氩气流量控制系统设计
PLC在气体流量控制技术上的应用

PLC在气体流量控制技术上的应用蒋 军Application of PLC in the Technique for Controlling Gas FluxJI ANG Jun(陕西理工学院(北区)电气工程与自动化系电工电子教研室,陕西汉中 723003)摘 要:分析了PC M脉冲编码技术中存在的不足,提出一种改进型的PC M脉冲编码技术。
应用双斜式A/D转换器的原理,利用PLC的内部的计数功能,将模拟量转换成时间量,在原有的不能处理模拟量的可编程控制器上,完成小型机或整体机PLC组建数字流量自动控制系统,以实现对气体流量的精确、快速地控制。
提高了系统的性能价格比。
此方案已成功地应用在数家炼钢厂的吹氩控制中。
关键词:PC M;气体流量控制;双斜式A/D转换器;PLC中图分类号:TP274 文献标识码:B 文章编号:1000 4858(2007)03 0033 04气体流量控制通常是靠流量控制阀来完成,而流量控制阀是通过改变阀的流通面积来实现流量或流速的控制。
对流体气体而言,改变流通面积不但使其阀管道的有效截面积改变,而且使气体的局部压力损失也改变。
对于以亚音速流动的气体,其流量的计算公式为q=22.7S p1(p1-p2)[2],其中q为气体流量(L/min),S为管路的有效截面积(mm2),p1,p2为节流孔前后的压力(105Pa)。
由于S改变,导致p1-p2= p也在改变,那么影响流量的2个量在改变时,较为精确地控制流量变得比较困难。
对于一般的流量控制流量控制阀尚且能满足要求,但对于比较精确地控制流量,现在多用PCM脉冲编码技术[1]。
从自动控制系统的角度来说,PC M脉冲编码技术仅是较为准确地完成执行环节的任务,从反馈控制原理得知,要控制那个物理量不变,必须引入此物理量的负反馈,显然,要想对气体流量精确的控制,就得对其形成闭环控制。
由于PLC是综合了计算机技术、自动控制技术和通信技术的一种通用的自动控制装置。
LF精炼炉底吹氩过程中的氩气流量控制
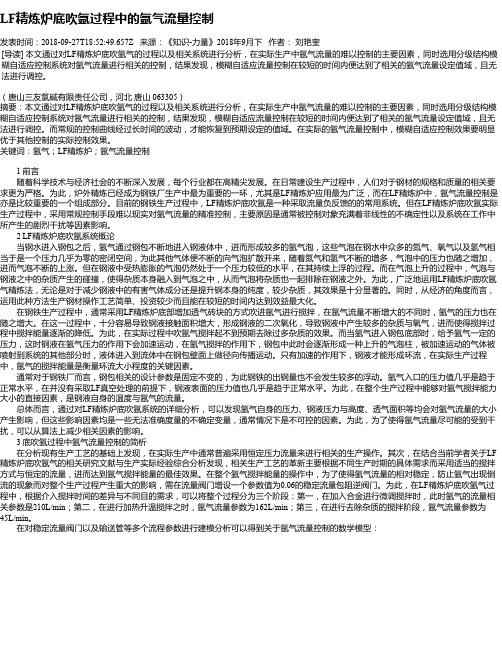
LF精炼炉底吹氩过程中的氩气流量控制发表时间:2018-09-27T18:52:49.657Z 来源:《知识-力量》2018年9月下作者:刘艳奎[导读] 本文通过对LF精炼炉底吹氩气的过程以及相关系统进行分析,在实际生产中氩气流量的难以控制的主要因素,同时选用分级结构模糊自适应控制系统对氩气流量进行相关的控制,结果发现,模糊自适应流量控制在较短的时间内便达到了相关的氩气流量设定值域,且无法进行调控。
(唐山三友氯碱有限责任公司,河北唐山 063305)摘要:本文通过对LF精炼炉底吹氩气的过程以及相关系统进行分析,在实际生产中氩气流量的难以控制的主要因素,同时选用分级结构模糊自适应控制系统对氩气流量进行相关的控制,结果发现,模糊自适应流量控制在较短的时间内便达到了相关的氩气流量设定值域,且无法进行调控。
而常规的控制曲线经过长时间的波动,才能恢复到预期设定的值域。
在实际的氩气流量控制中,模糊自适应控制效果要明显优于其他控制的实际控制效果。
关键词:氩气;LF精炼炉;氩气流量控制1 前言随着科学技术与经济社会的不断深入发展,每个行业都在高精尖发展。
在日常建设生产过程中,人们对于钢材的规格和质量的相关要求更为严格。
