高速线材工艺设计
高速线材生产工艺技术【轧钢厂培训资料】-建筑设计规划-在线
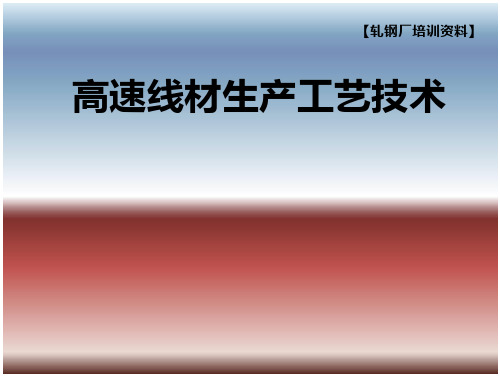
2)15º/75º的德国德马克(Demak) 型;
3)顶交45º的英国阿希洛(Ashlow) 型;
4) 0º/90º平-立布置的达涅利 (Danili)型。
各种机型各有优点,但基本工艺特点 差异不大,其中摩根机型应用最广泛。
现代高线轧机技术新进展
( l ) 无扭精轧机组。其发展趋势如下: 降低机组重心,降低传动轴高度,减少 机组的震动;强化轧机,增加精轧机组 的大辊径轧机的数量;改进轧机调整性 能。
控制冷却是分阶段控制自精轧机轧出的成品轧件的冷 却速度,尽量降低轧件的二次氧化量,可根据钢的化学 成分和使用性能要求,使散卷状态下的轧件从高温奥氏 体组织转变成与所要求性能相对应的常温金相组织。
高线轧机问世后,大盘重自然冷却使产品质量恶化 极为突出,这就使轧后控制冷却工艺被广泛采用,并随 用户对产品日益提高的要求而逐渐完善。轧后控制冷却 工艺已成为高速线材轧机不可分割的组成部分,是高线 轧机区别于老式线材轧机的特点之一。
线材表面不得有裂缝、折叠、结疤、夹层等缺陷,允 许有轻微的划痕。对冷镦、高碳钢丝和琴钢丝用线材,表 面质量要求更加严格,一般必须作酸洗检查。
含碳量在0.3%以上的线材,应严格控制其表面脱碳, 否则脱碳后的线材表面变软,疲劳强度降低。
质量控制手段
各种高质量的线材在质量控制上需要各工序 都具备生产高质量线材的能力,即:
颗粒最长达133μm,一般为≥50μm,进口国外线材最大≥30μ m,一般8μm左右。
(5)钢中气体含量也普遍比国外线材高,〔H〕、〔O〕、 (N〕一般比国外线材高1~2倍甚至更高。
其它差距
主要表现为线材在钢材中的比例、控 冷线材比、硬线比、合金线材比、制品用 线材比、线材直径、大规格盘条、盘重、 减面率、氧化铁皮量、散捆率、尺寸偏差、 不圆度、通条屈服应力差、含碳量、含磷 量、含硫量等方面。
高速线材生产工艺技术

高速线材生产工艺技术
一、前言
高速线材是一种重要的金属产品,在现代工业生产中扮演着重要的角色。
本文将介绍高速线材的生产工艺技术,包括材料选取、生产工艺流程、设备及技术要点等方面的内容。
二、材料选取
高速线材的生产需要选用优质的原材料,通常是优质碳素钢、合金钢等。
这些原材料需要具备良好的硬度、强度、韧性和耐磨性等特性,以确保生产出高质量的线材产品。
三、生产工艺流程
1.原材料准备:将选用的原材料进行清洗、除铁等预处理工序。
2.热处理:通过加热、保温、冷却等工艺,调整原材料的组织结构,
提高其机械性能。
3.坯料加工:将经过热处理的原材料进行拉拔、锻造等加工,使其形
成符合要求的线材坯料。
4.精整加工:通过轧制、精整等工艺,将坯料进行细致加工,使其直
径、表面质量等达到要求。
5.检验与包装:对成品进行检验,保证质量合格后进行包装。
四、设备及技术要点
1.轧机:高速线材的生产需要使用高效的轧机设备,以保证生产效率
和产品质量。
2.管控系统:通过先进的管控系统,实现对生产过程的精确把控,保
证产品质量的稳定性和可靠性。
3.冷却技术:采用合适的冷却技术,可以有效控制产品的温度和晶粒
结构,提高线材的硬度和强度。
五、结语
高速线材的生产工艺技术是一个复杂而精密的过程,需要依靠先进的设备和技术手段,才能生产出高质量的线材产品。
同时,生产过程中的质量管控和技术创新也是至关重要的。
希望本文所介绍的内容能够为相关行业提供一定的参考和帮助。
高速无扭轧机产线材(盘条)的生产工艺与流程解析

高速无扭轧机产线材(盘条)的生产工艺与流程解析高速无扭轧机产线材是一种重要的金属加工技术,通过对金属坯料进行锻压、拉伸等工艺,将其转化为盘条。
在此过程中,生产工艺与流程的设计和控制至关重要,直接影响产品质量和生产效率。
一、工艺流程高速无扭轧机产线材的工艺流程主要包括原料准备、加热处理、轧制、探伤和整理等环节。
下面将对每个环节进行详细解析。
1. 原料准备原料准备是生产过程的第一步,主要包括材料选择和切割。
在选择材料时,应注重材料的成分和性能,以确保产品的质量和性能要求。
切割则是将原料坯料按照一定的长度进行切割,以便后续处理。
2. 加热处理加热处理是为了提高金属坯料的可塑性,使其更容易在后续的工艺过程中进行变形和成形。
通常采用高温加热的方式,将金属坯料加热至一定温度范围内。
3. 轧制轧制是高速无扭轧机产线材的核心工艺环节,通过机械力的作用,将加热后的金属坯料进行连续轧制,最终形成所需的盘条。
4. 探伤轧制后的盘条需要进行探伤,以检测产品内部的缺陷和问题。
常用的探伤方法包括超声波探伤和磁粉探伤等,通过对产品进行全面检测,排除有缺陷的产品。
5. 整理整理是为了提高产品的表面质量,去除表面的氧化层和杂质。
常用的整理方法包括酸洗和钝化等,以确保产品的光洁度和表面质量。
二、工艺设计与控制1. 温度控制加热处理环节中,温度的控制非常关键。
温度过高会导致过度软化,降低产品的强度和硬度;温度过低则会影响金属的可塑性。
因此,在加热处理过程中,需要确保温度稳定且控制在合适的范围内。
2. 轧制参数控制轧制过程中,轧机的参数控制非常重要。
包括轧辊的速度、力度和轧制次数等参数的控制,直接影响产品的尺寸精度和表面质量。
通过合理的参数设定和控制,可以获得满足要求的产品。
3. 探伤精度控制在探伤环节中,需要确保探伤的精度和可靠性。
通过使用先进的探伤设备和技术,可以有效地检测产品内部的缺陷和问题,保证产品质量。
4. 整理工艺优化整理环节中,需要优化工艺参数和方法,以提高产品的外观和质量。
宣钢公司精品高速线材技术改造工程设计

宣钢公司精品高速线材技术改造工程设计摘要:主要介绍宣钢宣钢精品高速线材技术改造工程的设计、技术特点。
关键词:高速线材2.2.1炉型结构及炉温制度全连续式设计1 前言宣钢虽然目前已形成600万吨/年的综合配套生产能力,但运行的设备中有很多落后的工艺装备。
根据《钢铁产业发展政策》和国务院《钢铁产业调整和振兴规划》,列入国家产业政策淘汰和限制目录的装备很多,面临的淘汰落后的任务很艰巨。
宣钢在全面贯彻落实科学发展观、《钢铁产业发展政策》和国务院《钢铁产业调整和振兴规划》的前提下,提出了淘汰落后、装备升级、节能减排、结构调整的技术改造方针,通过设备大型化、淘汰落后、调整产品结构、节能减排、发展循环经济,把宣钢打造成为一个“紧凑型、生态型、创新型、开放型,设备大型化、操作自动化、管理信息化、管理理念精细化”的优质精品长材基地。
综上所述,精品高速线材技术改造工程建成投产后,将淘汰现有热带车间110万吨落后轧钢生产能力,符合宣钢提出的淘汰落后、装备升级、节能减排、结构调整的技术改造方针,对宣钢未来的生存和发展是至关重要。
2工艺设计简介及技术特点2.1设计条件及要求精品高速线材生产线1套(双线)由两个主轧线相互独立的全连续式高速线材生产线组成,分别称为一线和二线。
其中一线以生产精品线材为主,设计年产光圆盘条和螺纹盘条共50万t,二线以生产普通线材为主,设计年产光圆盘条和螺纹盘条共60万t。
每条生产线设1座150t/h的步进梁式加热炉、全连续式线材轧机1套,主轧机共30架,其中精轧机以8+4形式布置,最高终轧速度为112m/s。
坯料为炼钢生产的连铸坯,坯料尺寸165×165×10000mm,2083kg/支。
生产钢种为碳素结构钢、优质碳素结构钢、低合金钢、合金结构钢、冷镦钢、焊条钢、轴承钢、弹簧钢和钢帘线等。
2.2设计原则2.2.1尽量采用先进适用的技术,生产装备起点要高,保证产品的品种质量具有竞争力。
高线工艺流程

一、工艺流程简述炼钢生产的方坯,通过热送辊道进入轧钢厂原料跨,根据工艺要求,可以热装的钢坯,直接进入加热炉进行加热;不可以热装的钢坯,通过翻坯冷床下线冷却,冷却后的钢坯,再通过冷坯上料台架入炉加热。
根据不同钢种的加热制度,钢坯在步进梁式加热炉内加热至950℃~1150℃,再依据轧制节奏的要求,由出炉辊道逐根送出炉外。
