时效处理
时效处理工艺
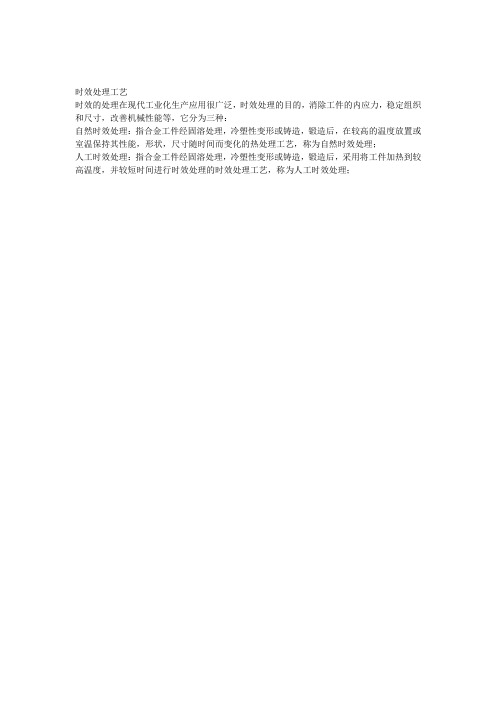
时效处理工艺
时效的处理在现代工业化生产应用很广泛,时效处理的目的,消除工件的内应力,稳定组织和尺寸,改善机械性能等,它分为三种:
自然时效处理:指合金工件经固溶处理,冷塑性变形或铸造,锻造后,在较高的温度放置或室温保持其性能,形状,尺寸随时间而变化的热处理工艺,称为自然时效处理;
人工时效处理:指合金工件经固溶处理,冷塑性变形或铸造,锻造后,采用将工件加热到较高温度,并较短时间进行时效处理的时效处理工艺,称为人工时效处理;。
时效处理名词解释
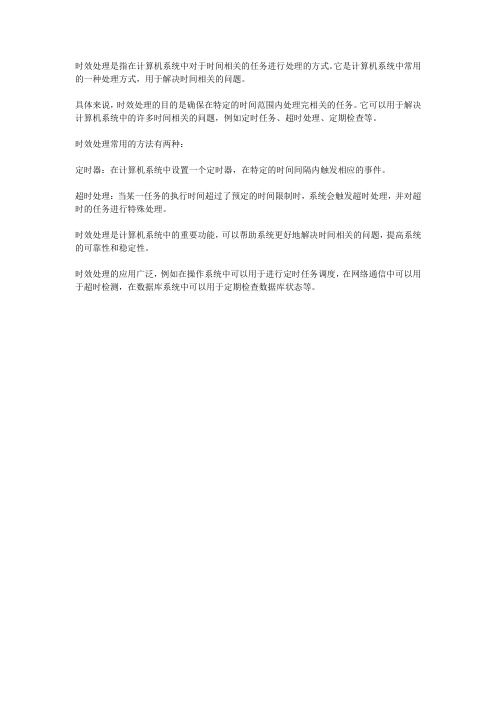
时效处理是指在计算机系统中对于时间相关的任务进行处理的方式。
它是计算机系统中常用的一种处理方式,用于解决时间相关的问题。
具体来说,时效处理的目的是确保在特定的时间范围内处理完相关的任务。
它可以用于解决计算机系统中的许多时间相关的问题,例如定时任务、超时处理、定期检查等。
时效处理常用的方法有两种:
定时器:在计算机系统中设置一个定时器,在特定的时间间隔内触发相应的事件。
超时处理:当某一任务的执行时间超过了预定的时间限制时,系统会触发超时处理,并对超时的任务进行特殊处理。
时效处理是计算机系统中的重要功能,可以帮助系统更好地解决时间相关的问题,提高系统的可靠性和稳定性。
时效处理的应用广泛,例如在操作系统中可以用于进行定时任务调度,在网络通信中可以用于超时检测,在数据库系统中可以用于定期检查数据库状态等。
金属学与热处理原理中的时效处理

金属学与热处理原理中的时效处理时效处理作为金属学与热处理原理中的一种重要工艺,广泛应用于诸多金属材料的制备与加工过程中。
它通过合理的时效参数设置,能够显著改善金属材料的力学性能与耐腐蚀性能,同时增强材料的整体结构稳定性。
本文将详细介绍时效处理的原理、工艺及其在金属学中的应用。
一、时效处理原理时效处理是指通过在高温下加热金属材料,使其过饱和固溶体中的析出相重新分布,形成更为稳定的强化相。
从而改变材料的晶粒结构,提高材料的强度、硬度和耐磨性能。
在时效处理过程中,主要通过以下几个步骤来实现:1. 固溶处理:将金属样品加热到高温区,使其形成过饱和固溶体。
过饱和固溶体具有较高的扩散速率,为后续析出相的形成提供了条件。
2. 快速冷却:将经过固溶处理的样品急冷至室温,以防止析出相的形成。
这一步骤非常关键,能够保持材料的均匀性和一定的过饱和度。
3. 时效处理:将冷却后的样品再次加热到较低的温度区域,保持一定的时间。
