304不锈钢连铸坯表面缺陷分析
精密铸造304不锈钢铸件黑点缺陷的解决措施

精密铸造304不锈钢铸件黑点缺陷的解决措施徐州市热卡铸造材料有限公司张云郑申涛一、综述熔模精密铸造不锈钢典型的材质是304,也就是1Cr19Ni9Ti,通常的金相组织是奥氏体,机械加工后铸件表面会出现小黑点而导致铸件成批报废,耽误交期不说,订单甚至客户会因此丢失,根据黑点的形态我们把黑点分为两类,一类是不规则黑点,另一是形态接近圆形(扫描断面是圆形,铸件中的形态是球状)的规则黑点,这类黑点较多特别是抛光后清晰可见,焊补几乎不可能,有的客户要求不允许焊补,一旦发现焊补立刻终止合同。
以下具体分析黑点的成因和解决措施,欢迎批评指正。
二、不锈钢黑点的成因根据对黑点成分取样分析得知,无论是不规则黑点还是规则黑点缺陷,都有氧元素的踪迹,其他成分包括碳、锰、硅、铬等。
碳的来源很少,所加入的不锈钢原料和合金没有碳,唯一的可能是脱蜡不干净所致,蜡料高温碳化粘附在型壳上,浇注后和氧、硅等元素结合形成复杂的碳化物或者多元氧化物夹杂。
生产实践中,不规则的黑点多发生在靠近浇冒口附近,这是因为氧化夹渣颗粒小比重小容易上浮。
这部分黑点的解决办法能够肯定是完善脱蜡工艺,不利于脱蜡的铸件可以设置脱蜡孔,另外保证脱蜡的温度压力时间严格按照工艺文件执行,应该都能得到顺利解决。
另一部分圆形的黑点的成因可以进行如下判断,首先是脱氧失败或者效果不彻底,大量游离的氧和钢液中的锰硅元素(可能来自铁合金也可能来自炉衬或者除渣剂)还有其他元素比如铬等形成多元的复杂的氧化夹渣,由于圆形应该说是球状体表面能最小,所以形成大量的球状氧化物颗粒,由于时间或者钢液粘度的影响未来得及上浮到液面,含有球状氧化物夹渣的钢水浇注后凝固成铸件从而形成黑点缺陷。
对于圆形的黑点缺陷这里多说几句,首先硅、锰、铬等元素是必须出现在钢液中,有的是合金有的竟然是为了脱氧加入的,而除渣剂中的各种成分复杂而多样化,又不可能不加除渣剂。
三、不锈钢黑点解决措施以下脱氧熔炼工艺经过现场测试和多家工厂使用,是一种效果好成本低的成熟工艺,特别对于304、316不锈钢黑点的解决效果非常明显,建议推广使用。
铸坯表面缺陷成因及对策

总热阻RT可表示为:
RT=R1+R2+R3+R4+R5+R6
R1:钢水-坯壳间的热阻, cm2℃/W 。
R2:通过坯壳的热阻, cm2℃/W ;
R3:通过保护渣膜的热阻, cm2℃/W ;
R4:通过气隙的热阻, cm2℃/W ;
R5:通过结晶器铜板的热阻, cm2℃/W ;
R6:结晶器壁-冷却水间的热阻,cm2℃/W;
t=0,0 x x1, Tp=Tp0
(3)
t=0, x1 x x2, Ts=Ts0
(4)
t 0, x=0, Tp=f(t)
(5)
0 t t1,x=x1,Ts=Tp
ks(s/x)=kp(p/x)
(6)
t1 t,x=x1,
ks(s/x)=kp(p/x)
= ((Ts/100)4- Tp/100)4)+h(Ts-Tp) (7)
22
纵裂纹在铸坯表面凹陷处形成
漏钢遗留坯壳厚度沿宽度方向的变化
23
铸坯纵裂纹长度与深度的对应关系
24
铸坯表层缺陷示意图
25
纵裂纹是在结晶器内产生的
纵裂纹开口表面光滑, 呈沿柱状晶低熔点晶界 开裂迹象。
粗大纵裂纹表面附近断口照片
裂纹开口表面覆盖有 液态保护渣膜。
26
粗大纵裂纹距表面一定距离处断口
