中国造船管理与日韩差距深度分析
中韩造船的差距
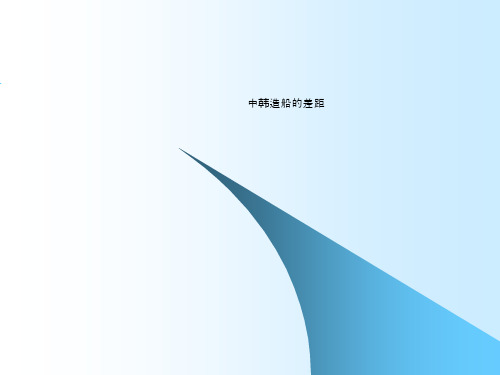
依赖于供应商 •卖方的市场 (钢板、主机,等) •选择面窄
(小的/特殊的项目) •对交货控制较差 •缺乏信息
管理: •没有体系
2
Comparison between Chinese & Korean Shipyard 中国船厂与韩国船厂之间的比较
Need information / data 需要数据和资料
7
Chinese Shipyard 中国船厂
Korean Shipyard 韩国船厂
5. N/C Machine : Cutting Condition 数控切割机:切割的状况
1. Cutting Notch must be grinded 切割口必须打磨 2. Waste Time, $$$, Material 浪费时间、金钱、材料 3. Quality problem (Welding) 质量问题(焊接) 4. Defects on painting 造成涂装的缺陷 5. Low accuracy 准确度低 6. Etc…等
很长的时间来找到正确的零件(对应于每个分 段)
All related with $$$ 所有都与金钱有关
Solution 解决措施 Steel store by Block 按分段存放钢材 Use Rack / Pallet 使用架子/托盘
•Save $, Improve quality & Productivity 节省金钱、 改善质量和生产效率 But Need information / data 但是,需要信息和数据 资料
11
Chinese Shipyard 中国船厂
各国造船技术比较
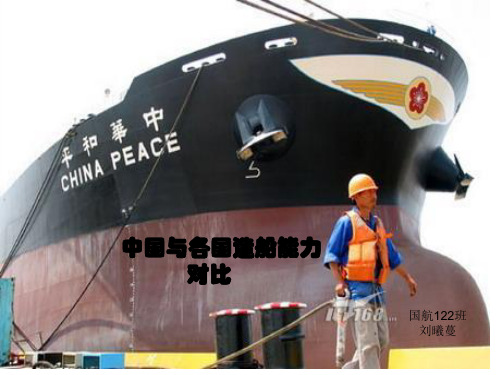
国本土化设备装船率超过80
%,而我国船用中低速柴油机、
辅机、发电设备、曲轴等配套
•
二是自主创新能力不强,
国 主要船舶配套设备专利还需要
差 从国外引进,海洋工程装备设
设备虽然实现了本土化生产, 但能力缺口在不断拉大,民船 配套自动化导航、仪器仪表等
计和总承包基本为空白,部分
距 很 高技术船舶仍然需要国外设计。
000万吨,而2003年仅有8
00余万吨,手持订单中散货船超
过60%,技术含量低、能力严重
过剩。目前过剩的主要是低水平造
船基础设施,即使世界航运和造船
市场回归正常水平,也有三分之一
左右的产能过剩。
外媒:亚洲没有哪个国家造船能力能媲美中国
日本《外交学者》网站文章称,“目前,中国军事造船厂在造船类型和数量方面超过了西 欧、日本和韩国。如果北京优先发展造船业,那么到2020年时,中国军用造船技术能力将 能赶上俄罗斯;到2030年,将接近美国现有造船技术。中国目前正在规模化生产至少6个 级别的现代柴电潜艇和水面战舰。”不仅如此,有预测称,在未来五年左右,与韩国、日
LNG船,需向法国GTT公司支付1000多万美元的
专利费。排名如下:
1、法国(虽然没有什么产量,但掌握核心技术)
2、韩国
3、日本
LNG基本介绍
• LNG Liquefied Natural Gas
CO2
-162℃
•
•
•
•
•
1/625 45%
站
成分天 的 量液成深水(缩
为四然ห้องสมุดไป่ตู้
气化液冷等脱写
LNG
1
2
•
中国已经成为世界第二造船大国许多年,近年来与
韩国和日本造船企业在中国投资的比较研究

韩国和日本造船企业在中国投资的比较研究上世纪90年代以来,韩、日造船企业纷纷在中国投资建厂,掀起国际造船业新一轮产业转移的高潮,由此引发的一系列中日韩造船业竞争与发展的问题,备受业界人士和专家学者的关注。
可以通过详细梳理韩、日造船企业在中国投资的整体情况,并在此基础上,采用比较研究和案例分析的方法,对韩日造船企业在中国投资的原因、目的进行深入的分析,对韩日造船企业在中国投资的成效进行客观的评估,对韩日造船企业在中国投资的发展前景进行一定程度的展望。
一、具体可以通过三个视角来研究1.是以韩日在中国投资为视角,观察韩日造船业的整体发展状况;2.是以案例分析的方法,以小见大,评估韩日造船产业在中国投资的成效;3.是在论述的过程中结合了国际产业转移的相关理论,使理论更具研究价值和说服力。
通过这种研究方法不仅可以更好地了解韩日本造船产业的发展现状,还可以看到韩、中、日三国造船业的优势与不足,并从中得出一些对造船产业发展有益的启示。
