能量集成及换热网络设计
化工设计竞赛换热网络与热集成(0002)

换热网络与热集成我国国民经济正处于一个高速发展的时期,这就不可避免地出现能源消耗的大幅度上升。
当前我国的能源消费量已超过世界能源消费总量的10%,但是我国的人均能源消费量仅约为世界平均水平的50%,这种情况表明未来我国经济发展所面临的能源问题将更加突出、更加严峻。
为了保证国民经济持续、快速、健康地发展,必须合理、有效地利用能源,不断提高能源利用效率。
在大型过程系统中,存在大量需要换热的流股,一些物流需要被加热,一些物流需要被冷却。
大型过程系统可以提供的外部公用工程种类繁多,如不同压力等级的蒸汽,不同温度的冷冻剂、冷却水等。
为提高能量利用率,节约资源与能源,就要优先考虑系统中各流股之间的换热、各流股与不同公用工程种类的搭配,以实现最大限度的热量回收,尽可能提高工艺过程的热力学效率。
热集成网络的分析与合成,本质上是设计一个由热交换器组成的换热网络,使系统中所有需要加热和冷却的物流都达到工艺流程所规定的出口温度,使得基于热集成网络运行费用与换热设备投资费用的系统总费用最小。
1.1 热集成1.1.1 概述进行流程的冷热流股之间的能量匹配设计并构建换热网络。
热集成旨在最大程度的利用流程内部的能量,减少公用工程的消耗,从而减少操作费用,降低生产成本。
通过对流程流股的深入分析,利用Aspen Energy Analyzer 设计换热网络,其主要步骤如下:(1)确定流程中需要换热的冷流股和热流股;(2)利用物流数据做出冷热流股的温焓图和总组合曲线图(GCC);(3)确定最小传热温差;(4)找出夹点及最小冷、热公用工程用量;(5)构建优化换热网络。
由于跨车间换热对管道伴热要求较高,使用的管道经济投资较大,在换热网络处理中,本设计将原料预处理工段、反应工段、二氧化碳捕集工段和分离提纯工段分别进行换热网络设计。
夹点设计技术原则:(1)流股数目准则夹点以上只能用热公用工程进行加热,所有的热流股都要用冷流股冷却到热夹点温度,夹点以下只能用冷公用工程进行冷却,所有的冷流股都要用热流股加热到冷夹点温度。
换热器网络的综合

换热器网络综合:确定具有最小设备投资,最小操作费用,能达
到过程要求的换热器网络结构。
具有可控性、稳定性和可操作性。
方法:
夹点设计法
有效能法
温度间隔法
热力学温差贡献法
数学规划法
5.2 夹点设计法
夹点设计法的基本原则: (1) 应该避免有热流量通过夹点; (2) 夹点上方避免引入公用工程冷却物流; (3) 夹点下方避免引入公用工程加热物流 。
夹点设计法的要点: (1)在夹点处,换热网络分隔开,热端和冷端分别处理。 (2)热端和冷端都先从夹点开始设计,遵循夹点匹配可行
性规则及经验规则。
(3)离开夹点后,采用经验规则,但传热温差约束紧张时 还应遵循可行性规则。
(4)考虑换热系统的操作性、安全性,以及生产工艺上特 殊要求等。
违背以上三条,就会增大公用工程负荷及相应的设 备投资。
5.2.1 夹点处物流间匹配换热的可行性规则
夹点匹配:指冷、热物流同时有一端直接与夹点相同,即同 一端具有夹点处的温度。
夹点匹配 非夹点规则: 规则1 对于夹点上方,热工艺物流(包括其分支物流)的数目 NH不大于冷工艺物流(包括其分支物流)数目NC,即:
5.2.2 物流间匹配换热的经验规则
经验规则1 每个换热器的热负荷应等于该换热器冷热物流匹配 中热负荷较小者,以保证经过一次换热,既可以使一个物流达 到规定的目标温度,以减少所用换热设备的数量。
