危害因素的辨识与风险评价
危害因素的辨识与风险评价
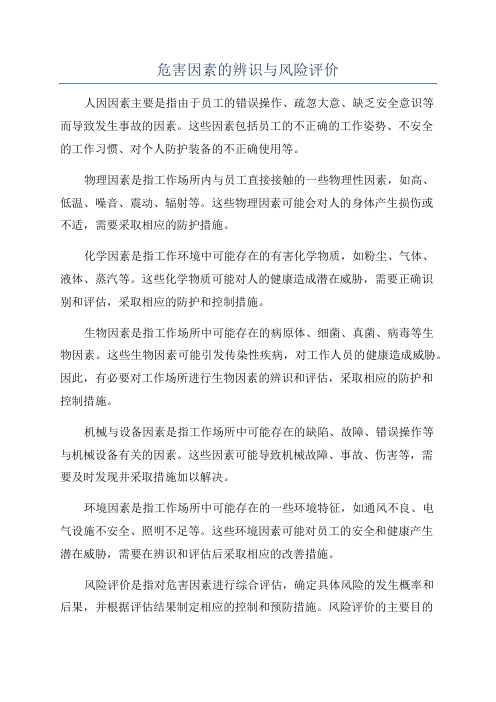
危害因素的辨识与风险评价人因因素主要是指由于员工的错误操作、疏忽大意、缺乏安全意识等而导致发生事故的因素。
这些因素包括员工的不正确的工作姿势、不安全的工作习惯、对个人防护装备的不正确使用等。
物理因素是指工作场所内与员工直接接触的一些物理性因素,如高、低温、噪音、震动、辐射等。
这些物理因素可能会对人的身体产生损伤或不适,需要采取相应的防护措施。
化学因素是指工作环境中可能存在的有害化学物质,如粉尘、气体、液体、蒸汽等。
这些化学物质可能对人的健康造成潜在威胁,需要正确识别和评估,采取相应的防护和控制措施。
生物因素是指工作场所中可能存在的病原体、细菌、真菌、病毒等生物因素。
这些生物因素可能引发传染性疾病,对工作人员的健康造成威胁。
因此,有必要对工作场所进行生物因素的辨识和评估,采取相应的防护和控制措施。
机械与设备因素是指工作场所中可能存在的缺陷、故障、错误操作等与机械设备有关的因素。
这些因素可能导致机械故障、事故、伤害等,需要及时发现并采取措施加以解决。
环境因素是指工作场所中可能存在的一些环境特征,如通风不良、电气设施不安全、照明不足等。
这些环境因素可能对员工的安全和健康产生潜在威胁,需要在辨识和评估后采取相应的改善措施。
风险评价是指对危害因素进行综合评估,确定具体风险的发生概率和后果,并根据评估结果制定相应的控制和预防措施。
风险评价的主要目的是为了确定预防与控制措施的紧急性和优先级,以便合理和有效地分配资源。
风险评价通常包括以下几个步骤:1.识别潜在危害:通过对工作环境、作业流程和员工行为的观察和分析,识别可能存在的潜在危害因素。
2.评估风险概率与后果:根据危害因素的特点、员工的暴露程度和潜在影响,评估风险的发生概率和后果,以确定风险级别。
3.制定控制和预防措施:根据评估结果,制定相应的控制和预防措施,以降低或消除风险的概率和后果。
4.实施措施和监测效果:根据制定的控制和预防措施,对其进行实施和监测,确保其有效性和可行性。
化学试验室危害因素识别和风险评价

化学试验室危害因素识别和风险评价化学试验室是一个潜在危险的工作环境,存在着各种危害因素。
为了保护工作人员的安全和健康,必须对这些危害因素进行识别和评估,以便采取相应的控制措施。
本文将重点讨论化学试验室中常见的危害因素,并介绍风险评价的方法。
一、危害因素的识别1.化学品危害:化学试验室中使用各种化学品,包括有毒物质、腐蚀剂、易燃物质等。
这些化学品可能对人体产生刺激性、损伤性、致畸性、致癌性等危害。
2.物理因素危害:物理因素包括噪音、震动、温度、湿度等。
在化学试验室中,噪音可能来自于仪器的工作声音或试验过程中的爆炸声;震动可能来自于仪器的振动或试验过程中的剧烈摇动;温度和湿度可能对试验人员的舒适度和健康产生影响。
3.生物因素危害:化学试验室中可能存在致病微生物、动物实验中的病原体等生物因素。
这些生物因素可能会引起传染病或过敏症状。
4.机械设备危害:化学试验室中使用的机械设备可能存在安全隐患,如不稳定的仪器、易于发生事故的旧设备等。
5.火灾和爆炸危害:化学试验室中存在可燃物质和易燃物质,如溶剂、气体等。
如果安全操作不当或存在其他火源,可能引发火灾和爆炸。
二、风险评价的方法1.作业分析法:通过对试验室中的工作过程进行细致的分析,确定危害源、暴露途径和受体,评估危害的可能性和严重程度。
