膜处理电镀废水讲解
电镀废水、印染废水等工业污水处理工艺说明
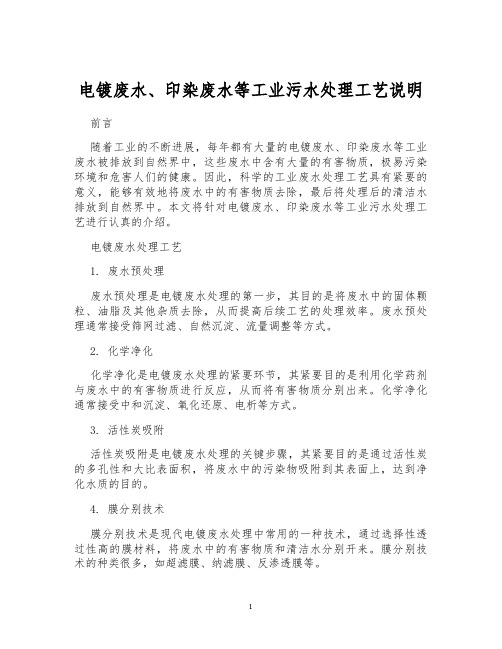
电镀废水、印染废水等工业污水处理工艺说明前言随着工业的不断进展,每年都有大量的电镀废水、印染废水等工业废水被排放到自然界中,这些废水中含有大量的有害物质,极易污染环境和危害人们的健康。
因此,科学的工业废水处理工艺具有紧要的意义,能够有效地将废水中的有害物质去除,最后将处理后的清洁水排放到自然界中。
本文将针对电镀废水、印染废水等工业污水处理工艺进行认真的介绍。
电镀废水处理工艺1. 废水预处理废水预处理是电镀废水处理的第一步,其目的是将废水中的固体颗粒、油脂及其他杂质去除,从而提高后续工艺的处理效率。
废水预处理通常接受筛网过滤、自然沉淀、流量调整等方式。
2. 化学净化化学净化是电镀废水处理的紧要环节,其紧要目的是利用化学药剂与废水中的有害物质进行反应,从而将有害物质分别出来。
化学净化通常接受中和沉淀、氧化还原、电析等方式。
3. 活性炭吸附活性炭吸附是电镀废水处理的关键步骤,其紧要目的是通过活性炭的多孔性和大比表面积,将废水中的污染物吸附到其表面上,达到净化水质的目的。
4. 膜分别技术膜分别技术是现代电镀废水处理中常用的一种技术,通过选择性透过性高的膜材料,将废水中的有害物质和清洁水分别开来。
膜分别技术的种类很多,如超滤膜、纳滤膜、反渗透膜等。
5. 消毒杀菌消毒杀菌是电镀废水处理的最后一步,其目的是将膜分别后的清洁水进行消毒处理,达到安全排放的标准。
消毒杀菌可以接受光解、氧化、紫外线等方式。
印染废水处理工艺1. 湿法氧化法湿法氧化法是印染废水处理中常用而有效的方法,其原理是将废水中的有机物通过氧化反应进行分解,并转化为无害物质。
在湿法氧化法中,一般会加入助氧剂,如过氧化氢、氧气等。
2. 活性污泥法活性污泥法是印染废水处理的一种传统方法,其紧要特点是使用含有大量微生物的活性污泥对废水中的有机物进行降解。
在活性污泥法中,废水会被污泥进行搅拌和摇摆,使污泥中的微生物和废水充分接触,从而使有机物得以分解。
3. 膜分别技术膜分别技术在印染废水处理中同样适用,其处理原理与电镀废水处理仿佛。
电镀污水处理工艺流程

电镀污水处理工艺流程电镀是一种常见的金属加工方法,也是一种污染环境的生产过程。
电镀污水中含有大量有害物质,如重金属离子、有机物等,对环境造成严重污染。
为了保护环境和资源,必须对电镀污水进行有效处理,减少有害物质的排放。
本文将介绍电镀污水处理的工艺流程。
一、电镀污水的主要污染物1. 重金属离子:电镀过程中使用的金属离子,如镍、铬、锡等,会随废水排放,对水体造成严重污染。
2. 有机物:电镀液中含有大量有机物,如有机酸、复合酸等,对水质造成污染。
3. 其他污染物:电镀过程中可能还会产生氨氮、氰化物等有害物质,对水体造成进一步污染。
二、电镀污水处理工艺流程1. 预处理:电镀污水在进入处理系统之前,需要进行预处理,包括除油、除渣等工序,以减少后续处理过程中的负担。
2. 中和处理:电镀污水经过预处理后,进入中和处理工艺。
中和处理主要是通过加入中和剂,调节污水的酸碱度,使金属离子和有机物以不易溶解的形式沉淀下来,从而实现去除。
3. 沉淀处理:经过中和处理后,污水中的沉淀物质会沉淀到底部,形成污泥。
污泥中含有大量的重金属离子和有机物,需要进行进一步处理,以减少对环境的影响。
