余热余压发电技术(钢铁)
2024年高炉余压发电市场前景分析

2024年高炉余压发电市场前景分析介绍高炉余压发电是一种利用高炉炼铁过程中产生的高压余热,通过适当的装置和设备转化为电能的技术。
随着我国钢铁工业的快速发展和节能减排政策的实施,高炉余压发电技术逐渐得到重视。
本文将分析高炉余压发电市场的发展前景。
市场需求1.节能减排政策的推动:随着环境保护意识的增强,钢铁行业需要采取节能减排措施。
高炉余压发电作为一种利用废热资源的技术,能够有效减少钢铁生产过程中的能源消耗和二氧化碳排放,符合节能减排政策的要求。
2.能源供给紧张:我国能源供给紧张,电力需求不断增长。
高炉余压发电可以增加钢铁企业自身的电力供应能力,减少对外购电的需求,缓解能源供给紧张的问题。
3.经济效益:高炉余压发电技术可以将废热转化为电能,提高钢铁企业的自给能力,减少能源成本。
此外,高炉余压发电技术还可以通过售电获取收入,进一步提高经济效益。
技术发展1.技术成熟度提高:随着高炉余压发电技术的不断发展和应用,其成熟度逐渐提高。
传统的蒸汽轮机和发电机组已经得到广泛应用,并且不断有新的技术和设备问世,如透平发电技术、余压发电机组等,进一步提高了高炉余压发电技术的效率和可靠性。
2.投资成本降低:随着技术的成熟和市场规模的扩大,高炉余压发电设备的生产和安装成本逐渐降低。
此外,政府对于节能减排的政策和经济刺激措施也为企业投资高炉余压发电提供了支持,进一步降低了投资成本。
市场前景1.市场规模扩大:随着我国钢铁行业的持续快速发展,高炉余压发电市场规模不断扩大。
据统计,我国钢铁企业中有相当一部分已经采用高炉余压发电技术,但整体普及率还不高,有很大的市场潜力。
2.政策支持力度加大:我国政府高度重视节能减排工作,通过出台一系列的政策文件和经济刺激措施来推动高炉余压发电技术的应用和普及。
政策的支持力度加大将促进高炉余压发电市场的快速发展。
3.国际市场需求增加:随着全球对于环境保护和可持续发展的需求增加,高炉余压发电技术也得到了国际市场的关注。
钢铁厂余热发电
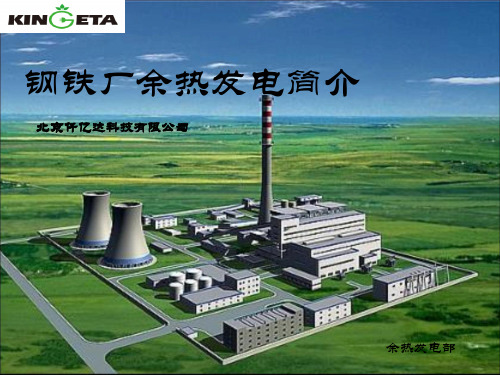
余热发电部
联系电话:010 56874500/01
干熄焦余热发电
定义:所谓干熄焦,是相对湿熄焦而言的,是指采用惰性气体将 红焦降温冷却的一种熄焦方法。通常CDQ是焦炭干法熄焦 的简称,Coke Dry Quenching 。
原理: 在干熄焦过程中,1000℃的红焦从干熄炉顶
部装入, 130℃的低温惰性循环气体由循环风机鼓 入干熄炉冷却段红焦层内,吸收红焦显热,冷却后 的焦炭(低于200℃ )从干熄炉底部排出,从干熄 炉环形烟道出来的高温惰性气体流经干熄焦锅炉进 行热交换,锅炉产生蒸汽,冷却后的惰性气体由循 环风机重新鼓入干熄炉,惰性气体在封闭的系统内 循环使用。
低温余热发电技术------面向钢铁余热方向 燃气轮机——蒸汽轮机联合发电
煤气燃烧余热发电
燃气轮机——蒸汽轮机联合循环发电流程图
低温余热发电技术------面向钢铁余热方向
设备 煤气燃烧余热发电
170t/h 燃气轮机尾气联合循环锅 炉(高炉煤气与焦炉煤气)
联合循环汽轮机
低温余热发电技术------面向钢铁余热方向
钢铁厂余热发电简介
北京仟亿达科技有限公司
余热发电部
低温余热发电技术------面向钢铁余热方向