为此,炉外精炼已经成为钢铁厂生产中最为重要的一环,尤其是LF精炼炉应用最为广泛,而在LF精炼炉中,氩气流量控制是亦是比较重要的一个组成部分。
目前的钢铁生产过程中,LF精炼炉底吹氩是一种采取流量负反馈的的常用系统。
但在LF精炼炉底吹氩实际生产过程中,采用常规控制手段难以现实对氩气流量的精准控制,主要原因是通常被控制对象充满着非线性的不确定性以及系统在工作中所产生的剧烈干扰等因素影响。
2 LF精炼炉底吹氩系统概论当钢水进入钢包之后,氩气通过钢包不断地进入钢液体中,进而形成较多的氩气泡,这些气泡在钢水中众多的氮气、氧气以及氢气相当于是一个压力几乎为零的密闭空间,为此其他气体便不断的向气泡扩散开来,随着氮气和氢气不断的增多,气泡中的压力也随之增加,进而气泡不断的上涨。
钢包底吹氩控制系统的优化设计

钢包底吹氩控制系统的优化设计一、引言钢包底吹氩控制系统在钢铁冶炼过程中起着至关重要的作用。
它通过控制底吹氩气的流量和压力,实现钢水中氧含量的控制,从而提高钢水质量和冶炼效率。
然而,在现有的底吹氩控制系统中,仍存在一些问题和待优化的空间。
本文将针对这些问题进行探讨,并提出一种优化设计方案,旨在改善底吹氩控制系统的性能。
二、问题分析1. 氩气流量不稳定:目前的底吹氩控制系统在控制氩气流量时存在一定的波动性,这可能导致钢水中氧含量无法稳定控制,使得钢水质量下降。
2. 压力控制不准确:底吹氩控制系统中的压力传感器精度有限,无法实现精确的压力控制,这可能影响到氩气的吹入效果。
3. 控制策略过于简单:目前的底吹氩控制系统采用的控制策略相对简单,无法充分考虑到钢水冶炼过程中的复杂动态变化,导致控制效果有限。
三、优化设计方案为了改善钢包底吹氩控制系统的性能,我们提出以下优化设计方案:1. 引入先进的气体流量控制技术:通过采用先进的气体流量控制器,可以实现对氩气流量的精确控制。
该控制器能够根据实时测量的氩气流量反馈信息,调整控制阀门的开度,以实现稳定的氩气流量输出。
2. 优化压力传感器选择:选择高精度的压力传感器,并进行准确的校准和调整,以提高底吹氩控制系统中压力的测量和控制精度。
3. 制定复杂的控制策略:结合钢水冶炼过程的动态特性,制定更为复杂的控制策略。
该策略应考虑到钢水温度、氧含量、氩气流量等多个因素的综合影响,并通过建立合适的数学模型和控制算法,实现对底吹氩控制系统的智能化控制。
四、实施方案在实施优化设计方案时,需要考虑以下几个方面:1. 系统硬件的更新:根据优化设计方案的要求,对底吹氩控制系统的硬件进行更新,包括更换控制器、传感器等设备,并确保其与现有系统的兼容性。
2. 软件算法的优化:根据新的控制策略,优化底吹氩控制系统的软件算法,确保其能够准确地根据实时数据进行控制决策,并实现智能化控制。
3. 系统测试与调试:在实施优化设计方案后,进行系统测试与调试,验证新设计的稳定性和性能。
炼钢精炼炉钢包底吹控制系统改造分析

71C omputer automation计算机自动化炼钢精炼炉钢包底吹控制系统改造分析沈江珠(酒钢集团榆中钢铁有限公司,甘肃 兰州 730104)摘 要:随着当前炼钢行业的不断发展进步,其冶炼工艺技术基于创新手段,极大的提高了冶炼产品质量和生产效率。
而钢包底吹作为冶炼工艺中的重要环节,现有炼钢精炼炉钢包底吹控制系统已经不能完全满足现代化工艺生产需求,必须要对原有控制系统进行一定的优化和改造,保障钢包底吹控制系统具有良好的实施效果,提高氩气流量控制的合理性。
