纺纱方法的区别
(完整版)不同纺纱方法的成纱结构和特性

不同纺纱方法的成纱结构和特性当前棉纺领域有5种实用的、倍受关注的纺纱方法,即传统环锭纺、转杯纺、喷气纺、涡流纺和改进环锭纺——紧密纺。
环锭纺纱方法已有逾一个半世纪的历史,而后四者是在近几十年甚至是近几年发展起来的,统称为新型纺纱方法。
不同的纺纱方法无论在产量、质量方面,还是在成纱结构和特性方面,都有各自非常独特之处。
1 成纱机理1.1 传统环锭纺环锭纺纱是将牵伸、加捻和卷绕同时进行的一种纺纱方法,粗纱在牵伸系统中被牵伸至所要求纱支的须条,再经钢领、钢丝圈的加捻和卷绕形成一根纱线。
由于牵伸作用,主牵伸区中的须条宽度是所纺纱线直径的数倍,此时各根纤维抵达前钳口线时呈自由状态。
当这些纤维离开前钳口线后即被捻合在一起,这样就形成了一个纺纱加捻三角区。
此纺纱加捻三角区阻止了边缘纤维完全进入纱体,部分边缘纤维脱离主体形成飞花,较多的边缘纤维则是一端被捻入纱体,而另一端形成毛羽。
这些纤维不但对纱线的均匀度、弹性等性能起消极作用,且对纱线的强力极其不利。
另外,在加捻时处于三角区外侧的纤维受到的张力最大,而在中心的纤维受到的张力最小,故成纱时这些纤维的初始张力不等,从而影响成纱的强力。
这些都是传统环锭纺纺纱三角区造成的缺陷。
1.2 转杯纺转杯纺又称气流纺,属于自由端纺纱方法。
直接喂入纺纱器的棉条经分梳辊分梳成了单纤维状,纤维靠分梳辊的离心力和纺杯内负压气流的作用脱离分梳辊表面经输棉管道而进入纺杯,并在凝聚槽中形成一个完整的纤维环,纤维环随着纺杯高速旋转,在接头纱的作用下,随着捻度不断的传递和连续剥离纤维束而成纱。
1.3 喷气纺喷气纺纱以日本村田公司制造的MJS(Murata Jet Spinner)机型为代表。
棉条直接喂入牵伸装置,经牵伸后的须条进入喷嘴,两个方向相反的高速旋转气流对纱条进行假捻并包缠成纱,纱条引出后经电子清纱器去除疵点后被卷绕在筒子上。
1.4 涡流纺涡流纺纱是继MJS之后,村田公司推出的新一代的喷气纺纱技术MVS(Murata Vortex Spinning)。
棉、毛、丝、麻纺纱工艺比较
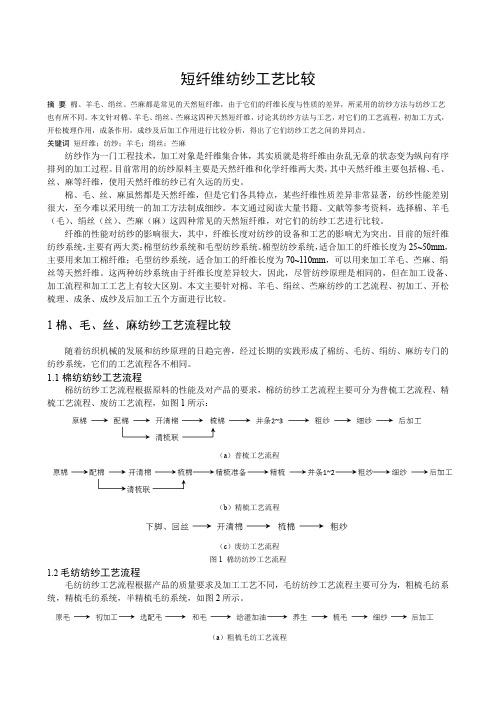
短纤维纺纱工艺比较摘要棉、羊毛、绢丝、苎麻都是常见的天然短纤维,由于它们的纤维长度与性质的差异,所采用的纺纱方法与纺纱工艺也有所不同。
