密封件用高硬度丁腈橡胶的混炼工艺
丁腈橡胶生产工艺

丁腈橡胶生产工艺
丁腈橡胶是一种合成橡胶,也称为NBR橡胶,是由丙烯腈(ACN)和丁二烯(BD)通过共聚反应制得的。
丁腈橡胶具
有较好的耐油性、耐磨性和耐寒性,广泛应用于汽车、机械、化工等领域。
丁腈橡胶的生产工艺主要包括以下几个步骤:
1. 原料准备:将丁苯橡胶和丙烯腈按照一定比例混合,加入有机溶剂进行预分散,得到橡胶分散液。
同时,准备共聚反应的引发剂、活化剂和其他助剂。
2. 共聚反应:将橡胶分散液注入反应釜中,加热至一定温度,加入引发剂和活化剂,搅拌均匀。
引发剂的作用是引发单体的聚合反应,活化剂的作用是加速反应速度。
反应过程中,丙烯腈和丁二烯会发生共聚反应,形成丁腈橡胶。
3. 分散和凝胶:反应结束后,将反应液通过分散机,使橡胶分散成微小颗粒状。
然后将分散液加入凝胶剂中,使橡胶凝胶成固体,形成凝胶。
4. 过滤和干燥:将凝胶状丁腈橡胶进行过滤,去除水分和杂质。
然后通过干燥机,将橡胶干燥至一定含水量,得到干燥的丁腈橡胶颗粒。
5. 热加工:将干燥的丁腈橡胶颗粒通过压延机或挤出机进行热加工,制成板材、管材、胶带等产品。
6. 检测和质量控制:对丁腈橡胶产品进行检测,包括外观质量、物理性能、化学性质等方面。
通过质量控制,确保产品达到规定的标准和要求。
以上是丁腈橡胶生产的主要步骤,每个步骤中都有具体的操作和参数控制要求。
随着科技的发展和工艺的进步,丁腈橡胶的生产工艺也在不断改进,以提高产品质量和生产效率。
一种高硬度丁腈橡胶的配方与制备方法

一种高硬度丁腈橡胶的配方与制备方法
配方:
1. 丁腈橡胶
2. 填充剂
3. 加工助剂
4. 交联剂
5. 抗老化剂
6. 加硫剂
7. 填充材料
8. 润滑剂
9. 柔化剂
10. 稳定剂
11. 硬度调节剂
制备方法:
1. 准备原材料:将所需原材料依次准备,并根据工艺要求进行筛选和预处理。
2. 按比例混合:将丁腈橡胶、填充剂、加工助剂、交联剂、抗老化剂、加硫剂、填
充材料、润滑剂、柔化剂、稳定剂以及硬度调节剂按照设计配方比例依次加入搅拌机中。
3. 搅拌混合:开启搅拌机,将原料进行充分的混合,确保各种成分均匀分布,并且
形成一定的流动性。
4. 粉碎:将混合好的原料通过粉碎机进行碾磨,以确保最终产品的细腻度和均匀
性。
5. 加热混炼:将粉碎好的原料放入混炼机中,升温至适宜的温度,加热并搅拌混合,直至原料完全熔化和分散。
6. 挤出:将混炼好的原料通过挤出机挤出成型,形成连续的橡胶条或其他形状。
