表面磨削力的建模和实验研究
磨削力数学模型的研究
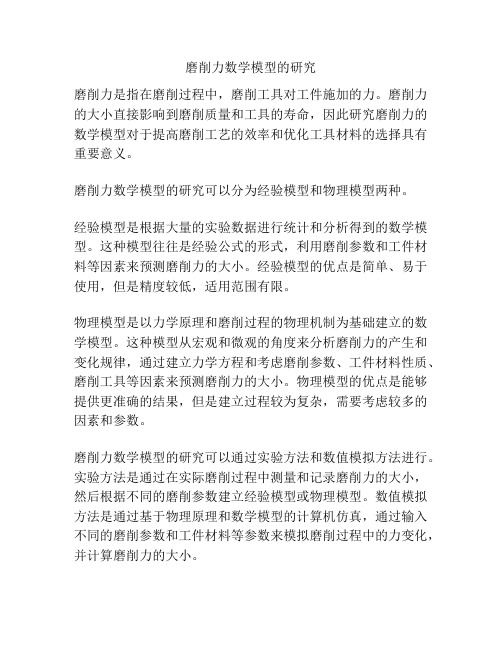
磨削力数学模型的研究
磨削力是指在磨削过程中,磨削工具对工件施加的力。
磨削力的大小直接影响到磨削质量和工具的寿命,因此研究磨削力的数学模型对于提高磨削工艺的效率和优化工具材料的选择具有重要意义。
磨削力数学模型的研究可以分为经验模型和物理模型两种。
经验模型是根据大量的实验数据进行统计和分析得到的数学模型。
这种模型往往是经验公式的形式,利用磨削参数和工件材料等因素来预测磨削力的大小。
经验模型的优点是简单、易于使用,但是精度较低,适用范围有限。
物理模型是以力学原理和磨削过程的物理机制为基础建立的数学模型。
这种模型从宏观和微观的角度来分析磨削力的产生和变化规律,通过建立力学方程和考虑磨削参数、工件材料性质、磨削工具等因素来预测磨削力的大小。
物理模型的优点是能够提供更准确的结果,但是建立过程较为复杂,需要考虑较多的因素和参数。
磨削力数学模型的研究可以通过实验方法和数值模拟方法进行。
实验方法是通过在实际磨削过程中测量和记录磨削力的大小,然后根据不同的磨削参数建立经验模型或物理模型。
数值模拟方法是通过基于物理原理和数学模型的计算机仿真,通过输入不同的磨削参数和工件材料等参数来模拟磨削过程中的力变化,并计算磨削力的大小。
磨削力数学模型的研究对于优化磨削工艺、提高加工效率和降低生产成本具有重要意义。
通过建立准确的数学模型,可以根据工件的材料性质和磨削参数来预测磨削力的大小,进而优化磨削工艺,提高磨削质量和工具的寿命。
同时,磨削力数学模型的研究还有助于选择合适的磨削工具材料和设计优化的磨削工具结构,提高磨削工具的耐用性和加工效率。
平面磨床的切削力建模与预测

平面磨床的切削力建模与预测平面磨床是一种常用的金属加工工具,广泛应用于各个领域的切削加工过程中。
切削力对于加工效率和加工质量具有重要影响,因此研究平面磨床的切削力建模和预测具有重要意义。
本文将针对平面磨床的切削力建模与预测展开讨论,并基于已有的研究成果进行分析和总结。
首先,切削力建模是研究平面磨床的切削力建模与预测的核心。
切削力的建模可以通过实验测量和理论分析两种方法进行。
实验测量方法是通过在实际切削过程中测量切削力的大小和变化趋势,然后将这些数据进行统计和分析。
理论分析方法是通过建立切削力的数学模型,基于切削参数和材料特性等因素对切削力进行模拟预测。
这两种方法可以相互结合,提高模型的准确性和可靠性。
其次,切削力的预测是基于建立好的切削力模型进行的。
根据模型的准确性和可靠性,可以预测切削力的大小和变化趋势。
切削力的预测可以帮助操作人员更好地控制切削过程,提高加工效率和加工质量。
预测切削力的方法可以分为基于经验公式和基于数学模型两种。
基于经验公式的方法是通过已有的实验数据和经验公式,根据切削参数和材料特性等因素进行切削力的估计和预测。
基于数学模型的方法是通过建立切削力的数学模型,基于切削参数和材料特性等因素进行切削力的计算和预测。
这两种方法可以根据具体情况选择使用,提高预测结果的准确性和可靠性。
在应用平面磨床的切削力建模与预测过程中,还需要考虑以下几点。
首先,切削参数的选择非常重要。
切削参数包括切削速度、进给速度和切深等因素,对切削力的大小和变化趋势有直接影响。
因此,在进行切削力建模和预测时,应根据实际情况选择合适的切削参数,并进行合理的调整和优化。
其次,材料的选择也是影响切削力的重要因素。
不同材料具有不同的硬度、韧性和切削性能等特点,对切削力的大小和变化趋势有直接影响。
因此,在进行切削力建模和预测时,应根据材料的特性进行合理的选择和分析。
最后,加工环境的控制也是切削力建模和预测过程中需要考虑的因素。
磨床的实验报告

磨床的实验报告
《磨床的实验报告》
在工业生产中,磨床是一种常见的加工设备,用于对工件进行精密加工和表面
处理。
为了更好地了解磨床的工作原理和性能特点,我们进行了一系列的实验
研究,并撰写了以下实验报告。
实验一:磨削力的测试
我们首先对磨床进行了磨削力的测试。
通过安装力传感器和数据采集系统,我
们对磨床在不同工艺参数下的磨削力进行了实时监测和记录。
实验结果显示,
磨床的磨削力受到磨料、工件材料、磨削速度等因素的影响,不同参数下的磨
削力表现出明显的差异。
实验二:磨削精度的评估
接着,我们对磨床的磨削精度进行了评估。
通过测量工件的尺寸和表面粗糙度,我们对磨床在不同工艺条件下的加工精度进行了分析。
实验结果显示,磨床的
磨削精度受到磨料磨损、磨削温度、磨削液等因素的影响,需要在实际生产中
进行精心调控。
实验三:磨削温度的测量
最后,我们对磨床的磨削温度进行了测量。
通过安装温度传感器和红外线测温仪,我们对磨床在不同工艺参数下的磨削温度进行了实时监测。
实验结果显示,磨床的磨削温度受到磨削速度、磨料性能、冷却液等因素的影响,需要加强对
磨削温度的控制和管理。
通过以上一系列实验研究,我们对磨床的工作原理和性能特点有了更深入的了解,为进一步优化磨床的加工效果和提高生产效率提供了重要的参考和依据。
希望本实验报告能够为相关领域的研究和生产实践提供有益的启示和借鉴。
磨削加工过程中机械表面质量的实验研究与分析

【活动背景】 纸是现代社会不可获缺的重要载体,在人类 的日常生活、学习、工作中有着广泛的用途。它的 出现促进了人类社会文明的进步,给人类带来极 大的便利。但是现在大部分的学生知道“树”是造 纸的原料,在我们的身边浪费严重的纸张可以重 新造出新的纸,此次活动的开展,以学生制作再生 纸为目的,让学生在探索与创造的过程中,体验制 作再生纸的乐趣,培养学生的动手能力,满足了孩 子的探究欲望、培养了他们勤俭节约,保护环境的 意识。 【活动目标】 1.让学生了解制作纸的众多材料中,用过的 废纸也能够再造出新纸来。 2.让学生知道再生纸的制作流程:制浆、抄 纸、压水、揭纸和晾干。 3.让学生亲身体验制作一张再生纸的乐趣。 【重点、难点】 1.重点:了解了解再生纸的制作的方法。 2.难点:能利用废纸制作再生纸。 【材料准备】 一张废纸、毛巾、矿泉水瓶、小石块、筛网、水 槽、泡沫块。 【活动过程】 (一)导入
- 189 -
综合园地
2016 年第 6 期
师:这节课,我们就上到这边,下课!
给了学生充分的活动空间和时间,又给了学生适
生:老师再见。
时的指导与帮助,这些做法都符合培养学生创新
师:同学们再见。
精神这一课程核心。同时,精心制作课件,即有理
专家点评
论的指导也有实践的参与,对帮助学生掌握再生
郑老师的《再生纸的制作》这一课,给我留下 了深刻的印象。下面就这节综合实践课谈谈我的 体会:
- 188 -
2016 年第 6 期 给大家准备再生纸制作的视频,请同学们认真观 看视频,并且记录再生纸的制作的流程,看看,屏 幕上的这些材料和工具都有哪些的用途,好不好?