经验规则2 应尽量选择热容量流率相近的冷、热流体进行匹配换 热,使得换热器在结构上相对合理,且在相同的热负荷及相同的 有效能损失下,其传热温差最大。
NH NC
H1
3
H2
1
H3
2
C4
化工设计大赛-作品创新性说明
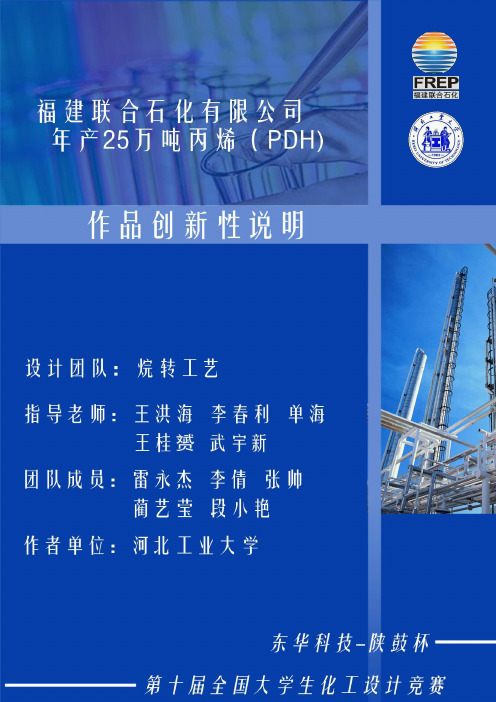
目录第1章反应器设计创新 (3)第2章分离技术与节能降耗技术创新 (8)第3章高效塔板的使用 (13)第4章高效催化剂的使用 (14)第5章工艺路线创新 (15)第6章环保技术创新 (16)第7章安全仪表系统SIS设计 (19)第1章反应器设计创新通过六个步骤,实现了丙烷脱氢反应器从无到有的完整设计。
设计思路如下:图1-1 反应器设计思路其中,反应器模拟模型的构建是通过Polymath实现的。
1.以目标产物丙烯的摩尔分率作为分析变量丙烷脱氢的主副反应如下:主反应:C3H8→C3H6+H2 △Hr=116.0754KJ/mol副反应:C3H8→C2H4+CH4 △H r=75.8671KJ/molC2H4+H2→C2H6△H r=-136.98KJ/molC3H8+H2→C2H2+C+4H2 △H r=330.595KJ/mol可以看出,丙烷脱氢是一系列的平行连串反应。
对于复合反应,我们不能单纯的考虑关键反应物丙烷的转化率,也要关注目标产物丙烯的选择性和收率。
所以本次设计以目标产物丙烯在混合气体中的摩尔分率为分析变量,分别找到丙烷和丙烯的最优转化率和选择性。
2.催化剂结焦本项目采用UOP公司的Oleflex生产工艺,装置为绝热式径向移动床反应器,催化剂是该公司自主研发高活性、高选择性的Pt-Sn/Al2O3。
由于反应条件是高温,会导致丙烷深度脱氢,并且在高温下C-C键裂解反应在热力学上比C-H键裂解更有利,这也加剧了碳(C )在催化剂表面沉积导致Pt-Sn/Al 2O 3催化剂失活。
本次设计采用新平《丙烷脱氢氧化制丙烯过程的模型化与优化》的动力学模型及参数,考虑结焦量对反应速率的影响,通过Polymath 对反应器进行模拟和优化,最终得到合适的反应器尺寸。
结焦动力学方程摘录如下:c k Cm C c k dtdC2)max (*12+-=C=C m +C M]*1max*1*1[*max 2tc k C tc k C Cm +=C M =k2c*t))11(*exp(*0tmt R Eaic ic k kic --= ]*3exp[**2)*11(CmCMa Cm a Cm a a -+-= ))11(1exp(*011tm t R Eaa a a --=部分动力学参数如下:表1-1 动力学参数表Polymath程序模拟与优化如下(R201):图1-2 Polymath模拟与优化程序丙烯摩尔分率沿反应器径向的变化:图1-3 丙烯摩尔分率沿反应器径向的变化得到各反应器的尺寸如下:表1-2 各反应器尺寸反应器位号 气体出口径/mm 反应器径/mm 催化剂床层厚度/mm 催化剂床层长度/m 材料 R202 1200 2400 340 6 0Cr18Ni9 R203 1200 2400 340 6 0Cr18Ni9 R204 1200240042060Cr18Ni9经过优化的反应器模型可使丙烷的单程转化率可达38%,丙烯总的选择性可达90%,总的收率可达70%,年产可达25万吨,满足设计要求。
化工过程的能量分析

