切削液常识
切削液基础知识
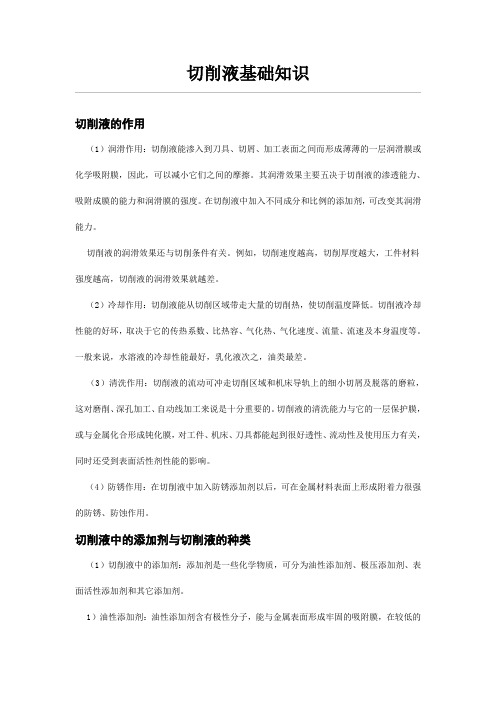
切削液基础知识切削液的作用(1)润滑作用:切削液能渗入到刀具、切屑、加工表面之间而形成薄薄的一层润滑膜或化学吸附膜,因此,可以减小它们之间的摩擦。
其润滑效果主要五决于切削液的渗透能力、吸附成膜的能力和润滑膜的强度。
在切削液中加入不同成分和比例的添加剂,可改变其润滑能力。
切削液的润滑效果还与切削条件有关。
例如,切削速度越高,切削厚度越大,工件材料强度越高,切削液的润滑效果就越差。
(2)冷却作用:切削液能从切削区域带走大量的切削热,使切削温度降低。
切削液冷却性能的好坏,取决于它的传热系数、比热容、气化热、气化速度、流量、流速及本身温度等。
一般来说,水溶液的冷却性能最好,乳化液次之,油类最差。
(3)清洗作用:切削液的流动可冲走切削区域和机床导轨上的细小切屑及脱落的磨粒,这对磨削、深孔加工、自动线加工来说是十分重要的。
切削液的清洗能力与它的一层保护膜,或与金属化合形成钝化膜,对工件、机床、刀具都能起到很好透性、流动性及使用压力有关,同时还受到表面活性剂性能的影响。
(4)防锈作用:在切削液中加入防锈添加剂以后,可在金属材料表面上形成附着力很强的防锈、防蚀作用。
切削液中的添加剂与切削液的种类(1)切削液中的添加剂:添加剂是一些化学物质,可分为油性添加剂、极压添加剂、表面活性添加剂和其它添加剂。
1)油性添加剂:油性添加剂含有极性分子,能与金属表面形成牢固的吸附膜,在较低的切削速度下能起到较好的润滑作用。
油性添加剂有动物油、植物油、脂肪酸、胺类、醇类、脂类等。
2)极压添加剂:极压添加剂是含有硫、磷、氯、碘等的有机化合物,他们在高温下与金属表面起化学反映,形成能耐较高温度和压力的化学润滑膜。
此润滑膜能承受很高的压强,能防止金属界面直接接触,降低摩擦因数,保持良好的切削润滑条件。
3)表面活性剂:表面活性剂即乳化剂,具有乳化作用和油性添加剂的润滑作用。
前者使矿物油和水混合乳化,形成乳化液;后者吸附在金属表面上形成润滑膜。
切削液基本资料.doc

切削液基础知识1、切削液历史介绍切削液是金属切削加工的重要配套材料。
人类使用切削液的历史可以追溯到远古时代。
人们在磨制石器、铜器和铁器时,就知道浇水可以提高效率和质量。
在古罗马时代,车削活塞泵的铸件时就使用橄榄油,16世纪使用牛脂和水溶剂来抛光金属盔甲。
从1775年英国的约翰?威尔金森(J.wilkinson)为了加工瓦特蒸汽机的汽缸而研制成功镗床开始,伴随出现了水和油在金属切削加工中的应用。
到1860年经历了漫长发展后,车、铣、刨、磨、齿轮加工和螺纹加工等各种机床相继出现,也标志着切削液开始较大规模的应用。
19世纪80年代,美国科学家就已首先进行了切削液的评价工作。
Taylor发现并阐明了使用泵供给碳酸钠水溶液可使切削速度提高对30%~40%的现象和机理。
针对当时使用的刀具材料是碳素工具钢,切削液的主要作用是冷却,故提出“冷却剂”一词。
从那时起,人们把切削液称为冷却润滑液。
随着人们对切削液认识水平的不断提高以及实践经验的不断丰富,发现在切削区域中注入油剂能获得良好的加工表面。
最早,人们采用动植物油来作为切削液,但动植物油易变质,使用周期短。
20世纪初,人们开始从原油中提炼润滑油,并发明了各种性能优异的润滑添加剂。