凝固坯壳厚度的不均匀性与碳含量的关系 43
不均匀凝固随冷却速率的增加而提高
住友金属杉谷泰夫等的实验:
铁と钢,67(1981),1508
44
杉谷实验得到的不同冷却速率下坯壳形貌
45
不同厚度钢板侧凝固坯壳的照片
46
坯壳不均匀与凝固速率的关系
凝固定律: d=kt1/2
304不锈钢精密铸造件加工外观缺陷的分析与改善

304不锈钢精密铸造件加工外观缺陷的分析与改善摘要:本文主要介绍了304不锈钢精密铸造件(以下简称精铸件)加工过程中暗花缺陷的原因分析及改善过程,因不锈钢精铸件的加工在行业内较为普通,且加工工艺较为特殊,因此希望本文有一定的推广及借鉴作用。
关键词:不锈钢;精密铸造;加工;外观缺陷本文所讲的精密铸造是熔模精密铸造,它是精密铸造的工艺方法之一。
是采用失蜡法制壳,利用废钢加合金的方式浇注成铸件,再通过机械加工等工序制作成符合客户要求的精密零件,是一种历史悠久的传统制造业,是工业门类中的基础行业之一。
304不锈钢为奥氏体不锈钢,熔炼浇注及机械加工是此类零件的关键质量控制点,品质问题轻则耽误订单交期,重则损失客户丢失市场。
因此,相关品质问题的改善就显得尤为重要。
1、缺陷概述本公司生产的一种材质为304的不锈钢精铸件,车加工后零件表面出现了大面积的白色暗花(见图1)不良率28%左右,形状、大小、位置不定,经擦拭、水洗、超声波清洗等表面处理后,缺陷仍无法消除掉。
精刀返车后暗花变淡但却未完全消失,初步判断该缺陷产生的原因是数控车加工工艺设置不当。
随后将车加工工序拆分为粗车和精车,同时提高转速,减少车削量。
经试加工后发现暗花缺陷无明显好转,结果表明车加工工艺的调整对零件表面暗花的改善收效甚微,不是暗花产生的根本原因。
零件表面暗花左图的局部放大图图12、缺陷分析为了进一步分析缺陷的产生原因,从宏观角度,安排专人对本批次零件的生产过程进行倒查,核查过程中未发现异常情况。
继而从微观角度,用电子显微镜对零件的暗花缺陷展开进一步的分析,发现暗花区域相对于正常区域来说,零件的走刀路径模糊杂乱,局部棱线崩缺且有类似粘刀的异物附着(见图2)。
通过缺陷区域的放大分析得知,暗花缺陷更像是铸件本身的组织缺陷。
参考上述检测结果,为了进一步对零件的内部组织进行分析,以查明暗花缺陷的根本原因,我们对零件暗花缺陷部位进行线割截取,交品质部制样后分别在200倍、500倍和1000倍的显微镜下进行金相检验,通过图3的金相图片可以看出,碳化物在奥氏体晶界上无规则的大量聚集,粗大且成网状分布。
连铸坯表面质量缺陷及处理措施

连铸坯表面质量缺陷及处理措施【摘要】对于连铸板坯而言,振痕和裂纹是其主要的质量缺陷问题。
虽然这个缺陷在大多数情况下对连铸坯的质量影响不大,但是如果不及时有效的处理调还会带来很多附加的质量问题。
尤其是在生产不锈钢和高强度钢品种时,这种质量缺陷所带来的弊端更加明显。
【关键词】连铸坯;振痕;质量影响1振痕形成机理在连铸坯生产中,振痕和裂纹是两种最为常见的质量缺陷问题,主要是由于弯月面顶端溢流造成的,该缺陷形成以后会附带其他质量缺陷一并产生。
2振痕对铸坯质量的影响振痕对连铸坯的质量影响会导致后期出现列裂纹,包括横裂纹、角部横裂纹及矫直裂纹。
如果连铸坯内掺杂的杂质较多,会导致大规模网状裂纹的出现,甚至出现穿钢现象。
