风力发电叶片
风力发电机叶片转动原理

风力发电机叶片转动原理
风力发电机的叶片转动原理是利用风的动能来推动叶片旋转,进而驱动发电机发电。
具体过程如下:
1. 风力发电机通常由三个叶片、轴承、主轴和发电机组成。
叶片通常采用光滑的曲线形状,并安装在主轴上。
2. 当风吹向风力发电机时,风的动能会击打叶片表面。
由于叶片设计成了类似于飞机翅膀的形状,这就会产生升力。
3. 升力会使得叶片开始旋转,转动的方向与顺风方向相反。
这是因为叶片的斜面使得风来不及通过,从而在叶片前方形成了高压区域,而在叶片背后形成了低压区域。
低压区域和高压区域之间的气压差推动了叶片旋转。
4. 主轴连接叶片,当叶片旋转时,主轴也会跟着旋转。
主轴的旋转通过轴承传到发电机上。
5. 发电机利用主轴的旋转动力来产生电能。
通常情况下,发电机由磁铁和线圈组成。
主轴上的磁铁旋转时,会产生一个磁场变化,进而在线圈中产生电磁感应,使电流通过线圈,从而产生电能。
通过风力发电机叶片转动原理,风能被转化为电能,实现了可再生能源的利用。
风力发电机叶片维修

风力发电机叶片维修
风力发电机叶片维修主要包括以下几个方面:
1. 受损叶片更换:如果叶片受到损坏,需要及时更换。
维修人员会检查叶片的损坏程度,如果只有局部损坏,可以进行修复;如果损坏过于严重,需要更换整个叶片。
2. 叶片表面清洁:风力发电机叶片在运行过程中会积累灰尘、油脂和其它污垢,影响风能的转换效率。
维修人员会使用清洁工具和清洁剂对叶片表面进行清洁,保持其表面光滑。
3. 叶片平衡校正:风力发电机叶片在长期运行过程中可能会出现平衡问题,导致震动和噪音增加。
维修人员会使用专业工具对叶片进行平衡校正,减少其振动和噪音。
4. 叶片涂层维护:叶片表面通常涂有特殊的防风化涂层,用于保护叶片免受风蚀和紫外线辐射的损害。
维修人员会定期检查叶片涂层的状况,如有需要会进行修复或重新涂层。
5. 叶片结构检查:维修人员会对叶片的结构进行检查,确保其没有裂缝、变形或其它潜在问题。
如果发现问题,会及时修复或更换叶片。
总之,风力发电机叶片维修需要由专业的维修人员进行,他们会根据实际情况选择合适的维修方法和工具,确保叶片的正常运行。
风力发电叶片转动原理
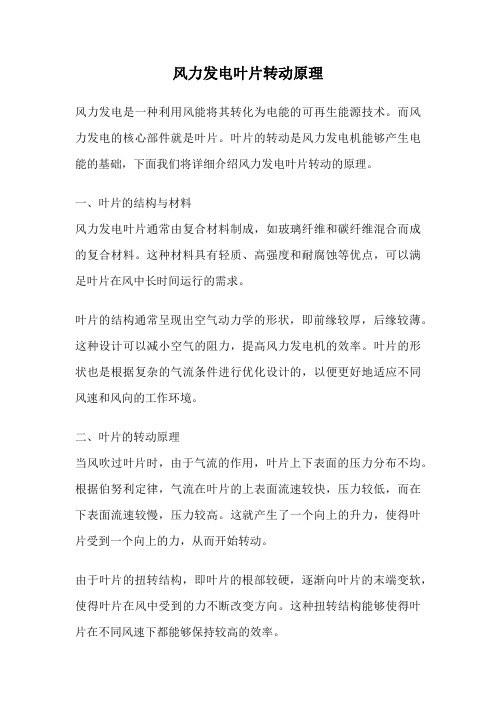
风力发电叶片转动原理风力发电是一种利用风能将其转化为电能的可再生能源技术。
而风力发电的核心部件就是叶片。
叶片的转动是风力发电机能够产生电能的基础,下面我们将详细介绍风力发电叶片转动的原理。
一、叶片的结构与材料风力发电叶片通常由复合材料制成,如玻璃纤维和碳纤维混合而成的复合材料。
这种材料具有轻质、高强度和耐腐蚀等优点,可以满足叶片在风中长时间运行的需求。
叶片的结构通常呈现出空气动力学的形状,即前缘较厚,后缘较薄。
这种设计可以减小空气的阻力,提高风力发电机的效率。
叶片的形状也是根据复杂的气流条件进行优化设计的,以便更好地适应不同风速和风向的工作环境。
二、叶片的转动原理当风吹过叶片时,由于气流的作用,叶片上下表面的压力分布不均。
根据伯努利定律,气流在叶片的上表面流速较快,压力较低,而在下表面流速较慢,压力较高。
这就产生了一个向上的升力,使得叶片受到一个向上的力,从而开始转动。
由于叶片的扭转结构,即叶片的根部较硬,逐渐向叶片的末端变软,使得叶片在风中受到的力不断改变方向。
这种扭转结构能够使得叶片在不同风速下都能够保持较高的效率。
三、叶片转动与发电机的连接叶片转动产生的机械能需要通过传动系统传递给发电机,进而转化为电能。
传动系统通常由主轴、齿轮和发电机组成。
当叶片转动时,主轴也会随之转动,通过齿轮的传动作用,将叶片的转动速度提高,并传递给发电机。
发电机利用叶片转动带来的机械能,通过电磁感应原理将其转化为电能。
四、风向的调整与控制为了使风力发电机能够在不同风向下都能够工作,通常在风轮前方设置一个风向调整装置。
这个装置可以通过感应风的方向来调整整个风轮的转向,使其始终面向风的方向。
这样可以最大程度地利用风能,提高发电效率。
为了保护风力发电机免受过大的风速和风向的影响,通常在风力发电机上设置风速传感器和控制系统。
当风速过大或风向异常时,控制系统会自动调整叶片的角度,或者直接停止运行,以保护整个系统的安全运行。
总结起来,风力发电叶片转动的原理是通过气流的作用,使叶片产生向上的升力,从而开始转动。
风力发电叶片

