面齿轮传动啮合刚度数值计算-机械工程论文-工程论文
面齿轮传动啮合刚度分析与修形减振优化

FUXuezhong1, FANGKongde1 , JIA Chao1, PENGXianlong2
( 1 . S c h o o l o f M e c h a n ic a l E n g in e e r in g , N o rth w estern P o ly te ch n ic U n iv e r s ity , X i / a n 7 1 0 0 7 2 ,C h in a ; 2 . S c h o o l o f M e c h a n ic a l E n g in e e r in g , X i ’ a n U n iv e rsity o f S c ie n c e a n d T e c h n o lo g y ,X i ’ a n 7 1 0 0 5 4 ,C h in a )
摘 要 : 为 准 确 求 解 面 齿 轮 传 动 的 啮 合 刚 度 ,基 于 齿 轮 的 承 载 接 触 分 析 ( L T C A ) 技 术 ,综 合 考 虑 变 位 、小 轮 偏 置 、齿
面 修 形 以 及 安 装 误 差 ,提 出 了 面 齿 轮 传 动 啮 合 刚 度 计 算 方 法 ,并 验 证 了 该 方 法 的 精 确 性 。 分 析 了 负 载 、变 位 、小 轮 偏 置 和 安 装 误 差 对 面 齿 轮 传 动 综 合 啮 合 刚 度 均 值 和 波 动 幅 值 的 影 响 ,并 将 L T C A 技 术 与 遗 传 算 法 相 结 合 ,建 立 了 面 齿 轮 传 动 修
A b s t r a c t # To accurately calculate mesliing stiffnes of face-gear drives,comprehensively considering effects of
斜齿轮的齿面载荷及啮合刚度数值分析

30机械工艺师2000.10—————————————————————————————————————————————————————————————————————————————————一~斜齿轮的齿面载荷及啮合刚度数值分析口林腾蛟李润方朱才朝杭华江擅要基于齿格啮合原理和接触问是有艰元法。
提出了一种白赫生成任意咕台位王有限元模型的算法,开发了啮合轮齿自动建模程序度接齄有限元分析程序,井对井啬轮进行分析计算,得到了培定啮夸住王齿面截荷分布曲线和运转过程啮合剐度的变化曲线。
关■词:辩齿轮自动t其接■问量有厦元法为了研究斜齿轮接触压力沿齿面分布情况,计算齿面啮台刚度,本文提出了一种自动生成齿面任意啮合位置接触有限元计算模型的方法,编制了相应的轮齿自动建模程序。
应用接触有限元混合计算公式,编制了轮齿接触有限元分析程序。
本文开发的程序巳用于多个工程实际项目的分析,计算结果可靠.对指导齿轮设计有较大的实际意义。
一、轮齿接继有限元自动建模1.轮齿阿格生成方法首先建立如图1所示的整体坐标系YOZ和旋转坐标系y10。
五,主动轮和被动轮的轴心分别通过原点0,和0。
YOZ坐标系中所示的轮齿为生成前端面网格的原始位置。
以大、小齿轮第一对齿在前蛸面节点啮合位置作为转角初始位置。
相对莱一转角位置各对齿的网格生成方法如下:1)确定轮齿接触线位置,计算前靖面的啮合点坐标。
以该点为分界点。
将主、被动轮齿顶部分网格均分,而齿根部分的嘲格由与其啮合的齿顶阿格决定。
2)根据齿根过渡曲线方程及轮体尺寸要求,计算前端齿根过渡部位及轮体部位离散点坐标.并生成阿格节点。
3)齿长方向各截面网格由前端面网格沿基圆柱旋转延伸生成。
2.轮齿的边界条件处理将被动轮轮体作为固定约束,主动轮轮体径向按斜约束处理,切向施加均布载荷,如图2所示。
载荷大小为:口=正,(‘U)…………………………………(1)式中羁——主动轮转矩‘——舶载面曲率半径‘——加赣面圆弧长度6——齿宽3.轮齿自动建模程序设计I鞋齿接■■垒标计算I-l计算齿膏^鼓点生标』晤甄而面商函葡而i鼐,、—————————jE——..。
齿面磨损对齿轮啮合刚度影响的计算与分析

* 式中,z 为齿数, ha 为齿顶高系数,刀具圆角系数
rc* c* /(1 sin ) i 为渐开线齿廓上任 意一点对应的压力角。
式中, i s /(2r ) (inv i inv ) ,s 为分度圆齿厚, r 为分度圆半径, ri 为渐开线齿廓上任意一点的回
M 20
Mg2
cos f sin f 0
sin f cos f 0
0 0 1
(5)
M g 2 中, 2 f 为齿根圆弧对应的圆心角,表达
式为
[13]
1
渐开线直齿轮齿廓曲线方程
* rc* sin ) f 2 tan (ha
* 国家自然科学基金资助项目(50935004)。 20141023 收到初稿, 20150320 收到修改稿
动力学分析的关键。研究点蚀和磨损引起的齿轮啮 合刚度变化对齿轮传动系统的动力学及故障诊断研 究具有重要意义。 齿轮啮合刚度的计算方法当前主要有:材料力 [3] 学法,弹性力学法和有限元法 。随着计算机技术 的发展,有限元法广泛地运用于齿轮的动力学分析 中 , 但 过 程 复 杂 计 算 繁 琐 。 在 ISO6336-1 和 GB3480-1997 等标准中,齿轮啮合刚度的计算主要 采用材料力学方法进行快速计算,如石川公式法以 [4-5] 但该方法难以计算故 及石川公式法的改进算法 , 障齿轮的啮合刚度。当前故障齿轮的啮合刚度计算 研究主要集中于齿根裂纹对啮合刚度及其动力学特
1 0 r 2 0 M 01 0 1 (3) 0 0 1 cos 2 sin 2 r cos( π / 2 2 ) cos 2 r sin( π / 2 2 ) (4) sin 2 0 0 1
齿轮刚度的计算
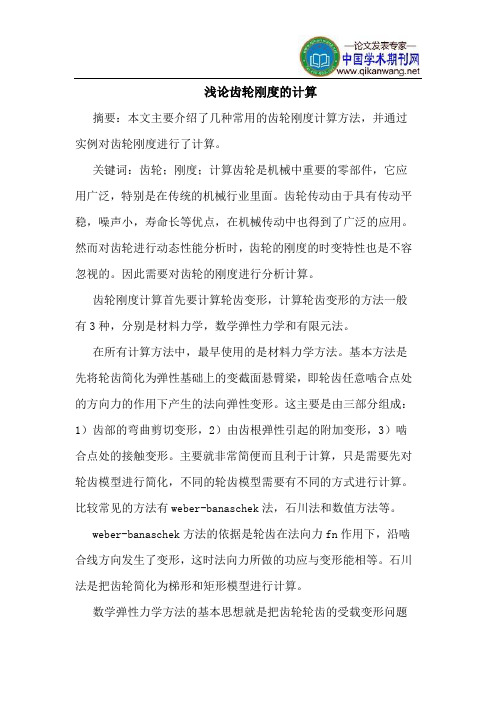
浅论齿轮刚度的计算摘要:本文主要介绍了几种常用的齿轮刚度计算方法,并通过实例对齿轮刚度进行了计算。
关键词:齿轮;刚度;计算齿轮是机械中重要的零部件,它应用广泛,特别是在传统的机械行业里面。
齿轮传动由于具有传动平稳,噪声小,寿命长等优点,在机械传动中也得到了广泛的应用。
然而对齿轮进行动态性能分析时,齿轮的刚度的时变特性也是不容忽视的。
因此需要对齿轮的刚度进行分析计算。
齿轮刚度计算首先要计算轮齿变形,计算轮齿变形的方法一般有3种,分别是材料力学,数学弹性力学和有限元法。
在所有计算方法中,最早使用的是材料力学方法。
基本方法是先将轮齿简化为弹性基础上的变截面悬臂梁,即轮齿任意啮合点处的方向力的作用下产生的法向弹性变形。
这主要是由三部分组成:1)齿部的弯曲剪切变形,2)由齿根弹性引起的附加变形,3)啮合点处的接触变形。
主要就非常简便而且利于计算,只是需要先对轮齿模型进行简化,不同的轮齿模型需要有不同的方式进行计算。
比较常见的方法有weber-banaschek法,石川法和数值方法等。
weber-banaschek方法的依据是轮齿在法向力fn作用下,沿啮合线方向发生了变形,这时法向力所做的功应与变形能相等。
