挤出设备计算与选型
挤出机械及口型设计课件

长径比 转速范围 生产能力
挤出机械及口型设计
4
概念解释
a.长径比: 螺杆外径和螺杆螺纹长度之比。
一般热喂料螺杆长径比 3—8
冷喂料螺杆长径比
8—17(20)
长径比是挤出机的重要技术参数之一,它直接反 映挤出机的生产能力,影响到挤出效果。
挤出机械及口型设计
5
b.压缩比:
压缩比是指螺杆加料端一个螺槽容积和出 料端一个螺槽容积的比。
程度更加均一。其断面形状如下图所示:
挤出机械及口型设计
15
单级流道的特点:
单级式流道板也是可更新、更换的,
相对而言胶料分布的均一性要差一些。 因为它没有第一级的预分散流道,完全 是靠在机筒内部机头的压力对胶料进行 分散。为弥补分散不均一的不足也采取 了一些措施,如机头有意加长,这样胶 料在机头内部停留时间加长,胶料有充 足的时间进行分散。
1.机头流道的设计:
1.1现有机头流道的形式\特点:
单级式流道板报 POMINI 日本中田 双级式流道板 TROESTER 各自 特点: 双级式流道板更新、更换方便,胶料在机 头内分布分散均匀,排胶断面对称性好。
挤出机械及口型设计
14
胶料在机筒的出口,流经流道板的第 一级进行初步分散,胶料流经流道板的第 二级进一步分散,这时胶料各部位的致密
挤出机械及口型设计
7
C1.实际测定法:
实际测定法是在挤出线速度一定的条件下, 设定不同的螺杆转速,测量单位时间内挤出胶 料的重量。
在这里挤出量和螺杆转速是成正比的。
Q=KR
Q-是挤出量 K-是一个系数 R-是螺杆转速
系数K和挤出机的温度设定,挤出机的螺纹形式等 因素有关.系数K可以通过数学的方法模拟出.在测定出 胶量的同时还要测定相应螺杆转速下的出胶温度。
挤出机螺杆型号及尺寸规格表及挤出量
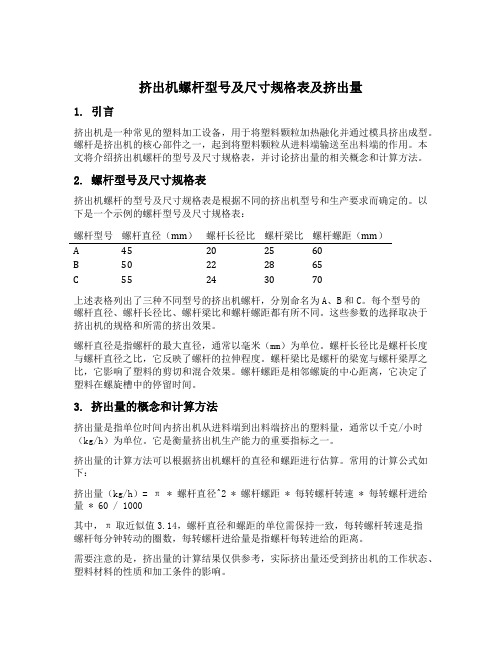
挤出机螺杆型号及尺寸规格表及挤出量1. 引言挤出机是一种常见的塑料加工设备,用于将塑料颗粒加热融化并通过模具挤出成型。
螺杆是挤出机的核心部件之一,起到将塑料颗粒从进料端输送至出料端的作用。
本文将介绍挤出机螺杆的型号及尺寸规格表,并讨论挤出量的相关概念和计算方法。
2. 螺杆型号及尺寸规格表挤出机螺杆的型号及尺寸规格表是根据不同的挤出机型号和生产要求而确定的。
以下是一个示例的螺杆型号及尺寸规格表:螺杆型号螺杆直径(mm)螺杆长径比螺杆梁比螺杆螺距(mm)A 45 20 25 60B 50 22 28 65C 55 24 30 70上述表格列出了三种不同型号的挤出机螺杆,分别命名为A、B和C。
每个型号的螺杆直径、螺杆长径比、螺杆梁比和螺杆螺距都有所不同。
这些参数的选择取决于挤出机的规格和所需的挤出效果。
螺杆直径是指螺杆的最大直径,通常以毫米(mm)为单位。
螺杆长径比是螺杆长度与螺杆直径之比,它反映了螺杆的拉伸程度。
螺杆梁比是螺杆的梁宽与螺杆梁厚之比,它影响了塑料的剪切和混合效果。
螺杆螺距是相邻螺旋的中心距离,它决定了塑料在螺旋槽中的停留时间。
3. 挤出量的概念和计算方法挤出量是指单位时间内挤出机从进料端到出料端挤出的塑料量,通常以千克/小时(kg/h)为单位。
它是衡量挤出机生产能力的重要指标之一。
挤出量的计算方法可以根据挤出机螺杆的直径和螺距进行估算。
常用的计算公式如下:挤出量(kg/h)= π * 螺杆直径^2 * 螺杆螺距 * 每转螺杆转速 * 每转螺杆进给量 * 60 / 1000其中,π取近似值3.14,螺杆直径和螺距的单位需保持一致,每转螺杆转速是指螺杆每分钟转动的圈数,每转螺杆进给量是指螺杆每转进给的距离。