7. 加硫固化:将挤出的橡胶条置于加硫装置中,进行加热和加压处理,使橡胶条与硫化剂反应生成交联结构,以增加硬度和强度。
8. 冷却切割:待加硫结束后,将已经固化的橡胶条取出,并进行冷却处理,然后根据需要进行切割或切片。
9. 补强处理:根据要求,对裁剪好的橡胶制品进行补强处理,以增加其耐磨和耐用性。
10. 储存包装:将制备好的高硬度丁腈橡胶制品进行储存和包装。
以上是一种高硬度丁腈橡胶的配方与制备方法的详细描述。
根据具体需求,可调整每个成分的配比和加工工艺,以获得满足特定需求的高硬度丁腈橡胶制品。
丁腈橡胶 工艺流程
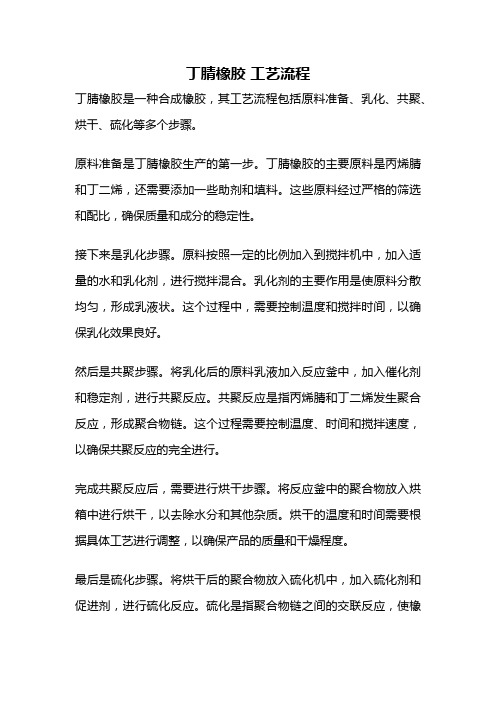
丁腈橡胶工艺流程丁腈橡胶是一种合成橡胶,其工艺流程包括原料准备、乳化、共聚、烘干、硫化等多个步骤。
原料准备是丁腈橡胶生产的第一步。
丁腈橡胶的主要原料是丙烯腈和丁二烯,还需要添加一些助剂和填料。
这些原料经过严格的筛选和配比,确保质量和成分的稳定性。
接下来是乳化步骤。
原料按照一定的比例加入到搅拌机中,加入适量的水和乳化剂,进行搅拌混合。
乳化剂的主要作用是使原料分散均匀,形成乳液状。
这个过程中,需要控制温度和搅拌时间,以确保乳化效果良好。
然后是共聚步骤。
将乳化后的原料乳液加入反应釜中,加入催化剂和稳定剂,进行共聚反应。
共聚反应是指丙烯腈和丁二烯发生聚合反应,形成聚合物链。
这个过程需要控制温度、时间和搅拌速度,以确保共聚反应的完全进行。
完成共聚反应后,需要进行烘干步骤。
将反应釜中的聚合物放入烘箱中进行烘干,以去除水分和其他杂质。
烘干的温度和时间需要根据具体工艺进行调整,以确保产品的质量和干燥程度。
最后是硫化步骤。
将烘干后的聚合物放入硫化机中,加入硫化剂和促进剂,进行硫化反应。
硫化是指聚合物链之间的交联反应,使橡胶具有优异的弹性和耐久性。
硫化的温度和时间需要根据产品的要求进行调整,以确保硫化效果良好。
以上就是丁腈橡胶的工艺流程。
通过原料准备、乳化、共聚、烘干和硫化等多个步骤,可以制备出质量稳定、性能优异的丁腈橡胶产品。
丁腈橡胶具有耐油、耐溶剂、耐热、耐寒等优良特性,在汽车、机械、建筑等领域有着广泛的应用。
丁腈橡胶的生产工艺不仅需要严格控制各个步骤的条件,还需要进行质量检验和控制,以确保产品的质量和性能达到预期要求。
耐酸碱高硬度低压变丁腈橡胶的配方
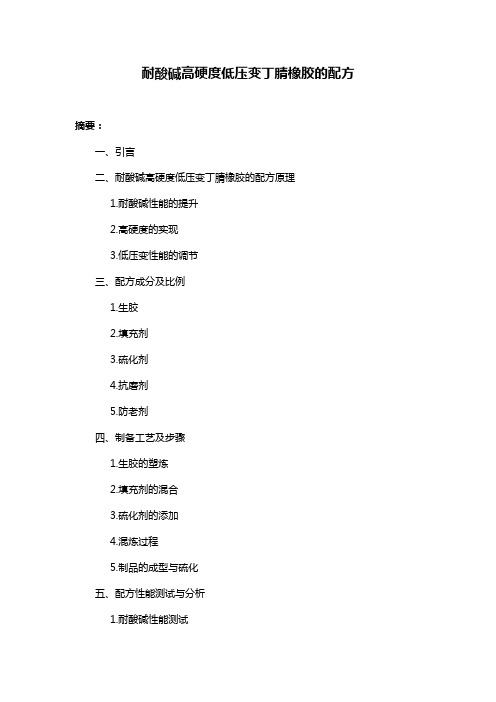