在第一次世界大战之后,开始研究和使用矿物油和动植物油合成的复合油。
1924年,含硫、氯的切削油获得专利并应用于重切削、拉削、螺纹和齿轮加工。
刀具材料的发展推动了切削液的发展,1898年发明了高速钢,切削速度较前提高2~4倍。
1927年德国首先研制出硬质合金,切削速度比高速钢又提高2~5倍。
随着切削温度的不断提高,油基切削液的冷却性能已不能完全满足切削要求,这时人们又开始重新重视水基切削液的优点。
1915年生产出水包油型乳化液,并于1920年成为优先选用的切削液用于重切削。
1948年在美国研制出第一种无油合成切削液,并在20世纪70年代由于油价冲击而使应用提高。
近十几年来, 由于切削技术的不断提高,先进切削机床的不断涌现,刀具和工件材料的发展,推动了切削液技术的发展。
切削液基本知识

切削液不得不知的基本知识金属加工液金属及其合金在切削、成形、处理和保护等过程忠使用的工艺润滑油统称为金属加工液,又名切削液。
在金属加工过程中,为了降低切削时的切削力,及时带走切削区内产生的热量以降低切削温度,提高刀具耐用度,从而提高生产效率,改善工件表面粗糙度,保证工件加工精度,达到最佳的经济效果,通常使用金属加工液。
金属加工液在金属加工过程中具有润滑、冷却、清洗、防锈等作用;其中核心作用是:一方面通过冷却作用降低加工过程中的变形热,另一方面通过润滑作用来减少金属加工过程中的磨擦热,从而来提高金属加工质量,延长刀具的使用寿命等。
1、冷却性能:冷却作用是通过乳化液和因切削而发热的刀具、切屑和工件间的对流和汽化作用把切屑热从固体(刀具、工件)处带走,从而有效地降低切削温度,减少工件和刀具的热变形,保持刀具硬度提高加工精度和刀具耐用度。
2、润滑性能:润滑作用就是其减少前刀面与切屑、后刀面与已加工表面间的摩擦形成部分润滑膜的作用,以防止刀具与切屑或工件间的粘着,所以良好的润滑可以减少功能消耗、刀具磨损和良好的表面光洁度。
3、清洗性能:在金属加工过程中,切屑、铁粉、磨屑、油污、沙粒等常常粘附在工件、刀具或砂轮表面及缝隙中,同时沾污机床和工件,不易清洗,使刀具或砂轮切屑刃口变钝,影响切削效果。
所以要求乳化液有良好的清洗作用。
乳化液的清洗性能就是指乳化液防止这些细颗粒粘结和利用液流的机械冲洗作用将其冲走的能力。
4、防锈性能:在金属加工过程中,工件要与环境介质如水、氧、硫、二氧化硫、二氧化碳、硫化氢、氯离子、游离酸碱和乳化液分解或氧化变质所产生的油泥等腐蚀性介质接触而受到腐蚀,机床部件与乳化液接触的部分会产生腐蚀。
因此要求乳化液有一定的防锈能力。
金属加工液除了应具有良好的冷却性、润滑性、清洗性、防锈性外,还应具有防腐蚀性、抗菌性、防垢性、抗泡性、热稳定性、无毒、无害、无刺激性气味、不污染环境、使用方便等条件。
金属加工液可分为纯油性切削液和水溶性切削液两种。
切削液不得不知的基本知识

切削液不得不知的基本知识金属加工液在金属加工过程中,为了降低切削时的切削力,及时带走切削区内产生的热量以降低切削温度,提高刀具耐用度,从而提高生产效率,改善工件表面粗糙度,保证工件加工精度,达到最佳的经济效果,通常使用金属加工液。
金属加工液在金属加工过程中具有润滑、冷却、清洗、防锈等作用;其中核心作用是:一方面通过冷却作用降低加工过程中的变形热,另一方面通过润滑作用来减少金属加工过程中的磨擦热,从而来提高金属加工质量,延长刀具的使用寿命等。