作业分析法可以帮助识别潜在的危害因素和风险,为采取控制措施提供依据。
2.概率论方法:概率论方法通过统计数据和概率模型对风险进行评估。
例如,可以利用历史数据和概率模型来计算其中一种事故发生的概率和严重程度。
这样可以判断其中一种危害因素产生的风险是否在可接受的范围内,并采取适当的控制措施。
3.专家评价法:专家评价法是指利用专家的知识和经验对风险进行评估。
专家可以依据他们的专业知识和经验,评估其中一种危害因素的潜在风险,并提出相应的控制建议。
专家评价法可以灵活应用于不同的情况,但需要依靠专家的主观判断。
三、风险评价的目标风险评价的目标是确定潜在的危害因素和风险,并为采取控制措施提供科学依据。
《危害因素辨识、风险评价工作指南》
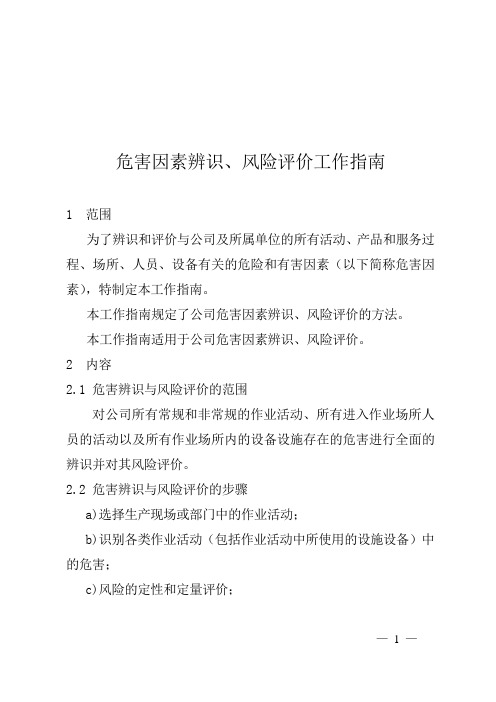
危害因素辨识、风险评价工作指南1范围为了辨识和评价与公司及所属单位的所有活动、产品和服务过程、场所、人员、设备有关的危险和有害因素(以下简称危害因素),特制定本工作指南。
本工作指南规定了公司危害因素辨识、风险评价的方法。
本工作指南适用于公司危害因素辨识、风险评价。
2内容2.1 危害辨识与风险评价的范围对公司所有常规和非常规的作业活动、所有进入作业场所人员的活动以及所有作业场所内的设备设施存在的危害进行全面的辨识并对其风险评价。
2.2 危害辨识与风险评价的步骤a)选择生产现场或部门中的作业活动;b)识别各类作业活动(包括作业活动中所使用的设施设备)中的危害;c)风险的定性和定量评价;d)确定重大风险。
2.3危害的分类根据《生产过程危险和有害因素分类代码》(GB/T13861-2009)的规定,将生产过程中的危害因素分为四类:——人的因素:在生产活动中,来自人员自身或人为性质的危害因素;——物的因素:机械、设备、设施、材料等方面存在的危害因素;——环境因素:生产作业环境中的危害因素;——管理因素:管理和管理责任缺失所导致的危害因素;2.4危害识别的方法——安全检查表:系统剖析,确定检查项目,按顺序编制表格,以提问或现场观察等方式了解检查项目的状况,确定危害因素。
——现场观察:对作业活动、设备运转或系统活动进行现场观测,分析人员、工艺、设备运转存在的危害因素。
——查阅资料:通过查阅有关事件、事故和环境监测数据等,从中发现存在的危害因素。
——座谈:召集HSE管理人员、专业人员和操作人员,集思广益、讨论分析作业活动或设备运转过程中存在的危害因素。
——工作安全分析(JSA):较细致地分析作业过程中存在危害的方法,把一项作业活动分解成几个步骤,识别每一步骤中的可能产生的危害。
适用于在各类作业活动中对作业人员操作活动中潜在危险和危害的识别,同时也适用于岗位人员工作活动的危害分析。
——工艺安全分析(PHA):通过系统的方法来识别、评估和控制工艺中的危害。
危害识别和风险评价

危害识别和风险评价危害识别和风险评价是指通过系统化的方法和流程,对可能造成的潜在危害进行辨识和评估的过程。
其主要目的是为了识别和评估潜在的危险因素,以便采取措施来减少或消除这些危险对个人、组织和环境的潜在伤害。
以下是关于危害识别和风险评价的简要分析。
首先,危害识别是指确定和辨别与特定活动、过程或环境相关的潜在危害因素。
这些危害因素可能包括物理危害(如高温、噪音、辐射等)、化学危害(如有害物质的存在)、生物危害(如病原体的传播)和人为因素(如不良操作行为)。