4. 氧化处理:经过沉淀处理后,还会有少量的有机物和重金属离子残留在水中。
这时,可以采用氧化处理方法,如臭氧氧化、高级氧化等,将有机物氧化成无害物质,进一步减少污水中的有害物质含量。
5. 活性炭吸附处理:氧化处理后,污水中可能还会有少量的有机物残留。
这时,可以采用活性炭吸附的方法,将残留的有机物吸附到活性炭上,从而达到去除有机物的目的。
6. 膜分离处理:经过以上处理后,电镀污水中的有机物和重金属离子已经大大减少。
为了进一步提高水质,可以采用膜分离方法,如微滤、超滤等,将残留的有机物和重金属离子去除,使污水的水质达到排放标准。
7. 消毒处理:经过膜分离处理后,电镀污水中的大部分有害物质已经去除。
为了确保排放水体的环境安全,还需要进行消毒处理,如高效臭氧消毒、紫外线消毒等,杀灭水中的细菌和病毒,确保排放水体的安全。
电镀废水处理方法

电镀废水处理方法摘要:一、电镀废水概述二、电镀废水处理方法1.物理方法2.化学方法3.生物方法三、各类处理方法的优缺点四、电镀废水处理发展趋势五、结论正文:电镀废水处理方法一、电镀废水概述电镀废水是指在电镀过程中产生的含有有毒有害物质的废水。
这类废水具有较高的化学需氧量、重金属含量和有机物含量,对环境和人体健康造成严重威胁。
因此,对电镀废水进行有效处理显得尤为重要。
二、电镀废水处理方法1.物理方法物理方法主要通过吸附、沉淀、膜分离等手段对电镀废水进行处理。
其中,吸附法具有较高的去除效率,可以有效地去除废水中的重金属离子;沉淀法通过加入化学沉淀剂使重金属离子转化为沉淀物,从而实现去除;膜分离技术则通过筛选作用将废水中的污染物分离出来。
2.化学方法化学方法主要包括中和法、氧化还原法、混凝沉淀法等。
中和法适用于处理酸性和碱性废水,通过加入中和剂调节废水的pH值,使重金属离子转化为沉淀物;氧化还原法通过加入氧化剂或还原剂,将废水中的有毒有害物质转化为无害或低毒物质;混凝沉淀法通过加入混凝剂使废水中的微小颗粒聚集成大颗粒,便于后续沉淀和分离。
3.生物方法生物方法主要利用微生物的代谢活性对电镀废水中的有毒有害物质进行降解。
常用的生物方法有活性污泥法、生物膜法、生物滤池法等。
这些方法具有处理效果好、运行费用低、能有效去除有机物和重金属离子等优点。
但生物方法对废水中的有毒有害物质浓度有一定要求,不适用于高浓度废水的处理。
三、各类处理方法的优缺点1.物理方法:优点:操作简便、设备占地面积小、处理效果较好;缺点:对废水中的有毒有害物质去除不彻底,易造成二次污染。
2.化学方法:优点:处理效果较好,能有效去除废水中的有毒有害物质;缺点:运行费用较高,对环境有一定的影响。
3.生物方法:优点:处理效果好、运行费用低、能有效去除有机物和重金属离子;缺点:对废水中的有毒有害物质浓度有一定要求,不适用于高浓度废水的处理。
四、电镀废水处理发展趋势1.集成处理技术:将物理、化学和生物方法相结合,实现废水的高效处理。
电镀废水处理
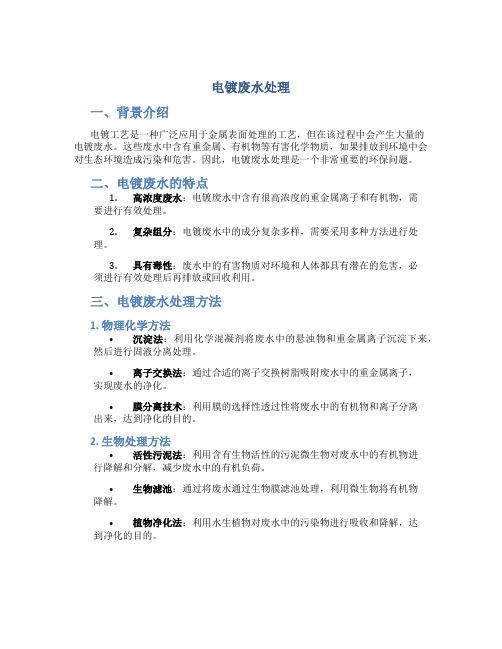
电镀废水处理一、背景介绍电镀工艺是一种广泛应用于金属表面处理的工艺,但在该过程中会产生大量的电镀废水。
这些废水中含有重金属、有机物等有害化学物质,如果排放到环境中会对生态环境造成污染和危害。
因此,电镀废水处理是一个非常重要的环保问题。
二、电镀废水的特点1.高浓度废水:电镀废水中含有很高浓度的重金属离子和有机物,需要进行有效处理。