因此本文从硬件配置以及PLC 编程角度出发,在原有控制系统管理基础上,对其进行优化改造,旨在更好的促进炼钢精炼炉钢包底吹控制系统满足生产工艺要求,进一步提高生产效率和效益。
关键词:炼钢精炼炉;钢包底吹;控制系统;改造中图分类号:TF769 文献标识码:A 文章编号:11-5004(2020)16-0071-2收稿日期:2020-08作者简介:沈江珠,男,生于1987年, 汉族, 甘肃临夏回族自治州人,本科,助工,研究方向:冶金工程。
钢包底吹是炼钢精炼炉在生产成品钢时,不可或缺的重要工艺手段。
其主要作用是通过搅拌和气洗钢水,以防止出现钢水氧化。
通常情况下,在开展钢包底吹工艺时,对精炼钢水质量影响最大的因素即是氩气流量的控制。
如氩气流量相对较大,则会导致穿液面发生严重的喷溅现象,从而致使钢水出现裸露氧化,致使夹杂物大量增加。
而如果吹氩气的流量较小,则会造成流量不够稳定、无法开展快速搅拌,不能完全的去除气体和夹杂物,影响炼钢过程的质量。
1 钢包底吹控制系统的原理炼钢精炼炉的钢包底吹控制系统改造的前提是了解和掌握其具体的工作原理。
一般情况下,钢包底吹控制系统是由两套氩气控制阀而组成,分别控制两组钢包底吹工艺的开展。
同时配备流量调节电磁阀,当其打开时,会产生对应的流量值。
而电磁阀的动作则是根据氩气流量工艺的实际要求而决定的,即是在HMI 设定炼钢工艺所需输出的流量值,通过计算后,能够准确得到电磁阀的动作状态,打开相应的阀而关闭其他无关阀。
钢包底吹氩控制系统的优化设计

钢包底吹氩控制系统的优化设计钢包底吹氩控制系统是钢铁生产过程中的重要环节,其优化设计能够提高钢铁生产的效率和质量。
本文将从钢包底吹氩控制系统的原理、优化设计的目的和方法以及实际应用效果等方面进行探讨。
一、钢包底吹氩控制系统的原理钢包底吹氩控制系统是通过控制钢包底部喷口的氩气流量和压力来实现钢水的混合和温度控制。
钢包底吹氩控制系统的主要组成部分包括氩气供应系统、氩气流量控制系统、氩气压力控制系统和温度控制系统等。
二、优化设计的目的和方法优化设计的目的是提高钢铁生产的效率和质量。
具体方法包括以下几个方面:1.优化氩气供应系统,确保氩气的稳定供应和质量。
2.优化氩气流量控制系统,提高氩气流量的精度和稳定性。
3.优化氩气压力控制系统,确保氩气压力的稳定和可靠性。
4.优化温度控制系统,提高钢水的温度控制精度和稳定性。
三、实际应用效果钢包底吹氩控制系统的优化设计在实际应用中取得了显著的效果。
通过优化设计,钢铁生产的效率和质量得到了大幅提升。
具体表现在以下几个方面:1.钢水的温度控制精度和稳定性得到了显著提高,减少了钢铁生产中的温度偏差和浪费。
2.钢水的混合效果得到了改善,减少了钢铁生产中的不均匀性和质量问题。
3.钢铁生产的效率得到了提高,减少了生产时间和成本。
4.钢铁生产的质量得到了提高,减少了废品率和质量问题。
综上所述,钢包底吹氩控制系统的优化设计是钢铁生产中的重要环节,其优化设计能够提高钢铁生产的效率和质量。
通过优化氩气供应系统、氩气流量控制系统、氩气压力控制系统和温度控制系统等方面的设计,可以实现钢水的混合和温度控制,从而提高钢铁生产的效率和质量。
在实际应用中,钢包底吹氩控制系统的优化设计取得了显著的效果,为钢铁生产的发展做出了重要贡献。
金鲁鼎氩弧自动焊机参数讲解