石川法是把齿轮简化为梯形和矩形模型进行计算。
数学弹性力学方法的基本思想就是把齿轮轮齿的受载变形问题简化为一个半无限体的受载变形,利用保角映射函数把轮齿的曲线边界c映射为直边边界场。
这样可以应用弹性力学中平面问题的复变函数解答求解集中力作用下的半无限体的位移场,再由此确定受载轮齿的位移场。
康焱用有限元方法计算了渐开线直齿内齿轮的轮齿刚度,其最后得到的渐开线直齿内齿轮的载荷作用点的轮齿刚度的计算公式为[2-3]:c=(e/a)(λx+1)b(x+1)c×10-9(3)式中:a=0.0011z2-0.1381z+12.8587b=-0.0056z+1.0483c=-0.0002z+0.0376计算出轮齿任意啮合点k处的法向弹性变形δk以后,单个轮齿的啮合刚度即可求出kk=fkδk,应该说明的是轮齿在不同的啮合点啮合时δk是不同的,因此轮齿的啮合刚度也是啮合点位置的函数。
面齿轮副啮合强度的简化计算

Journal of Mechanical Strength2023,45(5):1192-1198DOI :10.16579/j.issn.1001.9669.2023.05.024∗20230204收到初稿,20230411收到修改稿㊂国家自然科学基金项目(52265006),陕西省自然科学基础研究计划项目(2020JM-521)资助㊂∗∗何㊀飞,男,1995年生,湖北荆州人,汉族,西安科技大学硕士研究生,主要研究方向为齿轮传动㊂∗∗∗付学中(通信作者),男,1986年生,江西高安人,汉族,广西科技大学助理研究员,博士,硕士研究生导师,主要研究方向为齿轮传动理论及应用㊂面齿轮副啮合强度的简化计算∗SIMPLIFIED CALCULATION OF MESHING STRENGTHOF FACE GEAR PAIR何㊀飞∗∗1㊀钱卫香1㊀付学中∗∗∗2㊀彭先龙1(1.西安科技大学机械工程学院,西安710054)(2.广西科技大学机械与汽车工程学院,柳州545616)HE Fei 1㊀QIAN WeiXiang 1㊀FU XueZhong 2㊀PENG XianLong 1(1.School of Mechanical Engineering ,Xiᶄan University of Science and Technology ,Xiᶄan 710054,China )(2.School of Mechanical and Automotive Engineering ,Guangxi University ofScience and Technology ,Liuzhou 545616,China )摘要㊀为便于面齿轮初始设计阶段基本参数的选取,简化面齿轮副啮合强度的求解过程㊂参考已有的标准直齿圆柱齿轮强度计算公式建立了面齿轮全齿高的接触应力和弯曲应力解析计算模型㊂通过齿轮基本参数求解的齿面曲率,结合赫兹接触理论求解齿面接触应力㊂应用30ʎ切线法确定轮齿危险截面处齿厚,进而给出基于齿轮副基本参数表达的应力计算系数表,最终推导出齿根弯曲应力解析计算模型㊂以某一设计参数的面齿轮副为例,把通过解析计算模型得到的结果与有限元仿真计算结果进行对比分析,验证了模型的准确性㊂并在此基础上给出可通过齿轮副基本参数求解的面齿轮强度简化计算公式㊂关键词㊀面齿轮㊀接触应力㊀弯曲应力㊀有限元中图分类号㊀TH132.4Abstract ㊀In order to facilitate the selection of basic parameters in the initial design stage of face gear,and simplify theprocess of solving meshing strength of face gear pair.By referring to the existing strength calculation formula of the standard spurgear,the analytical calculation models of contact stress and bending stress of full tooth height of face gear were established.The curvature of tooth surface was solved by the basic parameters of the gear,and the contact stress of tooth surface was solved by theHertz contact theory.The tooth thickness at the dangerous section of gear teeth was determined by the 30ʎtangent method,andthe stress calculation coefficient table was given based on the expression of basic parameters of gear pair,finally,the analytical calculation formula of tooth root bending stress was deduced.Taking face gear pair with a certain design parameter as anexample,the results obtained from the analytical calculation models were compared with those from the finite element simulationto verify the accuracy of models.On this basis,a simplified formula for calculating the strength of face gear was given which canbe directly solved by the basic parameters of gear.Key words㊀Face gear ;Contact stress ;Bending stress ;Finite elementCorresponding author :FU XueZhong ,E-mail :fxznwpu @.The project supported by the National Natural Science Foundation of China(No.52265006),and the Natural Science BasicResearch Project of Shanxi Province(No.2020JM-521).Manuscript received 20230204,in revised form 