8D培训
8D 培训

8D 培训8D 培训:全面提升企业问题解决能力的利器一、引言随着市场竞争的加剧,企业面临着越来越多的挑战和问题。
为了提高企业的竞争力,提升问题解决能力显得尤为重要。
8D 方法作为一款高效的问题解决工具,已在全球范围内得到广泛应用。
本文将详细介绍 8D 培训的目的、内容、实施策略及效果评估,以期为企业提供全面提升问题解决能力的利器。
二、8D 培训的目的1. 提高企业问题解决能力:通过8D培训,使企业员工掌握一套系统、科学的问题解决方法,提高企业整体的问题解决能力。
2. 增强团队协作:8D方法强调团队协作,通过培训使员工学会如何在团队中发挥各自优势,共同解决问题。
3. 降低故障率和成本:通过8D培训,使企业能够快速、准确地找到问题的根源,并采取措施进行改进,从而降低故障率和成本。
4. 提升产品质量和客户满意度:8D方法帮助企业从根本上解决问题,提升产品质量,进而提高客户满意度。
三、8D 培训的内容1. 8D 方法概述:介绍8D方法的起源、发展及应用领域,使员工对8D方法有一个全面的认识。
2. 8D 步骤详解:详细讲解8D方法的八个步骤,包括:D0-问题识别、D1-团队组建、D2-问题描述、D3-临时措施、D4-问题原因分析、D5-永久措施、D6-实施与验证、D7-预防措施、D8-团队总结。
3. 8D 工具与技术:介绍在8D过程中常用的工具与技术,如鱼骨图、头脑风暴、5W1H等。
4. 案例分析与实操演练:通过案例分析,使员工了解8D方法在实际问题解决中的应用;通过实操演练,使员工掌握8D方法的操作要点。
四、8D 培训的实施策略1. 分层次培训:针对不同岗位、不同层级的员工,设计不同的培训内容,确保培训的针对性和实用性。
2. 混合式教学:采用线上与线下相结合的培训方式,充分利用网络资源,提高培训效果。
3. 案例驱动:以实际案例为主线,引导员工掌握8D方法的应用,提高问题解决能力。
4. 持续跟踪与反馈:培训结束后,对员工进行持续跟踪,了解培训效果,及时给予反馈和指导。
8D报告培训全

8D报告培训全8D报告培训全解析一、概述8D报告是一种广泛应用于品质管理和问题解决的工具,起源于美国汽车行业,后被众多企业借鉴和应用。
8D报告培训旨在帮助企业和员工掌握8D报告的方法和技巧,提高问题解决和品质管理能力。
本文将从8D报告的定义、培训内容、培训方法和培训效果等方面进行全面解析。
二、8D报告的定义和作用8D报告是一种结构化的问题解决方法,它包括8个D,即8个步骤,分别是:D0-问题识别、D1-团队组建、D2-问题描述、D3-临时措施、D4-根本原因分析、D5-永久措施、D6-实施和验证、D7-预防措施、D8-团队表彰和总结。
8D报告的作用在于帮助企业和员工系统地解决问题,避免问题重复发生,提高产品和服务的品质。
三、8D报告培训内容1. 8D报告的基本原理和步骤:培训学员了解8D报告的起源、发展、基本原理和8个步骤,掌握8D报告的结构和逻辑。
2. 问题识别和描述:培训学员学会如何识别和描述问题,包括问题的现象、影响、范围等。
3. 团队组建和沟通:培训学员学会如何组建高效的问题解决团队,以及如何进行有效的沟通和协作。
4. 临时措施和根本原因分析:培训学员掌握制定临时措施的方法,以及进行根本原因分析的技巧。
5. 永久措施和预防措施:培训学员学会制定和实施永久措施,以防止问题再次发生,以及制定预防措施,以避免类似问题的发生。
6. 实施和验证:培训学员学会如何实施和验证解决方案,确保问题得到有效解决。
7. 团队表彰和总结:培训学员学会如何进行团队表彰和总结,以激励团队成员,提高团队士气。
四、8D报告培训方法8D报告培训可以采用多种方法,如课堂讲授、案例分析、角色扮演、模拟演练等。
其中,模拟演练是一种非常有效的培训方法,它可以让学员在实际操作中学习和掌握8D报告的方法和技巧。
五、8D报告培训效果1. 提高问题解决效率:通过8D报告培训,企业和员工可以更加系统和高效地解决问题,提高问题解决效率。
2. 提升产品和服务的品质:通过8D报告培训,企业和员工可以更好地识别和解决产品和服务的质量问题,提升产品和服务的品质。
8D解决问题方法培训

