abaqus-铝合金A357切削加工有限元模拟
铝合金精密铣削有限元仿真的参数化建模

铝合金精密铣削有限元仿真的参数化建模王洪祥;徐涛;杨嘉【摘要】对有限元软件(ABAQUS)自带的编程语言(Python)以及ABAQUS GUI Toolkit工具的一些基本概念进行了简要介绍,阐述了利用有限元软件(ABAQUS)建模的基本过程.利用编程语言(Python)和ABAQUS GUI Toolkit工具,编写了可视化用户界面,实现了铝合金铣削过程的参数化建模.【期刊名称】《轻合金加工技术》【年(卷),期】2011(039)012【总页数】4页(P51-54)【关键词】有限元;铝合金;铣削;参数化建模【作者】王洪祥;徐涛;杨嘉【作者单位】哈尔滨工业大学机电工程学院,黑龙江哈尔滨150001;哈尔滨工业大学机电工程学院,黑龙江哈尔滨150001;哈尔滨工业大学机电工程学院,黑龙江哈尔滨150001【正文语种】中文【中图分类】TG146.21;TH164铝合金的切削过程是一个涉及影响因素较多的复杂过程,人们往往通过试验来研究铝合金切削性能,经过多次试验,才能优选出切削参数,这样不仅成本较高,而且试验周期很长。
随着计算机技术的发展,有限元法被越来越多地运用到铝合金切削过程的研究中,但是在利用有限元仿真技术对切削过程进行仿真时,需要大量的算例进行对比,操作较为繁琐,工作量大。
ABAQUS是法国Dassault Aviation公司开发的一款商业有限元软件,它自带的编程语言(Python)和ABAQUS GUI Toolkit工具可帮助用户构建可视化的界面,减少用户手工操作工作量,提高计算效率。
借助ABAQUS强大的功能,通过二次开发可实现航空用铝合金铣削过程有限元参数化建模。
1 Python编程语言Python是一种易于解释、面向对象的高级程序语言。
一直以来,人们都认为Python是一种脚本语言,但它也是一种支持脚本语言的编程语言。
Python语言拥有高效的数据结构和动态的类型识别模式,能够在多种平台上执行,实现多种功能[1-3]。
abaqus铝合金材料参数
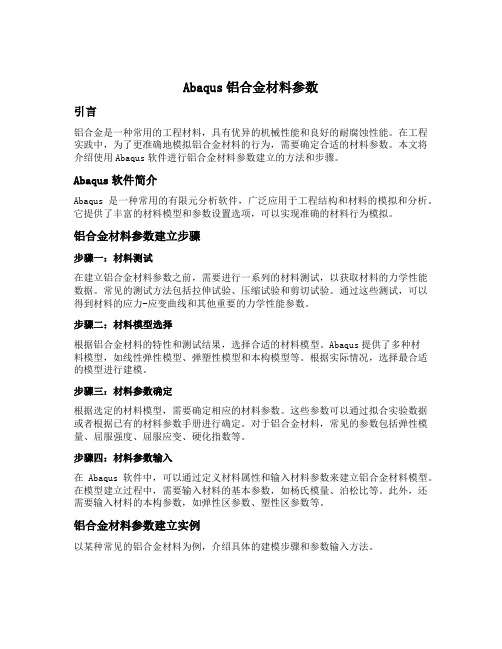
Abaqus铝合金材料参数引言铝合金是一种常用的工程材料,具有优异的机械性能和良好的耐腐蚀性能。
在工程实践中,为了更准确地模拟铝合金材料的行为,需要确定合适的材料参数。
本文将介绍使用Abaqus软件进行铝合金材料参数建立的方法和步骤。
Abaqus软件简介Abaqus是一种常用的有限元分析软件,广泛应用于工程结构和材料的模拟和分析。
它提供了丰富的材料模型和参数设置选项,可以实现准确的材料行为模拟。
铝合金材料参数建立步骤步骤一:材料测试在建立铝合金材料参数之前,需要进行一系列的材料测试,以获取材料的力学性能数据。
常见的测试方法包括拉伸试验、压缩试验和剪切试验。
通过这些测试,可以得到材料的应力-应变曲线和其他重要的力学性能参数。
步骤二:材料模型选择根据铝合金材料的特性和测试结果,选择合适的材料模型。
Abaqus提供了多种材料模型,如线性弹性模型、弹塑性模型和本构模型等。
根据实际情况,选择最合适的模型进行建模。
步骤三:材料参数确定根据选定的材料模型,需要确定相应的材料参数。
这些参数可以通过拟合实验数据或者根据已有的材料参数手册进行确定。
对于铝合金材料,常见的参数包括弹性模量、屈服强度、屈服应变、硬化指数等。
步骤四:材料参数输入在Abaqus软件中,可以通过定义材料属性和输入材料参数来建立铝合金材料模型。
在模型建立过程中,需要输入材料的基本参数,如杨氏模量、泊松比等。
此外,还需要输入材料的本构参数,如弹性区参数、塑性区参数等。
铝合金材料参数建立实例以某种常见的铝合金材料为例,介绍具体的建模步骤和参数输入方法。
步骤一:材料测试对该铝合金材料进行拉伸试验,得到应力-应变曲线。
根据试验数据,计算出屈服强度和屈服应变等力学性能参数。
步骤二:材料模型选择根据铝合金材料的非线性特性,选择弹塑性模型进行建模。
步骤三:材料参数确定根据试验数据,拟合得到材料的本构参数。
假设材料的本构关系为线性弹性-塑性本构关系,通过拟合得到以下参数: - 弹性模量:70 GPa - 屈服强度:300 MPa - 屈服应变:0.2 - 硬化指数:0.1步骤四:材料参数输入在Abaqus软件中,定义材料属性并输入材料参数。
铝合金高速切削有限元仿真及实验研究

铝合金高速切削有限元仿真及实验研究作者:汪健明刘康来源:《软件工程》2021年第12期摘要:为了研究不同切削参数对铝合金切削过程中切削力和切削温度的影响,以铝合金7075-T651为对象,采用仿真与实验验证结合的方法,利用金属有限元切削专用软件AdvantEdge建立了铝合金7075-T651的二维正交切削仿真模型,并进行合理的工件和刀具材料参数以及本构模型设置。
通过仿真分析,研究了切削力和切削温度与进给速度以及切削深度的关系,并通过实验进行验证。
仿真和实验结果表明:在一定范围内,随着进给速度和切削深度的增大,切削力和切削温度增大。
切削铝合金7075-T651时,应采用较小的切削深度和进给速度。
关键词:AdvantEdge;铝合金7075-T651;切削力;切削温度中图分类号:TP319 文献标识码:AAbstract: In order to study the influence of different cutting parameters on cutting force and cutting temperature in cutting process of aluminum alloy, this research uses aluminum alloy 7075-T651 as the object, and takes the method of combining simulation and experimental verification as the research method. This paper proposes to use special software AdvantEdge of metal finite element cutting to establish two-dimensional orthogonal cutting simulation model of aluminum alloy 7075-T651. Reasonable workpieces, tool material parameters and constitutive model are set. Through