汽车球头销台架试验标准讲解
汽车转向节总成性能要求及台架试验方法
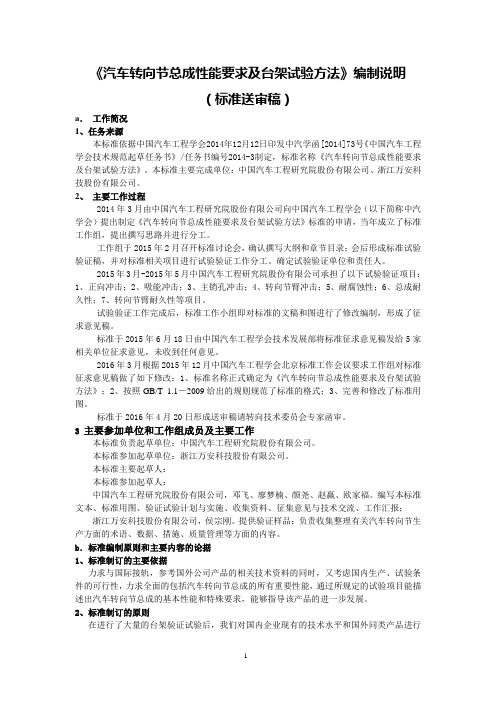
《汽车转向节总成性能要求及台架试验方法》编制说明(标准送审稿)a.工作简况1、任务来源本标准依据中国汽车工程学会2014年12月12日印发中汽学函[2014]73号《中国汽车工程学会技术规范起草任务书》/任务书编号2014-3制定,标准名称《汽车转向节总成性能要求及台架试验方法》。
本标准主要完成单位:中国汽车工程研究院股份有限公司、浙江万安科技股份有限公司。
2、主要工作过程2014年3月由中国汽车工程研究院股份有限公司向中国汽车工程学会(以下简称中汽学会)提出制定《汽车转向节总成性能要求及台架试验方法》标准的申请,当年成立了标准工作组,提出撰写思路并进行分工。
工作组于2015年2月召开标准讨论会,确认撰写大纲和章节目录;会后形成标准试验验证稿,并对标准相关项目进行试验验证工作分工、确定试验验证单位和责任人。
2015年3月-2015年5月中国汽车工程研究院股份有限公司承担了以下试验验证项目:1、正向冲击;2、吸能冲击;3、主销孔冲击;4、转向节臂冲击;5、耐腐蚀性;6、总成耐久性;7、转向节臂耐久性等项目。
试验验证工作完成后,标准工作小组即对标准的文稿和图进行了修改编制,形成了征求意见稿。
标准于2015年6月18日由中国汽车工程学会技术发展部将标准征求意见稿发给5家相关单位征求意见,未收到任何意见。
2016年3月根据2015年12月中国汽车工程学会北京标准工作会议要求工作组对标准征求意见稿做了如下修改:1、标准名称正式确定为《汽车转向节总成性能要求及台架试验方法》;2、按照GB/T 1.1-2009给出的规则规范了标准的格式;3、完善和修改了标准用图。
标准于2016年4月20日形成送审稿请转向技术委员会专家函审。
3 主要参加单位和工作组成员及主要工作本标准负责起草单位:中国汽车工程研究院股份有限公司。
本标准参加起草单位:浙江万安科技股份有限公司。
本标准主要起草人:本标准参加起草人:中国汽车工程研究院股份有限公司,邓飞、廖梦楠、颜尧、赵赢、欧家福。
球头实验方法及技术要求
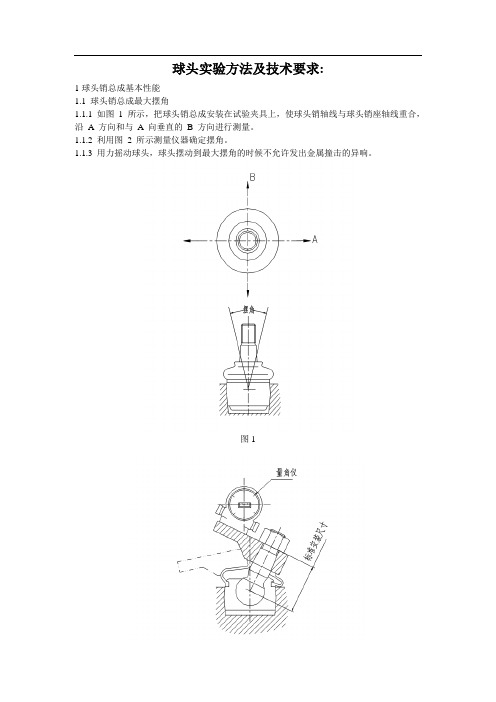
球头实验方法及技术要求:1球头销总成基本性能1.1 球头销总成最大摆角1.1.1 如图1 所示,把球头销总成安装在试验夹具上,使球头销轴线与球头销座轴线重合,沿A 方向和与A 向垂直的 B 方向进行测量。
1.1.2 利用图2 所示测量仪器确定摆角。
1.1.3 用力摇动球头,球头摆动到最大摆角的时候不允许发出金属撞击的异响。
图1图21.2. 球头销总成转动力矩1.2.1 如图3 所示,把球头销总成安装在试验夹具上,固定时应保证安装尺寸尽量与实车一致。
1.2.2 如图4 所示,试验前先使球头销沿任意方向往复摆动五次,摆动角度为最大摆角。
然后使球头销沿任意方向转动360°,再沿相反方向回到初始位置,重复共进行五次。
1.2.3 测量转动力矩时,可利用扭力计或其他任何能满足1.2.4 中规定的测量要求的测试仪器测量力矩。
1.2.4 如图4所示,将球头销轴线处于与球销座轴线重合的位置,以(3~18)°/s的转动速度在±40°范围内或在汽车最大转向角之间转动球销,同时记录转动力矩与转动角度的关系曲线。
1.2.5 使用扭力扳手测量时,可取稳定的数值作为均值。
图3图41.3 球头销总成摆动力矩1.3.1 如图3 所示,把球头销总成安装在试验夹具上,固定时应保证安装尺寸尽量与实车一致。