耐酸碱高硬度低压变丁腈橡胶的配方摘要:一、引言二、耐酸碱高硬度低压变丁腈橡胶的配方原理1.耐酸碱性能的提升2.高硬度的实现3.低压变性能的调节三、配方成分及比例1.生胶2.填充剂3.硫化剂4.抗磨剂5.防老剂四、制备工艺及步骤1.生胶的塑炼2.填充剂的混合3.硫化剂的添加4.混炼过程5.制品的成型与硫化五、配方性能测试与分析1.耐酸碱性能测试2.硬度测试3.低压变性能测试六、应用领域及市场前景1.工业领域2.汽车零部件3.电子产品4.市场前景展望七、结论正文:一、引言随着科技的不断发展,对材料性能的要求越来越高。
耐酸碱、高硬度、低压变性能的丁腈橡胶在众多领域具有广泛的应用。
为了满足这些性能要求,研究人员不断探索新的配方。
本文将介绍一种耐酸碱高硬度低压变丁腈橡胶的配方,并分析其性能及应用领域。
二、耐酸碱高硬度低压变丁腈橡胶的配方原理1.耐酸碱性能的提升在配方设计中,选择具有优异耐酸碱性能的生胶作为基础材料。
同时,添加一定比例的抗磨剂和防老剂,以提高橡胶的耐酸碱性能。
2.高硬度的实现通过调整硫化剂的种类和比例,使橡胶在硫化过程中形成较多的交联结构,从而提高硬度。
同时,在配方中添加一定比例的填充剂,以增强橡胶的硬度。
3.低压变性能的调节在制备过程中,通过控制硫化温度和时间,使橡胶在低压条件下具有良好的变性能。
三、配方成分及比例1.生胶:选用耐酸碱性能优异的生胶作为基础材料,占配方总量的60%。
2.填充剂:选用高硬度、高填充性的填充剂,如碳黑、硅烷等,占配方总量的20%。
3.硫化剂:选用对酸碱性能影响较小的硫化剂,如硫磺、促进剂等,占配方总量的15%。
4.抗磨剂:选用具有优异抗磨性能的抗磨剂,如酯类、酰胺类等,占配方总量的5%。
5.防老剂:选用对耐酸碱性能有良好改善的防老剂,如酚醛树脂、胺类等,占配方总量的5%。
四、制备工艺及步骤1.生胶的塑炼:将生胶放入炼胶机中,加热至一定温度,使其变得柔软易拉伸。
2.填充剂的混合:将填充剂与生胶混合均匀,增强橡胶的硬度。
丁腈橡胶成型工艺
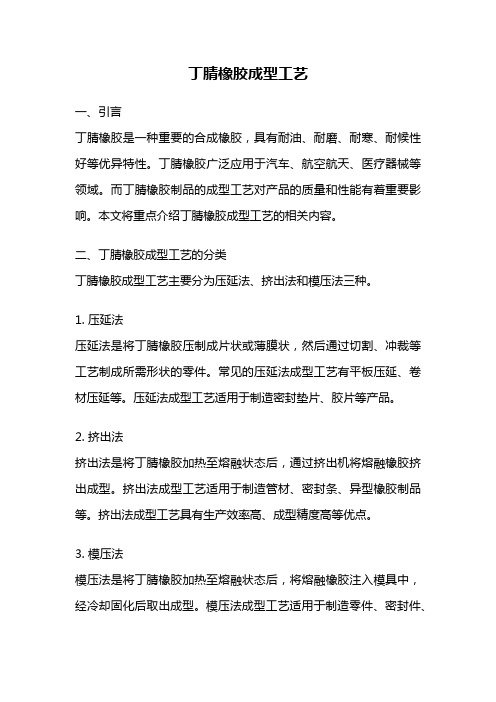
丁腈橡胶成型工艺一、引言丁腈橡胶是一种重要的合成橡胶,具有耐油、耐磨、耐寒、耐候性好等优异特性。
丁腈橡胶广泛应用于汽车、航空航天、医疗器械等领域。
而丁腈橡胶制品的成型工艺对产品的质量和性能有着重要影响。
本文将重点介绍丁腈橡胶成型工艺的相关内容。
二、丁腈橡胶成型工艺的分类丁腈橡胶成型工艺主要分为压延法、挤出法和模压法三种。