需要注意的是,挤出量的计算结果仅供参考,实际挤出量还受到挤出机的工作状态、塑料材料的性质和加工条件的影响。
4. 结论本文介绍了挤出机螺杆型号及尺寸规格表以及挤出量的相关概念和计算方法。
螺杆的型号和尺寸规格表是根据不同的挤出机型号和生产要求而确定的,螺杆直径、螺杆长径比、螺杆梁比和螺杆螺距的选择取决于挤出机的规格和所需的挤出效果。
挤出设备计算与选型

挤出设备计算与选型挤出设备是一种常见的工业设备,用于将塑料或橡胶等物料通过挤出机进行加热、塑炼、挤出成型的生产过程。
该设备有着广泛的应用领域,包括塑料制品、橡胶制品、食品包装等行业。
在进行挤出设备的选型和计算时,需要考虑多个因素,包括设备的规格、能耗、生产能力等。
下面将对挤出设备的计算与选型进行详细介绍。
一、挤出设备的计算在进行挤出设备的计算时,主要涉及到以下几个方面:1.生产需求计算首先需要明确生产需求,即每天需要生产的产品数量。
根据产品的类型和规格,可以得到每个产品的单个重量,然后通过每天需要生产的总重量,得到每天需要的挤出设备的生产能力。
2.设备能耗计算挤出设备的能耗主要包括电能和热能两部分。
在计算设备能耗时,需要考虑设备的运行时间、负载率、能源价格等因素。
通过设备的能耗计算,可以估算每天需要的电能和热能消耗,从而选择合适的能源供应方式。
3.设备尺寸计算挤出设备的尺寸对于生产效率和产品品质具有重要影响。
在进行设备尺寸计算时,需要考虑挤出机的螺杆直径、螺杆长度、进料口尺寸、出料口尺寸等因素,以确保设备能够适应所需生产能力。
4.动力系统计算挤出设备的动力系统包括电机和传动系统。
在进行动力系统计算时,需要考虑设备的驱动功率、传动效率等因素,以确保设备能够正常运行。
二、挤出设备的选型在进行挤出设备的选型时,需要综合考虑以下几个方面:1.生产需求根据每天需要生产的产品数量和规格要求,选择挤出设备的生产能力。
对于大批量生产的需求,可以选择生产能力较高的挤出设备;对于小批量多品种的需求,可以选择生产能力较低、换机快捷的挤出设备。
2.材料特性不同的挤出设备适用于不同的材料,如塑料、橡胶、食品等。
在选型时,需要根据所需生产的产品材料特性,选择适合的挤出设备。
3.设备质量与稳定性挤出设备是一个长期投资,需要考虑设备的质量和稳定性。
选择具有良好声誉的厂家和品牌,以确保设备质量可靠、维修方便。
4.经济性在选型时,还需要考虑挤出设备的经济性。
挤出滚圆设备选型

挤出滚圆系统设备选型分析文中华重庆力谱制药机械有限公司摘要:介绍挤出滚圆微丸系统的设备种类,主要阐述其设备构成、工作流程、工艺特点。
关键词:混合、挤出、滚圆、高粘度、热敏性挤出滚圆工艺以其高效、工艺可操作性强、重现性好、收率高等优势而在医药、化工、食品等含行业均得到广泛应用。
挤出滚圆属于湿法挤压制粒范畴,使用的基本设备包括湿法混合机、挤出机和离心滚圆机,另外还有输送设备、计量设备、干燥设备等。
在此对工艺中使用的基本设备做一简要描述,对各种设备进行分析,以方便用户进行相关设备选择。
一、湿法混合机湿法混合机的种类繁多,适合做挤出滚圆混合用的设备要求混合均匀度高、混合得到的软材均匀性好,常用的主要由以下几种。
1、槽型混合机槽型混合机用以混合粉状或糊状的物料,使不同质物料混合均匀。
是卧式槽形单桨(或双桨)混合,搅抖桨为通轴式,便于清洗。
与物体接触处全采用不锈钢制成,有良好的耐腐蚀性,混合槽可自动翻转倒料。