2.复杂组分:电镀废水中的成分复杂多样,需要采用多种方法进行处理。
3.具有毒性:废水中的有害物质对环境和人体都具有潜在的危害,必须进行有效处理后再排放或回收利用。
三、电镀废水处理方法1. 物理化学方法•沉淀法:利用化学混凝剂将废水中的悬浊物和重金属离子沉淀下来,然后进行固液分离处理。
•离子交换法:通过合适的离子交换树脂吸附废水中的重金属离子,实现废水的净化。
•膜分离技术:利用膜的选择性透过性将废水中的有机物和离子分离出来,达到净化的目的。
2. 生物处理方法•活性污泥法:利用含有生物活性的污泥微生物对废水中的有机物进行降解和分解,减少废水中的有机负荷。
•生物滤池:通过将废水通过生物膜滤池处理,利用微生物将有机物降解。
•植物净化法:利用水生植物对废水中的污染物进行吸收和降解,达到净化的目的。
3. 综合处理方法•组合工艺:采用多种处理方法的组合,如生物处理和物理化学方法结合,以提高废水处理效率和净化效果。
•回收利用:对处理后的废水进行回收再利用,如将废水中的水分回收,重金属进行资源化回收利用。
四、电镀废水处理技术的发展趋势1.高效化:发展更高效的处理方法和设备,提高废水处理效率和净化效果。
2.资源化:加强废水中有价值物质的回收利用,实现资源化利用和循环经济。
3.智能化:引入先进的智能控制技术,实现废水处理过程的自动化和智能化。
4.绿色化:研究开发绿色环保的处理方法,减少对环境的影响和损害。
五、结论电镀废水处理是一个重要的环境保护问题,需要采取有效的处理方法和措施。
结合物理化学方法、生物处理方法以及综合处理方法,可以有效地净化电镀废水,减少对环境的污染和危害。
电镀废水处理技术简介

电镀废水处理技术我国的工业迅速发展,电镀类企业为社会经济的进步奠定了基础,工业发展的同时,也带来了严重的废水排放问题。
1电镀废水来源1)前处理除油酸洗工序:前处理废水再电镀废水中很大比重,在前处理表面时除油会产生碱性废水(可能含有机溶剂),除锈会产生酸洗废水;2)镀件的清洗水:电镀生产线有很多清洗槽,带来了大量废水。
清洗废水的成分和镀液配方的成分基本一致,有重金属离子和添加剂以及络合剂。
3)废电镀液:电镀槽中的镀液经过长时间使用可能会出现变质,成分配比失调等现象,所以镀液也要更换和补充,就产生了高浓度废水。
成分和清洗水相似,电镀金属原料,还原剂,络合剂,光亮剂等等。
4)跑、冒、滴、漏的各种槽液和排水:由于电镀槽渗漏或是操作不当导致的污染。
5)设备水:只经过高温,没有污染。
2电镀废水排放标准《电镀污染物排放标准》(GB21900-2008),自2013年7月1日起,新建企业执行表2规定的水污染物排放限值。
根据环境保护工作的要求,在国土开发密度已经较高、环境承载能力开始减弱,或环境容量较小、生态环境脆弱,容易发生严重环境污染问题而需要采取特别保护措施的地区,应严格控制企业的污染物排放行为,在上述地区的企业执行表3规定的水污染物特别排放限值。
部分地区会要求执行各地的地方标准。
3电镀废水分类及处理方法1)含磷废水电镀废水中含磷物质有:磷酸、磷酸盐、次亚磷酸盐、亚磷酸、焦磷酸盐、植酸等,正磷酸盐比较容易除去,非正磷酸盐和有机磷酸盐则较难除去。
一般采取分类处理的方法,将含有正磷酸盐的废水分到前处理废水,非正磷酸盐的废水分到络合废水(含络合物的废水)。