1. 压延法压延法是将丁腈橡胶压制成片状或薄膜状,然后通过切割、冲裁等工艺制成所需形状的零件。
常见的压延法成型工艺有平板压延、卷材压延等。
压延法成型工艺适用于制造密封垫片、胶片等产品。
2. 挤出法挤出法是将丁腈橡胶加热至熔融状态后,通过挤出机将熔融橡胶挤出成型。
挤出法成型工艺适用于制造管材、密封条、异型橡胶制品等。
挤出法成型工艺具有生产效率高、成型精度高等优点。
3. 模压法模压法是将丁腈橡胶加热至熔融状态后,将熔融橡胶注入模具中,经冷却固化后取出成型。
模压法成型工艺适用于制造零件、密封件、O型圈等。
模压法成型工艺具有成型精度高、表面光洁度好等优点。
三、丁腈橡胶成型工艺的步骤无论是压延法、挤出法还是模压法,丁腈橡胶的成型工艺大致可分为以下几个步骤:1. 原料准备:将丁腈橡胶颗粒加入橡胶混炼机中,与填充剂、硫化剂、促进剂等进行混炼,使其成为均匀的橡胶混合料。
2. 加热熔融:将橡胶混合料加入加热机中进行加热,使其熔融成为熔胶。
不同的成型工艺对温度要求不同,需要根据具体工艺调整加热温度。
3. 成型:根据不同的成型工艺选择相应的设备和工艺参数,将熔胶进行压延、挤出或注入模具中,使其成型。
4. 冷却固化:将成型的丁腈橡胶制品进行冷却,使其固化成为具有一定硬度和形状的橡胶制品。
5. 后处理:对成型的丁腈橡胶制品进行修整、检验、包装等工序,使其达到产品质量要求。
四、丁腈橡胶成型工艺的关键因素丁腈橡胶成型工艺的质量和效率受到多个因素的影响,其中包括以下几个关键因素:1. 原料选择和配比:选用合适的丁腈橡胶原料,并合理配比填充剂、硫化剂、促进剂等,以满足产品的性能要求。
NBR橡胶工艺流程

NBR橡胶工艺流程NBR橡胶工艺流程NBR(丁腈橡胶)是一种合成橡胶,具有优良的耐油、耐热、耐臭氧和耐磨性能,广泛应用于汽车、工业、航空等领域。
下面将介绍NBR橡胶的工艺流程。
首先,原料准备。
NBR橡胶的主要原料是丁二烯和丙烯腈。
生产NBR橡胶时,将这两种原料按一定比例混合。
此外,还需要准备一些助剂,如加硫剂、活性剂、填充剂等。
这些助剂能够增加橡胶的加工性能和性能稳定性。
其次,混炼。
将原料放入橡胶混炼机中,进行混炼工艺。
混炼主要是通过剪切、挤压、翻滚等作用,使原料充分分散和均匀混合。
在混炼过程中,还需要加入适量的软化剂来提高橡胶的可加工性。
然后,压延。
混炼后的橡胶需要通过压延机进行加工。
压延是将橡胶在压条机上进行压制和切割,使其成为合适的厚度和宽度。