二、韩日造船企业在中国投资的原因及目的1.从国际产业转移的视角分析韩日造船企业在中国投资的原因国际产业转移(international industrial transfer),是指某些产业从一个国家和地区通过国际贸易和国际投资等多种方式转移到另一个国家和地区的过程。
半个多世纪以来,国际造船业主要经历了两次产业转移。
第一次是从西欧向东亚的转移,发生在上世纪50年代。
50年代日本造船业的崛起,打破了西欧造船国一统天下的局面。
第二次是从日本向韩国的转移。
韩国造船业从上世纪70年代开始逐步发展壮大,并赶超日本。
2000年,韩国造船产量首次超过日本,成为新的世界造船霸主。
当前,国际造船业正在经历第三次产业转移,即从日、韩向中国的转移。
2010年,中国造船完工量、新承接船舶订单量、手持船舶订单量三大指标均超越韩国,打破了韩国造船业7年来三大指标位居世界第一的格局,成为新的世界造船第一大国。
中国造船整体与世界先进水平有较大差距
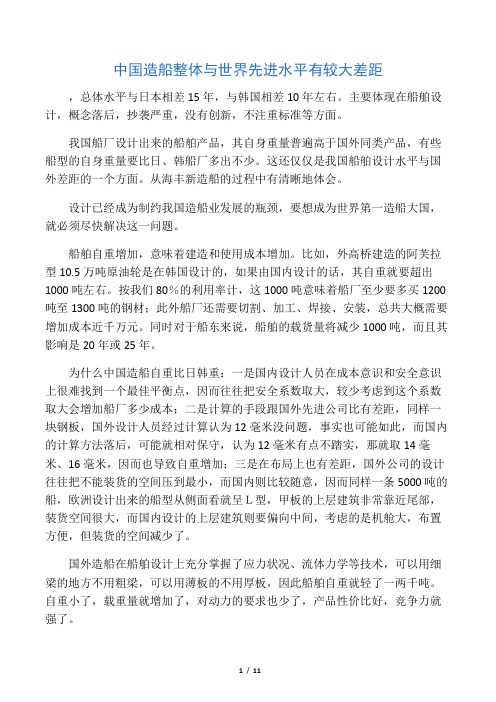
中国造船整体与世界先进水平有较大差距,总体水平与日本相差15年,与韩国相差10年左右。
主要体现在船舶设计,概念落后,抄袭严重,没有创新,不注重标准等方面。
我国船厂设计出来的船舶产品,其自身重量普遍高于国外同类产品,有些船型的自身重量要比日、韩船厂多出不少。
这还仅仅是我国船舶设计水平与国外差距的一个方面。
从海丰新造船的过程中有清晰地体会。
设计已经成为制约我国造船业发展的瓶颈,要想成为世界第一造船大国,就必须尽快解决这一问题。
船舶自重增加,意味着建造和使用成本增加。
比如,外高桥建造的阿芙拉型10.5万吨原油轮是在韩国设计的,如果由国内设计的话,其自重就要超出1000吨左右。
按我们80%的利用率计,这1000吨意味着船厂至少要多买1200吨至1300吨的钢材;此外船厂还需要切割、加工、焊接、安装,总共大概需要增加成本近千万元。
同时对于船东来说,船舶的载货量将减少1000吨,而且其影响是20年或25年。
为什么中国造船自重比日韩重:一是国内设计人员在成本意识和安全意识上很难找到一个最佳平衡点,因而往往把安全系数取大,较少考虑到这个系数取大会增加船厂多少成本;二是计算的手段跟国外先进公司比有差距,同样一块钢板,国外设计人员经过计算认为12毫米没问题,事实也可能如此,而国内的计算方法落后,可能就相对保守,认为12毫米有点不踏实,那就取14毫米、16毫米,因而也导致自重增加;三是在布局上也有差距,国外公司的设计往往把不能装货的空间压到最小,而国内则比较随意,因而同样一条5000吨的船,欧洲设计出来的船型从侧面看就呈L型,甲板的上层建筑非常靠近尾部,装货空间很大,而国内设计的上层建筑则要偏向中间,考虑的是机舱大,布置方便,但装货的空间减少了。
国外造船在船舶设计上充分掌握了应力状况、流体力学等技术,可以用细梁的地方不用粗梁,可以用薄板的不用厚板,因此船舶自重就轻了一两千吨。
自重小了,载重量就增加了,对动力的要求也少了,产品性价比好,竞争力就强了。
中国造船技术主要差距与应对措施
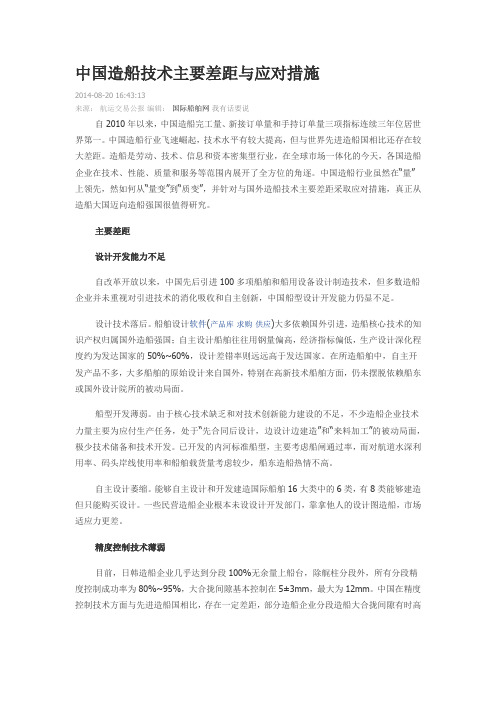
中国造船技术主要差距与应对措施2014-08-20 16:43:13来源:航运交易公报编辑:国际船舶网我有话要说自2010年以来,中国造船完工量、新接订单量和手持订单量三项指标连续三年位居世界第一。
中国造船行业飞速崛起,技术水平有较大提高,但与世界先进造船国相比还存在较大差距。
造船是劳动、技术、信息和资本密集型行业,在全球市场一体化的今天,各国造船企业在技术、性能、质量和服务等范围内展开了全方位的角逐。
中国造船行业虽然在“量”上领先,然如何从“量变”到“质变”,并针对与国外造船技术主要差距采取应对措施,真正从造船大国迈向造船强国很值得研究。
主要差距设计开发能力不足自改革开放以来,中国先后引进100多项船舶和船用设备设计制造技术,但多数造船企业并未重视对引进技术的消化吸收和自主创新,中国船型设计开发能力仍显不足。
设计技术落后。
船舶设计软件(产品库求购供应)大多依赖国外引进,造船核心技术的知识产权归属国外造船强国;自主设计船舶往往用钢量偏高,经济指标偏低,生产设计深化程度约为发达国家的50%~60%,设计差错率则远远高于发达国家。