仟亿达致力于余热发电行业
工业余热发电行业是国家新兴节能环保行业之一,符合国家关于节
能和资源综合利用政策,同时也蕴藏着巨大的市场空间。目前,公司 与多家专业科研单位合作,承担建材行业中的水泥窖、冶金行业中的 高炉煤气、烧结机、转炉、等工业余热回收,采用余热锅炉产生的蒸 汽带动汽轮机发电机组发电。
的结构形式,又可分为带式、环式、格式、塔式和盘式。鼓风环冷 是目前应用较普遍的一种方式。
低温余热发电技术------面向钢铁余热方向
钢铁生产余热、余压再利用技术的探讨
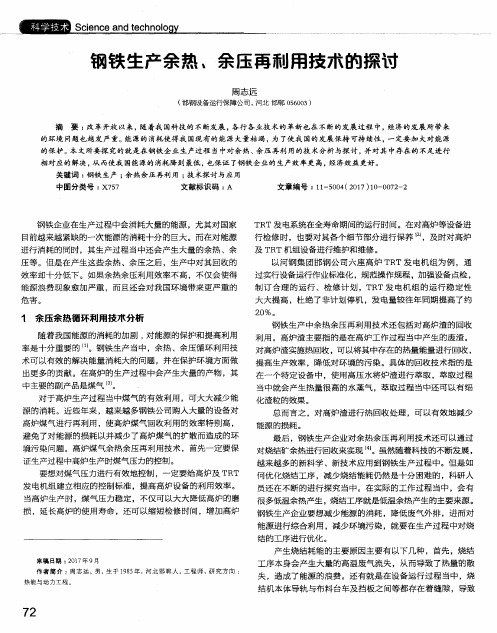
钢 铁生 产中余 热余 压再利 用技 术还包 括对 高炉渣 的 回收 利用 。高炉 渣主 要指 的是在 高炉工 作过程 当 中产生 的废 渣。 对高炉 渣实施热 回收 ,可 以将其 中存在的热 量能量进 行回收 ,
提高 生 产效率 ,降低 对环境 的污 染 。具 体的 回收技 术指 的是
T RT发 电系统在 全寿命期 间的运行 时间 。在 对高炉 等设备 进 行检 修时 ,也要 对其 各个细 节部 分进 行保养 ,及 时对高 炉 及 TR T机组设 备进行维护 和维修 。 以河 钢 集 团邯钢 公 司 六座 高炉 T RT发 电机 组为 例 ,通 过实 行设备运行 作业标准 化 ,规范操作 规程 ,加强 设备 点检 ,
中图 分类 号 : X7 5 7 文献 标 识码 : A 文章编号 : 1 1 — 5 0 0 4 ( 2 0 1 7) 1 0 - 0 0 7 2 — 2
钢铁 企业在 生产 过程 中会消耗 大量 的能源 ,尤其 对 国家 目前越 来越 紧缺 的一次能 源的 消耗十 分的 巨大 。而在对能 源
境污染 问题 。高炉煤 气余 热余 压再利 用技 术 ,首先 一定 要保
证生产 过程中高炉 生产时煤 气压力的控 制。 要 想对煤气 压力进行 有效地控 制 ,一定 要给高炉 及 TR T 发 电机组 建立相 应 的控制标 准 ,提 高高 炉设备 的利 用效率 。 当高炉生 产时 ,煤气 压力稳 定 ,不 仅可 以大大 降低高 炉 的磨 损 ,延长 高炉 的使用 寿命 ,还可 以缩短 检修 时间 ,增 加高 炉
来稿 日期 : 2 0 1 7 年9 月 作者 简 介 : 周志远, 男,生于 1 9 8 5 年, 河 北邯 郸人 , 工 程师 , 研 究方 向 热能 与动 力工程 。
钢铁企业利用余热余压发电的效益分析

ISSN1672-9064CN35-1272/TK能源与环境1概述钢铁行业是耗能大户,其能源的利用率仅为30% ̄50%。
生产过程中不仅有大量的余能被白白浪费,同时造成环境污染。
随着钢铁节能技术的发展,各种高效率的余能利用的技术越来越成熟。
其中利用钢铁生产过程中的余热、余压发电是许多钢铁企业技术改造的重要内容。
目前钢铁企业利用余能发电主要有3种形式:一是利用高温介质的显热,生产蒸汽进行热力发电。
如焦炭生产采取干熄焦工艺时,通过氮气熄焦降温时所产生的高温氮气,加热锅炉转换成蒸汽进行发电;二是利用富余的高炉煤气、焦炉煤气和转炉煤气,以燃料能的形式进行热力发电。
如钢铁企业建设自备电厂,实行热电联产发电;三是利用生产过程中各种压差,转换成电能的形式发电。
如利用高炉生产过程中的炉顶压力,采用TRT技术进行发电。