在时效处理过程中,过饱和固溶体中的溶质原子开始扩散聚集,形成纳米尺度的强化相。
4. 冷却:将时效处理后的样品冷却至室温,保持析出相的稳定性。
冷却过程中不应出现过快的降温速度,以免破坏析出相的结构。
时效处理的本质是通过对金属材料的热处理,改变其晶格结构和相组织,从而调控材料的性能。
二、时效处理的工艺时效处理的具体工艺参数根据不同的材料和要求而有所不同,通常包括时效温度、时效时间和冷却速率等。
1. 时效温度:时效温度是指进行时效处理时的加热温度。
不同材料和不同的强化相有着各自的最佳时效温度范围。
通过控制时效温度,可以控制强化相的粒径和分布,从而调节材料的力学性能。
2. 时效时间:时效时间是指在维持一定的时效温度下,样品所需要保持的时间。
时效时间与强化相的形成和生长速率密切相关。
通过合理选择时效时间,可以使强化相的分布均匀,并有效提高材料的强度和韧性。
3. 冷却速率:冷却速率指的是时效处理后的样品在冷却过程中的速度。
时效热处理的目的和原理
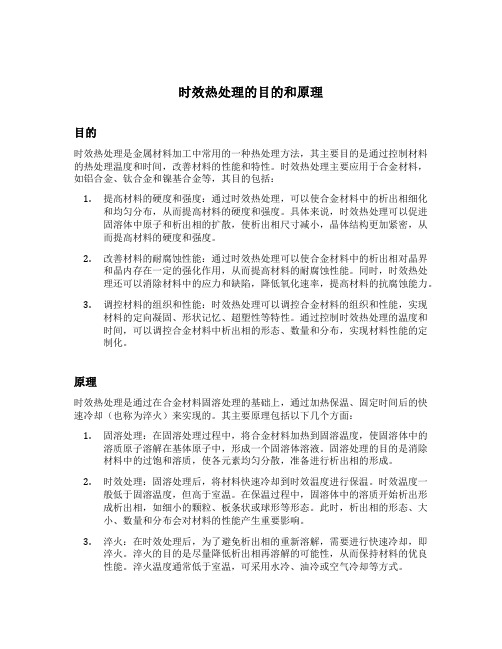
时效热处理的目的和原理目的时效热处理是金属材料加工中常用的一种热处理方法,其主要目的是通过控制材料的热处理温度和时间,改善材料的性能和特性。
时效热处理主要应用于合金材料,如铝合金、钛合金和镍基合金等,其目的包括:1.提高材料的硬度和强度:通过时效热处理,可以使合金材料中的析出相细化和均匀分布,从而提高材料的硬度和强度。
具体来说,时效热处理可以促进固溶体中原子和析出相的扩散,使析出相尺寸减小,晶体结构更加紧密,从而提高材料的硬度和强度。
2.改善材料的耐腐蚀性能:通过时效热处理可以使合金材料中的析出相对晶界和晶内存在一定的强化作用,从而提高材料的耐腐蚀性能。
同时,时效热处理还可以消除材料中的应力和缺陷,降低氧化速率,提高材料的抗腐蚀能力。
3.调控材料的组织和性能:时效热处理可以调控合金材料的组织和性能,实现材料的定向凝固、形状记忆、超塑性等特性。
通过控制时效热处理的温度和时间,可以调控合金材料中析出相的形态、数量和分布,实现材料性能的定制化。
原理时效热处理是通过在合金材料固溶处理的基础上,通过加热保温、固定时间后的快速冷却(也称为淬火)来实现的。
其主要原理包括以下几个方面:1.固溶处理:在固溶处理过程中,将合金材料加热到固溶温度,使固溶体中的溶质原子溶解在基体原子中,形成一个固溶体溶液。
固溶处理的目的是消除材料中的过饱和溶质,使各元素均匀分散,准备进行析出相的形成。
2.时效处理:固溶处理后,将材料快速冷却到时效温度进行保温。
时效温度一般低于固溶温度,但高于室温。
