磨削加工运动学及有限元建模与仿真
金属切削加工过程的有限元建模与仿真

江苏大学硕士学位论文金属切削加工过程的有限元建模与仿真姓名:吴勃申请学位级别:硕士专业:计算机科学与应用指导教师:蔡兰200603014.2切屑形成过程的仿真模型的构造大部分国内的切屑形成过程的有限元仿真都采用的是2.D模型‘蚓脚’,2.D有限元模型仅仅适合于萨交切削的仿真,在研究车削、刨削等切削加工时,必须对切削情况进行限定和简化,不仅视觉效果差,更重要的是仿真的范围受到极大的限制,因此,有必要发展3.D有限元模型来仿真切屑形成过程。
本部分主要采用3.D有限元模型仿真在正交切削和制刃切削条件下的切屑形成过程,为进一步对各种切削加工方法进行有效的有限元仿真奠定基础。
4.2.1几何模型的建立与网格划分本章主要研究刀具切入工件丌始到稳态切削这段过程的仿真。
采用三维有限元模型进行模拟,所建立的几何模型如图4.6所示。
网格划分可采用三维六面体网格,也可以采用三维四面体网格。
幽46网格划分图4.2.2材料属性的定义金属材料非线性的本构关系主要分为以下四种类型,即弹塑性、刚塑性、弹粘塑性、刚粘塑性。
有限元模拟的准确性很大程度上取决于本构关系能否真实反映材料的真实特性。
在金属切削有限元仿真中,采用弹塑性材料模型时,既有塑性变形又有弹性变形,较为符合会属切削过程的真实情况。
本课题中,为了保证仿真结果的更接近于实际情况,工件材料选用弹塑性模型,而刀具属性定义为刚性。
为了与实验结果进行比较,工件材利根掘需要选择相应材料。
与实验加工的材料相对应,输入丁F交材料属性(杨氏模量、泊松比、材料密度等),以及JohnsonandCook的经验模型公式中的参数A、B、n、C和m。
江苏人学硕十学何论文4.2.3施加约束与载荷假定工件在切削过程中为无限长。
而在仿真模型中的工件不可能很长,否则计算效率会很低,必须用长、高都不大的工件代替,用必要的约束来模拟真实工件的边界条件。
当研究切屑形成过程中的现象时。
女nX,j应力、应变、应变率和温度进行研究,以及对切屑卷曲现象进行研究时。
磨削强化过程的温度场计算机动态仿真与实验验证
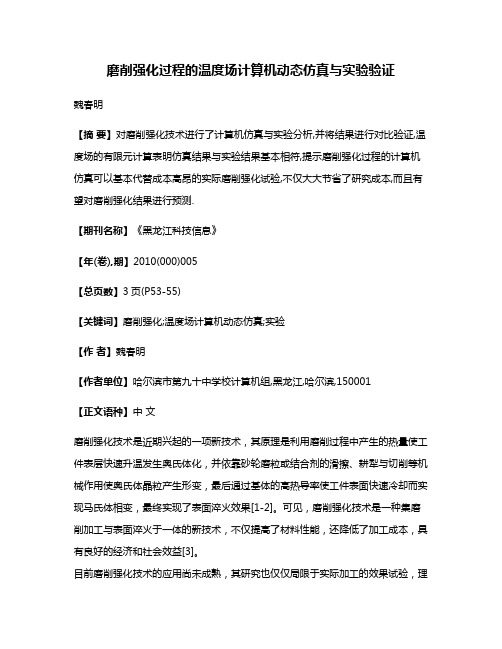
磨削强化过程的温度场计算机动态仿真与实验验证魏春明【摘要】对磨削强化技术进行了计算机仿真与实验分析,并将结果进行对比验证,温度场的有限元计算表明仿真结果与实验结果基本相符,提示磨削强化过程的计算机仿真可以基本代替成本高昂的实际磨削强化试验,不仅大大节省了研究成本,而且有望对磨削强化结果进行预测.【期刊名称】《黑龙江科技信息》【年(卷),期】2010(000)005【总页数】3页(P53-55)【关键词】磨削强化;温度场计算机动态仿真;实验【作者】魏春明【作者单位】哈尔滨市第九十中学校计算机组,黑龙江,哈尔滨,150001【正文语种】中文磨削强化技术是近期兴起的一项新技术,其原理是利用磨削过程中产生的热量使工件表层快速升温发生奥氏体化,并依靠砂轮磨粒或结合剂的滑擦、耕犁与切削等机械作用使奥氏体晶粒产生形变,最后通过基体的高热导率使工件表面快速冷却而实现马氏体相变,最终实现了表面淬火效果[1-2]。