所有这些技术,都在钢铁企业的生产过程中被成熟地应用,并取得了显著的经济效益和社会效益。
目前有少数钢铁联合企业,充分利用余热、余压发电,基本做到了电力自给。
三钢集团公司近年来把利用余热、余压发电作为企业综合利用的重点工程来抓。
除了利用干熄焦工艺发电,对于中小型焦炉因投资较大,回收期较长,目前尚未实施外,其它两种形式的发电,都已建成投产,并取得了预期的效益和效果。
(1)兴建一座自备电站。
电站2004年底开工建设,2005年3月底投产,项目投资5769万元。
利用富余的煤气为燃料,年发电能力为2.7×10kWh/a。
主要装备是一台75t/h高炉煤气和焦炉煤气混烧锅炉、二台15MW和一台6MW纯冷凝汽轮发电机组及相应配套设施。
(2)安装一套干式炉顶余压透平发电装置(简称TRT)。
项目于2005年1月开工,8月投入生产,投资2540万元。
利用4#高炉炉顶煤气的压力进行差压发电,年设计发电能力为3.0515×107kW·h。
技术改造主要项目有TRT透平主机系统、高低压发配电系统、大型阀门系统、液压伺服控制系统、润滑油系统、氮气密封系统、冷却水系统、自动化控制系统,以及主控楼,厂房等配套设施。
随着国内余热发电行业的发展,我国钢铁余热发电前景向好

随着国内余热发电行业的发展,我国钢铁余热发电前景向好余热发电是指利用生产过程中多余的热能转换为电能的技术。
余热发电不仅节能,还有利于环境保护。
余热发电的重要设备是余热锅炉。
它利用废气、废液等工质中的热或可燃质作热源,生产蒸汽用于发电。
由于工质温度不高,故锅炉体积大,耗用金属多。
用于发电的余热主要有高温烟气余热,化学反应余热、废气、废液余热、低温余热,低于200℃等。
鉴于此,在工业上,余热一般优先供生产自用,当有剩余时,虽然直接利用(如暖通空调用或动力用)对能源的利用率要更高一些,但限于暖通空调用量较小且季节变化较大的特点,以及作为动力用要求负荷相对稳定的特点,该种利用方式具有一定的局限性。
更多地,则是选择采用余热发电的技术对能源进行回收利用。
余热的回收利用途径很多。
一般说来,综合利用余热最好;其次是直接利用;第三是间接利用(产生蒸汽用来发电)。
如钢铁工业:钢铁厂中的焦炉。
目前我国大中型钢铁企业具有各种不同规格的大小焦炉50多座,除了上海宝钢的工业化水平达到了国际水平,其余厂家能耗水平都很高,大有潜力可挖。
炼钢厂中的转炉烟气发电,发电系统,可配置发电量为3000Kw的电站80座。
炼钢厂中的电熔炉,现如今全国有20多座,其中65吨级可发电量在5000Kw/座以上。
余热发电行业主要有三种模式,分别为传统设计模式、工程总承包模式和合同能源管理模式。
目前各个模式都有运用,但从发展历程来看,传统设计模式最早出现,随后工程总承包模式随着余热发电行业的发展出现,而合同能源管理模式在2007年前后快速崛起,因其具有合作方风险低、节能效率高等特点,更能适应市场需求,从而得到快速发展。
我国工业部门可回收的余热资源中,钢铁、有色、建材、化工、石化、轻纺等六行业占总数的90%左右。
目前我国投入运营或立项研究的余热发电技术主要分布在水泥行业、钢铁行业、石化行业等,其中水泥行业余热发电经过十多年的发展已接近国际先进水平,而其他行业的余热发电还基本处于起步阶段。
钢铁冶金行业余热发电技术