如果在连铸坯出现振痕的地方晶粒很大,就会产生晶间裂纹现象,在这样的情况下需要对连铸坯修磨,从而提高成材率。
3影响振痕深度的因素振动参数对振痕形状和深度有重要影响。
其中振幅、频率、负滑脱时间及振动方式最为重要;结晶器保护渣的耗量、粘度、保温性能及表面性能等有着重要影响;.钢的凝固特性对振痕有着重要影响,特别是当钢中碳含量和钢中Ni/Cr 比影响最突出。
当钢中碳含量为0.1%左右,Ni/Cr≈0.55左右,铸坯表面振痕最深。
4减少振痕深度的措施采用小振幅(s)、高频率(f)及减少负滑脱时间(tN),可以有效的减少振痕的深度;采用非正弦振动方式可以减少振痕的深度,这是因为非正弦振动其负滑脱时间tN比正弦振动短;采用渣耗量低,粘度高的保护渣,可以使振痕深度变浅。
采用保温性能好和能增加弯月面半径的保护渣可以减少振痕深度;提高不锈钢、钢液的过热度,尤其是含钛和含铝的不锈钢对减少该钢表面振痕深度是有效的。
提高结晶器进出冷却水的温差,对减少振痕深度是有利的。
5铸坯表面裂纹5.1表面纵裂纹铸坯表面纵裂纹是铸坯最主要表面缺陷,对铸坯质量影响极大,特别是板坯和圆坯最为突出,报废量和整修量很大。
5.1.1纵裂纹类型铸坯表面沟槽纵裂纹。
连铸坯表面裂纹缺陷分析

《 中国重型装备》
C I A H A Y E UP N H N E V Q I ME T
从 图 4可 以看 出 , 轧 态 、 火 态 和 调 质 态 热 正 6 S2 n钢 8 0C亚温 淬 火 的 转 变 产物 为 马 氏体 0 iM 0 ̄
体延 伸形成 的三 角 区部 位 晶粒 明显要 比裂 纹的 另 侧 晶粒要 细 , 纹两侧 组织 不 同 , 明裂纹 两侧 裂 说
一
端存 在沿 奥 氏体 晶界 向基体 延 伸 的 现象 , 明横 说
裂是 沿 晶开裂 , 钢水 结 晶成 固体 以后 产生 的 , 是 是
一
形成 组织 的温度不 同。三角 区部位 晶粒 细说 明该
钢亚 温淬火 后韧性 好 、 度高 的原 因之一 。 强
双相合 金 中双 相 的形 态对 试样 的力学性 能有
影响 , 主要表 现 在 对 裂纹 扩 展 的 阻碍 作 用 上 。当
铁 素体 呈针状 时 , 氏体 被铁 素 体 最 大限 度 的分 马 开 , 裂纹 的扩展 不仅 通过 马氏体 , 故 还必然 通过 铁 素体 。铁素 体在 断裂前会 产生 大量 塑性变形 而 消
若铁 素体呈 块状 形 态 时 , 则裂 纹 容 易 只沿 着 马 氏 体基 体扩展 , 而不 与孤立 的铁 素体相 遇 , 从而 使试 样 的韧性变 差 。另外 , 素体 呈针状 、 氏体 为细 铁 马
小板条 状时 , 晶界 总面积 较块状 时要 大 的多 , 也有 利 于力学性 能 的提 高 。针状组 织 比颗 粒状组 织细 小 , 材料变 形 和断 裂 的过 程 中能 吸收 更 多 的能 在
耗较 多 能量 , 而 对 裂 纹 的 扩 展 起 到 阻碍 作 用 。 从
连铸表面质量凹陷等

1前言新日铁光制铁所在板坯连铸机上进行了奥氏体304不锈钢等钢种连铸技术的开发,现在月产量达3万吨以上。
最近进行了提高铸坯表层质量技术的开发,从而可实现铸坯的无清理化并降低生产成本。
本文概要介绍了此铸坯的无清理化技术,还提出了今后的开发方向。
2钢板表面的重皮缺陷及其产生机理奥氏体304不锈钢连铸坯(简称板坯或铸坯)经热轧、冷轧后,在钢板表层产生了重皮缺陷。