可见,磨削强化技术是一种集磨削加工与表面淬火于一体的新技术,不仅提高了材料性能,还降低了加工成本,具有良好的经济和社会效益[3]。
目前磨削强化技术的应用尚未成熟,其研究也仅仅局限于实际加工的效果试验,理论研究较少,因此磨削强化的试验研究成本较高,而且具有很高的盲目性。
现针对这一缺点,提出并进行了磨削强化过程的计算机动态仿真,从而为试验过程中温度场的研究、强化效果的预测、各项加工参数的合理选择,以及强化过程的理论研究等内容提供了基础。
磨削强化过程中,砂轮与工件表面间的接触面即为热源。
由于砂轮与工件之间存在进给运动,因此该热源可视为沿着工件表面匀速移动;为了使工件表面产生良好的强化效果,该温度场还应当使工件与其接触时,表面迅速升温至Ac3以上并奥氏体化,并在其离开时迅速冷却,以产生足够的马氏体。
因此应当将移动热源和瞬态温度场结合,进行强化过程中工件表面的热分析。
根据传热学理论,三维瞬态温度场中的固体导热微分方程为[4-5]:式中 T——物体的瞬态温度(℃);t——过程进行的时间(s);λ——材料的导热系数;qm——热流密度;ρ——材料密度;cp——材料的定压比热(J/kg·℃)。
切削加工中的有限元模拟

切削加工中的有限元模拟作者:BerendDenkena、Luis De Leon、Maya Otte 来源:德国Werkstatt + Betrieb杂志借助于有限元分析工具(FEM)的灵活性可以全面地描述切削过程;与实验测试相比,有限元分析可以更好地描述难以测量或者原本无法描述的加工过程。
切削过程的建模以及模拟对于降低加工工时和成本至关重要。
模拟作为开发工具可以用于质量管理和质量优化,并尽可能降低生产起步阶段的风险和试制费用。
有限元分析(FEM)是一种数学方法,尤其适用于解决与工程实际相关的问题,并能在更广的范围内传播。
首先将需计算区域划分为若干大小有限的小单元。
在每一个不等于0的有限单元内寻找解决方案。
整个区域的解决方案通常情况下由相当庞大但精巧的、填充好的线性方程式运算得出。
使用有限元模拟可以借助数学方法对切削过程进行重建,同时将整个过程中任意部位和时间点的温度、延展、延展率、应力和受力计算出来。
因此,有限元模拟可以用来支持不同场合下的实验研究(图1)。
图1 切削加工中的有限元分析在刀具开发过程中,诸如刀具磨损和生产效率等的因素将发挥决定性的作用,因为在整个加工过程中生产效率和质量受到影响。
刀具结构的优化可以提高刀具本身的使用寿命和加工质量。
为了获得比较优化的刀具几何结构,需要考虑切削过程中的热负荷和机械负荷。
此外需要分析沿刀刃和位于刀具内部的应力和温度。
切削刃接触区域内应力、延展、延展率以及温度的详细信息可以用于分析切屑形成的机制。
工件方面,借助有限元方法可以预测固定工件的边缘区域所受到的影响。
对工件内应力形成机制的研究可以用来控制切削过程并进一步调整特定边缘区域的特性。
图2的实例是直角切入式磨削的建模过程。
第一步,使用有限元软件(本例中采用了“Deform 2D”)按照给出的几何参数将刀具自动划分网格。
工件划分网格后再施加额外的边界条件。
根据工件的弹性-塑性形变计算结果选择合适的材料模型。
【毕业设计】钛合金薄壁结构件磨削加工残余应力有限元仿真 开题报告