在保温过程中,固溶体中的溶质开始析出形成析出相,如细小的颗粒、板条状或球形等形态。
此时,析出相的形态、大小、数量和分布会对材料的性能产生重要影响。
3.淬火:在时效处理后,为了避免析出相的重新溶解,需要进行快速冷却,即淬火。
淬火的目的是尽量降低析出相再溶解的可能性,从而保持材料的优良性能。
淬火温度通常低于室温,可采用水冷、油冷或空气冷却等方式。
时效处理

时效处理 (1)固溶热处理: (1)热处理工艺中请问什么是人工时效? (3)什么是时效处理 (3)锻压:超塑成形 (3)预合金粉末与金刚石的扩散连接 (4)异种金属扩散连接技术研究 (7)时效处理金属结构件在铸造、焊接、锻压和机械切削加工过程中,由于热胀冷缩和机械力造成的变形,在工件内部产生残余应力,致使工件处于不稳定状态,降低工件的尺寸稳定性和机械物理性能,使工件在成品后使用过程中因残余应力的释放而产生变形和失效。
为消除残余应力,传统的工艺方法是采用自然时效和热时效。
自然时效是将工件长时间露天放置(一般长达六个月至一年左右),利用环境温度的不断变化和时间效应使残余应力释放。
热时效(TSR)工艺是目前广泛采用的传统机械加工方法,其原理是用炉窑将金属结构件加热到一定温度,保温后控制降温,达到消除残余应力的目的,可以保证加工精度和防止裂纹产生。
振动时效(VSR)工艺是一种可完全取代TSR和NSR的工艺,其原理是用振动消除残余应力,可达到TSR 工艺的同样效果,并在许多性能指标上超过TSR。
固溶热处理:将合金加热至高温单相区恒温保持,使过剩相充分溶速冷却,以得到过饱和固溶体的热处理工艺时效处理可分为自然时效和人工时效两种自然时效是将铸件置于露天场地半年以上,便其缓缓地发生形,从而使残余应力消除或减少,人工时效是将铸件加热到550~650℃进行去应力退火,它比自然时效节省时间,残余应力去除较为彻底.根据合金本性和用途确定采用何种时效方法。
高温下工作的铝合金适宜用人工时效,室温下工作的铝合金有些采用自然时效,有些必须人工时效。
从合金强化相上来分析,含有S相和CuAl2等相的合金,一般采用自然时效,而需要在高温下使用或为了提高合金的屈服强度时,就需要采用人工时效来强化。
比如LY11和LY12,40度以下自然时效可以得到高的强度和耐蚀性,对于150度以上工作的LY12和125-250度工作的LY6铆钉用合金则需要人时效。
铝合金欠时效,过时效国标

铝合金欠时效,过时效国标
在我们国家的工业生产中,铝合金材料的应用越来越广泛。
铝合金的时效处理是保证其性能的关键环节。
时效处理包括欠时效和过时效两种,那么这两种时效处理有哪些区别,如何满足国标要求,又会对铝合金产生哪些影响呢?