槽型混合机是间歇式混合机,需手动翻转出料,混合有死角,操作也不很方便,已渐渐被其他设备取代。
2、湿法混合制粒机湿法混合制粒机能一次完成混合加湿、制粒等工序,适用于制药、食品、化工等行业。
它是符合药品生产GMP要示的先进设备。
具有高效、优质、低耗、无污染、安全等特点。
湿法混合制粒机生产效率高,全自动操作,是混合一般物料的理想设备。
典型产品:德国GLATT、德国DIOSNA、中国625所、浙江明天机械等。
3、捏合机捏合机是一种对高粘度及超高粘度的弹塑性物料进行混炼、捏合、破碎、分散及聚合成化工产品的设备;其功能全、品种多,应用十分广泛,特别适用于塑料、橡胶、硅橡胶、染料、颜料、油墨、食品胶基、医药药剂、建筑涂料、碳素、纤素等各行业。
在挤出滚圆工艺中,用于对简单混合效果不理想的物料进行均匀混合。
典型产品:德国LCI、英国CALEV A、德国IKA、莱州龙兴集团等。
4、连续混(捏)合机连续混(捏)合机需配合连续定量供粉机、连续定量供液系统使用。
挤压机的计算

尺寸要求:直径为32mm,长度为500mm1实现拉拔过程的基本条件是安全系数K大于1。
拉拔时安全系数与被拉拔金属的直径、状态(退火或硬度)以及变形条件有关。
K值一般在1.4-2.0之间。
查表选定K=1.6。
σS=438MPaK=σS /σ1,σS ——金属出模口的变形抗力σ1——作用在被拉金属出模口横断面上的拉拔应力σ1=σS /K=438/1.6=273.75MPa又因为σ1=P1/F1,P1=273.75×(32÷2)²×π=220055.2N=22T拉拔力确定之后,那么这种拉拔机所能拉的最大材料直径就确定下来了。
查表选取延伸系数λ=1.4λ= F q/F h,F q=(32÷2)²×π×1.4=1125.376mm²,d q=38mm根据拉拔工艺参数及拉拔力选取双链拉拔机,双链连续拉拔机比单链连续拉拔机更平稳,所能传递的力更大。
双链连续拉拔机包含了双向开卷机、粗矫机、双链拉伸机、精矫机、液压剪切机、倒角机、两辊机、收料架。
主要技术参数:1. 加工对象:有色金属和黑色金属2.额定拉拔力:40T3.拉伸速度:5-25m/min4.成品规格:圆料Φ20~Φ40、方棒H16~27、六角S16~325.最大成品规格时断面缩减率:13.9%6.成品长度:2~6m7.成品表面粗糙度:Ra0.8~1.68.成品直线度:3mm/m9.成品外径公差:±0.01mm10.主电机功率(两台):165KW11.机组总功率:500KW12.电源相数:313.电源频率:50HZ14.电源电压:380V, 控制电压:DC24V15.气源:6Kg/cm2±1Kg/cm216.机组重量:约70T17.使用环境:-20oC~40oC18.周围介质:无爆炸、危险,无足以腐蚀金属和损坏金属和损坏绝缘层的气体或尘埃4 锭胚尺寸形状、表面质量要求及技术要求4.1挤压比的选择挤压比是指在挤压时挤压筒断面积与制品断面积的比值,一般根据金属或合金的塑性、产品性能以及设备能力等因素综合确定,挤压比的数值大致控制在6~100范围内。
挤出机选择参考

挤出机的选择:一,依成型制品规格进行选择:制品规格不同,用料量也不一样,可参照“螺杆直径与制品规格尺寸”,先选出螺杆的直径,然后由螺杆直径再进一步选出挤出机的规格型号。