现调查了此重皮缺陷和板坯表层的特征,推定了缺陷的产生机理。
2.1钢板重皮缺陷与板坯表层的关系钢板重皮缺陷多发生在距边缘300mm的范围内。
作为与此缺陷位置对应的板坯形状和表层部的特征,在板坯宽面侧边缘附近发现了凹陷部,在窄面侧发现了凸型膨胀,在凹陷部周围的振痕(oscillation mark以下简称OSM)较深。
因此,铸坯宽面侧表层不平滑就成了重皮缺陷的产生原因。
用砂轮机研磨板坯表层至平滑再冷轧成钢板时,即能抑制重皮的产生,这就验证了此推定的正确性。
2.2 板坯表层的实态为了查明板坯宽面侧的表面凹陷形状,采用粘度为0.08Pa·S的原来保护渣A进行连铸,结果查明在距窄面侧端部约lOOmm处存在实测深度0.5—3.Omm、平均深度2mm 的凹陷振痕。
另外,在铸坯宽面侧调查采用原来保护渣A连铸结果表明,在宽面侧中心部距端面500mm处的OSM进一步深到了大约500pm。
由在板坯宽面的凹陷四周所产生的OSM纵断面图可知:在OSM深度500—600μm 时,Ni正偏析长度约为200μm左右。
而且该部位S的浓度也增大了,还产生了裂纹(铸坯壳强度小所致)。
当OSM深度达300μm以上时,该沟部温度上升,强度则低到1kg/mm2以下。
2.3重皮缺陷产生机理和防止措施在前述的板坯表面实态的基础上,推测了其表层重皮缺陷产生的机理。
(1)热轧时凹陷部产生的裂纹窄面侧的结晶器锥度不足,造成结晶器散热不充分,铸坯壳强度小,致使窄面凸型膨胀。
另一方面,由于窄面与宽面交界的棱边从两面散热,故强度较高,即使窄面凸型膨胀,棱边仍可保持直角,在宽面凝固壳附近产生了凹陷部。
连铸板坯缺陷图谱及产生的原因分析(新)

第二篇连铸板坯缺陷(AA)第二篇连铸板坯缺陷(AA) (1)2.1表面纵向裂纹(AA01) (4)2.2表面横裂纹(AA02) (6)2.3星状裂纹(AA03) (7)2.4角部横裂纹(AA04) (8)2.5角部纵裂纹(AA05) (10)2.6气孔(AA06) (11)2.7结疤(AA07) (12)2.8表面夹渣(AA08) (13)2.9划伤(AA09) (14)2.10接痕(AA13) (15)2.11鼓肚(AA11) (16)2.12脱方(AA10) (17)2.13弯曲(AA12) (18)2.14凹陷(AA14) (19)2.15镰刀弯(AA15) (20)2.16锥形(AA16) (21)2.17中心线裂纹(AA17) (22)2.18中心疏松(AA18) (23)2.19三角区裂纹(AA19) (25)2.20中心偏析(AA20) (27)2.21中间裂纹(AA21) (28)2.1表面纵向裂纹(AA01)图2-1-11、缺陷特征表面纵向裂纹沿浇注方向分布在连铸板坯上下表面,裂纹深度一般为2mm~15mm,裂纹部位伴有轻微凹陷。
在连铸浇注过程中,当连铸板坯坯壳在结晶器内所受到的应力超过了坯壳所能承受的抗拉强度时,即产生表面纵向裂纹。
表面纵向裂纹缺陷在结晶器内产生,出结晶器后若二次冷却不良,裂纹将进一步加剧。
2、产生原因及危害产生原因:①钢中碳含量处于裂纹敏感区内;②结晶器钢水液面异常波动。
当结晶器钢水液面波动超过10mm时,表面纵向裂纹缺陷易于产生;③结晶器保护渣性能不良。