首先,我们来了解一下铝合金时效的基本概念。
时效处理是指在特定温度下,对铝合金进行一定时间的保温,以使其组织发生相应的变化,从而改善铝合金的性能。
其中,欠时效和过时效是两种常见的时效处理方式。
欠时效指的是铝合金在低于最佳时效温度下进行时效处理,这样会导致铝合金的力学性能不能充分提高,表现为强度较低。
而过时效则是铝合金在高于最佳时效温度下进行时效处理,可能导致铝合金的强度下降,塑性降低。
那么,铝合金过时效的国标要求是什么呢?根据我国相关标准,铝合金过时效的处理温度和时间都有明确的规定。
例如,针对Al-Mg-Si系铝合金,国标要求其过时效处理温度应在180℃左右,保温时间根据具体规格和要求来确定。
铝合金欠时效会影响其性能,如何应对呢?首先,要掌握合适的时效温度和时间,确保铝合金在最佳条件下进行时效处理。
其次,可以采用双重时效处理,即在较低温度下进行一次时效,然后在较高温度下进行第二次时效,以提高铝合金的性能。
最后,根据以上分析,我们提出以下提高铝合金时效质量的实用建议:
1.严格遵循国标要求,确保铝合金过时效处理的质量。
2.针对不同铝合金型号和用途,选择合适的时效处理参数。
3.加强生产过程的控制,确保时效处理的稳定性。
4.采用先进的检测手段,对时效处理后的铝合金进行性能检测,确保其质量达到要求。
铸铁件的时效处理及方法
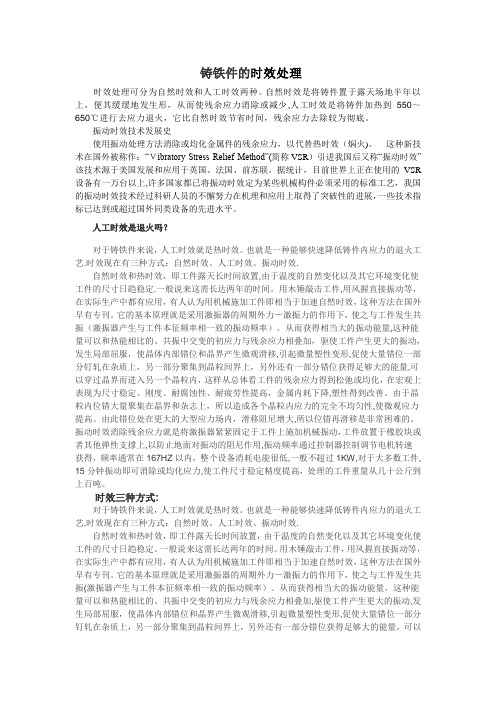
铸铁件的时效处理时效处理可分为自然时效和人工时效两种。
自然时效是将铸件置于露天场地半年以上,便其缓缓地发生形,从而使残余应力消除或减少,人工时效是将铸件加热到550~650℃进行去应力退火,它比自然时效节省时间,残余应力去除较为彻底。
振动时效技术发展史使用振动处理方法消除或均化金属件的残余应力,以代替热时效(焖火)。
这种新技术在国外被称作:“Vibratory Stress Relief Method”(简称VSR)引进我国后又称“振动时效”该技术源于美国发展和应用于英国、法国、前苏联。
据统计,目前世界上正在使用的VSR 设备有一万台以上,许多国家都已将振动时效定为某些机械构件必须采用的标准工艺,我国的振动时效技术经过科研人员的不懈努力在机理和应用上取得了突破性的进展,一些技术指标已达到或超过国外同类设备的先进水平。
人工时效是退火吗?对于铸铁件来说,人工时效就是热时效。
也就是一种能够快速降低铸件内应力的退火工艺.时效现在有三种方式:自然时效、人工时效、振动时效.自然时效和热时效,即工件露天长时间放置,由于温度的自然变化以及其它环境变化使工件的尺寸日趋稳定.一般说来这需长达两年的时间。
用木锤敲击工件,用风握直接振动等,在实际生产中都有应用,有人认为用机械施加工件即相当于加速自然时效,这种方法在国外早有专刊。
它的基本原理就是采用激振器的周期外力-激振力的作用下,使之与工件发生共振(激振器产生与工件本征频率相一致的振动频率)。
从而获得相当大的振动能量,这种能量可以和热能相比的、共振中交变的初应力与残余应力相叠加,驱使工件产生更大的振动,发生局部屈服,使晶体内部错位和晶界产生微观滑移,引起微量塑性变形,促使大量错位一部分钉轧在杂质上,另一部分聚集到晶粒间界上,另外还有一部分错位获得足够大的能量,可以穿过晶界而进入另一个晶粒内,这样从总体看工件的残余应力得到松弛或均化,在宏观上表现为尺寸稳定、刚度、耐腐蚀性、耐疲劳性提高,金属内耗下降,塑性得到改善。