生:好 PPT 播放再生纸制作的微视频(5 分钟) 师:同学们,制作再生纸都有哪些流程呢? 第一步是“制浆”,接第二布是“抄纸”,第三步 是“挤压”,第四步是“揭纸”,最后是“晾干”。 师:现在,你们知道怎么制作再生纸了吗? 生:知道 师:在活动之前老师还要给大家一个温馨提 示 PPT 展示:温馨提示 1.小组分工,合作完成。 2.制作过程,轻声细语。 3.小心用水,勿湿桌面。 4.音乐响起,安静坐好。 师:可以做到吗? 生:可以 (三)制作再生纸 师:当你们拿到材料之后就可以开始活动了。 现在请小组长上来领取活动材料。 生:(制作再生纸中……10 分钟后音乐响起) 师:你们都成功做出再生纸了吗? 生:成功了。 (四)比一比 师:请每个小组派出一位同学带上你们做的 最好的一张再生纸,到前面展示给大家,看看哪个 小组的再生纸做的最好。 师:同学们评一评,哪个小组的再生纸做的最 好,为什么? 生:我觉得,第一小组的再生纸做的最好,因 为他的纸做的比较细腻 师:观察的真仔细,你们都同意吗?你有不同 意见,请你说 生:我觉得第二的小组做的比较好,因为他的 再生纸做的很圆 师:你的表达非常清晰,大家一听就明白。你
硬脆材料精密磨削的磨削力及表面质量测试与分析实验
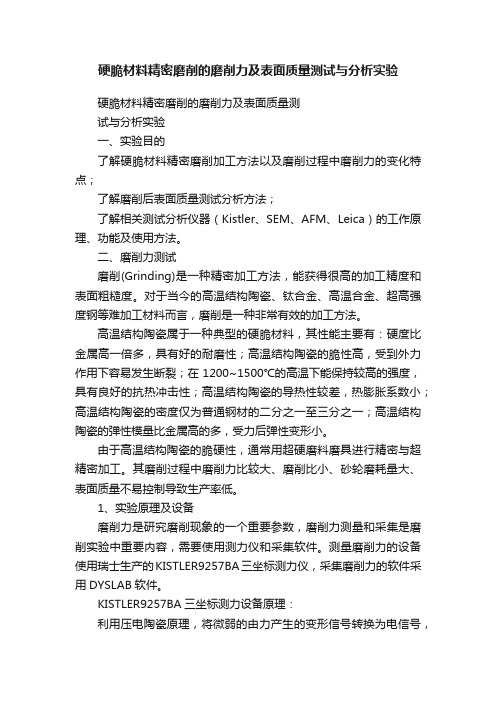
硬脆材料精密磨削的磨削力及表面质量测试与分析实验硬脆材料精密磨削的磨削力及表面质量测试与分析实验一、实验目的了解硬脆材料精密磨削加工方法以及磨削过程中磨削力的变化特点;了解磨削后表面质量测试分析方法;了解相关测试分析仪器(Kistler、SEM、AFM、Leica)的工作原理、功能及使用方法。
二、磨削力测试磨削(Grinding)是一种精密加工方法,能获得很高的加工精度和表面粗糙度。
对于当今的高温结构陶瓷、钛合金、高温合金、超高强度钢等难加工材料而言,磨削是一种非常有效的加工方法。
高温结构陶瓷属于一种典型的硬脆材料,其性能主要有:硬度比金属高一倍多,具有好的耐磨性;高温结构陶瓷的脆性高,受到外力作用下容易发生断裂;在1200~1500℃的高温下能保持较高的强度,具有良好的抗热冲击性;高温结构陶瓷的导热性较差,热膨胀系数小;高温结构陶瓷的密度仅为普通钢材的二分之一至三分之一;高温结构陶瓷的弹性模量比金属高的多,受力后弹性变形小。
由于高温结构陶瓷的脆硬性,通常用超硬磨料磨具进行精密与超精密加工。
其磨削过程中磨削力比较大、磨削比小、砂轮磨耗量大、表面质量不易控制导致生产率低。
1、实验原理及设备磨削力是研究磨削现象的一个重要参数,磨削力测量和采集是磨削实验中重要内容,需要使用测力仪和采集软件。
测量磨削力的设备使用瑞士生产的KISTLER9257BA三坐标测力仪,采集磨削力的软件采用DYSLAB软件。
KISTLER9257BA三坐标测力设备原理:利用压电陶瓷原理,将微弱的由力产生的变形信号转换为电信号,根据事先标定的值得到力值。
测力仪在上面板和底板之间有四个三向力传感器,它们都不接地。
隔热层保护传感器不受外界温度影响。
将测力仪用管接头和控制单元设备5233A1连接构成了测力系统(图1) 。
2、检测软件DASYLab是一个集数据采集、过程控制及数据分析于一体的软件系统。
在DASYLab中,通过选择和任意摆放模块元素,并且把鼠标把这些模块元素连接起来,能够直接在屏幕上对测量、过程控制或者仿真任务进行设置。
外圆磨削18CrNiMo7G6力模型及表面完整性研究

第35卷第3期中国机械工程V o l .35㊀N o .32024年3月C H I N A M E C HA N I C A LE N G I N E E R I N Gp p.381G393外圆磨削18C r N i M o 7G6力模型及表面完整性研究王㊀栋㊀陈㊀磊㊀张志鹏郑州大学机械与动力工程学院,郑州,450001摘要:为了准确和有效地控制磨削参数对磨削力及表面完整性的影响,通过解析法,以磨粒与材料间的塑性变形㊁压痕理论以及剪切应变效应为理论依据,建立了三阶段的磨削力理论模型.选定棕刚玉砂轮进行磨削试验,探究了磨削参数对磨削力的影响以及磨削参数和磨削力对表面完整性的影响,通过外圆横向磨削正交试验获得了外圆磨削最优工艺参数.结果表明,外圆磨削力模型法向磨削力和切向磨削力的预测平均误差分别为5.56%和7.08%;砂轮径向进给速度f r 对磨削力的影响最大,磨削宽度b 次之,工件转速n w 和砂轮粒度的影响较小;f r 和b 对残余应力的影响较大,砂轮粒度对表面粗糙度的影响最大;随着磨削力的增大,表面粗糙度值一直增大,残余应力先减小后增大,沿深度方向残余应力最大值先增大后减小,在试验所取参数条件下,影响残余应力的深度分布范围基本在20~40μm ;最优工艺参数组合如下:f r =0.15mm /m i n ,n w =120r /m i n ,b =10mm ,砂轮粒度80.关键词:外圆磨削;横向磨削;磨削力模型;18C r N i M o 7G6钢;表面完整性中图分类号:T H 16;T G 58D O I :10.3969/j .i s s n .1004 132X.2024.03.001开放科学(资源服务)标识码(O S I D ):S t u d y o nF o r c eM o d e l a n dS u r f a c e I n t e g r i t y o fC y l i n d r i c a lG r i n d i n g18C r N i M o 7G6S t e e l sWA N G D o n g ㊀C H E N L e i ㊀Z H A N GZ h i p e n gS c h o o l o fM e c h a n i c a l a n dP o w e rE n g i n e e r i n g ,Z h e n g z h o uU n i v e r s i t y ,Z h e n gz h o u ,450001A b s t r a c t :I no r d e r t oa c c u r a t e l y a n de f f e c t i v e l y c o n t r o l t h e i n f l u e n c e so f g r i n d i n gpa r a m e t e r so n g r i n d i n g f o r c ea n ds u r f a c e i n t e g r i t y ,at h r e e Gs t a g e g r i n d i n g f o r c et h e o r e t i c a lm o d e lw a se s t ab l i s h e d b a s e do n t h e p l a s t icdef o r m a t i o n ,i n d e n t a t i o n t h e o r y an d s h e a r s t r a i n e f f e c t b e t w e e n a b r a s i v e p a r t i c l e s a n dm a t e r i a l s b y a n a l y t i c a lm e t h o d .T h eb r o w nc o r u n d u m g r i n d i n g w h e e l sw e r e s e l e c t e d f o r g r i n d i n g e x p e r i m e n t s t o e x p l o r e t h e e f f e c t s o f g r i n d i n gp a r a m e t e r s o n g r i n d i n g f o r c e a n d t h e e f f e c t s o f g r i n d i n g p a r a m e t e r s a n d g r i n d i n g f o r c e o ns u r f a c e i n t e g r i t y .T h eo p t i m a l p r o c e s s i n gp a r a m e t e r s f o r c y l i n d r i c a l g r i n d i n g w e r e o b t a i n e d t h r o u g ho r t h o g o n a l e x p e r i m e n t s o f c y l i n d r i c a l t r a n s v e r s e g r i n d i n g .T h e r e s u l t s s h o wt h a tt h ea v e r a g e p r e d i c t