在所造船舶中,自主开发产品不多,大多船舶的原始设计来自国外,特别在高新技术船舶方面,仍未摆脱依赖船东或国外设计院所的被动局面。
船型开发薄弱。
由于核心技术缺乏和对技术创新能力建设的不足,不少造船企业技术力量主要为应付生产任务,处于“先合同后设计,边设计边建造”和“来料加工”的被动局面,极少技术储备和技术开发。
已开发的内河标准船型,主要考虑船闸通过率,而对航道水深利用率、码头岸线使用率和船舶载货量考虑较少,船东造船热情不高。
自主设计萎缩。
能够自主设计和开发建造国际船舶16大类中的6类,有8类能够建造但只能购买设计。
一些民营造船企业根本未设设计开发部门,靠拿他人的设计图造船,市场适应力更差。
精度控制技术薄弱目前,日韩造船企业几乎达到分段100%无余量上船台,除艉柱分段外,所有分段精度控制成功率为80%~95%,大合拢间隙基本控制在5±3mm,最大为12mm。
中日韩三国造船业的新比拼
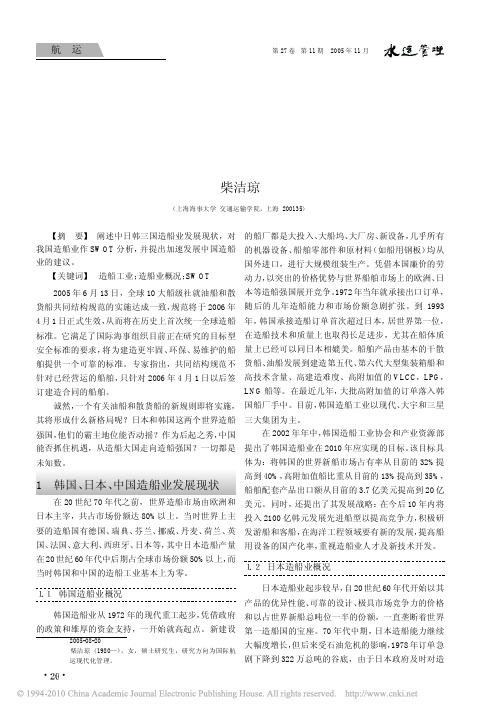
【摘要】阐述中日韩三国造船业发展现状,对我国造船业作SWOT 分析,并提出加速发展中国造船业的建议。
【关键词】造船工业;造船业概况;SWOT 2005年6月13日,全球10大船级社就油船和散货船共同结构规范的实施达成一致,规范将于2006年4月1日正式生效,从而将在历史上首次统一全球造船标准。
它满足了国际海事组织目前正在研究的目标型安全标准的要求,将为建造更牢固、环保、易维护的船舶提供一个可靠的标准。
专家指出,共同结构规范不针对已经营运的船舶,只针对2006年4月1日以后签订建造合同的船舶。
诚然,一个有关油船和散货船的新规则即将实施,其将形成什么新格局呢?日本和韩国这两个世界造船强国,他们的霸主地位能否动摇?作为后起之秀,中国能否抓住机遇,从造船大国走向造船强国?一切都是未知数。
1韩国、日本、中国造船业发展现状在20世纪70年代之前,世界造船市场由欧洲和日本主宰,共占市场份额达80%以上。
当时世界上主要的造船国有德国、瑞典、芬兰、挪威、丹麦、荷兰、英国、法国、意大利、西班牙、日本等,其中日本造船产量在20世纪60年代中后期占全球市场份额50%以上,而当时韩国和中国的造船工业基本上为零。
1.1韩国造船业概况韩国造船业从1972年的现代重工起步,凭借政府的政策和雄厚的资金支持,一开始就高起点。
新建设的船厂都是大投入、大船坞、大厂房、新设备,几乎所有的机器设备、船舶零部件和原材料(如船用钢板)均从国外进口,进行大规模组装生产。
凭借本国廉价的劳动力,以突出的价格优势与世界船舶市场上的欧洲、日本等造船强国展开竞争。
1972年当年就承接出口订单,随后的几年造船能力和市场份额急剧扩张。
到1993年,韩国承接造船订单首次超过日本,居世界第一位,在造船技术和质量上也取得长足进步,尤其在船体质量上已经可以同日本相媲美。
船舶产品由基本的干散货船、油船发展到建造第五代、第六代大型集装箱船和高技术含量、高建造难度、高附加值的VLCC ,LPG ,LNG 船等。
中韩造船业竞争差异
中韩造船业竞争差异作者:赵松秦书明孙宇洪梅来源:《中国科技博览》2013年第24期摘要:中国造船完工量连续12年排名世界第三,造船手持订单量连续两年位居世界第二。
2006年,中国造船完工量1452万载重吨,占世界的比例达到19%;船厂手持新船订单量6872万载重吨,占世界的比例达到24%。
作为目前世界最主要的造船基地,中国与韩国之间的差距正在迅速缩小。
关键词:造船;劳动成本。
中图分类号:F2241. 资料2. 劣势明显上游配套产业发展滞后,但是,长期以来中国在船用设备领域的研发投入严重不足,中国船舶配套业总体技术水平低。
中国远洋船舶的导航、通信、舱室、自动化设备,以及电机、电器等关键部件还大多需要进口。
目前,中国国产设备装船率不足40%,远低于韩国的85%以上。
进口船用低速机、中速机、船用发电机组占中国市场的比例(按马力计)分别为50%,50%和70%。
而中国自行设计制造的部分船用设备产品,主要只能为沿海小型船舶和内河船舶配套。
另外,中国造船企业在技术与设计上与韩国企业差距明显。
韩国造船业非常注重技术的进步,在高技术和高附加值的船舶市场上占有很明显的优势。
中国最大的造船企业只有大约200名船舶设计人员,而三星重工拥有1500多名设计人员。
不仅如此,中国造船企业在生产管理和质量控制上与韩国企业仍有较大的差距。