【毕业设计】钛合金薄壁结构件磨削加工残余应力有限元仿真开题报告天津职业技术师范大学毕业设计开题报告钛合金薄壁结构件磨削加工残余应力有限元仿真系别:机械工程学院班级:机自0901学生姓名:韩捷指导教师:霍文国2013 年 1 月 7 日毕业设计开题报告综合考虑工件与刀具的材料、加工方法、加工条件等多种因素 ,定量和定性分析残余应力,广泛吸收现代数学、力学理论,并借助计算机找到工程需要的数值解。
因此仿真的应用不论是在技术还是经济层面都具有重要的意义。
综上,对于钛合金磨削加工后残余应力数值模拟的仿真,是进一步提高钛合金产品性能和寿命的有力研究途径。
二、研究内容(一)钛合金材料1、钛合金的性能图1 钛合金图2 钛合金钛的一个显著特点是耐腐蚀性强,这是钛对氧的亲合力特别大,能在其表面生成一层致密的氧化膜,可保护钛不受介质腐蚀。
金属钛在大多数水溶液中,都能在表面生成钝化氧化膜。
因此,钛在酸性、碱性、中性盐水溶液中和氧化性介质中具有很好的稳定性。
钛合金以此特性在化学工业、化肥工业、电力工业、造纸和纺织工业中都有着广泛的应用。
钛是化学工业中优良的抗腐蚀材料;是化肥工业中取代不锈钢材料盛放尿素、胺、胺基胛酸胺等高温高压混合液的新材料;是电力工业中用作为热交换器的冷却管的材料;是海水淡化装置和造船工业的理想材料;是纺织印染工业中漂白设备的重要材料;还是医疗和制药部门用作人造肢体和器官的材料。
钛合金的密度一般在4.5g/cm3左右,仅为钢的60%,纯钛的强度接近普通钢的强度,一些高强度钛合金超过了许多合金结构钢的强度。
因此钛合金的比强度(强度/密度)远大于其他金属结构材料,可制出单位强度高、刚性好、质轻的零、部件。
在飞机的发动机构件、骨架、蒙皮、紧固件及起落架等都使用钛合金。
使用温度比铝合金高几百度,在中等温度下仍能保持所要求的强度,可在450-500℃的温度下长期工作这两类钛合金在150℃-500℃范围内仍有很高的比强度,而铝合金在150℃时比强度明显下降。
【毕业设计】钛合金薄壁结构件磨削加工残余应力有限元仿真开题报告

【毕业设计】钛合金薄壁结构件磨削加工残余应力有限元仿真开题报告天津职业技术师范大学毕业设计开题报告钛合金薄壁结构件磨削加工残余应力有限元仿真2013年1月 7日毕业设计开题报告一、研究目的、意义综合考虑工件与刀具的材料、加工方法、加工条件等多种因素,定量和定性分析残余应力,广泛吸收现代数学、力学理论,并借助计算机找到工程需要的数值解。
因此仿真的应用不论是在技术还是经济层面都具有重要的意义。
综上,对于钛合金磨削加工后残余应力数值模拟的仿真,是进一步提高钛合金产品性能和寿命的有力研究途径。
二、研究内容(一)钛合金材料1、钛合金的性能钛的一个显著特点是耐腐蚀性强,这是钛对氧的亲合力特别大,能在其表面生成一层致密的氧化膜,可保护钛不受介质腐蚀。
金属钛在大多数水溶液中,都能在表面生成钝化氧化膜。
因此,钛在酸性、碱性、中性盐水溶液中和氧化性介质中具有很好的稳定性。
钛合金以此特性在化学工业、化肥工业、电力工业、造纸和纺织工业中都有着广泛的应用。
