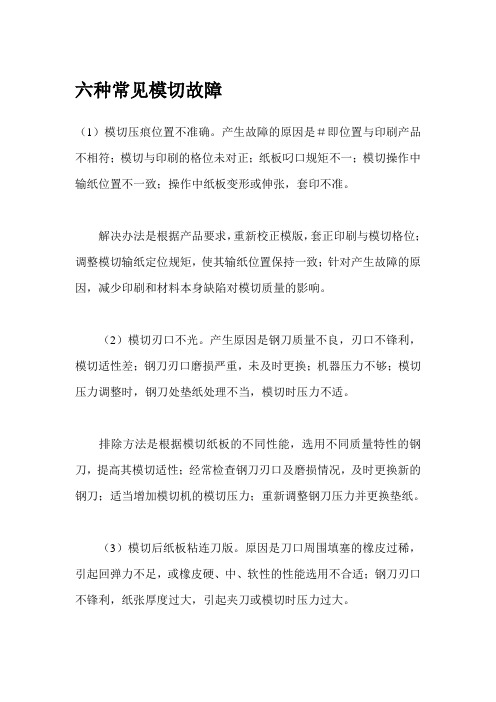
六种常见模切故障(1)模切压痕位置不准确。
产生故障的原因是#即位置与印刷产品不相符;模切与印刷的格位未对正;纸板叼口规矩不一;模切操作中输纸位置不一致;操作中纸板变形或伸张,套印不准。
解决办法是根据产品要求,重新校正模版,套正印刷与模切格位;调整模切输纸定位规矩,使其输纸位置保持一致;针对产生故障的原因,减少印刷和材料本身缺陷对模切质量的影响。
(2)模切刃口不光。
产生原因是钢刀质量不良,刃口不锋利,模切适性差;钢刀刃口磨损严重,未及时更换;机器压力不够;模切压力调整时,钢刀处垫纸处理不当,模切时压力不适。
排除方法是根据模切纸板的不同性能,选用不同质量特性的钢刀,提高其模切适性;经常检查钢刀刃口及磨损情况,及时更换新的钢刀;适当增加模切机的模切压力;重新调整钢刀压力并更换垫纸。
(3)模切后纸板粘连刀版。
原因是刀口周围填塞的橡皮过稀,引起回弹力不足,或橡皮硬、中、软性的性能选用不合适;钢刀刃口不锋利,纸张厚度过大,引起夹刀或模切时压力过大。
可根据模版钢刀分布情况,合理选用不同硬度的橡皮,注意粘塞时要疏密分布适度;适当调整模切压力,必要时更换钢刀。
(4)压痕不清晰有暗线、炸线。
暗线是指不应有的压痕,炸线是指由于压痕压力过重、纸板断裂。
引起故障的原因是:铜线垫纸厚度计算不准确,垫纸过低或过高;铜线选择不合适;模压机压力调整不当,过大或过小;纸质太差,纸张含水量过低,使其脆性增大,韧性降低。
应重新计算并调整钢线剪纸厚度;检查铜线选择是否合适;适当调整模切机的压力大小;根据模压纸板状况,调整模切压痕工艺条件,使两者尽量适应。
(5)折叠成型时,纸板折痕处开裂。
折叠时,如纸板压痕外侧开裂,其原因是压痕过深或压痕宽度不够;若是纸板内侧开裂,则为模压压痕力过大,折叠太深。
可适当减少钢线剪纸厚度;根据纸板厚度将压痕线加宽;适当减小楼切机的压力;或改用高度稍低一些的铜线。
(6)压痕线木规则。
原因是铜线垫纸上的压痕槽留得太宽,纸板压痕时位置不定;铜线垫纸厚度不足,槽形角度不规范,出现多余的圆角,排刀、固刀紧度不合适,铜钱太紧,底部不能同压板平面实现理想接故,压痕时易出现扭动;铜线太松,压痕时易左右窜动。
模切过程中存在六大质量问题及解决办法

模切过程中存在六大质量问题及解决办法1. 模切精度不高精度不高的原因有模切版本身的问题,也有来自印刷品的问题。
手工制作的模切版,误差较大;模切压痕与印刷的作业环境不同会造成纸张变形,导致模切压痕位置不准,尤其是经过上光、覆膜的纸张变形更严重,影响模切精度。
解决办法:选择先进的制版方式,提高模切版的精度:尽量保证模切压痕与印刷在同一作业环境下进行或保证作业环境的同一性(即有相同的温度、湿度等);对上光和覆膜的印张要进行模切预处理,尽量减少纸张变形对模切精度的影响。
2. 模切压痕产生爆线和暗线“爆线”是指由于模切压痕压力过大,超过了纸板纤维的承受极限,使纸板纤维断裂或部分断裂;“暗线”是指不应有的压痕线。
