金属切削过程有限元模拟开题报告
金属切削加工过程的有限元建模与仿真

江苏大学硕士学位论文金属切削加工过程的有限元建模与仿真姓名:吴勃申请学位级别:硕士专业:计算机科学与应用指导教师:蔡兰200603014.2切屑形成过程的仿真模型的构造大部分国内的切屑形成过程的有限元仿真都采用的是2.D模型‘蚓脚’,2.D有限元模型仅仅适合于萨交切削的仿真,在研究车削、刨削等切削加工时,必须对切削情况进行限定和简化,不仅视觉效果差,更重要的是仿真的范围受到极大的限制,因此,有必要发展3.D有限元模型来仿真切屑形成过程。
本部分主要采用3.D有限元模型仿真在正交切削和制刃切削条件下的切屑形成过程,为进一步对各种切削加工方法进行有效的有限元仿真奠定基础。
4.2.1几何模型的建立与网格划分本章主要研究刀具切入工件丌始到稳态切削这段过程的仿真。
采用三维有限元模型进行模拟,所建立的几何模型如图4.6所示。
网格划分可采用三维六面体网格,也可以采用三维四面体网格。
幽46网格划分图4.2.2材料属性的定义金属材料非线性的本构关系主要分为以下四种类型,即弹塑性、刚塑性、弹粘塑性、刚粘塑性。
有限元模拟的准确性很大程度上取决于本构关系能否真实反映材料的真实特性。
在金属切削有限元仿真中,采用弹塑性材料模型时,既有塑性变形又有弹性变形,较为符合会属切削过程的真实情况。
本课题中,为了保证仿真结果的更接近于实际情况,工件材料选用弹塑性模型,而刀具属性定义为刚性。
为了与实验结果进行比较,工件材利根掘需要选择相应材料。
与实验加工的材料相对应,输入丁F交材料属性(杨氏模量、泊松比、材料密度等),以及JohnsonandCook的经验模型公式中的参数A、B、n、C和m。
江苏人学硕十学何论文4.2.3施加约束与载荷假定工件在切削过程中为无限长。
而在仿真模型中的工件不可能很长,否则计算效率会很低,必须用长、高都不大的工件代替,用必要的约束来模拟真实工件的边界条件。
当研究切屑形成过程中的现象时。
女nX,j应力、应变、应变率和温度进行研究,以及对切屑卷曲现象进行研究时。
【开题报告】Ti6Al4V切削过程有限元分析
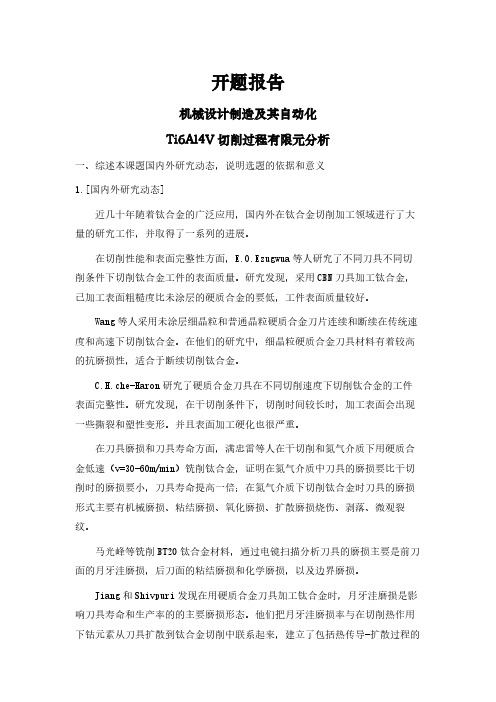
开题报告机械设计制造及其自动化Ti6Al4V切削过程有限元分析一、综述本课题国内外研究动态,说明选题的依据和意义1.[国内外研究动态]近几十年随着钛合金的广泛应用,国内外在钛合金切削加工领域进行了大量的研究工作,并取得了一系列的进展。
在切削性能和表面完整性方面,E.O.Ezugwua等人研究了不同刀具不同切削条件下切削钛合金工件的表面质量。
研究发现,采用CBN刀具加工钛合金,已加工表面粗糙度比未涂层的硬质合金的要低,工件表面质量较好。
Wang等人采用未涂层细晶粒和普通晶粒硬质合金刀片连续和断续在传统速度和高速下切削钛合金。
在他们的研究中,细晶粒硬质合金刀具材料有着较高的抗磨损性,适合于断续切削钛合金。
C.H.che-Haron研究了硬质合金刀具在不同切削速度下切削钛合金的工件表面完整性。
研究发现,在干切削条件下,切削时间较长时,加工表面会出现一些撕裂和塑性变形。
并且表面加工硬化也很严重。
在刀具磨损和刀具寿命方面,满忠雷等人在干切削和氮气介质下用硬质合金低速(v=30-60m/min)铣削钛合金,证明在氮气介质中刀具的磨损要比干切削时的磨损要小,刀具寿命提高一倍;在氮气介质下切削钛合金时刀具的磨损形式主要有机械磨损、粘结磨损、氧化磨损、扩散磨损烧伤、剥落、微观裂纹。
马光峰等铣削BT20钛合金材料,通过电镜扫描分析刀具的磨损主要是前刀面的月牙洼磨损,后刀面的粘结磨损和化学磨损,以及边界磨损。
Jiang和Shivpuri发现在用硬质合金刀具加工钛合金时,月牙洼磨损是影响刀具寿命和生产率的的主要磨损形态。
