刀具磨损破损和刀具耐用度PPT
第6章 刀具磨损和刀具耐用度
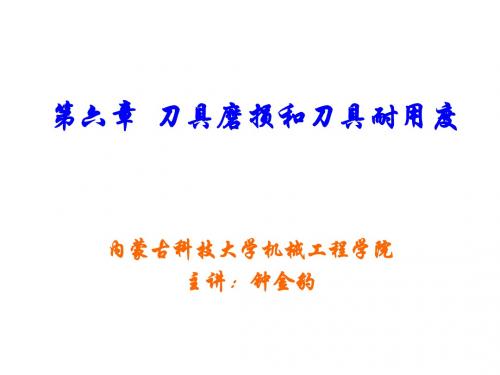
(vc3 、 T3)…各点。可发现,在一定切削速度范围内, 这
些点基本上在一条直线上。
c 1> c 2> c 3> c 4
VB
T1
T2 T
T3
T4
不同vc时的刀具磨损曲线
( ln ln ln ln
1 2 3 4
c 1,T1 )
(
c 2,T2 )
(
c 3,T3 )
ln
(
c 4,T4 )
lnT1
lnT2 lnT
14
切削速度对刀具磨损强度的影响
15 返回本章目录 返回本章目录
第三节 刀具磨损过程及磨钝标准
切削金属时,刀具一方面切下切屑,另一方面 刀具本身也要发生损坏。 刀具损坏的形式主要有磨损和破损两类。 前者是连续的逐渐磨损; 后者包括脆性破损(如崩刃、碎断、剥落、裂纹 破损等)和塑性破损两种。 刀具磨损后,使工件加工精度降低,表面粗糙 度增大,并导致切削力加大、切削温度升高, 甚至产生振动,不能继续正常切削。因此,刀 具磨损直接影响加工效率、质量和成本。
16
1.刀具的磨损过程
1)初期磨损阶段 2)正常磨损阶段 3)急剧磨损阶段
返回本章目录
17
1)初期磨损阶段
这一阶段磨损曲线的斜率较大。由于刃磨后的 新刀具,其后刀面与加工表面间的实际接触面 积很小,压强很大,故磨损很快。 新刃磨后的刀面上的微观粗糙度也加速了磨损。 初期磨损量的大小与刀具刃磨质量有很大关系, 通常在VB=0.05—0.1mm之间。 经过研磨的刀具,其初期磨损量小,而且要耐 用得多。
切削速度v(m/min)
800 600 500 400 300 200
陶瓷刀具 (VB=0.4mm) 硬质合金 (VB=0.4mm)
刀具磨损、破损和使用寿命(刀具耐用度

•
刀具与切屑、工件间的接触表面经常是新鲜表面;
• 接触压力非常大;
• 接触表面的温度很高;
磨料磨损
冷焊磨损 刀具磨损形式: 扩散磨损 氧化磨损 热电磨损(扩散磨损一种)
§ 6-2刀具磨损过程及磨钝标准
6.2.1刀具磨损过程(后刀面磨损值VB随时间延长而增大)
刀具磨损过程分为三个阶段:
①初期磨损阶段(OA段)
切削时间T
图6-11刀具磨损曲线
3)在双对数坐标上是一直线(在一定速度范围内)
lg vc = - m lg T + lg A
m = tg φ
A为当 T=1s (min)时纵坐标截距
泰勒公式 (6-4)
vc =A /Tm
或:
T= C1 /vcz
(z =1/m)
A— 与工件材料有关的系数 m— 切削速度对刀具使用寿命的影响程度
Cv T 1/ m 1/ n 1/ p vc f a p
※ 当用硬质合金车刀切削碳钢时,切削用 量与刀具的经验公式为
T
Cv v f
5 c 1.75 0.75 p Nhomakorabeaa
式中 C——与工件材料、刀具材料和其他条件 v 有关的常数。
※ 切削用量中切削速度对刀具使用寿命 T 影响最大;其次是进给量;切削深度影 响最小。
6.1.2后刀面磨损 6.1.3前、后刀面同时磨损
a)后刀面磨损
b)前刀面磨损 hd > 0.5mm
c)前、后刀面 同时磨损 0.1mm< hd <0.5mm
hd <0.1mm
图1 – 24 刀具磨损的形式
★刀具磨损原因 刀具磨损经常是机械的、热的、化学的三种作用 的综合结果。 ★刀具磨损特点(状态)
刀具磨损与耐用度

第1章 切削与磨削过程
பைடு நூலகம்
1.5 刀具磨损与耐用度
1
1.5 刀具磨损与耐用度
内容提要
1. 2. 3. 4. 5. 6.