出炉后的钢坯经过高压水除鳞装置除却表面的氧化铁皮,然后进入粗轧机组。
出炉钢坯经检查如有缺陷,由剔除装置从辊道剔除。
全线轧机28架,为全连续布置,分为粗轧机组、中轧机组、棒材精轧机组和精轧机组,其中粗轧机组、中轧机组、棒材精轧机组各有6架轧机,线材精轧机组有10架轧机,全线无扭轧制。
粗、中、棒材精轧机组采用平立交替布置,棒材和线材生产共用;线材精轧机组采用辊环悬臂式,45°顶交布置。
轧件经过粗、中、精轧机组的轧制后,由穿水冷却线进入导管,在夹送辊的夹送下进入线材轧制跨。
进入线材轧制跨的轧件,在4#飞飞剪处切头、切尾,然后通过侧活套进入线材精轧机组轧制。
轧件在线材精轧机组内一旦发生事故,4#飞飞剪立即启动,将轧件碎断,防止后续轧件继续进入线材精轧机组。
根据所生产产品的规格,轧件在线材精轧机组内轧制若干道次后被轧制成成品尺寸。
生产φ5.5㎜~φ7.0㎜的的线材时,保证速度为90m/s。
轧件在线材精轧机组内轧制后,进入由水冷装置和风冷运输机组成的控制冷却线。
水冷线共有3段水冷装置,用于控制线材的吐丝温度。
水冷后的线材由夹送辊送入吐丝机。
线材通过吐丝机后形成螺旋状线圈,均匀的铺散在散卷风冷运输辊道上。
根据钢种、规格的不同,可以按照工艺制度改变风机开闭的数量、风机的风量、辊道的运行速度等参数,以调节线卷的冷却速度,保证线卷在理想的冷却速度下实现金相组织的转变,从而获得良好的金相组织和所需机械性能的产品。
线卷在风冷运输辊道上按照所需的冷却速度完成组织转变后,通过线卷分配器平稳地落入集卷筒内,形成外径为φ1250㎜,内径为φ850㎜的盘卷。
高线设计参数(典型)

3.8.4高速线材生产线3.8.4.1产品方案设计规模:45万吨/年产品:Φ5.5~20mm光面盘条Φ6.0~16mm螺纹盘条主要钢种:低合金钢、碳素结构钢、优质碳素结构钢、标准件用钢、冷镦及冷挤压钢、焊条钢、焊网钢。
产品大纲详见表3.8-8。
表3.8-8 高线产品大纲1)盘条直径及盘卷重量线材产品以压紧打捆状态交货。
盘条直径:Φ5.5~20mm盘重:~2465kg2)盘卷尺寸盘卷外径:Φ1250mm盘卷内径:Φ850mm盘卷高度:≤2200mm(打捆后)3.8.4.3原料及金属平衡连铸方坯年需要量为46.5万t。
1)断面边长:165mm×165mm2)定尺长度:12000mm生产线的综合成材率为96.8%,金属平衡见表3.8-9。
表3.8-9 高线金属平衡表图3.8-3高线工艺流程框图3.8.4.5轧机组成轧机由粗轧机组(8架)、中轧机组(8架)、精轧机组(8架)和减定径机组(4架)共28架轧机组成。
粗轧机组、中轧机组前6架(1H~14V)采用平-立交替布置的短应力线轧机,其立式轧机采用上传动型式。
中轧机组的后2架采用V型顶交45º悬臂辊环轧机,精轧机组采用V型顶交45º悬臂辊环轧机,减定径机组采用V型顶交45°悬臂辊环轧机。
轧机基本参数见表3.8-10。
表3.8-10 轧机基本参数表3.8.4.6主要工艺设备组成1)冷坯上料台架数量:1套台面存放钢坯数量:30根2)步进式加热炉数量:1座冷装额定加热能力:150t/h 3)无头轧制焊机数量:1套4)1号飞剪数量:1台型式:曲柄式工作制度:启停工作制5)2号飞剪数量:1台型式:回转式工作制度:连续工作制6)预水冷装置数量:1套7)精轧后水冷装置数量:1套8)减定径后水冷装置数量:1套9)高速飞剪数量:1套10)夹送辊和吐丝机数量:1套吐丝机机型:卧式吐丝机11)散卷冷却运输线数量:1套12)集卷站数量:1套13)立式卷芯架及P/F运输线数量:1套14)打捆机数量:2台15)称重装置数量:1台16)卸卷站数量:1台(双工位)3.8.4.7工艺平面布置主厂房由钢坯跨、加热炉跨、主轧跨、成品跨、轧辊间组成。
高线棒材车间轧钢工艺选择设计

高线棒材车间轧钢工艺选择3 轧钢工艺3.1生产规模及产品3.1.1生产规模及产品方案全连续优质钢高速线材车间,设计生产能力为年产优质热轧圆钢和带肋钢筋62 万吨。
高线最大终轧速度120 m/s 。
直条最大终轧速度12 m/s产品规格为:Φ6~Φ25mm 热轧带肋钢筋和Φ 5.5 ~Φ22mm 的热轧盘圆。
主要钢种有:轴承钢、低碳钢、优质碳素钢、低合金钢等。
3.1.2产品质量部分线材按以下国家标准组织生产、进行检验和交货。
GB 1499.2-2007 钢筋混凝土用热轧带肋钢筋GB 1499.1-2008 钢筋混凝土用热轧光圆钢筋GB/T4354-2008 优质碳素钢热轧盘条GB/T 4155-2006 标准件用碳素钢热轧圆钢及盘条3.1.3成品交货状态成品线材以盘条成捆状态/直条成捆状态交货。
每捆线材重量:2000 ~4000kg打捆道次:捆4 道/盘条;5 道/直条;3.1.4原料及金属平衡连铸坯由本公司炼钢厂提供,经检验及钢坯修磨后,质量符合YB/T2011-2004 标准。
坯料技术条件如下:断面尺寸:150 ×150 ×12000mm ,单根坯料重量:2106kg1断面尺寸:165 ×165 ×12000mm ,单根坯料重量:2548kg 断面尺寸:180 ×180 ×12000mm ,单根坯料重量:3033kg最短钢坯长度6000mm ,短尺钢坯不超过钢坯总量的10%钢坯尺寸偏150 ×150 mm 钢坯:+5mm,-5mm;差:长度允许偏差:+20mm 。
165 ×165 mm 钢坯:+5mm,-5mm;长度允许偏差:+20mm 。
180 ×180 mm 钢坯:+5mm,-5mm;长度允许偏差:+20mm 。
对角线长度之差:150 ×150 mm / 165 ×165 mm/180 ×180 mm 坯料:最大允许7mm 。
年产60万吨高速线材车间工艺设计

序号
型钢品种
成品规格直径/mm
产量
万t/年
比例%
1
热轧盘条普碳钢
Ø5.5、Ø6.5、Ø8、Ø10、Ø12
30
46
2
焊接用钢热轧盘条
Ø5.5、Ø6.5、Ø8、Ø10、Ø12
5
7.6
3
混凝土用热轧盘条
Ø5.5、Ø6.5、Ø8、Ø10、Ø12
10
15.4
4
制丝用中高碳优质热轧盘条
6.1电机的校核
6.2典型产品电机的校核
6.3咬入条件校核
7型钢生产车间的生产能力计算及技术经济指标·····················38
7.1轧制工作图表
7.2典型产品的轧机小时产量
7.3轧机年可轧制时间
8典型产品孔型设计················································································40
177
201
227
254
283
314
注:1、表中的理论重量,按密度为7.85g/cm3计算。
2、表中带*不推荐使用。
(2)圆钢直径和方钢边长的允许偏差应符合表1-3的规定。
表1-3圆钢直径和方钢边长的允许偏差
圆钢直径d方钢边长a/mm
精度组别
圆钢直径d方钢边长a/mm
精度组别
允许偏差,mm
允许偏差,mm
盘条按用途分拉丝用和建筑或其他用途两类,代号为L(拉丝用)和J(建筑用或其他用途)。
(2)尺寸、外型、重量及允许偏差
盘条的公称直径为:5.5、6.0、6.5、7.0、8.0、9.0、10.0、11.0、12.0、13.0、14.0mm。根据供需双主协议也可以生产其他尺寸的盘条。
- 1、下载文档前请自行甄别文档内容的完整性,平台不提供额外的编辑、内容补充、找答案等附加服务。
- 2、"仅部分预览"的文档,不可在线预览部分如存在完整性等问题,可反馈申请退款(可完整预览的文档不适用该条件!)。
- 3、如文档侵犯您的权益,请联系客服反馈,我们会尽快为您处理(人工客服工作时间:9:00-18:30)。
高速线材车间工艺设计及帘线钢质量控制技术摘要本设计是依据鞍钢线材厂设计的年产量55万吨的高速线材车间工艺。
典型产品为Q235、Φ6mm的线材。
设计说明书包括文献综述,车间工艺设计,专题三个部分。