8D 问题解决方法(8D Problem Solving)质量是一组固有特性满足需求的程度– 全面质量管理(Total Quality Management)质量是免费的,他不是礼品,但它是免费的– 克劳士比质量无需惊人之举– 戴明质量并非意味着最佳,而是客户使用和售价的最佳– 費根堡姆20世纪是生产率的世纪,21世纪是质量的世纪– 朱兰质量是生产出来的不是检验出来的– 威廉戴明解决问题的方法很多,没有最好,只有最适用。
日产V-FASTPDCA循环是美国质量管理专家沃特·阿曼德·休哈特(Walter A. Shewhart)首先提出的,由戴明( W.Edwards.Deming )采纳、宣传,获得普及,所以又称戴明环。
全面质量管理的思想基础和方法依据就是PDCA循环。
PDCA循环的含义是将质量管理分为四个阶段,即Plan(计划)、Do(执行)、Check(检查)和 Act(处理)。
1、计划阶段。
要通过市场调查、用户访问等,摸清用户对产品质量的要求,确定质量政策、质量目标和质量计划等。
包括现状调查、分析、确定要因、制定计划。
2、设计和执行阶段。
实施上一阶段所规定的内容。
根据质量标准进行产品设计、试制、试验及计划执行前的人员培训。
3、检查阶段。
主要是在计划执行过程之中或执行之后,检查执行情况,看是否符合计划的预期结果效果。
4、处理阶段。
主要是根据检查结果,采取相应的措施。
巩固成绩,把成功的经验尽可能纳入标准,进行标准化,遗留问题则转入下一个PDCA循环去解决。
8D遵循PDCA原则,一种问题解决的方法,通常针对未知原因的问题。
8D(8D Problem Solving)8D又称团队导向问题解决方法、8D问题求解法(8D Problem Solving Report)是福特公司处理问题的一种方法,亦适用于制程能力指数低於其应有值时有关问题的解决,它提供了一套符合逻辑的解决问题的方法,同时对于统计制程管制与实际的品质提升架起了一座桥梁。
2024年8D培训心得怎样写通用版

培训目标与期望
掌握8D方法的基本理念和核心 步骤,能够在实际工作中运用 8D方法解决问题。
2024/2/28
提高分析问题和解决问题的能 力,培养系统思考和团队协作 的能力。
通过案例分析和实践演练,加 深对8D方法的理解和应用能力 。
5
自身参与原因及意义
参与8D培训有助于提升个人职 业素养和竞争力,更好地适应企
基于对当前工作的分析和理解, 我将设定下一阶段的具体目标, 包括提高问题解决速度、降低问
题复发率等。
制定行动计划
为了实现这些目标,我将制定详 细的行动计划,包括具体的步骤
、时间表和责任人。
跟踪和评估进展
我将定期跟踪和评估目标的进展 情况,及时调整行动计划以确保
目标的顺利实现。
2024/2/28
32
THANKS
8D方法是一种结构化的问题解决工具,旨在识别和消除问题的根本原因 ,防止问题再次发生。
8D代表8个解决问题的步骤,包括建立团队、定义问题、实施临时措施 、确定并验证根本原因、选择和验证永久措施、实施永久措施、防止问 题再次发生和总结经验教训。
2024/2/28
8D方法广泛应用于制造业、服务业等各个领域,以提高产品质量和客户 满意度。
误解和歧义的产生。
注重语言表达和倾听技巧
在沟通过程中,我注重语言表达的准确性和条理性,同时运用倾听技巧,认真理解对方 的观点和需求,为有效的沟通奠定了基础。
2024/2/28
及时反馈和调整沟通策略
在沟通后,我及时给予对方反馈,确认信息是否准确传达,并根据对方的反应调整自己 的沟通策略,确保沟通效果达到最佳。
业发展的需要。
通过学习8D方法,可以更加有 效地解决工作中遇到的问题,提
8D资料培训讲义
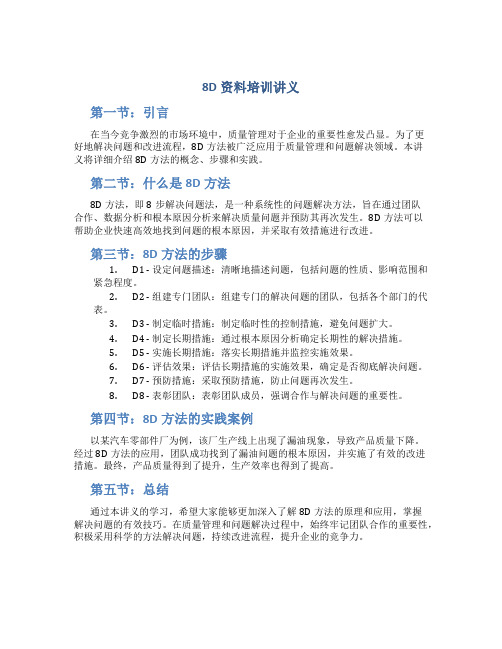
8D资料培训讲义第一节:引言在当今竞争激烈的市场环境中,质量管理对于企业的重要性愈发凸显。
为了更好地解决问题和改进流程,8D方法被广泛应用于质量管理和问题解决领域。
本讲义将详细介绍8D方法的概念、步骤和实践。
第二节:什么是8D方法8D方法,即8步解决问题法,是一种系统性的问题解决方法,旨在通过团队合作、数据分析和根本原因分析来解决质量问题并预防其再次发生。
8D方法可以帮助企业快速高效地找到问题的根本原因,并采取有效措施进行改进。