次磷酸根不能和金属离子形成难溶性沉淀,传统方法是使用芬顿法氧化或是双氧水强氧化成正价态的磷,再进行化学沉淀。
现在有公司针对次亚磷酸盐针对性地开发了次亚磷去除剂,能够通过均相共沉淀技术,与水中的次亚磷酸盐结合生成不溶性沉淀,无需转化为正磷,把总磷处理至0.5mg/L以下,目前已广泛应用在塑料电镀以及五金化学镀废水处理中。
电镀废水处理详细方法与工艺
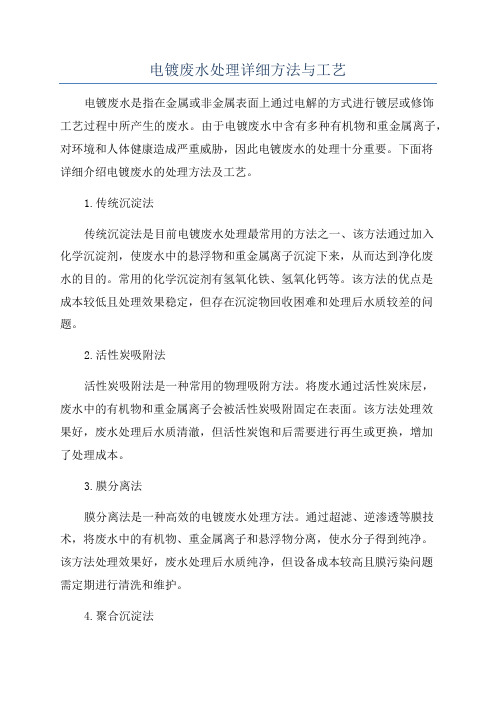
电镀废水处理详细方法与工艺电镀废水是指在金属或非金属表面上通过电解的方式进行镀层或修饰工艺过程中所产生的废水。
由于电镀废水中含有多种有机物和重金属离子,对环境和人体健康造成严重威胁,因此电镀废水的处理十分重要。
下面将详细介绍电镀废水的处理方法及工艺。
1.传统沉淀法传统沉淀法是目前电镀废水处理最常用的方法之一、该方法通过加入化学沉淀剂,使废水中的悬浮物和重金属离子沉淀下来,从而达到净化废水的目的。
常用的化学沉淀剂有氢氧化铁、氢氧化钙等。
该方法的优点是成本较低且处理效果稳定,但存在沉淀物回收困难和处理后水质较差的问题。
2.活性炭吸附法活性炭吸附法是一种常用的物理吸附方法。
将废水通过活性炭床层,废水中的有机物和重金属离子会被活性炭吸附固定在表面。
该方法处理效果好,废水处理后水质清澈,但活性炭饱和后需要进行再生或更换,增加了处理成本。
3.膜分离法膜分离法是一种高效的电镀废水处理方法。
通过超滤、逆渗透等膜技术,将废水中的有机物、重金属离子和悬浮物分离,使水分子得到纯净。
该方法处理效果好,废水处理后水质纯净,但设备成本较高且膜污染问题需定期进行清洗和维护。
4.聚合沉淀法聚合沉淀法是一种将废水中的有机物和重金属离子聚集起来形成絮凝物,再通过沉降或过滤将之从水中剔除的方法。
该方法处理效果较好,可以同时去除悬浮物和重金属离子,但处理过程需要添加聚合剂,同时产生的大量污泥需要进行处理。
5.生物处理法生物处理法是一种利用微生物代谢和生物降解作用来去除废水中有机物的方法。
该方法采用活性污泥法、生物膜法等技术,通过微生物降解废水中的有机物质,将其转化为二氧化碳、水等无害物质。
该方法处理效果好,且过程中无需要添加化学药剂,但对废水中重金属离子的去除效果较差。
综上所述,电镀废水处理方法及工艺研究中,传统沉淀法、活性炭吸附法、膜分离法、聚合沉淀法和生物处理法都是常用的处理方法。
根据废水的具体特点和处理要求,选取合适的处理方法以达到废水净化的目的。
电镀废水膜分离处理工艺流程
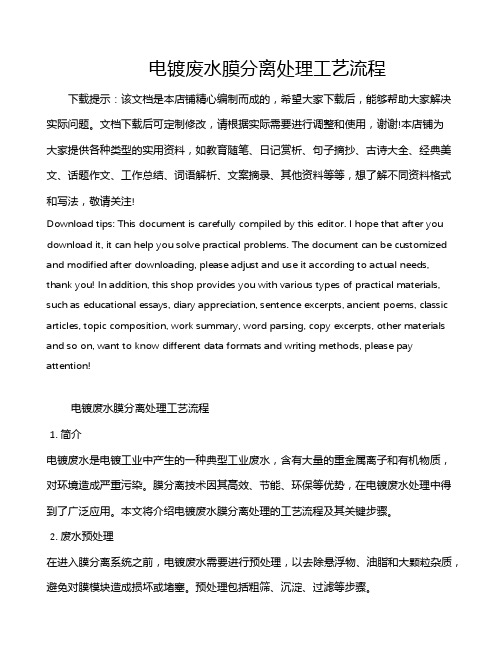
电镀废水膜分离处理工艺流程下载提示:该文档是本店铺精心编制而成的,希望大家下载后,能够帮助大家解决实际问题。
文档下载后可定制修改,请根据实际需要进行调整和使用,谢谢!本店铺为大家提供各种类型的实用资料,如教育随笔、日记赏析、句子摘抄、古诗大全、经典美文、话题作文、工作总结、词语解析、文案摘录、其他资料等等,想了解不同资料格式和写法,敬请关注!Download tips: This document is carefully compiled by this editor. I hope that after you download it, it can help you solve practical problems. The document can be customized and