他们把月牙洼磨损率与在切削热作用下钴元素从刀具扩散到钛合金切削中联系起来,建立了包括热传导-扩散过程的刀具磨损模型,还建立了切削过程中刀削接触面非等温条件下的粘塑性有限元模型。
在冷却液等切削介质的影响方面,E.O.Ezugwua等人研究发现在低速下,切削区域温度相对较低,冷却液的效果相当明显,有润滑、减小摩擦系数、降低切削力和刀具磨损率的作用。
模具钢Cr12MoV铣削过程的有限元仿真毕业设计开题报告
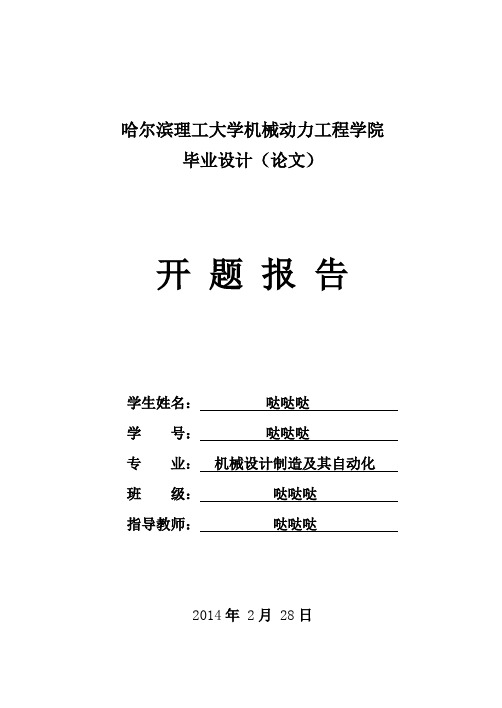
哈尔滨理工大学机械动力工程学院毕业设计(论文)开题报告学生姓名:哒哒哒学号:哒哒哒专业:机械设计制造及其自动化班级:哒哒哒指导教师:哒哒哒2014年 2月 28日课题题目及来源:题目:模具钢Cr12MoV铣削过程的有限元仿真来源:本课题来源于国家科技重大专项子项目:哒哒哒一、课题研究的意义和国内外研究现状:1.课题研究的意义:我国模具产业的发展给予制造业以有力支撑,同时,制造业的发展也推动了模具产业的发展。
作为汽车产量第一大国,我国的汽车模具加工能力还远远不能适应汽车改型换代的需要,虽然目前我国模具行业以每年巨大的进出口总额被誉为全球“制造大国”,但由于技术人才等因素的制约,都相对集中在中低端领域,中高档轿车关键覆盖件的模具制造加工还达不到设计要求。
因此,本项目针对轿车用大型覆盖件淬硬钢模具高品质加工技术的难点。
我国汽车及模具制造企业如何更好的通过技术创新和提高冲压工艺设计的合理性,以此减少模具调试工作量、缩短周期、降低成本,提高企业生产效能是一个具有重要实际意义的课题。
Cr12MoV有高淬透性,根据Cr12MoV的力学特性,可以选择硬态切削来代替传统的磨削加工。
硬态切削是指采用超硬刀具对硬度大于50HRC的淬硬钢进行精密切削的加工工艺。
与磨削相比,硬态切削具有良好的加工柔性、经济性和环保性能,精磨工序中采用硬态切削是加工淬硬钢的最佳选择。
球头铣刀铣削过程包含复杂的多物理场耦合作用,且球头铣刀刀刃特殊,分析较为困难。
在商业有限元软件Deform-3D前处理器中建立了球头铣刀铣削有限元模型,运用可靠的材料模型及切屑分离、断裂准则,采用合理的摩擦模型和传热模型,施加恰当的边界条件,进行了连续两刀齿的仿真模拟铣削过程,得到了铣削力、工件温度场和残余应力场的仿真结果,并分析了铣削速度、进给量、铣削深度等工艺参数对结果的影响。
与早期的刀具设计制造方法相比较,这项技术更为完善、精确,而且设计和制造开发周期更短,此项研究也因而受到我国模具行业的普遍重视,对于研究仿真刀具性能和虚拟制造具有非常深远的意义。
高速金属切削的摩擦分析及有限元模拟

-T r - Tr
式中: A、B、 n、 C、D、E 和 m 是由材料自身决定的
子表示:
常数; Tm 为 材料 的熔 点; T r 为室 温; T 为工 件 的瞬
f ( x ) = p 当 n ( x ) p, 0< x lp
( 2 a) 时温度; 为应变; 为应变速率。
f ( x ) = n ( x ) 当 n (x ) < p, lp < x lc ( 2b) 式中: f 为摩 擦 剪切 应力; p 是 工件 材 料的 剪切 强
刀刃倒角半径0012mm切削宽度1mm摩擦模型41库仑摩擦模型根据库仑摩擦定律r为了确定合适的摩擦因数作者应用平均摩擦因数法即通过试验得出多组切削力f和吃刀抗力f代入式46可得出相应的摩擦因数最后将所得的摩擦因数取平均值作为最终的摩擦因数
2007年 1月 第 32卷 第 1期
润滑与密封
LUBR ICAT ION ENG INEER ING
结摩擦区内, 摩擦 剪切应 力恒定; 在滑移 摩擦 区内, 摩擦因数恒定。前刀面上的摩擦剪切应力可由以下式
变、应变率和温度的函数。本研究使用的材料本构方
程为修改的 Johnson-Cook经验模型 [5] :
= (A + B n ) 1+ C ln (D - ET* m )