热交换网络的提出 一个化工生产过程的流程中,经常需要加热或冷却许多流股,用热水、蒸汽加热或用冷却水、冷冻液冷却。这种设计虽简单,设备投资费较少,但热力学效率常常是很低,能耗较 大,显然是不经济。 在流程内部用需要被冷却的较高温的流股来加热需要热量的低温的流股,可以实现能量的有效利用,从而节约了能量源,降低成本。
二、基本概念及热交换系统表示方法
换热网络的名词 热流:热交换网络内,那些需要由起始温度冷却到目标温度的流股。 冷流:热交换网络内,那些需要由起始温度被加热到目 标温度的流股。
在流程内建立热交换网络的根本目的:
减少流程对外界热源和冷源的需求,尽量使用流程内部的冷热流股互相搭配,以达到节约能源的目的。
热容流率的可行性原则
窄点处传热的温差最小为 △Tm,离开窄点处的传热温差应大于等于△Tm,即△T>△Tmin 因此,每个窄点匹配的流股热容流率应满足 窄点以上 CP热 < CP冷 窄点以下 CP热 > CP冷 同样上两式,可以合并成为一式,即窄点同一侧应满足 CP出 > CP入
3理想功、损失功和热力学效率
理想功是指系统在一定的环境下,沿着完全可逆的途径从一个状态变到另一个状态所能产生的最大有用功或必须消耗的最小有用功。 开系稳流过程的理想功计算式: Wid = ΔH - T0ΔS 损失功是由于过程的不可逆是系统产生熵而引起的作功能力的损失,不可逆过程的损失功计算式: WL = T0 ( ΔSsys + ΔSsur ) = T0ΔSt = T0ΔSg 损失功WL反映了实际过程的不可逆程度。
总流股数可行性原则 窄点以上流股数应满足 N热 < N 冷 窄点以上流股数应满足 N热 > N 冷 式中 N热 ------- 热流股数 N冷 ------- 冷流股数 根据前面的热交换网络的表示法,对于窄点来说,窄点以上热流股是流入的,冷流股是流出的。同样,窄点以下热流股是流出的,冷流股是流入的。所以上式可以合并用一个式子来表示,即在窄点的同一侧流股数必须满足: N流出 > N流入
_换热网络_夹点设计法完整版
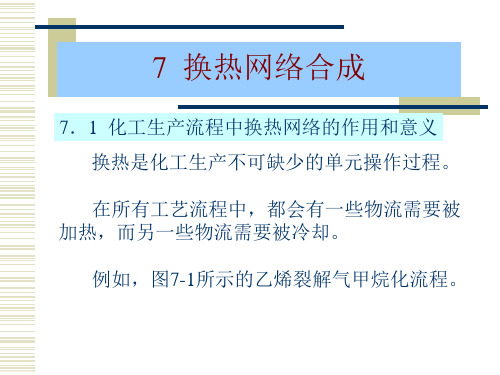
T(℃)
T(℃)
Q(kw)
H1 H2 C1 C2
2.0 8.0 2.5 3.0
150 90 20 25
60 60 125 100
180 240 262 225
一、夹点位置的确定及其意义:
1、采用问题表格法确定夹点位置 应用前提:各物料的比热可视为常数。 问题表格法求解夹点的步骤: (1)作出问题表格: 具体作法: a、分别作出冷热两侧流体标尺,标尺 的刻度相差△Tmin。
冷热物流按各自的始温终温落入相应的温度区间注意热物流的始湿终温应减去最小允许温差tmin由于落入各温度区间的物流已考虑了温度推动力所以在每个温度区间内都可以把热量从热物流传给冷物流即热量传递总是满足第二定律
7 换热网络合成
7.1 化工生产流程中换热网络的作用和意义
换热是化工生产不可缺少的单元操作过程。
Ik
DK Dk =
Ok
0 冷热均衡。 > 0 需外部提供热量。 < 0 有剩余热量。
Ik
DK
Ok
Ik:外界或其它网络供给 k 网的热,输入。 Ok:k网向外部或其它网排出的热量,输出。 则: 热衡式: Ik = Ok + Dk 变形:Ok = Ik – Dk (k = 1,2…N) 同时由于各网格间联系的存在,有: Ik+1 = Ok
热标尺
160
110
80
50 35 30
SN6
C2
C1
20
H1
H2
(2)对每个网格进行热量衡算