1.3.2 如图4 所示,试验前先使球头销沿任意方向往复摆动五次,摆动角度为最大摆角。
然后使球头销沿任意方向转动360°,再沿相反方向回到初始位置,重复进行五次。
1.3.3 测量摆动力矩时,可利用拉力计或其他任何能满足1.3.4 中规定的测量要求的测试仪器测量力矩。
1.3.4 如图4所示,使球头销可轴线处于与球头销座轴线重合的位置,以(3~18)°/s的摆动速度沿A向或与A向夹角为90°的B方向,在±20°范围内或在汽车最大摆角之间摆动球销,同时记录摆动力矩与摆动角度的关系曲线。
发动机台架试验解说
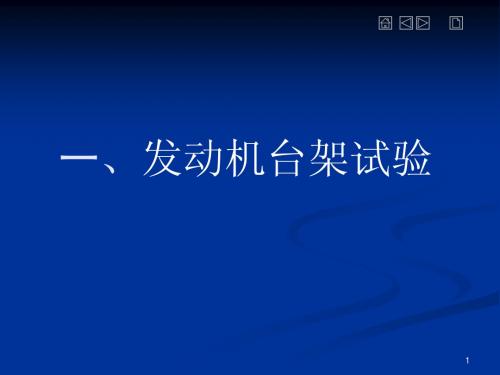
18
实验注意事项
实验时,负荷调整要平稳,供油拉杆调整 要缓慢,避免负荷大起大落。 实验时要注意安全。
19
20
六、柴油机负荷特性实验数据及数据处理表格
21
三、柴油机速度特性实验
22
1、实验目的
掌握测取柴油机速度特性的实验方法。
掌握测取柴油机速度特性所用仪器设 备的使用与操作。 根据试验结果,分析柴油机的性能。
32
2、实验原理
汽油机全负荷速度特性是汽油机节气门 位置处于最大时汽油机性能参数随转速的变 化关系,也称为外特性,如图1示。它表示汽 油机所能达到的最高性能。由此特性可确定 它所能达到的最大功率和最大扭矩以及相应 的转速,是标定和选择汽油机的主要依据。 测试汽油机外特性的方法是固定汽油机的油 门为最大位置,测量性能参数(Ttq、be、Pe 等)随转速的变化关系。
用此方法逐步测取80%nH,70%nH,60%nH, 50%nH,40%nH 下的各主要性能参数,直到 最低稳定转速。 用减少负荷的方法,使柴油机转速按上述转速点 上升,并分别测取和主要参数,记录下来。实验 完毕松油门固定专用夹具。上述方法测取的是全 负荷速度特性。 部分负荷速度特性的测取是方法是:调节油门, 使转速升至A%nH ,调节水力测功器手轮,使 负荷在额定负荷下,待稳定后装油门紧固夹具。 测取各主要性能参数并记录下来。按5、6项方 法测取其它工况点各主要性能参数。 按操作步骤完成试验后停机。清洁保养设备。
6135ZG柴油机一台; Y300水力测功器一台; SYZZ转速──油耗自动测量仪一套;
温度表、气压
检查仪器、仪表工作正常,接通燃油、冷却水通断 阀。 按常规启动柴油机,暖机,当油温、水温达到规定 值时,加载试验。 调节发动机油门,使其转速逐渐升至额定转速 (1500rpm) ,调节水力测功器手轮,使负荷逐渐 增加至额定负荷(Neh=125.8KW时,负荷F= 559.1)。反复调节油门和测功器手轮,使其转速 和负荷稳定在额定工况点上。用专用夹具固定油门。 测量记录转速n、负荷F、耗油时间t、单位时间 的耗油量M、烟度等。 调节水力测功器手轮,使发动机转速缓慢地下降到 某一定值(90%nH ),在新的转速和扭矩下达到 新平衡后,测取各主要性能参数并记录下来。 27
汽车转向节总成性能要求及台架试验方法-中国汽车工程学会标准

《汽车转向节总成性能要求及台架试验方法》编制说明(标准送审稿)a.工作简况1、任务来源本标准依据中国汽车工程学会2014年12月12日印发中汽学函[2014]73号《中国汽车工程学会技术规范起草任务书》/任务书编号2014-3制定,标准名称《汽车转向节总成性能要求及台架试验方法》。
本标准主要完成单位:中国汽车工程研究院股份有限公司、浙江万安科技股份有限公司。
2、主要工作过程2014年3月由中国汽车工程研究院股份有限公司向中国汽车工程学会(以下简称中汽学会)提出制定《汽车转向节总成性能要求及台架试验方法》标准的申请,当年成立了标准工作组,提出撰写思路并进行分工。