在综述部分叙述了线材的基本知识和当前线材生产的状况。
设计部分(从第二章到第九章)主要包括产品方案及工艺流程的设计及制定、生产设备的选择、工艺参数的计算及校核、年产量计算、导位装置及轧机调整、车间平面布局设计及图纸绘制,还有技术经济指标与环保措施。
专题部分主要阐述了对帘线钢质量控制的方法及研究。
关键词:高速线材;生产方案;孔型设计;校核;帘线钢High-speed wire rod plant process design and quality control of steel cordAbstractThis design which is based on Anshan Iron and Steel Wire Factory is planted 550,000 t annual workshop for high-speed wire rod plant technology. Typical produce is the Q235,Φ6mm wire. Design specification includs literature review, workshop process design andproject. The literature review part describes the basic knowledge of wire rod production andthe current situation. Design part (from chapter to chapter IX) describes the main program andthe process of product design and development, production and equipment selection, process parameter calculation and checking, annual basis, the guide position adjusting device andmill,shop flat design and layout drawings, as well as technical and economic indicators and environmental protection measures. The major topics describes method and technology in quality control of steel cord.Keyword:High-speed wire; production program; pass design; check;Steel Cord目录摘要............................................................................................................................................I Abstract...................................................................................................................................II 1文献综述..............................................................................................................................1 1.1线材生产的基本知识...................................................................................................1 1.1.1线材的定义.........................................................................................................1 1.1.2线材的种类.........................................................................................................1 1.1.3线材的品种与用途.............................................................................................1 1.2生产工艺.......................................................................................................................4 1.2.1线材的生产工艺流程.........................................................................................4 1.2.2线材的生产特点.................................................................................................4 1.2.3线材生产轧机布置.............................................................................................5 1.3产品的质量控制...........................................................................................................6 1.3.1坯料控制.............................................................................................................6 1.3.2加热控制.............................................................................................................7 1.3.3轧制控制.............................................................................................................8 1.3.4冷却控制.............................................................................................................8 1.4生产的发展...................................................................................................................9 1.4.1轧制速度进一步提高 (9)1.4.2采用减径定径机组 (10)1.4.3无扭轧机...........................................................................................................12 