simulation analysis, the relationship between cutting force and cutting temperature, feed speed and depth of cut are studied and verified by experiments. Simulation and experimental results show that within a certain range, with the increase of feed speed and cutting depth, cutting force and cutting temperature increase. When cutting aluminum alloy 7075-T651, smaller depth of cutting and feed rate should be used.Keywords: AdvantEdge; aluminum alloy 7075-T651; cutting force; cutting temperature1 引言(Introduction)由于鋁合金7075-T651具有高比强度和良好的热加工性能,以及高韧性和良好的耐腐蚀性,近年来在航空航天、模具加工、机械设备以及夹具中得到了越来越多的应用[1-2]。
基于ABAQUS有限元仿真的硬质合金刀具磨损机制研究
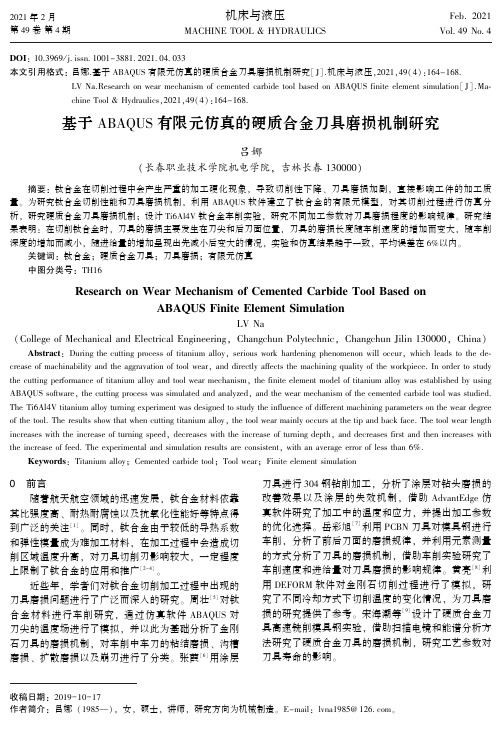
2021年2月第49卷第4期机床与液压MACHINETOOL&HYDRAULICSFeb.2021Vol 49No 4DOI:10.3969/j issn 1001-3881 2021 04 033本文引用格式:吕娜.基于ABAQUS有限元仿真的硬质合金刀具磨损机制研究[J].机床与液压,2021,49(4):164-168.LVNa.ResearchonwearmechanismofcementedcarbidetoolbasedonABAQUSfiniteelementsimulation[J].Ma⁃chineTool&Hydraulics,2021,49(4):164-168.收稿日期:2019-10-17作者简介:吕娜(1985 ),女,硕士,讲师,研究方向为机械制造㊂E-mail:lvna1985@126 com㊂基于ABAQUS有限元仿真的硬质合金刀具磨损机制研究吕娜(长春职业技术学院机电学院,吉林长春130000)摘要:钛合金在切削过程中会产生严重的加工硬化现象,导致切削性下降㊁刀具磨损加剧,直接影响工件的加工质量㊂为研究钛合金切削性能和刀具磨损机制,利用ABAQUS软件建立了钛合金的有限元模型,对其切削过程进行仿真分析,研究硬质合金刀具磨损机制;设计Ti6Al4V钛合金车削实验,研究不同加工参数对刀具磨损程度的影响规律㊂研究结果表明:在切削钛合金时,刀具的磨损主要发生在刀尖和后刀面位置,刀具的磨损长度随车削速度的增加而变大,随车削深度的增加而减小,随进给量的增加呈现出先减小后变大的情况,实验和仿真结果趋于一致,平均误差在6%以内㊂关键词:钛合金;硬质合金刀具;刀具磨损;有限元仿真中图分类号:TH16ResearchonWearMechanismofCementedCarbideToolBasedonABAQUSFiniteElementSimulationLVNa(CollegeofMechanicalandElectricalEngineering,ChangchunPolytechnic,ChangchunJilin130000,China)Abstract:Duringthecuttingprocessoftitaniumalloy,seriousworkhardeningphenomenonwilloccur,whichleadstothede⁃creaseofmachinabilityandtheaggravationoftoolwear,anddirectlyaffectsthemachiningqualityoftheworkpiece.Inordertostudythecuttingperformanceoftitaniumalloyandtoolwearmechanism,thefiniteelementmodeloftitaniumalloywasestablishedbyusingABAQUSsoftware,thecuttingprocesswassimulatedandanalyzed,andthewearmechanismofthecementedcarbidetoolwasstudied.TheTi6Al4Vtitaniumalloyturningexperimentwasdesignedtostudytheinfluenceofdifferentmachiningparametersontheweardegreeofthetool.Theresultsshowthatwhencuttingtitaniumalloy,thetoolwearmainlyoccursatthetipandbackface.Thetoolwearlengthincreaseswiththeincreaseofturningspeed,decreaseswiththeincreaseofturningdepth,anddecreasesfirstandthenincreaseswiththeincreaseoffeed.Theexperimentalandsimulationresultsareconsistent,withanaverageerroroflessthan6%.Keywords:Titaniumalloy;Cementedcarbidetool;Toolwear;Finiteelementsimulation0㊀前言随着航天航空领域的迅速发展,钛合金材料依靠其比强度高㊁耐热耐腐蚀以及抗氧化性能好等特点得到广泛的关注[1]㊂同时,钛合金由于较低的导热系数和弹性模量成为难加工材料,在加工过程中会造成切削区域温度升高,对刀具切削刃影响较大,一定程度上限制了钛合金的应用和推广[2-4]㊂近些年,学者们对钛合金切削加工过程中出现的刀具磨损问题进行了广泛而深入的研究㊂周壮[5]对钛合金材料进行车削研究,通过仿真软件ABAQUS对刀尖的温度场进行了模拟,并以此为基础分析了金刚石刀具的磨损机制,对车削中车刀的粘结磨损㊁沟槽磨损㊁扩散磨损以及崩刃进行了分类㊂张葭[6]用涂层刀具进行304钢钻