工作组于2015年2月召开标准讨论会,确认撰写大纲和章节目录;会后形成标准试验验证稿,并对标准相关项目进行试验验证工作分工、确定试验验证单位和责任人。
2015年3月-2015年5月中国汽车工程研究院股份有限公司承担了以下试验验证项目:1、正向冲击;2、吸能冲击;3、主销孔冲击;4、转向节臂冲击;5、耐腐蚀性;6、总成耐久性;7、转向节臂耐久性等项目。
试验验证工作完成后,标准工作小组即对标准的文稿和图进行了修改编制,形成了征求意见稿。
标准于2015年6月18日由中国汽车工程学会技术发展部将标准征求意见稿发给5家相关单位征求意见,未收到任何意见。
2016年3月根据2015年12月中国汽车工程学会北京标准工作会议要求工作组对标准征求意见稿做了如下修改:1、标准名称正式确定为《汽车转向节总成性能要求及台架试验方法》;2、按照GB/T 1.1-2009给出的规则规范了标准的格式;3、完善和修改了标准用图。
标准于2016年4月20日形成送审稿请转向技术委员会专家函审。
3 主要参加单位和工作组成员及主要工作本标准负责起草单位:中国汽车工程研究院股份有限公司。
本标准参加起草单位:浙江万安科技股份有限公司。
本标准主要起草人:本标准参加起草人:中国汽车工程研究院股份有限公司,邓飞、廖梦楠、颜尧、赵赢、欧家福。
QC T 304-1999汽车转向拉杆接头总成台架试验方法
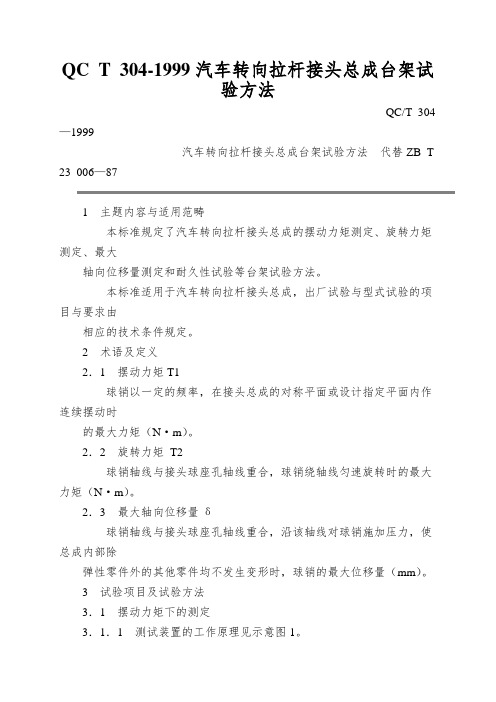
QC T 304-1999汽车转向拉杆接头总成台架试验方法QC/T 304—1999汽车转向拉杆接头总成台架试验方法代替ZB T 23 006—871主题内容与适用范畴本标准规定了汽车转向拉杆接头总成的摆动力矩测定、旋转力矩测定、最大轴向位移量测定和耐久性试验等台架试验方法。
本标准适用于汽车转向拉杆接头总成,出厂试验与型式试验的项目与要求由相应的技术条件规定。
2术语及定义2.1摆动力矩T1球销以一定的频率,在接头总成的对称平面或设计指定平面内作连续摆动时的最大力矩(N·m)。
2.2旋转力矩T2球销轴线与接头球座孔轴线重合,球销绕轴线匀速旋转时的最大力矩(N·m)。
2.3最大轴向位移量δ球销轴线与接头球座孔轴线重合,沿该轴线对球销施加压力,使总成内部除弹性零件外的其他零件均不发生变形时,球销的最大位移量(mm)。
3试验项目及试验方法3.1摆动力矩下的测定3.1.1测试装置的工作原理见示意图1。
3.1.2试验条件3.1.2.1环境温度:常温。
3.1.2.2测试仪器精度不低于1%。
3.1.3测试样品许多于3件。
3.1.4试验程序3.1.4.1测试前拆除总成的防尘装置。
3.1.4.2向总成内注满规定牌号的润滑脂。
3.1.4.3使球销处于接头总成的对称平面或设计指定平面内,以4~6min-1的频率连续摆动,摆动角为设计值的80%~90%。
3.1.4.4测试时球销先往复摆动5次再记录T1值,并运算5次测试结果的均值。
3.2旋转力矩T2的测定。
3.2.1测试装置的工作原理见示意图2。
3.2.2试验条件3.2.2.1环境温度:常温。
3.2.2.2测试仪器精度不低于1%。
3.2.3测试样品许多于3件。
3.2.4试验程序3.2.4.1测试前拆除总成的防尘装置。
3.2.4.2向总成内注满规定牌号的润滑脂。
3.2.4.3使球销轴线与接头球座孔轴线重合,球销以4~6r/min的转速绕轴线匀速旋转。
3.2.2.4测试时球销先旋转5圈再记录T2值,并运算5次测试结果的均值。
F5211车辆悬挂(完全)台架疲劳试验(块曲线)