第三节:8D方法的步骤1.D1 - 设定问题描述:清晰地描述问题,包括问题的性质、影响范围和紧急程度。
2.D2 - 组建专门团队:组建专门的解决问题的团队,包括各个部门的代表。
3.D3 - 制定临时措施:制定临时性的控制措施,避免问题扩大。
4.D4 - 制定长期措施:通过根本原因分析确定长期性的解决措施。
5.D5 - 实施长期措施:落实长期措施并监控实施效果。
6.D6 - 评估效果:评估长期措施的实施效果,确定是否彻底解决问题。
7.D7 - 预防措施:采取预防措施,防止问题再次发生。
8.D8 - 表彰团队:表彰团队成员,强调合作与解决问题的重要性。
第四节:8D方法的实践案例以某汽车零部件厂为例,该厂生产线上出现了漏油现象,导致产品质量下降。
经过8D方法的应用,团队成功找到了漏油问题的根本原因,并实施了有效的改进措施。
最终,产品质量得到了提升,生产效率也得到了提高。
第五节:总结通过本讲义的学习,希望大家能够更加深入了解8D方法的原理和应用,掌握解决问题的有效技巧。
在质量管理和问题解决过程中,始终牢记团队合作的重要性,积极采用科学的方法解决问题,持续改进流程,提升企业的竞争力。
8D培训课件(PPT 100页)

D0:准备过程
1. 避免浪费
➢ 避免浪费大量的时间、人员和资源 ➢ 避免用精深的8D过程来解决单一的问题
2. 保持顾客满意度
➢ D0允许执行ERA来保护顾客 ➢ ERA是保持顾客满意度的重要部分 ➢ ERA是达到我们目标的重要部分
标准
D0
目的 WHY ERA 标准
D0:准备过程
ERA
选择和核实 执行和证实
考虑因素
1. 领导 2. 负责人 3. 时间管理员 4. 抄写员 5. 记录员 6. 协调员 7. 成员
小组角色
D1 建立小组
1. 领导:
➢
行使职权来执行小组的建议。
➢
同小组一起评审评估问题表格
➢
同小组一起设置目标和任务
2. 负责人:
➢
制定会议和小组活动的日程
➢
监控按照日程的进展
3. 时间管理员:
D0
目的 WHY ERA 标准
D0:准备过程
开始8D的适用标准: 1. 如果六个标准都满足 ① 症状已被定义和量化 ② 受影响的各方已经被确定 ③ 量化结果表明有性能差异和/或症状的优先 ④ 原因不知道 ⑤ 管理层想要找出根本原因并预防再次发生 ⑥ 症状的复杂性超出了个人能解决的范围 2. 没有其它的8D小组正在解决相同或相似的问题
D0
目的 WHY ERA 标准
D0:准备过程
ERA
选择和核实 执行和证实
1. 执行前验证ERA ➢ ERA能够保护顾客 ➢ 不会产生新的问题 2. 验证可以包括: ➢ 试验和演示 ➢ 比较新的行动 ➢ 已验证过的相似行动 3. 在发布前回顾最近的设计文件 4. ERA可能很难用测量验证
ERA(Emergency response action )
2024年8D报告培训教材教程
8D报告培训教材教程1.引言8D报告是一种广泛应用于质量管理和问题解决的方法,其名称来源于8个解决问题的步骤(Disciplines)。
本教材旨在为您提供关于8D报告的全面培训,帮助您掌握8D报告的编写和应用技巧。
2.8D报告的背景和目的8D报告起源于汽车行业,并逐渐被其他行业所采用。
其主要目的是系统地解决问题,防止问题再次发生,并提高产品和服务的质量。
8D报告通常用于处理客户投诉和内部问题,以及推动持续改进。
3.8D报告的8个步骤3.1步骤1:建立团队在开始编写8D报告之前,需要建立一个跨部门的团队,团队成员应具备相关领域的专业知识和经验。
团队应由一名负责人领导,负责协调和推动整个解决问题的过程。
3.2步骤2:问题描述问题描述是8D报告的核心部分,需要清晰地描述问题的现象、影响和发生的时间。
问题描述应尽量具体、准确,并使用数据和事实来支持。
3.3步骤3:临时措施在找到根本原因之前,需要采取一些临时措施来减轻问题的影响。
这些措施应尽快实施,并在报告中详细说明。
3.4步骤4:根本原因分析根本原因分析是解决问题的关键步骤,需要运用各种工具和技术来找到问题的根本原因。
常用的工具包括鱼骨图、5个为什么等。
3.5步骤5:制定行动计划根据根本原因分析的结果,制定详细的行动计划来解决问题。
行动计划应包括具体的行动步骤、责任人和完成时间。