保护渣液渣层过厚、过薄或渣膜厚薄不均,使连铸板坯凝固壳局部过薄而产生表面纵向裂纹;④中间包浸入式水口与结晶器对中不良,钢水产生偏流冲刷连铸板坯凝固壳,而产生表面纵向裂纹。
危害:轻微的表面纵裂纹经火焰清理后均能消除;表面纵向裂纹严重时可能会造成漏钢;表面纵向裂纹若送热轧进行轧制可能导致热轧产品出现分层、开裂缺陷。
连铸坯缺陷及对策
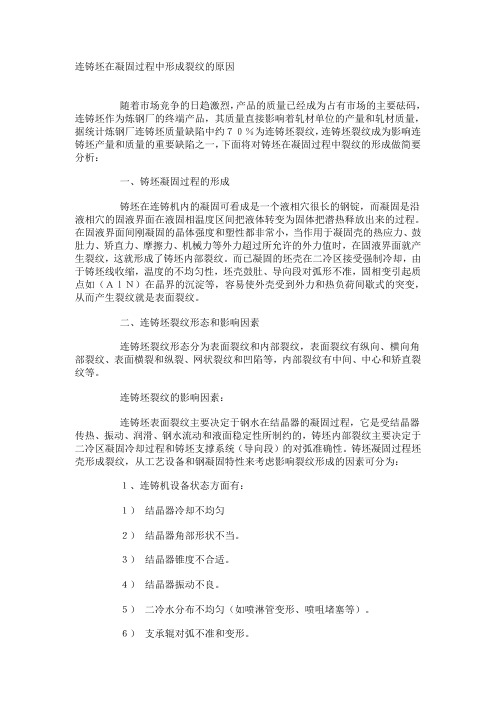
连铸坯在凝固过程中形成裂纹的原因随着市场竞争的日趋激烈,产品的质量已经成为占有市场的主要砝码,连铸坯作为炼钢厂的终端产品,其质量直接影响着轧材单位的产量和轧材质量,据统计炼钢厂连铸坯质量缺陷中约70%为连铸坯裂纹,连铸坯裂纹成为影响连铸坯产量和质量的重要缺陷之一,下面将对铸坯在凝固过程中裂纹的形成做简要分析:一、铸坯凝固过程的形成铸坯在连铸机内的凝固可看成是一个液相穴很长的钢锭,而凝固是沿液相穴的固液界面在液固相温度区间把液体转变为固体把潜热释放出来的过程。
在固液界面间刚凝固的晶体强度和塑性都非常小,当作用于凝固壳的热应力、鼓肚力、矫直力、摩擦力、机械力等外力超过所允许的外力值时,在固液界面就产生裂纹,这就形成了铸坯内部裂纹。
而已凝固的坯壳在二冷区接受强制冷却,由于铸坯线收缩,温度的不均匀性,坯壳鼓肚、导向段对弧形不准,固相变引起质点如(AlN)在晶界的沉淀等,容易使外壳受到外力和热负荷间歇式的突变,从而产生裂纹就是表面裂纹。
二、连铸坯裂纹形态和影响因素连铸坯裂纹形态分为表面裂纹和内部裂纹,表面裂纹有纵向、横向角部裂纹、表面横裂和纵裂、网状裂纹和凹陷等,内部裂纹有中间、中心和矫直裂纹等。
连铸坯裂纹的影响因素:连铸坯表面裂纹主要决定于钢水在结晶器的凝固过程,它是受结晶器传热、振动、润滑、钢水流动和液面稳定性所制约的,铸坯内部裂纹主要决定于二冷区凝固冷却过程和铸坯支撑系统(导向段)的对弧准确性。
铸坯凝固过程坯壳形成裂纹,从工艺设备和钢凝固特性来考虑影响裂纹形成的因素可分为:1、连铸机设备状态方面有:1)结晶器冷却不均匀2)结晶器角部形状不当。
3)结晶器锥度不合适。
4)结晶器振动不良。
5)二冷水分布不均匀(如喷淋管变形、喷咀堵塞等)。
6)支承辊对弧不准和变形。
2、工艺参数控制方面有:1)化学成份控制不良(如C、Mn/S)。
2)钢水过热度高。
3)结晶器液面波动太大。
4)保护渣性能不良。
5)水口扩径。
6)二次冷却水分配不良,铸坯表面温度回升过大。
- 1、下载文档前请自行甄别文档内容的完整性,平台不提供额外的编辑、内容补充、找答案等附加服务。
- 2、"仅部分预览"的文档,不可在线预览部分如存在完整性等问题,可反馈申请退款(可完整预览的文档不适用该条件!)。
- 3、如文档侵犯您的权益,请联系客服反馈,我们会尽快为您处理(人工客服工作时间:9:00-18:30)。
304不锈钢连铸坯表面缺陷分析摘要:本文对304不锈钢连铸坯进行了解剖分析。
在25%的铸坯深振痕或渣坑缺陷试样中观察到了微裂纹或气孔。
关键词:304不锈钢,连铸板坯,表面缺陷Investigation on Surface Defects of 304 Stainless Steel SlabAbstract: This paper dissected 304 stainless steel slabs. In 25 percents of samples, small cracks or pinholes can be observed under deep oscillation marks or slag hollows.Key Words: 304 stainless steel, slab, surface defect在不锈钢生产,特别是不锈钢冷轧产品生产中,产品的表面质量控制非常重要。