危害识别通常涉及对工作场所进行实地检查、调查和记录,以确定可能的危害源和其潜在的影响范围。
其次,风险评价是对已经辨识出的危害因素进行定量或定性评估,以确定其可能造成的损害和概率。
风险评价涉及到收集和分析有关可能危害源的数据,包括事故和事件的频率、严重性和潜在后果。
通过评估这些数据,可以计算出每个潜在危害因素的风险等级,以决定是否需要采取进一步的控制措施。
在进行危害识别和风险评价时,可以采用不同的方法和工具。
其中一种常用的方法是哈萨德矩阵(Hazard Matrix)方法,它将危害因素的严重性和概率进行分类,并根据这些分类确定风险等级。
此外,风险矩阵(Risk Matrix)也是常用的评估工具,它综合考虑了危害的严重性和可能性,并将其以图形方式表示。
这些方法和工具可以帮助决策者更加直观地理解风险的程度,并采取适当的控制措施。
值得注意的是,危害识别和风险评价是一个动态过程,需要不断更新和改进。
随着技术、环境和法规的变化,新的危害因素可能会出现,而旧的危害因素可能会发生变化或减少。
因此,定期的危害识别和风险评价是必要的,以确保对当前和潜在的危害因素有一个准确和全面的认识。
总结起来,危害识别和风险评价是在工作环境和活动中识别和评估潜在危害因素的过程。
它们的目的是为了保护个人、组织和环境免受潜在危害的伤害,减少事故和损失的发生。
通过合理选择和使用适当的方法和工具,可以使危害识别和风险评价更加科学和精确,并帮助决策者做出明智的决策来管理潜在的风险。
危害因素辨识风险评价及风险控制管理制度
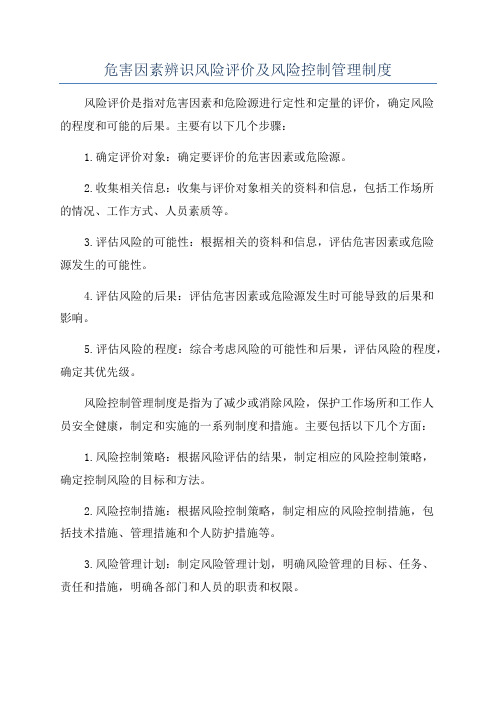
危害因素辨识风险评价及风险控制管理制度风险评价是指对危害因素和危险源进行定性和定量的评价,确定风险
的程度和可能的后果。
主要有以下几个步骤:
1.确定评价对象:确定要评价的危害因素或危险源。
2.收集相关信息:收集与评价对象相关的资料和信息,包括工作场所
的情况、工作方式、人员素质等。
3.评估风险的可能性:根据相关的资料和信息,评估危害因素或危险
源发生的可能性。
4.评估风险的后果:评估危害因素或危险源发生时可能导致的后果和
影响。
5.评估风险的程度:综合考虑风险的可能性和后果,评估风险的程度,确定其优先级。
风险控制管理制度是指为了减少或消除风险,保护工作场所和工作人
员安全健康,制定和实施的一系列制度和措施。
主要包括以下几个方面:
1.风险控制策略:根据风险评估的结果,制定相应的风险控制策略,
确定控制风险的目标和方法。
2.风险控制措施:根据风险控制策略,制定相应的风险控制措施,包
括技术措施、管理措施和个人防护措施等。
3.风险管理计划:制定风险管理计划,明确风险管理的目标、任务、
责任和措施,明确各部门和人员的职责和权限。
4.风险监测和评估:定期对风险控制措施进行监测和评估,及时发现和解决问题,确保风险控制的有效性。
5.风险沟通和培训:加强风险沟通和培训,提高员工对风险的认识和控制能力,增强风险意识和安全意识。
总之,危害因素辨识、风险评价及风险控制管理制度在工作场所安全管理中起着重要的作用。
通过系统地辨识危害因素、评价风险和制定控制措施,可以减少和消除工作场所的危险因素,保护员工的生命安全和身体健康。
危险有害因素识别与风险评价

目的:根据风险分析结果,制定控制措施,编制作业活动安全操作规程,控制风险。
选定作业活动。
3
分解工作步骤。
4