1.4.4低温轧制技术...................................................................................................12 1.4.5采用控制轧制和控制冷却...............................................................................12 1.4.6无头轧制 (13)1.4.7采用低温轧制和温控轧制技术.......................................................................13 1.4.8广泛采用在线测径及涡流探伤仪...................................................................13 1.4.9高线轧机的其他新设备...................................................................................13 1.5本设计的目的和意义.................................................................................................14 2产品大纲及金属平衡表制定......................................................................................15 2.1产品方案的确定.........................................................................................................15 2.1.1产品方案...........................................................................................................15 2.1.2产品大纲...........................................................................................................15 2.2坯料的确定.................................................................................................................15 2.2.1坯料的选择 (15)2.2.2坯料的技术条件...............................................................................................16 2.2.3对表面质量与内部质量的要求.......................................................................17 2.3生产方案的确定.........................................................................................................18 2.4金属平衡表的制定................................................................................. (19)3主要设备选择及其参数设定......................................................................................20 3.1加热炉.........................................................................................................................20 3.2轧机参数.....................................................................................................................22 3.2.1粗轧机组设备参数...........................................................................................22 3.2.2中轧机组设备参数...........................................................................................23 3.2.3预精轧机组设备参数.......................................................................................24 3.2.4精轧机组设备参数...........................................................................................25 3.3冷却设备.....................................................................................................................26 3.4辅助设备性能参数.....................................................................................................28 3.4.1飞剪、摆动剪、卡断剪 (28)3.4.2吐丝机...............................................................................................................28 3.4.3集卷筒...............................................................................................................29 3.4.4立活套、侧活套...............................................................................................29 4产品工艺制度制定.........................................................................................................30 4.1生产工艺流程.............................................................................................................30 4.2加热制度的制定.........................................................................................................31 