时效处理

时效处理为了消除精密量具或模具、零件在长期使用中尺寸、形状发生变化,常在低温回火后(低温回火温度150-250℃)精加工前,把工件重新加热到100-150℃,保持5-20小时,这种为稳定精密制件质量的处理,称为时效。
对在低温或动载荷条件下的钢材构件进行时效处理,以消除残余应力,稳定钢材组织和尺寸,尤为重要。
时效处理:指合金工件经固溶处理,冷塑性变形或铸造,锻造后,在较高的温度放置或室温保持,其性能,形状,尺寸随时间而变化的热处理工艺。
若采用将工件加热到较高温度,并较时间进行时效处理的时效处理工艺,称为工时效处理,若将工件放置在室温或自然条件下长时间存放而发生的时效现象,称为自然时效处理。
时效处理的目的,消除工件的内应力,稳定组织和尺寸,改善机械性能等调质处理;hardening and tempering;thermal refining性质:金属材料热处理工艺之一。
材料在淬火后高温回火叫调质处理。
目的是使钢件有很高的韧性和足够的强度,具有综合的优良机械性能。
例如立轴、丝杠、齿轮等。
一般是在零件加工后进行,也可将粗坯调质后再进行机械加工。
冷隔cold lap cold shut与流纹是不一样的.流纹主要是因为喷涂过多产生的.也可能是金属流过的痕迹.冷隔却是两股或多股金属液在对流时未完全融合..冷紋:原因:熔湯前端的溫度太低,相疊時有痕跡.改善方法:檢查壁厚是否太薄(設計或制造),較薄的區域應直接充填.檢查形狀是否不易充填;距離太遠、封閉區域(如鳍片(fin) 、凸起) 、被阻擋區域、圓角太小等均不易充填.並注意是否有肋點或冷點.縮知充填時間.縮短充填時間的方法:…改變充填模式.提高模溫的方法:…提高熔湯溫度.檢查合金成分.加大逃氣道可能有用.加真空裝置可能有用.ADC12是日本标准牌号Si 10.5~11.5Fe 0.3~0.6Cu 3.0~3.5Mg 0.2~0.3Mn 0.3~0.5Zn 0.6~0.9Ni 0.2~0.5Sn ≤0.3Al 余量日本的ADC10及ADC12,基本上是用废旧铝再生的,日本还制订出废铝再生压铸铝合金的标准。
- 1、下载文档前请自行甄别文档内容的完整性,平台不提供额外的编辑、内容补充、找答案等附加服务。
- 2、"仅部分预览"的文档,不可在线预览部分如存在完整性等问题,可反馈申请退款(可完整预览的文档不适用该条件!)。
- 3、如文档侵犯您的权益,请联系客服反馈,我们会尽快为您处理(人工客服工作时间:9:00-18:30)。
时效处理1、时效处理的概念为了消除精密量具或模具、零件在长期使用中尺寸、形状发生变化,常在低温回火后(低温回火温度150-250℃)精加工前,把工件重新加热到100-150℃,保持5-20小时,这种为稳定精密制件质量的处理,称为时效。
对在低温或动载荷条件下的钢材构件进行时效处理,以消除残余应力,稳定钢材组织和尺寸,尤为重要。
时效处理:指合金工件经固溶处理,冷塑性变形或铸造,锻造后,在较高的温度放置或室温保持,其性能,形状,尺寸随时间而变化的热处理工艺。
若采用将工件加热到较高温度,并进行时效处理的时效处理工艺,称为人工时效处理,若将工件放置在室温或自然条件下长时间存放而发生的时效现象,称为自然时效处理。