压延时,还需要使用一些顶杆和模板来塑造橡胶的形状。
接下来,硫化。
硫化是指将橡胶制品放入硫化炉中,在一定的温度和时间条件下进行硫化反应。
硫化可以使橡胶分子链发生交联,增加橡胶的耐热性和耐化学性能。
最后,整形和包装。
硫化后的橡胶制品需要进行整形,即将其切割成所需的形状和尺寸。
然后,将橡胶制品进行包装,以便储存和运输。
总的来说,NBR橡胶的工艺流程包括原料准备、混炼、压延、硫化和整形等步骤。
这些步骤通过合理的工艺和设备,使得NBR橡胶能够具备优良的性能和应用价值。
在实际生产中,需要严格控制每个步骤的工艺参数,以确保橡胶制品的质量和稳定性。
同时,还需要不断改进工艺流程和技术,以适应市场需求的变化。
树脂增硬丁腈橡胶配方
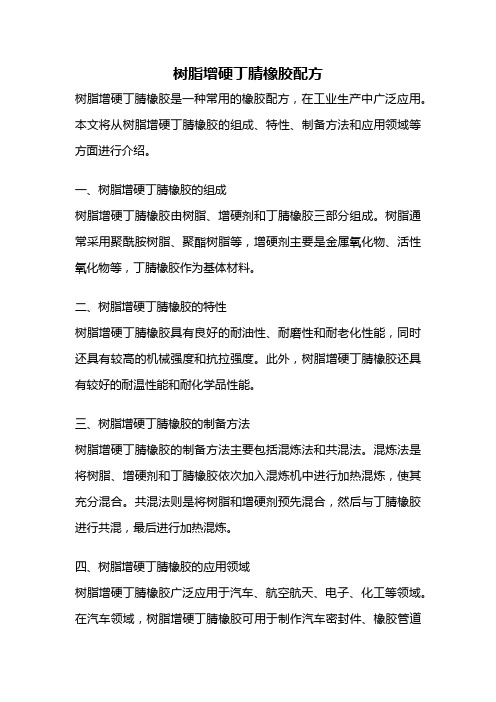
树脂增硬丁腈橡胶配方树脂增硬丁腈橡胶是一种常用的橡胶配方,在工业生产中广泛应用。
本文将从树脂增硬丁腈橡胶的组成、特性、制备方法和应用领域等方面进行介绍。
一、树脂增硬丁腈橡胶的组成树脂增硬丁腈橡胶由树脂、增硬剂和丁腈橡胶三部分组成。
树脂通常采用聚酰胺树脂、聚酯树脂等,增硬剂主要是金属氧化物、活性氧化物等,丁腈橡胶作为基体材料。
二、树脂增硬丁腈橡胶的特性树脂增硬丁腈橡胶具有良好的耐油性、耐磨性和耐老化性能,同时还具有较高的机械强度和抗拉强度。
此外,树脂增硬丁腈橡胶还具有较好的耐温性能和耐化学品性能。
三、树脂增硬丁腈橡胶的制备方法树脂增硬丁腈橡胶的制备方法主要包括混炼法和共混法。
混炼法是将树脂、增硬剂和丁腈橡胶依次加入混炼机中进行加热混炼,使其充分混合。
共混法则是将树脂和增硬剂预先混合,然后与丁腈橡胶进行共混,最后进行加热混炼。
四、树脂增硬丁腈橡胶的应用领域树脂增硬丁腈橡胶广泛应用于汽车、航空航天、电子、化工等领域。
在汽车领域,树脂增硬丁腈橡胶可用于制作汽车密封件、橡胶管道等。
在航空航天领域,树脂增硬丁腈橡胶可用于制作飞机密封件、航天器橡胶零件等。
在电子领域,树脂增硬丁腈橡胶可用于制作电子元件的密封圈等。
在化工领域,树脂增硬丁腈橡胶可用于制作耐油管道、耐磨零件等。
五、树脂增硬丁腈橡胶的优势和发展趋势树脂增硬丁腈橡胶具有良好的综合性能和广泛的应用领域,具有较高的市场需求。
随着科技的不断进步,树脂增硬丁腈橡胶的制备技术也在不断改进和提高,使其性能得到进一步提升。
未来,树脂增硬丁腈橡胶有望在新能源、高速铁路等领域得到更广泛的应用。