众所周知,钢中非金属夹杂物是冷轧产品表面质量最重要的影响因素之一。
我公司在几十年的不锈钢生产中,对钢中非夹杂物的控制做了大量研究和改进工作。
特别是自2004年开始,随着我公司不锈钢产量的迅猛增长和大量不锈钢新品种的开发,质量提升成为提高产品竞争力、扩大市场占有率的关键环节。
其中,钢质洁净度研究成为重点关注课题,开展了大量试验研究和工艺攻关[1-3],产品质量得到了明显提升,对我公司不锈钢产品顺利进入钟表、高档装饰面板、高档水槽等行业起到了有力的支撑和推动作用。
近年来,我公司不锈钢钢质洁净度得到大幅提高,产品质量已较为稳定,但目前在奥氏体不锈钢冷轧产品生产中仍存在0.4%左右的“夹杂”废品,且在某些时间内“夹杂”废品的比例会上升到1%以上。
随着各项研究工作的逐步推进和深入,我们发现这些冷轧产品“夹杂”缺陷并非都是由非金属夹杂物造成的。
在奥氏体不锈钢连铸生产过程中,连铸板坯的表面质量不仅会严重影响连铸坯修磨率,从而影响全线产品成材率,而且会严重影响冷轧产品表面质量。
其中一些连铸坯表面和皮下缺陷在轧材表面会形成形貌类似“夹杂”的缺陷。
这些连铸坯表面缺陷的形成与钢种特性、结晶器保护渣物性、结晶器冷却条件、结晶器振动参数等因素有着直接关系。
本文未对奥氏体不锈钢连铸板坯表面缺陷的形成原因及解决措施进行论述。
本文选取奥氏体不锈钢中产量最大的304不锈钢,对其连铸板坯表面凹坑、振痕紊乱等缺陷进行了解剖分析。
目的是提高我们对连铸坯表面缺陷的认识,为深入研究其产生原因起到铺垫作用。
1.奥氏体不锈钢连铸板坯表面缺陷形貌特征及分布在奥氏体不锈钢连铸板坯表面存在多种缺陷。
部分连铸板坯宽面靠近两边部的区域存在局部纵向凹陷,少量连铸坯宽面中部也存在凹陷。
连铸坯宽度越大,出现局部凹陷的几率也越大。
多数连铸坯宽面距边部30~180mm的范围内振痕较深,且振痕有紊乱的现象。
部分连铸坯在宽面上不规则的分布有渣坑。
随着奥氏体不锈钢中合金含量的提高和钢的组织越来越趋向于纯奥氏体组织,铸坯表面的局部凹陷及小渣坑也越多。
即钢种从304到316L再到310,连铸板坯表面小渣坑出现的几率增大,数量增多。
图1是奥氏体不锈钢连铸板坯表面几种常见缺陷的示意图。
2.缺陷分析方法为分析局部凹陷、渣坑、深振痕和振痕紊乱处的连铸板坯表面及皮下缺陷,在4个炉号的8块304不锈钢连铸坯表面取了16个缺陷部位试样,试样尺寸约15×15×15mm。
从中各取8个试样分别进行水平方向解剖和纵向解剖。
然后用光学显微镜和扫描电镜观察剖面上是否存在大颗粒夹杂、微裂纹或其它缺陷。
这8块连铸坯的全氧量在27~33ppm,硫含量在10~14ppm。
图1 奥氏体不锈钢连铸板坯表面缺陷示意图Fig.1 Scheme of surface defects in austenitic stainless steel slabs图2 试样解剖方法Fig.2 Dissections of samples水平方向解剖是,平行于铸坯表面,每次磨下一定厚度,抛光后进行观察,每个试样观察7个不同深度的水平抛面。