20230411.0㊀引言㊀㊀面齿轮传动具有简化动力传输系统结构㊁提高系统可靠性等特点,已成功应用在直升机传动系统中[1]㊂随着航空技术的发展,对面齿轮的承载性能提出了极高的要求[2]㊂面齿轮的啮合强度对其承载性能有着重大影响,因此在面齿轮的设计阶段,需要计算面齿轮的接触应力和弯曲应力㊂目前,面齿轮没有标㊀第45卷第5期何㊀飞等:面齿轮副啮合强度的简化计算1193㊀㊀准的接触应力和弯曲应力计算公式,这给面齿轮设计参数的选取带来了诸多不便㊂国内外很多学者对齿轮传动装置的接触应力和弯曲应力进行了大量研究㊂LIU S Y等[3]利用有限元法比较了不同加工方法获得的面齿轮在相同工况下的接触应力和弯曲应力,计算结果表明,面滚齿准双曲面齿轮具有更好的齿强度㊂ZSCHIPPANG H A等[4]通过解析方法和有限元分析相结合的办法,根据接触路径和角位移的结果确定面齿轮的载荷分配和接触应力㊂赵玉龙[5]建立了弧线齿面齿轮多齿有限元模型,分析在不同负载情况下,弧线齿面齿轮接触应力与弯曲应力的变化规律㊂ZHANG C等[6]精确推导齿面柔度矩阵,结合有限元分析切片模型计算出网格刚度,模拟了理想和误差条件下轮齿的局部接触变形㊂周镇宇等[7]利用有限元法分析了修形与不修形对面齿轮副的接触轨迹及接触应力的影响㊂王爽[8]建立端曲面齿轮副复合传动轮齿修形设计模型,通过有限元方法对其接触应力与弯曲应力进行分析,结果表明在对端曲面齿轮修形设计时,同时对小轮采用齿向修形设计,可以在提高齿面承载能力的同时改善齿面接触情况㊂杨主希等[9]建立了非正交修形斜齿面齿轮传动接触应力计算公式,但其接触点的主曲率求解过程复杂,无法通过齿轮副的基本参数直接求解㊂现有文献大都通过有限元法计算面齿轮的接触应力与弯曲应力,没有类似于圆柱齿轮或锥齿轮的标准承载能力计算公式㊂本文通过求解齿面曲率一般表达式,结合赫兹接触理论,给出了计算接触应力所需的系数表,并计算面齿轮副的接触应力;通过确定轮齿的危险截面,给出了弯曲应力计算系数表,并计算面齿轮副的弯曲应力;将计算结果和有限元法计算得到的结果进行对比验证,最终给出一套类似圆柱齿轮ISO标准强度计算公式的简化计算模型㊂1㊀齿面接触应力的解析计算1.1㊀面齿轮副齿面曲率㊀㊀齿轮副齿面方程的建立是齿轮性能分析的基础,文献[10]建立相应的齿面方程,其中小齿轮(i=1)和插齿刀(i=s,s表示插齿刀)的齿面方程表示为R i=r b i(sin(θ0i+θi)-θi cos(θ0i+θi))-rb i(cos(θ0i+θi)+θi sin(θ0i+θi))r b i/m2i cosφθ1éëêêêêêêùûúúúúúú(1)式中,r b i为基圆半径;θ0i=π/2N i-tanα+α为基圆上的齿槽宽系数;N i为齿数;α为压力角;θi为端面渐开线参数;φθ=θ0i+θi+φi;φi为小轮或刀具转角;m2i为齿轮副传动比㊂面齿轮的齿面方程表示为R2=r bs cosφ2(sinφθ-θs cosφθ)-sinφ2m2s cosφθ()-r bs sinφ2(sinφθ-θs cosφθ)+cosφ2m2s cosφθ()-r bs(cosφθ+θs sinφθ)1éëêêêêêêêêêùûúúúúúúúúú(2)式中,φ2=m2sφs㊂根据齿面在啮合过程中的连续相切条件,面齿轮与圆柱小齿轮在齿面接触点处的位矢和法矢相等[11]268-270㊂当以面齿轮转角φ2作为输入参数时,对转角φ2进行离散,便可求得得各个接触点的坐标,获得如图1所示的齿面接触迹线㊂齿面上接触点的方向和其在齿面上的法线分别用e和n表示,e和n可以确定齿面在接触点处沿e方向上的法截面,而法截面与齿面的交线称为齿面在接触点沿e方向的法截线㊂可通过求解法截线的曲率得到齿面曲线的曲率㊂图1㊀齿面接触路径示意图Fig.1㊀Diagram of tooth surface contact path为简化计算公式,在曲率的推导过程中均以单位载荷和单位模数计入计算,在最后公式中加入对应的载荷和模数㊂小齿轮(i=1)和插齿刀(i=s)的主曲率ki1㊁k i2可以表示为ki1=-2/(Niθi cosα)ki2=0{(3)㊀㊀参考文献[11]231-240可推导面齿轮与插齿刀之间齿面主方向夹角,并简化为γ=0.5arctan-2N2N s cosα()(4)式中,N s㊁N2分别为插齿刀和面齿轮的齿数㊂面齿轮齿面主曲率表示为k21=0.5-2N sθs cosα+a213+a223a33-2a13a23a33sin2γ()k22=0.5-2N sθs cosα+a213+a223a33+2a13a23a33sin2γ()ìîíïïïïïï(5)式中,参量a13㊁a23和a33分别为㊀1194㊀机㊀㊀械㊀㊀强㊀㊀度2023年㊀a 13=-tan α/θs a 23=N s cos α/N2a 33=N 3s 2N 22(sin αcos 2α-θs cos 3α)+N s sin 2α2θs cos αéëêêùûúúìîíïïïïïï(6)1.2㊀法向载荷的求解㊀㊀为了方便计算齿轮在一个啮合周期中,各接触点上的接触应力和弯曲应力,需要求解啮合时各接触点处的法向载荷㊂齿轮在啮合过程中,接触的齿对数目会成规律性变化,轮齿所承受的载荷也会随之改变㊂假设此时有n (n >1)对轮齿同时参与啮合,因此根据载荷分布系数的定义,各齿对的载荷分布系数为c i =F iT 1/(0.5mN 1cos α)(7)式中,F i (i =1,2, ,n )为各齿对分担的载荷;T 1为输入转矩;N 1为小齿轮齿数;m 为齿轮模数㊂且系数满足如下关系:c 1+c 2+ +c n =1(8)㊀㊀根据变形协调条件,多个齿对在载荷作用下同时接触时,各齿对的总传动误差必定相同[12],因此:c 1ζ1+Δφ1=c 2ζ2+Δφ2= =c n ζn +Δφn (9)式中,ζi 为单齿啮合时,不同接触点处的接触变形和弯曲变形引起的传动误差;Δφi 为各齿对的几何传动误差,根据齿面接触分析(Tooth Contact Analysis,TCA)直接求解㊂联立式(7)~式(9)可求得在两对齿同时啮合时,各齿对上分布的载荷表示为F 1=2T 1mN 1cos αˑΔφ2-Δφ1+ζ2ζ1+ζ2F 2=2T 1mN 1cos αˑΔφ1-Δφ2+ζ1ζ1+ζ2ìîíïïïïïï(10)1.3㊀齿面接触应力的解析计算模型㊀㊀结合第1.1节中的计算式,单位载荷和单位模数下的面齿轮在啮合点处的接触椭圆长半轴a 和短半轴b 分别为a =αc31.5k 11+k 12+k 21+k 22(1-ν21E 1+1-ν22E 2)(11)b =β31.5k 11+k 12+k 21+k 22(1-ν21E 1+1-ν22E 2)(12)式中,αc =32E (e )/[π(1-e 2)];β=αc 1-e 2;ν1㊁ν2分别指小齿轮和面齿轮的泊松比;E 1㊁E 2分别指小齿轮和面齿轮的弹性模量;E (e )是第二类椭圆积分㊂为方便计算,在图2中列出了根据公式求解的接触椭圆长㊁短轴计算系数值,后续应用时可直接在图中提取相应系数㊂其中A ㊁B 满足关系式A =0.5(k 11+k 12+k 21+k 22)(13)B =0.5n 21+n 22+2n 1n 2cos 2γ(14)式中,n 