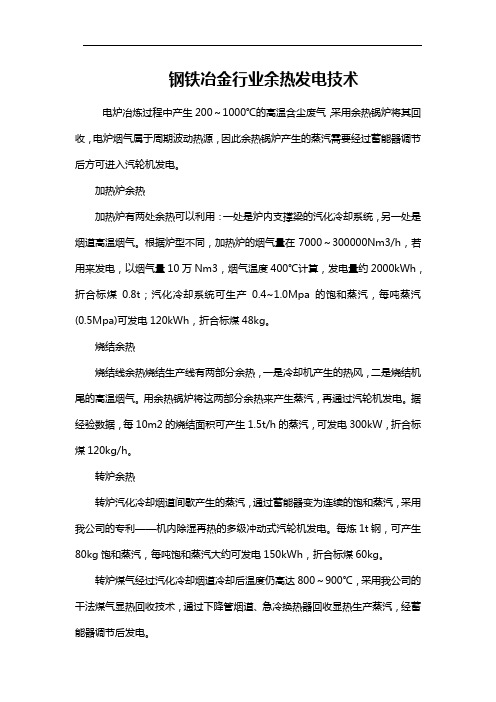
钢铁冶金行业余热发电技术电炉冶炼过程中产生200~1000℃的高温含尘废气,采用余热锅炉将其回收,电炉烟气属于周期波动热源,因此余热锅炉产生的蒸汽需要经过蓄能器调节后方可进入汽轮机发电。
加热炉余热加热炉有两处余热可以利用:一处是炉内支撑梁的汽化冷却系统,另一处是烟道高温烟气。
根据炉型不同,加热炉的烟气量在7000~300000Nm3/h,若用来发电,以烟气量10万Nm3,烟气温度400℃计算,发电量约2000kWh,折合标煤0.8t;汽化冷却系统可生产0.4~1.0Mpa的饱和蒸汽,每吨蒸汽(0.5Mpa)可发电120kWh,折合标煤48kg。
烧结余热烧结线余热烧结生产线有两部分余热,一是冷却机产生的热风,二是烧结机尾的高温烟气。
用余热锅炉将这两部分余热来产生蒸汽,再通过汽轮机发电。
据经验数据,每10m2的烧结面积可产生1.5t/h的蒸汽,可发电300kW,折合标煤120kg/h。
转炉余热转炉汽化冷却烟道间歇产生的蒸汽,通过蓄能器变为连续的饱和蒸汽,采用我公司的专利——机内除湿再热的多级冲动式汽轮机发电。
每炼1t钢,可产生80kg饱和蒸汽,每吨饱和蒸汽大约可发电150kWh,折合标煤60kg。
转炉煤气经过汽化冷却烟道冷却后温度仍高达800~900℃,采用我公司的干法煤气显热回收技术,通过下降管烟道、急冷换热器回收显热生产蒸汽,经蓄能器调节后发电。
电炉余热冲渣热水。
每吨铁排出约0.3t渣,每吨渣可产生80~95℃,5~10t的冲渣水,将这部分热水减压产生低压蒸汽,再进入饱和蒸汽凝汽式汽轮机发电。
每吨90℃热水可发电1.5kWh,折标煤0.6kg,80℃热水可发电1kWh,折标煤0.4kg。
干法熄焦采用惰性气体来冷却红焦,加热后的气体在余热锅炉中产生蒸汽,蒸汽可发电或并入蒸汽管网。
吨焦可生产3.9Mpa、300℃的蒸汽0.45t~0.6t,可发电85~115kWh,折合标煤35~46kg。
高炉煤气余压利用高炉炉顶煤气的压力能和热能,通过透平膨胀机做功发电,但不影响煤气后续利用。
钢铁、冶金企业余能利用PPT
钢铁、冶金企业节能之余热余压利用钢铁生产过程消耗大量的电能和煤炭,产生大量的煤气和余热。
钢铁企业应当优化能源结构和能源利用,在能源效率最大化的前提下,利用钢铁生产流程中的余热余能和副产煤气发电,与电力行业构成钢铁—电力循环经济产业链。
在钢铁企业,可以发电的余热余能形式和过程有高炉炉顶余压发电(TRT)、余热锅炉蒸汽发电、煤气—蒸汽联合循环发电(CCPP)、全烧高炉煤气或气煤混烧锅炉余热发电。
如莱钢推广应用高炉、转炉煤气回收利用技术,TRT、CCPP和干熄焦(CDQ)发电技术、低温余热发电技术;研究高炉冲渣水低温余热利用技术、转炉余热锅炉蒸汽发电技术、烧结机余热蒸汽发电技术等,形成二次能源循环链,不断提高余热余能回收利用水平。
炼铁工序高炉煤气余压利用高炉炉顶煤气的压力能和热能,通过透平膨胀机做功发电,但不影响煤气后续利用。
高炉炉顶压力达0.15~0.25Mpa,平均每吨铁可发电20~50kWh,折标煤8~20kg,单位投资费用约4500元/kW,根据压力及除尘方式不同(湿法除尘、干法除尘),投资回收期在2—6年。
1956年苏联开始研制TRT。
1962年第一套装置(6MW)在马格尼托哥尔斯克钢铁公司8号高炉(1370m3 )投产。