时效处理的目的,消除工件的内应力,稳定组织和尺寸,改善机械性能等。
时效处理可分为自然时效和人工时效两种。
自然时效是将铸件置于露天场地半年以上,便其缓缓地发生形,从而使残余应力消除或减少,人工时效是将铸件加热到550~650℃进行去应力退火,它比自然时效节省时间,残余应力去除较为彻底。
金属结构件在铸造、焊接、锻压和机械切削加工过程中,由于热胀冷缩和机械力造成的变形,在工件内部产生残余应力,致使工件处于不稳定状态,降低工件的尺寸稳定性和机械物理性能,使工件在成品后使用过程中因残余应力的释放而产生变形和失效。
为消除残余应力,传统的工艺方法是采用自然时效和热时效。
自然时效是将工件长时间露天放置(一般长达六个月至一年左右),利用环境温度的不断变化和时间效应使残余应力释放。
热时效(TSR)工艺是目前广泛采用的传统机械加工方法,其原理是用炉窑将金属结构件加热到一定温度,保温后控制降温,达到消除残余应力的目的,可以保证加工精度和防止裂纹产生。
振动时效(VSR)工艺是一种可完全取代TSR和NSR的工艺,其原理是用振动消除残余应力,可达到TSR工艺的同样效果,并在许多性能指标上超过TSR。
将合金加热至高温单相区恒温保持,使过剩相充分溶速冷却,以得到过饱和固溶体的热处理工艺时效处理可分为自然时效和人工时效两种自然时效是将铸件置于露天场地半年以上,便其缓缓地发生形,从而使残余应力消除或减少,人工时效是将铸件加热到550~650℃进行去应力退火,它比自然时效节省时间,残余应力去除较为彻底。
超声波时效法用于对机械零件焊接修复部位进行消除残余应力和强化处理。
因此,超声波时效法在机械制造业和维护过程中具有广阔的应用前景。
超声波时效方法的特点:1.是目前最彻底消除残余应力的时效方法(各种时效方法消除残余应力的情况如下:振动时效230-55%、热时效40-80%、热时效40-80%、超声波时效80-100%。
2.用于消除局部残余应力,完全可替代热处理和振动时效等方法,且处理工艺简单,效果稳定可靠。
3.不受工件材质、形状、结构、钢板厚度、重量、场地之限制,特别是在施工现场、焊接过程和焊接修复时用于消除焊接应力更显灵活方便。
4.环保、节能、安全、无污染,施工现场使用更显灵活方便。
5.在焊接过程汇总边焊接超声处理可明显减少焊接变形。
6.一般只适用于对焊接应力的消除2、选用原则根据合金本性和用途确定采用何种时效方法。
高温下工作的铝合金适宜用人工时效,室温下工作的铝合金有些采用自然时效,有些必须人工时效。
从合金强化相上来分析,含有S相和CuAl2等相的合金,一般采用自然时效,而需要在高温下使用或为了提高合金的屈服强度时,就需要采用人工时效来强化。
比如LY11和LY12,40度以下自然时效可以得到高的强度和耐蚀性,对于150度以上工作的LY12和125-250度工作的LY6铆钉用合金则需要人时效。
含有主要强化相为MgSi,MgZn2的T相的合金,只有采用人工时效强化,才能达到它的最高强度。
将淬火后的金属工件置于室温或较高温度下保持适当时间,以提高金属强度的金属热处理工艺。
在机械生产中,为了稳定铸件尺寸,常将铸件在室温下长期放置,然后才进行切削加工。
这种措施也被称为时效。
但这种时效不属於金属热处理工艺。