钛是化学工业中优良的抗腐蚀材料;是化肥工业中取代不锈钢材料盛放尿素、胺、胺基胛酸胺等高温高压混合液的新材料;是电力工业中用作为热交换器的冷却管的材料;是海水淡化装置和造船工业的理想材料;是纺织印染工业中漂白设备的重要材料;还是医疗和制药部门用作人造肢体和器官的材料。
钛合金的密度一般在4. 5g/cm3左右,仅为钢的60%,纯钛的强度接近普通钢的强度,一些高强度钛合金超过了许多合金结构钢的强度。
因此钛合金的比强度(强度/密度)远大于其他金属结构材料,可制出单位强度高、刚性好、质轻的零、部件。
在飞机的发动机构件、骨架、蒙皮、紧固件及起落架等都使用钛合金。
使用温度比铝合金高几百度,在中等温度下仍能保持所要求的强度,可在450-500 *C的温度下长期工作这两类钛合金在150・C-500・C范围内仍有很高的比强度,而铝合金在1509时比强度明显下降。
钛合金的工作温度可达5009,铝合金则在200°C以下。
仿真技术及其在磨削加工中的应用

模型可以分为物理模型和数学模型 。物理模型又 称为实体模型 ,它是实际系统在尺寸上缩小或放大后 的相似体 。数学模型是用数学方程来描述实际系统的 结构和性能的模型[1] 。数学模型建模包括经验公式 法 、基本定律法和非线性隐式法三大类 。
输入磨削类型 、工件属性 、磨削砂轮规格和加工参数 ,
来预报各磨削特性 ,如力 、功率 、挠度 、温度 、比能 、粗糙
度和椭圆度等 。校准过程中 ,系统首先比较在初磨阶
段的最初过渡期间测量和预报的功率来估计系统刚度 。
表 1 用 GRINDSIM 优化仿真的磨削时间比较
粗磨
精磨
光磨
I
进给率 mmΠsp 时间 s
随后用初磨阶段稳定期间内的平均功率来校准初始砂 轮磨损的平面模型 。在优化阶段 ,一般的优化目标是 最小化周期时间 。
表一是运用 GRINDSIM 优化仿真的一个时间比 较 。I 是普通的磨削加工参数 ,加工一个零件共需要 31. 9 秒 。在同样的加工条件下 ,用软件以最小化周期 时间为目标进行优化仿真 ,II 服从无烧伤约束 ,加工时 间减小到了 23. 1 秒 ,此时磨削弧区达到了烧伤极限 。 III 是允许在粗磨阶段烧伤 ,在随后的精磨阶段去除烧 伤的热损伤材料 ,可以进一步减少磨削时间到 15. 5 秒 ,而且用此软件的热模型还可以计算出粗磨时的热 损伤深度[16] 。
“仿真”一词的确切含义目前仍有争议 ,简单地说 , 仿真是建立相应物理系统的数学模型在计算机上解算 的过程[14] 。由于数字计算机执行的对象只能是离散 (数字) 形式的 ,所以仿真技术的最大特征是在模型中 使用时间离散值 。这样 ,仿真对象的任何时刻的运行 状态都可以用仿真软件来清楚地描述[7] 。 2. 5 建模与仿真的关系
薄板零件磨削变形有限元仿真

薄板零件磨削变形有限元仿真作者:朱传敏胡骁来源:《物联网技术》2019年第03期摘要:航空航天设备中常用到一些高精度薄板零件,如各类密封圈和垫片,这类零件对表面质量和形状精度有极高的要求。
磨削常被作为薄板类零件的最终加工工序,磨削加工引起的零件变形会直接影响零件表面的形状精度与使用性能。
目前对薄板零件磨削变形的研究多针对如何抑制与补偿,对薄板零件磨削变形的机理研究尚存不足。
文中借助Abaqus软件建立薄板零件平面磨削有限元模型,计算磨削造成的温度场和应力场,经过与中厚板的仿真结果比较分析,探讨了薄板零件磨削变形的机理。