风力发电叶片1. 简介风力发电是利用风能产生电力的一种可再生能源技术。
在风力发电系统中,风力发电叶片是将风能转化为机械能的重要组成部分。
本文将介绍风力发电叶片的结构设计、材料选择和性能优化等相关内容。
2. 结构设计风力发电叶片的结构设计是保证其工作效率和稳定性的关键。
一般而言,风力发电叶片采用对称的空气动力学外形,以提高其抗风载荷和动态特性。
常见的风力发电叶片设计结构包括单叶片结构、双叶片结构和三叶片结构。
2.1 单叶片结构单叶片结构是最简单的风力发电叶片设计,通常由一根悬臂梁构成。
该结构的优点是结构简单、重量轻,适用于小型风力发电系统。
然而,由于单叶片结构的刚度较低,容易受到外部风载荷的影响,稳定性较差。
2.2 双叶片结构双叶片结构是常见的风力发电叶片设计,由两个对称的叶片组成。
该结构的优点是稳定性较高,能够在较强的风力环境中工作。
同时,双叶片结构还具有较好的平衡性能和动态特性。
2.3 三叶片结构三叶片结构是目前最常用的风力发电叶片设计。
该结构具有良好的平衡性能和稳定性,能够适应不同风力环境下的运行要求。
此外,三叶片结构在启动和停止过程中的动态响应也较为平稳。
3. 材料选择风力发电叶片的材料选择是确保其强度和耐久性的重要因素。
常用的风力发电叶片材料包括玻璃纤维增强塑料(FRP)、碳纤维增强塑料(CFRP)和复合材料等。
3.1 玻璃纤维增强塑料(FRP)玻璃纤维增强塑料是一种常用的风力发电叶片材料。
其优点包括价格低廉、良好的抗腐蚀性能和较高的强度。
然而,玻璃纤维增强塑料的密度较大,导致叶片重量较重,不利于提高风力发电系统的效率。
3.2 碳纤维增强塑料(CFRP)碳纤维增强塑料是一种轻质高强度的风力发电叶片材料。
相比于玻璃纤维增强塑料,碳纤维增强塑料具有更大的比强度和比刚度,可以显著减轻叶片的重量,提高风力发电系统的效率。
然而,碳纤维增强塑料的价格较高,制造成本较大。
3.3 复合材料复合材料是一种由两种或两种以上的材料组成的材料。
风力发电机组的叶片