金鲁鼎氩弧自动焊机参数讲解摘要:一、引言1.金鲁鼎氩弧自动焊机的背景介绍2.金鲁鼎氩弧自动焊机在焊接行业的地位和作用二、参数讲解1.焊接电流2.焊接电压3.焊接速度4.氩气流量5.焊丝直径6.控制系统三、金鲁鼎氩弧自动焊机的优势1.提高焊接效率2.保证焊接质量3.降低操作难度4.环保节能四、应用领域1.建筑行业2.制造业3.工程机械行业4.船舶行业五、结论1.金鲁鼎氩弧自动焊机的市场前景2.对我国焊接行业的推动作用正文:【引言】金鲁鼎氩弧自动焊机是一款具有高效、高质量、高稳定性等特点的焊接设备,广泛应用于各个行业。
氩弧自动焊机采用氩气作为保护气体,具有焊接速度快、熔接强度高、焊缝质量好等特点,大大提高了焊接效率和质量。
【参数讲解】1.焊接电流:金鲁鼎氩弧自动焊机采用微电脑控制,可精确调节焊接电流,保证焊接过程中的稳定性。
2.焊接电压:根据不同材料和厚度,金鲁鼎氩弧自动焊机可自动调节焊接电压,确保焊接质量。
3.焊接速度:金鲁鼎氩弧自动焊机具有高速焊接功能,可提高生产效率,降低生产成本。
4.氩气流量:金鲁鼎氩弧自动焊机配备高精度氩气流量控制系统,可保证氩气流量稳定,提高焊接质量。
5.焊丝直径:金鲁鼎氩弧自动焊机支持多种焊丝直径,满足不同焊接需求。
6.控制系统:金鲁鼎氩弧自动焊机采用微电脑控制系统,操作简便,易于维护。
【金鲁鼎氩弧自动焊机的优势】1.提高焊接效率:金鲁鼎氩弧自动焊机采用自动化焊接技术,焊接速度快,大大提高了生产效率。
2.保证焊接质量:金鲁鼎氩弧自动焊机具有高精度的参数控制系统,可确保焊接质量稳定。
3.降低操作难度:金鲁鼎氩弧自动焊机采用微电脑控制,操作简便,降低了操作人员的技术要求。
4.环保节能:金鲁鼎氩弧自动焊机采用氩气保护,无污染,符合环保要求。
同时,由于焊接速度快,节省了能源消耗。
【应用领域】1.建筑行业:金鲁鼎氩弧自动焊机广泛应用于建筑钢结构、钢筋焊接等领域,提高焊接质量和效率。
ws400氩弧焊机结构论述

ws400氩弧焊机结构论述
WS400氩弧焊机是一种常见的氩弧焊设备,它由以下几个部分组成:
1. 机身:WS400氩弧焊机的机身通常由金属材料制成,以提供良好的机械强度和散热效果。
机身上通常有一些控制按钮和指示灯,用于调节焊接参数和显示机器工作状态。
2. 电源系统:WS400氩弧焊机的电源系统包括变压器、整流器和电子元件。
变压器用于将外部交流电源的电压升高,然后通过整流器将其转换为直流电源。
电子元件用于控制和调节焊接电流和电压的大小。
3. 控制系统:WS400氩弧焊机的控制系统由控制电路板、控制按钮和显示屏组成。
控制电路板接收用户输入的焊接参数,并通过控制按钮和显示屏将这些参数传递给电源系统。
控制系统还可以监测焊接过程中的电流、电压和温度等参数,并在需要时进行自动调节。
4. 气体系统:WS400氩弧焊机的气体系统由氩气罐、气体流量计和喷枪组成。
氩气罐储存氩气,气体流量计用于调节氩气的流量,喷枪用于将氩气喷射到焊缝上。
氩气的作用是在焊接过程中产生保护气氛,防止焊缝受到氧气和湿气的影响。
5. 冷却系统:WS400氩弧焊机的冷却系统包括水冷却器和冷却管路。
在长时间高负荷工作时,氩弧焊机会产生较高的热量,需要通过冷却系统将其散发出去,
以保持设备的正常工作温度。
总之,WS400氩弧焊机由机身、电源系统、控制系统、气体系统和冷却系统等部分组成,通过这些部件的协调工作,实现对焊接电流、电压和氩气流量等参数的控制和调节,并保证焊接过程中的安全和稳定性。
【精品】真空镀膜机控制系统的设计
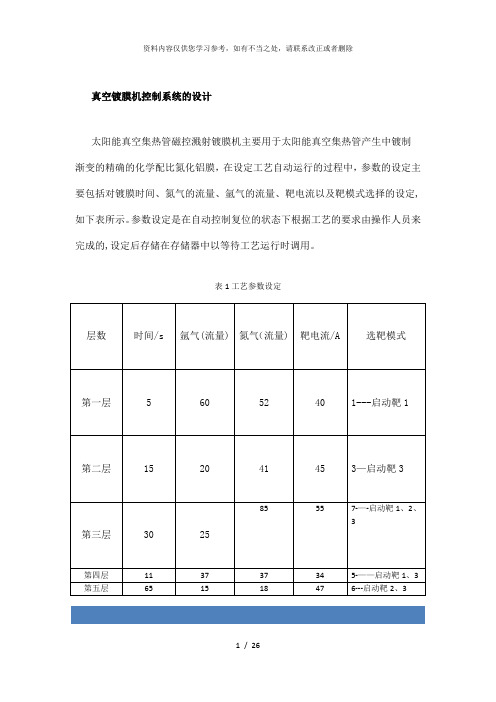