二,按挤出成型制品所用的原材料选择:PVC挤出成型用设备①单螺杆挤出机.20多年前,PVC挤出成型多采用渐变型单螺杆式挤出机,由于PVC是一种热敏性塑料,挤出机的螺杆转速不能过高,要先把PVC粉(片)料造粒后,再投入制品的生产,后来有了PVC粉料专用挤出机,不需要造粒,可直接把粉料混合好后投入挤出机生产成型制品即可.注:对于PVC料中需加入增塑剂的软质PVC制品,挤出成型前还必须先造粒,然后挤出成型。
②锥形异向双螺杆挤出机.这类种的挤出机价格适当,对于PVC粉料的挤出不会引起过高的摩擦热,避免了原料的分解,挤出料量稳定、成品产量高且性能又得到保证,目前用PVC混合粉料生产硬质PVC制品时,首先考虑用这种挤出机。
③平行异向双螺杆挤出机.用这种挤出机可直接把PVC粉料直接挤出成型管材、异形材,也适合HDPE料挤出管材,产量也比以上两种挤出机高,但由于价格过高且维修较复杂,目前应用还较少。
2,其他塑料挤出成型设备对于PE 、PP、PS、PC、ABS塑料的挤出成型,目前选用单螺杆挤出机,这主要是这种挤出机的价格便宜,操作和维修比较方便,而且现在也有了高效的单螺杆挤出机,长径比为30:1,螺杆转速可达100-300r/min。
三,设备生产厂商的选择挤出机的类型和规格型号确定后,如何找设备生产商也是应该注意的一个问题,国内质量较好的生产厂商主要分布在上海、青岛、大连、顺德、张家港一带,这些厂家建厂时间长,势力雄厚且有多年的实践经验,品质可靠,使用寿命长,售后好!1.螺杆的转速这是影响一台挤出机产能最关键的因素。
螺杆转速不仅是提高对物料的挤出速度和挤出量,更重要的是使挤出机在实现高产量的同时得到好的塑化效果。
以往要提高挤出机产量,主要的办法是加大螺杆直径。
铝型材挤压后部设备参数计算
铝型材挤压机后部设备参数计算冷床计算参数一、需要生产车间提供的基本参数:1.型材最大外圆、最大矩形截面以及最大长度;2.挤压机中心高;3.最大米重和最小米重,最大挤压比,挤出型材最大速度;4.铝锭尺寸,挤压机挤压速度;5.挤压铝合金牌号;6.型材成品的最大定尺长度和最小定尺长度;7.压缩空气最大使用量以及工作压力;8.现场供电电源;9.牵引机的最大牵引力,在线拉伸机的最大拉伸力;10.现场设备准备安装位置。
二、计算后部设备每个部分参数:1.出口导正:①动作元件:3条油缸2.淬火装置:①需要计算元件:a.高压离心风机—进行风冷淬火;b.水泵—进行水冷淬火;c.油缸(同步减速电机)—用于淬火装置上风罩的提升,便于牵引机进入淬火装置牵引第一根型材;d.气缸:用于升降上风罩的挡水板。
风冷时,气缸升起挡水板;水冷时,挡水板下降,防止水溅出;e.板式换热器(内循环淬火)—提高淬火质量。
②购买方提供的参数:a.型材的温降△T(型材初始温度T1①、型材出淬火装置温度T2②)、淬火用水的初始温度T’③;b.风冷时生产型材的最大米重M④及挤出速度V⑤;c.生产最大米重型材时的最大挤出速度V⑥;d.使用内循环板式换热器时,需要提供冷媒水的温度。
3.牵引机:①需要计算元件:a.主牵引机和副牵引机(随动锯)的行走电机;b.主、副牵引机中使用的油缸;c.副牵引机(随动锯)中锯片、锯片电机以及除尘器的离心风机;d.根据牵引机行走电机的选择,算出导出辊道的长度。
4.导出辊道:①需要计算元件:a.导出辊道中升降气缸(或者气弹簧);5.出料辊道:①需要计算元件:a.出料辊道升降使用的油缸,计算其工作压力P和速度V。
6.出料辊道挑料:①需要计算元件:a.驱动电机7.冷床平台:①需要计算元件:a.驱动电机8.过桥:①需要计算元件:a.驱动电机b.过桥伸缩用气缸9.拉伸机:①需要计算元件:a.拉伸机中各个油缸的选择b.尾拉伸中液压马达的选择c.有升起装置时,其液压缸的选择10.储料平台:①需要计算元件:a.驱动电机11.锯前辊道挑料:①需要计算元件:a.驱动电机12.锯前辊道:①需要计算元件:a.锯前辊道升降使用的油缸,计算其工作压力P和速度V。