把正常的工作分解为几个主要步骤,即首先做什么、其次做什么等等。
5
用几个字说明一个步骤,只说做什么,不说如何做。
6
班组集体讨论。
工作危害分析(JHA)
识别每一步骤的主要危险、有害因素和后果。 识别思路:1、谁会受到伤害?(人、财产、环境)2、伤害的后果是什么?3、找出造成伤害的原因(危害) 识别现有安全控制措施 管理措施、人员胜任、安全设施
风险及风险评价
风险—发生特定危害事件的可能性与后果的结合。 风险评价—评价风险程度并确定其是否在可接受范围的全过程。 可承受的风险—根据用人单位的法律义务和职业安全健康与环境方针,用人单位可接受的风险。
风险及风险评价
单击此处添加小标题
= ×
单击此处添加小标题
风险度R
单击此处添加小标题
可能性L
1
有充分、有效的防范、控制、监测、保护措施,或员工安全卫生意识相当高,严格执行操作规程。极不可能发生事故或事件。
事件发生的可能性(L)
风险度
等级
应采取的行动/控制措施
实施期限
20-25
巨大风险
在采取措施降低危害前,不能继续作业,对改进措施进行评估
立刻
15-16
重大风险
采取紧急措施降低风险,建立运行控制程序,定期检查、测量及评估
发生死亡
部分装置( > 2套)或设备停工
大规模、公司外
重大国际国内影响
4
潜在违反法规
丧失劳动能力
2套装置停工、或设备停工
公司内严重污染
行业内、省内影响
危害因素辨识风险评价及风险控制管理制度

危害因素辨识风险评价及风险控制管理制度一、引言危害因素辨识风险评价及风险控制管理制度是一种重要的管理工具,旨在识别和评估潜在风险,并采取相应的控制措施以减少或消除风险。
本文将对危害因素辨识、风险评价以及风险控制管理制度的相关内容进行介绍和讨论。
二、危害因素辨识危害因素辨识是指识别潜在的危害因素,即可能导致事故、伤害或损失的因素。
常见的危害因素包括但不限于物理因素、化学因素、生物因素、人为因素以及环境因素等。
在进行危害因素辨识时,可以采用多种方法,如现场观察、实验分析、历史数据分析等。
三、风险评价风险评价是对潜在风险的严重程度和可能性进行定量或定性的评估。
通过风险评价,可以确定风险的优先级,为制定相应的控制措施提供依据。
常用的风险评价方法有风险矩阵法、层次分析法、事件树分析法等。
在进行风险评价时,需要考虑以下几个因素:1.风险的严重程度:即风险发生时可能造成的损失的大小和影响的程度。
2.风险的可能性:即风险发生的概率或频率。
3.风险的暴露度:即人员、财产或环境暴露在风险之下的程度。
四、风险控制管理制度风险控制管理制度是为了减少或消除潜在风险而制定的一套管理措施和方法。
制定风险控制管理制度时,需要考虑以下几个方面:1.风险控制目标:确定减少或消除风险的具体目标。
2.风险控制措施:制定相应的控制措施,包括技术措施、管理措施和人员培训等。
3.风险控制责任:确定风险控制的责任人和责任部门,明确责任分工。
4.风险控制监督:建立监督机制,对风险控制措施的执行情况进行监督和检查。
五、风险控制管理制度的实施风险控制管理制度的实施需要以下几个步骤:1.制定风险控制计划:根据风险评价的结果,制定相应的风险控制计划,明确控制目标和措施。
2.实施风险控制措施:按照计划,执行相应的风险控制措施,确保其有效实施。
3.监督和检查:建立监督机制,对风险控制措施的执行情况进行监督和检查,及时发现和纠正问题。
4.评估和改进:定期评估风险控制管理制度的实施效果,根据评估结果调整和改进制度。