真空镀膜机控制系统的设计太阳能真空集热管磁控溅射镀膜机主要用于太阳能真空集热管产生中镀制渐变的精确的化学配比氮化铝膜,在设定工艺自动运行的过程中,参数的设定主要包括对镀膜时间、氮气的流量、氩气的流量、靶电流以及靶模式选择的设定,如下表所示。
参数设定是在自动控制复位的状态下根据工艺的要求由操作人员来完成的,设定后存储在存储器中以等待工艺运行时调用。
表1工艺参数设定采用手动控制和自动控制相结合的设计思路,设计采用FPGA为核心控制芯片,基于VHDL 语言,这个自动控制系统的设计分成工序流程控制模块、参数设置及调用模块和通信模块三个模块.其中工序流程模块采用有限状态机设计,完成工序流程的控制;参数设置及调用模块主要完成系统所需的参数的设置,需要设置的参数包括镀膜的时间,氮气流量,氩气流量、靶电流大小以及对靶的模式,参数设置及调用模块主要为SRAM的设计;通信模块设计了UART接口,便于与计算机或其他设备之间进行通信。
系统的设计原理框图如下:图1:系统原理框图3。
1工序控制流程模块:用状态机来设计,状态机是数字设计的重要组成部分,是实现高效率,高可靠逻辑控制的重要途径.此模块采用MOORE状态机来描述,其状态机的状态转移图如下图所示,其中包好了17个状态,即包含了整个工序控制的流程,没有标明条件的是一种“无条件”转换。
图2:工序自动运行的状态转移图1。
自动控制模块的功能仿真及分析如图3所示,在复位信号reset变为高电平(reset=’1’)后,开自动运行(atom_hand='1'),接着自动运行工序;开机械泵(machinpump=’1’),开预抽阀(beforeluntvalve='1’),判断真空度1(vacuity=’1'时);关预抽阀(beforeluntvalve=’0’),开前级阀(prevalve=’1’),开高阀(highvalve=’1'),关维持阀(naintainvalve=’0'),关维持泵(maintainpump=’0’),判断真空度2(vacuity2=’1'时);关光闸阀(lightbarriervalve=’1’),开截止阀(cutvalve='1’),判断真空度3(vacuity3='1’时);开氮气控制(nitrogenontrol='1')和氩气控制(argoncontrol=’1’),开工件旋转(workpiecerun='1'),开靶运行(buttrun=’1’),加靶电流(buttcurrent1、2、3),自动运行(crafrun=’1’);运行完毕后,开充气阀(aeratevalve=’1’),开门信号(onoffdoor='1’),取工件,进行下一个工序;图3:自动控制系统模块的功能仿真(1)图3:自动控制系统模块的功能仿真zoomout(2)由于此程序较长,具体的程序设计见附录。
- 1、下载文档前请自行甄别文档内容的完整性,平台不提供额外的编辑、内容补充、找答案等附加服务。
- 2、"仅部分预览"的文档,不可在线预览部分如存在完整性等问题,可反馈申请退款(可完整预览的文档不适用该条件!)。
- 3、如文档侵犯您的权益,请联系客服反馈,我们会尽快为您处理(人工客服工作时间:9:00-18:30)。
自动控制系统课程设计设计题目:氩气流量控制系统设计班级:学号:XX:指导教师:设计时间:摘要氩气在金属冶炼、金属焊接、半导体工业、医疗器械、科学研究及国防工业上有着广泛应用,在这些应用中对氩气流量的控制有较高的要求。