第一个水平抛面的深度为凹坑或振痕深度的一半左右,第二个水平抛面为正好在凹坑或振痕的底部,正好全部将黑皮磨去。
然后再磨4个抛面进行观察,每个抛面的与上一个抛面间的磨下深度控制在0.2~0.3mm。
最后在第6个抛面的基础上再磨下约0.5mm,抛光后作为第7个观察面。
纵向解剖的观察面垂直于铸坯表面,每个试样观察3个抛面,其中一个抛面通过缺陷中心。
3.试样水平方向解剖分析结果在8个水平解剖试样中,1#和2#试样为深振痕,3#和4#试样为深振痕且振痕紊乱处,5#、6#、7#和8#试样为小凹坑或渣坑。
每个试样观察不同深度的7个抛面,共56个抛面。
其中,2#样振痕沟深度约0.6mm,在第二个抛面上(即正好在振痕沟底部)发现有微裂纹(见图3)。
在第三个抛面上(即振痕沟底部以下约0.2mm的抛面),微裂纹仍然存在。
从第四个抛面(即振痕沟底部以下约0.45mm的抛面)以后的各个抛面上均未观察到微裂纹或其它皮下缺陷。
图3 2#样振痕沟底部的微裂纹照片Fig.3 Small crakes under the oscillation markin 2# sample7#样表面有小凹坑,在其第二个抛面上(即凹坑底部,此时试样总的磨下深度约为0.8mm)发现有微裂纹(图4(B))。
在其第三个抛面上(第二个抛面以下约0.2mm)仍能观察到微裂纹(图4(C))。
在第四个抛面上(第二个抛面以下约0.5mm)存在大量30~60μm的缺陷(图4(D)),应是裂纹末端或孔洞。
从第五个抛面(第二个抛面以下约0.7mm)以后的各个抛面上均未再观察到微裂纹或孔洞缺陷。
A 、7#样原始表面形貌B 、第二个水平剖面上的微裂纹C 、第三个水平剖面上的微裂纹D 、第四个水平剖面上的皮下缺陷图4 7#样振痕沟底部的微裂纹照片Fig.4 Small crakes under the oscillation mark in 7# sample除上述2#和7#样外,在其它6个样中均未发现微裂纹、洞孔、裹渣等皮下缺陷。
用金相法对这8个试样的共计56个抛面上的非金属夹杂物进行了观察。
除每个试样的第一个抛面主要观察缺陷周边是否存在大颗粒夹外,对其余48个抛面,每个抛面统计了100个视场(共80mm 2)中5μm 以上的非金属夹杂物数量。
结果显示,8个试样的第一个抛面上均未发现20μm 以上的夹杂物。
在其它48个抛面上,平均每100mm 2视场中5μm 以上的非金属夹杂物数量为47.5个,粒度在5~10μm 的夹杂物占总量的81.3%,粒度在10~20μm 的夹杂物占总量的17.1%,20μm 以上的夹杂物占总量的1.6%。
在20μm 以上的夹杂物中,只在4#样的第三个抛面上观察到一颗36μm 的非金属夹杂物,其它夹杂物粒度在20~26μm 。
从夹杂物观察结果来看,钢质的洁净度是较好的。
4.试样纵向解剖分析结果在8个纵向解剖试样中,9#和10#试样为深振痕,11#和12#试样为深振痕且振痕紊乱处,13#、14#、15#和16#试样为小凹坑或渣坑。
每个试样解剖3个纵面抛面,共24个观察抛面。
13#试样为一小凹坑,凹坑周围振痕紊乱。
在凹坑正中心位置的抛面上观察到一处皮下微裂纹,深度约0.4mm (图5)。
其它两个抛面上未观察到皮下缺陷。