刀具的磨损方式; 刀具的磨损原因; 刀具的磨损过程; 刀具的磨钝标准; 刀具耐用度; 刀具的破损。
重点难点
1. 刀具的磨损原因; 2. 刀具耐用度的概念及影响因素。
18
1.5.4 刀具的磨钝标准
在金属切削的科学研究中多数按后刀面磨损宽度VB来制 定磨钝标准。规定磨钝标准的两点考虑:
①充分利用正常磨损阶段的磨损量,适用于粗加工和半 精加工。 ② 根据加工精度和表面质量要求规定磨钝标准。
国际标准ISO推荐硬质合金外圆车刀的磨钝标准,可以 是以下任何一种: (1) VB=0.3mm; (2)如果主后刀面为无规则磨损,取VB max=0.6mm; (3)前面磨损量KT=0.06+0.3f(f为进给量)
◆ 粘结磨损(冷焊) —— 刀具材料与工件材料亲和力大 —— 刀具材料与工件材料硬度比小 —— 中等偏低切速
粘结磨损加剧
◆ 扩散磨损 —— 高温下发生 ◆ 氧化磨损 —— 高温情况下,在切削刃工作边界发生
15
1.5.3 刀具的磨损过程
刀具磨损过程 3个阶段
后刀面磨损量VB 初期磨损 正常磨损 急剧磨损
在双对数坐标上的T—v曲线
26
1.5.5 刀具耐用度 1)切削用量对刀具耐用度的影响 b. 进给量、背吃刀量与刀具耐用度的关系
f= B / Tn ap= C/Tp
综合以上三式,可以得到切削用量三要素与耐用度的关系:
T CT / vc
ym
f ap
刀具磨损与刀具耐用度
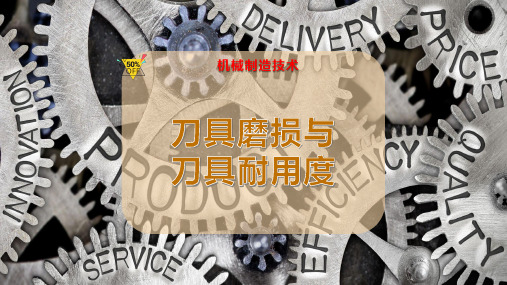
(2)粘结磨损
粘结又称为冷焊,是指刀具与工件或切屑接触 到原子间距离时产生结合的现象。粘结磨损是指工 件或切屑的表面与刀具表面之间的粘结点因相对运 动,刀具一方的微粒被对方带走而造成的磨损。
各种刀具材料都会发生粘结磨损。在中、 高速切削下,当形成不稳定积屑瘤时,粘结磨损 最为严重;当刀具和工件材料的硬度比较小时, 由于相互间的亲和力较大,粘结磨损也较为严重; 当刀具表面的刃磨质量较差时,也会加剧粘结磨 损。
3.刀具磨损过程
如右图所示,刀 具的磨损过程可以分 为初期磨损阶段、正 常磨损阶段和急剧磨 损阶段。
(1)初期磨损阶段
初期磨损阶段的磨损特点是:在开始磨损的 极短时间内,后刀面磨损量VB上升很快。初期磨 损阶段的后刀面磨损量VB一般为0.05~0.1mm, 其大小与刀具刃磨质量有关。
Hale Waihona Puke (2)正常磨损阶段(3)扩散磨损