i o ne r r o r so fn o r m a la n dt a n g e n t i a l g r i n d i n g f o r c e s i nt h ec y l i n d r i c a l g r i n d i n g f o r c em o d e l a r e 5.56%a n d 7.08%,r e s p e c t i v e l y .T h e r a d i a l f e e d s p e e do f t h e g r i n d i n g wh e e l h a s t h e g r e a t e s t i m p a c t o n g r i n d i n g f o r c e ,f o l l o w e d b y g r i n d i n g w i d t h ,a n d t h e i n f l u e n c e s o fw o r k pi e c e s p e e d a n d g r i n d i n g w h e e l p a r t i c l e s i z e a r e r e l a t i v e l y s m a l l .T h e r a d i a l f e e d s p e e d a n d g r i n d i n g wi d t ho f t h e g r i n d i n g w h e e l h a v eas i g n i f i c a n t i m p a c to nr e s i d u a l s t r e s s ,a n dt h e p a r t i c l es i z eo f t h e g r i n d i n gw h e e l h a st h e g r e a t e s t i m p a c to ns u r f a c er o u g h n e s s .A st h e g r i n d i n g fo r c ei n c r e a s e s ,t h es u r f a c e r o u g h n e s s v a l u e c o n t i n u o u s l y i n c r e a s e s ,a n dt h er e s i d u a l s t r e s s f i r s t l y de c r e a s e sa n dt h e n i n c r e a s e s .T h em a x i m u m r e s i d u a ls t r e s sv a l u ea l o n g t h ed e p t hd i r e c t i o nf i r s t l y in c r e a s e sa n dt h e nd e c r e a s e s .W i t h i n t h e p a r a m e t e r s t a k e n i nt h e e x p e r i m e n t s ,t h ed i s t r i b u t i o nr a n g eo f r e s i d u a l s t r e s s i sb a s i c a l l y20~40μm.T h e o p t i m a l c o m b i n a t i o no f p r o c e s s i n gp a r a m e t e r s i s a r a d i a l f e e d s pe e dof 0.15mm /m i n f o r t h eg r i n d i n g wh e e l ,aw o r k pi e c e s p e e do f 120r /m i n ,a g r i n d i n g w i d t ho f 10mm ,a n da g r i n d i n gw h e e l pa r t i c l e s i z e o f 80.K e y wo r d s :c y l i n d r i c a l g r i n d i n g ;p l u n g e g r i n d i n g ;g r i n d i n g f o r c em o d e l ;18C r N i M o 7G6s t e e l ;s u r Gf a c e i n t e g r i t y收稿日期:20230718基金项目:国家自然科学基金重点项目(U 1804254);河南省重大科技专项(201400211200)0㊀引言外圆磨削具有较高的材料去除能力和加工精度,普遍应用于难切削材料的轴类零件加工生产中[1],尤其是在零件的最终加工阶段,需要保证较好的表面完整性和精确的公差,外圆磨削工艺是实现这一目标的最优加工方法[2].由于外圆磨削加工过程中影响加工质量的参数较多,且它们之183间也会相互影响,其中磨削力是与磨削参数和磨削质量相关的重要过程变量,常常被用来对磨削质量进行分析和预测,故建立科学㊁可靠的外圆磨削力理论模型进行外圆磨削力和工件表面完整性试验研究,探究磨削参数对磨削力的影响,揭示磨削参数对表面完整性的影响过程,对外圆磨削力的预测㊁磨削机理的研究和外圆磨削加工参数优化具有重要意义[3].近年来,国内外学者在磨削力的产生机理㊁加工参数的影响规律和预测模型等方面进行了诸多研究.尹国强等[4]通过有限元仿真和数学解析的方法研究了微磨削加工机理,并构建了相应的磨削力预测模型.L I U等[5]提出了晶粒有效作用面积的概念,在随机晶粒的几何特征基础之上建立了更为完善的磨削力模型.Z H A N G等[6]利用锥形磨粒等效模型,考虑塑性堆积和材料去除机理,建立了磨削力模型,并确定了磨削耕犁和切屑形成阶段的临界切削厚度,以未变形的切屑厚度来区分滑擦㊁耕犁和切屑形成阶段.J AM S H I D I 等[7]考虑磨粒与工件之间的微观相互作用,针对平面磨削建立了一种考虑不同磨削阶段的磨削力预测模型,该模型对于切向磨削力和法向磨削力预测的误差分别为12%和11%.S A V A R I A 等[8]基于著名的C r o s s l a n d准则,提出了一种考虑微观组织变化㊁残余应力和表面粗糙度的三维疲劳模型来预测航空感应表面淬火正齿轮的弯曲寿命极限,研究结果表明,残余应力对弯曲疲劳寿命有着显著影响.S U N等[9]提出了一种考虑综合动态特性㊁机械热相互作用和相变效应的残余应力预测模型,结果表明,随着磨削位置和切削深度的变化,残余应力分布的一致性有很大的变化,相比之下,在稳定磨削区,切削深度越大,残余压应力越大.X I A O等[10]通过试验重点探索了残余应力对疲劳寿命的影响,发现在一般情况下,磨削热作用下的热塑性变形和塑性变形效应产生拉伸残余应力,磨粒机械应力导致挤光效应,从而产生残余压应力,同时,残余压应力可以提高疲劳寿命,而任何程度的残余拉应力对疲劳寿命都会有负面影响.在难切削材料中,加工后的表面粗糙度和残余应力一直是超精密加工领域的主要研究对象,对提高关键零部件的疲劳寿命和评定磨削性能具有重要作用.本文在建立的外圆磨削力模型基础上,将磨削力作为中间变量,分析磨削参数㊁磨削力和表面完整性的关系.1㊀外圆磨削砂轮选取试验1.1㊀试验条件及检测装置本试验测试工件为18C r N i M o7G6渗碳钢圆棒,其工件尺寸是ϕ24mmˑ80mm,渗碳层厚度为1.3~1.6mm,18C r N i M o7G6钢的化学成分及机械性能参数分别见表1㊁表2.试验所用磨床为数控外圆磨床MK E1620A,采用棕刚玉砂轮进行切入式逆向磨削,砂轮结构尺寸为400mmˑ35mmˑ203mm.使用水基乳化液进行降温.在磨削过程中由砂轮磨耗磨损㊁磨屑细小等因素导致砂轮磨损㊁堵塞所产生的问题不容忽视,本试验选用单颗粒金刚石笔修整砂轮,每进行完4组试验后对砂轮修整一次,将修整后的砂轮预磨工件2次,使其进入正常磨削状态后再进行磨削试验.表1㊀18C r N i M o7G6钢的化学成分(质量分数)T a b.1㊀C h e m i c a l c o m p o s i t i o n(m a s s f r a c t i o n)o f18C r N i M o7G6s t e e l%w(C)w(S i)w(M n)w(S)w(P)0.15~0.210.40.5~0.9<0.035<0.035w(C r)w(N i)w(M o)w(C u)1.5~1.81.4~1.70.25~0.35ɤ0.3表2㊀18C r N i M o7G6钢的机械性能参数T a b.2㊀M e c h a n i c a l p r o p e r t i e s o f18C r N i M o7G6s t e e l 弹性模量(G P a )屈服强度(M P a)抗拉强度(M P a )21010161220泊松比υ维氏硬度(HV)延展率(%)0.1570614㊀㊀试验及检测装置如图1所示.