modified after downloading, please adjust and use it according to actual needs, thank you! In addition, this shop provides you with various types of practical materials, such as educational essays, diary appreciation, sentence excerpts, ancient poems, classic articles, topic composition, work summary, word parsing, copy excerpts, other materials and so on, want to know different data formats and writing methods, please pay attention!电镀废水膜分离处理工艺流程1. 简介电镀废水是电镀工业中产生的一种典型工业废水,含有大量的重金属离子和有机物质,对环境造成严重污染。
《电镀废水处理技术》课件
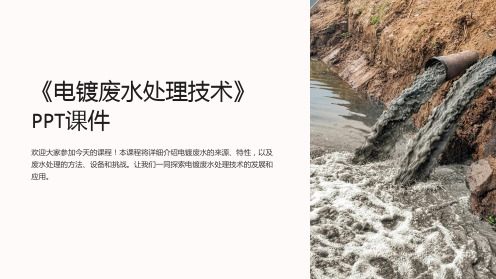
废水处理设备
常见处理设备
• 沉淀池 • 活性污泥反应器 • 膜分离设备
设备的使用效果与注意事项
• 设备使用效果的评价 • 设备的维护与保养
应对电镀废水处理的挑战
• 电镀废水产生的新技术 • 废水处理设备的更新换代 • 废水治理环境政策的不断改变
结语
• 电镀废水处理技术的发展趋势 • 对电镀行业的启示
《电镀废水处理技术》 PPT课件
欢迎大家参加今天的课程!本课程将详细介绍电镀废水的来源、特性,以及 废水处理的方法、设备和挑战。让我们一同探索电镀废水处理技术的发展和 应用。
废水来源与特性
• 电镀工艺流程 • 废水排放特性
废ห้องสมุดไป่ตู้处理方法
传统处理方法
• 化学沉淀法 • 活性污泥法
先进处理技术
• 膜分离技术 • 生物反应器技术 • 高级氧化技术
- 1、下载文档前请自行甄别文档内容的完整性,平台不提供额外的编辑、内容补充、找答案等附加服务。
- 2、"仅部分预览"的文档,不可在线预览部分如存在完整性等问题,可反馈申请退款(可完整预览的文档不适用该条件!)。
- 3、如文档侵犯您的权益,请联系客服反馈,我们会尽快为您处理(人工客服工作时间:9:00-18:30)。
集成膜分离技术处理电镀综合废水可行性研究作者:赵胜利上传:tuzhi 来源:网络收集 2006-03-07 09:061.概述采用集成膜技术处理电镀综合废水,实现水在线回用、清洁生产,以美国通用公司OEM生产汽车轮毂企业上海某电镀厂项目为案例,该项目日处理废水量为480M3,要求零排放设计,实现循环水85%利用,处理后水质要求理化指标与上海自来水标准相同。
处理工艺主体完全采用当今世界先进的膜分离技术,利用OSMONICS一种具有半透性能的高分子合成膜材料,在外压趋动力作用下实现废水溶液中某些组分选择性透过的分离技术。
膜材质选型为芳香族聚酰胺,可脱除污水中的有机物、细菌、病毒、盐类等物质,操作压力为0.4-1.0MPa。
利用这种新技术、新设备的净化装置其性能优良、经济适用、效果突出、节省投资,运行成本低廉,占地面积小,在污水深度净化处理中实现开电镀综合废水处理循环利用先河。