一般是由模切版和压痕钢线选择不合适,模切压力调节不当,纸张质量差,纸张的纤维方向与模切版排刀方向不一致或纸张的含水量低导致纸张柔韧性下降所引起的。
解决方法:选择合适的模切版;适当调节模切机的压力;在模切之前先把要模切的纸张放置在车间里一段时间;加大车间环境的湿度。
另外还有一种特殊情况,就是在模切硬盒烟包小盒时,由于很多位置的压痕线之间距离很近,如果按正常情况配置压痕钢线的高度,模压时对纸张的拉力过大,也会造成爆线。
因此,应设法把对纸张产生的拉力降到最小。
方法有两个:一是降低压痕钢线的高度;二是减少压痕底模条的厚度,两者不能同时使用,否则起不到很好的压痕效果。
较好的方法是降低压痕钢线的高度,降低的高度通常为0.1~0.2mm。
根据纸张厚度确定具体降低多少,定量在350g/m2以上的纸张需降低0.2mm,350g/m2以下的纸张降低0.1mm为宜。
3. 压痕线跑位.不饱满压痕钢线在模切压力的作用下出现扭动会导致压痕线跑位;模切压力不足会导致压痕不饱满。
分别采用更换模切版和加大模切压力的方法可改善此问题。
4. 模切起毛,起尘在模切时,经常会出现模切产品切边不光洁、起毛的现象,特别是一些离压痕线较近的切边处更是严重。
模切工程改善方案

模切工程改善方案摘要模切工程是制造业中常见的一种加工工艺,是通过专用模刀对材料进行切割成特定形状的工艺。
模切工艺在许多行业中都有着重要的应用,如印刷包装、汽车制造、电子产品等。
然而,模切工程在实际生产中存在一些常见的问题,例如工艺精度不高、生产效率低、模刀磨损严重等,这些问题严重影响了生产质量和效益。
因此,本文将针对模切工程的问题进行分析,并提出相应的改善方案,以期提高模切工程的生产效率和产品质量。
第一部分:模切工程存在的问题及原因分析1.1 工艺精度不高模切工程中,对模刀的精度要求较高,模刀一旦精度不够就会导致产品尺寸不准确,影响产品质量。
而造成这个问题的主要原因有以下几点:a. 模刀设计不合理:模具设计不合理、结构复杂,导致模具切割精度不高。
b. 刀具磨损和变形:由于模切生产时间长,刀具磨损严重,导致切割精度下降。
c. 材料变形:在模切过程中,因为材料的紧张翘曲或弹性回缩等导致产品尺寸变形。
1.2 生产效率低模切过程中,生产效率的低下也是一个比较普遍的问题。
主要原因包括:a. 刀具更换频繁:由于模切刀具磨损严重,需要频繁更换,导致生产效率低下。
b. 调试时间长:由于模切机器设备和模刀的调试时间长,也影响了生产效率。
c. 人为操作不当:操作人员对模切工艺不熟悉,导致操作不当,影响了生产效率。
1.3 模刀磨损严重模切生产中,模刀的磨损严重也是一个普遍问题,主要原因有:a. 材料质量差:模刀的材料质量差,磨损速度快。
b. 切割压力过大:模切切割压力过大,加速了模刀的磨损。
c. 刀具材料选择不当:刀具材料硬度不够或者不适用于实际生产场景。