关键词:薄板零件;磨削加工;有限元仿真;航空航天;Abaqus;ANSYS仿真中图分类号:TG582 文献标识码:A 文章编号:2095-1302(2019)03-00-030 引言薄板零件常用于航空航天设备中,需要极高加工精度,相比于大厚度零件的磨削加工,在磨削过程中,薄板零件散热条件差,磨削热本身会引起厚度方向的不均匀膨胀,造成磨削深度的变化。
磨削温度同时会提高材料塑性性能,在磨削力作用下材料更易发生塑性形变,磨削过程中的热力耦合是导致薄板零件磨削变形的原因,而热力耦合作用的机理十分复杂,目前的研究尚存不足。
基于Malkin磨削能量分配比例相关研究成果[1],部分学者将磨削热等效为传入工件热流密度,在ANSYS仿真软件中加载移动热流密度,较为准确地仿真了磨削中瞬态温度场[2-3]。
Junming[4-5]等学者运用单砥砺切削模型计算单个磨粒在切削过程中的力和热,并基于砥砺分布模型建立了较为准确的磨削热力耦合模型,用来预测磨削力与磨削温度。
以上研究中,ANSYS进行移动热源加载略过了磨削热的产生机理,而单砥砺切削模型无法反映砂轮的实际磨削过程与多砥砺的交互作用效果,无法解释磨削变形。
本文借助Abaqus软件建立薄板零件平面磨削有限元模型,计算磨削造成的温度场和应力场,经过与中厚板的仿真结果比较分析,探讨了薄板零件磨削变形的机理。
工程陶瓷高效深磨温度场的有限元仿真

工程陶瓷高效深磨温度场的有限元仿真
Vol. 21 No. 2 Jun. 2009
郭 力 1,2, 何利民 1,2
(1. 湖南大学 国家高效磨削工程技术研究中心, 湖南 长沙, 410082; 2. 湖南大学 机械与运载工程学院, 湖南 长沙, 410082)
摘 要:在磨削温度实验的基础上, 运用有限元法对工程陶 瓷氧化铝及部分稳定氧化锆进行了高效深磨磨削温度场的
传入工件的 热分配比:%
10/17/21 0.8/0.6/10 0.8/0.3/1.8/13 28.6/31/39.2 2.1/15.1/8.7 15.1/13.1/4.1/2.4
第2期
郭 力, 何利民 工程陶瓷高效深磨温度场的有限元仿真
59
2.2 工程陶瓷磨削条件 结合实验环境, 本文的磨削温度场仿真加载如
图 3 热分析体单元 SOLID70
图 4 表面热效应单元 SURF152
3 结果分析
图 5、图 6 描述了在已加工工件表面及工件表 层下,Al2O3 及 ZrO2 两种工程陶瓷在砂轮速度为 120 m/s,工件速度为 40 mm/s,磨深为 0.5 mm,湿磨及 干磨两种状态下的温度场分布等值线和变化趋势.
图 2 所示, 在磨削表面加载三角形热源, 热流加载 在磨削弧长上, 冷却液及周围空气的对流加载如图 2 所示,其他面为环境温度. 为节省计算时间且达到 一定的计算精度,在越接近磨削表面处网格划分越 密. 因有限元分析软件 ANSYS[9]中不能对同一单元 同时加载热流及对流载荷,故在如图三个加载对流 的表面生成表面热单元,在表面单元上加载空气或 冷却液对流载荷. 在体单元上加载热流密度,加载 方式采用逐步移动法,热源移动速度为工件速度 vw .