扩散磨损是指由于在高温作用下,刀具与工件 接触面间分子活性较大,造成合金元素相互扩散置换, 使刀具材料的机械性能降低,再经摩擦作用而造成的 磨损。扩散磨损是一种化学性质的磨损。
扩散磨损的速度主要取决于切削速度和切削温 度。切削速度和切削温度愈高,扩散磨损速度愈快。
(4)氧化磨损
氧化磨损是指在高温下,刀具表面发生氧 化反应生成一层脆性氧化物,该氧化物被工件和 切屑带走而造成的磨损。氧化磨损也是一种化学 性质的磨损。在主、副切削刃工作的边界处与空 气接触,最容易发生氧化磨损。
正常磨损阶段的磨损特点是:磨损缓慢、均匀, 后刀面磨损量VB随切削时间延长近似成比例增加。
正常磨损阶段是刀具工作的有效阶段。曲线的 斜率代表了刀具正常工作时的磨损强度。磨损强度 是衡量刀具切削性能的重要指标之一。
金属切削原理PPT课件
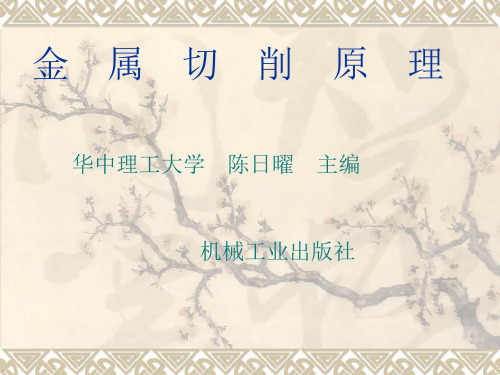
3. 背吃刀量 对外圆车削(图1-1) 和平面刨削(图1-2)而言,背吃刀量等于已 加工表面与待加工表面间的垂直距离;其中外圆 车削的背吃刀量:
总之,任何切削加工方法都必须有一个主运 动,可以有一个或几个进给运动。主运动和进给 运动可以由工件或刀具分别完成,也可以由刀具 单独完成(例如在钻床上钻孔或铰孔)。
二 工件上的加工表面
在切削过程中,通常工件上存在三个表面, 以图1-1的外圆车削和图1-2的平面刨削为 例,它们是:
1.待加工表面 它是工件上即将被切去的
三 切削用量
所谓切削用量是指切削速度,进给量和背吃 刀量三者的总称。它们分别定义如下:
1. 切削速度v 它是切削加工时,刀刃上选
定点相对于工件的主运动的速度.刀刃上各点的 切削速度可能是不同的。
当主运动为旋转运动时,刀具或工件最大直 径处的切削速度由下式确定:
式中 d——完成主运动的刀具或工件的最大直径 (mm);
(一)刀具在正交平面参考系中的标注角度
刀具标注角度的内容包括两个方面:一是确
定刀具上刀刃位置的角度;二是确定前刀面与后 面位置的角度。以外圆车刀为例(图1-9), 确定车刀主切削刃位置的角度有二:
主偏角 它是在基面上,主切切削忍与 基面的夹角。当刀尖在主切削刃上为最低的点时, 为负值;反之,当刀尖在主切削刃上为最高的点 时, 为正值。必须指出,这个规定是根据IS O标注,同过去某些书上关于正负号的规定恰好 相反。