以上就是模切工程目前存在的一些问题和原因分析,下面我们将就这些问题提出相应的改善方案。
第二部分:模切工程的改善方案2.1 模刀设计优化首先,应该对模刀进行设计优化,提高模刀的切割精度和使用寿命。
要解决模刀设计不合理的问题,可以采取以下几种方法:a. 使用高精度的数控加工工艺,提高模刀的加工精度和表面光洁度。
薄膜分切常见问题及解决方案

薄膜分切常见问题及解决方案薄膜除了在生产制造过程中,因吹膜和流延等工艺对薄膜质量产生影响,其实在后道工序,如收卷、分切等过程也会对薄膜品质产生影响,薄膜生产厂家也应引起重视。
我们通过整理,归纳一些分切过程中常见问题及解决方案。
1. 分切时膜面出现划伤原因:在进行镀铝膜、涂布膜以及印刷膜时,各导辊、过辊表面有异物,就会划伤膜面,发生质量问题。
解决方法:在进行分切工艺前,清洁分切设备各导辊、过辊,做到清洁无异物 2. 分切时薄膜出现拉伸现象原因:在进行PE、PP、WMPET等薄膜的分切时,因收卷张力过大极易造成薄膜拉伸现象。
解决方法:适当减小收卷张力。
3. 分切膜卷端面整齐度差原因1:分切时光电跟踪不准确。
解决方法:1.光电眼调整方法及工作状态选择不正确,应按操作规程要求重新调整。
2.跟踪线色差不明显,应增大色差对比。
原因2:收卷张力小。
解决方法:增加收卷张力,必要时向磁粉离合器中加入适量的新磁粉。
原因3:薄膜产生静电积累,薄膜之间发生粘连或漂移。
解决方法:在分切设备上接入导静电设备,并将触角之一接触膜卷背面。
4. 分切时出现皱折原因1:在分切过程中,压辊与膜卷成接触状态并向膜卷施加压力,起到缓冲膜卷震动和防止空气卷入膜卷的作用。
当压辊直径大于膜卷直径时,膜与压辊形成的包角大,就会有空气卷入膜卷而产生纵向皱折;随着膜卷直径的增加,当压辊直径小于膜卷直径时,膜与压辊形成的包角变小,卷入的空气就少,膜卷较为整齐。
解决方法:选用直径大的纸芯,减小压辊直径。
原因2:压辊作用于膜卷的压力由气缸压力产生,并随着膜卷直径和分切线速度的增加而增加。
由于压辊压力的增加,容易造成膜卷“内松外紧”现象,皱折由此而产生。
解决方法:随着膜卷直径和分切线速度的增加,适当调小压辊压力。
原因3:在分切过程中,张力设置过大,膜卷收卷时横向受力分配不均匀。
膜卷平整度较差,极易产生皱折。
若张力设置太小,膜卷收卷时容易发生跑边、膜卷松动。
模切中存在的质量问题及其解决方法

解决 方 法 :首先 要根 据纸 张选 用不 同类 型 的模切 刀 。模 切 刀包括 直 纹 刀和 横 纹 刀 两 种 纹路 的 刀锋 又有高 矮 之分 刀锋 形成 的纹 路和 高 矮不 同 直 接 关系 到 模切 质 量和模 切 刀 的使 用寿 命 。在避 免模 切 起毛 方 面 直纹 刀 比横纹 刀好 在使 用寿 命方 面 矮 锋 刀 比高 锋 刀好 。在 模切 覆 膜 卡 纸 时 应 选 用直 纹 高 锋 刀 要求 刀锋 是 磨 制 的 .最好 不要 采 用压 凹凸一 次
. 一 . .