挤出设备计算与选型
第4章挤出设备计算与选型4.1 挤出生产线的设备计算依据设计任务书,要求要设计年产量25万吨PUC-U塑钢型材生产车间,生产时间设置为6744小时。
选择的挤出机为TSH-135双螺杆挤出机,其生产能力为5000kg/h,则所需挤出机台数为:254957.44÷5÷6774=7.56台,实际中取为8台。
即能完全符合产量要求,且留有增大产量空间,可减少机器满负荷运转的时段。
并且该PVC-U型材推拉框生产线,自动化程度高,性能稳定,变频调速等多项特点。
所以选用TSH-135双螺杆挤出机设备,其技术参数见表4-1[15]。
表4-1 锥形双螺杆挤出机设备工技术参数4.2 混合机组的设备计算4.2.1 高速混合机的选取与计算每年需要高混的物料量为:268376.25t每天需要高混的物料量为:268376.25/281=955.1t每小时需要高混的物料量:955.1/24=39.80t每10分钟可以混一锅料,则每小时混6锅料,则每锅混料量:39.80/6=6.63t PVC-U粉料的表观密度为0.45t/m3,每锅可装粉料量:6.63t/0.45=14.7m3;则需要高混机的最小容积为14.7m3。
所以选用WLD-H-35高速加热/冷却混合机组,其技术参数见表4-2。
高混机的有效容积取15m3,PVC-U粉料的表观密度为0.45t/m3,每锅可装粉料量:0.45×15=6.75 t每10分钟可以混一锅料,则每小时混6锅料,则每小时混料量:6.75×6=40.5 t/h需要高混机:268376.25/(40.5×6744)=1.78台所以选用2台WLD-H-35热混机。
4.2.2 冷混机的选取与计算与WLD-H-35热混机配套的冷混机可选用WLD-H-35冷却机。
WLD-H-35冷却机技术参数见表4-3。
表4-3 WLD-H-35冷混机技术参数需要冷混机的台数:268376.25/(40.5×6744)=1.78所以选用2台WLD-H-35冷混机。
挤出量计算方式
挤出量计算方式挤出量是指在挤出过程中通过挤出机将塑料料柱挤出成型的速度和量。
挤出量是衡量挤出机生产能力的重要指标,它直接影响着挤出产品的质量和生产效率。
因此,准确计算挤出量对于挤出加工行业来说至关重要。
挤出量的计算可以通过以下公式来实现:挤出量 = 单位时间挤出重量 / 塑料的比重挤出量的计算方式有多种,下面将分别介绍常见的两种计算方式。
1. 根据挤出机的螺杆转速和进给速度计算挤出量在挤出机挤出过程中,螺杆的转速和进给速度是影响挤出量的两个重要参数。
根据这两个参数,可以通过如下公式计算挤出量:挤出量 = 螺杆转速× 进给速度× 单位时间其中,螺杆转速是指螺杆每分钟旋转的圈数,进给速度是指螺杆每分钟前进的距离。
单位时间可以根据实际需要来确定,常见的单位时间有小时、分钟等。
2. 根据挤出机的进给量和螺杆的截面积计算挤出量挤出机的进给量是指挤出机每分钟进给的塑料料柱的体积,螺杆的截面积是指螺杆槽横截面的面积。
根据这两个参数,可以通过如下公式计算挤出量:挤出量 = 进给量 / 螺杆截面积进给量可以通过测量料筒进给的长度来确定,螺杆截面积可以通过测量螺杆槽的宽度和深度来计算。
在实际应用中,根据不同的生产情况和需求,可以选择适合的挤出量计算方式。