1、冷却性能:冷却作用是通过乳化液和因切削而发热的刀具、切屑和工件间的对流和汽化作用把切屑热从固体(刀具、工件)处带走,从而有效地降低切削温度,减少工件和刀具的热变形,保持刀具硬度提高加工精度和刀具耐用度。
2、润滑性能:润滑作用就是其减少前刀面与切屑、后刀面与已加工表面间的摩擦形成部分润滑膜的作用,以防止刀具与切屑或工件间的粘着,所以良好的润滑可以减少功能消耗、刀具磨损和良好的表面光洁度。
3、清洗性能:在金属加工过程中,切屑、铁粉、磨屑、油污、沙粒等常常粘附在工件、刀具或砂轮表面及缝隙中,同时沾污机床和工件,不易清洗,使刀具或砂轮切屑刃口变钝,影响切削效果。
所以要求乳化液有良好的清洗作用。
乳化液的清洗性能就是指乳化液防止这些细颗粒粘结和利用液流的机械冲洗作用将其冲走的能力。
4、防锈性能:在金属加工过程中,工件要与环境介质如水、氧、硫、二氧化硫、二氧化碳、硫化氢、氯离子、游离酸碱和乳化液分解或氧化变质所产生的油泥等腐蚀性介质接触而受到腐蚀,机床部件与乳化液接触的部分会产生腐蚀。
因此要求乳化液有一定的防锈能力。
金属加工液除了应具有良好的冷却性、润滑性、清洗性、防锈性外,还应具有防腐蚀性、抗菌性、防垢性、抗泡性、热稳定性、无毒、无害、无刺激性气味、不污染环境、使用方便等条件。
金属加工液可分为纯油性切削液和水溶性切削液两种。
金属加工液应具有如下作用:1、改善加工表面,提高表面光洁度;2、提高加工件尺寸的精密度;3、延长切削工具的寿命;4、随时排除切削屑末,洗净加工面;5、防止加工件腐蚀或生锈;6、提高切削加工效率;7、随时冷却加工件表面和加工刀具。
切削液培训资料

切削液的选用
-磨削加工
➢ 磨削:磨削区域温度较高(800~1000℃),易引起工 作表面局部烧伤;磨削热应力易使工件变形,产生 裂纹;影响表面质量。
➢ 选用要求:良好冷却性和润滑性,一定清洗性和防 锈性。
对应于
➢ 一般磨削-3%~5%合成乳化液 ➢ 精磨削-H-1精磨液 或 5%~10%乳化液 ➢ 超精磨-98%煤油与2%石油磺酸钡混合液 或 含氯极压
切削油 ➢ 难加工材料-极压乳化液 或 极压切削油 ➢ 磨齿磨螺纹-低黏度矿物油 或 极压切削油
切削液选用参考
结束
精加工 铜及合金和铝及合金- 10%~20%乳化 液 或 煤油 或 50%煤油及L-AN10
精加工 铸铁-7%~10%乳化液 或 煤油
切削液的选用
-半封闭加工
半封闭加工如:深孔钻、拉削、攻内螺纹等
刀具半封闭下工作,排屑困难,切削热无法 传出,易烧损刀刃,工件加工表面粗糙。
选用要求:良好的润滑性,一定的冷却性和 清洁性
少切削力、延长刀具寿命、获得较 小加工表面粗糙度
切削液的种类
-水溶性切削液
2.乳化液
➢ 组成:水+乳化油 搅拌 乳白色液体 ➢ 低浓度时以冷却为主,用于粗加工和普
通磨削加工
➢ 高浓度时以润滑为主,用于精加工和复 杂刀具加工
➢ 细分为:防锈、清洗、极压和透明乳化 液4种
切削液的种类
-水溶性切削液
3.水溶液
高温润滑性,较高化学稳定性 涂抹法涂于刀具表面 有效抑制积屑瘤、减小切削力、延长刀
具寿命、减小加工表面粗糙度
切削液添加剂
1.油性添加剂——使金属加工处于边界润滑状态。 用于低速精加工
切削液常识

切削液常识1. 切削液的作用2. 切削液的分类3. 切削液的选用4. 切削液的使用方法5. 切削液的维护与管理6. 切削液的废液处理一.切削液的作用在金属切削过程中,为提高切削效率,提高工件的精度和降低工件表面粗糙度,延长刀具使用寿命,达到最佳的经济效果,就必须减少刀具与工件、刀具与切屑之间磨擦,及时带走切削区内因材料变形而产生的热量。