时 间 :提高 车 间环境 的相 对 湿度 。
另外 还 有 一 种 特 殊 的 情 况 ,就 是 在 模 切 硬 盒 烟 包 小 盒 时 , 由于 很 多 位 置 的压 痕 线 之 间 距 离 很 近 ,如 果 按 正 常 情 况 配 置 压 痕 钢 线 的高 度 模 压 时 对 纸 张 的拉
切 版和 压 痕 钢线 选择 不 合适 模 切 压 力调 节 不 当 纸 张
线 不 饱满 。
3 28 2 0 0
j; t0
目 警 - :l 0 蛹 _
印技 包 装 印 刷 术・ 装 潢 刷
维普资讯
技术看台
专 题报道
解决方法 :分别采用更换模切版和加大模切压力的方法可改善此问题。
压 痕 钢 线 对 纸 张 产 生 的 拉 力 。如 模 切 定 量 为 3 0 / 的纸张 时通 常选 用0 4 m ×1 r m 0 g m r a 3 a
版 的精 度 。尽 量保 证 模切 压 痕 与印 刷过 程在 同一 作 业 环 境 下 进 行 或保 证 作 业 环境 的 同一 性 ( 即相 同 的温 度 相 对 湿 度等 ) ;对 上 光 和 覆膜 后 的纸 张要 进行 模 切 预处 理 .尽 量减 少纸 张 变形对 模切 精度 的影 响 。
纸箱厂复瓦印刷模切三道工序常见质量问题分析及处理

修复或更换瓦楞辊 更换瓦楞原纸或改善预热器效果 适当调整张力控制系统,加大张力
修正、调整瓦楞辊,校正平行度 调整配合压力 降低车速或更换原纸 调整预调整器 调整退纸架张力控制器 清理、修正或更换瓦楞辊 增加瓦楞辊的呲合力 清理、更换或调整导纸板 调整退纸架张力控制器 调整预调器的效果
加大输送过桥的张力控制系统,增加或
清除异物,保持表面清 适当预热或间隙,减少
4、楞不均
5、楞损伤
清理瓦楞辊表面清洁 修正上、下瓦楞贴合间 检查、修正、清理或更换 加大预热包角 适当调整张力控制 修复或更换瓦楞辊 修正、调整贴合间隙 检查、修正、清理或更换 清理压力辊,修正压力辊、校 检查、修复机械性不当造成 更换瓦楞原纸或提高预热
瓦楞纸板生产中的质量控制
质量问题
产生原因
解决办法
1)瓦楞辊表面温度不均衡 2)瓦楞辊磨损 3)瓦楞辊运转不正常 4)瓦楞辊贴合间隙不一致 5)上、下瓦楞不平行 6)瓦楞辊表面不干净 7)导纸板位置不当,带脏污磨损 1、高低楞 8)导纸板架不平行 9)压力辊的轴承磨损 10)输送过桥张力不均衡 11)涂胶辊、浮动辊间隙不当 12)胶黏剂质量不好 13)箱纸板和瓦楞原纸含水量不均匀、张力小 14)对瓦楞原纸的蒸汽喷雾不足 1)瓦楞辊不平行 2)瓦楞辊贴合间隙太小 3)输送过桥张力过大 2、楞倾斜(倒楞) 4)涂胶辊和浮动辊不平行 5)双面机压辊位置不当或压力大 6)瓦楞原纸含水量过高 7)双面机的传送带打滑 1)瓦楞辊表面不清洁 2)瓦楞辊热量不匀衡 3)瓦楞辊表面磨损、变形或调节不良 4)瓦楞辊配合压力不合适 5)导纸板位置不当、带脏或磨损