定义Dk:本网格需要的热量,或称本网格冷热 物流换热赤字(相当于输出)。显然: Dk = ∑Cpcold ( Tk – Tk+1 ) –∑Cphot (Tk’ – Tk+1’) = (∑Cpcold - ∑Cphot ) (Tk – Tk+1 )
换热网络.ppt

• 第一节 换热网络合成的基本问题 • 第二节 夹点技术基础 • 第三节 夹点设计
第四章
第一节 换热网络合成的基本问题
一、换热网络的合成
• 换热器网络的最优合成,就是要合成出一定意义上最优的, 并满足把过程的每个物流由初始温度加热或冷却到目标温 度的换热器网络。
给定的条件
1. 一些需要加热的物流和一些需要冷 却的物流
H1 240 960 1200
Heat into 480 960
H1
H2
C1
100
C2
60
C3
60
200
C4
C5
300
CU1
175
H3
H4
H5
HU1
300
200
50
125
150
400
100
100
200
方案3的改进
FCp=3 H1
600
FCp=1 C1
100
Q=480 580
FCp=2
C2
100
220
Q=240
580 Q=720
122000
220400
200
检验可行性:是否满足最小温差20度
第四章
第二节 夹点技术的基础理论
换热网络的设计步骤
(1)选择过程物流以及所要采用的公用工程加热、 冷却物流的等级;
(2)确定适宜的物流间匹配换热的最小允许传热 温差以及公用工程加热与冷却负荷;
(3)综合出一组候选的换热网络; (4)对上述网络进行调优,得出适宜的方案; (5)对换热设备进行详细设计,得出工程网络; (6)对工程网络作模拟计算,进行技术经济评价
和系统操作性分析。如对结果不满意,返回第 (2)步,重复上述步骤,直至满意;
换热网络集成与优化研究进展_王彧斐
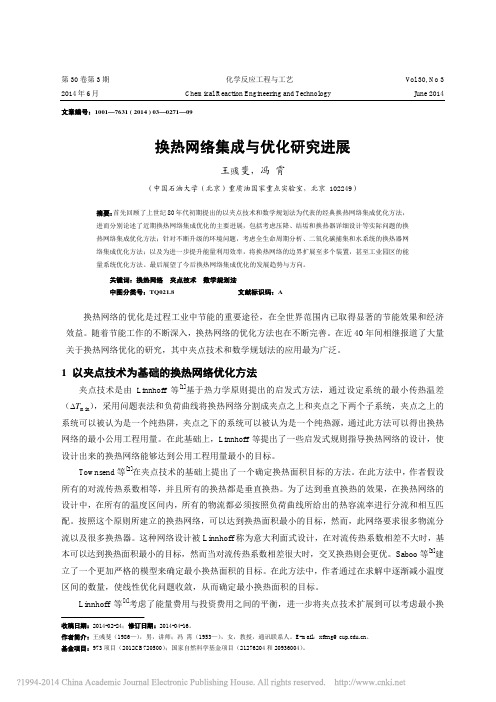
第30卷第3期 化学反应工程与工艺 V ol 30, No 3 2014年6月 Chemical Reaction Engineering and Technology June 2014 收稿日期:2014-02-24;修订日期:2014-04-16。
作者简介:王彧斐(1986—),男,讲师;冯 霄(1953—),女,教授,通讯联系人。
E-mail :xfeng@ 。
基金项目:973项目(2012CB720500);国家自然科学基金项目(21276204和20936004)。
文章编号:1001—7631 ( 2014 ) 03—0271—09换热网络集成与优化研究进展彧王斐,冯 霄(中国石油大学(北京)重质油国家重点实验室,北京 102249)摘要:首先回顾了上世纪80年代初期提出的以夹点技术和数学规划法为代表的经典换热网络集成优化方法,进而分别论述了近期换热网络集成优化的主要进展,包括考虑压降、结垢和换热器详细设计等实际问题的换热网络集成优化方法;针对不断升级的环境问题,考虑全生命周期分析、二氧化碳捕集和水系统的换热器网络集成优化方法;以及为进一步提升能量利用效率,将换热网络的边界扩展至多个装置,甚至工业园区的能量系统优化方法。
最后展望了今后换热网络集成优化的发展趋势与方向。
关键词:换热网络 夹点技术 数学规划法中图分类号:TQ021.8 文献标识码:A换热网络的优化是过程工业中节能的重要途径,在全世界范围内已取得显著的节能效果和经济效益。