(3)
其中 T*
=
T Tm
表 2 切削工艺参数
进给量
0 075 mm
刀具后角
15 3
切削速度
300 m /m in 刀具前角
-7
刀刃倒角半径 0 012 mm
切削宽度
1 mm
根据库仑摩擦定律 f (x ) = n ( x ), 为 了确定合 适的摩擦因数 , 作者应用平 均摩擦因数 法, 即通过
切削加工中的有限元模拟

切削加工中的有限元模拟作者:BerendDenkena、Luis De Leon、Maya Otte 来源:德国Werkstatt + Betrieb杂志借助于有限元分析工具(FEM)的灵活性可以全面地描述切削过程;与实验测试相比,有限元分析可以更好地描述难以测量或者原本无法描述的加工过程。
切削过程的建模以及模拟对于降低加工工时和成本至关重要。
模拟作为开发工具可以用于质量管理和质量优化,并尽可能降低生产起步阶段的风险和试制费用。
有限元分析(FEM)是一种数学方法,尤其适用于解决与工程实际相关的问题,并能在更广的范围内传播。
首先将需计算区域划分为若干大小有限的小单元。
在每一个不等于0的有限单元内寻找解决方案。
整个区域的解决方案通常情况下由相当庞大但精巧的、填充好的线性方程式运算得出。
使用有限元模拟可以借助数学方法对切削过程进行重建,同时将整个过程中任意部位和时间点的温度、延展、延展率、应力和受力计算出来。
因此,有限元模拟可以用来支持不同场合下的实验研究(图1)。
图1 切削加工中的有限元分析在刀具开发过程中,诸如刀具磨损和生产效率等的因素将发挥决定性的作用,因为在整个加工过程中生产效率和质量受到影响。
刀具结构的优化可以提高刀具本身的使用寿命和加工质量。
为了获得比较优化的刀具几何结构,需要考虑切削过程中的热负荷和机械负荷。
此外需要分析沿刀刃和位于刀具内部的应力和温度。
切削刃接触区域内应力、延展、延展率以及温度的详细信息可以用于分析切屑形成的机制。
工件方面,借助有限元方法可以预测固定工件的边缘区域所受到的影响。
对工件内应力形成机制的研究可以用来控制切削过程并进一步调整特定边缘区域的特性。
图2的实例是直角切入式磨削的建模过程。
第一步,使用有限元软件(本例中采用了“Deform 2D”)按照给出的几何参数将刀具自动划分网格。
工件划分网格后再施加额外的边界条件。
根据工件的弹性-塑性形变计算结果选择合适的材料模型。
金属切削过程模拟的有限元仿真

金属切削过程模拟的有限元仿真摘要: 本文在建立车削三维有限元模拟基础上,运用有限元对车削过程中车削的变形系数,工件与刀具的温度分布,切削力进行了模拟,并对结果进行了分析讨论。
该模拟的结果对实际工作有重要的现实作用。
关键词:切削 有限元 模拟1 绪 论1.1本课题的研究背景1.1.1微电子等领域突出的散热问题在现代工业领域,有很多专门用途的设备,它们的工作性能和工作效率取决于关键零件的结构和性能,如空气冷却器,热交换器的散热管,激光器热辐射表面,环保设备的过滤表面,螺纹表面等等。
我们把这类起特定作用的表面统称为“功能表面”。
这些表面大多数采用组装式结构(套装、镶嵌、钎焊、高频焊)、切削、滚压等方法加工。
早在19世纪中期,Jone 就提出在管内插入螺旋线以强化蒸汽的冷凝过程,从此人们就开始了在传热管等传热材料上进行翅加工技术的研究。
70年代出现能源危机,研究翅化管的加工技术及其强化传热机理有了进一步的发展,随着加工制造技术的不断进步,近20年来对强化换热元件的研究在化工、能源、制冷、航空、电子等工业部门有了很大的进展,各式各样的强化换热元件层出不穷,为提高传热效率作出了重要的贡献。
但是随着微电子及化工等领域,尤其是微电子领域对产品性能的无限追求,芯片集成度不断提高,带来致命的高热流密度,电子器件的冷却问题越来越突出。