削加工,分析了涂层对钻头磨损的改善效果以及涂层的失效机制,借助AdvantEdge仿真软件研究了加工中的温度和应力,并提出加工参数的优化选择㊂岳彩旭[7]利用PCBN刀具对模具钢进行车削,分析了前后刀面的磨损规律,并利用元素测量的方式分析了刀具的磨损机制,借助车削实验研究了车削速度和进给量对刀具磨损的影响规律㊂黄亮[8]利用DEFORM软件对金刚石切削过程进行了模拟,研究了不同冷却方式下切削温度的变化情况,为刀具磨损的研究提供了参考㊂宋海潮等[9]设计了硬质合金刀具高速铣削模具钢实验,借助扫描电镜和能谱分析方法研究了硬质合金刀具的磨损机制,研究工艺参数对刀具寿命的影响㊂基于此,为进一步研究硬质合金刀具车削钛合金时的耐用性能,提高加工后的表面质量和加工精度,利用ABAQUS软件建立硬质合金刀具车削钛合金的有限元模型,研究不同工艺参数条件下切削区域温度场和应力场的变化情况,分析刀具切削过程中的磨损机制,并通过钛合金车削实验,对刀具磨损理论模型的合理性进行验证㊂1 有限元仿真1 1㊀建立几何模型为降低刀具切削实验过程的经济成本,首先通过有限元仿真方式对硬质合金刀具的磨损机制进行研究㊂如图1所示为利用有限元仿真软件ABAQUS建立的硬质合金刀具和钛合金工件的几何模型㊂图1㊀车削仿真几何模型在加工中刀具磨损受到多方面因素的影响,主要为加工参数㊁加工环境㊁冷却条件以及机床设备等㊂为了提高仿真结果的准确性,对ABAQUS仿真进行如下假设:(1)加工过程中不会发生崩刃等刀具损坏情况;(2)工件材料各向同性并且材质均匀,并且不会发生切削相变等情况;(3)车削加工中始终保持稳定状态,不会出现积屑瘤等情况㊂1 2㊀材料本构方程车削加工中刀具磨损的主要因素包含了切削温度,因此使用在材料热软化㊁应变以及应变率方面具有强关联性的Johnson-Cook模型作为本构方程,可表示为σ=A+Bεn[]1+clnε㊃ε㊃0æèçöø÷éëêêùûúú㊃1-T-TrTm-Træèçöø÷méëêêùûúú(1)式中:σ为材料在加工中受到的流动应力;A为材料的屈服强度;B为材料的极限强度;c为应变敏感率;n为应变硬化指数;m为温度敏感系数;ε㊃0为参考应变速率;Tr为参考温度;Tm为材料的熔点㊂模型的具体参数[10]如表1所示㊂表1㊀钛合金参数参数A/MPaB/MPacnm参数值8757930.0110.3860.711 3㊀接触属性设置为研究车削加工中的刀具磨损情况,首先要定义硬质合金刀具和钛合金工件的接触属性㊂对于刀具和工件之间的接触方式,将法向的接触属性设置为 硬 接触;在切向方向,由于加工时二者之间的相互摩擦对切削力和切削温度的变化具有重要影响,根据库仑摩擦定律对摩擦因数进行设置,其表达式为τf=μσn㊀㊀㊀μσn<τmaxτmax㊀㊀㊀μσnȡτmax{(2)式中:τf为接触面位置的摩擦剪切压力;σn为工件和刀具之间的正压力;τmax为接触面位置的最大摩擦剪切压力;μ为摩擦因数㊂1 4㊀材料失效准则工件材料的失效方式采用剪切失效模型,当单元节点上的等效塑性应变值参数D超过1时,就可以判定工件发生失效分离,此处单元将被删除[9]㊂D=ðΔεpiεpf(3)式中:D为量纲一化的累计损伤参数;εpi为瞬时塑性应变增量;εpf为材料的失效应变㊂1 5㊀仿真及分析图2所示为钛合金车削仿真,可以看出:随着硬质合金刀具和工件接触,刀具切削刃受到工件的冲击,在冲击作用下刀具表面出现应力集中㊂此时由于刀具进给速度不大,并没有出现崩刃等导致刀面损坏的情况,与实际加工基本一致㊂图2㊀钛合金车削仿真随着刀具切削刃压入深度逐渐增加,工件基体受到切削刃的作用产生弹性变形,当最大应力超过工件的最大强度极限后,材料和基体发生分离形成切屑㊂图3所示为切削仿真中加工区域温度的变化㊂在切削过程中,第一切削区域内工件受到刀具的挤压产生较大的变形,单元格之间的扭曲变形十分严重,并且温度出现明显的升高;第二切削区域内受到加工时切屑变形的影响,温度在工件和刀具接触的位置出现最大值,若不进行冷却降温处理,会对硬质合金刀具的耐用性产生显著的影响;第三切削区域内刀具的后刀面和加工后的表面之间受到挤压和摩擦作用产生热㊃561㊃第4期吕娜:基于ABAQUS有限元仿真的硬质合金刀具磨损机制研究㊀㊀㊀量,导致温度升高㊂图3㊀工件和刀具温度仿真图4所示为车削仿真中刀具和工件应力的变化㊂工件在第一切削区域和第三切削区域内受到的应力处于较高的水平,在第二切削区域内的应力水平略低,此时在工件内部应力梯度的变换十分平缓,没有出现应力集中现象㊂相较于工件内部平稳的应力分布情况,此时在工具的切削刃和后刀面上应力较为集中,并且明显高于刀具其他位置的应力等级,在此位置将容易发生刀具磨损现象㊂图4㊀刀具和工件应力仿真图5所示为刀具受切削温度影响而产生的磨损㊂可以看出:在切削加工时虽然切屑温度较高,但热量并没有有效地转移到前刀面上,此时前刀面受到温度的影响较小;而切削刃和后刀面处由于与工件充分接触,加剧了切削刃的磨损程度㊂图5㊀刀具磨损和温度仿真图6所示为刀具受切削应力影响而产生的磨损㊂可以看出:切削刃处受到工件的挤压和划擦,表面应力集中现象十分明显并发生轻微的磨损,和切屑接触的前刀面位置虽然存在应力升高情况,但此时并没有造成刀具磨损㊂图6㊀刀具磨损和应力仿真2 车削实验为验证有限元仿真模型,设计了硬质合金刀具车削钛合金实验,如图7所示,使用高精密车床,工件材料为Ti6Al4V钛合金棒料㊂图7㊀车削加工实验实验前将棒料除去氧化层并加工至统一尺寸,实验过程中使用切削液对加工区域进行冷却和润滑,棒料车削长度和深度分别为50㊁2mm,控制每组实验过程中工件的车削体积为定值,车削实验参数和仿真参数保持一致,加工参数如表2所示,每次实验后更换新刀具进行下一组实验㊂表2㊀车削加工参数编号车削速度/(m㊃min-1)车削深度/mm进给量/(mm㊃r-1)1-760 1800.250.38-141200.15 0.450.315-211200.250.1 