随着节能工作的不断深入,换热网络的优化方法也在不断完善。
在近40年间相继报道了大量关于换热网络优化的研究,其中夹点技术和数学规划法的应用最为广泛。
1 以夹点技术为基础的换热网络优化方法夹点技术是由Linnhoff 等[1]基于热力学原则提出的启发式方法,通过设定系统的最小传热温差(∆T min ),采用问题表法和负荷曲线将换热网络分割成夹点之上和夹点之下两个子系统,夹点之上的系统可以被认为是一个纯热阱,夹点之下的系统可以被认为是一个纯热源,通过此方法可以得出换热网络的最小公用工程用量。
换热器网络的优化及可视化

未来需要进一步深入研究微通道换热器的性能提升、成本控制以及应用领域的 拓展等问题。
谢谢观看
参考内容
在能源转换和利用领域,换热器作为一种重要的设备,其性能优劣直接影响到 整个系统的效率和成本。本次演示将围绕换热器的热力学分析与优化设计进行 深入探讨,旨在提高换热器的性能和降低能耗。
换热器在各种工业过程中扮演着重要角色,例如在石油化工、制冷、核能等领 域。然而,随着能源成本的上升和对环保的重视,对换热器性能的要求也越来 越高。因此,对换热器进行热力学分析并寻求优化设计方案具有重要意义。
选型管壳式换热器需要遵循一定的步骤。首先,需要初步确定换热器的类型和 规格,这需要根据工艺要求和实际需求进行选择。接着,需要考虑与换热器相 连接的管道规格和尺寸,以确保流体流速和流量适应换热器的要求。随后,需 要计算流体的流量、温度等参数,以确定换热器的传热系数和热阻,并评估其 是否满足工艺要求。最后,还需要考虑设备的材料、加工精度、保温和防腐等 方面的因素,以确保换热器具有较高的可靠性和使用寿命。
管壳式换热器是一种将两种不同温度的流体通过热交换实现能量传递的设备。 它主要由壳体、管束、折流板、进出口等组成。根据不同的工艺要求和应用场 景,管壳式换热器可以分为多种类型,如单管程、多管程、套管式等。这些不 同类型的换热器具有各自的特点和适用范围,因此,在优化选型时,需要根据 实际需求进行选择。
三、优化设计
微通道换热器的优化设计主要涉及以下几个方面:通道数、通道直径、通道长 度、流动方式等。这些参数的选择和设计直接影响到换热器的传热效果和阻力 损失。具体优化方法如下:
1、参数优化:通过调整通道数、通道直径和通道长度等参数,寻求最佳的传 热效果和阻力损失。
2、数值优化:借助数值模拟方法,对微通道换热器进行性能预测和优化。常 用的数值模拟软件包括Fluent、ANSYS等。
- 1、下载文档前请自行甄别文档内容的完整性,平台不提供额外的编辑、内容补充、找答案等附加服务。
- 2、"仅部分预览"的文档,不可在线预览部分如存在完整性等问题,可反馈申请退款(可完整预览的文档不适用该条件!)。
- 3、如文档侵犯您的权益,请联系客服反馈,我们会尽快为您处理(人工客服工作时间:9:00-18:30)。
2018年“东华科技-陕鼓杯”第十二届全国大学生化工设计竞赛中石化镇海炼化分公司年产1.2万吨叔丁胺和1.8万吨聚异丁烯项目能量集成及换热网络设计ZJU C.E.O团队叶骐瑜陈宁洁方譽錡俞彬彬李锦秀指导老师:***目录1概述 (3)2原始工艺流股提取 (3)3原始工艺流股的能耗分析 (4)4工艺流程的改进 (6)5改进工艺流股的提取及分析 (7)6换热网络设计 (10)7热泵技术分析 (13)8相变潜热利用分析 (14)9节能技术利用总结 (15)10总结 (16)1概述本项目是中石化镇海炼化分公司MTBE来源粗异丁烯利用子项目。