电镀废水主要包括电镀工艺的前处理废水、镀层漂洗废水、后处理废水、废镀液以及设备冲洗废水、刷洗地坪和极板废水以及由于操作或管理疏漏而引起的跑冒滴漏产生的废水,还有:在废水传统的化学处理过程中导致的二次污染等。
电镀表面处理工艺过程,常用的镀种有镀镍、镀铜、镀铬、镀锌等。
电镀工艺根据不同镀种分类,在镀件生产过程中,除油、酸洗和电镀等所产生的镀件清洗、镀液过滤、废液、渗漏及地面冲洗等,废水中污染物的浓度不尽相同,其中电镀前处理工序的除油、除锈、活化等过程产生的大量的化学药剂、重金属离子和有机添加剂而形成的酸碱废水总量占50%以上。
废水处理的目的是将废水中的有害物质加以分离,或使有害物质改性变成无害物。
电镀废水的处理方法大体可分为物理法、物化法和生化处理法。
物理处理法主要是去除或回收废水中较大颗粒的悬浮物和油类等,包括自然沉淀、浮选、过滤、离心、蒸发等;物化法主要是去除或回收废水中的细小悬浮物、胶体和溶解物质,或者将有毒物质改性转化为无毒物质,包括混凝沉淀、中和、氧化还原、萃取、吸附、离子交换、反渗透、电渗析等;生化处理法主要是通过生物作用将废水中胶体的和溶解的有机物分解破坏而加以分离去除。
以集成膜技术处理电镀废水就是以筛分为机理按电镀废水的特性分级分段或多级多段处理。
集成膜过程是进几年来在膜分离技术的发展中的又一项新技术,即:将几种膜分离过程联合起来,或将膜分离与其它分离方法结合起来,将它们各自用在最适合的条件下,发挥其最大的效率。
随着集成膜分离技术的不断发展和完善,膜分离技术在工业生产领域中将发挥更大的作用。
2.项目来源与背景上海闵行某电镀有限公司是美国通用公司、福特、戴姆勒-克莱斯勒三大汽车制造公司的整车轮毂OEM生产厂。
项目单位概况:厂区占地面积13876平方米,建筑面积6716.7平方米,绿化面积2775.2平方米,绿化率20%。
年产电镀轮毂30万只、销售12240万元、利润3000万元。
设计电镀废水总排放量184M3/D,实际电镀废水排放总量768M3/D(其中含有生活区26M3/D 生活污水)。
该电镀厂位于上海黄浦江上游准水源保护区、上海世博园区东南隅,新建项目要求不得向准水源排污,实现重金属废水闭路处理与循环水利用。
3.项目设计依据镀件前处理废水: 15M3/HR;铜系漂洗废水: 3M3/HR;镍系漂洗废水: 6M3/HR;铬系漂洗废水: 3M3/HR;锌系漂洗废水: 4M3/HR;含氰废水: 5M3/HR;跑冒滴漏废水: 12M3/HR(含冲洗水);电镀生产线总废水量:768M3/D (8×2班次);电镀原废水水质主要成分表1序号工序成分温度1 前处理(脱脂、脱蜡)碳酸钠70℃磷酸三钠硅酸钠2 阴极除油碳酸钠70-80℃磷酸三钠3 碱浊氢氧化钠常温4 沉锌氢氧化钠40-50℃氧化锌5 脱锌硝酸常温6 预镀镍硫酸镍55℃氯化镍硼酸7 镀铜前酸活化硫酸常温8 光亮镀铜硫酸铜50℃硫酸9 半亮镍硫酸镍60℃氯化镍硼酸BTLTL-210 高硫镍硫酸镍50℃氯化镍硼酸BTLTN11 亮镍硫酸镍60℃氯化镍硼酸12 镍封硫酸镍50-60℃氯化镍硼酸BNT-BBNF-110BNF-22013 镀铬前酸活化铬酐30℃14 镀铬铬酐30℃硫酸4.