4.2.1加热目的...........................................................................................................31 4.2.2加热温度...........................................................................................................31 4.2.3钢坯的加热速度和加热时间...........................................................................32 4.3轧制温度的确定.........................................................................................................33 4.4延伸系数的确定 (34)4.4.1轧制道次的确定...............................................................................................34 4.4.2各道次延伸量的确定.......................................................................................34 4.5冷却工艺的确定.........................................................................................................35 5孔型设计............................................................................................................................36 5.1孔型设计的基本内容.................................................................................................36 5.1.1孔型设计的内容...............................................................................................36 5.1.2孔型设计的要求...............................................................................................36 5.1.3孔型的分类.......................................................................................................36 5.1.4孔型设计的原则...............................................................................................36 5.2线材生产中的孔型系统.............................................................................................37 5.2.1孔型类型...........................................................................................................37 5.2.2线材中孔型系统选择分析...............................................................................37 5.3孔型设计.....................................................................................................................38 5.3.1圆孔型设计.......................................................................................................38 5.3.2椭圆孔型设计...................................................................................................39 5.3.3箱型孔型设计...................................................................................................40 5.3.4连轧常数及轧制速度.......................................................................................40 6轧制力能参数及设备校核...................................................................... (42)6.1摩擦系数确定.............................................................................................................42 6.2轧制力计算.................................................................................................................42 6.3咬入能力校核.............................................................................................................44 6.4轧辊强度校核.............................................................................................................45 6.4.1粗轧机组轧辊强度校核...................................................................................46 6.4.2中轧机组轧辊强度校核...................................................................................47 7年产量计算.......................................................................................................................50 7.1轧机工作图表的绘制.................................................................................................50 