危害因素的辨识与风险评价

辩识方法辩识危害因素的辨识方法采取一种或结合多种评估方法。
主要的评价方法有询问交谈、现场勘查、查阅有关记录、获取外部信息、平安检查〔SCL〕、工作危险源分析〔JHA〕、预先危害因素分析〔PHA〕、故障假说分析〔WI〕、失效模式与影响分析〔FMEA〕、危害与可操作性研究〔HAZOP〕。
危害因素辩识方法第一类危险源第一类危险源:系统中存在的、可能发生意外释放的各种能量或危险物质。
1、危险物质辨识:如氢气、原油、天然气、液化气、汽油、乙决、甲烷、煤油等可燃物质;硫化氢、一氧化碳、氯、氨、二氧化碳、氮气二氧化硫、甲醇等有毒物质;生产过程中使用的危险化学品。
2、能量辨识:辨识产生、供应能量和能量的载体。
包括以下几个方面:a.具的动能的各类机械运动部件、工件和人体及产生的机械性、动力性等振动部件。
b.具有势能的平台及坑、井、沟口处等场所上的人体和物体。
c.带电体的电能,包括雷电、静电;d.高温设备和管线的热外表、高温介质及剧烈热反响工艺装置的热能及低温介质所具有的冷量。
e.盛装具有能量的介质的压力容器。
f.机械性、动力性等噪声的声能。
g.化学反响的化学能。
h.紫外线、激光射频辐射,超高压电场等非电离辐射等。
第二类危险源第二类危险源:对第一类危险源控制设施和措施失控的状态和行为。
主要包括以下几个方面:1、控制设施和措施缺陷。
无控制设施和措施或控制设施不符合法律、法规、标准和设计标准等要求。
控制措施不好,起不到应有的作用。
2、人员失误:人的不平安行为中产生不良后果的行为。
3、管理缺陷:缺少规章制度、操作规程、工作职责不明确;组织不全;缺乏协调或协调不当、检查不及时、不到位;奖惩不清楚;培训不到位等。
4、作业环境和场所不良:引起设备故障或人员失误的温度、温度、风雨雪、照明、视野、噪声、扰动、通风换气,色彩、作业区环境不良等环境因素。
危险源识别方法简介一、工作危险源分析〔JHA〕:是一种较细致地分析工作过程中存在危险源的方法,把一项工作活动分解成几个步骤,识别每一步骤中的危险源和可能的事故,设法消除危险源。
- 1、下载文档前请自行甄别文档内容的完整性,平台不提供额外的编辑、内容补充、找答案等附加服务。
- 2、"仅部分预览"的文档,不可在线预览部分如存在完整性等问题,可反馈申请退款(可完整预览的文档不适用该条件!)。
- 3、如文档侵犯您的权益,请联系客服反馈,我们会尽快为您处理(人工客服工作时间:9:00-18:30)。
辩识方法
辩识危害因素的辨识方法采取一种或结合多种评估方法。
主要的评价方法有询问交谈、现场勘查、查阅有关记录、获取外部信息、安全检查(SCL)、工作危险源分析(JHA)、预先危害因素分析(PHA)、故障假说分析(WI)、失效模式与影响分析(FMEA)、危害与可操作性研究(HAZOP)。
危害因素辩识方法
第一类危险源
第一类危险源:系统中存在的、可能发生意外释放的各种能量或危险物质。
1、危险物质辨识:如氢气、原油、天然气、液化气、汽油、乙决、甲烷、煤油等可燃物质;硫化氢、一氧化碳、氯、氨、二氧化碳、氮气二氧化硫、甲醇等有毒物质;生产过程中使用的危险化学品。
2、能量辨识:辨识产生、供给能量和能量的载体。
包括以下几个方面:
a.具的动能的各类机械运动部件、工件和人体及产生的机械性、动力性等振动部件。
b.具有势能的平台及坑、井、沟口处等场所上的人体和物体。
c.带电体的电能,包括雷电、静电;