要达到这些目的,一方面是通过开发高硬度耐高温的刀具材料和改进刀具的几何形状,如随着碳素钢、高速钢硬质合金及陶瓷等刀具材料的相继问世以及使用转位刀具等,使金属切削的加工率得到迅速提高;另一方面采用性能优良的切(磨)削液往往可以明显提高切削效率,降低工件表面粗糙度,延长刀具使用寿命,取得良好和经济效益切削液作用有如下几方面:1.冷却作用冷却作用是依靠切削液的对流换热和汽化把切削热从固体(刀具、工件和切屑)带走,降低切削区的温度,减少工件变形,保持刀具硬度和尺寸。
切削液的冷却作用取决于它的热参数值,特别是比热容和热导率。
此外,液体的流动条件和热交换系数也起重要作用,热交换系数可以通过改变表面活性材料和汽化热大小来提高。
水具有较高的比热容和大的导热率,所以水基的切削性能要比油基切削液好。
改变液体的流动条件,如提高流速和加大流量可以有效地提高切削液的冷却效果,特别对于对于冷却效果差的油基切削液,加大切削液的供液压力和加大流量,可有较提高冷却性能。
在枪钻深孔和高速滚齿加工中就采用这个办法。
采用喷雾冷却,使液体易于汽化,也可明显提高冷却效果。
切削液的冷却效果受切削液的渗透性能所影响,渗透性能好的切削液,对刀刃的冷却速度快,切削液的渗透性能与切削液的粘度和浸润性有关。
低粘度液体比高粘度液体渗透性能要好,油基切削液的渗透性能比水基切削液渗透性能要强,含有表面活性剂的水基切削液其渗透性能则大大有所提高。
切削液的浸润性能与切削液的表面张力有关,当液体表面张力大时,液体在固体的表面向周围扩张聚集成液滴,这种液体的渗透性能就差;当液体表面张力小时,液体在固体表面向周围扩展,固体-液体-气体的接触角很小,甚至为零,此时液体的渗透性能就好,液体能迅速扩展到刀具与工件,刀具与切屑接触的缝隙中,便可加强冷却效果。
切削液的使用方法和注意事项
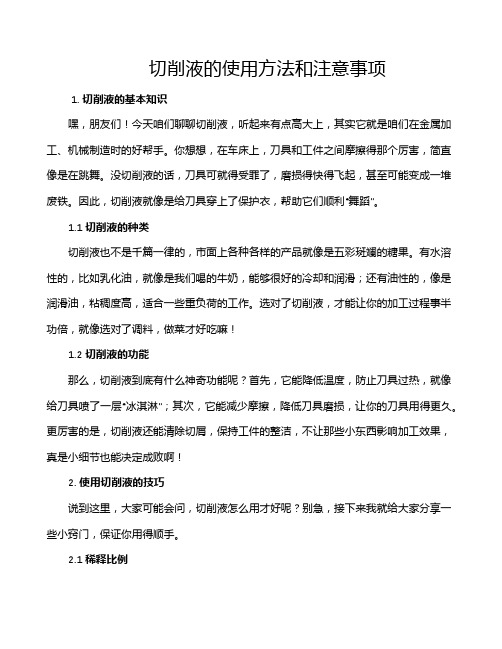
切削液的使用方法和注意事项1. 切削液的基本知识嘿,朋友们!今天咱们聊聊切削液,听起来有点高大上,其实它就是咱们在金属加工、机械制造时的好帮手。
你想想,在车床上,刀具和工件之间摩擦得那个厉害,简直像是在跳舞。
没切削液的话,刀具可就得受罪了,磨损得快得飞起,甚至可能变成一堆废铁。
因此,切削液就像是给刀具穿上了保护衣,帮助它们顺利“舞蹈”。
1.1 切削液的种类切削液也不是千篇一律的,市面上各种各样的产品就像是五彩斑斓的糖果。
有水溶性的,比如乳化油,就像是我们喝的牛奶,能够很好的冷却和润滑;还有油性的,像是润滑油,粘稠度高,适合一些重负荷的工作。
选对了切削液,才能让你的加工过程事半功倍,就像选对了调料,做菜才好吃嘛!1.2 切削液的功能那么,切削液到底有什么神奇功能呢?首先,它能降低温度,防止刀具过热,就像给刀具喷了一层“冰淇淋”;其次,它能减少摩擦,降低刀具磨损,让你的刀具用得更久。
更厉害的是,切削液还能清除切屑,保持工件的整洁,不让那些小东西影响加工效果,真是小细节也能决定成败啊!2. 使用切削液的技巧说到这里,大家可能会问,切削液怎么用才好呢?别急,接下来我就给大家分享一些小窍门,保证你用得顺手。
2.1 稀释比例首先,稀释比例可得注意。