实际上,除了由上述切削平面和基面组成的 参考平面系以外,还应该有一个平面作为标注和 测量刀具前,后刀面角度用的 “测量平面”。通 常根据刃磨和测量的需要与方便,可以选用不同 的平面作为测量平面。在刀刃上同一选定点测量 其角度时,如果测量平面选得不同,刀具角度的 大小也就不同。
刀具破损磨损崩刃怎么办+刀具寿命如何估算(培训课件)
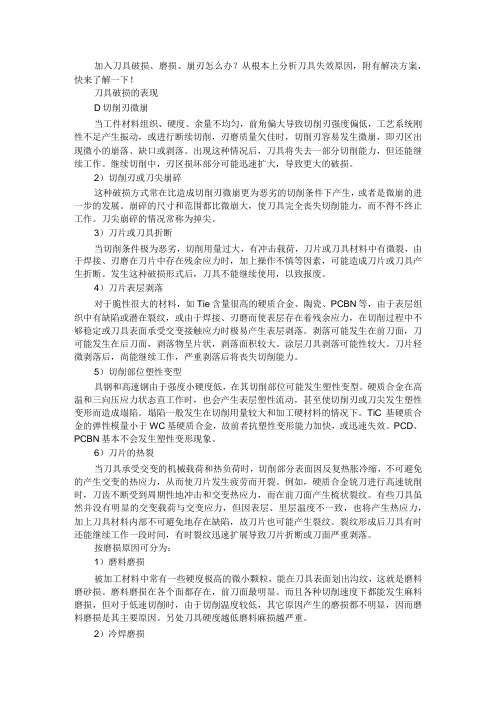
加入刀具破损、磨损、崩刃怎么办?从根本上分析刀具失效原因,附有解决方案,快来了解一下!刀具破损的表现D切削刃微崩当工件材料组织、硬度、余量不均匀,前角偏大导致切削刃强度偏低,工艺系统刚性不足产生振动,或进行断续切削,刃磨质量欠佳时,切削刃容易发生微崩,即刃区出现微小的崩落、缺口或剥落。
出现这种情况后,刀具将失去一部分切削能力,但还能继续工作。
继续切削中,刃区损坏部分可能迅速扩大,导致更大的破损。
2)切削刃或刀尖崩碎这种破损方式常在比造成切削刃微崩更为恶劣的切削条件下产生,或者是微崩的进一步的发展。
崩碎的尺寸和范围都比微崩大,使刀具完全丧失切削能力,而不得不终止工作。
刀尖崩碎的情况常称为掉尖。
3)刀片或刀具折断当切削条件极为恶劣,切削用量过大,有冲击载荷,刀片或刀具材料中有微裂,由于焊接、刃磨在刀片中存在残余应力时,加上操作不慎等因素,可能造成刀片或刀具产生折断。
发生这种破损形式后,刀具不能继续使用,以致报废。
4)刀片表层剥落对于脆性很大的材料,如Tie含量很高的硬质合金、陶瓷、PCBN等,由于表层组织中有缺陷或潜在裂纹,或由于焊接、刃磨而使表层存在着残余应力,在切削过程中不够稳定或刀具表面承受交变接触应力时极易产生表层剥落。
剥落可能发生在前刀面,刀可能发生在后刀面,剥落物呈片状,剥落面积较大。
涂层刀具剥落可能性较大。
刀片轻微剥落后,尚能继续工作,严重剥落后将丧失切削能力。
5)切削部位塑性变型具钢和高速钢由于强度小硬度低,在其切削部位可能发生塑性变型。
硬质合金在高温和三向压应力状态直工作时,也会产生表层塑性流动,甚至使切削刃或刀尖发生塑性变形而造成塌陷。
塌陷一般发生在切削用量较大和加工硬材料的情况下。
TiC基硬质合金的弹性模量小于WC基硬质合金,故前者抗塑性变形能力加快,或迅速失效。
PCD、PCBN基本不会发生塑性变形现象。
6)刀片的热裂当刀具承受交变的机械载荷和热负荷时,切削部分表面因反复热胀冷缩,不可避免的产生交变的热应力,从而使刀片发生疲劳而开裂。
刀具磨损、破损与耐用度必考知识范例(ppt 14页)

[例6,2] 什么叫刀具使用寿命?刀具使用寿命 和哪些因素有关?