磨削加工过程中使用D y n o W a r e软件进行磨削力信号数据的采集及处理,测力装置由K i s t l e r公司生产的9257B 三坐标测力仪改装得到,如图1a所示.采用图1b所示高速X射线残余应力分析仪(P r o t oGL D R(a)K i s t l e r磨削力检测平台㊀(b)残余应力分析仪㊀㊀(c)三维形貌测量系统图1㊀试验及检测装置F i g.1㊀E x p e r i m e n t a l a n d t e s t i n g e q u i p m e n t283中国机械工程第35卷第3期2024年3月型)对试样表面的残余应力进行测量,其测量原理是利用X射线衍射技术测量材料中晶体的变形和应变,从而计算出残余应力.试验检测工件表面及表层沿深度方向的残余应力,每一层在加工区域选取三个检测点,取其均值作为残余应力的测量值.采用非接触N P F L E X型三维形貌表面测量系统对改性后试样三维形貌以及表面粗糙度值进行测量,如图1c所示.1.2㊀外圆磨削试验方案现有的外圆磨床砂轮的转速为恒定值1488r/m i n,试验所用砂轮的直径为400mm,砂轮线速度为31.2m/s.本文选取工件转速n w㊁磨削宽度b及砂轮径向进给速度f r作为试验参数,并设置进给量为0.2mm,即总磨削深度a p=0.2mm.结合现有设备能力,制定试验方案前通过开展预试验工作来缩小最优参数水平范围,试验方案见表3㊁表4.测量磨削力时每组参数做三组试验,并求其平均值作为最终磨削力数值.每根工件均选取五个点对粗糙度与表面残余应力进行测量,并去除最小与最大值,剩下三个取平均值作为最终数值.表3㊀外圆磨削正交试验参数T a b.3㊀G r i n d i n g w h e e l s e l e c t i o n e x p e r i m e n t p a r a m e t e r s径向进给速度f r(mm/m i n)工件转速n w(r/m i n)磨削宽度b(mm)砂轮粒度(目)0.15,0.30,0.45,0.6060,90,120,15010,20,30,4046,60,80,100表4㊀外圆磨削单因素试验参数T a b.4㊀S i n g l e f a c t o r t e s t p a r a m e t e r s o f c y l i n d r i c a l g r i n d i n g序号径向进给速度f r(mm/m i n)工件转速n w(r/m i n)磨削宽度b(mm)砂轮粒度(目)10.1520.330.4540.6120308056780.36090120150308091011120.31201020304080131415160.3120304660801002㊀外圆磨削力模型理论推导磨削过程具有一定的复杂性,故从简化的单个磨粒开始进行研究.目前研究中一般将磨粒形状分为四种类型:圆锥形㊁球形㊁圆台形和棱锥形.虽然磨粒形状会对磨削力的大小产生影响,但磨削力产生机理不会因此而改变,故在推导单磨粒模型时可以选择圆锥形作为磨粒简化模型[11G12].本研究使用在理论模型研究中普遍应用的圆锥角为2θ的等效圆锥磨粒模型.磨削过程中,由于磨粒与工件的作用方式不同,通常将其分为三个阶段,分别为滑擦㊁耕犁与切屑形成,如图2所示.其中,f a为单个磨粒的平均切削深度,h g c为临界未变形切屑厚度,h g m为最大未变形切屑厚度,其单位均为mm.图2㊀单磨粒磨削过程示意图F i g.2㊀S c h e m a t i c d i a g r a mo f s i n g l e a b r a s i v eg r i n d i n gp r o c e s s在横向外圆磨削中,轴向磨削力F a远小于法向磨削力F n和切向磨削力F t,可以忽略.因此,根据磨削阶段的划分,总磨削力可分为切向磨削力F t和法向磨削力F n:F t=F t s l+F t p g+F t c hF n=F n s l+F n p g+F n c h}(1)式中,F n s l㊁F n p g㊁F n c h分别为法向滑擦力㊁耕犁力和切屑形成力;F t s l㊁F t p g㊁F t c h分别为切向滑擦力㊁耕犁力和切屑形成力.2.1㊀滑擦力YO U N I S等[13]的试验结果表明,滑擦阶段的法向磨削力和工件与磨粒实际磨损平面或接触面积δ㊁磨削时工件单位面积所受的平均接触压力Δp成正相关,因此,单颗磨粒在滑擦阶段的法向磨削力Fᶄn s l为Fᶄn s l=δΔp(2)工件和砂轮间的平均接触压力Δp几乎与砂轮当量半径和切削路径的曲率半径偏差η成正比[14]:Δp=p0η=4p0v wv s d s(3)式中,p0为常数;v w为工件线速度,m/s;v s为砂轮速度, m/s;d s为砂轮直径,mm.砂轮表面随机分布了大量的磨刃,为了表示实际参与磨削的有效磨刃,本文将磨粒近似视为圆锥形,引入砂轮表面静态磨粒密度N s,其表达式为[15]383外圆磨削18C r N i M o7G6力模型及表面完整性研究 王㊀栋㊀陈㊀磊㊀张志鹏N s =C 2/3ad 2g (13πs i n θ2c o s θ)2/3=C 2/3a k s d 2g (4)k s =[(πs i n θ2c o s θ)/3]2/3其中,C a 为砂轮磨粒浓度,mm -3;d g 为砂轮磨粒平均粒径,mm .根据砂轮特性及工作条件的不同,有效磨粒数约占砂轮表面总磨粒数的10%~50%[16],故动态有效磨刃密度N d 为沿砂轮与工件接触弧上测得的单位面积上的有效磨粒数,即N d =αd N s(5)式中,αd 为动态与静态磨刃数的比例系数.则动态有效磨粒总数N d t 可表示为N d t =αd N s l c b =k s αd C 2/3a l cb /d 2g(6)其中,l c 为几何接触弧长;b 为有效磨削宽度;d g 为砂轮粒径.在切入式外圆磨削中,几何接触弧长l c 和砂轮当量直径d e 分别为[17]l c =f ad e d e =d s d wd s +d w}(7)式中,f a 为工件每转的磨削深度;d w 为工件直径.由于磨粒分布随机性与加工过程中的机械应力和磨削热引起的磨粒脱落与破碎现象,工作磨粒中仅有一部分起摩擦作用,一部分只在工件表面划出沟痕,还有一部分仅与工件表面发生切削.假设滑擦㊁耕犁和切屑形成阶段中的动态有效磨粒数占比分别为εs l ㊁εp g 和εc h ,则可得到不同阶段动态有效磨粒数[18]:[N d s l ㊀N d p g ㊀N d c h ]T =N d t [εs l ㊀εp g ㊀εc h ]T(8)其中,N d s l ㊁N d p g ㊁N d c h 分别为滑擦阶段㊁耕犁阶段和切屑形成阶段的动态有效磨粒数.由式(3)㊁式(4)和式(8),可得滑擦阶段总法向磨削力F n s l :F n s l =N d s l δp -=k 1f 0.5a bv w d g 2v s d sd s d wd s +d w(9)k 1=4k s εs l p 0δαd C 2/3a其中,k 1单位为N /mm 2.因此,总的切向滑擦力可表示为F t s l =μ1F n s l =k 2f a 0.5b v wd 2g v s d sd s d wd s +d w(10)k 2=μ1k 1式中,μ1为滑擦阶段的平均摩擦因数.2.2㊀耕犁力Z H A N G 等[6]研究发现,耕犁力产生的主要原因是切削过程中材料发生的塑性变形,与材料特性和磨削中的加工参数有关.为了计算总法向和切向耕犁力对单位宽度磨削面积的影响,P A T N A I K 等[19]通过结合可变摩擦因数和耕犁力的综合效应来模拟总磨削力,该模型展示了包括耕犁力的重要性.划痕硬度H s 是工件材料的抗划擦强度,为磨粒耕犁阶段的法向力F n g 与划痕的承载面积A b 的比值.据此建立单磨粒耕犁力模型的基础形式:F ᶄn p g =H sA b =H s e (e +h )t a n 2α=㊀H s e c ᶄd g 2t a n αt a n 2α=k n p gt a n αH s e d g F ᶄt p g =A 1F n g =A 1k n p g t a n αH s e d g =k t p gt a n αH s e d g üþýïïïï(11)k n p g =c ᶄ/2㊀㊀k t p g =A 1k n p g其中,k n p g ㊁k t p g 为常数;A b 为耕犁面积;e 为磨粒划擦深度;H 为去除材料堆积高度;α为磨料半顶点角;c ᶄ为乘法系数;A 1为切向耕犁力与法向耕犁力比值常数,取决于工件的材料特性[20].该模型的具体形式如图3所示.