有些朋友觉得,切削液越浓越好,其实不然。
就像喝酒,酒精浓度太高可不好,切削液也需要根据使用说明书来调整稀释比例,通常是1:5到1:10。
稀释得当,才能充分发挥它的作用,让你刀具的表现如虎添翼,事半功倍。
2.2 液体更换再来就是切削液的更换,别以为用了一次就能一劳永逸。
切削液在使用过程中会被杂质污染,逐渐失去效果。
建议每隔一段时间就检查一下,如果发黑、发臭,那就果断换掉吧!保持切削液的清洁,就像保持厨房的整洁,才能做出美味佳肴。
3. 注意事项最后,咱们来说说使用切削液的一些注意事项,这可是非常重要的哦!3.1 安全防护首先,安全第一,永远记住这一点。
切削液有时候可能含有一些化学成分,对皮肤和眼睛有刺激。
切削液基础知识

切削液基础知识切削液是一种用在金属切、削、磨加工过程中,用来冷却和润滑刀具和加工件的工业用液体切削液是金属切削加工的重要配套材料。
18世纪中后期以来,切削液在各种金属加工领域中得到了广泛的应用。
20世纪初,人们从原油中提炼出大量润滑油,发明了各种润滑油添加剂,真正拉开了现代切削液技术的历史序幕。
一、切削液的组成及性能特点切削液的品种繁多,作用各异,分为油基切削液和水基切削液两大类。
油基切削液也叫切削油,它主要用于低速重切削加工和难加工材料的切削加工。
水基切削液分为3大类乳化切削液、微乳化切削液和合成切削液。
二、切削液的作用使用切削液的主要目的是为减少切削能耗,及时带走切削区内产生的热量以降低切削温度、减少刀具与工件间的摩擦和磨损、提高刀具使用寿命,保证工件加工精度和表面质量,提高加工效率,达到最佳经济效果。
切削液在加工过程中的这些效果主要来源于其润滑作用、冷却作用、清洗作用和防锈作用。
此外,因为切削液是油脂化学制品,直接与操作人员、工件和机床相接触,对其安全性和腐蚀性也必须有一定的要求。
三、切削液的发展趋势众所周知,切削液具有润滑、冷却、清洗及防锈等作用,对提高切削加工质量和效率、减少刀具磨损等均有显著效果。
近十多年来,我国的切削液技术发展很快,切削液新品种不断出现,性能也不断改进和完善,特别是20世纪70年代末生产的水基合成切削液和近几年发展起来的半合成切削液(微乳化切削液)在生产中的推广和应用,为机械加工向节能、减少环境污染、降低工业生产成本方向发展开辟了新路径。
四、切削液的选用切削液都是按照油基切削液和水基切削液来选用的。
总体上看,在加工质量和刀具寿命方面,油基切削液比水基切削液要优越,尽管随被加工材料、加工方法、加工条件的不同其优劣程度会有所差异。
所以,水基切削液应该用于存在着比加工质量和刀具寿命更优先的场合。
五、其他切削液1)膏状及固体润滑剂在攻螺纹时,常在刀具或工件上涂上一些膏状或固体润滑剂。
- 1、下载文档前请自行甄别文档内容的完整性,平台不提供额外的编辑、内容补充、找答案等附加服务。
- 2、"仅部分预览"的文档,不可在线预览部分如存在完整性等问题,可反馈申请退款(可完整预览的文档不适用该条件!)。
- 3、如文档侵犯您的权益,请联系客服反馈,我们会尽快为您处理(人工客服工作时间:9:00-18:30)。
切削液的作用在金属切削过程中,为提高切削效率,提高工件的精度和降低工件表面粗糙度,延长刀具使用寿命,达到最佳的经济效果,就必须减少刀具与工件、刀具与切屑之间磨擦,及时带走切削区内因材料变形而产生的热量。