1=k 11-k 12;n 2=k 21-k 22㊂在求解完系数后,根据载荷与应力的关系式,面齿轮各接触点处的接触应力表示为σc =(1.5F )1/3παc βm 2A 1-ν21E 1+1-ν22E 2()éëêêùûúú2/3{}(15)图2㊀椭圆长㊁短轴的计算系数Fig.2㊀Calculation coefficients of major and minor axes of ellipse2㊀齿根弯曲应力的解析计算模型㊀㊀面齿轮作为非标准齿轮,目前也没有标准的方法准确地计算齿根弯曲应力,这里参考圆柱齿轮齿根弯曲应力的计算方法[13]求解面齿轮的弯曲应力㊂图3所示为面齿轮齿根危险截面示意图,过齿廓对称中线上的一点,作与对称中线成30ʎ夹角的直线,且使该直线与齿根过渡曲面相切,则两侧过渡曲面上切点的连线即可作为该轮齿的危险截面S F ,此截面到作用点的距离称为作用力臂h F ,αF 为载荷作用角㊂图3㊀面齿轮齿根危险截面示意图Fig.3㊀Diagram of face gear tooth root dangerous section接触点所在截面内,齿廓曲线上任意点的法矢第㊀第45卷第5期何㊀飞等:面齿轮副啮合强度的简化计算1195㊀㊀二分量为0,αF 只和接触点法矢在x 轴方向上的投影有关,可表示为αF =arccos n 2x(16)式中,n 2x 为接触点法矢沿x 轴方向的投影㊂法向力作用点沿z 轴方向的坐标为z P =R 2z -|R 1x tan αF |(17)式中,R 2z =-r ps +m ,r ps 为插齿刀节圆;R 1x 为接触点位矢R 1沿坐标轴x 方向上的投影㊂利用危险截面与过渡曲面交点的法矢与30ʎ切线垂直的条件,可以求解30ʎ切线处的切点坐标㊂确定了切点的位矢和法向作用力方向之后,作用力臂h F 和危险截面可以表示为h F =z P -R 2c z(18)S F =2|R 2c x |(19)式中,R 2c x ㊁R 2c z 分别为过渡曲面上切点沿x 和z 轴上的分量㊂因此,齿轮受到的弯矩可表示为M =Fh F cos αF(20)㊀㊀齿轮的抗弯截面系数为W =bs 2F 6(21)式中,b 为轮齿的宽度㊂以不同的标准计算齿根强度时,考虑的应力类型不一样,计算式不尽相同㊂由于ISO 标准和国标的方法更具有代表性,此处参考ISO 6336-3标准,引用应力修正系数为Y sa =(1.2+0.13L a )qL a /(1.12L a +2.3)(22)式中,L a =S F /h F ;q =0.5S F /ρ,ρ为过渡曲面30ʎ切线处的曲率半径㊂联立式(16)~式(22)可得齿轮齿根弯曲应力为σb =M W Y sa =F cos αbmY Fa Y sa(23)式中,Y Fa 为齿形系数,可表示为Y Fa =6h F m cos αFS 2F cos α(24)㊀㊀图4给出了小轮比插齿刀齿数少2个齿时,部分常用压力角下不同齿数对应的应力修正系数和齿形系数的求解结果,根据面齿轮具有高传动比的特性,传动比范围选取了4~20㊂在计算面齿轮的齿根弯曲应力时,可直接查此图获取系数㊂图5展示了在小轮齿数为25,压力角为25ʎ时,刀具与小轮的不同齿数差引起的齿形系数与应力修正系数的变化情况㊂由图5可知,齿形系数的最大变化量不足0.002,应力修正系数的最大变化量不足0.028,而在图4给出的各参数范围内,齿形系数的变化不足3ɢ,应力修正系数的变化不足2%,因此在面齿轮齿根弯曲应力的计算过程中,齿数差对弯曲应力的影响可忽略不计㊂图4㊀面齿轮弯曲应力计算系数Fig.4㊀Calculation coefficient of bending stress of facegear图5㊀齿数差引起的计算系数变化示意图Fig.5㊀Diagram of calculation coefficient variationcaused by tooth number difference3㊀算例分析3.1㊀面齿轮应力的有限元计算及对比㊀㊀为了验证所提方法的准确性,以五齿接触模型的计算结果与有限元结果进行对比分析㊂应用文献[14]中面齿轮有限元网格模型的构建方法,建立如图6所示的齿轮副模型,为提高计算结果的准确性,在实际验算过程中,会加大模型的网格密度,使模型整体节点数达到159732个㊂表1所示为面齿轮传动的基本参数㊂㊀1196㊀机㊀㊀械㊀㊀强㊀㊀度2023年㊀图6㊀齿轮副五齿模型Fig.6㊀Gear pair five teeth model表1㊀齿轮副参数Tab.1㊀Gear pair parameters参数Parameter 数值Value小齿轮齿数Number of pinion teeth25插齿刀齿数Number of gear shaper teeth27面齿轮齿数Number of face gear teeth160压力角Pressure angle /(ʎ)25模数Modulus /mm6.35泊松比Poissonᶄs ratio0.3弹性模量Elasticity modulus /GPa210面齿轮内径Inside diameter of face gear /mm480面齿轮外径Outer diameter of face gear /mm560为了验证模型,利用有实验数据的文献进行仿真,通过对比仿真结果和文献的实验结果证明模型的可靠性㊂由于接触应力实验的操作难度大,国内外鲜有直接做接触应力实验的文献㊂在一篇面齿轮耐久性实验报告中,给出了面齿轮在7200lb-in(约813N ㊃m)的转矩作用下,最大齿面接触应力为275ksi (约为1896.1MPa)[15]1018-1027㊂此处结合报告中表1所示的面齿轮副参数构建算例1,将算例1的最大接触应力与上述的最大齿面接触应力进行对比㊂用文献[16]4301-4318中表1所示的面齿轮参数构建算例2,将算例2的最大弯曲应力与文献的实验结果进行对比㊂由表2㊁表3可以看出,两个算例的误差均不超过9%,此结果说明了建模方法的正确性㊂表2㊀接触应力对比Tab.2㊀Comparison of contact stress文献References[15]1018-1027算例Case 1误差Error /%最大接触应力Maximum contact stress /MPa1896.11855.92.1表3㊀弯曲应力对比Tab.3㊀Comparison of bengding stress文献References[16]4301-4318算例Case 2误差Error /%最大弯曲应力Maximum bending stress /MPa205.5187.28.9㊀㊀图7(a)是转矩为1600N ㊃m 时,从齿根开始的第12个接触点处的接触应力云图,该点处于两齿啮合状态,观测齿对(第三对齿)的接触应力云图位于节锥面附近,而相邻齿对在齿根处产生了边缘接触,此时可在Abaqus 中运行python 语言编写的后处理程序,直接输出观测齿对的接触应力㊂图7(b)是第12个接触点对应的弯曲应力云图,由于接触区域受压,所以应力值显示为负值,而齿根区域受拉,显示为正的应力值㊂图7㊀面齿轮应力云图Fig.7㊀Stress