该项目采用传统的MTBE精制路线,直接以镇海炼化MTBE生产装置裂解提纯得到高纯异丁烯,利用部分高纯异丁烯来生产1.8万吨/年的纯度为99.7%的中分子量聚异丁烯,另一部分高纯异丁烯进一步催化胺化生产 1.2万吨/年附加值更高的叔丁胺。
运行操作成本是一个重要评价参数。
原料的预热、精馏等都是非常耗能的过程,会消耗大量的公用工程。
本项目工艺由异丁烯提纯、叔丁胺合成、叔丁胺提纯、异丁烯聚合和聚异丁烯后处理五个工段组成。
流程中冷热物流均比较多,潜在的热量可供回收,通过对换热网络的设计和优化,可以尽可能地实现流程内部热量的集成和最大化利用,以减少公用工程的消耗,降低能耗。
为此,我们运用Aspen Energy Analyzer V10软件来进行换热网络的设计,并且寻找可能节能的措施,以最大限度的降低成本。
通过对本项目工艺流股温位和换热要求的分析,为了尽可能降低系统能耗费用以及母厂可供公用工程的来源,本换热网络需要的冷公用工程包括循环冷却水、空气和冷冻剂,热公用工程包括为125℃的低压蒸汽、175℃的中压蒸汽、250℃的高压蒸汽和400℃的热油,均可由厂区公用工程站和冷冻站提供,形成与母厂的公用工程集成。
通过对系统工艺流股的能耗分析,为了尽可能地利用组合曲线平台区潜热,在工艺流程中采用了双效精馏技术和热泵技术,并进一步进行了换热网络的集成和优化,可以回收热量10782.97kW,占比27.21%,效精馏技术和热泵的采用消耗了约31kW,总计节约能量约10751.97Kw。
2原始工艺流股提取根据所设计的工艺流程的Aspen模拟结果,由Aspen Energy Analyzer V10分析后提取的流股如下表1和表2所示(物流号及设备标号参照[1-原始工艺流股(全流股模拟,不含热泵、双效精馏).bkp])。
表中并不包含反应器R0101、R0201以及R0401所需的换热要求,其解决方案在下节工艺流股能耗分析中进一步说明。
表1 工艺过程物流信息表(不含节能措施)表2 塔设备物流信息表(不含节能措施)3原始工艺流股的能耗分析在Aspen Energy Analyzer V10中评估了最小传热温差对系统经济性的影响,获得系统总费用与最小传热温差的关系曲线如图2所示。
图 1 总费用-最小传热温差关系曲线图(不含节能措施)由图1可以看出,传热温差为23℃时总费用最小,因此选取最小传热温差为23℃。
在此最小传热温差下的过程组合曲线见图2,总组合曲线如图3所示。
图 2过程组合曲线图(不含节能技术)图 3 优化前的总组合曲线图(不含节能技术)图2所示的组合曲线表明工艺流股中所有热流股和冷流股的换热量及温位要求。
除了上述工艺流股的换热任务外,本系统中还有反应器R0101、R0201以及R0401有换热要求,可以选用公用工程或工艺流股来实现。
其中,MTBE裂解反应器R0101反应吸热,反应温度为265℃-300℃,由图3的总组合曲线可知,系统中没有合适的热工艺流股可以利用,所以使用热公用工程热油对R0101进行换热。
叔丁胺合成反应器R0201需要流股伴热,反应温度为525K-535K,可进一步利用与R0101换热后的热油,以减少热公用工程用量。
之后的分析都在Aspen 模拟中加入反应器所需利用的热油进行分析。
异丁烯聚合反应器R0401为恒温反应器,反应温度为-25℃,为了保证控制反应器的恒温,不便于采用工艺换热,因此采用公用工程液氨维持反应温度恒定。