中国部分造船厂存在造船周期较长、交船拖期等问题,使中国造船企业信誉度受损。
在2000年6月,中机海川国际船舶公司和芜湖造船厂签订建造6艘2.7万吨级散货船,当第4艘船交付时已经拖延近10个月。
此外,中国造船企业存在产品质量把关不严的问题,中国某些造船厂建造的船舶中使用了未经船级社检验的部件导致主机出现问题。
目前,在LNG等高附加值船舶市场上,韩国拥有绝对优势,中国还缺乏相应的设计、技术与生产能力。
近期韩国企业重点加强了对快速、大型、高附加值的船型如LNG、豪华邮船、海洋建筑船等的质量提升和IT技术应用。
我国造船业形势严峻 与国外相比还有很大差距
我国造船业形势严峻与国外相比还有很大差距对于几乎全部的中国船舶企业而言,2012年注定都是艰难的一年。
虽然早在2008、2009年金融危机的“威力”初步显现时,造船行业就已经做好了在3年后迎来最艰难时刻的心理准备,可当2012年真的来临时,这个行业似乎仍然感受到了难以承受之重。
虽然船舶工业的低谷是全球性的,可是中国船舶工业的形势却又似乎格外严峻。
产能过剩、融资不畅,更重要的是中国船舶工业虽贵为世界第一,但在高端船舶研发和制造方面、在利润空间更加客观的海工装备制造方面,与世界造船强国日本和韩国还有较大差距。
逆境中发力,这是中国船舶工业的必须选择,也是唯一可行的道路。
事实上,它们已经在做。
迎来艰难时世“一般来说,造船企业从承接订单到最终交付需要大约2年至3年的时间,目前造船企业手中的订单多为2010年或者2011年交付。
所以,随着前几年承接的订单陆续完工交付以及新船订单需求不足,船舶工业最艰难的日子还在后面。
”三年前,原中国船舶工业经济研究中心高级分析师梁志勇就向《中国产经新闻》记者表明了他的判断。
三年后,中国船舶工业的艰难时世如约而至。
谈及订单,尤其是新承接订单数量,几乎所有的造船厂都讳莫如深。
“现在行业内全国的形势都很惨淡,我们谈起来也很为难,说得太好或者太不好,都不合适。
”一家大型国有造船企业负责人向《中国产经新闻》记者如此表示。
实际上,该企业在行业内已经算情形较好的一类,但企业内部的纠结心态依然非常明显。
而记者从另一知情人士那里获悉,该企业2012年新承接订单数量依然为“0”。
8月10日,扬子江船业公布第二季度业绩,净利润跌8.9%至8.781亿元,低于去年的9.639亿元,营收较去年的35亿元增加13%,至39亿元。
与此同时,撤单情形严重,该公司表示,因客户没有付款,第二财季取消了8份造船合同。
中船重工旗下的船舶制造企业中国重工的业绩同样惨淡。
其一季报与惨淡的2011年年报相比,业绩呈现加速下滑的态势。
中国和韩国造船产业竞争力对比分析
对外经济贸易大学硕士学位论文中国和韩国造船产业竞争力对比分析姓名:林俊兑申请学位级别:硕士专业:企业管理指导教师:刘子安20070401第一章中韩两国造船产业现状分析第一节世界造船产业现状分析一.世界造船市场概况1.海运增长引发的熊市期2003年开始到2005年为止国际海运船腹量的需求增加和陈旧船的交替出现重叠熊市。
2005年下半年开始出现集装箱船订货量急减,从而结束了海运增长引发的熊市期2.高油价引发的熊市期开始(2006年一至今)在进入2006年,因为高油价引发船舶的订货量急增加。
出现了高油价引发的熊市是因为远距离输送原油和精油的需求量增加,对Tanker的需求急增,由于对代替能源的需求,对LNG船的订货量急增,由于对海洋石油追加开发的需求,对海洋全套设备的订货也增加等现象。
其中的一个特征是有船舶大型化的趋势。
LNG船及海洋全套设备部门具有独步的竞争力和保持世界占有率第一位并集中了超大型建造设备的韩国是高油价引发的旺市中最大受益者。
图1:2005.20061季度新造船订赁量比较资料来源:韩国造船工协会业中国和韩国造船产业竞争力对比分析作者:林俊兑学位授予单位:对外经济贸易大学1.期刊论文王世新韩国光复军与中国国民政府关系试析——以韩国光复军征募三分处为中心-当代韩国2009,""(2)1940年于重庆成立的韩国光复军在中国抗日战争史、韩国独立运动史和中韩关系史上留下了绚烂的一笔.有关韩国光复军与中国国民政府的关系在学界一直存在着几种不同的看法,本文拟从韩国光复军征募三分处的视角,论述、说明韩国光复军与中国国民政府一直存在事实上的隶属关系.2.