英特尔公司负责芯片设计的首席执行官帕特-盖尔欣格指出,如果芯片耗能和散热的问题得不到解决,到2005年芯片上集成了2亿个晶体管时,就会热得象“核反应堆”,2010年时会达到火箭发射时高温气体喷射的水平,而到2015年就会与太阳的表面一样热。
目前芯片发热区域(cm cm 5.15.1 )上的功耗已超过105W ,且未来有快速增加的趋势。
芯片产生的这些热量如果不能及时散出,将使芯片温度升高而影响到电子器件的寿命及工作的可靠性,因而电子器件的有效散热方式已成为获得新一代电子产品的关键科学问题之一。
两种典型金属高速切削过程有限元模拟与分析的开题报告
两种典型金属高速切削过程有限元模拟与分析的开题报告题目:两种典型金属高速切削过程有限元模拟与分析的研究一、研究背景金属加工是现代工业生产的重要组成部分,其中高速切削技术是一种重要的金属加工技术。
通过高速旋转的刀具对金属进行切削,可以快速地制造出各种形状的金属零件。
然而,在高速切削过程中,由于切削力、热量等因素的影响,会导致切削质量下降、加工精度降低、设备寿命缩短等问题,因此需要进行优化和控制。
有限元模拟是一种重要的工程仿真方法,已经广泛应用于金属加工领域。
通过建立相应的有限元模型,可以对金属加工过程中的力、温度、应变等参数进行预测和分析,为工艺的优化和控制提供理论依据。
因此,对于金属高速切削过程的有限元模拟和分析研究,具有重要的理论和实际意义。
二、研究内容本研究将以两种典型的金属高速切削过程——铣削和车削为研究对象,开展有限元模拟与分析研究,探讨切削参数对加工质量的影响,为优化和控制金属高速切削过程提供参考。
1. 铣削过程有限元模拟与分析铣削是一种常见的金属加工技术,其加工过程包括切入、切削和切出三个阶段。
在铣削过程中,切入阶段和切出阶段的切削角度较小,切削阶段的切削角度较大,因此这三个阶段对应的切削力和切削温度分布规律也不同。
本研究将建立铣削过程有限元模型,对切入、切削和切出三个过程的切削力、切削温度等参数进行模拟和分析,揭示不同切削参数对切削力和切削温度的影响规律。
2. 车削过程有限元模拟与分析车削是一种高效的金属加工技术,可以用于加工圆形、柱形等各种形状的零件。
在车削过程中,刀具切入工件后,与之接触的区域产生高温,导致金属发生塑性变形。
本研究将建立车削过程有限元模型,对切削力、切削温度等参数进行模拟和分析,揭示不同切削参数对加工质量的影响规律。
三、研究意义通过本研究,可以深入了解金属高速切削过程中的力学、热学和材料学等基本规律,为优化和控制切削过程提供理论依据。
此外,通过对不同切削参数对切削力、切削温度等参数的影响规律的分析,可以为金属加工工艺的优化和改进提供实用的建议和方法。
切削加工有限元模拟
铝合金A357切削加工有限元模拟1铝合金A357切削加工有限元模型金属切削加工有限元模拟,是一个非常复杂的过程。
这是因为实际生产中,影响加工精度、表面质量的因素很多,诸如:刀具的儿何参数、装夹条件、切削参数、切削路径等。
这些因素使模拟过程中相关技术的处理具有较高的难度。
本文建立的金属正交切削加工热力耦合有限元模型是基于以下的假设条件:(1)刀具是刚体且锋利,只考虑刀具的温度传导;(2)忽略加工过程中,由于温度变化引起的金相组织及其它的化学变化; (3)被加工对象的材料是各向同性的; (4)不考虑刀具、工件的振动;(5)由于刀具和工件的切削厚度方向上,切削工程中层厚不变,所以按平面应变来模拟;1.1材料模型1.1.1A357的Johnson-Cook 本构模型材料本构模型用来描述材料的力学性质,表征材料变形过程中的动态响应。
在材料微观组织结构一定的情况下,流动应力受到变形程度、变形速度、及变形温度等因素的影响非常显著。
这些因素的任何变化都会引起流动应力较大的变动。
因此材料本构模型一般表示为流动应力与应变、应变率、温度等变形参数之间的数学函数关系。