图3㊀磨粒耕犁过程模型F i g .3㊀G r i n d i n g g r a i n p l o u g h i n gpr o c e s sm o d e l 根据塑性变形理论,二维划擦变形下的划痕硬度H s 随磨削深度和工件线速度的增大而增大,随砂轮线速度的增大而减小,因此,H s e d g 经验公式可表示为[19]㊀H s e d g =f (v s ,v w ,f a ,d g )=εv αa w v1-αa s f ∂b a d αc g (12)式中,ε为常数;αa ㊁αb ㊁αc 为指标系数.由式(11)和式(12),可将单磨粒的切向耕犁力和法向耕犁力进一步表示为F ᶄn p g =k n p g εt a n α(v w /v s )αa f αb a d αc g F ᶄt p g =k t p g εt a n α(v w /v s )αa f αb a d αc g}(13)由式(8)和式(13)得到总的法向耕犁力和切向耕犁力的模型:F n p g =k n p g εN d p g t a n α(v w /v s )αa f αb a d αc g F t p g =k t p g εN d p g t a n α(v w /v s )αa f αb a d αc g}(14)由式(5)~式(8)㊁式(14)更进一步得到F n p g =k3(v w v s )α1f α2a d α3g b d s d w d s +d w F t p g =k4(v w v s )α1f α2a d α3g b d s d w d s +d w üþýïïïï(15)k 3=k n p g εk s αd C 2/3a εp gt a n αk 4=k t p g εk s αd C 2/3a εp gt a n αα2=αb +0.5α3=αc -2式中,k 3㊁k 4㊁α1㊁α2㊁α3为待求系数.2.3㊀切屑形成力的分析与建模2.3.1㊀切屑形成能外圆磨削的切屑形成阶段是一个非常复杂的483 中国机械工程第35卷第3期2024年3月过程[21G22],它可以简化为数以万计的切削刃去除工件材料.因此,某种程度上可以认为,单颗粒磨削过程中的材料去除机理与传统的车削和铣削类似,都可以认为是剪切去除,故剪切应变效应也可用于研究磨削过程中的切屑形成力.磨削比能u 表示在磨削过程中去除工件上单位体积的材料所消耗的能量[23],即u =F t v s b v w f a(16)根据上式可得到具体的切屑形成能u c h (单位J /mm 3):u c h =F t c hv s b v w f a(17)同时,已知切屑形成能主要由材料去除过程中的剪切能和刀具摩擦能组成,其剪切能占75%,刀具摩擦产生的能量占25%[15],则剪切能与切屑形成能的关系为u c h =u s h +u r h u c h =ωu s h}(18)式中,u s h 为材料去除过程中的剪切能;u r h 为材料去除过程中的摩擦能;ω为常数(通常ω>1).2.3.2㊀材料动态塑性本构关系在剪切变形中,动态塑性变形的本构关系表示为[23]τ=f (γ,γ,T )(19)式中,τ为剪切流变应力;γ为剪切应变;γ为剪切应变速率;T 为材料变形温度.随着γ㊁γ的增大,材料的剪切流变应力τ也会增大.随着变形温度的升高,材料的剪切流变应力τ减小.动态剪切能u s h 与剪切流变应力成正比,是剪切应变效应㊁剪切应变速率效应和热软化效应共同作用的结果[23].单粒磨削剪切变形如图4所示.图4㊀单粒磨削剪切变形示意图F i g .4㊀S c h e m a t i c d i a g r a mo f s i n g l e g r a i n g r i n d i n gs h e a r d e f o r m a t i o n根据切削变形理论,二维剪切变形下的剪切应变率经验公式可表示为[18]γ=k γv βa w v 1-βa sf βb a d βc s c o s θ(20)式中,k γ为常数;βa ㊁βb ㊁βc 为指标系数;θ为刀具前角,即圆锥顶角.根据试验所设总切削深度a p =0.2mm ,时间t =0.2/f r ,在外圆磨削过程中剪切应变γ与v w ㊁v s ㊁d s 的关系式为γ=ʏ0.2/f0k γv βa w v 1-βa sf βb a d βcs c o s θd t (21)单位体积内的剪切应变能[24]记作v ε:v ε=τγ/2(22)其中,τ为剪切应力,γ1为相应的剪切应变.由剪切胡克定律知τ=G γ,G 为剪切模量,则上式可以写成v ε=τγ/2=G γ2/2(23)2.3.3㊀切屑形成力假设外圆磨削过程中产生的切屑都具有相同的体积和形状,且在单位时间内产生每个切屑的体积与切屑数量的积等于材料体积的去除率,N ᶄd 为切削刃密度即砂轮单位面积上的动态有效磨粒数,V c 为单个切屑的体积,则有[25]N ᶄdb v s Vc =f a v w b (24)如图5所示,假定切屑宽度b 与最大未变形厚度h g m 成正比r ,在h g m ≪l c 的情况下,未变形切屑的形状近似为一个三棱锥,由三棱锥体积计算公式可知,切屑体积是切屑最大截面积r h 2gm /2和长度l c 乘积的1/3[25],即V c =r h 2gm l c /6(25)图5㊀三角形切屑示意图F i g .5㊀S c h e m a t i c d i a g r a mo f t r i a n g u l a r c h i p磨粒的顶锥角为2θ,则r =2t a n θ,最大未变形厚度h g m 计算公式为h g m =(1t a n θN d v wv sf a d e)1/2(26)将式(26)代入式(25),得到切屑体积V c :V c =r h 2g m l c6=3r v w f a 6t a n θv s N d(27)根据式(21)㊁式(23)㊁式(27),单颗磨粒去除单位材料体积的剪切应变能可表示为u s h =G γ2V c /2=k s h v 2βa +1wd 2β3s N d v 2βa -1sf 2r (28)k s h =124r 6250c o s 2θt a n θG k 2γ=c o s 2θ75t a n θG k 2γ由式(17)㊁式(18)可得到单颗磨粒在切屑形成阶段的切向力F ᶄt c h :㊀F ᶄt c h =ωu s h b v w f a /v s =k t c hv 2βa +2wf 2βb +2a d 2βc s b N d v 2βa s f 2r(29)k t c h =ωk s h583 外圆磨削18C r N i M o 7G6力模型及表面完整性研究王㊀栋㊀陈㊀磊㊀张志鹏根据F n c h =F t c h /μ2,可以得到单颗磨粒的法向切屑形成力:F ᶄn c h =k n c hv 2βa +2w f 2βb +2a d 2βcs bN d v 2βasf 2r(30)根据式(5)~式(8),由式(30)更进一步得到总的切屑形成力:F n c h =k 5v β1w f β2a d β3s b2vβ1-2sf2rd s d w d s +d w F t c h =k 6v β1w f β2a d β3s b2vβ1-2sf2rd s d w d s +d w üþýïïïï(31)k 5=k n c h εc h ㊀㊀k 6=k t c h εc h ㊀㊀β1=βa +2β2=βc +2.5㊀㊀β3=2βc 式中,k 5㊁k 6㊁β1㊁β2㊁β3为待定系数.2.4㊀磨削力预测模型通过对滑擦㊁耕犁和切屑形成力的分析,分别得到相应关系式,总的磨削力模型可以表示为F n =bd s d w d s +d w (k 1f 0.5av w d 2g v s d s+k 3(v w v s )α1f α2a d α3g +㊀k 5v β1w f β2a d β3s b v β1-2sf 2r )F t =b d s d w d s +d w (k 2f 0.5a v w d 2g v sd s +k 4(v w v s )α1f α2a d α3g +㊀k 6v β1w f β2a d β3s b v β1-2sf 2r )üþýïïïïïïïïïï(32)3㊀外圆磨削力模型的求解及验证3.1㊀模型求解通过式(32)可以更为具体地了解外圆磨削力及各因素的影响程度,为了准确预测分析各磨削参数对磨削力的影响效果,就必须求解出公式中的各个待求系数,因此开展正交试验,并基于遗传算法优化非线性优化函数的方法针对上述模型进行求解[26].试验方案及正交试验因素水平见表5.