0.4㊀㊀实验结束后使用激光共聚焦显微镜对加工后的刀具形貌进行拍摄,并使用软件对后刀面的磨损长度进行测量㊂图8所示为硬质合金刀具车削加工后的表面磨损形貌㊂㊃661㊃机床与液压第49卷图8㊀硬质合金刀具磨损从图8(a)中可以看出:切削刃和后刀面位置的磨损量最大,距离切削刃的位置越远磨损量越小㊂这是由于车削加工时刀尖最先和工件接触,此时强度较低的刀尖承受较大的应力,造成以刀尖为中心的区域迅速磨损,因而形成突出的硬质点压入刀具材料基体内部,在摩擦的作用下对刀具表面进行刻划,形成犁沟状划痕㊂从图8(b)中可以明显观察到其他材料粘附在刀具表面,经超声清洗后黏接物仍无法有效去除;在刀具磨损平面存在一些不规则凹坑,说明加工过程中还存在着材料之间的粘接磨损㊂这是由于工件和刀具之间的相对速度较大,在强烈的摩擦和变形作用下导致温度升高,在工件材料导热率较低的情况下刀尖温度迅速升高进而达到工件的熔点,导致工件和刀具之间的原子相互吸引而结合在一起,形成粘接磨损㊂3㊀结果与分析通过对实验后刀具的磨损形貌进行观察,可以看出在不同的工艺参数条件下硬质合金刀具的磨损量具有显著的区别,使用后刀面的磨损长度作为磨损量的评价指标进行具体评价分析㊂(1)车削速度对刀具磨损的影响图9所示为不同车削速度条件下,实验和仿真后硬质合金刀具磨损长度的变化情况㊂可以看出:以车削速度为单因素变量的实验和仿真中,整体上看刀具的磨损长度和车削速度之间呈正相关㊂当车削速度处于较低水平时,刀具的磨损长度几乎没有太大增长,这是由于较低的车削速度产生的切削热较少,可以通过工件和切削液得到有效扩散,降低了刀具发生粘接磨损的概率㊂当车削速度增大后,由于切削区域的热量传递到刀具表面,导致刀尖位置温度升高,降低了硬质合金刀具的强度并且加剧了工件和刀具之间的粘接磨损情况㊂对比实验和仿真结果,可以得出实验和理论之间的平均误差为4 1%左右㊂(2)车削深度对刀具磨损的影响图10所示为不同车削深度条件下,实验和仿真后硬质合金刀具磨损长度的变化情况㊂可以看出:随着车削深度的增加,硬质合金刀具的磨损长度整体上呈现出逐渐降低的趋势㊂在车削深度较小时属于加工硬化层中切削,对刀具的磨损造成显著的影响;随着车削深度的增加,切削刃逐渐远离硬化层,刀具磨损量平稳降低㊂实验和理论之间的平均误差为5 6%左右㊂图9㊀刀具磨损长度和车削速度的关系㊀㊀图10㊀刀具磨损长度和车削深度的关系(3)进给量对刀具磨损的影响图11所示为不同进给量条件下,实验和仿真后硬质合金刀具磨损长度的变化情况㊂可以看出:随着进给量的增加,磨损长度呈现出先降低后升高的趋势㊂初期由于进给量的增加,避免了刀具在加工硬化图11㊀刀具磨损长度和进给量的关系层内对工件进行切削,随着刀具远离钛合金加工硬化层,硬质合金刀具磨损长度逐渐降低;之后进给量继续增加造成切削刃温度过高,减弱了刀具的强度,从而加剧了刀具的磨损㊂实验和理论之间的平均误差为5 7%左右㊂4㊀结束语本文作者首先通过ABAQUS软件建立了车削的仿真模型,从刀具的温度和应力角度分析了磨损机制,并进行了硬质合金刀具车削钛合金的实验,对理论模型进行了验证㊂主要得出以下几点结论:(1)在进行钛合金车削加工过程中,硬质合金刀具的磨损主要发生在刀尖和后刀面位置,磨损的基本方式为摩擦磨损和粘接磨损㊂(2)当车削速度在140mm/min以下时,刀具的磨损长度呈现出平稳波动的趋势,当车削速度大于140mm/min时,磨损长度出现急剧增加的趋势;随着车削深度的增加,刀具磨损长度整体上呈现逐渐降低的趋势,在使用硬质合金刀具车削钛合金时应使用较大的车削深度;随着进给量的增加,刀具的磨损长度出现先降低后增加的情况,当进给量达到0 2mm/r时,刀具磨损量最低㊂(3)通过对比实验和仿真模型的刀具磨损长度,可以得出两者之间的平均误差在6%以内㊂研究结果为刀具寿命预测以及切削参数的选取提供了参考㊂㊃761㊃第4期吕娜:基于ABAQUS有限元仿真的硬质合金刀具磨损机制研究㊀㊀㊀参考文献:[1]EZUGWUEO,BONNEYJ,YAMANEY.Anoverviewofthemachinabilityofaeroenginealloys[J].JournalofMate⁃rialsProcessingTechnology,2003,134(2):233-253.[2]赵民,张阔.金刚石铣刀切削石材磨损实验研究[J].机械设计与制造,2019(4):143-145.ZHAOM,ZHANGK.Experimentalstudyoncuttingstonewearofdiamondmillingcutters[J].MachineryDesign&Manufacture,2019(4):143-145.[3]邵维范.基于纳米流体冷却的钛合金车削温度场分析[J].金刚石与磨料磨具工程,2019,39(5):97-102.SHAOWF.Analysisofturningtemperaturefieldoftitani⁃umalloybasedonnanofluidcooling[J].Diamond&Abra⁃sivesEngineering,2019,39(5):97-102.[4]任梦羽,姜增辉,于海鸥.铣削方式对高速铣削TC4钛合金刀具磨损的影响[J].机械设计与制造,2015(7):77-79.RENMY,JIANGZH,YUHO.InfluenceontoolwearofmillingmodeinhighspeedmillingofTC4[J].MachineryDesign&Manufacture,2015(7):77-79.[5]周壮.纳米流体微量润滑钛合金切削刀具磨损研究[D].哈尔滨:哈尔滨工业大学,2018.ZHOUZ.Toolwearintitaniumalloyturningundernanoflu⁃idsminimumquantitylubracation[D].Harbin:HarbinIn⁃stituteofTechnology,2018.[6]张葭.304钢的涂层刀具切削性能和失效机理研究[D].西安:西安理工大学,2018.ZHANGJ.Studyoncuttingperformanceandfailuremecha⁃nismofcoatingtoosfor304steelcutting[D].Xi an:Xi anUniversityofTechnology,2018.[7]岳彩旭.模具钢硬态切削过程刀具磨损及表面淬火效应研究[D].哈尔滨:哈尔滨理工大学,2012.YUECX.Toolwearandsurfacequenchingmechanismforhardcuttingprocessofdiesteel[D].Harbin:HarbinUni⁃versityofScienceandTechnology,2012.[8]黄亮.模具钢金刚石切削时冷却润滑条件对刀具磨损影响的研究[D].哈尔滨:哈尔滨工业大学,2015.HUANGL.Researchontheinfluenceofcoolingandlubri⁃cationconditionsontoolwearindiamondcuttingofdiesteel[D].Harbin:HarbinInstituteofTechnology,2015.[9]宋海潮,冯晓梅,滕宏春,等.涂层硬质合金力高速铣削Crl2模具钢的破损失效分析[J].