改进后的第二套装置是带煤气预热器的二级轴流冲动式透平机。
1974年日本川崎钢铁公司水岛钢铁厂2号高炉(2857m3 )建成首套二级径流向心式透平机(8MW),采用喷水措施防止透平机积灰堵塞。
1982年第一套采用袋式干式除尘装置的TRT在住友金属工业公司小仓钢铁厂2号高炉投产6.6MW。
1985年采用干式电除尘装置的TRT在日本钢管公司福山钢铁厂2号高炉投产8.2MW。
20世纪80年代,中国在几座1000m3 以上高炉上装备了TRT,1991年开始在3200m。
高炉上应用干式电除尘器和干式TRT。
随着技术发展,新的大型余压发电透平机常制成干式高效轴流式结构,进口静叶片可随煤气量和压力变化调整,并有防积灰、防腐蚀等多种改进措施。
余热余压发电技术(钢铁)
优点:节能环保,减少能源消耗,降低生产成本
应用领域:钢铁、化工、水泥等高能耗行业Βιβλιοθήκη 钢铁行业中的重要性添加标题
添加标题
添加标题
添加标题
提高能源利用率:余热余压发电技术可以将钢铁生产过程中的余热余压转化为电能,提高能源利用率。
节能减排:余热余压发电技术可以有效降低钢铁行业的能源消耗和碳排放。
降低生产成本:余热余压发电技术可以降低钢铁行业的生产成本,提高企业的经济效益。
余热余压发电技术案例
04
国内外典型案例介绍
添加标题
添加标题
添加标题
添加标题
首钢集团:采用余热锅炉发电,年发电量达到6亿千瓦时
宝钢集团:利用高炉余热发电,年发电量超过10亿千瓦时
德国蒂森克虏伯:利用高炉余热发电,年发电量超过7亿千瓦时
美国通用汽车:利用汽车制造过程中的余热发电,年发电量达到3亿千瓦时
技术创新和研究方向
提高余热余压发电效率
降低发电成本
提高发电稳定性和可靠性
研究新型发电技术和设备
探索余热余压综合利用途径
加强与其他领域的交叉学科研究
感谢观看
汇报人:XX
促进可持续发展:余热余压发电技术符合国家节能减排政策,有利于钢铁行业的可持续发展。
技术发展历程
19世纪末,首次提出余热余压发电的概念
20世纪初,开始研究余热余压发电技术
20世纪50年代,开始商业化应用
20世纪80年代,技术逐渐成熟,广泛应用于钢铁、化工等行业
21世纪初,技术不断创新,效率不断提高,成为节能减排的重要手段
技术应用效果分析
环保效果:余热余压发电技术可以减少废气、废水、废渣等污染物的排放,降低环境污染
余热余压发电技术(钢铁)课件
振动筛
炼铁高炉
ppt课件
13
烧结生产工艺简介
机
防常机
和皮 电除生费 坚 抽 区
混
1、烧结原、燃料及烧结矿 3、烧结 5、烧结矿冷却
2、配料 4、烧结饼破碎和筛分 6、烧结矿整粒和成品矿贮存
ppt课件
14
烧结生产工艺简介
ppt课件
15
ppt课件16ຫໍສະໝຸດ 按冷却风流的通过方式,可分为抽风和鼓风两种形式。 按冷却机的结构形式,又可分为带式、环式、格式、塔 式和盘式。鼓风环冷是目前应用较普遍的一种方式。
连铸、轧钢、板材
ppt课件
4
钢铁基本工艺流程简介
高炉炼铁
钢
锭 废
钢
氧气顶吹转
炉炼钢
钢 液
a)上注
b)下注 铸锭
生
铁
钢
坯
炼铁
电弧炉炼钢
炼钢
连续铸锭
浇注
钢 板 钢板轧机
型 钢
型钢轧机
钢 管
钢管轧机
钢 丝 拉丝机
钢材生产
ppt课件
5
目前钢铁余热回收利用
原料 煤 石灰石 铁矿石