表5㊀正交试验因素水平T a b .5㊀O r t h o g o n a l e x pe r i m e n t a lf a c t o r l e v e l 序号进给速度f r (mm /m i n )工件转速n (r /m i n)磨削宽度b (mm )砂轮粒度(目)法向力F n (N )切向力F t (N )10.156010468.304.1020.3060206026.6112.0130.4560308053.0026.7040.60604010070.0338.8350.1590208012.856.2760.30901010010.315.5670.4590404663.9633.8080.6090306059.4027.8590.151203010018.199.66100.30120408041.4123.49110.45120106013.997.00120.60120204643.0518.78130.15150406026.2114.07140.30150304632.9716.69150.451502010026.6113.78160.60150108019.919.60㊀㊀遗传算法经过选择㊁交叉和变异等操作从而达到预定的优化目标,获得相应个体的最优适应度,从而得到初始最优系数组合并作用于非线性优化函数.非线性优化函数搜寻到16组试验数据最小残差值的结果为8.05.最终得到外圆磨削力最优系数组合,见表6.表6㊀最终系数结果T a b .6㊀F i n a l c o e f f i c i e n t r e s u l tk ᶄ1k ᶄ2k ᶄ3k ᶄ4k ᶄ5k ᶄ659256.1236258.918012257.793911519.71657385.79880132.87α1α2α3α4α5α60.42630.70280.41403.86785.25190.5342㊀㊀将上述各系数代入式(32),得到磨削力的最终表达式:F n =b d s d w d s +d w (59256.12f 0.5a v wd 2g v s d s +㊀8012257.79(v w v s)0.43f 0.70a d 0.41g +㊀657385.79v 3.88w f 5.25a d 0.53s bv 1.88s f 2r)F t =b d s d w d s +d w (36258.91f 0.5a v wd 2g v s d s+㊀3911519.71(v w v s )0.43f 0.70a d 0.41g +㊀880132.87v 3.88w f 5.25a d 0.53s b v 1.88s f 2r)üþýïïïïïïïïïïïïïïï(33)3.2㊀预测结果及验证为了验证非线性优化函数G A GL S Q 求解模型的可靠性和预测精度,开展了外圆磨削单因素试验来进行验证.将验证集数据代入数学模型中,计算得到外圆磨削中法向磨削力和切向磨削力的平均预测误差分别为5.56%和7.08%,各组数据误差见表7.可见外圆磨削力模型具有较高的精度,预测效果较好.本文在求解模型时的原则是全局最优,算法以随机选取的若干组试验数据的误差二范数最小为寻优原则,试验中的干扰因素(如机床振动㊁试验操作不规范等)会对个别数据造成影响,故在不同试验组下会有个别数据误差偏大.4㊀磨削参数对磨削力的影响设F n ㊁F t 分别表示外圆磨削法向力和切向力试验值,F ᶄn ㊁F ᶄt 分别表示外圆磨削理论模型法向力和切向力预测值.4.1㊀砂轮径向进给速度对磨削力的影响如图6所示,在工件转速不变的情况下,砂轮径向进给速度增大,工件每转的磨削深度增大,使外圆磨削力在径向进给速度的作用下一直增大.此外,法向磨削力与切向磨削力预测结果与试验结果吻合较好.683 中国机械工程第35卷第3期2024年3月表7㊀模型验证试验T a b .7㊀M o d e l v a l i d a t i o n t e s t序号进给速度f r (mm /m i n )工件转速n (r /m i n )磨削宽度b (mm )砂轮粒度(目)法向力F n (N )切向力F t (N )预测值实际值误差(%)预测值实际值误差(%)10.15120308020.1716.3923.0610.288.8715.9020.3120308032.0833.985.5916.2815.465.3030.45120308042.1347.2710.8721.3222.244.1440.6120308051.1456.289.1325.8430.7215.8950.360308036.3436.010.9218.1818.190.0660.390308033.6533.830.5316.9616.234.5070.3120308032.0831.770.9816.2815.226.9780.3150308031.0430.551.6015.8515.840.0690.3120108010.6910.561.235.436.1812.14100.3120208021.3822.354.3410.8511.707.27110.3120308032.0829.568.5316.2819.1514.99120.3120408042.7742.750.0521.7024.8312.61130.3120304635.9539.649.3117.7516.696.35140.3120306033.6236.227.1816.7316.332.45150.3120308032.0832.731.9916.2815.465.30160.31203010032.3031.163.6616.6616.810.89图6㊀砂轮径向进给速度对磨削力的影响F i g .6㊀E f f e c t o f t r a n s v e r s e f e e d s p e e do n g r i n d i n g fo r c e 4.2㊀工件转速对磨削力的影响如图7所示,随着工件转速的提高,单位时间内参与磨削的有效磨粒数增加,使每颗磨粒平均未变形切削厚度减小.另外,在进给速度恒定的情况下,工件每转的磨削深度会随着工件转速n w 的增大而减小,以至于单位时间内外圆磨削单颗磨粒未变形切屑厚度减小,进而使外圆磨削力一直减小.图7㊀工件转速对磨削力的影响F i g .7㊀E f f e c t o fw o r k p i e c e s p e e do n g r i n d i n gf o r c e 4.3㊀磨削宽度对磨削力的影响如图8所示,磨削宽度的增大使单位时间内参与磨削的有效磨粒数和材料去除率均增大,两者的共同作用使磨削力不断增大.因此,法向磨削力和切向磨削力均随着砂轮的磨削宽度呈近似线性增加.之所以不是完全的线性关系可能与砂轮表面的磨粒分布规律有关.图8㊀磨削宽度对磨削力的影响F i g .8㊀E f f e c t o f g r i n d i n g w i d t ho n g r i n d i n g fo r c e 4.4㊀砂轮粒度对磨削力的影响如图9所示,在不同粒度的棕刚玉砂轮磨削18C r N i M o 7G6过程中,外圆磨削力随砂轮粒度的增大而缓慢减小.这是因为磨粒粒度越小,其顶锥角和尖端圆弧半径越小,单颗磨粒就越锋利,从而有利于磨粒的切削作用.其次在粒度较大的情况下其最大未变形切屑厚度也很小,从而导致单颗磨削力较小.另外根据式(33),砂轮粒度参数仅对摩擦力㊁耕犁力有影响,而摩擦力㊁耕犁力约占法向力和切向力的60%[27],并且本文选取的粒度变化范围相对较小,这可能是磨削力随砂轮粒度缓慢减小且对磨削力影响较小的原因.783 外圆磨削18C r N i M o 7G6力模型及表面完整性研究王㊀栋㊀陈㊀磊㊀张志鹏图9㊀砂轮粒度对磨削力的影响F i g .9㊀I n f l u e n c e o f g r i n d i n g w h e e l s i z e o n g r i n d i n gf o r c e 5㊀磨削参数对表面完整性的影响5.1㊀单位宽度法向力与温度的关系在实际加工中,磨削力和热之间存在紧密的联系.张锦涛[28]通过红外测温技术实现了干磨时的温度测量.在外圆横向磨削中,法向和切向磨削力有一定的比例关系,并且两者随参数变化的趋势相近,因此,本文只考虑单位宽度法向磨削力与磨削温度的关系,如图10所示.然后充分考虑磨削力和热对磨削过程的综合影响,用以分析磨削参数与表面完整性的作用规律.由图10可以看出,当F ᶄn <1.56N /mm 时,磨削热对表面完整性的影响程度较大,当F ᶄn >1.56N /mm 时,磨削力对表面完整性的影响程度较大.图10㊀单位宽度法向力与温度的关系F i g .10㊀T h e r e l a t i o n s h i p be t w e e nn o r m a lf o r c e p e r u n i t w i d t ha n d t e m pe r a t u r e 5.2㊀外圆磨削参数对表层残余应力的影响磨削工艺参数对表面完整性的影响见图11.5.2.1㊀砂轮径向进给速度对粗糙度的影响图11a ㊁图11b 所示为砂轮径向进给速度f r对残余应力与残余应力层的影响曲线,由图11a 可以看出残余压应力随砂轮径向进给速度的增大先减小后增大.