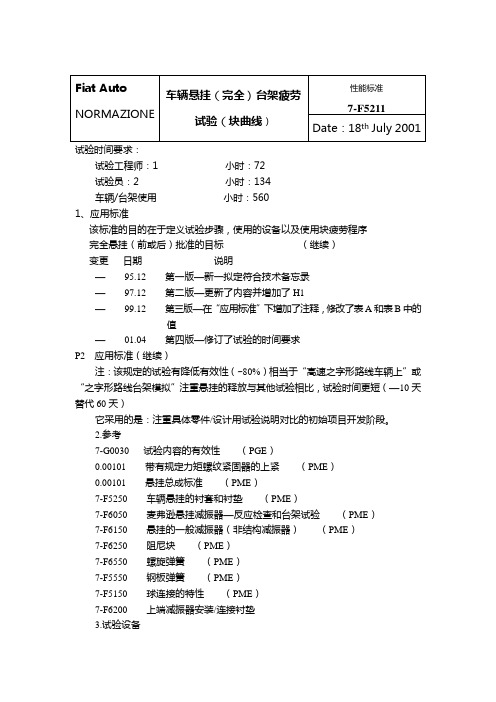
试验时间要求:试验工程师:1 小时:72试验员:2 小时:134车辆/台架使用小时:5601、应用标准该标准的目的在于定义试验步骤,使用的设备以及使用块疲劳程序完全悬挂(前或后)批准的目标(继续)变更日期说明—95.12 第一版—新一拟定符合技术备忘录—97.12 第二版—更新了内容并增加了H1—99.12 第三版—在“应用标准”下增加了注释,修改了表A和表B中的值—01.04 第四版—修订了试验的时间要求P2 应用标准(继续)注:该规定的试验有降低有效性(~80%)相当于“高速之字形路线车辆上”或“之字形路线台架模拟”注重悬挂的释放与其他试验相比,试验时间更短(—10天替代60天)它采用的是:注重具体零件/设计用试验说明对比的初始项目开发阶段。
2.参考7-G0030 试验内容的有效性(PGE)0.00101 带有规定力矩螺纹紧固器的上紧(PME)0.00101 悬挂总成标准(PME)7-F5250 车辆悬挂的衬套和衬垫(PME)7-F6050 麦弗逊悬挂减振器—反应检查和台架试验(PME)7-F6150 悬挂的一般减振器(非结构减振器)(PME)7-F6250 阻尼块(PME)7-F6550 螺旋弹簧(PME)7-F5550 钢板弹簧(PME)7-F5150 球连接的特性(PME)7-F6200 上端减振器安装/连接衬垫3.试验设备●三轴疲劳试验台,MTS型完全用控制电器●T-RACMTS型控制信号管理的编程器●专用的486计算机●车辆底盘模型,模拟悬挂连接或者(如果是严格目的)车身的部分●6频道记录仪注:可以用相同的设备替代,但其特性必须等于或超过所替设备的性能P4 5 试验零件的重要性/有效性评价试验有效性的零件的权及特性零件类型有效性%(A) 权影响试验有效性零件主要特性最小制制造等级有效0.09 横架,底盘子材料、尺寸 C有效0.09材料、尺寸 C有效0.05 完全支柱材料、尺寸 C有效0.05 减振器材料、性能 C有效0.09 阻尼块材料、性能 C有效0.09 衬套材料、性能 C有效0.09 稳定杆材料、性能 C有效0.05 球连接材料、性能 C有效0.05 衬垫材料、性能 C有效0.09 支柱,转向横拉杆材料、性能 C有效0.09 减振器连接衬垫材料、性能 C有效0.08 螺旋弹簧、钢板弹簧材料、性能 C有效0.09 螺纹紧固器材料 C试验零件的有效位(%)=∑(A×B)=注:对于每一个零件,标准7-G0030中指明了评价三个不同等级的有效性%P5 6 基本操作6.1 得到设计技术文件(轴上重量、最大轨迹、悬挂移动、图纸或螺纹连接的标准上紧力矩)最新的总成图,并在试验内容名称中输入这些数据。
汽车发动机台架标定全程讲解

汽车发动机台架标定全程讲解概述:发动机台架标定作为ECU标定的第一步,通过进气模式、扭矩模型、喷油点火等标定来最大程度的发挥发动机的性能,是整车标定的基础。
一.台架标定核心工作45天:●VVT选择●点火角标定●温度模型标定●扭矩模型标定●VVT VE标定●爆震控制●外特性●万有特性二:标定手段●控制油门:PUMA设备直接调节.●控制发动机转速:PUMA设备直接调节.●控制平均缸内压力:PUMA工具可设置油门开度为100%,即可通过调节标定改变缸内压力.●控制点火角:即可通过设置SprkAdvSlewValue改变点火提前角度数.●控制空燃比:通过设置FUEL.SlewValue改变点火提前角度数.●控制VVT开度:设置Intk_DsrdPstn.mode=1即可.三.