本文设计了一套以PLC可编程控制器为控制核心,由工业计算机、氩气流量计、电动调节阀等组成的氩气流量控制系统。
系统采用PID负反馈控制,实现了对氩气流量精确、快速地控制。
关键词:氩气流量控制;PLC;PID控制目录摘要 (I)1概述 (1)2课程设计任务及要求 (2)2.1设计任务 (2)2.2设计要求 (2)3理论设计 (3)3.1方案论证 (3)3.2系统设计 (3)3.2.1结构框图及说明 (3)3.2.2系统原理图及工作原理 (4)3.3单元电路设计 (4)3.3.1单元电路工作原理 (4)3.2.2元件参数选择 (7)4系统设计 (9)4.1软件设计 (9)4.2编程过程 (9)4.3编程结果 (12)5安装调试 (13)5.1安装调试过程 (13)5.2故障分析 (13)6结论 (15)7使用仪器设备清单 (18)8收获、体会和建议 (19)9参考文献 (20)1 概述氩气广泛应用于金属冶炼、飞机制造、原子能研究及国防研究等工业。
它的性质十分不活泼,既不能燃烧,也不助燃。
在对特殊金属(例如铝、镁、铜及其合金和不锈钢)进行焊接时,往往用氩气作为焊接保护气,防止焊接件被空气氧化或氮化。
在金属冶炼方面,氧、氩吹炼是生产优质钢的重要措施,每炼1t钢的氩气消耗量为1~3m3。
此外,对钛、锆、锗等特殊金属的冶炼,以及电子工业中也需要用氩气作保护气。
随着生产工艺的提高,传统的二次仪表已经无法满足现有的控制要求。
为了实现在这些生产工艺中对氩气流量的精确控制,本文提出了一套基于PLC可编程控制器为核心的氩气流量控制系统。
作为目前广泛应用的新一代工业控制装置,PLC采用可以编制程序的存储器,用来在其内部存储执行逻辑运算、顺序运算、计时、计数和算术运算等操作的指令,并能通过数字式或模拟式的输入和输出,方便地与各种生产机械进行通信,控制各种类型的机械或生产过程。
为此,使用PLC作为控制核心,气体电动调节阀器作为执行元件,对气体流量进行精确、快速、可靠的自动控制。
2 课程设计任务及要求2.1设计任务设计氩气流量控制系统,控制对象为管径φ5㎜内的氩气流量。
氩气流量可以在一定X围内由人工设定,实现自动控制,以保证氩气流量的准确。
氩气工作压力为0.5MPa。
2.2设计要求1.选择合适的传感器、执行器、控制器,设计控制方案。
2.设计合适的控制算法及算法参数,达到以下要求:(1)流量设定X围10~100N㎡/Min,最小区分度为1N㎡/Min。
(2)控制的静态误差≤0.1N㎡/Min。
(3)实现氩气流量的温度、压力补偿。
(4)操作界面的设计,包括(输入量的显示、设定参数的输入、控制参数的输入)3 理论设计3.1 方案论证氩气流量控制系统由工业计算机、PLC可编程控制器、电动阀和氩气流量计等组成。
氩气流量设定值由计算机输入界面人工给定。
氩气流量计检测出管道内流量信号,通过变送装置反馈给PLC可编程控制器,与设定值进行比较。
PLC可编程控制器作为PID控制器,控制电动阀调节器,实现氩气流量的快速、无静差控制。
在氩气流量调节过程和正常生产过程中,可通过计算机的监视画面实时监控氩气流量。
3.2系统设计3.2.1 结构框图及说明整个控制系统由工业计算机、PLC可编程控制器、电动阀和氩气流量计等组成,结构如图3.1所示。