六、树脂增硬丁腈橡胶的市场前景树脂增硬丁腈橡胶作为一种具有广泛应用前景的橡胶材料,其市场需求量逐年增长。
随着汽车、航空航天、电子、化工等行业的发展,树脂增硬丁腈橡胶的市场前景将更加广阔。
总结:树脂增硬丁腈橡胶是一种性能优良的橡胶材料,具有良好的耐油性、耐磨性和耐老化性能。
它的制备方法简单,应用领域广泛,市场前景良好。
丁腈橡胶制品的生产工艺
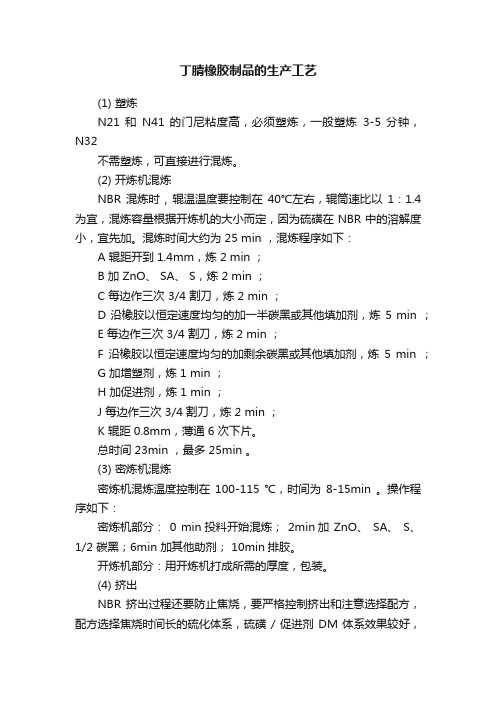
丁腈橡胶制品的生产工艺(1) 塑炼N21 和N41 的门尼粘度高,必须塑炼,一般塑炼3-5 分钟,N32不需塑炼,可直接进行混炼。
(2) 开炼机混炼NBR 混炼时, 辊温温度要控制在40℃左右,辊筒速比以1:1.4 为宜,混炼容量根据开炼机的大小而定,因为硫磺在 NBR 中的溶解度小,宜先加。
混炼时间大约为 25 min ,混炼程序如下:A 辊距开到 1.4mm,炼 2 min ;B 加 ZnO、 SA、 S,炼 2 min ;C 每边作三次 3/4 割刀,炼 2 min ;D 沿橡胶以恒定速度均匀的加一半碳黑或其他填加剂,炼 5 min ;E 每边作三次 3/4 割刀,炼 2 min ;F 沿橡胶以恒定速度均匀的加剩余碳黑或其他填加剂,炼5 min ;G 加增塑剂,炼 1 min ;H 加促进剂,炼 1 min ;J 每边作三次 3/4 割刀,炼 2 min ;K 辊距 0.8mm,薄通 6 次下片。
总时间 23min ,最多 25min 。
(3) 密炼机混炼密炼机混炼温度控制在100-115 ℃,时间为8-15min 。
操作程序如下:密炼机部分: 0 min投料开始混炼; 2min加 ZnO、 SA、 S、1/2 碳黑;6min 加其他助剂; 10min排胶。
开炼机部分:用开炼机打成所需的厚度,包装。
(4) 挤出NBR 挤出过程还要防止焦烧,要严格控制挤出和注意选择配方,配方选择焦烧时间长的硫化体系,硫磺 / 促进剂 DM 体系效果较好,加适量的润滑剂,也有利于防止焦烧。
采用热喂料挤出机时,胶料挤出前要用开炼机进行热炼,热炼条件为前辊40℃,后辊50℃,时间4-5min ,热炼时,挤出返回胶的掺用比例应控制一定,防止胶料塑性值波动,热炼的胶料必须及时供给挤出机。
NBR 胶料的挤出条件一般为:机筒,螺杆温度 40-60 ℃,口型温度80-90 ℃,机头温度90-100℃,为防止焦烧,机筒、螺杆的温度应保持低温,最后在口型温度处提高温度,为此螺杆最好用冷却水冷却。