发动机改造及台架搭建:2天●4个进气歧管温度热电偶、4个排气歧管热电偶、1个催化器中心热电偶.●进气压力传感器(发动机自带)、空滤前压力传感器、节气门前压力传感器、排气背压传感器.●油耗分析仪、空燃比检测仪(ES630).●开发电脑、ES590 592.●燃烧分析仪,缸压信号.●示波器采集58X,凸轮轴信号、喷油信号、点火信号、爆震传感器信号.●测功机、油门踏板和PUMA设备.●废气分析仪.●台架搭建:线束改造、发动机安放.四:数据准备:0.5天●Engine dyno disable function 因在台架上进行试验,缺少整车上的必要线束、传感器等,为保证正常标定,需关闭ECU的部分诊断功能.●关闭误报的各种EOBD故障码.●关闭闭环控制长期自学习值.●关闭碳罐控制.●COT 关闭.●PE关闭.●DFCO关闭.●关闭失火诊断.●关闭Baro预测.●设置VVT开度.五:台架标定:1.1第一次外特性和信号一致性检查目的:●检验原始发动机是否接近工程目标●检查4缸一致性方法:●根据扭矩特性,选择标定最佳VVT开度.●根据扭矩特性,选择最佳空燃比.●根据扭矩特性,选择最优点火角.●节气门全开工况,从1200rpm开始,每隔400rpm,稳定一定时间(如15S)采数,直到6000rpm.数据处理:●根据外特性数据,作出最大扭矩、最大功率、最小比油耗值曲线1.2各缸排温一致性检查:通过对各缸排温温度在WOT工况下对比排温偏差。
球头销试验大纲car-反馈-101009
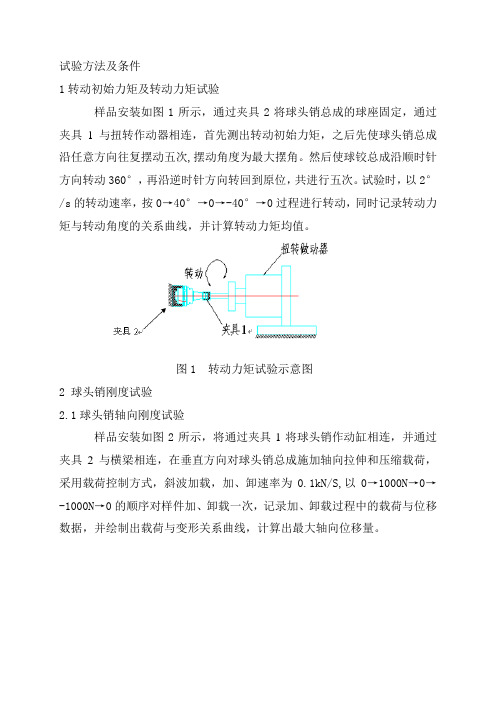
试验方法及条件1转动初始力矩及转动力矩试验样品安装如图1所示,通过夹具2将球头销总成的球座固定,通过夹具1与扭转作动器相连,首先测出转动初始力矩,之后先使球头销总成沿任意方向往复摆动五次,摆动角度为最大摆角。
然后使球铰总成沿顺时针方向转动360°,再沿逆时针方向转回到原位,共进行五次。
试验时,以2°/s的转动速率,按0→40°→0→-40°→0过程进行转动,同时记录转动力矩与转动角度的关系曲线,并计算转动力矩均值。
图1 转动力矩试验示意图2 球头销刚度试验2.1球头销轴向刚度试验样品安装如图2所示,将通过夹具1将球头销作动缸相连,并通过夹具2与横梁相连,在垂直方向对球头销总成施加轴向拉伸和压缩载荷,采用载荷控制方式,斜波加载,加、卸速率为0.1kN/S,以0→1000N→0→-1000N→0的顺序对样件加、卸载一次,记录加、卸载过程中的载荷与位移数据,并绘制出载荷与变形关系曲线,计算出最大轴向位移量。
图2 球头销轴向刚度试验示意图2.2 球头销径向刚度试验样品安装如图3所示,将通过夹具2将球头销球座与作动器相连,并通过夹具1将球头销固定,在径向对球头销总成施加径向拉伸和压缩载荷,采用载荷控制方式,斜波加载,加、卸速率为0.1kN/S,以0N→3000N→0N →-3000N→0N的顺序对样件加、卸载一次,记录加、卸载过程中的载荷与位移数据,并绘制出载荷与变形关系曲线,计算出最大径向位移量。
图3 球头销径向刚度试验示意图3 动态力矩特性样品安装如图4所示,通过夹具2将球头销总成的球座固定,通过夹具1与扭转作动器相连,先使球头销总成沿任意方向往复摆动五次,摆动角度为最大摆角,然后使球头销总成沿任意方向转动五次,最后将球头销处于中间位置,试验时,转动角度为±5°,转动频率从0.5慢慢增加到15Hz,记录力矩与频率关系曲线。