机床与液压,2010,38(20):10-11.SONGHC,FENGXM,TENGHC,etal.AnalyseontoolfracturemechanisminCr12millingwithcoatedcarbidetools[J].MachineTool&Hydraulics,2010,38(20):10-11.[10]XIY,BERMINGHAMM,WANGG,etal.FEAmodellingofcuttingforceandchipformationinthermallyassistedmachiningofTi6Al4Valloy[J].MaterialsScienceForum,2013,765:343-347.(责任编辑:张楠)(上接第182页)[10]BARBARINOS,SAAVEDRAFLORESEI,AJAJRM,etal.Areviewonshapememoryalloyswithapplicationstomorphingaircraft[J].SmartMaterialsandStructures,2014,23(6):063001.[11]MINOROWICZB,LEONETTIG,STEFANSKIF,etal.De⁃sign,modellingandcontrolofamicro⁃positioningactuatorbasedonmagneticshapememoryalloys[J].SmartMateri⁃alsandStructures,2016,25(7):075005.[12]ZHANGQX,FUQH,WANGLP,etal.Researchandexperimentalanalysisofdampingcharacteristicsofmag⁃neticshapememoryalloy[J].TransactionsonElectricalandElectronicMaterials,2018,19(4):272-278.[13]RICCARDIL,NASOD,JANOCHAH,etal.Apreciseposi⁃tioningactuatorbasedonfeedback⁃controlledmagneticshapememoryalloys[J].Mechatronics,2012,22(5):568-576.[14]涂福泉,毛阳,刘春雨,等.MSMA驱动器温控装置的设计与实现[J].材料导报,2013,27(24):140-143.TUFQ,MAOY,LIUCY,etal.Designandimplementa⁃tionoftheMSMAactuatortemperaturecontroldevice[J].MaterialsReview,2013,27(24):140-143.[15]LIKHACHEVAA,ULLAKKOK.Quantitativemodeloflargemagnetostraineffectinferromagneticshapememoryalloys[J].EPJDirect,2000,1(1):1-9.[16]施虎,何彬,汪政,等.磁控形状记忆合金驱动特性及其在液压阀驱动器中的应用分析[J].机械工程学报,2018,54(20):235-244.SHIH,HEB,WANGZ,etal.Magneto⁃mechanicalbehav⁃iorofmagneticshapememoryalloyanditsapplicationinhydraulicvalveactuator[J].JournalofMechanicalEngi⁃neering,2018,54(20):235-244.[17]JOKINENT,ULLAKKOK,SUORSAI.Magneticshapememorymaterials⁃newpossibilitiestocreateforceandmovementbymagneticfields[C]//ProceedingsofInter⁃nationalConferenceonElectricalMachines&Systems.Shenyang:IEEE,2001.[18]ZHANGAY,TUFQ,CHENKS,etal.AtypeofMSMAelectro⁃hydraulicservovalvebasedonneuralnetworkin⁃versesystemcontrol[C]//Proceedingsofthe32ndChi⁃neseControlConference.Xi an:IEEE,2013.[19]TUFQ,MAOY,XURB.Anewtypeelectrohydraulicservovalvebasedonmagneticshapememoryalloy[J].AdvancedMaterialsResearch,2013,873:91-94.[20]SARENA,SMITHAR,ULLAKKOK.Integratablemag⁃neticshapememorymicropumpforhigh⁃pressure,preci⁃sionmicrofluidicapplications[J].MicrofluidicsandNanofluidics,2018,22(4):38.(责任编辑:张楠)㊃861㊃机床与液压第49卷。
基于ABAQUS镜像铣削铝合金表面残余应力有限元分析
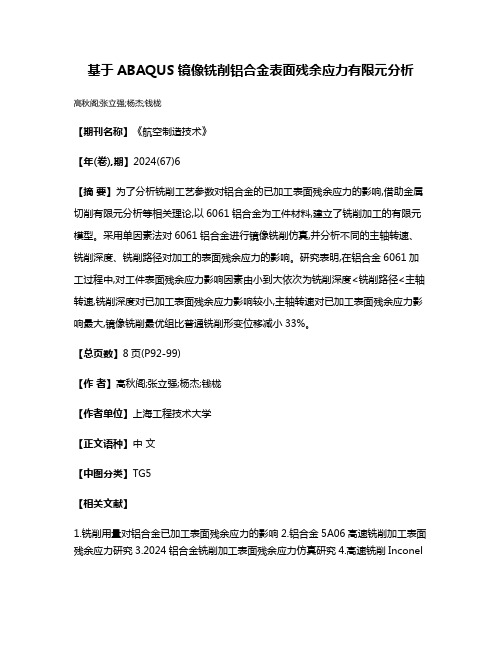
基于ABAQUS镜像铣削铝合金表面残余应力有限元分析高秋阁;张立强;杨杰;钱栊
【期刊名称】《航空制造技术》
【年(卷),期】2024(67)6
【摘要】为了分析铣削工艺参数对铝合金的已加工表面残余应力的影响,借助金属切削有限元分析等相关理论,以6061铝合金为工件材料,建立了铣削加工的有限元模型。
采用单因素法对6061铝合金进行镜像铣削仿真,并分析不同的主轴转速、铣削深度、铣削路径对加工的表面残余应力的影响。
研究表明,在铝合金6061加工过程中,对工件表面残余应力影响因素由小到大依次为铣削深度<铣削路径<主轴转速,铣削深度对已加工表面残余应力影响较小,主轴转速对已加工表面残余应力影响最大,镜像铣削最优组比普通铣削形变位移减小33%。
【总页数】8页(P92-99)
【作者】高秋阁;张立强;杨杰;钱栊
【作者单位】上海工程技术大学
【正文语种】中文
【中图分类】TG5
【相关文献】
1.铣削用量对铝合金已加工表面残余应力的影响
2.铝合金5A06高速铣削加工表面残余应力研究
3.2024铝合金铣削加工表面残余应力仿真研究
4.高速铣削Inconel