3.6步骤6:实施行动计划按照行动计划,组织资源并实施解决方案。
在实施过程中,需要监控进度,并及时调整计划以确保问题得到有效解决。
3.7步骤7:效果验证在实施解决方案后,需要对效果进行验证,以确保问题得到根本解决。
验证可以通过数据分析、客户反馈等方式进行。
3.8步骤8:预防措施和持续改进为了防止问题再次发生,需要制定预防措施,并对整个问题解决过程进行总结和反思,提出改进建议。
4.8D报告的编写技巧4.1结构清晰8D报告应遵循一定的结构,包括引言、问题描述、临时措施、根本原因分析、行动计划、实施结果、效果验证、预防措施和持续改进等部分。
2024年8D报告知识培训
8D报告知识培训一、引言8D报告是一种广泛应用于企业管理中的问题解决方法,其核心思想是通过团队合作、系统分析、根本原因探究和持续改进,实现问题的快速定位和有效解决。
为了提高员工在问题解决方面的能力,提高工作效率,本次培训将针对8D报告的编写方法和应用技巧进行详细讲解。
二、8D报告的基本概念1.什么是8D报告8D报告是一种结构化的问题解决方法,起源于美国汽车行业,后被广泛应用于各个领域。
8D报告的名称来源于其包含的8个基本步骤,分别为:D0(预备阶段)、D1(成立团队)、D2(问题描述)、D3(临时措施)、D4(根本原因分析)、D5(制定和实施永久措施)、D6(实施永久措施)、D7(预防措施)、D8(团队总结与认可)。
2.8D报告的特点(1)结构化:8D报告提供了一套完整的问题解决流程,使问题解决过程具有可操作性和可重复性。
(2)团队合作:8D报告强调团队在问题解决过程中的作用,鼓励团队成员发挥各自专长,共同解决问题。
(3)系统分析:8D报告要求从系统层面分析问题,找出问题的根本原因,从而制定有效的解决方案。
(4)持续改进:8D报告强调在问题解决过程中,要不断总结经验教训,完善工作流程,实现持续改进。
三、8D报告的编写方法1.D0(预备阶段)在D0阶段,要明确问题,确定问题解决的优先级,并通知相关人员。
还需对问题进行初步评估,判断是否需要启动8D报告流程。
2.D1(成立团队)在D1阶段,根据问题的性质和影响范围,组建一支跨部门、跨职能的团队。
团队成员应具备相关专业知识,能够共同参与问题解决过程。
3.D2(问题描述)在D2阶段,要对问题进行详细描述,包括问题的现象、发生时间、地点、影响范围等。
同时,还需收集与问题相关的数据和信息,为后续分析提供依据。
4.D3(临时措施)在D3阶段,要制定并实施临时措施,以减轻问题的影响。
临时措施应能够在短时间内见效,为后续根本原因分析争取时间。
5.D4(根本原因分析)在D4阶段,要通过数据分析、现场调查等方法,找出问题的根本原因。
8d报告培训
8d报告培训8D报告培训。
一、概述。
8D报告是一种针对问题解决和持续改进的方法,它由八个步骤组成,可以帮助团队有效地识别、解决和预防问题。
本次培训将重点介绍8D报告的基本概念、步骤和工具,以及如何在实际工作中应用这些知识来解决问题。
二、8D报告的概念。
8D报告是一种质量管理工具,它起源于美国汽车工业,后来被广泛应用于各个行业。
它的核心思想是通过系统性的方法来解决问题,以确保问题不再发生。
8D报告的八个步骤分别是,明确问题、建立团队、制定临时措施、确定根本原因、制定长期解决方案、实施解决方案、预防措施和确认效果。
每个步骤都有相应的工具和技术支持,可以帮助团队更好地完成任务。
三、8D报告的步骤。
1. 明确问题,首先要明确定义问题,包括问题的性质、影响范围和紧急程度。
这一步需要收集相关数据和信息,确保对问题有全面的了解。
2. 建立团队,确定一个专门的团队来负责解决问题,团队成员需要具备不同的技能和经验,以便全面分析和解决问题。
3. 制定临时措施,在确定长期解决方案之前,需要先采取一些临时措施来减轻问题带来的影响,确保生产和服务的正常进行。
4. 确定根本原因,通过使用工具如5为什么分析、鱼骨图等,找出问题的根本原因,而不是仅仅解决表面问题。
5. 制定长期解决方案,基于对根本原因的分析,制定长期解决方案,并评估其可行性和效果。
6. 实施解决方案,将长期解决方案付诸实施,并监控其进展情况,确保按计划推进。
7. 预防措施,为了避免问题再次发生,需要采取一些预防措施,如改进流程、加强培训等。