图4 动态力矩特性试验示意图4 球头销总成拉伸和挤压强度试验样品安装如图5所示,将通过夹具1将球头销作动缸相连,并通过夹具2与横梁相连,分别对球头销施加轴向拉伸和压缩载荷,采用位移控制方式,斜波加载,加载速率为0.1mm/S,直至球头销总成破坏或载荷达到100kN时试验终止,记录载荷与变形关系曲线;之后在曲线中找出最大载荷及破坏载荷。
- 1、下载文档前请自行甄别文档内容的完整性,平台不提供额外的编辑、内容补充、找答案等附加服务。
- 2、"仅部分预览"的文档,不可在线预览部分如存在完整性等问题,可反馈申请退款(可完整预览的文档不适用该条件!)。
- 3、如文档侵犯您的权益,请联系客服反馈,我们会尽快为您处理(人工客服工作时间:9:00-18:30)。
前言本标准以符合国家标准和行业标准为前提,在立足市场需求和产品性能的实际情况下指定的。
同时在格式和内容编排上均符合GB/T1.1-2000和GB/T1.2-2002规定。
本标准由XXXX机械有限公司提出本标准由XXXX机械有限公司归口本标准起草单位:XXXX机械有限公司标准起草人:XXX汽车球头销台架试验标准1 范围本标准规定了XX公司悬架使用的球销节(以下简称“球销总成”)的有关台架试验的方法和技术要求。
本标准适用于XX公司的所有汽车悬架球销总成。
2 规范性引用文件下列文件中的条款通过标准的引用而成为本标准的条款。
凡是注日期的引用文件,其随后的修改单(不包括勘误的内容)或修订版均不适合与本标准,然而,鼓励根据本标准达成协议的各方研究是否可以使用这些文件的最新版本,凡是不注日期的引用文件,其最新版本适用用本标准。
GB/T 7762-2003 硫化橡胶或热塑性橡胶耐臭氧龟裂静态拉伸试验JIS K 6301 硫化橡胶的物理试验方法3 目的本标准的目的是使球销总成的性能、强度和耐久性试验的试验方法标准化,以便得到评定质量的统一方法。
4 试验种类(1)摆角试验(2)力矩试验(3)刚度试验(4)挤压和拉伸强度试验(5)球头销静态强度试验(6)疲劳强度试验(7)工作温度下的耐磨持久性试验(8)高温下的耐磨持久试验(9)耐泥水持久性试验(10)防尘罩耐臭氧试验(11)防尘罩低温试验(12)防尘罩耐热性试验(13)防尘罩拉伸强度试验5 试验的一般条件试验条件一般适用于上面列举的所有试验,内容如下;(1)除非另有规定,试验应在常温常压下进行;(2)试验件应固定在刚度足够大的装置上,这样才不会消弱试验目的;(3)安装夹具的形状应不影响试验目的;6 球销总成试验方法6.1 摆角试验这个试验是测量球销的工作摆角,按如下方法进行6.1.1 试验装置如图1所示,把销总成安装在试验夹具上6.1.2 试验条件测量方向:如图1所示,使球头销铅垂直立,沿A方向和A方向垂直的B方向进行测量。
.图16.1.3 试验步骤利用如图2所示测量仪器确定摆角。
摆角是最大可以摆动的角度,在这个角度范围内,球头销不与任何零件相抵触图26.1.4 测量项目和记录(见图3)摆角是机械上能摆动的角度6.2 力矩试验该试验是用来测试球销总成转动和摆动力矩,其方法如下。
6.2.1如图3所示,把球销总成安装于夹具上,固定时应保证安装防尘罩的公称尺寸,利用扭力计或其它任何能满足6.2.2规定的测量要求的测量仪器测量力矩。
注:球销总成和夹具的配合公差请具体协商确定图3图46.2.2 试验条件(表1)测量项目转向力矩(N·m)摆动力矩(N·m)测量方法在±40°范围内或在最大转向角度之间往复运动,转动时应使球头销铅垂向上,如图3所示根据实际摆动方向,测量摆动角度,摆动角度根据实际工作角度确定实车上作用的静荷载通常不加载静载荷进行试验,如有必要加载,需要双方协定测量速度3(°)/s~18(°)/s气温一般在常温常压下进行试验,如有必要,也可在低温(-40℃~30℃)和高温(+70℃及其以上)下进行试验。