718已加工表面残余应力的有限元分析5.7075铝合金铣削残余应力及表面质量试验研究
因版权原因,仅展示原文概要,查看原文内容请购买。
基于ABAQUS的金属切削过程模拟
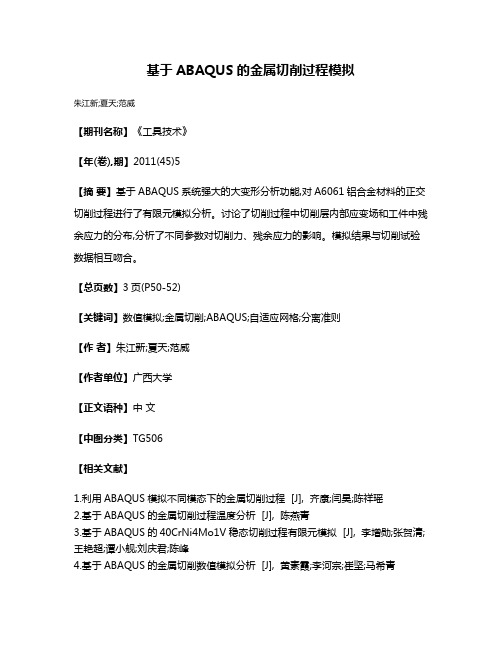
基于ABAQUS的金属切削过程模拟
朱江新;夏天;范威
【期刊名称】《工具技术》
【年(卷),期】2011(45)5
【摘要】基于ABAQUS系统强大的大变形分析功能,对A6061铝合金材料的正交切削过程进行了有限元模拟分析。
讨论了切削过程中切削层内部应变场和工件中残余应力的分布,分析了不同参数对切削力、残余应力的影响。
模拟结果与切削试验数据相互吻合。
【总页数】3页(P50-52)
【关键词】数值模拟;金属切削;ABAQUS;自适应网格;分离准则
【作者】朱江新;夏天;范威
【作者单位】广西大学
【正文语种】中文
【中图分类】TG506
【相关文献】
1.利用ABAQUS模拟不同模态下的金属切削过程 [J], 齐康;闫昊;陈祥瑶
2.基于ABAQUS的金属切削过程温度分析 [J], 陈燕青
3.基于ABAQUS的40CrNi4Mo1V稳态切削过程有限元模拟 [J], 李增勋;张贺清;王艳超;谭小舰;刘庆君;陈峰
4.基于ABAQUS的金属切削数值模拟分析 [J], 黄素霞;李河宗;崔坚;马希青
5.基于ABAQUS的金属切削过程中刀具温度场模拟研究 [J], 阳启华;杜茂华;蒋志涛
因版权原因,仅展示原文概要,查看原文内容请购买。
abaqus铝合金材料参数
abaqus铝合金材料参数【原创实用版】目录1.Abaqus 铝合金材料概述2.Abaqus 铝合金材料参数说明3.Abaqus 铝合金材料参数应用实例正文一、Abaqus 铝合金材料概述Abaqus 是一款广泛应用于工程领域的有限元分析软件,其强大的功能和便捷的操作赢得了许多工程师的青睐。
在 Abaqus 中,铝合金材料是一种常见的金属材料,具有良好的机械性能和耐腐蚀性能,广泛应用于航空航天、汽车制造等领域。
二、Abaqus 铝合金材料参数说明Abaqus 中铝合金材料的参数主要包括以下几类:1.材料属性:包括弹性模量、泊松比、密度等,这些参数决定了铝合金材料的基本力学性能。
2.应力 - 应变曲线:描述了铝合金材料在拉伸过程中的应力 - 应变关系,可以帮助工程师了解材料的变形能力和破坏强度。
3.硬化模型:Abaqus 提供了多种硬化模型,如线性硬化模型、非线性硬化模型等,用于描述铝合金材料在变形过程中的硬化行为。
4.失效准则:包括屈服准则、断裂准则等,用于判断铝合金材料在受力过程中是否会发生失效。
三、Abaqus 铝合金材料参数应用实例假设我们要分析一个由铝合金制成的飞机机翼结构,在 Abaqus 中,我们可以按照以下步骤设置铝合金材料参数:1.创建一个新的材料卡片,输入铝合金材料的弹性模量、泊松比、密度等基本属性。
2.创建一个应力 - 应变曲线,输入拉伸过程中的应力 - 应变数据。
3.选择合适的硬化模型,并根据实际需求调整模型参数。
4.设置失效准则,如选择屈服强度和断裂强度等。
完成以上设置后,我们就可以使用该铝合金材料参数对飞机机翼结构进行有限元分析,从而得到结构在不同受力条件下的应力、应变和变形情况,为结构设计提供参考依据。
针对铝合金材料仿真分析的Abaqus软件二次开发刘卉羽
针对铝合金材料仿真分析的Abaqus软件二次开发刘卉羽发布时间:2021-08-09T03:32:48.112Z 来源:《防护工程》2021年11期作者:刘卉羽付嘉宝张云鹏[导读] 随着仿真软件在机械加工领域的广泛应用,如何贴近实际加工的情况模拟的状态,成为未来亟待解决的问题,而Python语言为通用的仿真软件Abaqus的后台程序语言。
航空工业沈阳飞机工业(集团)有限公司辽宁沈阳 110850摘要:本文介绍了利用Abaqus仿真软件针铝合金材料的建模方法,为提高材料模型的构建效率,采用Python语言编制脚本文件,通过运行脚本程序自动构建材料模型,进而提高仿真分析效率。
关键词:Abaqus二次开发;仿真分析;铝合金0引言随着仿真软件在机械加工领域的广泛应用,如何贴近实际加工的情况模拟的状态,成为未来亟待解决的问题,而Python语言为通用的仿真软件Abaqus的后台程序语言。
本文利用Python脚本语言,针对Abaqus有限元仿真软件进行二次开发,实现模型高效构建。
1Abaqus仿真软件Abaqus是一款通用仿真分析软件,其广泛应用于机械、建筑、材料等领域,仿真分析技术可通过进行大量的仿真试验,来总结规律,而后以少量实际加工试验进行验证和修正,进而降低成本、缩短周期。
然而仿真分析将分析对象的几何模型导入Abaqus软件后,需通过设定其材料属性来赋予工件物理性能,这需要操作者在Abaqus软件的Material模块针对所研究的指定材料各力学、热力学等属性(根据分析内容有所不同),可能包括:材料密度、弹性模量、塑性、电导率等等,而仿真分析试验需要进行大量的建模工作,需要进行繁复的鼠标及键盘操作,每次建模都需要重复点选各材料属性。
其工作量较大且极为繁琐。
本文采用该软件的后台语言Python,通过编制脚本程序,并在构建材料模型时运行该程序,可迅速完成材料属性设定,并可通过调整脚本程序中各参数来修改材料属性。
abaqus切削模拟教程教育课件
GH4169为合金钢,将会 赋予给未撕裂的切屑和工件
Abaqus赋予材料属性
创建材料GH4169的参数:
3.点‘力学’、‘塑性’,选择‘与 温度有关的数据’,赋予数据
4.设置线膨胀系数,,点‘力学’‘膨胀’
5.设置热传导率,点‘热学’‘传导率’, 输入数据
Abaqus赋予材料属性
创建材料GH4169的参数:
5.点‘热学’‘非弹性热份额’
6.点‘热学’‘比热’,输入参数
Abaqus赋予材料属性
创建材料GH4169_FAIL的参数:
1.点 ,选GH4169,‘复制’, 命名‘GH4169_FAIL’
2.选‘GH4169_FAIL’,点‘编辑’‘力学’ ‘延性金属损伤’‘剪切损伤’,破坏机
制参数如下
3.点‘子选项’‘损伤演化’ ‘破坏位移参数’如下
定义元素集合:定义约束点和初始温度点的集合
.菜单工具中创造如下‘集’
3.ALL_2:定义刀具的初始温度
1.ENCASTRE(点):用于限制工件自由度
2.ALL1(点):用于定义工件初始温度
定义载荷幅度曲线: 工具‘幅值’,幅值 曲线如下
Abaqus定义边界条件和载荷
定义约束边界条件:
1.夹持工件:点
定义接触对: 总共有5对接触
1.点 ,选择接触的2个面‘CHIP_BOT’ ‘CHIP_TOP’,力学接触为罚接触 ,接 触属性为Initial_on