建立材料本构模型,无论是在制定合理的加工工艺方面,还是在金属塑性变形理论的研究方面都是极其重要的。
在以塑性有限元为代表的现代塑性加工力学中,材料的流动应力作为输入时的重要参数,其精确度也是提高理论分析可靠度的关键。
在本课题研究中,材料本构模型是切削加工数值模拟的必要前提,是预测零件铣削加工变形的重要基础,只有建立了大变形情况下随应变率和温度变化的应力应变关系,才能够准确描述材料在切削加工过程的塑性变形规律,继而才能在确定的边界条件和切削载荷下预测零件的变形大小及趋势。
在切削过程中,工件在高温、大应变下发生弹塑性变形,被切削材料在刀具的作用下变成切屑时的时间很短,而且被切削层中各处的应变、应变速率和温度并不均匀分布且梯度变化很大。
因此能反映出应变、应变速率、温度对材料的流动应力影响的本构方程,在切削仿真中极其关键。
正交金属切削过程的有限元分析
正交金属切削过程的有限元分析Chandrakanth Shet,Xiaomin Deng机械工程系,南卡罗来纳州大学,哥伦比亚,SC 29208部,美国1999年4月8日收到摘要在本文中,正交金属切削过程是在平面应变条件下用有限元法分析的。
修改过的库伦摩擦定律模拟了刀-屑接触面的摩擦作用,切屑的分离是基于临界应力准则,并且是利用节点释放过程模拟切屑的分离。
对温度、应力、应变、应变率的领域的有限元法已经获得了一系列的刀具前角和摩擦系数值。
结果显示到-屑接触面的摩擦如何影响场分布的是新的,并添加到现有的知识基础中。
本文还报告了程序和特定的建模技术,他们用于使用通用的有限元计算机代码模拟正交金属切削过程。
本文的研究结果对于理解和改善正交金属切削过程提供了有益的启示。
©2000 Elsevier科学S.A.公司保留所有权利。
关键词:有限元法;正交金属切削;热机械领域1. 引言在金属切削过程中,不需要的材料从工件中以切屑的形式移除来制造所需要的尺寸和精度的成品部件。
金属切削是一个高度非线性的并且热耦合的过程,在这个过程中机械工作是把在切屑的形成过程中和刀具、切屑和工件之间的摩擦工作所涉及的塑性变形转换成热能。
在这样的热机械热量转换中,向上的温度上升到1000℃已经在文献中报道[1,2]。
在金属切削中深入了解材料去除工艺对选择刀具材料和刀具的设计是必不可少的,以及在确保成品的一致尺寸精度和表面完整性。
最早解释金属切削机械的分析模型是由Merchant[3,4],Piispanen[5]和Lee and Shaffer[6]提出。
这些模型被称为剪切角模型;他们确定了剪切角和刀具前角之间的对应关系。
Kudo[7]提出了弯曲剪切并解释了弯曲切屑和直刀面之间的控制联系。
这些模型完美的假设材料为刚塑性材料。
Palmer[8]和Oxley[9]等提出的分析模型考虑了构件硬化和应变率的影响。
沿着刀具和切屑接触面的摩擦都由Doyle[10]等人纳入了这些粘塑性模型。
金属难加工材料切削及刀具磨损虚拟仿真报告(一)
金属难加工材料切削及刀具磨损虚拟仿真报告(一)金属难加工材料切削及刀具磨损虚拟仿真报告挑战:金属难加工材料的切削加工•金属难加工材料的定义•高温、高硬度导致的切削困难•切削加工的关键问题方法:利用虚拟仿真技术进行分析•虚拟仿真技术的定义和优势•应用虚拟仿真技术分析金属难加工材料的切削行为•仿真模型的建立和参数设置结果:切削过程中的问题及研究成果•切削力的变化规律及影响因素•切削温度的分布和变化趋势•切削表面质量和切削力之间的关系讨论:刀具磨损与切削性能的关系•刀具磨损的原因和影响因素•切削力和刀具磨损的关系•如何通过优化切削参数延缓刀具磨损总结:虚拟仿真技术在切削加工中的应用前景•虚拟仿真技术的优势和局限性•未来发展方向和研究重点•为实际切削加工提供参考和决策依据金属难加工材料切削及刀具磨损虚拟仿真报告挑战:金属难加工材料的切削加工•金属难加工材料的定义–金属难加工材料是指具有高硬度、高强度和高耐磨性的金属材料,如钛合金、高速钢等。