7.1.1轧制节奏时间的确定.......................................................................................50 7.1.2轧机工作图表的绘制.......................................................................................51 7.2轧机年产能力计算 (52)7.2.1轧机平均小时产量...........................................................................................52 7.2.2车间年产量计算...............................................................................................53 7.3加热炉生产能力计算.................................................................................................53 7.4仓库面积计算.............................................................................................................54 8车间平面布置及主要技术经济指标........................................................................55 8.1车间平面布置.............................................................................................................55 8.1.1主要设备间距的确定.......................................................................................55 8.1.2车间原料仓库和成品仓库面积的确定...........................................................55 8.2 车间主要技术经济指标和环保..............................................................................56 8.2.1车间主要技术经济指标...................................................................................56 8.2.2能源消耗...........................................................................................................56 8.3环境保护对车间设计的要求.....................................................................................58 9专题 帘线钢的质量控制技术.............................................................................60 9.1生产工艺.....................................................................................................................60 9.1.1钢帘线的生产工艺...........................................................................................60 9.1.2钢帘线钢的生产技术.......................................................................................61 9.2对钢帘线钢的质量要求及控制措施.........................................................................61 9.2.1钢帘线钢的化学成分 (61)9.2.2夹杂物控制.......................................................................................................62 9.2.3中心偏析...........................................................................................................62 9.2.4有害气体含量及残余元素的控制...................................................................63 9.2.5表面质量及内部缺陷.......................................................................................63 9.2.6结构特性...........................................................................................................63 9.3钢帘线钢生产的现状和展望.....................................................................................63 9.3.1国内外部分钢厂生产钢帘线钢的概况...........................................................63 9.3.2钢帘线钢高强度化的努力方向.......................................................................64 9.3.3钢帘线钢生产今后的展望...............................................................................64 9.4结论.............................................................................................................................65 附录A 计算机C 程序代码...................................................................... (66)附录B 孔型图 (70)参考文献 (73)结束语...................................................................... (74)1文献综述1.1线材生产的基本知识1.1.1线材的定义线材是热轧型钢中断面尺寸最小的一种。