同时,还需要注意以下几点:1. 在进行挤出量计算时,需要准确测量和记录相关参数,以确保计算结果的准确性。
2. 挤出量的计算结果应该与实际生产情况相符合,如果存在较大的偏差,可能需要检查和调整挤出机的工作参数。
3. 挤出量的大小会直接影响挤出产品的质量和生产效率。
合理控制挤出量可以提高产品的均匀性和一致性,降低生产成本。
4. 挤出量的计算对于挤出加工行业来说非常重要,它不仅可以用于生产计划和生产效率评估,还可以作为产品质量控制的依据。
挤出量的准确计算对于挤出加工行业来说至关重要。
通过选择合适的计算方式,并严格控制相关参数,可以提高产品的质量和生产效率,进而提升企业的竞争力和盈利能力。
4 挤压力计算及设备选择
2.反挤模具参数的影响 反挤凸模工作部分 的变化主要有三种形 式: ①R的影响(如右图) R,p。但R大到 一定程度之后对压力 的影响不明显了,所 以R要适当。
②ab的影响(如图) ab从0°, 9~11°时p 有显著,自260°下降到248Kg/mm。
而11°以上,ab 对压力的影响减弱。(曲线平坦了)
第四节 单位挤压力的理论计算法
一、主应力求解法 1.正挤实心件 2.反挤杯形件
d0 h1 p 2 (ln 2u )e d1 d1
2uh0 d0
2 2 2 d0 d0 d0 p 2 ln 2 2 +(1 3u)(1 ln 2 2 ) d 0 - d1 d1 d 0 - d1 (1 3u)(1 - ln(1 - F)) - ln(1 - F)/F
第六节 挤压力图算法
一.黑色金属挤压力图算法 1.图算法I(DVE)德国工程师协会 ①实心件正挤(如下图) 特点:考虑了 a.材质;b.润滑;c.正挤; d.F;e.h0/d0; f.a; g.V.等全部七种因素, 比较准确。
Ho/do =1.5 a=90 度 DT1
P=105 0
A=64
P=4600kn
五.有限元法
有限元法是利用计算机进行计算分析
第五节 单位挤压力的经验公式计算法 单位挤压力:p=Xnb
其中 n=aln(A0/A1)+b 对低碳钢 a=2.8 b=0.75 对有色金属 a=3.14 b=0.8 A0;A1--毛坯挤压以后的截面积 X--模具形状影响系数 镦挤力:p=ykA1 y--模具约束系数
七.变形速度的影响 (如图) 当F<40%时 ,硬化 为主, F -p
F>40%时, 热效 应为主 , F - p
- 1、下载文档前请自行甄别文档内容的完整性,平台不提供额外的编辑、内容补充、找答案等附加服务。
- 2、"仅部分预览"的文档,不可在线预览部分如存在完整性等问题,可反馈申请退款(可完整预览的文档不适用该条件!)。
- 3、如文档侵犯您的权益,请联系客服反馈,我们会尽快为您处理(人工客服工作时间:9:00-18:30)。
第4章挤出设备计算与选型
挤出生产线的设备计算
依据设计任务书,要求要设计年产量25万吨PUC-U塑钢型材生产车间,生产时间设置为6744小时。
选择的挤出机为TSH-135双螺杆挤出机,其生产能力为5000kg/h,则所需挤出机台数为:÷5÷6774=台,实际中取为8台。
即能完全符合产量要求,且留有增大产量空间,可减少机器满负荷运转的时段。
并且该PVC-U型材推拉框生产线,自动化程度高,性能稳定,变频调速等多项特点。
所以选用TSH-135双螺杆挤出机设备,其技术参数见表4-1[15]。
表4-1 锥形双螺杆挤出机设备工技术参数
混合机组的设备计算
高速混合机的选取与计算