本文针对棉、羊毛、绢丝、苎麻这四种天然短纤维,讨论其纺纱方法与工艺,对它们的工艺流程,初加工方式,开松梳理作用,成条作用,成纱及后加工作用进行比较分析,得出了它们纺纱工艺之间的异同点。
关键词短纤维;纺纱;羊毛;绢丝;苎麻纺纱作为一门工程技术,加工对象是纤维集合体,其实质就是将纤维由杂乱无章的状态变为纵向有序排列的加工过程。
目前常用的纺纱原料主要是天然纤维和化学纤维两大类,其中天然纤维主要包括棉、毛、丝、麻等纤维,使用天然纤维纺纱已有久远的历史。
棉、毛、丝、麻虽然都是天然纤维,但是它们各具特点,某些纤维性质差异非常显著,纺纱性能差别很大,至今难以采用统一的加工方法制成细纱。
本文通过阅读大量书籍、文献等参考资料,选择棉、羊毛(毛)、绢丝(丝)、苎麻(麻)这四种常见的天然短纤维,对它们的纺纱工艺进行比较。
纤维的性能对纺纱的影响很大,其中,纤维长度对纺纱的设备和工艺的影响尤为突出。
目前的短纤维纺纱系统,主要有两大类:棉型纺纱系统和毛型纺纱系统。
棉型纺纱系统,适合加工的纤维长度为25~50mm,主要用来加工棉纤维;毛型纺纱系统,适合加工的纤维长度为70~110mm,可以用来加工羊毛、苎麻、绢丝等天然纤维。
这两种纺纱系统由于纤维长度差异较大,因此,尽管纺纱原理是相同的,但在加工设备、加工流程和加工工艺上有较大区别。
本文主要针对棉、羊毛、绢丝、苎麻纺纱的工艺流程、初加工、开松梳理、成条、成纱及后加工五个方面进行比较。
1棉、毛、丝、麻纺纱工艺流程比较随着纺织机械的发展和纺纱原理的日趋完善,经过长期的实践形成了棉纺、毛纺、绢纺、麻纺专门的纺纱系统,它们的工艺流程各不相同。
1.1棉纺纺纱工艺流程棉纺纺纱工艺流程根据原料的性能及对产品的要求,棉纺纺纱工艺流程主要可分为普梳工艺流程、精梳工艺流程、废纺工艺流程,如图1所示:(a)普梳工艺流程(b)精梳工艺流程(c)废纺工艺流程图1 棉纺纺纱工艺流程1.2毛纺纺纱工艺流程毛纺纺纱工艺流程根据产品的质量要求及加工工艺不同,毛纺纺纱工艺流程主要可分为,粗梳毛纺系统,精梳毛纺系统,半精梳毛纺系统,如图2所示。
不同纺纱方法纺制竹浆纤维纱的成纱质量对比

不同纺纱方法纺制竹浆纤维纱的成纱质量对比
张勇
【期刊名称】《棉纺织技术》
【年(卷),期】2012(040)003
【摘要】以竹浆纤维为原料,采用赛络纺、涡流纺和传统环锭纺三种纺纱方法制得竹浆纤维18.2 tex纱,通过对比各类纱的成纱质量,分析纺纱方法对成纱质量的影响.具体对比结果如下.