焦化
焦炉煤气 红焦显热回收 焦炉烟气余热
20
烧结生产中烟气余热的特点
烧结生产能耗一般占吨钢能耗的10~20%,冷却机废气显热和 烧结烟气显热占烧结过程热耗的30~50%,具有很高的回收价值。
煤气燃烧热
5.4%
CO 损失 7.1%
烟气显热
23.6%
空气显热 3.7%
烧结矿显热 6.5%
焦粉燃烧热 88.2%
冷
烧结饼显热 44.5%
却 机
废气显热29.3%
余热余压发电原理
余热余压发电原理说起余热余压发电的原理,我有一些心得想分享。
大家都知道,在咱们日常生活中,有很多能量其实是被浪费掉的。
就像我们家里烧水,水烧开了之后,水壶还很烫,这个热量其实就类似余热。
而余压呢,您可以想象成一个气球,您吹好气之后把口扎紧,气球里面的压力就是余压。
那在工业上怎么利用这些看似被浪费的余热余压来发电呢?先来说余热。
比如说钢铁厂的高炉,铁矿石在炉子里被冶炼的时候,会产生大量的热。
这时候有很多热量是随着废气之类的跑掉了。
但是我们可以通过一种设备,就像一个特殊的大容器,它能够把这些带着热量的废气收集起来。
这个设备内部呢有一种介质,耐高温的那种,比如说某种特殊的油或者气体。
废气把热量传递给这个介质,这个介质温度就升高了,体积就膨胀了,然后带动涡轮机转动,涡轮机一转,就像咱们看到的风车被风吹转动一样,这样就可以带动发电机发电了。
这里面还有一点我一开始不是很理解,就是这个热量传递的效率问题。
老实说,我一开始以为只要有热气就能轻松地把能量全都传过去了,后来学习才知道中间也会有各种损耗。
打个比方吧,这就像咱们拿着一个暖手宝给另一个东西加热,暖手宝很热,但是中间如果隔了很厚的一层布,热量就不能很好地传递过去。
工业上要想提高这种热量传递的效率,就得不断完善设备和介质之类的。
余压发电的原理更像是家里的水压发电小玩具。
工厂里有些地方像是高压容器或者管道里面,存在高压气体或者液体。
当这些高压的东西被释放到压力低的地方,就像从一个高地势到低地势的水一样,这种压力的释放会产生冲击力。
我们用特殊的装置,比如压力转换装置,把这种冲击力收集起来,转化成涡轮机的转动,接着带动发电机发电。
说到这里,你可能会问,这余热余压发电有什么特别的注意事项呢?首先就是设备的维护。
因为这些设备在高温高压的环境下工作,就像一个人一直在很艰苦的环境下工作容易生病一样,设备也容易出故障。
所以要按时检查设备,看看有没有泄漏,有没有部件磨损之类的。
- 1、下载文档前请自行甄别文档内容的完整性,平台不提供额外的编辑、内容补充、找答案等附加服务。
- 2、"仅部分预览"的文档,不可在线预览部分如存在完整性等问题,可反馈申请退款(可完整预览的文档不适用该条件!)。
- 3、如文档侵犯您的权益,请联系客服反馈,我们会尽快为您处理(人工客服工作时间:9:00-18:30)。
烧结余热发电系统简介
烧结机烟气余热利用
烧结过程是个热加工过程,烧结料层中温度变化随主排风机 自上而下抽入空气、烧结台车不断前移而变化。其中温度最高烧 结过程结束一般控制在接近烧结机尾的风箱位置。一般烧结机尾 部倒数第二个风箱温度最高。 一般烧结烟气焓硫较高,为了确保非回收区的烟气流经机头 电除尘器至烧结机主抽风机时,不至于结露,对回收的烟气和非 回收的烟气都要严格测算,才能确保烧结机烟气余热回收利用合 理。
什么是转炉炼钢?