d.高温设备和管线的热表面、高温介质及剧烈热反应工艺装置的热能及低温介质所具有的冷量。
e.盛装具有能量的介质的压力容器。
f.机械性、动力性等噪声的声能。
g.化学反应的化学能。
h.紫外线、激光射频辐射,超高压电场等非电离辐射等。
第二类危险源
第二类危险源:对第一类危险源控制设施和措施失控的状态和行为。
主要包括以
下几个方面:
1、控制设施和措施缺陷。
无控制设施和措施或控制设施不符合法律、法规、标准和设计规范等要求。
控制措施不好,起不到应有的作用。
2、人员失误:人的不安全行为中产生不良后果的行为。
3、管理缺陷:缺少规章制度、操作规程、工作职责不明确;组织不全;缺乏协
调或协调不当、检查不及时、不到位;奖惩不分明;培训不到位等。
4、作业环境和场所不良:引起设备故障或人员失误的温度、温度、风雨雪、照明、视野、噪声、扰动、通风换气,色彩、作业区环境不良等环境因素。
危险源识别方法简介
一、工作危险源分析(JHA):
是一种较细致地分析工作过程中存在危险源的方法,把一项工作活动分解成几个步骤,识别每一步骤中的危险源和可能的事故,设法消除危险源。
分析步骤:
(1)把正常的工作分解为几个主要步骤,即首先做什么、其次做什么等等,用3—4个词说明一个步骤,只说做什么,而不说如何做;
分解时应:
——观察工作
——与操作者一起讨论研究
——运用自己对这一项工作的知识
——结合上述三条
(2)对于每一步骤要问可能发生什么事故,给自己提出问题,比如操作者会被什么东西打着、碰着;他会撞着、碰着什么东西;操作者会跌倒吗;有无危险源暴露,如毒气、辐射、焊光、酸雾等等;
(3)识别每一步骤的主要危险源后果;
(4)识别现有安全控制措施;
(5)进行风险评价;
(6)建议安全工作步骤。
二、安全检查表分析(SCL):
是基于经验的方法,是分析人员列出一些项目,识别与一般工艺设备和操作有关的已知类型的危险源、设计缺陷以及事故隐患。
安全检查分析表分析可用于对物质、设备或操作规程的分析。
分析步骤:
(1)建立安全检查表,分析人员从有关渠道(如内部标准、规范、作业指南)选择合适的安全检查表。
如果无法获取相关的安全检查表,分析人员必须运用自己的经验和可靠的参考资料制定检查表;
(2)分析者依据现场观察、阅读系统文件、与操作人员交谈、以及个人的理解,通过回答安全检查表所列的问题,发现系统的设计和操作等各个方面与标准、规定不符的地方,记下差异;
(3)分析差异(危险源),提出改正措施建议。
三、故障假设分析(WI):
故障假设分析方法是对工艺过程或操作的创造性分析方法。
危险分析人员在分析会上围绕分析人员所确定的安全分析项目对工艺过程或操作进行分析,鼓励每个分析人员对假定的故障问题发表不同看法。
故障假设分析方法可用于设备设计和操作的各个方面(如建筑物、动力系统、原料、产品、贮存、物料的处理、装置环境、操作规程、管理规程、装置的安全保卫等)。
对于一个简单的系统,故障假设分析只需要一个或两个分析人员就能够进行。
分析步骤:
(1)确定分析范围,分析装置及工艺过程,包括工艺过程说明、图纸、操作规程、装置的安全防范、安全设备、卫生控制规程;
(2)依据工艺流程,分别提出故障假设问题,集中主要危险源部位;
(3)识别每一故障假设问题的主要危险源后果;
(4)识别现有安全控制措施;
(5)进行风险评价;
(6)建议改进措施。
四、预危险源性分析(PHA):