修正、调整瓦楞辊的平
6、楞折皱
6、楞折皱
2)瓦楞辊磨损 3)瓦楞原纸质量不好或水分不均衡 4)瓦楞原纸张力太小
印刷模切中常见问题
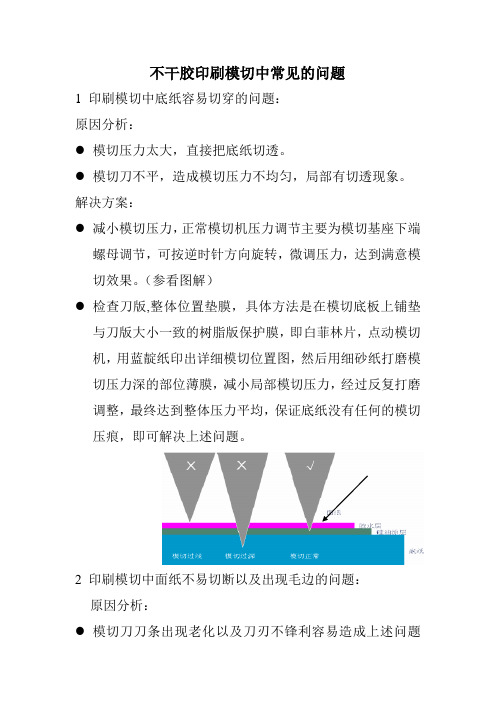
不干胶印刷模切中常见的问题1 印刷模切中底纸容易切穿的问题:原因分析:●模切压力太大,直接把底纸切透。
●模切刀不平,造成模切压力不均匀,局部有切透现象。
解决方案:●减小模切压力,正常模切机压力调节主要为模切基座下端螺母调节,可按逆时针方向旋转,微调压力,达到满意模切效果。
(参看图解)●检查刀版,整体位置垫膜,具体方法是在模切底板上铺垫与刀版大小一致的树脂版保护膜,即白菲林片,点动模切机,用蓝靛纸印出详细模切位置图,然后用细砂纸打磨模切压力深的部位薄膜,减小局部模切压力,经过反复打磨调整,最终达到整体压力平均,保证底纸没有任何的模切压痕,即可解决上述问题。
2 印刷模切中面纸不易切断以及出现毛边的问题:原因分析:●模切刀刀条出现老化以及刀刃不锋利容易造成上述问题发生。
●模切压力不足也容易导致上述问题发生。
解决方案:●检查并更换刀版的模切刀条,区分模切纸类和膜类材料的区别。
参看图解,刀条刀刃角度较宽的适合模切纸类材料,刀条刀刃较窄的适合模切膜类材料。
主要应用在圆刀模切上。
●增加模切刀版压力,顺时针旋转模切机压力螺母,调到合适压力。
3印刷模切中出现的溢胶问题:原因分析:•模切刀条老化以及刀刃不锋利,参看图解2,刀刃磨损钝化后,模切纸张时,胶水被挤向两边,面纸虽被切断,但是胶水没有完全被切断,造成排废时胶水拉丝及胶水回流,形成溢胶。
•模切刀胶丝未完全切断,参看图解1,造成排废拉丝。
•模切压力太深硅油层及底纸被切穿,造成胶水被挤入底纸中,导致排完费边后,标签周围有胶水残留,形成溢胶现象。
•收卷过程中,因为收卷张力过大,造成标签缠绕过紧形成溢胶及标签移位,,主要体现在卫星轮转机和有张力收卷的间歇机上。
解决方案:•更换刀条保持刀刃锋利,并在刀刃上喷涂少量硅油脱模剂,杜绝模切后标签与排废边再次重新复合,影响排废效果。
•调整模切压力与模切刀的平整。
•减小收卷张力,避免张力过大造成标签移位及胶水溢出,具体张力数值依据轮转机机器型号不同,而有所区别,主要张力数值控制在8-16之间,具体数值可咨询机器制造厂家,张力数值大小调节主要体现在纸类收卷和膜类收卷上,膜类收卷张力普遍要小于纸类收卷张力。
- 1、下载文档前请自行甄别文档内容的完整性,平台不提供额外的编辑、内容补充、找答案等附加服务。
- 2、"仅部分预览"的文档,不可在线预览部分如存在完整性等问题,可反馈申请退款(可完整预览的文档不适用该条件!)。
- 3、如文档侵犯您的权益,请联系客服反馈,我们会尽快为您处理(人工客服工作时间:9:00-18:30)。
改用质量好的模切刀