- 1、下载文档前请自行甄别文档内容的完整性,平台不提供额外的编辑、内容补充、找答案等附加服务。
- 2、"仅部分预览"的文档,不可在线预览部分如存在完整性等问题,可反馈申请退款(可完整预览的文档不适用该条件!)。
- 3、如文档侵犯您的权益,请联系客服反馈,我们会尽快为您处理(人工客服工作时间:9:00-18:30)。
磨削加工运动学及有限元建模与仿真韩振鲁 李长河(青岛理工大学 山东青岛 266033)摘 要 介绍了建立磨削加工运动学模型的基本方法,讨论了对砂轮表面形貌的模拟,多种运动几何模型的比较以及应用运动学经验模型解析公式。
详细介绍了有限元分析的基础,在磨削加工中利用有限元分析的理论,所开发的有限元仿真自主软件,能够自动产生完全的模拟仿真过程。
研究表明,建模仿真对于研究磨削过程是非常适合的方法。
有限元仿真方法可以让使用者对于加工过程有更好的理解,并可以帮助分析复杂的试验结果。
经过计算机程序中的误差处理后,加工工件就能达到较高的精度,同时降低了制造成本。
关键词运动学模型 表面形貌 模拟仿真 有限元分析1 运动学模型自从建立第一个磨削过程的运动模型,迄今已有45年了。
尽管从那时到现在所有的方法都用来开发建模,包含对砂轮、工件和磨削运动学的描述,但是各种模型间仍具有显著的差异。
20世纪60年代和20世纪70年代早期的磨削运动学模型奠定了二维磨削理论的基础,在1980年后,当计算机运算速度大大提高后,人们建立了更加复杂的模型,这些方法中最典型的是对磨削过程采用三维立体的观点,主要是基于工件表面和砂轮表面的在几何学上的互相渗透的经验运动模型。
该模型中,磨削过程的输出参数可以通过解析和经验公式计算出来。
1.1 砂轮表面形貌的模拟在讨论磨削加工的所有模型中,对砂轮表面形貌的模拟是必不可少的一部分。
现在有两种方法来对砂轮表面形貌进行定量描述:一是直接对砂轮表面进行扫描,二是运用统计学的方法对砂轮表面进行分析来合成砂轮表面形貌。
Inasaki在他的磨削过程模拟中,提出了一个直接得到砂轮表面形貌的方法。
他得到了绕砂轮一周的表面形貌数据,并将这些数据储存在微机以供日后模拟使用。
通过已扫描的表面来分析砂轮的特性进而导出砂轮的表面形貌的一般数据信息。
利用这些统计的砂轮表面形貌数据,例如磨粒大小的平均值和分布、磨粒分布的方向以及磨粒突出表面的高度等等,综合这些参数就有可能得到比较合理的砂轮表面形貌数据。
磨粒的形状常常看作是简单的球体或者锥体,或者是一些修正后的基本几何形状(如八面体、长方体和四面体)。
在这些模型中通常使用随机数来分配砂轮表面的磨粒个数。
1.2 运动模拟的基本方法在磨削过程的运动学建模仿真领域,第一个仿形法是由Yoshikawa、Kassen和Law提出来的。
基本上,这些方法都是利用二维的磨粒模型,通过计算切屑厚度和工件表面粗糙度或者横截面的地貌来描述平面磨削或外圆磨削过程。
磨削过程模拟的前提仅是砂轮和工件的理想运动,也就是说砂轮的偏向挠曲和工件的塑性变形都被忽略了。
事实上,磨粒和工件接触作用产生的新的表面轮廓可以通过矩阵公式的坐标变换计算出来。
除了理想的材料去除之外,Yoshikawa开始研究摩擦和磨粒断裂磨损的影响。
运动模拟的基本方法的关键在于对表面轮廓的模拟和在垂直磨削方向或者磨削方向的工件的表面粗糙度。
此外,Yoshikawa主要研究磨粒的间隔和切屑的形状,同时Kassen致力于切屑厚度和长度以及动态切削刃的数目方面的研究。
1.3 运动几何模型运动几何模拟的基本原理与基本的运动模拟方法在某种意义上是相似的,两者都是取决于工件和砂轮的几何学上的渗透。
与基本的二维运动模拟方法相比,运动几何模拟的关键点是在更高的离散化的水平上详细地计算砂轮和工件间的渗透值。