主要是在项目发展的初期(如概念设计阶段)识别可能存在的危险源,是今后危险源性分析的基础。
当只希望进行粗略的危险源和潜在可能性分析时,也用PHA对已建成的装置进行分析。
分析步骤:
(1)收集装置或系统的有关资料,以及其他可靠的资料(如任何相同或相似的装置,或者即使工业过程不同但使用相同的设备和物料),知道过程所包含的主要化学物品、反应、工艺参数、主要设备的类型(如容器、反应器、换热器等)、装置的基本操作说明书、防火及安全设备;
(2)识别可能导致不希望的后果的主要危险源和事故的情况,考虑:——危险设备和物料,如有毒物质、爆炸、高压系统;
——设备与物料之间的与安全有关的隔离装置,如物料的相互作用、火灾/爆炸的产生和发展、控制/停车系统;
——影响设备和物料的环境因素,如地震、洪水、静电放电;
——操作、测试、维修及紧急处理规程;
——与安全有关的设备、如调节系统、备用、灭火及人员保护设备。
(3)分析这些危险源的可能原因及导致事故的可能后果。
通常并不需找出所有的原因以判断事故的可能性,然后分析每种事故所造成的后果,这些后果表示可能事故的最坏的结果;
(4)进行风险评价;
(5)建议消除或减少风险控制措施。
五、失效模式与影响分析(FMEA):
失效模式与影响分析就是识别装置或过程内单个设备或单个系统(泵、阀门、液位计、换热器)的失效模式以及每个失效模式的可能后果。
失效模式描述故障是如何发生的(打开、关闭、开、关、损坏、泄漏等),失效模式的影响是由设备故障对系统的应答决定的。
分析步骤:
(1)确定FMEA的分析项目、边界条件(包括确定装置和系统的分析主题、其他过程和公共/支持系统的界面);
(2)标识设备:设备的标识符是唯一的,它与设备图纸、过程或位置有关;
(3)说明设备:包括设备的型号、位置、操作要求以及影响失效模式和后果特征(如高温、高压、腐蚀);
(4)分析失效模式:相对设备的正常操作条件,考虑如果改变设备的正常操作条件后所有可能导致的故障情况;
(5)说明对发现的每个失效模式本身所在设备的直接后果以及对其他设备可能产生的后果,以及现有安全控制措施;
(6)进行风险评价;
(7)建议控制措施。
六、危险与可操作性分析(HAZOP):
HAZOP分析是系统、详细地对工艺过程和操作进行检查,以确定过程的偏差是否导致不希望的后果。
该方法可用于连续或间歇过程,还可以对拟定的操作规程进行分析。
HAZOP的基本过程以关键词为引导,找出工作系统中工艺过程或状态的变化(即偏差),然后继续分析造成偏差的原因、后果以及可以采取的对策。
HAZOP分析需要准确、最新的管道仪表图(P&ID)、生产流程图、设计意图及参数、过程描述。
对于大型的、复杂的工艺过程,分析人员需要5-7人,包括设计、工艺或工程、操作、维修、仪表、电气、公用工程等方面的人员;对相对较小的工艺过程,可组成3-4人具有丰富经验的分析小组。
分析步骤:
(1)选择一个工艺单元操作步骤,收集相关资料;
(2)解释工艺单元或操作步骤的设计意图;
(3)选择一个工艺变量或任务;
(4)对工艺变量或任务用引导词开发有意义的偏差;
(5)列出可能引起偏差的原因,偏差如何出现,操作员如何知道偏差;
(6)解释与偏差相关的后果;
(7)识别现有防止偏差的安全控制措施或保护装置;
(8)基于后果、原因和现有安全控制措施或保护装置评估风险度;
(9)建议控制措施。
风险评价方法
(L×S法)
评估危险源及影响后果的严重性(S)
危险源发生的可能性(L)及频率
风险评价等级表。