要达到这些目的,一方面是通过开发高硬度耐高温的刀具材料和改进刀具的几何形状,如随着碳素钢、高速钢硬质合金及陶瓷等刀具材料的相继问世以及使用转位刀具等,使金属切削的加工率得到迅速提高;另一方面采用性能优良的切(磨)削液往往可以明显提高切削效率,降低工件表面粗糙度,延长刀具使用寿命,取得良好的经济效益。
切削液作用有如下几方面:1.冷却作用冷却作用是依靠切削液的对流换热和汽化把切削热从固体(刀具、工件和切屑)带走,降低切削区的温度,减少工件变形,保持刀具硬度和尺寸。
切削液的冷却作用取决于它的热参数值,特别是比热容和热导率。
此外,液体的流动条件和热交换系数也起重要作用,热交换系数可以通过改变表面活性材料和汽化热大小来提高。
水具有较高的比热容和大的导热率,所以水基的切削性能要比油基切削液好。
改变液体的流动条件,如提高流速和加大流量可以有效地提高切削液的冷却效果,特别对于对于冷却效果差的油基切削液,加大切削液的供液压力和加大流量,可有效提高冷却性能。
在枪钻深孔和高速滚齿加工中就采用这个办法。
采用喷雾冷却,使液体易于汽化,也可明显提高冷却效果。
切削液的冷却效果受切削液的渗透性能所影响,渗透性能好的切削液,对刀刃的冷却速度快,切削液的渗透性能与切削液的粘度和浸润性有关。
低粘度液体比高粘度液体渗透性能要好,油基切削液的渗透性能比水基切削液渗透性能要强,含有表面活性剂的水基切削液其渗透性能则大大有所提高。
切削液的浸润性能与切削液的表面张力有关,当液体表面张力大时,液体在固体的表面向周围扩张聚集成液滴,这种液体的渗透性能就差;当液体表面张力小时,液体在固体表面向周围扩展,固体-液体-气体的接触角很小,甚至为零,此时液体的渗透性能就好,液体能迅速扩展到刀具与工件,刀具与切屑接触的缝隙中,便可加强冷却效果。
冷却作用的好坏还与泡沫有关,由于泡沫内部是空气,空气的导热性差,泡沫多的切削液冷却效果会降低,所以一般含表面活性剂的合成切削液都加入了少量的乳化硅油,起到消泡作用。
近年的研究表明,离子型水基切削液能通过离子的反应,迅速消除切削和磨削时由于强烈磨擦所产生的静电荷,工件不产生高热,起到良好的冷却效果,这类离子型切削液已广泛用作高速磨削和强力磨削的冷却润滑液。
2.润滑作用在切削加工中,刀具与切削、刀具与工件表面之间产生磨擦,切削液就是减轻这种磨擦的润滑剂。
刀具方面,由于刀具在切削过程中带有后角,它与被加工材料接触部分比前刀面少接触压力也低,因此,后刀面的摩擦润滑状态接近于边界润滑状态,一般使用吸附性强的物质,如油性剂和抗剪强度降低的极压剂,能有效地减少摩擦。
前刀面的状况与后刀面不同,剪切区经变形的切屑在受到刀具推挤的情况下被迫挤出,其接触压力大,切屑也因塑性变形而达到高温,在供给切削液后,切屑也因受到骤冷而收缩,使前刀面上的刀与切屑接触长度及切屑与刀具间的金属接触面积减少,同时还使平均剪切应力降低,这样就导致了剪切角的增大和切削力的减少,从而使工件材料的切削加工性能得到改善。
在磨削过程中,加入磨削液后,磨削液渗入磨粒与工件及磨粒与磨屑之间形成润滑膜,由于这层润滑膜使得这些界面的摩擦减轻,防止磨粒切削刃的摩擦磨损,工件表面粗糙度降低。
切削液的润滑作用,一般油基切削液比水基切削液优越,含油性、极压添加剂的油基切削液效果更好。
油性添加剂一般是带有极压性基等的长链有机化合物,如高级脂肪酸、高级醇、动植物油脂等。
油基添加剂是通过极性基吸附在金属的表面上形成一层润滑膜,减少刀具与工件、刀具与切屑之间的摩擦,从而达到减少切削阻力,延长刀具寿命,降低工件表面粗糙度的目的。