风力发电机组的叶片风力发电是一种非常环保且具有广阔应用前景的新能源,其利用风能将其转换为电能的方式实现了对人类能源需求的贡献。
然而,在实际应用风力发电技术时,风力发电机组的叶片是关键所在,其质量、气动性能的良好与否,直接决定着风力发电的效率和成本。
风力发电机组的叶片关键参数风力发电机组的叶片是介于风机轴心和风机尾部之间的组成部分,其由从根部到尖端逐渐变细的两翼结构组成,因此具有较高的气动弯曲强度和柔韧性。
根据叶片的气动设计和制造材料的不同,其长度和尺寸参数也会有所差异。
常见的风力发电机组的叶片长度在60-100米之间,而其长度也是其风能转换的重要参数之一。
在实际应用中,风力发电机组的叶片主要需要满足以下关键参数:1.重量风力发电机组的叶片重量由气动设计和制造材料所决定,其过重不仅会导致风力发电机组的结构疲劳和寿命缩短,同时也会增加其制造和运输环节的成本。
2.耐腐蚀性风力发电机组的叶片常常面临着强烈的日晒、雨淋等环境,因此其制造材料需要具有较高的耐腐蚀性,减少其耗损和故障的概率。
3.气动性能风力发电机组的叶片要求具有较好的气动性能,包括阻力小、湍流等特点,以提高风能转换的效率。
4.稳定性风力发电机组的叶片需要具有较好的稳定性,以应对风力、风向等自然条件的变化。
风力发电机组的叶片制造技术叶片的制造技术是制约其质量和气动性能的另一个重要因素。
目前,风力发电机组的叶片制造技术主要有以下几种:1.复合材料叶片制造技术这种制造技术主要采用碳纤维、玻璃钢等复合材料制成一个个小型复合件,再将其拼接成大型叶片完成制造。
这样制造出的叶片不仅具有较好的气动性能,同时也具有较好的抗腐蚀性、轻量化等特点。
2.全铝合金叶片制造技术这种制造技术采用高强度的铝合金材料制造,相对于复合材料制造的叶片,全铝合金叶片制造技术更为成熟和完善,其叶片能够足够承受较高的气动负载和动荷载。
总之,在实际应用风力发电技术时,风力发电机组的叶片是一个十分重要的组成部分,其对风力发电的效率、成本、制造和运输等方面都有着重要的影响。
风力发电叶片质量标准

风力发电叶片质量标准
风力发电叶片的质量标准包括以下几个方面:
1. 材料质量:叶片通常采用玻璃纤维和碳纤维等复合材料制造,材料必须符合相应的国家标准或行业标准,确保叶片的强度、刚度和耐久性等性能。
2. 外观质量:叶片的外观应该光滑、平整,表面不能有明显的凹凸、裂纹、气泡等缺陷,以确保叶片在运行过程中的aerodynamic performance。
3. 尺寸准确性:叶片的尺寸应符合设计要求,并且保持一致性。
叶片的长度、宽度、厚度和弯曲角度等参数必须在一定的公差范围内,以确保叶片的 aerodynamic performance。
4. 力学性能:叶片必须能够承受风力的作用并转化为机械能,因此其力学性能非常重要。
叶片的强度、刚度、耐久性等指标必须符合设计要求,在实际运行中能够承受风力的冲击和变化。
5. 静态与动态平衡:叶片安装在风力发电机上后,需要具有良好的静态和动态平衡,以减少振动和噪声,并保证风力发电机的正常运行。
以上是一些常见的风力发电叶片质量标准,具体的标准和要求可能会根据国家、行业以及叶片制造商的要求而有所不同。
风力发电机叶片材料

风力发电机叶片材料
风力发电机叶片是风力发电机的重要组成部分,其材料选择直接影响着风力发
电机的性能和效率。
目前,常见的风力发电机叶片材料主要包括玻璃钢、碳纤维复合材料和木质材料等,每种材料都有其特点和适用场景。
玻璃钢是一种由玻璃纤维和树脂复合而成的材料,具有重量轻、强度高、耐腐
蚀等优点,因此在风力发电机叶片中得到了广泛应用。
玻璃钢材料的优点在于其成本相对较低,且易于加工和维护,适用于大部分风力发电机叶片的制造。
然而,玻璃钢材料也存在着易老化、易磨损等缺点,需要定期进行维护和更换。
碳纤维复合材料是近年来风力发电机叶片材料的新宠,其具有重量轻、强度高、耐腐蚀、抗风压等优点,能够有效提高风力发电机的效率和稳定性。
碳纤维复合材料的使用可以减轻叶片的重量,降低振动和噪音,延长使用寿命,但其制造成本较高,加工难度大,需要高技术要求和昂贵的设备。
木质材料是传统的风力发电机叶片材料,具有资源丰富、成本低廉等优点,适
用于一些小型风力发电机的制造。
然而,木质材料在强度、耐腐蚀等方面不如玻璃钢和碳纤维复合材料,且易受湿度、虫蛀等影响,需要定期保养和更换。
除了以上几种常见的风力发电机叶片材料外,还有一些新型材料如生物质复合
材料、金属材料等也在研究和应用中。
这些材料各有特点,可以根据具体的风力发电机的使用环境、功率大小、使用寿命等因素进行选择。
总的来说,风力发电机叶片材料的选择应综合考虑材料的重量、强度、耐腐蚀性、成本等因素,以及具体的使用环境和要求。
未来随着材料科学的发展和技术的进步,相信会有更多更优秀的材料出现,为风力发电机的发展提供更好的支持。
风力发电机叶片检测方法