转炉炼钢 converter steelmaking这种炼钢法使用的氧化剂是氧气。把氧气鼓 入熔融的生铁里,使杂质硅、锰等氧化。在氧化的过程中放出大量的热量 (含1%的硅可使生铁的温度升高200摄氏度),可使炉内达到足够高的温度。 因此转炉炼钢不需要另外使用燃料。炉料主要为铁水和造渣料(如石灰、石 英、萤石等),为调整温度,可加入废钢以及少量的冷生铁块和矿石等。
氧气顶吹转炉总图
转炉生产工艺概况
煤气净化回收与利用技术按净化方式分为湿法和干法2大类 干法系统包括烟气冷却净化系统与煤气回收系统。由活动烟罩捕集并经汽化冷 却烟道冷却至1600℃左右的转炉烟气,首先进入蒸发冷却器降温和初除尘,温 度降至180℃~200℃左右,进入静电除尘器进行精除尘。然后根据CO含量、 O2含量由阀门切换站进行煤气回收或放散操作。回收期煤气需经冷却器二次冷 却,温度降至70℃后进入煤气柜回收;放散期煤气需点火燃烧,排放气体的含
烧结余热发电技术发展
从利用目的上分,烧结余热的回收利用方式,可分为热风点火、 预热、保温等直接利用方式,和生产蒸汽、发电、制冷等间接利用方 式。其中,以发电和生产蒸汽最为普遍,两者的利用原理和技术路线 相通。 烧结余热发电技术的发展,大体上可划分为三个阶段。
第一阶段,上世纪70年代末及80年代,为烧结余热发电技术 在日本的诞生及发展期,各种系统相继出现,烧结余热利用技术 在日本得到迅速推广。 日本钢管扇岛厂(1978年12月) 和歌山4#(1979年3月) 和歌山5#(1981年9月) 小仓3#(1981年10月) 鹿岛2#(1981年12月) 新日铁大分2#(1982年12月)
余热余压发电技术
(钢铁)
二o一一年三月—北京
钢铁工艺流程简介 烧结生产工艺及余热发电技术
转炉生产工艺及余热发电技术
高炉生产工艺及高炉煤气发电技术
高炉煤气压差发电技术
第一部分
钢铁工艺流程简介
钢铁基本工艺流程简介 钢铁行业是一个高耗能、高污染的产业,也是节能减排潜力最大的 行业之一。中国钢铁产能分散,企业处于多层次、不同结构、不同技 术装备水平共同发展阶段,因此,节能减排任务艰巨。 随着我国钢铁工业持续快速发展,能否进一步节能降耗、保护环 境、实现清洁生产,不仅关系到企业的经济效益,而且直接关系到企 业的形象和生存,影响到企业可持续发展,因此,节能和环保已成为 钢铁企业降低成本、提高企业竞争力、走可持续发展的必由之路。
烧结余热发电系统简介
主烟道
余热锅炉
余热
余热锅炉
汽轮机
发电机
~
热力系统
循环冷却水系统
凝汽器 冷却塔
烧结机烟风系统
环冷机烟风系统
电气系统 热工控制系统 化学水处理系统
烧结余热发电技术
1)锅炉蒸汽系统:强制循环和自然循环 2)取风方式:单段取风和多段取风
3)热力系统:单压系统和双压系统
4)冷却机取热方式:开路系统、半循环和闭路循环
尘浓度≤15mg/Nm3。
转炉煤气干法回收工艺[LT法(Lurgi-Thyssen)]
转炉煤气湿法回收工艺[OG法(Oxygen Converter Gas Recovery System)]
OG(湿法)工艺:冶炼中产生的近1450℃煤气,通过冷却烟道冷却到约900℃后进入溢流文 氏管,使煤气中80%左右的固体颗粒脱离后进人重力脱水器脱水,煤气温度降至约70℃。在风 机的抽引下煤气流速突增并继续进入R—D文氏管,经水雾处理去除8μm以上的固体颗粒后再 水雾分离得到纯净的煤气。系统设置有气体分析仪,当煤气合格(CO > 35%、O2<2%)时三 通阀切换至回收状态,煤气借助风机后的正压,经水封逆止阀、V型水封送入气柜。如煤气不 合格则三通阀切换至放散状态,经放散塔点火燃烧后排放到大气中。
烧结生产中烟气余热的特点
烧结生产能耗一般占吨钢能耗的10~20%,冷却机废气显热和 烧结烟气显热占烧结过程热耗的30 ~ 50%,具有很高的回收价值。
烧结机尾部余热利用部分
环冷机余热发电利用部分
烧结矿产量及温度 余热利用的影响因素 冷却介质流量 烧结机及冷却机机速 有无热筛
冷却介质初温 料层厚度 环冷机漏风 烟温限制
具有间歇性、波动性和周期性的特点。
转炉余热发电技术
转炉烟气流量及温度变化曲线图
转炉余热发电技术
关键技术:蒸汽参数选择、蒸汽蓄热器选型、蓄热器控制
转炉余热发电技术
• 4×45t转炉