(需要在恒温箱内放置24小时后进行试验)注:当对车轮施加静载荷时,在球销总成上便施加了轴向的拉伸或压缩载荷表2球销间隙力矩对照表球直径种类轴向间隙轴向加载力径向间隙径向加载力旋转和摆动力矩启动力矩23 1 0.1±4000.15±2500 0.5~3 ≤2 0.15 0.325 1 0.12±10000.2±3000 1~4 ≤2 0.15 0.327 1 0.12±10000.25±4000 1~5 ≤2 0.15 0.3530 1 0.15±14000.28±5000 1~5 ≤2 0.2 0.3532 1 0.15±14000.28±5000 1~6 ≤2 0.2 0.3535 1 0.15±20000.32±6000 1.5~6 ≤2 0.2 0.440 1 0.15±30000.35±9000 2~10 ≤2 0.2 0.456.2.3 试验步骤测量前使球头销摆动到最大角度五次和五次正、反向旋转360°。
然后把球头销时效24小时以后测量启动力矩和工作力矩。
接着又使球头销摆动到最大摆角五次和正、反向转动360°五次。
然后测量启动力矩和工作力矩。
6.2.4 测量项目和记录a)与6.2.2有关(测量方法和测量速度)的试验条件;b)启动力矩-摆动曲线图5(注1)c)启动力矩;d)工作力矩最大、最小值和的平均值=[(最大值+最小值)/2](注2)注1:当从扭力扳手上直读取力矩值时,可省略该项测量。
注2:使用扭力扳手测量时,可取稳定的数据作为平均值,而最大、最小值的测量可以省略图5 力矩-角度曲线6.2.5 测量结果判定依据启动力矩:满足表2规定力矩转动力矩:满足表2规定力矩6.3 刚度试验进行该试验测试球销总成的刚度,步骤和方法如下:6.3.1 试验装置如图6所示,把球销总成安装在试验夹具上。
注:球销总成和夹具的配合公差请具体协商确定图66.3.2 试验条件加载方向,使球头销铅垂向上,在轴向与轴向垂直的方向对球头销施加拉伸和压缩载荷(力的轴线通过球头销中心),直至规定的表二规定的应力值。
毅200N/s的速度施加力。
6.3.3 试验步骤(a)试验件组装后放置24小时以上;(b)在加载到规定的载荷值一个循环后,在施加规定的拉伸和压缩静载荷,然后测量球头销的位移。
(要求夹具及测量系统的总刚度1*E6N/mm以上,否则需要先测台架系统包括动系统刚度,再测量球座在台架上的测量刚度,然后再计算球座实际刚度时将台架的影响出去)6.3.4测量项目和记录(a)规定荷载和位移值(b)荷载-位移曲线(图7)轴向力:参见表2规定力值,轴向间隙≤表2规定对应间隙径向力:参见表2规定力值,轴向间隙≤表2规定对应间隙注:特殊要求车型刚度试验要求按双方协定确商图76.4 拉脱和压脱试验该试验是测试球壳或球壳外端部的破坏强度,其方法如下:6.4.1 试验装置如图8所示,安装球销总成到试验夹具上。
图8(a)加载方向:挤压和拉伸方向(挤压根据实际结构选用);(b)载荷:从0到破坏载荷(N)6.4.3 试验步骤安装球销总成到试验夹具上并对球头销施加载荷。
试验夹具的材料、硬度和拧紧螺母的力矩最好与有关各方协商,因为它们都可能影响试验结果6.4.4 测量项目和记录(a)载荷-位移曲线(见图9)图9 载荷-位移曲线(b)最大载荷(挤压和拉伸)(c)破坏情况6.4.5 判定标准最大拉伸载荷:≥25KN(可双方协商确定)最大挤压载荷由双方协商确定6.5 球头销的静态刚度试验该试验是测试球销总成球头销在与其曲线垂直方向上的强度,其方法如下:6.5.1 试验装置如图10所示,把球头销安装于试验夹具上(安装节目应完全和球销总成在整车上实际的安装情况完全相同,推荐使用实际的转向节安装)图106.5.2 试验条件(a)加载方向:与球头销的轴线相垂直的方向;(b)荷载:从0到最大荷载(N),均速加载,每秒200N递加。