期刊论文王培文.WANG Pei-wen中国境内韩国无政府主义运动及其评价-上饶师范学院学报2009,29(1)中国境内韩国无政府主义运动史可分为三个阶段:1919-1923年是无政府主义运动的兴起时期,1924-1936年是无政府主义者建立组织、开展无政府主义运动的时期,1937-1945年中国抗日战争时期是中国境内韩国无政府主义运动参与民族统一战线,积极参加中国抗日战争的阶段.韩国无政府主义者在中国境内的活动,在韩国独立运动史上,占有一定的历史地位,在近代中韩关系史上写下了独特的一笔.3.期刊论文金惠珍.JIN Hui-zhen中国社会主义新农村运动与韩国新村运动——对胶南市公务员赴韩国大邱市进修培训的调查-黑龙江社会科学2007,""(4)中韩建交15年来,国家间交流日益加深,特别是政治、经济等方面交往不断扩大.2006年中国大规模推进的"新农村建设"运动,很多方面是以20世纪六七十年代的韩国新村运动为模式来进行的,中国国内许多地区向韩国派出了公务员学习其先进的行政体系.2006年,中国青岛胶南市即派遣29名公务员赴韩国大邱市参加为期6个月的进修培训,在行政管理、情报通信、国际交流、招商引资、经济管理、科学技术、文化·观光、环境管理、保健·福利·女性、自来水·污水政策、城市交通管理、建设防灾管理、韩国语等方面,就韩国新村运动的背景,新村运动的推广过程、成果等进行了学习.4.学位论文金玟宣韩国对中国投资的贸易效应研究2003该文共三部分.第一部分,对韩国对中国投资的投资规模、行业分布、投资主体与方式、地区分布进行分析,然后就韩中贸易的贸易额、商品结构、地区分布做了概括分析.第二部分回顾国际直接投资与国际贸易关系的理论发展,分别从东道国和投资国的角度来说明FDI对贸易的各种效应.第三部分,实证分析韩国对中国投资的贸易效应.接着从以下三个方面就韩国对中国直接投资的进出口效应进行分析:一、以统计数据为依据,根据韩国对中国的投资额、韩中进出口额,利用SPSS法,进行相关性分析,计算了投资与进出口的相关系数.二、根据韩国对中国贸易类型,分析韩国对中国投资子公司的进出口效应;韩国母企业通过原材料和零部件的供应关系,可以把握韩国母公司与中国当地企业间的联系程度.并进一步影响子公司的进出口.三、由于韩国对华投资主要以制造业为主、地区分布上主要集中于沿海地区,因此,接下来通过对中国8个地区韩国对制造业投资与进出口贸易的相关性进行分析,可以获得某一地区的制造业投资比重高时该地区的进出口比重也高的结论.5.期刊论文李光烈.姚远.韩隽.LI Guang-lie.YAO Yuan.HAN Jun中韩合作抗战时期韩国在华期刊出版考-西北大学学报(哲学社会科学版)2009,39(3)为求廓清韩国在华期刊出版的历史脉络及其传播学贡献,通过文献调研和考证,论述了从1913年至1945年的40余种韩人在华出版的期刊,并对最具代表性的<韩民月刊>作了具体分析.认定1913年7月创刊的<新兴学友报>为韩人在华创刊最早的期刊.这些期刊对激励韩国人民抗倭独立斗争、促使中韩人民团结合作抗击日寇、促进中国与韩国人民的文化交流和传统友谊,特别是在传播联华抗倭复国精神方面做出了重大贡献,不仅是韩国革命史的珍贵文献,同时也是中国新闻传播史的珍贵文献.6.期刊论文郑凤霞.张顺兴.ZHENG Feng-xia.ZHANG Shun-xing中国儒家传统文化对韩国社会发展的影响-延边大学学报(社会科学版)2009,42(4)中国与韩国是友好近邻,两国地缘相近,文化交流源远流长,关系密切.中国是世界文明发达最早的国家之一,已有近4000年的文字可考的历史.韩国人则善于学习,总以开明的态度欢迎中国文化和现代的西方文化,吸收中西方文化的精华,创造了具有本国特色的优秀文化.特别是中国儒家文化在古代朝鲜半岛就已影响深远,对韩国现代化和当今社会也产生了深刻影响.7.期刊论文满岩韩国基督教会在中国传教活动探析-东京文学2008,""(10)震惊世界的阿富汗韩国人质引起了全世界对韩国基督教的迅猛发展与韩国基督教会多年来步履匆忙的宣教行动的关注.就了解,在韩国派出的1.6万海外传教队伍中,大部分布道者就在中国,因此韩国基督教会在中国的传教活动,也必须引起我们的注意.本文从韩国基督教会传教热情根源、韩国基督教会在中国传教活动现状调查等方面综合分析了韩国基督教会在中国的传教活动及我国对策.8.学位论文王琦中国国民政府援助韩国独立运动的缘起和发展2007韩国民族独立运动与中国的反帝爱国运动是近代东方民族反帝独立斗争的重要组成部分。
中日造船业比较 -----中日科技文化交流