4工艺流程的改进由图2的组合曲线可以看出,夹点附近存在较长的平台区,经分析可知,蓝色线的冷流体平台一部分表示异丁烯精制精馏塔T0102塔底再沸液体蒸发过程的相变热,红色线的热流体平台一部分表示异丁烯脱重塔T0101塔顶蒸汽冷凝过程的相变热,若增加T0101塔压后,T0101塔顶气体温度升高,可作为T0102塔底再沸器的热源进行换热,实现相变潜热的多效利用。
平台区一部分是叔丁胺精制精馏塔T0302塔顶及塔底的相变热,而且T0302塔顶、塔釜温度差为22.8℃,该塔可以通过热泵技术提高塔顶流股温位,用以加热塔釜流股,增加系统内部换热量,减少公用工程的消耗量。
5改进工艺流股的提取及分析加入双效精馏和热泵精馏后,在ASPEN中重新模拟全流程,得到新的流股信息(物流号及设备位号参考[3-改进工艺流股(全流程模拟,含热泵、双效精馏).bkp])见表3和表4.表3 工艺过程物流信息表(含节能措施)表4 塔设备物流信息表(含节能措施)T0201 Condenser 3.6 3.4 2999.831T0301 Reboiler 139.7 139.8 40.53918T0301 Condenser 49.9 40.2 1432.754T0501 Reboiler 93.5 93.7 1440.278T0501 Condenser 81.8 53.8 7.516667对最小传热温差进行经济评估,得到新的总费用-最小传热温差关系曲线,见图4。
图 4 总费用-最小传热温差关系曲线图(含节能技术)可以看出,随着最小传热温差的增大,总费用先减小后增大。
选择总费用最小时的最小传热温差:20℃。
将最小传热温差设为20℃,可以得到热集成过程的能量目标:图 5 过程的能量目标由上图可以看出,理论上最少需要热公用工程能量为:3.439×107kJ/h=9552.7kW理论上最少需要冷公用工程能量为:4.622×107kJ/h=12838.9kW夹点温度为:热流股49.9℃;冷流股29.9℃得到优化后的过程组合曲线图及总组合曲线图:图6过程组合曲线图(含节能技术)图7 总组合曲线图(含节能技术)通过对组合曲线进行分析,可以得出流程内部换热后,需要达到的最高温度在317.3℃,由保持反应器温度的热公用工程热油进行加热,其他使用蒸汽进行加热,同时为了节约成本,应该使用多种品味蒸汽以降低高品位蒸汽消耗,因此我们热公用工程采用400℃的热油、125℃的低压蒸汽、175℃的中压蒸汽和250℃的高压蒸汽。
需要达到的最低温度为-56.6℃,因此需要采用低温冷冻剂,其他使用循环冷却水及空气冷却即可。
6换热网络设计换热网络的设计,自由度较大,所获得的方案数目众多,但是合理的换热网络需要经过筛选与优化。
在设计换热网络时,需要考虑工艺流股换热的可能性,最好还要将设备费用等因素也考虑进去,以便获得最为合理的换热网络。
在Aspen Energy Analyzer V10给出的Design中选取其中最为经济且换热面积较小的设计方案进行后续优化过程。
设计方案如图8所示:图 8 设计方案图分析比较10种Design的Total Cost,综合考虑所需费用以及换热面积,选用Design 6进行后续的优化过程。
未优化前的换热网络:图 9 未优化前的换热网络按照最小换热器台数原则,还可以去若干台换热器。
当用多种公用工程换热时,可适当减少操作费,但会增加换热器数目和设备费。
比如在使用冷却水和制冷剂冷却时,如果冷却水冷却的负荷较小,则可直接使用制冷剂,而不使用两种公用工程,以节省设备费。