油性添加剂的作用只限于温度较低的状况,当温度超过200℃,油性剂的吸附层受到破坏而失去润滑作用,所以一般低速、精密切削使用含有油性添加剂的切削液,而在高速、重切削的场合,应使用含有极压添加剂的切削液。
所谓极压添加剂是一些含有硫、磷、氯元素的化合物,这些化合物在高温下与金属起化学反应,生成硫化铁、磷化铁、氯化铁等,具有低剪切强度的物质,从而降低了切削阻力,减少了刀具与工件、刀具与切屑的摩擦,使切削过程易于进行。
含有极压添加剂的切削液还可以抑制积屑瘤的生成,改善工件表面粗糙度。
氯化铁的结晶呈层状结构,所以剪切强度最低。
氯化铁与硫化铁相比,其熔点低,在高温下(约400℃)会失去润滑作用。
磷酸铁介于氯化铁和硫化铁之间,硫化铁耐高温性能(700℃)最好,在重负荷切削及难切削材料的加工中一般都使用含有硫极压剂的切削液。
极压添加剂除了和钢、铁等黑色金属起化学反应生成具有低剪切强度的润滑膜外,对铜、铝等有色金属同样有这个作用。
不过有色金属的切削一般不宜用活性极压添加剂,以免对工件造成腐蚀切削液的润滑作用同样与切削液的渗透性有关,渗透性能好的切削液,润滑剂能及时渗入到切屑与刀具界面和刀具与工件界面,在切屑、工件和刀具表面形成润滑膜,降低摩擦系数,减少切削阻力。
切削液除上述的润滑效果外,最近研究认为,切削可以直接渗入到金属表面的微小裂纹中,改变了被加工材料的物理性质,从而降低切削阻力,使切削过程容易进行。
3.清洗作用在金属切削过程中,切屑、铁粉、磨屑、油污等物易粘附在工件表面和刀具、砂轮上,影响切削效果,同时使工件和机床变脏,不易清洗,所以切削液必须有良好的清洗作用。
对于油基切削液,粘度越低,清洗能力越强,特别是含有柴油、煤油等轻组份的切削液,渗透和清洗性能就更好。
含有表面活性剂的水基切削液清洗效果较好,表面活性剂一方面能吸附各种粒子、油泥,并在工件表面形成一层吸附膜,阻止粒子和油泥粘附在工件、刀具和砂轮上,另一方面能渗入到粒子和油污粘附的界面上把粒子和油污从界面上分离,随切削液带走,从而起到清洗作用。
切削液的清洗作用还应表现在对切屑、磨屑、铁粉、油污等有良好的分离和沉降作用。
循环使用的切削液在回流到冷却槽后能迅速使切屑、铁粉、磨屑、微粒等沉降于容器的底部,油污等物悬浮于液面上,这样便可保证切削液反复使用后仍能保持清洁,保证加工质量和延长使用周期。
4.防锈作用在切削加工过程中,工件如果与水和切削液分解或氧化变质所产生的腐蚀介质接触,如与硫、二氧化硫、氯离子、酸、硫化氢、碱等接触就会受到腐蚀,机床与切削液接触的部位也会因此而产生腐蚀,在工件加工后或工序间存放期间,如果切削液没有一定的防锈能力,工件会受到空气中的水分及腐蚀介质的侵蚀而产生化学腐蚀和电化学腐蚀,造成工件生锈,因此,要求切削液必须具有较好的防锈性能,这是切削液最基本的性能之一。
切削油一般都具备一定有防锈能力,如果工序间存放周期不长,可以不加防锈添加剂,因为在切削油中加入石油磺酸钡等防锈添加剂会使切削油的抗磨性能下降。
切削液的分类切削液分为油基切削液和水基切削液两大类1.油基切削液的分类切削液是以矿物油为主要成分,根据加工工艺和加工材料的不同,可以用纯矿物油,也可以加入各类油性添加剂和极压添加剂以提高其润滑效果1)纯矿物油主要采用煤油、柴油等轻质油。
轻质油主要用于铸铁的切削及珩磨、研磨加工,有利于铁粉的沉降。