[答案] 刀具由刃磨后开始切削,一直到磨损 量达到刀具磨钝标准所用的切削时间。通常用T 表示。刀具使用寿命与切削用量、刀具材料、 工件材料、刀具几何参数、加工条件、刀具结 构形式等因素有关。
[例6.3] 刀具磨损原因有哪几种?分析其 产生的原因。
[答案] 刀具磨损的原因主要有:硬质点磨损、 粘结磨损、扩散磨损和化学磨损。
(1)硬质点磨损。硬质点磨损主要是由于工件 材料中的杂质、材料基体组织中可含的碳化物、 氮化物和氧化物等硬质点以及积屑瘤的碎片等 所造成的机械磨损。 低速刀具易产生硬质点 磨损。工具钢(包括高速钢)刀具这种磨损比较显 著,而硬质合金刀具不易出现此类磨损。加工 冷硬铸铁、夹砂的铸件表层等材料时,易出现 此类磨损。
[例6.3] 刀具磨损原因有哪几种?分析其 产生的原因。
(2)粘结磨损。粘结是刀具和工件材料接触到原 子间距离时所产生的结合现象。是在刀具和工 件材料实际接触摩擦面上,由于有足够大的压 力和温度,产生塑性变形而发生的所谓冷焊现 象。两摩擦面的粘结点因相对运动,晶粒或晶 群受剪或受拉而被对方带走,是造成粘结磨损 的原因。
第六节 刀具磨损和刀具寿命讲解

T=CT/V1/m f1/m1 ap1/m2 =CT/Vx f yapz
式中 CT——刀具寿命系数,与工件材料、切削条件有关; x、y、z——指数,分别表示切削用量对刀具寿命T的影响, x>y>z.
切削用量对刀具寿命T影响由大到小的顺序为:V → f → ap
五、刀具破损
刀具破损分为脆性破损和塑性破损。脆性破损又分为早期和后期两种。 早期脆性破损——切削刚开始或短时间切削后即发生破损,前后刀面尚未产生明显的磨损
通常,高速钢刀具主要磨损原因:硬质点磨损、粘接磨损。
三、刀具磨损过程及磨钝标准
1、刀具的磨损过程 随着切削时间的延长,刀具的磨损将增加。根据切削试验,以切削时间和刀具后刀面
磨 损量VB(或前刀面月牙洼磨损深度KT)为横坐标和纵坐标,可得刀具的磨损典型曲线,如 图所示。由图可知:刀具磨损过程可以分三个阶段。
⑴ 初期磨损阶段 这一阶段磨损曲线的斜率较大,说明磨损较快。因为新刃磨的刀具刃口锋利 ,后刀面
与加工表面接触面积较小,压应力较大;且新刃磨刀具的后刀面存在粗糙不平之处及显微裂 纹等缺陷,所以这一阶段磨损速率较大。
这一阶段时间较短,磨损量通常为:0.05~0.1mm,其大小与刃磨质量有关。 ⑵ 正常磨损阶段
1、刀具寿命及刀具总寿命 刀具寿命:一把刀具由刃磨后开始使用,直至达到磨钝标准所经历的实际切削时间称刀具寿 命。
刀具总寿命:一把新刀从第一次投入使用,直至这把刀完全报废为止所经历的实际切削时间 称刀具总寿命。
2、刀具寿命的经验公式(切削用量与刀具寿命的关系)
⑴ 切削速度与刀具寿命的关系
选定磨钝标准,固定其他切削条件,在常用的切削速度范围内,取不同的的速度进行
⑶ 关于磨钝标准的几点说明 ① 手册中的磨钝标准,不是固定不变的,应根据实际加工条件灵活应用。 a) 粗加工时,VB值可取偏大值,VB=0.6mm; 精加工时, VB值应取偏小值,VB=0.1mm; b) 加工工艺系统刚性差时,为避免在磨钝标准内产生振动,VB值应取小值。 c) 加工难加工材料时, VB值应取偏小; d) 加工大型工件,为避免中途换刀, VB值可取偏大值,此时通常采用较低的切削速度。