每年需要高混的物料量为:
每天需要高混的物料量为:281=
每小时需要高混的物料量:24=
每10分钟可以混一锅料,则每小时混6锅料,则每锅混料量:6= PVC-U粉料的表观密度为m3,每锅可装粉料量:=;
则需要高混机的最小容积为。
所以选用WLD-H-35高速加热/冷却混合机组,其技术参数见表4-2。
表4-2 WLD-H-35热混机技术参数
高混机的有效容积取15m3,PVC-U粉料的表观密度为m3,每锅可装粉料量:×15= t
每10分钟可以混一锅料,则每小时混6锅料,则每小时混料量:
×6= t/h
需要高混机:×6744)=台
所以选用2台WLD-H-35热混机。
冷混机的选取与计算
与WLD-H-35热混机配套的冷混机可选用 WLD-H-35冷却机。
WLD-H-35冷却机技术参数见表4-3。
表4-3 WLD-H-35冷混机技术参数
需要冷混机的台数:×6744)=
所以选用2台WLD-H-35冷混机。
其它设备计算
粉碎机(技术参数见表4-4)及磨粉机(技术参数见表4-5)因只在回收粉碎废品时使用,年需破碎、磨粉量为吨,全年需要破碎下脚料为吨,选用PE-200×300型破碎机,每小时破碎量为3-6t/h,因此选用大型的PE-200×300型粉碎机和同规格的磨粉机即可满足生产;这些设备8条生产线选用一台机器就可满足生产要求。
表4-4 粉碎机设备技术参数
续表4-4 粉碎机设备技术参数
表4-9 磨粉机设备工艺技术参数
根据设备的耗水量技术参数:混合机组:5m3/h;PVC-U型材生产线:4m3/h。
根据冷水机的技术参数(见表4-10):h,1台设备满足生产条件。
表4-10 冷水机技术参数
续表4-10 冷水机技术参数
生产车间平面布置和工艺流程
生产工艺要求
(1)生产车间布置合理按照生产顺序布置设备,各条通道用途归置要合理避免相互交叉,车间内总体上要符合国家安全防火与环境保护的规定[16]。
(2)原材料取用要方便,运输路线合理布置,成品的堆放运输也要本着方便易行的原则。
(3)配电设备应尽可能靠近用电量大的设备,以减少电压降低和电能损耗;
(4)经济效果要好,在满足工艺要求的情况下,尽量减少占地面积,充分利用空间,以减少建设总投资费用,降低成本。
设备安转、检修
(1)再生产过程中,生产设备可能会存在一定几率的故障发生,所以在进行车间布局时一定考虑到设备的检修等行为所需要的空间,所以要在两条产线之间留有一定的空间,以避免在检修时不会对相邻的产线造成影响,降低生产效率。
(2)车间的大门应该足够机器进入车间。
大门的规格应比设备高~1m,比设备宽~,若属于一次性搬运,可考虑在安装位置的外墙预留墙洞,待设备安装后再砌封[17]。
(3)应有一定的面积和空间供设备检修、拆卸和运送物料用。
综上所述,生产车间平面布置总原则应该是简单实用、顺畅安全、经济效果要好。
完整的硬聚氯乙烯型材生产车间应包括车间办公室、卫生间、生产产线、成品仓库、配电房等。
根据布置的原则,在本设计中各个空间应该互相联通,从而节省空间并降低成本,同是增大了操作的安全系数。
厂房平面轮廓选用长方形,因为长方形厂房便于通道的布置,使设备可以紧凑,集中,经济效果好,便于生产管理,操作方便,采光通风也较好。
在这样布置中,可以将运输距离缩至最短,节省生产时间与人力消耗;配电房生产车间相邻,则方便操作,更减短电缆线布置长度,降低成本。
车间中生产线直线排列,前端预留3m的安全距离,而由于产品具有一定长度 6m,生产线的末端也预留了一定的安全距离[18]。