nephogram of face gear3.2㊀解析与有限元应力计算的对比㊀㊀应用表1所示数据,在转矩T 1=1600N ㊃m 时计算的各接触点处接触应力如图8所示,因为第1~7个点,及第16~20个点为边缘接触点,无法适用于这套公式,所以此处只展示无边缘接触的第8~15个点㊂计算公式得到整个啮合周期内最大的接触应力为919.7MPa,通过有限元提取第3个齿面的最大接触应力为823.2MPa㊂对比解析法和有限元法的计算结果,两种计算方法相差96.5MPa,误差为11.7%㊂图8㊀面齿轮齿面接触应力Fig.8㊀Tooth contact stress of face gear由图9可以看出,解析计算模型得到的啮合周期内最大的弯曲应力为85.8MPa,有限元提取的最大弯曲应力为82.3MPa㊂两种计算方法的误差为4.3%㊂㊀第45卷第5期何㊀飞等:面齿轮副啮合强度的简化计算1197㊀㊀计算应力时,误差主要来源于多齿啮合时的载荷分配误差,以及在图表中取值时的误差,但上述所求误差量在实际工程应用中均可以被接受㊂图9㊀面齿轮副的齿根弯曲应力Fig.9㊀Tooth root bending stress of face gear4㊀接触应力与弯曲应力的简化计算公式㊀㊀接触应力与弯曲应力的解析计算模型适用于求解齿轮在整个啮合过程中各接触点的应力㊂但需要先借助TCA 求解法向载荷,然后得到相应的应力结果㊂为脱离TCA 的限制,进一步对解析模型进行简化,得到面齿轮在节锥面上的强度计算公式㊂4.1㊀面齿轮副的重合度㊀㊀在第1.2节中是利用变形协调条件求解的各接触点处的载荷㊂面齿轮重合度反映了载荷在轮齿间的分配情况,此处直接考虑重合度的影响,给出重合度的简便计算公式㊂重合度的定义为ε=Δϕ12π/N 1(25)式中,Δϕ1为相互啮合的一对齿从开始进入啮合到退出啮合期间小轮所转过的角度,可以通过齿轮副的啮合轨迹方程结合齿面的几何限制条件求解㊂在无安装误差的情况下,求解式为Δϕ1=θa1-r s -m -d -r b1cos αr b1sin α(26)式中,θa1=r2a1-r2b1/r b1;d =(r bs -r b1)/cos α;r a1为小轮齿顶圆半径;r s 为插齿刀分度圆半径㊂代入式(25)可得重合度表达式为ε=θa1N 1sin αcos α-(N 1-2-N 1cos 2α)2πsin αcos α(27)4.2㊀接触应力的简化计算公式㊀㊀因为随着啮合位置的变动,齿轮上的载荷和曲率都在变化,导致接触应力也在改变,且在节锥面上达到最大,所以下面推导节锥面处的赫兹应力,以此代表齿面接触强度㊂此时θs =tan α(28)㊀㊀联立式(3)~式(6)可得A =0.5(k 11+k 12+k 21+k 22)=N s +N 1m 22scos 2αN 1N s sin α(29)B =0.5n 21+n 22+2n 1n 2cos(2γ)=㊀㊀1N 21sin 2α+4m 22sN 2stan 2αsin 2(2γ)+Z H(30)式中,Z H =4m 2s /[N 1N s sin αtan αtan(2γ)];m 2s =N s /N 2㊂此时,利用式(29)㊁式(30)可以完全根据齿轮副的基本参数求解接触椭圆计算系数㊂法向载荷与转矩的关系为F =2T 1/(mN 1cos α)(31)㊀㊀因此,在节锥面处的接触应力简化计算公式可表示为σc =312T 1A 2m 3Z 2E N 1cos α㊃1παc βε(32)式中,Z E =(1-ν21)/E 1+(1-ν22)/E 2㊂将齿轮副基本数据代入公式,最终求得最大齿面接触应力为660.3MPa㊂对比有限元结果小162.9MPa,误差为19.7%㊂4.3㊀弯曲应力的简化计算公式㊀㊀根据式(23)㊁式(27)和式(31)可知,面齿轮齿根弯曲应力简化计算公式可以表示为σb =2T 1bm 2N 1εY Fa Y sa(33)㊀㊀同理,代入基本参数可以得最大齿根弯曲应力为76.3MPa㊂对比有限元结果,误差为7.3%㊂此结果比解析计算模型得到的误差大㊂5㊀结论㊀㊀本文基于面齿轮曲率公式的简化求解,结合赫兹公式给出了全齿高的接触应力解析计算模型;通过对弯曲应力计算系数的求解,推导了齿根弯曲应力的解析计算模型;并在此基础上提出了面齿轮接触和弯曲强度的简化计算公式㊂通过把模型和简化公式的计算结果分别与仿真结果进行比较,结果表明:1)在给定条件下,本文提出的全齿高应力解析计算模型所求结果均略大于有限元计算结果,是一种偏安全的计算方法㊂2)根据强度简化计算公式结果与有限元计算结果对比发现,由简化计算公式得到的结果偏小,但误差均在20%以内,对齿轮设计参数的选取有一定的参考作用㊂未来可以通过加入使用系数和动载系数等参数进一步优化此公式,得到更精确的结果㊂参考文献(References )[1]㊀谭武中,王祁波.面齿轮在直升机传动系统中的应用前景分析[J].机械制造与自动化,2020,49(1):52-55.TAN WuZhong,WANG QiBo.Application prospect analysis of face㊀1198㊀机㊀㊀械㊀㊀强㊀㊀度2023年㊀gear in helicopter transmission system[J].Machine Building&Automation,2020,49(1):52-55(In Chinese).[2]㊀靳园园,徐红玉,李㊀莉,等.航空面齿轮热滚轧表层残余应力分析[J].塑性工程学报,2022,29(9):216-223.JIN YuanYuan,XU HongYu,LI Li,et al.Analysis of surface residualstress of hot-rolled aviation face gear[J].Journal of PlasticityEngineering,2022,29(9):216-223(In Chinese).[3]㊀LIU S Y,SONG C S,ZHU C C,et al.Investigation on contact andbending stress of face-hobbed and face-milled hypoid gear[J].Mechanism and Machine Theory,2020,150:103873.[4]㊀ZSCHIPPANG H A,NATANAEL L,Küçük K A,et al.Face-geardrive,assessment of load sharing,transmission characteristics androot stress based on a quasi-static analysis[J].Mechanism andMachine Theory,2020,151:103914.[5]㊀赵玉龙.弧线齿面齿轮加载啮合分析及接触应力研究[D].