【总页数】1页(P36)
【作者】张勇
【作者单位】安徽职业技术学院
【正文语种】中文
【相关文献】
1.R20型转杯纺纱机纺制纯棉针织纱及与环锭纺针织纱的比较 [J], 薛蓉;徐卫红
2.R20型转杯纺纱机纺制纯棉针织纱及与环锭纺针织纱的比较 [J], 薛蓉;徐卫红
3.紧密纺纱与传统纺纱成纱质量对比 [J], 房英杰;王爱萍;苏海员
4.赛络纺乃呙流纺廊锭纺竹纤维成纱质量对比分析 [J], 张勇
5.不同纺纱方法纺制的棉涤混纺纱质量对比分析 [J], 曹梦龙;徐伯俊;刘新金;方壹伟
因版权原因,仅展示原文概要,查看原文内容请购买。
棉纺5种实用纺纱方法

棉纺5种实用纺纱方法
1.环锭纺纱法:这种方法是目前最常用的棉纺方法之一。
将纤维放在环锭上,并在锭子周围绕着钩针上。
随着锭子的旋转,纤维就被拉伸并旋转成线。
这种方法适用于各种不同类型的棉纤维。
2. 摇杆纺纱法:这种方法是一种古老的技术,但仍然在某些地区使用。
它需要手动操作,使用一个摇杆来拉伸并旋转纤维成线。
这种方法通常用于生产特定类型的面料和纤维,如丝绸。
3. 吸气纺纱法:这种方法将纤维放在一个吸气管上,然后使用吸气力将纤维拉伸并旋转成线。
这个过程非常快,因此适用于大批量棉纺生产。
4. 水力纺纱法:这种方法使用高压水流将纤维拉伸并旋转成线。
这种方法非常快速和高效,但需要先将纤维处理成一定程度的湿润状态。
5. 气流纺纱法:这种方法使用空气流动将纤维拉伸并旋转成线。
这个过程非常快,因此适用于大批量棉纺生产。
但它需要特殊的设备来产生足够的气流。
- 1 -。
各种包芯纱纺纱方法__概述说明以及解释

各种包芯纱纺纱方法概述说明以及解释引言部分是整个文章的开篇,主要是为了介绍包芯纱纺纱方法这个话题,让读者对文章内容有一个整体的认识。
在概述部分,我们将简要说明包芯纱纺纱方法的意义和作用。
在目的部分,我们将明确本文旨在通过详细说明各种包芯纱纺纱方法,来帮助读者更好地了解这一领域。
在结构部分,我们将介绍本文各章节的内容安排,以及各章节之间的逻辑关系,为读者阅读提供清晰的指引。
包芯纱纺纱方法一是一种将外部纤维包覆在内部纤维周围的纺纱方法。
这种方法通常用于生产具有特殊性能要求的功能性纺织品。
首先,选取适合的内外纤维,内部纤维通常为强力较高的材料,如聚酯;而外部纤维则可以根据需要选择不同性能的材料,比如棉、涤等。
接着,在进行包芯纱的生产过程中,首先需要将内部和外部纤维混合,并通过特殊工艺进行混合撚合。
之后,在最终加工环节中,通过设备将经过混合处理的内外纤维进行拉伸、捻股、整较等步骤,最终形成包芯结构。
这种包芯结构能够赋予纺织品更好的耐久性、保暖性、抗拉强度等性能。
因此,在户外服装、运动用品、汽车座椅面料等领域得到了广泛应用。
3. 包芯纱纺纱方法二:3.1 定义:包芯纱纺纱方法二是一种将外层包覆材料包裹在内部纤维素纺丝芯外的技术。
通过向内部芯线添加覆盖层,以提高纺织品的抗拉强度和耐磨性。
3.2 方法步骤:首先,在准备好的内核材料上进行初次成型,然后将外层包覆材料均匀地涂覆在内核表面。
接着经过一系列的加工处理(如拉伸、卷绕等),最终形成具有包心结构的新纤维产品。
3.3 优缺点分析:包芯纱纺纱方法二相比传统纺法具有以下优势:增加了产品的服用寿命;提高了产品的抗压能力和耐磨性;增加了产品的柔软性和舒适度。
但也存在一些缺点,如生产过程中需要较高技术水平和设备投入,成本较高;封装层与内核之间可能出现质量问题导致产品不稳定等。
4. 包芯纱纺纱方法三4.1 原理解析包芯纱纺纱方法三是一种利用特殊设备将包覆材料与芯线进行二次捻合的技术,通过此过程,使得包覆材料能够紧密地包裹在芯线表面,形成一种具有特殊功能和性能的新型纱线。
织布有哪些不同的纺织方法?