随着新中国第一个五年计划的完成,造船业也和许多重工 业一起迅速恢复、发展。1958年,大连造船厂和江南造船厂在 造船“速度竞赛”中分别建成国内自主设计的5000吨级沿海散 货船“和平25”号与“和平28”号,在创造纪录的同时也促成 了多项技术革新。
中国造船史
• 1958年年11月27日,由苏联转让 技术和设备建造的第1艘“567” 型万吨级远洋货轮“跃进”号下 水。这是第二个五年计划期间国 家重点产品。" 跃进号"是新中国 建造的第一艘万吨级远洋货船, 是国家重点建设项目,她的建造 成功,为中国船舶生产探索了道 路,积累了经验。锻炼了造船职 工队伍,提高了职工业务技术素 质,也提高了我国造船整体水平。 它标志着新中国造船工业进入了 一个新阶段。这是中国造船业由 建造小型船舶到建造大型船舶的 飞跃。
中日造船业竞争力差异
1.劳动力成本 造船属于劳动、资金、技术三要素都密集的行业,劳动力成本很 重要。造船业需要大量低技术含量的工人,高收入国家的居民不 大愿意作造船厂的工人,日本、韩国都出现了造船工人来源不足 的问题。中国劳动力数量众多,成本远低于欧洲、日本、韩国等 造船业大国。日本、韩国的人均工资成本大约是中国的7-8倍, 中国造船企业工资占销售收入的比例一般都低于10%,而日本造 船企业的该比例约为30%,这削弱了日本造船企业的竞争力。中 国造船业当前拥有的综合劳动成本优势,可保持相当长时间。造 船业作为劳动密集型行业,同时考虑人力成本和生产率而计算出 的综合劳动成本在成本控制中起到关键作用。未来5-10年内中国 造船业综合劳动成本仍将远低于韩国企业。
中国造船史
建国初期,我国船舶工业伴随着共和国成长的步伐,自力 更生、自主创新,在非常薄弱的基础上艰难起步。鉴于当时船 舶工业遭受战争的严重破坏,我国尚不具备自行建造现代化船 艇的基本条件,引进成套器材在国内建造便成为首选。1955- 1957年,我国船舶工业集中力量建造了一批苏联转让的护卫舰、 木质鱼雷快艇、鱼雷潜艇、猎潜艇、基地扫雷艇等5型舰艇。
- 1、下载文档前请自行甄别文档内容的完整性,平台不提供额外的编辑、内容补充、找答案等附加服务。
- 2、"仅部分预览"的文档,不可在线预览部分如存在完整性等问题,可反馈申请退款(可完整预览的文档不适用该条件!)。
- 3、如文档侵犯您的权益,请联系客服反馈,我们会尽快为您处理(人工客服工作时间:9:00-18:30)。
中国造船管理与日韩差距深度分析(待续)随着船舶工业的快速发展,我国已进入与日本、韩国造船业展开正面竞争的主战场。
尽管我国引进了与日、韩造船企业基本相同的加工设备,建立了不同形式的分道生产流水线,但我国船企与日、韩船企的差距仍是全方位的。
一、生产效率按人均生产修正总吨计算,日本的生产效率为185.6修正总吨/人年,韩国的生产效率为123.33修正总吨/人年,而中国为19.54修正总吨/人年。
按修正总吨消耗工时计算,日本为10小时/修正总吨,韩国为15小时/修正总吨,中国为95小时/修正总吨。
我国人工成本较低,但这一优势被生产效率低下、产品功能过剩、规模效益低下大大抵消了。
以下为几家船厂4万吨散货船建造工时对比表。
船厂工时(万小时)日本大岛造船厂10日本川崎17日本大阪船厂24南通中远川崎34中国新港船厂100(日报工时:72)我国造船企业与日、韩造船企业生产效率差距如此之大,体现在设计、生产、管理等方面。
生产方面主要是在如何压缩生产过程中的无效作业时间上存在差距。
造船产品在生产过程中所耗费的作业时间分为有效作业时间和无效作业时间,在传统造船模式中,无效作业时间远远大于有效作业时间。
日、韩造船企业提高生产效率的基本方法就是压缩无效作业时间。
压缩无效作业时间的关键是从管理上不断消除产生无效作业时间的环节。
日、韩造船企业采取的方法是:开展岗位分析。
按区域/阶段/类型对造船生产作业流程中各个环节的饱和程度不间断地进行跟踪分析,通过岗位合并,培训复合技能人员,提高工时利用率。
日本大阪船厂上世纪80年代对船台划线作业进行分析,通过改革划线工具,把本来由两个人完成的划线作业合并为1人,提高划线工时利用率50%。
大岛船厂在上世纪90年代末,针对船坞和码头施工的不同特点,按“船台完成安装,码头进行调试”的原则,对舾装作业人员重新进行调整,把舾装、设备安装和调试分开,消除了不同工种交叉作业的混乱现象,提高了生产效率,从事舾装工作的人员由179压缩到162人。