江西:南昌航空大学,2021:60-66.ZHAO YuLong.Research on loaded meshing analysisand contactstress of arc tooth face gear[D].Jiangxi:Nanchang HangkongUniversity,2021:60-66(In Chinese).[6]㊀ZHANG C,DONG H M,WANG D L,et al.A new effective meshstiffness calculation method with accurate contact deformation modelfor spur and helical gear pairs[J].Mechanism and Machine Theory,2022,171:104762.[7]㊀周镇宇,唐进元,丁㊀撼.变位非正交面齿轮副小轮齿向修形轮齿接触分析[J].中国机械工程,2016,27(15):2003-2009.ZHOU ZhenYu,TANG JinYuan,DING Han.Tooth contact analysis ofprofile-shifted non-orthogonal face gear drive with longitudinalmodified pinion[J].China Mechanical Engineering,2016,27(15):2003-2009(In Chinese).[8]㊀王㊀爽.端曲面齿轮副复合传动轮齿修形设计及分析[D].重庆:重庆大学,2021:52-62.WANG Shuang.Modification design and analysis of curve-face gearpair compound transmission[D].Chongqing:ChongqingUniversity,2021:52-62(In Chinese).[9]㊀杨主希,邬远航,唐进元.非正交修形斜齿面齿轮传动接触应力计算研究[J].机械传动,2020,44(2):16-21.YANG ZhuXi,WU YuanHang,TANG JinYuan.Research ofcalculation method of contact stress of non-orthogonal modified face-gear drive with helical pinion[J].Journal of MechanicalTransmission,2020,44(2):16-21(In Chinese).[10]㊀靳广虎.正交面齿轮传动的强度与动力学特性分析研究[D].南京:南京航空航天大学,2012:13-15.JIN GuangHu.Research on strength and dynamic characteristics oforthogonal face gear drives[D].Nanjing:Nanjing University ofAeronautics and Astronautics,2012:13-15(In Chinese). [11]㊀LITVIN F L.Gear geometry and applied theory[M].New Jersey:PTR Prentice Hall Inc,1994:231-270.[12]㊀王永强,魏冰阳,徐家科,等.摆线针轮多齿啮合特性与承载接触分析方法研究[J].中国机械工程,2023:1-8[2023-03-10].WANG YongQiang,WEI BingYang,XU JiaKe,et al.Research onmulti tooth meshing characteristics and load bearing contact analysismethod of cycloid pinwheel[J].China Mechanical Engineering,2023:1-8[2023-03-10](In Chinese).[13]㊀朱孝录,鄂中凯,蔡春源.齿轮承载能力分析[M].北京:高等教育出版社,1992:193-197.ZHU XiaoLu,E ZhongKai,CAI ChunYuan.Analysis of bearingcapacity of gear[M].Beijing:Higher Education Press,1992:193-197(In Chinese).[14]㊀徐琪超.基于解析建模的面齿轮承载接触仿真分析[D].西安:西安科技大学,2020:15-32.XU QiChao.Simulation analysis of face gear loading contact based onanalytical modeling[D].Xiᶄan:Xiᶄan University of Science andTechnology,2020:15-32(In Chinese).[15]㊀LEWICKI D G,HEATH G F,FILLER R R,et al.RDS-21face-gearsurface durability tests:NASA/TM-2007-214970[R].WashingtonDC:NASA,2007,2:1018-1027.[16]㊀GUINGAND M,VAUJANY J P D,JACQUIN C Y.Quasi-staticanalysis of a face gear under torque[J].Computer Methods inApplied Mechanics and Engineering,2005,194:4301-4318.。
基于渐开线齿轮精确建模的啮合刚度的数值计算

{ 0 l t o o t h p r o i f l e mo d fc i ti a o n t o r e d u c e t h e v i b r a t i o n d u r i n g t h e ea g r m e s h i n g .
i s m a d e o n t h e n u me r i c a l i n t e g r lf a o r mu l a b se a d o n We b e r e n e r g y me t h o d, a n d t h e 0’ D o n n e l l c o e f ic f i e n t s i s i n t r o d u c e d w i t h
机 械 设 计 与 制 造
Ma c h i n e r y De s i g n & Ma n u f a c t u r e
ห้องสมุดไป่ตู้
第 2期 2 0 1 3年 2月
基 于渐开线齿轮精确建模 的啮合 刚度 的数值计算
张奎 晓 , 胡 鹏, 张 义民
1 1 0 8 1 9 ) ( 东北大学 机械工程与 自动化学院, 辽宁 沈阳
摘
要: 给 出 了基 于齿轮 加 工 工 艺的 渐 开线 齿轮 精 确建模 的方 程 , 对基 于 We b e r 能量 法 的数值 积 分公 式 进行 了详 细 的推