织布有哪些不同的纺织方法?一、手工纺织方法手工纺织是最早出现的纺织方法之一,以人工操作纺纱纺织器具完成纺织过程。
这种方法的特点是操作简单,适用于小规模生产和个体经营。
手工纺织在一些地区仍然被保留下来,具有一定的历史和文化价值。
手工纺织的优点在于保留了传统的工艺技术和文化,使得纺织品更富有个性和特色。
手工纺织的缺点在于生产效率低下,无法满足大规模生产的需要。
二、机械纺织方法机械纺织是利用机械设备完成纺织过程的方法,它代替了手工操作,提高了生产效率。
机械纺织主要分为以下几种方法:1. 细纱纺织法:通过纺锭旋转,将纤维材料进行拉伸,形成细纱。
这种方法适用于生产高密度、高强度的织物。
2. 纺纱纺织法:通过用喷丝、空气、液体或旋转方式将材料分离并成纱,再进行纺织。
这种方法适用于生产纤维度较大、颗粒形状不规则的纺织品。
3. 平针织纺织法:利用针筒上的平针搭建织物。
这种方法适用于生产弹力织物和厚实织物。
4. 圆针织纺织法:利用针筒上的圆针搭建织物。
这种方法适用于生产连续管状织物。
三、化学纺织方法化学纺织是利用化学方法将纤维素等原料转化为纺织品的方法。
它不同于传统的纺纱纺织方法,更多地依赖于化学反应和材料变化。
1. 溶胶纺织法:通过将纤维素等溶解于溶剂中,再将溶液抽出纺丝,形成纤维。
这种方法适用于生产纤维细、柔软的纺织品。
2. 熔融纺织法:将合成纤维或其他熔点较低的材料,加热至熔融状态后经过喷射、空气流、旋转等方式,形成纤维。
这种方法适用于生产高强度、高韧性的纺织品。
3. 溶胶-凝胶纺织法:将纤维素等材料转化为凝胶状,再通过拉丝或其他方式形成纤维。
这种方法适用于生产高分子纳米纤维。
四、生物纺织方法生物纺织是利用生物体或其分泌物进行纺织的方法,主要应用于丝绸、羊毛和毛织物等的制造。
1. 蚕丝纺织法:利用蚕的丝腺分泌的丝蛋白通过加工和纺丝制成丝线。
这种方法适用于生产丝绸。
2. 羊毛纺织法:利用羊和其他动物的毛发通过修剪、清洗、分离纤毛和纺纱制成毛线。
喷气涡流纺与环锭纺转杯纺三种纺纱方法综合对比分析

差(%) CVb% +0.5 +1.6 +1.7 2.01 1.46 1.38
环锭纺 转杯纺 喷气涡 流纺
从以上对比数据中可以看出: 条干CV%和细节-50%:环锭纺最好,其次喷气涡流纺,转杯 纺最差。 粗节+50%:环锭纺最好,其次喷气涡流纺,转杯纺最差。 棉结+200%:喷气涡流纺最好,其次环锭纺,转杯纺最差。 单纱断裂强度:环锭纺最高,其次涡流纺,转杯纺最低。 条干CVb%:喷气涡流纺最好,其次转杯纺,环锭纺最差。
涡流
切向 开口 进风孔
涡流管
负压装置
2 原料使用
三种纺纱方法由于成纱结构不一样,相同规格 的原料所纺出的纱在强力、条干方面差异较大 针对不同的纺纱方法和纺纱支数,需要选择不同 规格的原料来弥补各自成纱中的不足
环锭纺选用 原料规格为 1.67dtex×3 8mm 100%, 成纱纤维根 数为118根 转杯纺配置 ¢33mm纺杯, 所选原料 1.33dtex×32m m 100%,成纱 纤维根数为148 根 喷气涡流纺 选用原料为 1.33dtex×3 8mm 100%, 成纱纤维根 数为148根
生产效率(%) 97.4 96.0 95.2 94.4 93.1 91.7 90.0 87.8 85.9 每台每小时断头率(根) 204.1 280.2 320.4 370.7 416.1 440.4 455.4 469.8 513.1 折千锭时断头率(根) 2551 3503 4005 4634 5201 5505 5693 5873 6414
3 工艺流程
3 喷气涡流 纺
FA002抓棉机→SFA035混开棉机→FA106A梳针开棉机→FA161振 动棉箱给棉机→A076F成卷机→FA204C梳棉机→FA306A并条机 (二道)→RSB D401自调匀整并条机→种纺纱方法生产的19.7tex粘胶纱成纱质量指标对比 原料 纺纱方 法 ( 条干 细节50% 3 13 6 dtex·mm) CV% 规格 1.67×38 1.33×32 1.33d×38 12.67 13.80 13.39 粗节 +50 % 17 38 29 棉节 +200 % 28 59 23 单纱强 力CV% 9.3 8.9 10.0 单纱断裂 强度 (cN/tex) 15.1 11.5 12.8 百米重 量 CV% 1.8 1.1 0.9 重量偏 条干