A 、13#样凹坑中心位置剖面照片B 、剖面处裂纹照片图5 13#样中心位置剖面上的微裂纹 Fig.5 Small crack in central section of 13#sample14#试样表面为一小渣坑,在其3个纵剖面上都观察到了皮下缺陷。
图6是14#试样的表面形貌及3个纵剖面的位置。
其中A-A剖面与B-B 剖面距离约4mm,B-B剖面与C-C剖面相距约3mm。
图6 14#样表面形貌及纵剖面位置Fig.6 Surface shape of 14# sample and positionof its three sections在A-A剖面的缺陷部位下观察到了形状不规则的裂纹及孔洞,裂纹距表面的深度约为0.2mm(见图7)。
图7 A-A剖面中的皮下缺陷Fig.7 Defect in A-A setion在B-B剖面的缺陷部位下观察到两个孔洞,一个距表面约2.1mm,直径约110μm(图8(B)),另一个距表面约1mm,直径约160μm(图8(C))。
孔洞形状近似于圆形,图8中孔洞上的附着物为钢的基体和试样抛光时嵌入的外来物质,孔洞本身是中空的,因此判断应为皮下气孔。
A、B-B剖面下的两个气孔B、左侧孔洞形貌C、右侧孔洞形貌图8 B-B剖面中的皮下气孔Fig.8 Pinholes in B-B setion在C-C剖面的渣坑两侧也发现有裂纹存在,剖面处的裂纹最大深度约220μm(图9)。
图9 C-C剖面中的表面裂纹Fig.9 Surface cracks in C-C setionA B C A B C除上述13#和14#样外,在其它6个样的18个纵剖面中均未发现裂纹、洞孔、裹渣等皮下缺陷。
5.结论从上面的试样解剖结果来看,在25%的试样中观察到了微裂纹、气孔等缺陷。
也就是说,在304不锈钢连铸板坯渣坑、局部凹陷、深振痕等处出现裂纹或其它皮下缺陷的几率是很大的。
这些铸坯缺陷都会造成在冷轧产品表面形成肉眼可见的缺陷。
从不锈钢连铸坯修磨的角度来说,我们观察到的缺陷大多分布在距渣坑底部或振痕沟底部1mm的深度范围内,再考虑到铸坯表面渣坑或深振痕的深度可达到0.8mm。
那么,当连铸坯修磨量约为2mm时可将大多数表面微裂纹或其它皮下缺陷去除。
但还是会有少数皮下缺陷保留下来,如本文在14#中观察到的一个气孔距表面约2.1mm。
目前我公司304不锈钢连铸坯的修磨率约在0.5~1.0%,刚好修去黑皮,对200mm厚的连铸坯磨下量约在0.5~1.0mm。
在这一修磨量下,本文中观察到的大多数表面和皮下缺陷都会保留下来。
从铸坯中非金属夹杂物数量统计来看,我公司304不锈钢的钢质洁净度较好,不应造成较大比例的冷轧产品表面夹杂废品。
也就是说,当冷轧产品表面质量明显下降时,我们不仅应当关注钢质洁度,而且要关注连铸坯表面质量。
参考文献:[1] 范光伟, 王贵平, 李志斌. 0Cr18Ni9不锈钢中非金属夹杂物来源[J]. 北京科技大学学报, 2007, Vol.29(8), 776-780.[2] 冯焕林, 刘承志. 0Cr18Ni9纯净不锈钢75tLF精炼工艺的优化[J]. 特殊钢, 2007, Vol.28(6): 49-50.[3] 王贵平, 李志斌, 夏焱. 304不锈钢连铸坯中的非金属夹杂物数量分布[J]. 材料与冶金学报, 2009, Vol.8(3), 161-164.。