- 1、下载文档前请自行甄别文档内容的完整性,平台不提供额外的编辑、内容补充、找答案等附加服务。
- 2、"仅部分预览"的文档,不可在线预览部分如存在完整性等问题,可反馈申请退款(可完整预览的文档不适用该条件!)。
- 3、如文档侵犯您的权益,请联系客服反馈,我们会尽快为您处理(人工客服工作时间:9:00-18:30)。
(1) 初期磨损阶段。新刃磨的刀具,由于表面粗糙不平,
在切削时很快被磨去,故磨损较快。经研磨过的刀具,初期的
形式:后角=0的磨损面
(VB:平均磨损宽度,VBmax :最大磨损宽度) 形成条件:加工塑性材料, v 较小, ac 较小;加工脆性材料
影响:切削力↑, 切削温度↑, 产生振动,降低加工质量
3
3、边界磨损(前、后刀面磨损)
切削塑性材料且ac=0.1~0.5 mm时,兼有前两种磨损的
形式;加工铸、锻件,主切削刃靠近工件外皮处及副切削刃靠
1
2
(a)刀具磨损形式 (b)边界磨损发生的地方 (c)测量磨损的地方
2、后刀面磨损
切削脆性材料或ac>0.1 mm的塑性材料时,切屑与前刀
面的接触长度较短,其上的压力与摩擦均不大,而相对的刀刃 钝圆使后刀面与工件表面的接触压力却较大,磨损主要发生在
后刀面。其值以磨损带宽度VB表示(如图所示)。
高速钢刀具(硬质点磨损和粘结磨损); 硬质合金刀具(粘结磨损和扩散磨损); 氧化铝陶瓷刀具(机械磨损和粘结磨损); 立方氮化硼刀具的扩散磨损很小,而金刚石刀具的扩散磨损 很大,金刚石刀具不宜加工钢料。
损
急剧磨损
后刀面磨损量VB
一、刀具的磨损过程
切削时间
硬质合金刀具高速切削钢料时,主要是扩散磨损,并伴随 有粘结磨损和化学磨损等;对一定刀具和工件材料,起主导作 用的是切削温度,低温时以机械磨损(硬质点磨损)为主,高 温时以热、化学磨损(粘结、扩散、氧化磨损)为主;合理地 选择刀具材料、 几何参数、 切削用量、 切削液,控制切削温 度, 有利于减少刀具磨损。
11
刀具磨损
刀具磨损原因
◆ 硬质点磨损
—— 各种切速下均存在 —— 低速情况下刀具磨损的主要原因
◆ 粘结磨损(冷焊)
—— 刀具材料与工件材料亲和力大 —— 刀具材料与工件材料硬度比小 —— 中等偏低切速
粘结磨损加剧
◆ 扩散磨损 —— 高温下发生
◆ 氧化磨损 —— 高温情况下,在切削刃工作边界发生
12
8
• 减小粘结磨损的途径: 1、硬质合金的晶粒加以细化,硬质合金表面涂覆TiC、 TiN、Al2O3等。 2、高速钢刀具表面要进行表面处理使表面形成一层抗 粘结的减磨层或高硬度的抗磨层,如氧氮化处理; 3、适当提高切削速度使运动平稳减小振动,避开积屑 瘤的不稳定区域; 4、使用润滑性能良好的切削液等。
刀具磨损与一般机械零件不同: (1)刀具与切屑、工件间的接接触表面经常是化学活性很 高的新鲜表面,不存在氧化膜等污染; (2)前后刀面的接触压力非常大,有时超过被切材料的屈 服强度; (3)刀-屑、刀具-工件接触表面的温度很高,硬质合金 刀具加工钢料时达800~1000度,高速钢刀具加工钢料时 达300~600度。 正常磨损的原因主要是机械、热和化学三种作用的综合 结果。