压缩辅助作业工时。
日本大岛船厂非常重视压缩吊运、整理等辅助作业时间。
在材料管理上.按材料使用顺序确定材料存放位置,尽量减少集配整理时间。
在流程上。
要求物件在物流过程中不停顿、不倒退、不转向,尽量缩短物流路线,减少吊运时间。
与大岛船厂相比,我国船厂的差距较大。
大岛船厂小组立构件焊缝打磨、清理占作业时间的2%,新港船厂(35200吨散货船)比大岛船厂超出9.3%。
大阪船厂上世纪80年代80吨货舱底段船台吊装定位时间为15分钟,大岛船厂上世纪90年代600吨艏总段船坞搭载定位时间为1.5小时.我国造船企业现在的搭载速度远没达到日本造船企业20年前的水平。
为了减少分段吊运搭载过程中的无效作业时间,日、韩造船企业制定了精细的船坞门机吊装计划表,吊车使用时间按分钟计,如此精细化的门吊使用计划大大提高了门机使用效率。
目前.韩国大字船厂530米长的大坞同时建造4艘船,只配置一台900吨门机,但能够做到40天打开一次坞门,9天交一艘船。
积极推进工序前移。
大岛船厂把工序前移形象地定义为“l、3、6、9法则”——小组立、大组立、船台、码头各工艺阶段在分别完成相同工作量的情况下,所消耗的作业时间比例为l:3:6:9。
我国各造船企业近几年推进工序前移也取得了成效。
根据新港船厂对32500吨散货船统计分析可以看出.将下游工序的工作前移到上游工序,对提高生产效率可以取得事半功倍的效果。
大组立效率高于船台19%,中组立效率高于大组立40%,小组立效率高于中组立31%。
目前,我国各造船企业推进工序前移发展不平衡,效果有差别,特别是在理解有效劳动和无效劳动的深刻含义上,我国造船企业和日本有明显差距。
在生产过程中,我们对无效劳动的大量存在估计不足,对通过压缩无效作业时间提高生产效率的重要意义认识不足,没有很好地认识到生产技术准备不到位、生产资源配置不精细等一系列管理问题是产生无效作业时间的主要原因。
一旦生产“卡壳”首先想到的是增加设备、加斑加点。
各企业复合技能培训工作开展不平衡,一人工作多人干的现象依然存在。
由于企业生产组织的设置和中间产品的生产还没有完全形成对应关系,导致工种交叉、相互冲突,从而产生大量无效劳动。
二、物耗和能耗降低产品资源消耗是降低造船成本的根本途径。
日、韩造船企业降低造船资源消耗的基本方法是全面推行精细化设计、精细化生产和精细化管理。
日、韩造船企业从合同设计、初步设计到详细设计、生产设计,全过程推行功能成本分析,对船体自重、设备选型、管系布置、电缆走向等专业设计进行优化分析,全面开展消除多余功能的研究。
我国造船业的资源消耗明显高于日、韩等先进造船国家的造船业,功能过剩,同等吨位的船体设计自重高于日、韩10%左右。
中、韩设计自重对比如下表:船型韩国设计自重(吨)中国设计自重(吨)4.5万吨散货船9500 108107.5万吨散货船11600 1280010.5万吨油船16800 1800017.5万吨散货船21800 235004250TEU集装箱船17200 18500VLCC 41000 44500我国造船企业能耗水平与日、韩相比差距跟大,中国船厂的平均电耗达到3606度/万美元产值,是世界先进造船企业的10倍以上。
产生如此差距的原因一是我国造船企业在粗放型管理模式下,追求吨位及产值增长的热情较高,习惯于以外延扩大再生产方式发展造船经济,对降低造船资源消耗没有紧迫感;二是企业的设计、生产、管理人员对开展功能成本分析、消除产品多余功能缺少积极性和主动性。
为了减少设计与生产脱节而造成的重复消耗,大宇船厂提出:设计部门要改变思考问题的方式,树立以生产为主的先进理念,必须依据生产部门的需求而不是按照自己的理解向生产现场提供图纸和相应数据。
大宇船厂副总裁徐浣澈一再强调:“在初步设计阶段就将生产现场的意见反馈到初步设计部门,使初步设计和分段划分相互联系起来,这样的船厂才是高效率的船厂。
” 降低成本的关键在设计。
根据日、韩造船企业的经验,我国造船企业应积极推行造船成本管理工作前移,把设计作为降低成本的第一步。
三、中间产品生产社会化目前,日、韩造船企业加快了推行总装化的步伐,各总装厂的上层建筑、管子零部件和单元模块基本委托专业生产厂家生产。
韩国东方精工株式会社是上层建筑、烟囱的专业生产厂,也是克令吊、救生艇、绞车等甲板机械设备生产厂。
该社是韩国现代、大宇、三星以及日本川崎等大型造船企业长期合作的外协企业,每年生产上层建筑达100余个。