导, 基体变形量引入 了0’ D o n n e l l 的基体变形 因子, 并采用最大变形条件定义基点 M。 通过计算单对轮齿啮合的总变形量 来计算啮合 刚度。编制 了 M a t l a b计算程序 , 将得到的数值计算结果与 1 S 0 6 3 3 6 、 日本机械学会得到结果相 比较 , 该方法得 出的数据误 差小、 准确, 可以很好 的指导齿廓修形 , 以减少齿轮啮合过程 中的振动冲击。 关键词 : 渐开线齿轮 ; 精确建模 ; We b e r 能量法; 啮合刚度 ; I S O6 3 3 6
面齿轮传动啮合刚度分析与修形减振优化

面齿轮传动啮合刚度分析与修形减振优化付学中;方宗德;贾超;彭先龙【摘要】为准确求解面齿轮传动的啮合刚度,基于齿轮的承载接触分析(LTCA)技术,综合考虑变位、小轮偏置、齿面修形以及安装误差,提出了面齿轮传动啮合刚度计算方法,并验证了该方法的精确性.分析了负载、变位、小轮偏置和安装误差对面齿轮传动综合啮合刚度均值和波动幅值的影响,并将LTCA技术与遗传算法相结合,建立了面齿轮传动修形减振优化模型.研究结果表明:面齿轮传动综合啮合刚度幅值波动较大,存在阶跃突变现象,但波动幅值对负载、变位、小轮偏置和安装误差并不敏感,而综合啮合刚度均值受负载、小轮偏置和安装误差影响较大,且在3类安装误差中,轴夹角误差对综合啮合刚度均值影响最大;优化小轮修形参数后使综合啮合刚度的波动幅值大幅下降,从而可有效减小面齿轮传动的振动和噪声.【期刊名称】《振动与冲击》【年(卷),期】2019(038)005【总页数】8页(P265-272)【关键词】面齿轮传动;啮合刚度;修形;减振;优化;遗传算法【作者】付学中;方宗德;贾超;彭先龙【作者单位】西北工业大学机电学院,西安710072;西北工业大学机电学院,西安710072;西北工业大学机电学院,西安710072;西安科技大学机械工程学院,西安710054【正文语种】中文【中图分类】TH132.41轮齿变形和啮合刚度的精确计算是研究轮齿齿面修形、振动与噪声、动态特性、寿命预测、故障诊断的基础[1-2],也是确定齿轮传动系统内部附加动载荷、齿面载荷分布及齿间载荷分配系数的重要因素。
关于轮齿变形和啮合刚度的计算方法[3-4],国内外学者已进行了大量的研究,并形成了以材料力学方法和数学弹性力学方法(即保角映射法)为代表的理论计算方法、以边界元法和有限元法为代表的数值计算方法。
材料力学方法是使用最早应用最广的一种方法,以Ishikawa公式和Weber-Banaschek公式最具代表性[5],前者在日本和国内应用较多,后者在国外应用较多[6]。
基于weber能量法的直齿轮时变啮合刚度数值计算

基于weber能量法的直齿轮时变啮合刚度数值计算文章标题:基于Weber能量法的直齿轮时变啮合刚度数值计算一、引言在机械传动系统中,直齿轮是一种常见的机械元件,其传动效率和稳定性对整个系统的性能起着至关重要的作用。
而直齿轮啮合刚度则是评估其传动性能的重要参数之一。
本文将基于Weber能量法,探讨直齿轮时变啮合刚度的数值计算方法,以期为工程实践提供有益的参考。
二、Weber能量法概述Weber能量法是一种广泛应用于机械系统分析的方法,其核心思想是通过对系统的能量变化进行分析,推导出系统的基本动力学方程。
在直齿轮系统中,Weber能量法可以有效地描述啮合过程中的能量转换和传递关系,从而为计算啮合刚度提供了理论基础。
三、直齿轮啮合刚度的基本概念啮合刚度是指在一定啮合几何条件下,轴向载荷改变时,啮合点处齿轮轴向位移与载荷之比的物理量。
直齿轮啮合刚度是对直齿轮在啮合过程中的刚度特性进行描述的重要参数,其大小和变化对于齿轮传动的动态特性具有重要影响。
四、基于Weber能量法的直齿轮时变啮合刚度数值计算1. 通过Weber能量法建立直齿轮系统的动力学模型,考虑齿轮的轴向位移、载荷和啮合几何条件等因素。
2. 根据啮合接触几何关系和实际工况条件,确定直齿轮系统的能量变化规律。
3. 建立直齿轮系统的动力学方程,利用Weber能量法推导出直齿轮啮合刚度的数值计算公式。
4. 通过数值计算的方法,对直齿轮啮合刚度在不同工况下的变化规律进行分析和评估。
5. 结合实际工程案例,验证基于Weber能量法的直齿轮时变啮合刚度数值计算的有效性和准确性。
五、个人观点和总结基于Weber能量法的直齿轮时变啮合刚度数值计算,是一种理论与实践相结合的方法,可以有效地描述直齿轮系统的动力学特性,为工程实践提供了有益的参考。
在实际工程中,我们可以根据该方法计算并优化直齿轮系统的传动性能,提高其工作效率和稳定性。
对于未来的研究方向,我认为可以进一步探讨基于Weber能量法的直齿轮系统动态响应特性分析,为直齿轮传动系统的设计和优化提供更多的理论支持和实用方法。
- 1、下载文档前请自行甄别文档内容的完整性,平台不提供额外的编辑、内容补充、找答案等附加服务。
- 2、"仅部分预览"的文档,不可在线预览部分如存在完整性等问题,可反馈申请退款(可完整预览的文档不适用该条件!)。
- 3、如文档侵犯您的权益,请联系客服反馈,我们会尽快为您处理(人工客服工作时间:9:00-18:30)。
面齿轮传动啮合刚度数值计算-机械工程论文-工程论文
——文章均为WORD文档,下载后可直接编辑使用亦可打印——
0、引言
作为机械装置中的一个重要零部件,齿轮传动被广泛应用于航空、风电、汽车等领域。
随着工作转速的逐步提高,齿轮传动的动力学性能越来越受到设计、制造及使用者的重视。
相比较其他类型的传动系统,齿轮传动系统的主要不同之处在于: 它不但会因为外部激励而产生动态响应,同时会因为传动过程中啮合齿对数的改变、轮齿的弹性变形及轮齿误差而导致啮合刚度发生变化,从而产生轮齿动态啮合力,且此种由于啮合综合刚度的时变性引起的动态激励是齿轮传动中最主要的动态激励形式之一。
因此,确定齿轮传动的时变啮合刚度一直是齿轮动力学研究中的重要问题。
对于圆柱齿轮的啮合刚度计算问题,已有较多的学者进行过
深入研究,得到了一些比较成熟的计算方法。
对于面齿轮及螺旋锥齿轮等结构相对复杂的齿轮传动形式的啮合刚度计算问题,由于其齿面为复杂曲面,要准确计算时变啮合刚度存在较大难度,因此相关研究文献较少。
Gosselin 等基于有限条法给出了计算螺旋锥齿轮刚度的方法,但也只得到了沿齿高和齿长方向的位移曲线,并没有得到刚度曲线。
Mennem等使用有限单元法计算了不同载荷下轮齿接触柔度,获得了时变刚度。
面齿轮传动是近二十年才真正发展起来的一种主要用于航空领域的齿轮传动形式,针对其啮合刚度的计算方法,目前尚未见文献报道。
在面齿轮的动力学研究中,齿轮啮合刚度都采用经过傅里叶变换后的一次正余弦函数来近似,与实际啮合刚度存在比较大的差异。
有学者研究发现,采用近似时变啮合刚度得到的系统动态因子比采用实际啮合刚度时大,而且不能有效地得到系统在低频阶段的动态响应。
因此,采用近似时变啮合刚度来拟合实际啮合刚度研究齿轮传动系统
动力学行为,并不能正确反映齿轮系统的动态特性。
本文提出了一种新的齿轮传动时变啮合刚度数值计算方法。
首先以直齿圆柱齿轮为例,建立合理的有限元模型,得到直齿圆柱齿轮时变啮合刚度曲线,并与ISO6336方法计算结果进行对比,说明该啮合刚度计算方法的正确性及有限元模型的精确性; 然后应用该啮合刚度计算方法,研究面齿轮传动时变啮合刚度变化规律,得到精确的面齿轮传动时变啮合刚度曲线。