系统主体工程设计(1)设计电镀废水收集槽收集来自电镀生产线的各镀种漂洗废水(含冲洗、跑冒滴漏废水),收集槽废水停留时间8h;(2)经提升泵进入前置预处理去除悬浮物固体;(3)初处理废水进入UF分子筛分子系统去除大分子物质及胶体、去除部分COD;(4)实现NF/RO进水要求时由多级分离增压泵送入离子筛分系统,同时在线调整pH值,使分离后水质指标达到电镀生产工艺用水及漂洗水要求;(5)系统产水收集备用并提升至高位水箱输送到生产线;(6)系统设计pH自动加药调整、集成膜分离维护药洗系统;(7)系统过程控制设PLC自动报警控制系统,在线监测ORP、TDS、pH,确保循环利用水水质标准;(8)膜分离后少量浓缩液经一步法化学处理,上清液导入原废水池进入系统循环处理,少量残渣取出定期处理(6个月或12个月清理一次)。
5.集成膜系统构成系统构成(图1):6.工艺流程及设备配置分析工艺流程(图2):系统设备配置及运行工况分析:膜法水处理与传统工艺不同在于,膜处理过程是物理过程,不发生相变、在常温下运行、选择性强、无化学变化、适应性强。
克服了传统工艺能耗高、二次污染、占地面积大、自动化控制难和操作繁琐的缺点。
前置预处理系统由DGF/ACF/MF装置组成:前置预处理系统废水来源破氰、镀铬及综合废水,经多介质滤器进入系统处理,使SS基本去除后进一步降低浊度而实现部分重金属吸附去除。
多介质过滤有效去除废水中的生物絮体和胶体物质,去除化学絮凝过程产生的铁盐、铝盐、等沉积物,显著降低出水的悬浮物含量和浊度,使出水安全进入下一个系统,以保证UF分子筛分系统的正常运行。
活性炭过滤进一步降低出水的BOD、COD值,对重金属、细菌、病毒有很高的去除率。
MF过滤装置:微滤是以静压差为推动力,利用筛网状过滤介质膜的“筛分”作用进行分离的膜过程,其原理与普通过滤相类似,但过滤的微粒在0.03~15μm,因此又称其为精密过滤,是过滤技术的最新发展。
在静压差作用下,小于膜孔的粒子通过膜,比膜孔大的粒子则被截留在膜面上,使大小不同的组分得以分离,操作压力为0.7~7Kpa。
MF膜的截留作用大体可分为以下几种:A、机械截留作用指膜具有截留比它孔径大或孔径相当的微粒等杂质的作用,即筛分作用。
B、物理作用或吸附截留作用如果过分强调筛分作用就会得不出不符合实际的结论,除了要考虑孔径因素外,还要考虑其他因素的影响,其中包括吸附和电性能的影响。
C、架桥作用通过电镜可以观测到,在孔的入口处,微粒因为架桥作用也同样可以被截留。
D、网络型膜的网络内部截留作用是将微粒截留在膜的内部,并非截留在膜的表面。
UF分子筛分装置:超滤是介于微滤和纳滤之间的一种膜过程,膜孔径范围为0.05μm(接近MF)至1nm(接近NF),超滤的典型应用是从溶液中分离大分子物质和胶体,所分离的溶质分子量下限为几千Dalton(1Dalton即1Da,1Da=1.66054×10-27kg)。
超滤膜对溶质的分离过程主要有:A、在膜表面及微孔内吸附;B、在孔中停留而被去除;C、在膜面的机械截留。
超滤对于水中悬浮物、固体、胶体、大分子、细菌有较高的去除率,对BOD和COD有部分的去除率。
超滤膜可通过定期反洗和化学清洗,保持长期使用。
NF(RO)离子筛分装置:RO系统原理:在浓液的一边加上比自然渗透压更高的压力,扭转自然渗透方向,把浓溶液中的溶剂(水)压到半透膜的另一边稀溶液中,这是和自然渗透过程相反的。
这种现象表明,当对盐水一侧施加的压力超过水的渗透压时,可以利用半透膜装置从盐水中获得淡水。
反渗透对于水中溶质、盐(悬浮物、大分子、离子、二价和多价阳离子盐)有很高的脱除率。