20世纪初叶,德国工程师A.维尔姆研究硬铝时发现,这种合金淬火后硬度不高,但在室温下放置一段时间后,硬度便显着上升,这种现象后来被称为沉淀硬化。
这一发现在工程界引起了极大兴趣。
随后人们相继发现了一些可以采用时效处理进行强化的铝合金、铜合金和铁基合金,开创了一条与一般钢铁淬火强化有本质差异的新的强化途径——时效强化。
绝大多数进行时效强化的合金,原始组织都是由一种固溶体和某些金属化合物所组成。
固溶体的溶解度随温度的上升而增大。
在时效处理前进行淬火,就是为了在加热时使尽量多的溶质溶入固溶体,随后在快速冷却中溶解度虽然下降,但过剩的溶质来不及从固溶体中分析出来,而形成过饱和固溶体。
为达到这一目的而进行的淬火常称为固溶热处理。
经过长期反复研究证实,时效强化的实质是从过饱和固溶体中析出许多非常细小的沉淀物颗粒(一般是金属化合物,也可能是过饱和固溶体中的溶质原子在许多微小地区聚集),形成一些体积很小的溶质原子富集区。
在时效处理前进行固溶处理时,加热温度必须严格控制,以便使溶质原子能最大限度地固溶到固溶体中,同时又不致使合金发生熔化。
许多铝合金固溶处理加热温度容许的偏差只有5℃左右。
进行人工时效处理,必须严格控制加热温度和保温时间,才能得到比较理想的强化效果。
生产中有时采用分段时效,即先在室温或比室温稍高的温度下保温一段时间,然后在更高的温度下再保温一段时间。
这样作有时会得到较好的效果。
马氏体时效钢淬火时会发生组织转变,形成马氏体。
马氏体就是一种过饱和固溶体。
这种钢也可采用时效处理进行强化。
低碳钢冷态塑性变形后在室温下长期放置,强度提高,塑性降低,这种现象称为机械时效。
LY12CZ---十二号硬铝/淬火(自然时效)、LY12--十二号硬铝、C—淬火、Z—自然时效、碳钢的热处理符号:D--氮化、Y--油淬根据合金本性和用途确定采用何种时效方法。
高温下工作的铝合金适宜用人工时效,室温下工作的铝合金有些采用自然时效,有些必须人工时效。
从合金强化相上来分析,含有S相和CuAl2等相的合金,一般采用自然时效,而需要在高温下使用或为了提高合金的屈服强度时,就需要采用人工时效来强化。
比如LY11和LY12,40度以下自然时效可以得到高的强度和耐蚀性,对于150度以上工作的LY12和125-250度工作的LY6铆钉用合金则需要人时效。
含有主要强化相为MgSi,MgZn2的T相的合金,只有采用人工时效强化,才能达到它的最高强度。
对于一般铝合金,自然时效时,屈服强度稍低而耐蚀性较好,采用人时效时,合金屈服强度较高而伸长率和耐蚀性都降低。
对于铝-锌-镁-铜系合金入LC4则相反,当采用人工时效时,合金耐蚀性比自然时效好。
人工时效就是人为的方法,一般是加热或是冰冷处理消除或减小淬火后钢内的微观应力、机械加工残余应力,防止变形及开裂。
稳定组织以稳定零件形状及尺寸。
也叫稳定处理或稳定回火。
其方法是:将钢件加热到120-150摄氏度,或更低的温度(80-120度)长时间保温后(5-20小时)随炉或取出在空气中冷却。
时效温度一般均比低温回火要低或更低,保温时间要长或更长;与冰冷处理相比,效果虽不如冰冷处理,但操作简便、无需专门的冷处理设备、成本低、一般工厂均可进行;适用于处理各种量具、卡规、卡尺、样板等和与此类似要求的精密机械上的零件,低温时效在半精加工后、精加工前进行。