8. 确认效果,最后需要对解决方案的效果进行确认,确保问题得到了彻底解决。
四、应用实例。
以某公司生产线上频繁出现的产品质量问题为例,我们可以运用8D报告来解决这一问题。
首先,明确问题是产品质量不达标,影响生产进度和客户满意度。
然后,建立一个由生产、质量、工程等部门成员组成的团队,共同分析问题。
接着,制定一些临时措施来减少不合格品的产生,同时进行5为什么分析,找出问题的根本原因。
2024版8D培训心得怎样写(通用)
通过学习和实践8D方法,参与者能够推动组织内部流 程的改进,提高整体运营效率。
培养团队协作精神
8D方法强调跨部门、跨职能的团队协作,有助于培养 参与者的团队协作精神。
8D方法简介
80%
8D的起源与发展
8D方法起源于汽车行业,后来逐 渐在制造业、服务业等领域得到广 泛应用。
100%
8D的核心思想
流程和结果。
对8D培训的建议与意见
1 2 3
加强实践环节 建议在培训过程中增加更多的实践环节,让学员 有机会亲自运用8D方法解决问题,从而加深对 理论知识的理解和记忆。
结合案例分析 通过结合具体的案例分析,可以让学员更好地理 解8D方法在实际问题中的应用,提高培训的实 用性和针对性。
提供后续支持 在培训结束后,可以提供一定的后续支持,例如 定期举办复习课程、提供在线资源等,以帮助学 员巩固和深化所学知识。
8D方法的应用范围
产品质量问题
8D方法最初应用于产品质量问题 的解决,包括设计缺陷、制造过
程问题、来料质量问题等。
生产过程问题
8D方法也可应用于生产过程问题 的解决,如生产效率低下、设备 故障频繁等。
管理问题
8D方法还可应用于企业管理问题 的解决,如流程不畅、沟通不畅 等。
其他问题
除了以上领域,8D方法还可应用 于其他领域的问题解决,如服务
为公司和团队创造更大的价值。
THANK YOU
感谢聆听
实施解决方案并验证效果
总结经验教训并持续改进
按照制定的解决方案实施改进 措施,并对改进效果进行验证, 确保问题得到有效解决。
在问题解决后,要及时总结经 验教训,完善相关流程和制度, 避免类似问题再次发生。同时, 要持续关注改进效果,不断进 行优化和改进。
- 1、下载文档前请自行甄别文档内容的完整性,平台不提供额外的编辑、内容补充、找答案等附加服务。
- 2、"仅部分预览"的文档,不可在线预览部分如存在完整性等问题,可反馈申请退款(可完整预览的文档不适用该条件!)。
- 3、如文档侵犯您的权益,请联系客服反馈,我们会尽快为您处理(人工客服工作时间:9:00-18:30)。
Thanks to Kay Shreve (Monroe, MI), Michael Brown (Paragould, AR) and Eunice Spradlin (Cozad, NE) for their work on this project. 感谢 Kay Shreve (Monroe, MI), Michael Brown (Paragould, AR) 和 Eunice Spradlin (Cozad, NE) 对此项目所作的工作。
10
D-2 Describe the Issue描述问题 描述问题
• TOOLS TO USE 可用工具
– Process flow diagram 工序流程图 – Check sheets to collect data 用检 查表来收集数据 – Any data that is reporting the issue 反映问题的任何数据 • Customer complaints 客户抱怨 • Current SPC/Data collection sheets 现有的SPC/数据收集表 • PFMEA 过程FMEA • Scrap/rework reports 废品/返工报表
Tenneco Automotive 8-D/2000 11
D-2 Describe the Issue描述问题 描述问题 Incorrect 不正确 Correct 正确
It doesn’t work 不好用 Scrap is too high
废品率太高
It is noisy 噪音太大 Part is out of specification 零件不合格 Audit was not successful