通过直接模拟每一个磨粒/工件的接触过程,计算出每个磨粒去除的局部工件材料的值,以此作为工件和砂轮相对运动的根据。
这样可以为在微观水平上对磨削过程进行更深入的分析和更综合的过程分析打下良好的基础。
20世纪80年代早期更先进的计算机系统的出现使在数值模拟中使用三维的运动几何模型成为可能。
从那时以来建模变得更加逼真而且有助于完善磨削条件,也完善了对磨削过程的理解。
Becker、Cooper、Domala、Fawcett、Goerne、Gong、Inasaki、Kempa、König、Koshy、Steffens、Tuerich、Warnecke、Zhou和Zitt等人都建立了运动几何模型。
大多数的基本运动模拟方法都将表面粗糙度作为最主要的输出参数,而运动几何模拟的方法提供了更有趣的磨削过程输出参数。
利用切屑横截面、工件材料的磨削力、砂轮速度和工件速度就能够估算出单个磨粒的磨削力或者应力分布和切屑厚度的统计数值以及静态磨粒和动态磨粒的数目。
大多数模型都是假定了理想的微切削或者理想的材料去除方式,也就是说砂轮磨粒能够去除所接触的全部的工件材料,而不考虑塑性变形和碰撞。
有些模型没有将砂轮/工件的相互作用理想化,而是考虑了一些影响进程模拟结果的因素和方面,例如工件材料的相互挤压碰撞、工件的变形、工件/刀具系统的弹性变形以及热量对机械装置的影响。
这些能够计算出工件和接触区域的温度。
而且磨粒的磨削力用来评估砂轮的耐磨程度,利用这个能够得到磨粒的磨损和断裂磨耗。
Kempa和Fawcett利用他们的模型对磨削工艺进行了优化处理。
他们的目标是使表面抛光达到一个想要的水平或者对磨削加工中的共绕因素进行鉴定和削减,例如砂轮的安装误差。
与许多基本的运动模拟方法相比,运动几何模型要灵活很多,并且不受磨削过程中磨粒/工件相互作用的限制。
适当调整加工运动,这个研究磨削表面的方法也可以适用于内圆和外圆磨削、角磨削、精密轮廓磨削、单程表面磨削和齿根轮廓的磨削。
König,Steffens和Inasaki通过扫描砂轮表面建立了砂轮的模型。
Chen,Warnecke和Zitt以及Koshy 在对砂轮和砂轮的扫描数据进行统计学分析的基础上,研究了砂轮表面形貌。
König和Steffens在Steffens研究的基础上,提出了封闭回路模拟法。
这个封闭回路分析法包含了对磨削过程的迭代的数学计算,主要用到了以下输入参数:砂轮表面形貌、机床安装参数、工件材料随温度变化的性能(如屈服应力和导热系数)以及机床―砂轮―工件系统的弹塑性机械性能。
这种方法对内圆和外圆表面的磨削均可以进行模拟仿真。
输出参数有法向力和切向力以及工件的表面粗糙度。
此外,接触区域的热通量也可以沿着接触长度描述出来。
Inasaki提供了一个模型来预测磨削运动特性。
假设理想条件下的材料去除,通过储存的沿砂轮一周的表面轮廓的已测数据就可以模拟出砂轮的表面形貌。
可以模拟出的结果有:每个加工轮廓表面的切削力、切向和法向磨削力、磨削热、工件的表面和最终光整面的表面粗糙度。
Chen提供了一个三维的表面形貌模型,就像大量的球体随机的分布在砂轮表面。
此外,砂轮的模型可以用理想的修整工具进行修整,也可以包含一些磨粒组成的层面。
通过模拟每个磨粒的运动造成的切削运动来对磨削过程进行研究。
加工过程中磨粒的弹性形变和磨粒对工件表面造成的塑性挤压也考虑在内。
而且Chen定义了切削效率为75%,因此有25%未变形的切屑仍然残留在工件上。
这种模拟仿真适合外圆和平面磨削。
这个模拟仿真的输入参数包括砂轮的规格、材料的物理性质、加工和磨削参数。
输出参数是工件表面轮廓、工件表面粗糙度和磨削力。