东方精工株式会社生产的上层建筑舾装相当完整,电缆、铁舾件、设备安装及内外舾装工程全部完成,满足船厂对中间产品完整性的要求。
韩国杰森管子加工株式会社是管子零部件和管子单元的生产厂,是大宇、三星、现代造船企业长期合作的外协单位。
生产能力为每月生产两万件。
目前韩国有40家管子加工企业,规模较大的有4~5家。
上世纪80年代.我国造船企业开始学习和引进日本造船企业的先进经验,在推行总装造船的起步阶段,主要是推行“壳、舾分离”模式,也就是把铁舾件生产从造船生产作业主流程中分离出来.逐步向外扩散。
广船国际在分段扩散外协制造方面积累了成功的经验,原大连新船重工推行单元、模块社会化生产取得了显著成效。
但是,我国造船中间产品社会化程度和日、韩相比还有很大差距。
至今,我国还没有专业化的上层建筑制造厂家。
除大连外.其他地区还没有专业化的管子单元、模块制造厂家。
由于上层建筑、单元、模块等中间产品生产厂家在我国还未形成合理的布局,致使正在或准备扩建、迁厂的造船企业处于两难境地:一方面,在工厂规划设计上,如果把上层建筑、管子生产都放在厂内,不符合总装造船的发展方向;另一方面,在配套体系不健全的情况下,如果不考虑管子和上层建筑等中间产品由工厂自己生产,将会给造船正常生产带来严重影响。
为加快总装造船的发展步伐,我国在重点发展总装造船基地的同时,应该把建立与总装造船基地相配套、布局合理的中产品专业化协作厂提到议事日程上来,把总装厂的规划建设与配套厂的建设紧密结合起来,建设不同规模的中间产品加工中心,如钢材加工中心、管子加工中心、模块加工中心、上层建筑加工中心,与总装厂形成长期稳定的协作关系,这是推进我国船舶工业实现跨越式发展的重要举措。
四、精细化造船精细化造船包括精细化设计、精细化生产和精细化管理。
推行精细化设计、精细化生产、精细化管理的关键是强化数据管理。
日、韩造船企业经过多年的积累,已经形成了完备的设计、生产、管理数据体系。
企业从上至下非常重视数据管理工作,并把能否有效推进数据管理作为评价管理人员是否合格的标准。
大阪船厂对管理人员的评价标准是“数据、常识、良心”。
所谓数据就是用数据说话,所谓常识就是像运用常识一样熟练运用技术管理知识,所谓良心就是事业心与进取心。
日、韩造船企业的设计邮门能提供系统完整的满足生产部门需要的生产管理数据,生产现场也能通过规范的信息反馈渠道收集到完整的反馈信息,形成有效的数据管理循环。
工程计划管理完全依据物量、工时、能率等一系列数据计算生产能力,进行生产负荷和资源配置的动态平衡分析,编制日程计划、负荷计划和资源配置计划。
上世纪80年代初,大阪船厂计算机辅助设计、生产、管理还没有完全铺开,就已经积累了100多艘船的物量、工时、能率数据,这些数据是采用人工统计的方式完成的。
我国造船企业和日、韩造船企业数据管理的差距是惊人的,通过对日本造船企业上世纪70年代、80年代、90年代有关资料分析,可以发现,我国造船企业的数据管理水平落后日本30年!目前我国造船企业数据管理的最大问题就是设计部门不能提供系统完整的生产管理数据,生产现场也不能收集到规范的反馈信息。
我国造船企业在数据管理上存在两大障碍:一是认为现在企业的数据不真实,收集整理这样的数据没有实际意义;二是习惯于调度式的生产指挥方式。
关于对反馈工时信息真实性的认识,我国船企和日、帏造船企业有明显的区别。
日本船企有非常明确的观点:一是反馈工时信息收集必须坚持日报制度,只要是推行日报,而不是周报、月报,并能长期坚持下去,就会收集到可靠的信息。
日报信息可能一天、两天不真实,但不可能一年365天都不真实,这是采集数据的基本规律所决定的。
二是反馈工时信息的处理分析不是把某些局部的、个别的数据作为制订计划的依据,而是对大量的、系统的数据进行数理统计分析,以加权平均值、统计平均值作为制订计划的依据,因此个别不真实数据对数据分析结果影响不大。
我国造船企业推行数据管理困难还有管理机制上的原因。
工时日报管理在日、韩造船企业已经推行了几十年,是收集反馈信息的重要渠道,已经成为企业开展工程计划管理不可缺少的一个重要环节,而在我国推行工时日报管理却困难重重,阻力极大。
我国造船企业推行数据管理,要学习日、韩造船企业数据管理的先进理念,深刻理解并掌握日、韩造船企业数据管理的三大关键环节,理解数据管理的精髓,在实践中脚踏实地做好数据的积累工作,这是推进现代造船模式深入发展不可跨越的一个环节。