2,按相同方法,按实际接触 定义其他4对接触
3.定义刀具为刚性约束。在菜单中创建一个集合, 命名为‘TOOL_EL’,选择所有刀具网格后确定
Abaqus定义边界条件和载荷
常用操作:
对整个零件进 行自适应网格 对零件的每条边 分布种子
基于ABAQUS的高速切削铣削力的有限元分析与研究
车 、船 舶 、模 具 、航 空航天 等行 业 中 。
陪] ]㈤
式中, , , 为 等 效 塑 性应 变 , , , 为 等 效 塑 性 应 变 率, 为应 变 率参 量 ( 通 常为1 . 0 I s ) ,T 。 为参 考 温 度 ( 一般 取 室温 ),T 为 材料 的熔 点温 度 ,A 是初 始 屈服 应力 ( MP a ) ,B 是 硬化 模 量 ,c 是 依赖 于应 变 率 的 系
流动 应 力 。
式 中,
为失 效 的等 效 塑性 应 变 ,p , q 为无 量 纲 的
偏应 力 比值 ( p 为 压应 力 ,q 为米 塞 斯应 力 ),d l ~d 5 为 材料 失效 参数 。 J C 模 型 的 断裂 失效 模 型 中 ,当材 料 失效 参数 W 大 于 1 时 ,材 料 即为 失效 ,若在 所 有 积分 点 的材 料都 发 生 失
数 ( MP a ),n 是 加工 硬化 指数 ,m是热 软化 系数 ,其 中
目前 高速切 削在 加 工实 例和 加工 参数 上还 没 有完 整
的依据 ,且 由于 高速 切 削在 切屑 的形 态 、刀 具 的受力情
况 以及 刀具 的 失效形 式等 与传 统 的切 削完 全不 同,在 高 速切 削 中 刀具 的失效 形式 是 与加 工条 件和 工件 材料 相关
1 - 2 切 屑 分离准 则 公式( 1 ) 只 描 述 了切 削 加工 过 程 的流 动 应 力 , 只 是 涉及 材料 在这 一 过程 中 的塑性 变形 和 弹性变 形 阶段 。如 果想 要模 拟 断屑 的形 成 ,必须 要有 相应 的断裂准 则 , 以 判 断 材料 何 时从工 件本 体 上脱离 。本 文采 用 了J C 剪 切 失
- 1、下载文档前请自行甄别文档内容的完整性,平台不提供额外的编辑、内容补充、找答案等附加服务。
- 2、"仅部分预览"的文档,不可在线预览部分如存在完整性等问题,可反馈申请退款(可完整预览的文档不适用该条件!)。
- 3、如文档侵犯您的权益,请联系客服反馈,我们会尽快为您处理(人工客服工作时间:9:00-18:30)。
铝合金A357切削加工有限元模拟 1铝合金A357切削加工有限元模型金属切削加工有限元模拟,是一个非常复杂的过程。
这是因为实际生产中,影响加工精度、表面质量的因素很多,诸如:刀具的儿何参数、装夹条件、切削参数、切削路径等。
这些因素使模拟过程中相关技术的处理具有较高的难度。
本文建立的金属正交切削加工热力耦合有限元模型是基于以下的假设条件: (1)刀具是刚体且锋利,只考虑刀具的温度传导;(2)忽略加工过程中,由于温度变化引起的金相组织及其它的化学变化; (3)被加工对象的材料是各向同性的; (4)不考虑刀具、工件的振动;(5)由于刀具和工件的切削厚度方向上,切削工程中层厚不变,所以按平面应变来模拟;1.1材料模型1.1.1A357的Johnson-Cook 本构模型材料本构模型用来描述材料的力学性质,表征材料变形过程中的动态响应。
在材料微观组织结构一定的情况下,流动应力受到变形程度、变形速度、及变形温度等因素的影响非常显著。
这些因素的任何变化都会引起流动应力较大的变动。
因此材料本构模型一般表示为流动应力与应变、应变率、温度等变形参数之间的数学函数关系。
建立材料本构模型,无论是在制定合理的加工工艺方面,还是在金属塑性变形理论的研究方面都是极其重要的。
在以塑性有限元为代表的现代塑性加工力学中,材料的流动应力作为输入时的重要参数,其精确度也是提高理论分析可靠度的关键。
在本课题研究中,材料本构模型是切削加工数值模拟的必要前提,是预测零件铣削加工变形的重要基础,只有建立了大变形情况下随应变率和温度变化的应力应变关系,才能够准确描述材料在切削加工过程的塑性变形规律,继而才能在确定的边界条件和切削载荷下预测零件的变形大小及趋势。
在切削过程中,工件在高温、大应变下发生弹塑性变形,被切削材料在刀具的作用下变成切屑时的时间很短,而且被切削层中各处的应变、应变速率和温度并不均匀分布且梯度变化很大。
因此能反映出应变、应变速率、温度对材料的流动应力影响的本构方程,在切削仿真中极其关键。
当前常用的塑性材料本构模型主要有:Bodner-Paton 、Follansbee-Kocks 、Johnson-Cook 、 Zerrilli-Armstrong 等模型,而只有Johnson-Cook 模型描述材料高应变速率下热粘塑性变形行为。
Johnson —Cook 模型认为材料在高应变速率下表现为应变硬化、应变速率硬化和热软化效应,Johnson —Cook 模型如下所示:01ln 1m n r m r T T A B c T T εσεε∙∙⎡⎤⎛⎫⎡⎤⎛⎫-⎢⎥ ⎪⎡⎤⎢⎥=++- ⎪⎣⎦⎢⎥ ⎪-⎢⎥⎝⎭⎣⎦⎝⎭⎣⎦ 式中第一项描述了材料的应变强化效应,第二项反映了流动应力随对数应变速率增加的关系,第三项反映了流动应力随温度升高指数降低的关系。
o ε∙、Tr 分别表示参考应变速率和参考温度,Tm 为材料熔点。
式中A 、B 、n 、C 、m 、D 、k 是7 个待定参数;A 、B 、n 表征材料应变强化项系数;C 表征材料应变速率强化项系数;m 表征材料热软化系数;t θ,m θ分别为常温材料熔点。
1.1.2材料失效准则实现切屑从工件分离,本文采用的是剪切失效模型。
剪切失效模型是基于等效塑性应变在积分点的值,当损伤参数达到1时,单元即失效,失效参数定义如下:0pl plplfεεωε---+∑∆=式中:ω为失效参数,0plε-为等效塑性应变初始值,plε-∆为等效塑性应变增量,pl fε-为失效应变。
失效应变0plε-设定以来于以下几个方面:依据塑性应变率,无量纲压应力与偏应力之比p/q(p 为压应力,q 为Mises 应力),温度,预定义域变量。
这里采用Johnson —Cook 模型定义失效应变。
pl f ε-=12345exp 1ln 1pl o p d d d d d q εθε∙-Λ∙⎡⎤⎛⎫⎢⎥ ⎪⎡⎤⎛⎫⎛⎫⎢⎥ ⎪+++ ⎪⎢⎥ ⎪⎝⎭⎢⎥ ⎪⎝⎭⎣⎦ ⎪⎢⎥⎝⎭⎣⎦式中:1d —5d 为低于转变温度的条件下测得的实效常数。
o ε∙为参考应变率, pl ε∙-为塑性应变率。