三分钟教你了解纺纱方式

三分钟教你了解纺纱方式一、纺纱方式介绍’1、环锭纺环锭纺纱是现时市场上用量最多,最通用的纺纱方法。
环锭纺纱指条子或粗纱经牵伸后的纤维条通过环锭钢丝圈旋转引入,筒管卷绕速度比钢丝圈快,棉纱被加捻制成细纱,广泛应用于各种短纤维的纺纱工程。
如普梳、精梳及混纺,钢丝圈由筒管通过纱条带动绕钢领回转进行加捻,同时,钢领的摩擦使其转速略小于筒管而得到卷绕。
纺纱速度高,环锭纱的形态,为纤维大多呈内外转移的圆锥形螺旋线,使纤维在纱中内外缠绕联结,纱的结构紧密,强力高,适用于制线以及机织和针织等各种产品。
2、集聚纺条从前罗拉前口输出后,先经过异形吸风管外套网眼皮圈,须条在网眼皮圈上运动,由于气流的收缩和聚合作用,通过异形管的吸风槽使须条集聚、转动,逐步从扁平带状转为圆柱体,纤维的端头均捻入纱线内,因此成纱非常紧密,纱线外观光洁、毛羽少。
集聚纺纱线强力较高,毛羽较少。
在编织过程中最不易产生磨毛的现象。
传统环锭纺与集聚纺对比集聚纺的目的是在纱线加捻前使纤维之间尽可能平行并接近,对于高质量的集聚纺纱线这是重要的评判标准。
使纤维尽可能平行并保持一致在加捻前是其优势的前提。
集聚纺的优点有:成纱毛羽很少,特别是3 mm以上毛羽极少,同时也提高了后道织机效率,以及布面平整光滑度;纱线之间抱合力大,强力高;条干不匀,粗、细节指标比传统纱要好。
但是集聚纺设备的造价较高,增加了纺纱厂的设备投资,且除了毛羽指标有很大的改善之处,纱线的其它指标如条干、粗、细节等改善幅度不大。
3、赛络纺两根须条在捻合以前已有少量捻回加在单根须条上,因此捻合后的纱条具有与一般单纱不同的股线风格。
如果采用色纺粗纱搭配喂入,则可以纺制出花纹状的“AB”混纺纱。
赛络纺纺纱图示赛络纺的初始设计目的是用于毛纺上,特点是毛羽少,强力高,耐磨性好,达到毛纱能单纱织造的效果,以实现毛织物的轻薄化。
尽管赛络纺在许多方面比较同类常规纱有了较大的改善,要真正达到毛纺单纱不上浆织造,尚有一定距离。
- 1、下载文档前请自行甄别文档内容的完整性,平台不提供额外的编辑、内容补充、找答案等附加服务。
- 2、"仅部分预览"的文档,不可在线预览部分如存在完整性等问题,可反馈申请退款(可完整预览的文档不适用该条件!)。
- 3、如文档侵犯您的权益,请联系客服反馈,我们会尽快为您处理(人工客服工作时间:9:00-18:30)。
各种纺纱方法对纱线性质的影响
1短纤维的物理特性
不同的短纤维纺纱工艺技术对纱线物理性质及外观影响不同,甚至影响最终产品的特性也不相同。
(1)不同纺纱方法对纱线结构,短纤维纱的结构与长丝不同,首先是纱的外部及内部纤维的排列,外部结构包括纱的外观及表面构造。
如:纤维在纱表面的排列;纱的毛羽;纱的磨擦系数;纱的特性;纱的耐磨及表面其它特性。
(2)纱线内部结构主要是纤维在纱体的整个横截面及纱的纵向排列,纤维定向性、伸率、
位移及捻度内部结构包括:纱的强度;纤维混合程度;抗弯曲强度;可压缩性;回弹性(有纽结倾向)。
以上对结构含意的解释不一定完整,但却提供了纱线特性的复杂性。
2纺纱工艺
为了获得纺纱工艺对纱线结构影响的概念应用3dtex、38 mm粘纤短纤维,在5种不同纺线工艺系统中进行试纺。
(1)传统环锭纺纱工艺;(2)紧密纺环锭纺纱工艺;(3)双喷咀(MTS)假念包缠纺纱工艺;(4)涡流纺(MVS)纺纱;(5)转杯纺纱。
(1)如上述提到的纱线外部结构可以扫描式电子显微镜摄影仪上看出。
应用微电子摄影照片:包括转杯纺、喷气纺,涡流纺、普通环锭纺及紧密环锭纺五种,从照片中可看到五种工艺生产的纱线外部纤维定向性,其中紧密环锭纱的外部结构中更多纤维形成纱线,几乎所有纤维形成在纱体中,改进了短纤维纱,纱的捻度结构看到很清楚,而且纤维的一端沿纱的长度拈入纱体中,紧密环锭纱的定向性最好.