采用进口超低压膜进行除盐,脱盐率可达到99.5%以上,使产水电导率下降到200μs/cm以下。
PLC在线控制系统及相关辅助设备:RO系统的控制(集中控制)方式采用手动控制(按钮操作)和全自动控制(PLC 运行)方式两种。
在全自动控制方式无故障情况下不采用手动控制方式,确保反渗透系统正常运行,避免在操作失误的情况下造成不必要损失。
RO控制系统采用模拟屏显示,各种运行参数、状态及水质情况直观明了;整套控制系统配有在线ORP/TDS/pH监测仪、高压泵低压保护装置、在线压力传感器、水箱液位传感器、在线温度传感器、在线流量传感器等全套在线仪表,确保各种运行参数都能在模拟显示屏上反应出来。
同时具有运行状态及故障报警远传功能。
系统运行工况受进水及预处理水箱的液位自动控制,高位运行,低位停止。
系统处理后水质情况表2序号项目原水水质指标中水水质指标系统产水水质1 pH值 1.82 9.03 6.5-7.52 CN- (mg/L) 79 0.7 <0.053 Cr6+ (mg/L) 256 0.78 <0.054 总铬(mg/L) 284 0.84 <0.15 Ni2+ (mg/L) 35.5 0.672 <0.026 Cu2+ (mg/L) 52 4.3 <0.57 电导(μs/cm) -- -- <150膜对不同价离子的截留性能表3化合物/无机盐膜A 膜B 膜C 膜DNaCl 15.81 33.15 35.15 40.81Na2CO362.26 72.53 75.51 78.18Na2SO485.87 91.02 92.60 96.21MgSO480.70 87.37 93.09 98.48KCl 20.57 40.57 42.21 42.71CaCl247.36 52.80 68.51 73.63BaCl238.22 46.66 62.32 76.177.经济效益分析设计每天电镀综合废水进水处理量:Q进=768m 3/d;即: 768 m/d 3×75%=576m3/d;设计每天系统产水回用量(75%): Q出=576m3/d ;(不含系统回流)回用水按自来水单价2.5元/ m3计算即:576 m3×2.5元=1440元/d;年直接水回用量:576m3/d×300天=172,800m3/a;年直接回用水产生效益:172,800m3/a×2.5=432,000元/a;年节约排污费用:排污费按3.0元/m3计算即:768m3/d×3.0元/m3×300天=691,200元/a;运行费用:以处理量 768m3/d计,耗电45kw/h,按0.5元/kw·h计即:45kw/h×0.5元×16h=360元/d ;则年用电费用:360元×300=108000元/年;材料损耗费用:更换UF/RO膜元件,设膜寿命三年,整套设备需配膜组件108支,单支膜平均单价按2,500元/支计即:2,500元×108=270,000元(平均每三年间歇更换一次);则每年损耗费为: 270,000元÷3=90,000元/a;电镀废水回用工程实际创造效益:年节水:140,400m3/a;年节水产生效益:432,000元/a;年节约排污费用:691,200元年水回用直接效益+节约补给水效益+节约排污费-(用电费用+材料费用)即:( 432,000+691,200元)/年–(108000元+90,000元)/年=925,200元/年则:年实现效益925,200元。