风力发电机叶片检测方法摘要:一、引言二、风力发电机叶片检测方法概述1.视觉检测2.红外热像检测3.超声波检测4.激光雷达检测5.振动检测三、各类检测方法的优缺点四、发展趋势与展望五、结论正文:一、引言随着风力发电在我国的普及和可持续发展,风力发电机叶片的安全运行已成为关注的焦点。
叶片作为风力发电机的关键部件,其运行状态直接影响到整个风力发电系统的性能和寿命。
因此,对风力发电机叶片进行有效的检测具有重要意义。
本文将对风力发电机叶片的检测方法进行综述,以期为风力发电机叶片的安全运行提供参考。
二、风力发电机叶片检测方法概述1.视觉检测视觉检测是通过观察叶片的外观、表面损伤、裂纹等方面来判断叶片的运行状态。
这种方法直观、简单,但受限于观察角度、光照条件等因素,检测效果有限。
2.红外热像检测红外热像检测是通过测量叶片表面的温度分布,分析叶片在不同温度场下的热传导性能。
这种方法可发现叶片内部的温度异常,从而判断叶片是否存在损伤或故障。
3.超声波检测超声波检测是通过发射超声波扫描叶片,检测叶片内部的结构和厚度。
这种方法可发现叶片内部的裂纹、疏松等缺陷,具有较高的检测准确性。
4.激光雷达检测激光雷达检测是通过激光束扫描叶片表面,获取叶片的三维几何信息。
这种方法可实现对叶片表面的高精度检测,适用于大型风力发电机叶片的检测。
5.振动检测振动检测是通过测量叶片在运行过程中的振动参数,分析叶片的运行状态。
这种方法可发现叶片是否存在不平衡、损伤等问题,但对叶片的安装角度和运行条件有一定要求。
三、各类检测方法的优缺点1.视觉检测:优点是直观、简单;缺点是检测效果受限于观察角度、光照条件等因素。
2.红外热像检测:优点是可发现叶片内部的温度异常;缺点是对叶片表面的清洁度要求较高,且不易检测到表面损伤。
3.超声波检测:优点是检测准确性高;缺点是检测过程较为复杂,对操作人员要求较高。
4.激光雷达检测:优点是高精度、适用于大型叶片检测;缺点是设备成本较高,对环境条件有一定要求。
- 1、下载文档前请自行甄别文档内容的完整性,平台不提供额外的编辑、内容补充、找答案等附加服务。
- 2、"仅部分预览"的文档,不可在线预览部分如存在完整性等问题,可反馈申请退款(可完整预览的文档不适用该条件!)。
- 3、如文档侵犯您的权益,请联系客服反馈,我们会尽快为您处理(人工客服工作时间:9:00-18:30)。
• 玻璃纤维复合材料风力发电叶片的有限元模型 • 有限元模型边界条件,加载条件 • 有限元分析结果 • 碳纤维复合材料在叶片的有限元模型的应用 • 碳纤维复合材料叶片的有限元分析结果
a
1
• 玻璃纤维复合材料风力发电叶片的有限元模型
• 有限元分析软件:Abaqus 6.11 • 叶片总长度:40米 • 有限元单元类型:S4 (4节点壳体单元) • 有限元模型主要结构:形状
2. 应力分布
最大应力:9.451兆帕
3. 应变分布
最大应变:0.2739%
4. 位移分布
最大位移:1.781米
a
7
• 分析结果: edgewise静载荷条件,碳纤维
1. 叶片变性前后形状
2. 应力分布
最大应力:8.339兆帕
3. 应变分布
最大应变:0.2265%
4. 位移分布
固定根部
F1=105N
F2=3x105N
10m
30m
a
3
• 分析结果: flapwise静载荷条件,玻璃纤维
1. 叶片变性前后形状
2. 应力分布
最大应力:18.19兆帕
3. 应变分布
最大应变:0.5156%
4. 位移分布
最大位移:5.114米
a
4
• 分析结果: edgewise静载荷条件,玻璃纤维
最大位移:0.8488米
a
8
结论
在同样的加载条件下,碳纤维复合材料叶片的应力, 应变,位移均比玻璃纤维复合材料叶片小。
a
9
面壳结构(skin),主梁(shear web)等 • 有限元模型材料:玻璃纤维强化复合材料 • 复合材料纤维铺层方向:零度,正负四十五度
a
2
• 有限元模型边界条件,加载条件
条件1:固定根部,施加flapwise静载荷
固定根部
F1=105N
F2=3x105N
10m
30m
条件1:固定根部,施加edgewise静载荷
1. 叶片变性前后形状
2. 应力分布
最大应力:14.49兆帕
3. 应变分布
最大应变:0.4095%
4. 位移分布
最大位移:1.748米
a
5
• 碳纤维复合材料在叶片的有限元模型的应用
•横梁盖(红色部分): 玻璃纤维复合材料 碳纤维复合材料
比起玻璃纤维,碳纤维具有更高 的刚度和强度。
a
6
• 分析结果: flapwise静载荷条件,碳纤维