研究结果为面齿轮传动的动力学分析及设计提供参考。
1 齿轮传动啮合刚度计算方法
在齿轮运转过程中,轮齿之间的啮合作用可以简化为一个在啮合线方向上的时变弹簧,弹簧刚度等于该时刻的啮合刚度,如图 1 所示。
图中, 为主动轮转速,Rbp、Rbg分别为主从动轮基圆半径,Km为啮合刚度,T为负载扭矩,LOA(line of action) 表示啮合线。
齿轮啮合刚度的一般表达式为Kn= Fn/ n(1)其中,Fn为法向接触力;n为法向综合弹性变形,它应包括由于局部赫兹接触产生的接触弹性变形量H、轮齿弯曲产生的接触位置的位移F、轮毂变形产生的接触位置的位移R、轴和支撑结构变形对接触点位置的影响量A。
由于考虑轴、轴承及支撑结构变形会使问题过于复杂,故本文暂只考虑H、F及R,因此可以得到
在齿轮传动过程中,由于轮齿受载变形及齿轮误差,从动轮转动位置会偏离其不考虑受载变形及齿轮误差时所应处的理想转动位置。
齿轮传递误差eT在1958 年被Harris定义为从动轮实际转动位移与理想转动位移之差,如图2 所示,其一般表达式为
式中,p、g分别为主从动轮转角; zp、zg分别为主从动轮齿数。
假设齿轮没有承受载荷,此时轮齿没有弹性变形,但是由于轮
齿误差的存在,依旧会产生无负载传递误差eNLT。
在齿轮传动的加载接触分析中,由于存在几何模型误差、有限元网格划分产生的几何误差以及网格划分产生的尺侧间隙,故无负载传递误差是不可避免的。
无负载传递误差导致齿轮啮合过程中轮齿产生刚性位移,该位移在计算轮齿受载变形时必须减除。
同时,为了方便理解,将传递误差转换成啮合线方向上的位移,因此可以得到齿轮副在一定负载下的受载传递误差eLT一般表达式
由此可以得到轮齿啮合过程中综合弹性变形
2、啮合刚度数值计算方法验证
由于结构的复杂性,面齿轮传动啮合刚度计算方法目前尚未
见相关文献报道。
为了说明上述啮合刚度计算方法的正确性及有限元模型的精确性,本文先以直齿圆柱齿轮为例进行计算,并将其与ISO6336: 2006 方法的计算结果进行对比。
2. 1 有限元建模
基于唐进元等提出的齿轮虚拟加工制造方法,采用表1 所示齿轮传动参数,得到高精度的直齿圆柱齿轮三维几何装配模型。
为了节约计算成本,忽略轴及轴承等支撑结构的影响。
鉴于静力学分析中质量分布不会影响分析结果,因此在模型中仅考虑可能产生啮合的5 对轮齿,其他部分简化为一个轮缘圆柱,并分别在大小轮内孔面与其对应旋转轴线上的参考点之间建立刚性耦合约束,在大轮耦合节点施加负载扭矩,在小轮耦合节点施加转动位移,以此来模拟小轮通过与大轮啮合抵消大轮反抗扭矩带动大轮运转的实际工况,边界条件如图 3 所示。
对可能发生接触的 5 对轮齿进行局部网格细化,齿
厚方向最小网格尺寸为0. 037 mm,齿高方向最小网格尺寸为0. 142 mm,总节点数为180 462,总单元数为158 592。
网格模型如图4 所示。
将大轮及小轮的工作齿面定义为接触对,暂不考虑摩擦对啮合刚度的影响。
采用隐式静力学分析算法,输出接触力及大小轮的绕自身旋转轴线的旋转位移历程曲线。
2. 2 直齿圆柱齿轮啮合刚度计算
理论上,标准渐开线齿轮的静态传递误差为零,但考虑到有限元模型不可避免地存在网格划分带来的几何误差,且有限元分析时必须要有完整的边界约束条件,因此,本文近似以大轮负载为13. 2 Nm 时的传递误差作为无负载传递误差,该负载与额定负载660 Nm 相比较小,产生的轮齿接触变形及弯曲变形可以忽略不计。
基于上述齿轮传动啮合刚度计算方法,计算得到该齿轮副时变啮合刚度曲线,并与ISO6336: 2006 给出的计算公式得到的结果进行对比,如图5 所示。
由图 5 可知,所提出的方法得到的时变啮合刚度曲线与ISO6336: 2006 方法计算结果相比,平均值相对误差为5. 86%。
因此可以证明所提出的齿轮传动时变啮合刚度计算方法的正确性,同时说明有限元模型已足够精确。
3、面齿轮传动啮合刚度数值计算
3. 1 有限元模型
面齿轮传动几何参数如表2 所示,其中面齿轮轮缘系数定义为面齿轮轮齿高度与面齿轮齿根平面到面齿轮齿底平面之间距离的比值。
采用上述有限元建模方法,将可能发生接触的5 对轮齿之外的部分简化为一个阶梯圆柱,忽略轴及轴承等支撑结构变形对面齿轮传动接触位置的影响,在小轮内孔面与位于其旋转轴线上的参考节点之间建立刚性耦合约束,在面齿轮与位于其旋转轴线上的参考节点之间建立刚性耦合约束,即将轴及轴承简化为刚性支撑,在小轮参考节点施加旋转位移,在面齿轮参考节点施加负载扭矩,以模拟小轮通过与大轮啮合作用带动大轮抵消负载扭矩而运转的实际工况,边界条件设置如图6 所示。
对于未修形的直齿面齿轮传动而言,面齿轮由齿顶进入啮合,由齿根退出啮合,其理论接触轨迹在齿高方向大致呈一条竖直线。
经齿轮接触分析得到,该对齿轮理论接触轨迹大致位于半径为1 . 4 mm 处,因此对面齿轮靠近内端的一半轮齿及配对小轮对应啮合位置进行网格细化,其网格密度与上述直齿圆柱齿轮模型中细化部分网格密度基本一致,总节点数为242 312,总单元数为201 420,网格模型如图7
所示。
接触定义、材料参数及分析步设置与上述直齿圆柱齿轮有限元模型保持一致。
此时对于单个面齿轮轮齿而言,约有54 个计算点。
3. 2 面齿轮传动啮合刚度数值计算
采用上述有限元模型,在大轮额定载荷为1536. 8 Nm 条件下,取负载为38. 42 Nm 时的传递误差为无负载传递误差。
额定载荷作用下各齿对法向接触力历程曲线如图8 所示。
由图8 可知,该对齿轮副存在双齿接触区(DT) 及三齿接触区(TT) ,并且,由于在三齿接触区时前一对轮齿即将退出啮合,后一对轮齿刚刚进入啮合,齿间载荷分布非常不均匀,因此该对轮齿法向接触力最大值出现在该啮合区域。
进一步根据式(6) 计算得到面齿轮传动时变啮合刚度曲线,如
图9 所示。
由图9 可以看出,面齿轮传动时变啮合刚度曲线类似于一条正弦曲线,呈现明显的周期特征,其最小值大致出现在三齿接触区内前后两对轮齿受载相同的位置(图8中点A 处) 。
此时该两对轮齿约各承担总载荷的6. 44% ,中间一对轮齿约承担总载荷的87. 15% ,齿间载荷的分布非常不均匀,并且此时前后两对轮齿分别在靠近齿根及齿顶位置接触,因此该啮合位置齿轮副弹性综合变形最大,啮合刚度最小。
啮合刚度最大值出现在双齿啮合区内参与啮合的两对轮齿受载相同的位置(图8 中点 B 处) ,此时该两对轮齿各承担总载荷的50%,载荷分布最为均匀,因此该啮合位置齿轮弹性综合变形最小,啮合刚度最大。
图9 时变啮合刚度曲线(T =1536. 8 Nm)
4、结论
(1) 提出了一种新的齿轮传动时变啮合刚度数值计算方法,并给出了相应的加载接触分析有限元建模方法。
(2) 以直齿圆柱齿轮为例,采用该方法得到该齿轮副时变啮合刚度曲线,与ISO6336 方法计算结果相对比,验证了上述方法的正确性及所建有限元模型的精确性。
(3) 应用该啮合刚度数值计算方法得到了面齿轮传动载荷分布规律及时变啮合刚度曲线。