图3.1 氩气控制系统结构图1.工业计算机部分采用国内最稳定的研华原装工业电脑型号:研华IPC-610H(2.4GHz/6006LV)配置如下:◆P4 2.4G CPU;512M DDR2内存;32M显卡;80G硬盘;软驱;光驱;4个USB2.0接口;双10/100M网卡;◆17英寸三星CRT显示器、联想天工工业键盘、鼠标套装。
2.工业计算机软件部分◆微软WINDOWS 2000或WINDOWS XP操作系统◆亚控科技组态王6.53◆三菱PLC编程软件GX-DEVELOPER 73.可编程控制器PLC采用日本三菱的Q00J系列可编程控制器,含DA和AD转换模块。
4.氩气流量计采用XX安锐自动化仪表XX生产的AVS100系列氩气流量计(含温度传感器和压力变送器),工作压力≤1.6Mpa,输出信号为三线制电压脉冲或4~20mA标准电流,方便与自动化系统连接。
5.电动调节阀选用FISHER公司生产的SAR10.1-ED型调节阀(含定位器),工作压力0.5MPa,工作温度0~263℃,采用电开方式。
3.2.2 系统原理图及工作原理工作原理:系统的被控对象为管道,系统给定量由计算机设定,被控量为管道内氩气流量,反馈量由氩气流量计检测并送入PLC中,并与给定量进行比较,调节器按PID控制算法计算出实时控制量,来控制电动调节阀的控制阀开度,从而调节管路的流量,构成单闭环流量控制系统,系统原理图如图3.2所示。
图3.2 氩气控制系统原理图比例、积分、微分控制(PID控制)结构简单、稳定性好、工作可靠、调整方便。
PID调节的实质就是根据输入的偏差值,按比例、积分和微分的函数关系进行运算,其运算结果用以输出控制。
它在比例的基础上引入积分,可以消除稳态误差,再加入微分作用,又能提高系统的稳定性。
3.3 单元电路设计3.3.1单元电路工作原理工业计算机和PLC用RS232通讯协议进行连接,通过计算机编制PID程序,然后下载到PLC中。
PLC使用三菱Q00J系列,Q62DA和Q64AD这两个模块进行信号的输入和输出。
Q62DA模块和电动阀进行连接,通过DA模块输出不同的电压值来控制电动阀的开度,进而实现氩气流量的控制。
Q64AD模块和氩气流量计进行连接,把氩气流量计反馈的电压值送入PLC中,进而判断氩气流量的大小。
硬件接线图如图3.3和图3.4所示。
图3.3 硬件连线图图3.4 电机主回路连线图下面对系统的各个部分进行详细介绍。
1.调节器——三菱Q系列PLCQ系列PLC是三菱公司从原A系列PLC基础上发展过来的中、大型PLC系列产品,Q系列PLC采用了模块化的结构形式,系列产品的组成与规模灵活可变,最大输入输出点数达到4096点;最大程序存储器容量可达252K步,采用扩展存储器后可以达到32M;基本指令的处理速度可以达到34ns;其性能水平居世界领先地位,可以适合各种中等复杂机械、自动生产线的控制场合。
Q系列PLC的基本组成包括电源模块、CPU模块、基板、I/O模块等。
通过扩展基板与I/O模块可以增加I/O点数,通过扩展储存器卡可增加程序储存器容量,通过各种特殊功能模块可提高PLC的性能,扩大PLC的应用X围。
Q系列PLC可以实现多CPU模块在同一基板上的安装,CPU模块间可以通过自动刷新来进行定期通信或通过特殊指令进行瞬时通信,以提高系统的处理速度。
特殊设计的过程控制CPU模块与高分辨率的模拟量输入/输出模块,可以适合各类过程控制的需要。
最大可以控制32轴的高速运动控制CPU模块,可以满足各种运动控制的需要。