3、处理实例选用不同品种钢材作塑料模具,其化学成分和力学性能各不相同,因此制造工艺路线不同;同样,不同类型塑料模具钢采用的热处理工艺也是不同的。
本节主要介绍塑料模具的制造工艺路线和热处理工艺的特点。
一、塑料模具的制造工艺路线1.低碳钢及低碳合金钢制模具例如,20,20Cr,20CrMnTi等钢的工艺路线为:下料→锻造模坯→退火→机械粗加工→冷挤压成形→再结晶退火→机械精加工→渗碳→淬火、回火→研磨抛光→装配。
2.高合金渗碳钢制模具例如12CrNi3A,12CrNi4A钢的工艺路线为:下料→锻造模坯→正火并高温回火→机械粗加工→高温回火→精加工→渗碳→淬火、回火→研磨抛光→装配。
3.调质钢制模具例如,45,40Cr等钢的工艺路线为:下料→锻造模坯→退火→机械粗加工→调质→机械精加工→修整、抛光→装配。
4.碳素工具钢及合金工具钢制模具例如T7A~T10A,CrWMn,9SiCr等钢的工艺路线为:下料→锻成模坯→球化退火→机械粗加工→去应力退火→机械半精加工→机械精加工→淬火、回火→研磨抛光→装配。
5.预硬钢制模具例如5NiSiCa,3Cr2Mo(P20)等钢。
对于直接使用棒料加工的,因供货状态已进行了预硬化处理,可直接加工成形后抛光、装配。
对于要改锻成坯料后再加工成形的,其工艺路线为:下料→改锻→球化退火→刨或铣六面→预硬处理(34~42HRC)→机械粗加工→去应力退火→机械精加工→抛光→装配。
二、塑料模具的热处理特点(一)渗碳钢塑料模的热处理特点1.对于有高硬度、高耐磨性和高韧性要求的塑料模具,要选用渗碳钢来制造,并把渗碳、淬火和低温回火作为最终热处理。
2.对渗碳层的要求,一般渗碳层的厚度为~1.5mm,当压制含硬质填料的塑料时模具渗碳层厚度要求为~1.5mm,压制软性塑料时渗碳层厚度为~1.2mm。
渗碳层的含碳量为%~%为佳。
若采用碳、氮共渗,则耐磨性、耐腐蚀性、抗氧化、防粘性就更好。
3.渗碳温度一般在900~920℃,复杂型腔的小型模具可取840~860℃中温碳氮共渗。
渗碳保温时间为5~10h,具体应根据对渗层厚度的要求来选择。
渗碳工艺以采用分级渗碳工艺为宜,即高温阶段(900~920℃)以快速将碳渗入零件表层为主;中温阶段(820~840℃)以增加渗碳层厚度为主,这样在渗碳层内建立均匀合理的碳浓度梯度分布,便于直接淬火。
4.渗碳后的淬火工艺按钢种不同,渗碳后可分别采用:重新加热淬火;分级渗碳后直接淬火(如合金渗碳钢);中温碳氮共渗后直接淬火(如用工业纯铁或低碳钢冷挤压成形的小型精密模具);渗碳后空冷淬火(如高合金渗碳钢制造的大、中型模具)。
(二)淬硬钢塑料模的热处理1.形状比较复杂的模具,在粗加工以后即进行热处理,然后进行精加工,才能保证热处理时变形最小,对于精密模具,变形应小于%。
2.塑料模型腔表面要求十分严格,因此在淬火加热过程中要确保型腔表面不氧化、不脱碳、不侵蚀、不过热等。
应在保护气氛炉中或在严格脱氧后的盐浴炉中加热,若采用普通箱式电阻炉加热,应在模腔面上涂保护剂,同时要控制加热速度,冷却时应选择比较缓和的冷却介质,控制冷却速度,以避免在淬火过程中产生变形、开裂而报废。
一般以热浴淬火为佳,也可采用预冷淬火的方式。
3.淬火后应及时回火,回火温度要高于模具的工作温度,回火时间应充分,长短视模具材料和断面尺寸而定,但至少要在40~60min以上。