Scrap is too high 废品率太高
目前第 12 部门的焊透(代码 12)废品率 为 38%。目标为 3%。发生时间为过去 三个月。
Tenneco Automotive 8-D/2000 13
D-2 Describe the Issue
Incorrect 不正确
It is noisy 噪音太大
Tenneco Automotive 8-D/2000
1
DISCIPLINES TO PROBLEM SOLVING 解决问题的8项纪律
8
8-D 2005
This course was developed by a team of Tenneco Automotive employees who have worked on problem solving efforts for the past fifteen to twenty years. This course is a summary of the problem solving process that was formerly known as PEP (People Eliminating Problems) within the ride control business unit and QUIP (Quality Improvement Process) within the exhaust business unit. Ford Motor Company is acknowledged as the developer of the “8-D” process. ) 该课程由一个由天纳克员工组成的,在过去的15-20年内致力于解决各 种问题的团队开发的,是对解决问题程序的总结。这一程序以前在减 震系统业务中被称为PEP(消除问题团队), 在排气系统业务中被称为 QUIP(质量改进程序)。福特公司被公认为是8-D程序的开发者。
• HOW BIG 多大
– How many objects have the defect 有多少有缺陷的事物 – How many defects per object 每件 事物上有多少缺陷 – What is the trend 趋势如何
Tenneco Automotive 8-D/2000
Tenneco Automotive 8-D/2000
4
8 - Disciplines of Problem Solving 解决问题的8项纪律 解决问题的 项纪律
D-1 Form the Team 建立团队 D-2 Describe the Issue描述问题 描述问题 D-3 Containment Activities临时控制措施 Activities临时控制措施 D-4 Find and Verify Root Cause查找并确定根本原因 查找并确定根本原因 D-5 Select the Best Solution选择最佳解决方案 选择最佳解决方案 D-6 Verification of Corrective Action纠正措施验证 纠正措施验证 D-7 D-8 Prevent Recurrence预防问题重复发生 预防问题重复发生 Congratulate the Team祝贺团队 祝贺团队
Tenneco Automotive 8-D/2000
3
8 - Disciplines of Problem Solving 解决问题的8项纪律 解决问题的 项纪律
D-1 Form the Team 建立团队 D-2 Describe the Issue描述问题 描述问题 D-3 Containment Activities临时控制措施 临时控制措施 D-4 Find and Verify Root Cause查找并确定根本原因 查找并确定根本原因 D-5 Select the Best Solution选择最佳解决方案 选择最佳解决方案 D-6 Verification of Corrective Action纠正措施验证 纠正措施验证 D-7 D-8 Prevent Recurrence预防问题重复发生 预防问题重复发生 Congratulate the Team祝贺团队 祝贺团队