•高温、高硬度导致的切削困难–由于金属难加工材料的硬度较高,切削时需要更大的切削力。
–高温会导致材料软化和脆性增加,使刀具损耗加剧。
•切削加工的关键问题–如何降低切削力和温度,提高切削效率和加工质量。
方法:利用虚拟仿真技术进行分析•虚拟仿真技术的定义和优势–虚拟仿真技术利用计算机模拟真实物理过程,可以减少实验成本、提高研究效率。
–通过虚拟仿真可以提前预测切削加工过程中的各种参数和结果。
•应用虚拟仿真技术分析金属难加工材料的切削行为–通过建立切削仿真模型,可以模拟金属难加工材料在切削过程中的变形、热力分布等行为。
–利用仿真结果可以分析切削力、切削温度和切削表面质量等参数的变化趋势。
•仿真模型的建立和参数设置–建立金属难加工材料的切削仿真模型。
–设置切削参数,如切削速度、进给速度和切削用量。
–调整模型和参数以获得准确的仿真结果。
结果:切削过程中的问题及研究成果•切削力的变化规律及影响因素–切削力随着切削速度的增加而增加,随着进给速度的增加先增加后减小。
- 1、下载文档前请自行甄别文档内容的完整性,平台不提供额外的编辑、内容补充、找答案等附加服务。
- 2、"仅部分预览"的文档,不可在线预览部分如存在完整性等问题,可反馈申请退款(可完整预览的文档不适用该条件!)。
- 3、如文档侵犯您的权益,请联系客服反馈,我们会尽快为您处理(人工客服工作时间:9:00-18:30)。
1994年,Zhang和Bagchi建立的正交有限元模型是利用两节点间的连续单元来模拟切削的分离,并以刀具的几何位置条件作为切屑分离的准则。当刀具进行切削时,这些连续的单元会依次分离从而形成切屑和工件的加工表面。
2006年,江苏大学卢树斌采用DEFORM软件建立了二维和三维金属切削模型,研究了高速金属切削原理,模拟了高速切削下切屑的形成过程,并对刀具的磨损状况进行了预测。
2007年,刘胜永等讨论了二维切削中摩擦系数对切屑变形、切削温度等的影响。
综上可见,尽管国内外关于金属切削过程有限元模拟方面的研究工作已经开展多年,三维有限元模型也被越来越多的人采用,但三维有限元模型中的多数工作也仅仅是针对简化后几何结构,且很少涉及到刀具的磨损,其模拟结果有较大的理想型,在一定的程度上限制了模拟结果对实际加工的预测和指导意义。
(2)实际切削过程的诸多工艺因素的影响在切削加工模拟中不在被简化或忽略。例如,车床的振动、冷却液、切削过程中的非正交、间歇切削等。
(3)在实际切削加工中,工件材料的组织性能变化非常复杂,在特定的刀具-工件系统中,具备发生相变的热力学和动力学条件。成分和组织的变化将引起性能的变化,因此工件材料一旦发生相变,刀具材料的磨损机制、切削力、切削变形和加工表面质量也将发生相应变化。但是,目前在这方面的研究还很少。
1985年,Stren-Kowski和Carrol建立了一个较新的有限元模型,此模型包括一个基于有效塑性应变的切屑分离准则,一些以前被忽略的参数被考虑进有限元模型,如构件、刀具被考虑为弹塑性材料,刀具与切屑之间的摩擦等。
1990年,Stren-Kowsk和Moon利用Eluer有限元模型研究正交切削,模拟了切屑形状,预测了工件、刀具以及切屑中的温度分布;Usui等人首次将低碳钢流动应力假设为应变、应变速率和温度的函数,以此模拟了连续切削中产生的切削瘤,而且在刀具和切屑接触面上采用库伦摩擦模型,利用正应力、摩擦应力和摩擦系数之间的关系模拟了切削工艺;Komvopoulos和Erpenbeck用弹塑性有限元模型研究了钢质材料正交切削中刀具侧面磨损、积屑瘤及工件中的残余应力等。
金属切削数值模拟的首要任务就是切削模型的建立。早在1937年,著名学者Piispanen最先建立了切削模型(卡片运动模型)。这一模型是一个比较理想化的模型。它把稳态切削状态下产生切屑的原因描述为一叠卡片在刀具的挤推作用下沿着刀具的前刀面滑动而形成,并假象剪切区域是在一个绝对的平面上,因此,它无法解释切屑卷曲变形等问题。但是,它为以后切削模型的建立奠定了良好的基础。