序号 1 转炉 项目 生产能力 冶炼周期 汽化冷却烟道运行压力 数量 总蒸汽流量 容积 数量 出口压力范围 装机容量 平均发电量 单位 t/炉 min/炉 MPa 座 t/h m3 台 MPa MW MW 数据 45 25 1.5 4 28~32 60 4 1.0~1.1 5 4.2
强度高,还原性好,含有一定的CaO、MgO,具有足够的碱度,而且已事
先造渣,高炉可不加或少加石灰石。 通过烧结可除去矿石中的S、Zn、Pb、As、K、Na等有害杂质,减少
其对高炉的危害。高炉使用冶炼性能优越的烧结矿后,基本上解除了天
然矿冶炼中常出现的结瘤故障;同时极大地改善了高炉冶炼效果。 烧结中可广泛利用各种含铁粉尘和废料,扩大了矿石资源,又改善
序号 1 2 余热回收流程 开路回收利用流程 闭路循环回收利用流程
烧结机烟气余热利用
主烟道
M
300 ~400 ℃
过热蒸汽
M
M
M
旁 路 烟 囱
≈ 200℃
水泵来水
引风机
冷却机废气余热利用
烧结矿从烧结机尾经过热破碎后卸到 冷却机上,卸出的烧结饼温度平均在 500∽800℃之间。热烧结矿经过冷却机冷 却,使得从冷却机排出的烧结矿温度在 150 ℃以下。热烧结矿在冷却过程中其热 能变为废气显热,废气温度随冷却机部位 的不同而不同,给矿部温度最高,在450 ℃以上,排矿部温度最低。
转炉的分类
耐火材料性质:分为碱性(用镁砂或白云石为内衬)和酸性(用硅质材料为内
衬);酸性转炉不能去除生铁中的硫和磷,须用优质生铁,因而应用范围受到限制。 碱性转炉适于用高磷生铁炼钢,曾在西欧得到较大发展。 气体吹入炉内的部位:分为底吹、顶吹和侧吹; 按吹炼采用的气体,分为空气转炉和氧气转炉。空气吹炼的转炉钢,因含氮量高, 质量不如平炉钢,且原料有局限性,又不能多配废钢,未能像平炉那样在世界范围 内广泛采用。1952年氧气顶吹转炉问世,逐渐取代空气吹炼的转炉和平炉,现在 已经成为世界上主要炼钢方法。
主要基本工艺: 炼铁 炼钢 浇注 钢材成型
钢铁基本工艺流程简介
目前钢铁余热回收利用
第二部分 烧结生产工艺及余热发电技术
烧结生产工艺简介
钢铁工业是能源消耗最大的产业部门之一,烧结生产一般占吨钢能耗的
10∽20%,仅次于炼铁。烧结节能在钢铁企业节能中占有十分重要的地位。 高炉炼铁生产前,将各种粉状含铁原料,配入适量的燃料和熔剂,加入适
烧结机工艺流程
烧结机工艺流程
烧结生产工艺简介
1、烧结原、燃料及烧结矿 3、烧结 5、烧结矿冷却
2、配料 4、烧结饼破碎和筛分 6、烧结矿整粒和成品矿贮存
烧结生产工艺简介
按冷却风流的通过方式,可分为抽风和鼓风两种形式。 按冷却机的结构形式,又可分为带式、环式、格式、塔 式和盘式。鼓风环冷是目前应用较普遍的一种方式。
量的水,经混合和造球后在烧结设备上使物料发生一系列物理化学变化,烧结
成块的过程。主要包括烧结料的准备,配料与混合,烧结和产品处理等工序。 富矿粉和贫矿富选后得到的精矿粉都不能直接入炉冶炼,必须将其重新造 块,烧结是最重要最基本的造块方法之一。
烧结生产工艺简介 通过烧结得到的烧结矿具有许多优于天然富矿的冶炼性能,如高温
冷却机废气余热利用方案
序号 废气余热利用
高温段 用于余热锅炉产蒸汽 中温段 用作点火保温炉的助燃 风 低温段 用作混合料预热
余热可以分为高、中、低三个温区分
别利用。
400℃ 1#
M M M
2#
M
300℃
烟风系统
主蒸汽Leabharlann 环冷机1段环冷机2段
余 热 锅 炉
M
M
旁 路 烟 囱
M
M
M
新风 循环 风机
烧结机烟气和冷却机废气余热回收利用技术
烧结机烟气和冷却机废气余热利用系统图
2×360m2环冷机余热发电,装机30MW,年发电量可达2.08亿kWh,年 节约标媒4.4万吨,年减排CO2约8万吨,同时减少粉尘排放10万吨/年。 单位投资费用6000--8000元/kw左右,投资回收期为3~4年。
第三部分
转炉生产工艺及余热发电技术
钢与铁的区别
转炉余热发电技术
• 冶金企业在生产过程中产生大量低参数饱和蒸汽,由于工艺过程及生产技 术等因素,这部分中低温饱和蒸汽没有得到有效利用,被白白地排放到了 环境中。 • 随着低参数饱和蒸汽汽轮机技术的进步,给这些余热资源的利用提供了一 个很好的途径。 转炉蒸汽特性: 转炉炼钢的工艺决定了转炉高温烟气具有间歇性、波动性和周期性。 受转炉烟气的影响,转炉汽化冷却烟道产生的低参数饱和蒸汽同样也