6
•
•
Tenneco Automotive 8-D/2000
D-1 Form The Team建立团队 建立团队 CAUTIONS注意 ! ! !
• Ensure cross-functional team members 确保有多个功能部门的团队 成员 • Include process owners (those who do the work) 要包括过程当事人 (实际作这 项工作的人员) • Include champion and leader as road-block removers 要包括团队负责人和团队组 长作为路障排除人
Correct 正确
Bushing 38427 produces a “clicking” sound – measures 6 decibels in the sound booth. Was reported by Ford Lorain assembly plant (MRR # BR-549 – 2/30/00 – 5000 pieces), confirmed in lab 3/4/00. 衬套 38427 发出一种’咔啦’声音—测 音室测量为 6 分贝。由福特 Lorain 组 装厂发现(MRR # BR-549 – 2/30/00 – 5000 件), 00 年 3 月 4 日试验室确认。 10840 piston rod nut has overall height Part is out of specification of .874; spec is .750 max. Seen in dept 零件不合格 13 assembly line on 5/4/00; caused discs to crush in asm. – causes 20% reject rate. 活塞杆螺栓 10840 整体高度为.874, 要求为最高.750。发生于 00 年 5 月 4 日第 13 部门的组装线上。导致轮盘 在总成内被压跨,继尔导致 20%次品 Tenneco Automotive 8-D/2000 率。
Tenneco Automotive 8-D/2000 7
8 - Disciplines of Problem Solving 解决问题的8项纪律 解决问题的 项纪律
D-1 Form the Team 建立团队 D-2 Describe the Issue描述问题 描述问题 D-3 Containment Activities临时控制措施 Activities临时控制措施 D-4 Find and Verify Root Cause查找并确定根本原因 查找并确定根本原因 D-5 Select the Best Solution选择最佳解决方案 选择最佳解决方案 D-6 Verification of Corrective Action纠正措施验证 纠正措施验证 D-7 D-8 Prevent Recurrence预防问题重复发生 预防问题重复发生 Congratulate the Team祝贺团队 祝贺团队
审核未通过
Tenneco Automoቤተ መጻሕፍቲ ባይዱive 8-D/2000 12
D-2 Describe the Issue描述问题 描述问题 Incorrect 不正确 Correct 正确
It doesn’t work 不好用
Welder 123 does not hold consistent dwell time – varies from 9 sec to 16 sec every 3 hrs. This was first seen 3/1/00 and has been reported each day since on all shifts. 焊机 123 停顿时间不一致,每三个小时会 从 3 秒变到 16 秒。首次发生在 00 年 3 月 1 日,以后每天每班都会发生。 Scrap for burn through (code 12) is currently at 38% in dept. 12. Goal is 3%. This has been seen for the past 3 months.