Warnecke和Zitt提出了模块化、结构化的仿真适用于对平面磨削的运动模拟仿真、内圆和外圆磨削,其中的准备工作是由Warnecke、Merz和Spiegel 来完成的。
Zitt主要致力于磨削中运动学上的关系和合成三维砂轮模型的产生等方面的研究。
这里的砂轮从宏观几何学和微观几何学的角度进行描述。
宏观几何学表明沿着砂轮圆周是理想的循环轮廓,该轮廓可以通过叠加测量的轮廓来模拟圆度误差、砂轮表面卡紧和不均匀分布的影响。
从微观几何学角度描述砂轮模型,随机的磨粒的形状和粘合的背部界面以及静态磨粒的数量和在三维空间的统计分布等。
利用扫描电子显微镜检查法对磨粒几何形状进行统计分析来确定统计学函数,并在此函数的基础上产生出磨粒模型参数。
磨削过程的运动模拟就是砂轮和工件包络轮廓之间的渗透作用。
假设在理想的微切削条件下,未变形的切屑厚度、切屑长度、切屑横截面、工件表面和磨削力作为模拟的输出量都可以计算出来。
有限元建模仿真的概念中描述的机械部件(如刀具系统、砂轮磨粒)的挠曲变形也被嵌入到封闭回路的仿真过程中。
利用Zitt的模拟技术,进一步地研究致力于具有清晰的磨粒结构的砂轮的发展和应用,以便于提高磨削性能,比如说降低磨削力和工件的表面粗糙度等。
Koshy建立了一个模型,用来模拟三维金刚石砂轮加工后的工件表面。
该模型中假定磨粒是球形的,磨粒直径值正常分散并且磨粒在砂轮体积上的空间分布是统一不变的。
Koshy主要研究切入表面的磨削过程并且假定满足微磨削的理想条件。
模拟的砂轮表面形貌、加工运动学和工件材料的性能是必需的输入参数。
这个模拟的主要目的是研究工件材料对工件表面粗糙度的影响。
在进一步的模拟中,Koshy在砂轮表面以特殊的空间格局分布磨粒来使砂轮发挥到最佳性能。
1.4 运动学经验模型运动学经验模型提供了与运动学几何模型相似的输出参数。
区别在于计算加工特性和结果的方法不同。
运动学几何模型计算加工特性和结果是通过砂轮和工件间的刀具的轨迹的变化,而运动学经验模型则是利用经验解析公式来计算。
Chiu模拟了圆柱切入磨削加工的过程。
这个模拟虽然没有预测到加工过程准确的性能,但是却得到了在循环磨削中的主要影响。
磨削模型包含了解析的和经验的数学模型,模拟了磨削力、材料实际去除、热损伤、热膨胀、砂轮磨损、工件表面粗糙度和圆度。
Hecker的磨削仿真模型是在未变形切屑厚度的概率模型的基础上建立的。
该模型是在用Rayleigh 概率分布表达建立的,通过对抛光的砂轮进行取样调查来分析砂轮表面。
接下来的研究项目是,用白光干涉仪来扫描抛光表面来研究切削刃的几何形状,并且计算静态切削刃的密度。
这种仿真方式应用于外圆磨削、平面磨削、切入磨削和纵向进给磨削。
磨粒假定为标准的圆锥形状。
模拟的结果包括切屑厚度、每个磨粒的法向力、总磨削力、总磨削能量、工件表面粗糙度和塑性变形的深度。
1.5 讨论和展望运动学模型考虑了很多方面的因素,但是在高速磨削过程中材料的去除过程仍然没有很充分地模拟出来。
因此,对这些情况下的磨削力进行精确的预测是不可能的,而推断的方法在一定范围内也不能达到较高的质量。
一般说来,在对超硬度材料的加工过程进行模拟时,如果考虑到材料间的相互挤压碰撞就能得到高质量的仿真。
但是如果要考虑到这个因素,现在也只能对其进行简化处理。
因此对高速磨削过程中的材料去除机制进行广泛研究是很有必要的。
另一个进一步的研究领域是对接触区域温度的模拟仿真。
实际磨削过程中的温度测量仍然有很多没有解决的难题,因此要对其进行高质量的模拟仿真更加困难。
在磨削运动学模型的基础上对工件表面的热损伤进行预测是很困难的,现在只能通过微结构分析进行鉴别。