θΛ由下式确定:0()/()1transition transiton melt transition transition melt melt for for for θθθθθθθθθθθ⎧⎪--≤≤⎨⎪⎩θ是当前温度,melt θ是熔点,transition θ是室温。
下图描述了材料在遭受破坏时的应力应变的特征。
各向同性强化弹塑性材料的破坏有两种形式:屈服应力的软化和弹性的退化,图1.1中实线代表了材料已经破坏的应力应变的响应,而虚线是当破坏不存在的时候的应力应变响应。
图1.1累进损伤退化应力应变图1.1中yo σ和0plε为材料开始损伤时的屈服应力和等效塑性应变。
plf ε是材料失效时即图中D=1时的等效塑性应变。
材料失效时的等效塑性应变plf ε依赖于单元的特征长度,不能作为描述材料损伤演化的准则。
相反,材料损伤演化的准则又等效塑性位移plu 或者断裂耗散能量f G 决定。
当材料开始损伤破坏时,应力应变曲线已经不能准确的描述材料的行为。
继续应用该应力应变曲线会导致应变集中,变化过于依赖建模时所画的网格,以致当网格变密后耗散能量反而降低。
Hillerborg 能量失效法被提出用应力位移响应曲线来表征破坏过程减少了分析对网格的依赖性。
利用脆性断裂概念定义一个使单元破坏的能量Gf 作为材料的参数。
通过这种方法,损伤开始的软化效应是一种应力位移响应而不是应力应变响应。
破坏能量有下式表示:f G plplf fplplu ply y oL d du εεσεσ==⎰⎰ (2.12)表达式中的plu 为等效塑性位移,它描述了当损伤开始之后裂纹变化的屈服应力,在损伤开始之前plu =0.在损伤开始之后plu =L plε,L 为与积分点相关的单元特征长度,单元特征长度的定义基于单元的集合形状,平面单元长度为积分点区域面积的平方根,而立方体单元长度为积分点区域体积的立方根。
基于有效塑性位移定义损伤演化用Linear 方法定义即如下图所示:图错误!文档中没有指定样式的文字。
.2线性损伤演化pl pl pl plf fL u d u u ε∙==该准则使有效塑性位移达到pl u =plf u时,材料的刚度完全丧失,模型的失效网格被自动删除,也就是材料此时发生断裂,切屑开始形成错误!未找到引用源。
1.1.3 A357与刀具材料参数A357铝合金,密度ρ=2680Kg/m3,弹性模量E=79GP ,泊松比μ=0.33其他参数如下表:表1.1 A357的化学成分合金 AL Si Mg Ti Mn Be Fe A357(%)基体6.5~7.00.55~0.600.1~0.20.1~0.04~0.07≤0.080.2表1.2 A357热导率θ,K300 400 500 600 700 800 λ,W/(m.℃)18192020.621.622.2表1.3 A357比热容θ,K300 400 500 600 700 800 C ,J/(Kg K )253.0259.0265.2271.6278.1285.4表1.4 A357线膨胀系数θ,K300 400 500 600 700 800α,10-6K14.2614.7815.3115.8516.4317.06表1.5 A357 Johnson-Cook 模型材料参数材料 A (Mpa ) B (Mpa ) n c m A357370.41798.70.733150.01281.5282刀具使用的是硬质合金,密度ρ=15000Kg/m3,弹性模量E=210GP ,泊松比μ=0.22其其它参数如下表:表1.5 刀具材料参数杨氏模量泊松比(Mpa )线膨胀系数(m/m.℃)比热(J/kg. ℃)导热率(W/m.k)8E+110.224.7E-62004.6E11.2摩擦模型金属切削过程中,刀具前刀面的摩擦状态非常复杂,通常把前刀面得摩擦区分为粘结区和滑动区,粘结区的摩擦状态与材料的临界剪应力有关,滑动区可近似认为摩擦系数为常值可以用下式来表示: c n s min τμστ=(,)(2.14)式中:c τ为接触面的滑动剪切应力;μ为摩擦系数;n σ为接触面上的压力;s τ为材料的临界屈服压力。
1.2.1质量放大质量放大可以在不人为的提高加载速率的情况下缩短计算时间。
对于含有率相关材料或率相关阻尼的问题,由于材料的应变率与加载速率成正比,所以不能以提高加载速率的方法来减少计算成本,只能用质量放大的方法。
稳定时间增量的表达式如下:e edLtC∆===式中,e L为特征单元长度,d C为材料的膨胀波速,E为材料的弹性模量,ρ为材料的泊松比。
从式中可以看出将材料密度增加2n倍,则材料波速就会下降n倍,从而将稳定时间增加量提高n倍。
当全局的稳定极限增加时,进行同样的分许所需要的增量步就会减少,所需的计算时间也会相应减少,这就是质量放大的目的。
本次模拟中E=79000000pa, ρ=2680kg/m3 e L=0.00001m 所以增量步时间要取5.8E-8 s 只有按这个数值计算才是准确的,所以一个计算事例会话费很多时间。
但是人为的提高加载速率和放大质量对模型具有相同的影响,即会提高模型的惯性力,使动态效果增加。
因此无论是人为的增加加载速率还是用质量放大都是有一定的限度的,过大的质量放大系数和过度提高加载速率都有可能导致错误的结果。
在实际的模拟过程中,如何确定一个合理的放大系数或者一个合理的加载速率是非常重要的问题,这在很大程度上依赖于分析者的经验。
由于切削仿真是一个比较复杂,单元量较大且是三维六面体单元,同时计算时间比较长,所以计算量比较大。
在这里我们通过大量的对比分析,采用适当的质量放大系数,保证计算结果精确度的同时尽可能的加快计算速度。
2 abaqus商用仿真软件中限元模型建立2.1建立部件(本文采用的统一单位:N, Pa, m, s, K, J 软件版本:6.8-1)(K是华氏温度室温的20°C就是297K)1.启动ABAQUS,选择主菜单中的Part选项,选择下拉菜单,单击Create,如图2-1-1所示。
图2-1-12.创建未变形切屑模型。
(就是切削下来的0.1mm即0.0001m的切削层)在弹出的对话框中,设定模型的名称为CHIP,在建模空间选项中选择2DPlanar.类型选择Deformable,基本特征选择Shell,近似尺寸选择。
0.01m。
点击Continue进入绘制草图步骤。
图2-1-2在随后出现的草图绘制模块中,按照图2-1-3所示的尺寸建立一个平面图;(图中100E-6m就是你要求的初始分析的切削厚度0.1mm即0.0001m)去切削长度为2E-3m(如果建立15mm的模型就会很大,对加工精度没有太大作用,反而影响计算时间)图2-1-3点击Done完成上面的未变形切削模型的绘制。