结合图6对磨削力进行单位宽度化处理,当f r =0.45mm /m i n 时,单位宽度法向力F ᶄn 为1.58N /mm .结合图10可知,F ᶄn <1.56N /m i n 时,磨削接触弧区产生的瞬时温度的增长速率大于磨削力的增长速率,磨削热应力作用增强,残余压应力在0.15~0.45mm /m i n 范围内快速减小;在此之后磨削力的增长速率开始加快,而温度的增长速率变慢,此时磨削机械应力的作用相对增强,残余压应力在机械应力的作用下再次增大.所以残余压应力随砂轮径向进给速度的增大先减小后增大.由图11b 可以看出,由磨削所引起的残余应力变化层大概在20~30μm .其中,f r 在0.3~0.45mm /m i n 范围时,沿深度方向残余应力最大值相对较大(在-140M P a 左右).5.2.2㊀工件转速对残余应力的影响图11d ㊁图11e 所示为工件转速对表面残余应力的影响,由图11d 可以看出,工件表面残余压应力随着工件转速的增大而缓慢增大.由图7可知,磨削力随工件转速的增大而减小,工件转速n w 在60~150r /m i n 范围时,其单位宽度法向力均小于1.56N /mm .同理,结合图10可知,此时磨削接触弧区产生的瞬时温度的降低速率要大于磨削力的减小速率.随着n w 的增大,砂轮与工件单位面积的接触时间变短,磨削温度变低且散热更快,此时残余压应力整体呈现为缓慢增大;在距离表面20~30μm 区间内残余压应力达到最小,其中工件转速为60r /m i n 时其最小残余应力出现位置稍稍后移,然后在-200M P a 左右趋于平缓.5.2.3㊀磨削宽度对残余应力的影响图11g ㊁图11h 所示为磨削宽度对表面残余应力的影响.虽然随着磨削宽度b 的增大,总磨削力一直增大,但单位宽度的磨削力基本保持不变,所以当b <30mm 时,残余应力变化幅度不大;但当b >30mm 时,磨削温度会有所升高,热应力作用会增强,残余压应力减小.表面残余压应力随磨削宽度的增大先稳定波动后减小,因此在外圆横向磨削中,磨削宽度应尽量小于30mm .而表层残余压应力最小值出现的深度也略有增加,基本上在20~30μm ,并且使磨削对残余应力分布深度的影响逐渐增大.5.2.4㊀砂轮粒度对残余应力的影响图11j ㊁图11k 所示为砂轮粒度对残余应力的影响曲线.当砂轮粒度较小时,磨粒的尺寸较大,磨粒具有较大的顶锥角及圆弧半径,未变形切削厚度增大,塑性变形和耕犁压力较为显著,从而使单颗磨粒的磨削力增大,进而形成较大的残余压应力.随着砂轮粒度的增大,磨粒粒径变小,总的磨削力也会相应减小.但是当磨粒粒径过小时,磨粒之间的距离较近,容屑空间较小,容易导致砂883 中国机械工程第35卷第3期2024年3月。
磨边机的磨削过程的数学模型的研究
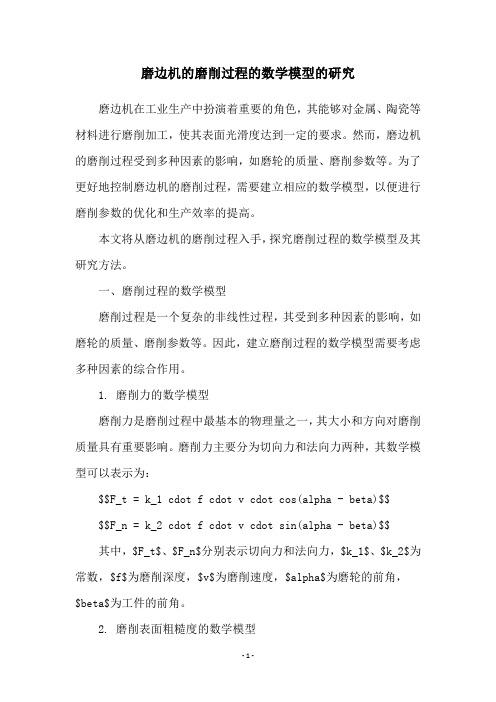
磨边机的磨削过程的数学模型的研究磨边机在工业生产中扮演着重要的角色,其能够对金属、陶瓷等材料进行磨削加工,使其表面光滑度达到一定的要求。
然而,磨边机的磨削过程受到多种因素的影响,如磨轮的质量、磨削参数等。
为了更好地控制磨边机的磨削过程,需要建立相应的数学模型,以便进行磨削参数的优化和生产效率的提高。
本文将从磨边机的磨削过程入手,探究磨削过程的数学模型及其研究方法。
一、磨削过程的数学模型磨削过程是一个复杂的非线性过程,其受到多种因素的影响,如磨轮的质量、磨削参数等。
因此,建立磨削过程的数学模型需要考虑多种因素的综合作用。
1. 磨削力的数学模型磨削力是磨削过程中最基本的物理量之一,其大小和方向对磨削质量具有重要影响。
磨削力主要分为切向力和法向力两种,其数学模型可以表示为:$$F_t = k_1 cdot f cdot v cdot cos(alpha - beta)$$$$F_n = k_2 cdot f cdot v cdot sin(alpha - beta)$$ 其中,$F_t$、$F_n$分别表示切向力和法向力,$k_1$、$k_2$为常数,$f$为磨削深度,$v$为磨削速度,$alpha$为磨轮的前角,$beta$为工件的前角。
2. 磨削表面粗糙度的数学模型磨削表面粗糙度是衡量磨削质量的重要指标之一,其数学模型可以表示为:$$R_a = frac{1}{2pi} int_0^{2pi} h(x) cdot cos(x) dx$$ 其中,$R_a$为磨削表面粗糙度,$h(x)$为表面高度函数。
3. 磨削温度的数学模型磨削过程中会产生大量的热量,磨削温度对磨削质量具有重要影响。
磨削温度的数学模型可以表示为:$$T = T_0 + k_3 cdot f cdot v cdot ln(frac{t}{t_0})$$ 其中,$T$为磨削温度,$T_0$为初始温度,$k_3$为常数,$t$为磨削时间,$t_0$为初始时间。
单晶材料微磨削表面粗糙度与磨削力实验研究

单晶材料微磨削表面粗糙度与磨削力实验研究孙杨1,2,巩亚东2,周云光2,蔡明2(1.沈阳城市建设学院,辽宁沈阳110167;2.东北大学机械工程与自动化学院,辽宁沈阳110819)来稿日期:2017-11-24基金项目:国家自然科学基金资助项目—单晶零件微尺度切削磨削工艺理论与关键技术研究(51375082)作者简介:孙杨,(1991-),男,辽宁盘锦人,硕士研究生,助教,主要研究方向:微尺度加工理论与技术;巩亚东,(1958-),男,辽宁本溪人,博士研究生,博士生导师,教授,主要研究方向:磨削与精密加工技术、数字化制造技术1引言随着产品微型化的到来,新兴材料的发展,各领域对微小型器件的需求不断加大,同时对产品的制造工艺质量和高温环境下的稳定性都提出了更高的要求[1]。
与多晶材料比,单晶材料具有耐高温、抗氧化和热疲劳性能等优点,被广泛应用于更多的设备中。
微磨削作为微加工的最后一道工序,可获得良好的工件表面质量,在制造精度上能达到微米级,可以实现产品微小型的制作。
镍基单晶高温合金仅有一个晶粒,是由一个晶粒沿一定方向进行生长制备,并且不存在晶界[2],其剪切断裂方式与多晶材料有较大的区别,且微尺度磨削不同于传统磨削,微磨削后的表面质量将直接影响到零件的使用寿命和力学性能。
目前,国内外对微磨削方面的研究也在开展之中[3-6],文献[7]研究了KDP 晶体精密磨削工艺实验,研究磨削参数对径向磨削力的影响;文献[8-9]研究了铣削表面形貌的影响规律和微磨削的机理;文献[10]采用晶体结构剪切滑移理论解释了不同切削方向获得不同粗糙度的原因。
从当前的研究成果看,很少发现关于特定单晶材料DD98的微磨削的研究,因此对单晶DD98进行微磨削实验有重要的理论意义。
2单晶D D 98微磨削实验2.1实验条件微磨削机床选JX-1A 型精密机床;磨棒选磨粒为500#、磨头直径为0.9mm ;检测仪器选用国外某公司生产的某三维轮廓仪;实验材料选用镍基单晶高温合金DD98。
- 1、下载文档前请自行甄别文档内容的完整性,平台不提供额外的编辑、内容补充、找答案等附加服务。
- 2、"仅部分预览"的文档,不可在线预览部分如存在完整性等问题,可反馈申请退款(可完整预览的文档不适用该条件!)。
- 3、如文档侵犯您的权益,请联系客服反馈,我们会尽快为您处理(人工客服工作时间:9:00-18:30)。
组参数试验三次,然后取平均值,见表 3) ,7 个未知参数(见表 4)通过求解线 性方程组确定。 将表 4 中的实验常数代入等式(27) ,可以得到磨削力的计算公式
由等式(13)得到
通过利用等式(2) ,在磨削加工中的切向切屑形成力可以得到
这里 K1 (Vw ap / Vs) b 是静态切向切屑形成力,K2 (bVw ap / Vs) ln (Vs1.5 /ap0.25 Vw0.5 )是动态切向切屑力。 设φ 1 和φ 2 分别为静态普通切屑形成力与静态切向切屑形成力之比和动态法向 切屑形成力与动态切向切屑形成力之比,法向切屑形成力为
图 3:Kistler 精密Fra bibliotek电晶体测力计 等式(25)的推导过程表明,切向磨削力构成的切屑形成力与法向磨削力构成 的切屑变形力的比由磨粒半顶角和其他几何参数决定, 但已发表的关于磨削力的 论文指出这个比值为常数。 在实践中, 在磨削加工过程中, 当磨削加工参数改变, 有效磨粒数也改变。因此,本文中定义的计算公式通过一个与砂轮速度,工件进 给速度和磨削深度有关的函数重新定义了切削形成力与切屑变形力之比。因此, 如此建立的磨削力数学模型是比较合理的。 切向磨削力的滑动力与法向磨削力的滑动力的比, 即摩擦系数在许多已发表的 计算磨削力的公式中被定义为一个常数。然而,实际中,摩擦系数随磨削加工参 数改变而改变, 摩擦系数被定义为一个与等式 (25) 中机械加工参数有关的函数。 这显然是更真实。 3.实验研究 一组实验在一台具有水平轴的高精度数控平面磨床(型号为 MGK7120 × 6, 如 图 2 所示)上展开。 用 Kistler 精密压电晶体测力计 (如图 3 所示) 去测磨削力, 它的参数在表 1 中已经列出。实验条件在表 2 中列出。 用热溶解粘剂把工件粘合在夹紧台上, 然后用六角螺母把夹紧太固定在测力计 上。最后把测力计吸附在工作台上。磨削力测试系统如图 4 所示。 表 3.实验数据