空气中的氧易与硬质合金中的Co、WC、TiC发生氧化作用, 产生低硬度的氧化物(Cr3O4、TiO2、WO3等)被切屑和工件带 走,从而使刀具磨损。
5、热电磨损 切削时,刀具与工件构成一自然热电偶, 产生
热电势,工艺系统自成回路,热电流在刀具和工件中通过,从 而促进扩散作用而加速刀具磨损,这称为热电磨损。
粘结是指刀具与工件材料接触到原子间距离时所产生的结 合现象。两摩擦表面的粘结点因相对运动,晶粒或晶粒群受剪 或受拉被对方带走,是造成粘结磨损的原因。
由于刀具材料有组织不均匀、存在内应力、微裂纹及空隙、 局部软点等缺陷,所以刀具表面常发生破裂而被切屑或工件带 走,形成粘结磨损,在前刀面上形成不规则的凹坑。
9
3、扩散磨损 刀具与工件、切屑的接触面,在高温下双方金属中的化学
元素从高浓度处向低浓度处迁移,这种固态下元素相互迁 移而造成的刀具磨损称为扩散磨损。
高温下,刀具材料中的W、 Co、Ti 、 C等易扩散到工件 和切屑中去;而切屑中的Fe、Si、Mn、Cr等也会扩散到刀 具中来, 从而改变刀具材料中的化学成分, 使其硬度下降, 加速刀具磨损。
与铁相互扩散强度的由大到小的顺序为: 金刚石-碳化硅-立方氮化硼-氧化铝 与钛合金相互扩散的由大到小的顺序为: 氧化铝-立方氮化硼-碳化硅-金刚石
10
4、化学磨损(氧化磨损)
在高温下(700~800℃),刀具材料与某些周围介质起化学 作用,在刀具表面形成一层硬度较低的化合物而被切屑带走, 这样形成的刀具磨损称为化学磨损。
5
1、硬质点磨损
硬质点磨损是指工件上具有一定擦伤能力的硬质点,如碳 化物、积屑瘤碎片、已加工表面的硬化层等, 在刀具表面上 划出一条条沟纹而造成的磨损。
硬质点硬度超过刀具材料基体的硬度。 硬质点磨损是拉刀、板牙等高速钢制造的低速切削刀具磨 损的主要原因,硬质合金刀具发生硬质点磨损的情况较少。
6
2、粘结磨损
高速钢、硬质合金、陶瓷刀具、立方氮化硼和金刚石刀具 都会因粘结而发生磨损。
7
粘结磨损程度主要取决于刀具材料和工件材料在不同 温度下的相互亲和能力。(粘结强度系数K0)
硬质合金晶粒越小,磨损越慢; 刀具与工件的硬度比,刀具表面形状和组织,切削条 件和工艺系统刚度等都影响粘结磨损的速度。 切削钢料应用YT类硬质合金。(但不锈钢和高温合金 不宜用YT类,因为YT类合金中的钛元素易于工件中的钛 元素发生亲和而导致粘结,在高温下扩散磨损也较剧烈。)
第六章 刀具磨损、破损和刀具耐用度
6.1 刀具磨损形态
◆ 刀具的失效形式:正常磨损和破损
1、前刀面磨损(月牙洼磨损)
切削塑性材料且ac>0.5 mm时,切屑与前刀面在高温、
高压下相互接触,产生剧烈摩擦,以形成月牙洼磨损为主,
其值以最大深度KT表示(如图6-1(c)所示)。 形成条件:加工塑性材料,v大,ac大 影响:削弱刀刃强度,降低加工质量 。
近刀尖处,因为ac减小、切削刃打滑,所以磨出较深的沟纹(如
图6- 1(a)、(b)所示)。加工铸、锻件等外皮粗糙的工件,也 容易发生边界磨损。
磨损形式随切削条件的改变可以互相转化。在大多数情况 下,后刀面都有磨损,且VB直接影响加工精度,加之便于测量, 所以常以VB表示刀具磨损程度。
4
6.2 刀具磨损的原因