(2)传统环锭纺纱,捻度相同条件下传统环锭纺纱表面紊乱,大量纤维尾端没有捻入纱体中,单个纤维伸在纱体外,可能是由于钢领/钢丝圈或导纱器造成。
(3)涡流纺纱,近似于环锭纺纱,纤维在纱体中排列很好,纺纱速度350/分时,
包缠纤维呈细旋状。
捻度基本上与环锭纱相同,纱的实际捻度与计算捻度基
本相同。
包缠纤维与无捻纱芯纤维之比,占的百分比很高,几乎全部复盖了纱芯纤维,因此,涡流纱的外观基本与环锭纱相似,外部包缠纤维与无捻纱芯一起形成真捻。
(4)双喷咀假捻纱,双喷咀假捻纱,与涡流纱其实质是不同的,双喷咀喷气纱的包缠纤维仅占全部纤维的6%-8%约有90%的纤维是伸展无捻的,可以清楚看到包缠纤维对纱芯的包缠紧度比涡流纱大。
(5)转杯纺纱,不管转杯纱是否属于真捻范畴,但转杯纱上纤维排列紊乱,纱中部纤维显示Z向及S向没有清楚的螺旋状,纤维是伸直的。
可清楚的看到被包缠的纱无缠结状,这是转杯纱的优点,是转杯纱特性的基础。
3毛羽
纺纱形成的飞花及毛羽是个十分麻烦的问题,毛羽在下游工序加工时有许多负面作用,纺织品手感及最终产品性质受毛羽影响,应用zweigle毛羽测试议将1mm-2 mm的毛羽分级并分出3 mm以上的有害毛羽。
假如环锭细纱毛羽为100%,则紧密环锭纱、涡流纱及转杯纱1 mm-2mm毛羽比环锭纱毛羽减少,双喷咀假捻包缠纱,包缠情况较差,毛羽较多,应用SO—Called检测仪可测出纱线在后工序加工时由于摩擦而形成的飞花,摩擦力应用橡胶圈进行测量。
紧密纱要比非传统纱抗摩擦性能好。
转杯纱伸出的毛羽较少,尤其粘胶纤维更为明显,纱上的纤维不会断裂,但许多毛羽被包缠纤维缠在纱体上,所以转杯纱毛羽较少。
4纱的体积
纱线体积是反映纱线覆盖能力的重要指标,紧密纺环锭纱与普通环锭纱在同样捻度时,后者最终产品复盖能力较低。
紧密纺环锭纱在保持同等强力条件下可适当减少捻度以增加纱线体积,可获得相当于普通环锭纱的复盖能力,捻度可减少5%~10%。
邓肯道夫(Denkenolorf)纱线结构试验仪提供了纱线长度为0.3mm的实测纱线体积。
纱线体积的检测包括同样纱线支数双喷咀MJS喷气纱,由于喷气纱是包缠纱、假捻,因此同样纱支比环锭纱体积大,用微电子扫描摄影技术摄制的图形表明,少量包缠纤维在纱芯上,而且长度很短使纱线许多部分纤维基本上是无捻的。
经纱的耐磨擦及应力负荷是应用So-Called模似指标,可同时试验所需要的
15根纱。
理想的紧密环锭纱的纤维排列显示出比普通环锭纱优异。
非传统纺纱技术都有不足之处,这种新型纺纱在做经纱时必须经过处理,在喷气纺技术中,相对于真捻纱,纱线上的纤维很少,有伸直缠绕的情况,因此,纱线机械物理性能不一,尤其在卷绕时(络筒)更明显,还是非传统纺纱与环锭纱的区别。
5纱线内部结构