在这里, C 是砂轮单位面积上有效的研磨刀刃的数量, r 是切屑宽度与切屑厚度 的比率,de 是砂轮的等效直径。 将式(9)代入等式(8) ,得到磨削应变速率为
实验数据 (刘, 1991) 表明, 剪切流应力与剪切应变率近似成正比, 也就是说, 动态的特定切屑形成能 ud 与剪切应变率对数近似成正比,即:
这里 ac 是切削深度。将等式(7)带入等式(6)得到
K 是常数。 式(8)表明剪切带的剪切应变率与切削深度近似成反比,并与切割速度 v 近 似成正比,所以切屑深度与切割速度 v 对剪切带的剪切应变率有显着的影响。 一般都广泛认可,金属研磨过程与车削和铣削加工相似,金属材料摆脱其本体 的剪切过程(马尔金,2002 年) 。所以,从切割分析推到来的结论可以运用到研 究在磨削加工中的切屑变形力。 金属切割速度 v 对应于磨削中的砂轮速度 Vs,切 削深度 ac 对应于未变形切屑平均厚度。 未变形切屑平均厚度 (Shinji 等人, 1985) 是
K2 和
是由实验确定的常数,将等式(10)代入(11)式可得
2.1.4 热软化效应 实验数据(马尔金,2002 年)表明,随着砂轮轮速度 Vs 增加和工件速度 Vw 在同一时间减小, 磨削区的温度和金属材料的变形温度都会上升,热软化效果会 加强。因此,剪切流压力和动太特性切屑形成能 Ud 减少。 磨削过程中的金属去除的动态特性切屑形成能值是应变率效应和热软化的效 果综合效应的结果。式(12)反映了这种综合合效应。系数是正值,则意味着, 应变率效应超过热软化的效果, 该系数为负的值,这意味着热软化效应超过应变 率效应。 2.1.5 切屑形成力计算 将等式(12 代入代入(3)式可得
在研究成果的基础上,结合马尔金的磨削理论(马尔金,2002 年)和著名的金 属材料切削变形理论(刘,1991;真嗣等人,1985) ,一个新的易于使用的表面磨 削力数学模型被提出,改进的模型考虑到了磨削 参数和金属材料的切割动态力学表现之间的关系, 还有磨削参数对工件与砂轮之 间的摩擦系数的影响,磨削力模型中与砂轮和工件有关的常量是由实验得到的。 比较这个新的磨削力数学模型计算结果和实验结果,模型的有效性得到了证明。 2。磨削力数学模型 磨削力可以分为两部分,切削变形力和滑动力,切割变形力可以分离成切屑形 成力和耕作力。在磨削力的计算模型中忽略耕作力因为它是远小于切屑变形力 (马尔金,2002 年) ,因此磨削力可以分为两个部分:切屑形成力和滑动力。 Fn = Fn,ch + Fn,sl Ft = Ft,ch + Ft,sl (1)
这里
是剪切流动应力,
剪应变,
是剪切应变率,T 是变形温度。
当于剪切应力 ,剪切应变率 增加,剪切流 的材料的应力将增加。当 变形温度上升时,材料的剪切流动应力会减少。动态具体切屑形成能 ud 和剪切 流动应力的变化是成正比, 这是剪切应变效应,剪切应变率效应和热软化的效应
综合作用的结果。 2.1.2。剪应变效应 在两维的切割情况下,剪切带的剪切应变(Shinji 等人,1985)是
在这里,Fn 是法向磨削力,Ft 是切向磨,Fn.ch 法向切屑形成力, Ft.ch 是 切向切屑形成力,Fn.sl 是法向滑动力,Ft.sl 是切向滑动力。 因此, 具体的磨削能分为具体切屑形成能和特定的滑动能源,特定切屑形成能 uch(马尔和库克,1971 年)由如下方程确定
(2) 在这里,Vs 是砂轮速度,Vw 是工件进给速度,ap 是磨削深度, b 是磨削宽 度。 2.1.切屑形成力 特定的切屑形成能可以被分成两个部分:静态的特定切屑形成能 us 和动态 特定切屑形成能 Ud uch = us + ud (3) 这里静态的特定切屑形成能源是一个常数是由元件材料和砂轮材料实验确定的。 动态特定切屑形成能是由元件材料,研磨轮材料和磨削加工参数决定的。 2.1.1。材料的动态塑性本质关系 剪切变形的情况下,材料的动态塑性本质关系常见形式(Shinji 等人,1985) 是
表面磨削力的建模和实验研究
唐金元,杜金,陈永平 现代复杂装备设计与极端制造(中南大学)的重点实验室, 教育部,湖南长沙 410083,中国 校机械与电气工程学院,中南大学,湖南长沙 410083,中国 文章信息: 文章历史 2007 年 9 月 13 日收到。 2008 年 6 月 3 日收到修订版 2008 年 6 月 22 日采录 关键词:磨削力 动态切削形成力 静态切削形成力 摩擦系数 概要: 磨削力是由切屑形成力和滑动力构成。在本篇论文中,建立了一个新的表面磨削 力数学模型。 此模型进行有效性由比较实验结果和模型计算结果可以得到。切屑 形成力可分为静态切屑形成力和动态切屑形成力。动态切屑力主要受剪应变,剪 应变率和在金属去除处理中的产热的影响。 通过分析特定切屑形成能和切屑形成 力之间的关系, 提出了切屑形成力的计算公式。 结合其他研究人员所取得的成绩, 一个新的考虑工艺参数对摩擦系数的影响力的滑动力计算公式即可获得。 1. 介绍 磨削是精密机械加工的主要方法之一。砂轮的磨损,制造设备的动力性能,几 何精度和工件表面质量都受磨削力很大的影响, 所以不同的创始人在计算磨削力 方面去得了相当多的进展。 基于对磨削力和磨削砂轮磨损平面之间的关系实验结果,马尔金·库克(1971 年)提出了由切屑变形力和滑动力组成的磨削力,但没有提出切向磨削力公式。 另一个磨削力模型的建立基于转动的实验的基础, 李和傅(1981)提出法向切屑 形成力基公式, 。Badger and Torrance(2000)提出了两种磨削力模型,第一个 模型是基于 Challen 和 Oxley 两维(2-D)的平面应变滑移线场理论,第二个模 型是基于威廉姆斯和谢的三维(3-D)的金字塔状的凹凸模型。这两种模型模拟 了磨削工件界面的严格塑性接触, 这种接触的机械行为受磨削斜率和砂轮与磨损 材料界面之间的摩擦系数影响。 另一个不同磨削力模型由海克尔等人提出 (2004) 。 在他的模型中, 切屑厚度假定为按瑞利概率密度分布,并且概率密度函数的参数 考虑的到运动学条件,材料性能,磨轮的微观结构,和其他磨削加工动态效果的 影响。 磨削力模型受到研究人员非常广泛的研究,但还有问题要研究,有以下几个原 因:在磨削过程中,工作加工界面动态力学现象是非常复杂且非线性。磨削过程 中的谷物有不规则的几何形状和呈现随机分布。研磨率是非常高的,这使得磨削 是高温,高应变和高应变率材料去除过程(Tönshoff 等人,1992) 。 磨削过程中的材料应变率通常比普通切削过程大一个数量级,更重要的是,存在 规模效应(陈,唐,2007 年) 。大多数已发表的磨削力模型认为,摩擦系数是恒 定的参数,但在实际上,砂轮和工件之间的摩擦系数并不总是一个常数,它和其 他磨削参数随着磨削过程的进行而改变。 为了实现可控的和可预测的磨削过程, 研究磨削力的数学模型有其显著的意义。
图 2 高精度平面磨削机床 MGK7120×6. 式中,W 是法向负荷,A0 是接触面积, 性能确定的系数。 表 1 测力计性能参数 测量范围 灵敏度 线性度 固定频率 工作温度范围 Fx , Fy : ±5 kN, Fz :−5/+10 kN Fx , Fy :10 mV/N, Fz : 5 mV/N ±1% Fx , Fy : 2 KHz, Fz : 3.5 KHz 0–60℃ 和 通过接触界面的物理和机械
其中 剪切角, 是刀具的前角。 切削深度和切削宽度对剪应变有很小的影响的结论, 通过实验结果得到证明 (刘, 1991;Tso 和杨,1998 年) ,所以剪切应变的影响在切屑形成力的研究中被忽视。 2.1.3。剪切应变率效应 两维切割条件下,剪切带剪切应变速率(Shinji 等人,1985)是:
在这里,S1 是剪切带的宽度和被切割速度 实验结果(Shinji 等人,1985)表明:
考虑 K3 = ϕ1 K1 和 K4 = ϕ2 K2,等式(16)得到
2.2 滑动力 在磨粒的几何动力学分析中,使用抛物线函数来近似切割路径, 磨削砂轮半 径和切割路径曲率半径之间的误差(哈恩,1955)是:
在这个方程中,正号用于向上磨削,负号是用于向下磨削。 实验数据(Kannappan 和马尔金,1972 年)表明,工件和粗糙磨粒包裹的平面 之间的平均接触压力 p 随着曲率半径误差 的增加近似呈线性增加 (参照图 1) ,