6.5.3 试验步骤把球头销固定在夹具上,沿与轴线相垂直的方向加荷载(载荷与球头销中的偏置距离和实际整车情况相吻合)。
试验夹具的材料、硬度、和拧紧螺母的力矩最好与相关个方相互协商,因为他们都可能影响试验结果;6.5.4 测量项目和记录(a)荷载-位移曲线(见图11)图11(b)屈服荷载(c)最大荷载和位置(d)变形和破坏情况6.6 疲劳强度试验该试验是测试球座和球销总成的球头销的疲劳强度,其方法如下:6.6.1 试验装置如图12所示,安装球销总成到试验夹具上,然而安装角度应按有关双方协议要求而定。
图126.6.2 试验条件(a)重复载荷(b)加载方向与球头销的轴线相垂直(球销总成),与球头销的轴线相重合(球销总成)(C)重复速度:3Hz~15Hz(d)试验循环次数规定的循环数,但对于最小荷载应为106次以上。
6.6.3 试验步骤紧固球销总成与试验夹具上并对球头销施加重复载荷。
安装球头销的试验夹具最好与实车有同样的硬度的同种材质制造,并且如果更换时,应和球销总成一起同时更换。
6.6.4 测量项目与记录(a)在6.6.2中规定的试验条件(b)荷载-循环次数曲线(见图13)图13 (c)断裂的部分及断裂性质;(d)可能出现的任何其它异常情况。
6.7 工作温度下耐磨持久性试验该试验是测试球销总成磨蚀的耐久性,其方法如下;6.7.1 试验装置如图14所示,安装球销总成到试验夹具上。
图146.7.2 试验条件(a)摆角±20°或车辆设计最大摆角(撞击回弹和转向角度)的80%或以上;(如有方向性,摆动方向应选取实际球销的工作方向)(b)摆动重复速度:1Hz~3Hz:(c)转向角度:±40°或车辆最大转向角度的80%或以上:(d)转动重复速度:0.3Hz~1Hz:(e)荷载与有关双方协商确定;(f)试验循环次数:摆动次数为106次或以上6.7.3 试验步骤(a)给定球销总成摆角、转动角度和荷载;(b)在6.7.2中有关试验条件的范围内的某个不变条件下进行试验;(c)由于试验条件不同,球销总成可能会发热。
因此必须给定冷却方法(空气冷却等)或停止时间间隔6.7.4 测量项目和记录(a)在6.7.2中规定的试验条件(b)在6.2中规定的初始的和试验后的力矩(c)在6.3中规定的初始的和试验后的刚度和自由行程;(d)在试验完成后,拆下球销总成并检查球座和球头销的磨损程度,证实已密封了适当的锂基脂;(e)可能出现的其它异常情况。
6.7.5 在做耐磨持久性试验前进行力矩试验。
耐磨持久性试验后放置24小时后进行力矩试验,试验后需保留40%的力矩6.8高温下的耐磨持久性试验该试验是测试球销总成在高温下磨蚀的耐久性;其方法如下:6.8.1 试验装置如 6.7.16.8.2 试验条件(a)试验温度:80℃需进行散热,防止工作面温度过高(b)摆角±10°或车辆设计最大摆角(撞击回弹和转向角度)的40%或以上;(如有方向性,摆动方向应选取实际球销的工作方向)(c)摆动重复速度:1Hz~3Hz:(d)转向角度:±15°或车辆最大转向角度的40%或以上(e)转动0.3Hz~1.5Hz:(f)荷载与有关双方协商确定(g)试验循环次数30万次以上。
6.8.3试验步骤(a)给定球销总成摆角、转动角度和荷载;(b)在6.7.2中的有关试验条件的范围内的某个不变条件下进行试验;(c)由于试验条件不同,球销总成可能会发热。