换热网络中存在loop回路。
图 10(1) loop回路图图 10(2) loop回路图在实际操作中,一般不能有loop回路的存在,故应该删去负荷或者换热面积较小的换热器,将其合并到其他换热器,打破回路,减少换热器数目。
再通过path通路来调节换热量,使换热器的热负荷得到松弛,另外,相距较远的物流间换热会使管路成本增大,增加设备投资成本,且操作不稳定,此类换热器也需要删除。
经过以上调整,将换热网络优化为:图11 优化后的换热网络图优化后的换热网络所需要的换热器数目为25台,包括7台热量回收利用换热器(E0101,E0105,E0203,E0204,E0304,E0401,E0501),可回收热量10782.97kW。
7热泵技术分析在无热泵技术的情况下时,组合曲线如图12所示。
图12 组合曲线(不含节能措施)由图可以看出,在45℃左右存在平台区且热量较大,经分析可知,该平台处有一部分为叔丁胺精制精馏塔(T0302),塔顶塔底温差为22.8℃,且存在较大的相变热,可以采用热泵技术。
如果通过改变物质的汽化温度,使两平台“错开”,从而回收更多的能量。
结合以上两点原因,我们设计了热泵蒸发的方式来进行有效的能量回收。
通过热泵蒸发,将功转化成热能,提高流股的温位,使原本不能换热的流股可以进行换热,从而减少公用工程的用量。
这样,消耗少量电能(用以做功)便可以节省大量的冷量与热量,从而节能。
将叔丁胺精制精馏塔T0302的冷凝器取消,直接引出塔顶气相,通过压缩机加压,使得塔顶气相的温度提高一个等级,作为热源至塔釜再沸器换热,放出热量冷凝部分气体,再经节流阀减压降温,由于叔丁胺产品纯度要求,故在节流后继续通过较为经济的二次冷凝,用公用工程降温至43.6℃,从而得到符合产品春的要求的叔丁胺,一部分液体回流至塔内进行再次分离。
塔釜则在换热过程中已经达到再沸负荷的要求,其结构如图所示:图13 塔顶气体压缩式热泵精馏流程图表5 有无热泵技术对比表项目无热泵技术热泵技术塔顶冷凝能耗(kW)302.048 136.343塔底再沸能耗(kW)195.892 0压缩机功率(kW)0 30.208 总能耗(kW)497.94 166.551由上表可知,考虑压缩机做功和冷却器能耗,热泵技术比无热泵技术节省能耗331.389kW,节省幅度达66.6%。
热泵技术节省冷耗54.9%,节省热耗100%。
8相变潜热利用分析双效精馏系统由不同操作压强的塔组成。
利用较高压力的塔顶蒸汽作为压力较低的精馏塔再沸器的热源。
此较低压力精馏塔的再沸器即为较高压力精馏塔的冷凝器。
塔顶蒸汽的汽化潜热被系统本身回收利用。
因此在较大程度节约了精馏装置的能耗。
本项目将工艺过程中异丁烯提纯工段异丁烯脱重塔T0101塔压提高0.2bar 后,塔顶气相温度为63.41℃,为高品位的热源。
异丁烯精制精馏塔T0103为低压塔,塔底再沸液体的温度为40.25℃。
因此,异丁烯精制精馏塔T0102的再沸器可以以T0101塔顶气相作为热源塔顶气相作为热源进行换热,如下图所示:图14双效精馏流程图表6 普通精馏与双效精馏对比表项目普通精馏双效精馏塔顶冷凝能耗(kW)8516.298 7862.33塔底再沸能耗(kW)8895.31 8246.29 总能耗(kW)17411.608 16108.62由上表可知,考虑T0101和T0103的塔顶冷凝器和塔釜再沸器能耗,通过相变潜热的多效利用,节省能耗1303.0kW,节省幅度为7.5%。