1981年,Usui、Maekawa和Shirakashi等学者假设工件的流应力是应变、应变率和温度的函数,利用有限元法建立刀刃切削连续产生切屑的模型,采用库伦摩擦定律处理切屑-刀具接触面的发向力、摩擦力及摩擦系数的关系。
1982年,Usui和Shirakashi为了建立稳态的正交切削模型,第一次提出了刀面角、切屑几何形状和流线等概念,预测了应力应变和温度等参数;1984年,Iwata利用等塑性有限元方法分析了在低切削速度、低应变速率下的稳态切削。但是,他们都没有考虑弹性变形,所以没有计算出残余应力。
(3)切削的控制和刀具设计 前刀面形状的设计对于控制切屑的流动和减少刀具的受力、磨损和失效具有非常重要的意义。切屑的流动和控制也主要依赖于刀具的几何形状和切削条件。
(4)目前有限元在实际生产中的应用主要在研究刀具设计和材料加工性能发面。由于其计算时间太长还无法应用到制造车间作为在线控制和优化工具,只能作为离线的评价工具。这说明需要对影响切削加工的各要素做进一步研究
(5)迭代收敛法由于其计算效率高仍然是是研究稳态切削的重要工具:弹塑性自适应网格更新拉格朗日法是最完善的研究非稳态切削的方法:在弹性形变可以忽略和减少计算量的时候可以选用钢塑性模型。
4.应用领域:
(1)积屑瘤的形成机理 在切削大多数多相合金的时候,在一定的切削速度下,就会形成积屑瘤。积屑瘤是一小块来自切屑和工件材料所构成的楔形金属,它包围着切削刃,能够代替前刀面和切削刃进行切削。
(2)易切刚的可加工性 易切钢相对于普通碳钢在低速切削时,具有切削力小,剪切角比较大的特点。对这一现象的解释是易切钢中内含的MnS颗粒对主变形区的金属起到了脆化作用,同时又对前刀面起到了润滑效果。
1959年Palmer和Oxley、1961年Oxley等在他们的模型中考虑了构件硬化和应变率对加工过程造成的影响,使材料模型更加的合理;1965年Kudo建立了切屑卷曲模型,但这些模型都没有考虑切削热对材料的影响。
有限元方法最早被应用在切削加工的模拟是在70年代,1973年,B.E.Klamechi最先系统的研究了金属切削加工中切屑形成的原理,并用三维有限元模型分析了切屑形成的初始阶段。
2.发展趋势:
到目前为止有限元法更多的是作为理解切削加工机理的重要工具。随着研究的进一步深入,预期下列几方面将成为研究的重点。
(1)切削模型的进一步完善化。目前,大多数研究工作者还是致力于建立能反映一般切削过程的切削模型。将来反应切削过程中各种特定现象的切削模型将成为研究的热点。例如,能反应积屑瘤、鳞刺、切削层中的分流等现象的切削模型,以期通过对这些模型的分析,更好的阐明切削过程中各种现象的本质,提出控制这些现象的措施,进而建立能根据切削过程各种力学参数的变化而预测切削结果的预测理论。
2003年,宋金玲等通过计算机模拟金属切削连续稳态成屑过程,以三角元素进行有限元网格划分,采用Von-Mises屈服判据和Prandtl-Reuss流动定律,对工件切屑进行弹塑性变形及受力分析。
2004年,邓文君等华南理工大学建立了高强度耐磨铝青铜的正交切削有限元模型,该模型用了热-力耦合方法,形成的是连续形切屑。刀具使用增量步法移动,使用有限元分析软件MARC的网格重复技术,对刀具开始切削到切削温度达到一个稳定的状态的切削过程进行了有限元仿真。分析了在不同的切削速度和切削深度下应力、应变、温度、应变速率以及切屑形状,该模型也是二维模型。
毕业论文开题报告
题 目金属切削过程的有限元模拟
学生姓名李飞峰学号**********
所在院(系)机械工程学院
专业班级机自S1102班
指导教师王燕燕
2015年3月15日
题 目
金属切削过程的有限元模拟