纯矿物油成本低、稳定性好,对金属不腐蚀,使用周期长。
在使用过程中,即使有少量切削液漏入齿箱、轴承和液压系统中或部分润滑油漏入切削油中,都不致影响机床的使用性能。
但纯矿物油由于不含润滑添加剂,润滑效果较差,承载能力低,一般只适用于轻负荷切削及易切削钢材和有色金属的加工。
对于要求低温流动性能好的切削油,可用聚烯烃等合成油,凝点可达-30℃以下,但价格较贵。
2)脂肪油(或油性添加剂)+矿物油脂肪油曾被广泛用作切削油,一般用于精车丝杠、滚齿、剃齿等精密切削加工,常用的有菜籽油、豆油、猪油等。
脂肪油主要由脂肪酸组成,对金属表面有较强的吸附性能,具有良好的润滑性能,其缺点是易氧化变质,并在机床表面形成难于清洗的粘膜(即“黄袍”)。
脂肪油也可按一定比例(约10%~30%)加入矿物油中,以提高矿物油的润滑效果,但由于脂肪油为食用油,货源少,近年来已逐渐被油性添加剂所替代,其摩擦系数可达到菜籽油的水平,用于精车丝杠、插齿刨齿、拉削等均获得良好效果。
3)非活性极压切削油由矿物油+非活性极压添加剂组成。
所谓非活性极压切削油是指切削油在100℃,3h的腐蚀试验中,铜片腐蚀在2级以下(中等程度均匀变色)。
氯化石蜡、磷酸脂、高温合成的硫化脂肪油等属非活性极压添加剂。
这类切削油的极压润滑性能好,对有色金属不腐蚀,使用方便,被广泛用于多种切削加工。
4)活性极压切削油由矿物油+反应性强的硫系极压添加剂配制而成。
这类切削油对铜片的腐蚀为3~4级,对有色金属有严重腐蚀。
它有良好的抗烧结性能和极压润滑性,可以提高高温条件下刀具使用寿命,对刀具积屑瘤有强的控制能力,多用于容易啃刀的材料和难加工材料的切削。
5)复合切削油由矿物油+油性和极压添加剂配制而成。
油性添加剂,如高级脂肪酸、脂肪油等,这些化合物在表面产生物理吸附和化学吸附,形成一个分子膜吸附层,可降低切削时的摩擦阻力,但这类添加剂只在较低的温度时才有效,当温度高于200℃时,极性化合物产生解吸和分解而失去润滑作用,这时,需要极压添加剂发挥作用,在上面已提到,此处不再重复。
同时,含有油性剂和硫、磷、氯极压添加剂的复合切削油,可以在很宽的范围内保持良好的润滑状态,适合于多工位切削及多种材料的加工。
2.水基切削液的分类1)防锈乳化液由矿物油、乳化剂、防锈剂等组成,矿物油的含量约为50%~80%,在水中形成水包油型乳化液。
与油基切削液相比,乳化液的优点在于冷却效果好,一般稀释为5%~10%的水溶液使用,成本低,使用安全。
乳化液最大的缺点是稳定性差,易受细菌的侵蚀而发臭变质,使用周期短。
2)防锈润滑冷却液这类乳化液含有动植物脂肪或长链脂肪酸(如油酸),具有较好的润滑性。
缺点是这些动植物脂肪或长链不饱和脂肪酸更易受微生物的侵蚀而分解,使用周期很短。
为了延长其实用周期,可在乳化液中加入少量的碳酸钠、硼砂或苯甲酸钠(约为水稀释后乳化液的0.1%~0.3%),可提高乳化液的pH值和增强抗霉菌的能力,延长使用周期.3)极压乳化液这类乳化液含有油溶性的硫、磷、氯型极压添加剂,具有强的极压润滑性,可用于攻丝、拉削、带锯等重切削加工,也用于不锈钢、耐热合金钢等难切削材料的加工。
4)微乳液这类乳化液含油量较少(约10%~30%)含表面活性剂量大,可在水中形成半透明状的微乳液,乳化颗粒在0.1µm以下一般乳化液的颗粒>1µm)。
微乳液的优点是稳定性较乳化液大大提高,使用周期也比乳化液长。