纱线内部纤维的形成与纱线外部结构相关,纱线内部纱芯的排列,纤维沿纱线长度方向延伸可以经过电子扫描摄影在牵伸过程中获得,从纱线横截面中看到纤维高度平行,并影响纱线强力,纱线强力特点与试验时夹持长度相关。
减少细节及强力弱环的可能性:正常的纱线强力是在夹持长度为520 mm强力机上试验的,也有100 mm及18mm的夹持长度。
夹持长度减少、纱线断裂强力增加,这是由于夹持长度短,强力弱环及细节出现概率减少,断裂长度减少,断裂机会少。
假如纤维分布定向好,试验夹持长度减少,纱线断裂强度显著增加,环锭纱及紧密环锭纱更为明显。
转杯纱断裂强力较低,即使断裂长度低于纤维长度,由于纤维形成弯钩,即使断裂长度短,转杯纱断裂强度也不会提高。
总之纱线纤维被夹持数量越多,纤维纵向定向性好,纱线断裂强度增加.从电子摄影扫描图中看出转杯纱属缠绕结构,即使夹持长度低于5mm,会使100%的纤维被夹持及纤维断裂,夹持长度在0 mm,纤维断裂长度低于纤维长度,纱芯纤维定向性差造成断裂强度低。
喷气纱强力介于环锭纱,紧密纱及转杯纱之间,主要是喷气纱,纱芯比转杯纱平行,包缠纤维比较少,强力比转杯纱少高。
6纱的形成影响纱线变形的特征
如纱抗弯曲强力就是纱线形成过程中影响的特性,但纱线抗弯曲强力的检测很困难。
目前已开发了一种最新的检测纱线抗弯曲强力的方法。
试验表明,假如紧密纱抗弯强度为100%,则转杯纺及涡流纺为200%,双喷咀喷气纱为300%,这些数值关系可从一些非传统纺纱,在机织物及针织物上与环锭纱作比较,非传统纺纱的织物手感比普通环锭纱产品粗硬,普通环锭纱与紧密纱之间的抗弯强度亦小有区别。
另外产生一个问题,当纱线变形时在经纬纱横截面上纱线受压后变偏平变形
的情况.纱线粗节的检测表明当纱线压缩力增加时,粗节减少。
转杯纱线结构造成纤维分布状况,在纤维包缠处,手感较硬,比没有包缠处的纱变形力小。
转杯纱生产的针织物及机织物往往使外观比环锭纱不均匀、粗硬。
为了进行比较,将纱线粗节在1OOcN压力条件下检测,表明纱线具有最佳捻度结构,同等变形的MTS双喷咀喷气纱中约有95%平行无捻的纤维,更容易产生变形,根据这个试验,转杯纱手感比较硬,在织机或针织布外观上可以通过纱的紧密情况检测纱线变形情况。
7纱线的回弹性
纱线的回弹对纺织加工是十分重要的,例如针织布产生歪斜变形。
回弹性由检测纱线纽结力测得,紧密环锭纱、普通环锭纱等真捻纱与非传统纱之间的回弹力不同,转杯纱正捻或反捻的纱其纽结均较低。
喷气纺纱回弹力较低,主要因为平行无捻纤维比例较高,真捻纱比非传统纱的回弹力大,
因此在进一步加工成针织布时织物歪斜情况少。
8结语
纱线结构是纱线重要特性之一,纱线外观与纱线性质相关,纱线内部纤维排列对纱线性质影响很大,尤其对纱线进一步加工及最终产品性质的影响更为显著。
较差纱线结构对后工序加工很有影响,应用好的纱线结构具有特别好的功能,用途也很好,在适应性能上紧密纺纱线的纺织品,外观结构是最理想的。