一、选题的目的及研究意义
金属切削过程是机械制造业中最重要的过程之一,它在机械制造工业中占据着重要的地位,并对国家经济和技术的发展有着深远的影响。金属切削加工的实质就是刀具和工件的相互作用用刀具切除工件上多余的金属层,从而获得形状、精度及表面质量都符合要求的工件的过程。在此过程中会伴随着各种现象,如切削变形、切削力、切削热、刀具的磨损与耐用度等,并且这些现象严重影响着产品的质量及生产成本。实际上,切削过程是一个很复杂的过程,它涉及到弹性力学、塑性力学、断裂力学还有热力学、摩擦学等诸多学科。切削质量受到刀具形状、切屑的流动、温度分布、热流和刀具磨损等影响,切削表面的残余应力和残余应变严重影响了工件的精度和疲劳寿命。为了研究金属切削的机理,使切削参数的选取、刀具的设计更加合理,学者们已经做了大量的研究工作,先后建立了许多简化的力学模型,其中比较著名的有Merchant切削模型和Oxley切削模型,对切削机理的研究起到了积极的推动作用。但是切削过程中各个变形区的变化过程、应力分布、应变分布、切削温度的分布等,仅仅通过解析法求解是不能解决的。随着计算机硬件技术和软件技术的快速发展,有限元(FEM)已经成为金属切削过程仿真的有效工具,实践证明,采用有限元来数值模拟解决工程实际问题能够达到所需的精度具有很高的可靠性。而且还可以得到许多从实验中很难得到的重要数据,仿真结果形象,直观,对实践有着很高的指导价值。利用有限元仿真技术研究金属切削加工过程以及各种参数之间的关系成为可能。并且能够方便地分析各种工艺参数对切削过程的影响,为优化切削工艺和提高产品精度与性能提供理论和实用手段。有限元所提供的分析方法,对于实际生产中工艺参数的优化,切削质量的控制,刀具设计提供了依据,同时对于提高金属切削效率并改善加工表面质量,优化加工工艺具有重要意义。
1940年,最早研究金属切削机理的是Merchant,Piispanen,Lee and Shaffer等人,他们建立了金属切削的剪切角模型,并确定了剪切角与前角之间的对应关系。此后,大量学者开始将切削过程中的摩擦、高速应变率、加工硬化和切削温度对工件和加工精度的影响考虑到切削的模型中去,这使得对金属切削仿真计算的结果与实际测量数据更加接近,增加了人们对金属切削机理的认识。
1995年,Shih建立了一个二维应变有限元模型来模拟正交切削连续切削形成的过程。其中工件材料考虑了弹性、粘塑性、温度、大应变和高应变效率,同时引入不平衡力的递减方法来改善切屑形成时单元分离过程中的稳定性。并建立了粘-滑动摩擦模型,用来解决切削-刀具接触面的摩擦问题。
1996年,Sasahara和Obikawa等利用弹塑性有限元法,忽略了温度和应变速率的效果,模拟了低速连续切削时被加工表面的的残余应力和应变;Zone-Ching Lin,Yuung-Der Yarng利用更新的拉格朗日方程及增量理论建立了三维弹塑性有限元模型,并研究了不同切削速度下切削中碳钢时切削力及残余应力的变化。
(6)最后值得一提的是,纳米级的微细切削加工模拟也已经出现。可见从微观角度来研究切削加工机理也开始被重视起来。
3.研究方法:
本课题采用有限单元法对金属切削过程进行分析,它的基本思想是将一个连续体离散化,即将连续体变换成为由有限数量的有限大的单元体的集合,而且认为单元之间只通过被称为节点的连接点连接起来。由于单元能按不同的联结方式进行组合,且单元本身有可以有不同形状,因此可以模型化几何形状复杂的求解域。
2002年,P.J.Arrazola,F.Meslin,C.R.Lin,Y.B.Guo等人对三维金属切屑过程的模拟进行了深入研究,分别建立了金属切削仿真的二维和三维切削模型,他们采用了网格自适应重划算法来解决刀-屑接触区局部单元所产生的大变形问题,分析了切削过程中的工件和刀具中的温度场、VonMises应力分布等,成功的模拟了切削的性形成过程。