可将纸板进行抽湿处理再进行模切
按纸板厚度合理选择压痕线型号
按纸板厚度和压痕线宽度合理选择痕模切压力大小,纸板含水量过低, 纸板干燥使其脆性变大;纸面纤维抗张强度 差,爆纸情况发生,可在产生爆纸的刀或线 两侧贴8-10mm宽的硬度较大的海绵,用于局 部压扁纸板,减小模切中的纸面拉伸,此外 可在纸板爆裂处泼水加湿处理,便会降低纸 板物理性能,不宜大量、经常使用
模切生产中的质量控制
质量问题
产生原因
解决办法
1)模切刀刃口不锋利,模切钢刀质量差,模切钢刀规格选择 排除方法是根据模切纸板的不 不合理 不同规格的优质模切刀,提高
2)模切刀刃口磨损严重或模切刀变形,
经常检查模切刀的使用情况, 要及时更换模切刀
1、模切刃口纸毛和纸尘
3)模切刀与海绵的选择或安装不规范,
因为海绵胶条应有足够的硬度 张,让模切刀顺利地将纸张切 的纸板选用不财硬度的海绵胶 的安装位置离模切刀身1-2mm 距离太小,如果距离太小,模 绵胶条的受压后,只能向背离 胀,此时纸张还未完全被模切 海绵拉断,这样会产生起毛及 整个模切版上,海绵胶的数量 度,应在各个位置进行均衡的
1)模切刀不够锋利,
3)模切压力过小
适当增大模切压力
4、纸板局部压线爆线
爆线是指模切后的纸板表面纸层开裂,产生的原因:压痕线 型号选择不正确,压痕底模选择不正确,模切压力过大,
适当调整模切压力大小,纸板 纸板干燥使其脆性变大;纸面 差,爆纸情况发生,可在产生 两侧贴8-10mm宽的硬度较大的 部压扁纸板,减小模切中的纸 可在纸板爆裂处泼水加湿处理 板物理性能,不宜大量、经常
可根据模切刀分布选择硬度适中的海绵,密 适度的分布黏贴
改用质量好的模切刀
2、纸板边缘闭口
2)纸板含水率过高,超过13%时,会导致纸板物理性能及加 工性的全面下降,纸板抗压性能降低,纸板边缘瓦楞被压 溃,挺度差,受压后不易恢复形变。
可将纸板进行抽湿处理再进行
1)压痕线型号选择不正确,
按纸板厚度合理选择压痕线型
3、压痕不清晰 2)压痕底模选择不正确
按纸板厚度和压痕线宽度合 型号
5、模切后纸板黏在模切版上
引起纸板黏贴在模切版上的原因是模切刀两侧海绵数量不 足,海绵弹性导致海绵回弹力不足
可根据模切刀分布选择硬度适 适度的分布黏贴
解决办法
排除方法是根据模切纸板的不同材质,选用 不同规格的优质模切刀,提高其模切适应性
经常检查模切刀的使用情况,磨损或变形后 要及时更换模切刀 因为海绵胶条应有足够的硬度才可以压紧纸 张,让模切刀顺利地将纸张切开,不同材质 的纸板选用不财硬度的海绵胶条,海绵胶条 的安装位置离模切刀身1-2mm的距离,不能 距离太小,如果距离太小,模切刀两边的海 绵胶条的受压后,只能向背离模切刀一方膨 胀,此时纸张还未完全被模切刀切开,而被 海绵拉断,这样会产生起毛及纸尘。另外在 整个模切版上,海绵胶的数量,硬度和高 度,应在各个位置进行均衡的分布