通过GX Developer访问CPU,执行编程/监视功能,还可以设定参数,使PLC 系统简单易用。
PLC有两种工作状态,即运行(RUN)状态和停止(STOP)状态。
在运行状态,PLC通过执行反映控制要求的用户程序来实现控制功能。
为了使PLC的输出及时地响应随时可能变化的输入信号,用户程序不是只执行一次,而是反复不断地重复执行,直到PLC停机或切换到STOP工作状态。
除了执行用户程序外,每次循环过程中,PLC还要完成内部处理、通信处理等工作,一次循环可分为5 个阶段,如图3.5所示。
图3.5 PLC执行流程图2.检测变送装置——氩气流量计AVS100系列氩气流量传感器是根据“卡门涡街”原理研制成的一种流体振荡型流量仪表,主要用于测量工业管道中气体、液体、蒸气等流体的体积流量和质量流量。
其特点是压力损失小,量程X围大,精度高。
无可动机械部件,因此可靠性高,维护量小,仪表常数能长期稳定。
插入式仪表在管道的插入口安装,装卸简单,在脏污介质中运行时,可以方便地定期清洗和维修。
本仪表采用压电应力式传感器,可靠性高,可在-40ºC至+350ºC的工作温度X围内工作。
,工作压力≤1.6Mpa,输出信号为三线制电压脉冲或4~20mA标准电流,方便与自动化系统连接。
3.执行器——电动调节阀FISHER公司生产的SAR10.1-ED型调节阀调节阀用于调节氩气的的流量。
根据调节部位信号,自动控制阀门的开度,从而达到氩气流量的调节。
氩气进入阀门,并通过导向筒上端的孔迅速进入平衡室。
由于氩气均衡作用于导向筒的内腔及外端,使得阀杆作用于导向筒的力趋于均衡,执行机构的载荷不随氩气压力的变化而过度变化,因此,运行过程中不平衡力小,稳定性好,不易振动,阀门内件不易损坏。
随着阀杆带动导向筒向上运动,氩气进入阀笼的第一、二层节流孔,直至流出调节阀体。
导向筒的上下运动,改变着阀笼上节流孔的数量,即氩气流过节流孔的节流面积。
形成各种流量特性,并实现流量的调节。
其流量特性如图3.6所示。
图3.6 电动调节阀流量特性3.3.2元件参数选择1.工业计算机部分:采用国内最稳定的研华原装工业电脑型号:研华IPC-610H(2.4GHz/6006LV)配置如下:◆P4 2.4G CPU;512M DDR2内存;32M显卡;80G硬盘;软驱;光驱;4个USB2.0接口;双10/100M网卡;◆17英寸三星CRT显示器、联想天工工业键盘、鼠标套装。
2.可编程控制器PLC:选用三菱公司的Q00J型PLC(含Q64DA模块是62DA AD模块是64AD和Q62DA模块),最大输入输出点数达到4096点;最大程序存储器容量可达252K步,采用扩展存储器后可以达到32M;基本指令的处理速度可以达到34ns。
3.电动调节阀:选用FISHER公司生产的SAR10.1-ED型调节阀,含定位器,采用电开方式。
驱动方式:电动380V,定位器信号输出:4~20mA。
4.氩气流量计:采用XX安锐自动化仪表XX生产的AVS100系列氩气流量计,工作压力≤1.6Mpa,输出信号为三线制电压脉冲或4~20mA标准电流,方便与自动化系统连接。
4. 系统设计4.1 软件设计利用组态王软件可以开发出友好的人机界面,实现对控制参数进行实时输入,并且能够直观地显示控制系统的实时趋势曲线。
系统的PID参数在一定的X 围内可以任意调节,能够满足客户在不同场合下的不同要求。
同时氩气的流量也应该在监控画面上通过数字和曲线实时显示出来,以便客户方便地监控流量的变化。