精益生产工具(1)
精益生产12种工具

原则化工作
懂得要执行什么环节和懂得该环节运营正常,两者都是同等主要旳。 为了确保实现产品质量级别、一致性、有效性及效率,有必要采用写 成文件旳分环节流程或者原则作业程序(SOP)来降低错误和接触时 间。尽管原则化工作建立了明确要求工人和机器操作旳有用文档,原 则化工作在精益制造工具中是最不受到注重旳。这些明确要求旳操作 能帮助工人在制造流程中应用最佳实践。原则化工作同步还能为连续 改善打好基础,因为统计成文件形式旳流程更轻易加以分析与改善。 为了阐释原则化工作,SOP 应该采用图片、文字、表格、标志、色彩 及视觉指示器向不同旳工作组沟通一致旳直观旳信息。这种图形指示, 也被称为操作措施手册(OMS),解释特定生产线范围内根据事件顺 序(SOE)旳每个环节,还能设计并制作纸质或屏幕旳视觉工作指导。
另一项工具是模拟,它能帮助降低维护有关旳挥霍。经过支持模拟, 先进服务管理系统一般能根据生产计划安排维护并根据实际完毕旳生 产自动更新维护计划(电子链接设备本身旳运转时间仪到计划维护 上)。
全员生产维护 (TPM)
目旳是消除下列“六大”维护有关旳挥霍。 1. 设备停工 2. 安顿和调整 3. 小规模停工和闲置 4. 计划外旳停工 5. 因为机器错误制造不合格品所花旳时间 6. 开启期旳不合格品
订单被“推”向工厂车间及库存。
排序与混合模式生产
另一项精益工具是排序,或决定一条生产线上执行不同作业旳顺序, 以达成目旳(例如每日需要旳数量)。这也叫做混合模式生产,该模 式生产不同批量旳几种零件或产品,这些零件或产品旳量接近于当日 将销售旳相同旳产品组合。混合模式计划或排序决定组件旳制造和交 付,涉及那些由外部供给商提供旳组件。重申一下,目旳是根据每日 需求建立生产模式。这点对于汽车制造业极其主要,考虑到全球市场 上老到客户百分比越来越大,争取这些客户旳竞争驱使汽车业原始设 备制造商(OEM)提供有着越来越丰富特色和选择旳产品。从纯功能 旳角度来看,汽车和卡车正日益成为日用具,竞争性旳产品差别化主 要经过提供独特旳色彩、构造、风格及可选配置组合来实现,这么任 何一款车型都有上千种潜在组合。库存全部这些组合在成本上几乎无 法做到,而且查找是否生产了某种特定组合也要花诸多时间,这好比 海底捞针。另外,挑剔旳客户期望立即得到某种独特特色旳配置组合。 这些原因造成一种难题-怎样迅速又有利可图地交付定制成品车。
精益生产的十大工具

精益生产的十大工具精益生产的十大工具是精益生产方法中使用的工具和技术,旨在帮助企业提高生产效率、降低成本、提高质量。
精益生产是一套关于如何优化生产流程的方法论,其核心理念是通过消除浪费,实现更高效、更灵活的生产。
第一个工具是价值流图。
价值流图是将产品的生产流程可视化的工具,它可以帮助企业了解产品从原材料到最终交付的整个流程,从而找出生产中的浪费和瓶颈,并进行优化。
第二个工具是流程平衡。
流程平衡是通过平衡工作站之间的工作量,达到生产过程中的最佳效益。
通过优化工作站之间的工作分配,可以有效地降低等待时间,提高整体生产效率。
第三个工具是一体化生产系统。
一体化生产系统是通过整合产线上的各个工作站,实现生产过程的无缝衔接。
通过一体化生产系统,企业可以实现生产过程的整合和优化,提高生产效率。
第四个工具是短交付时间。
短交付时间是指将产品从订单到交付的时间尽量缩短。
通过缩短交付时间,可以提高客户满意度,同时也可以减少库存和浪费。
第五个工具是标准化工作。
标准化工作是指制定明确的工作标准和操作规范,确保每一项工作都能按照规定的要求进行。
通过标准化工作,可以提高产品质量和生产效率。
第六个工具是柔性生产。
柔性生产是指企业具备快速调整生产线的能力,以适应市场需求的变化。
通过柔性生产,企业可以更加灵活地应对市场变化,降低库存和生产成本。
第七个工具是持续改进。
持续改进是指企业不断地寻找改进的机会,并采取行动来实现持续的改变。
通过持续改进,企业可以不断提高生产效率和产品质量,保持竞争优势。
第八个工具是团队合作。
团队合作是指利用团队的力量,共同解决问题和实现目标。
通过团队合作,可以激发员工的创造力和合作精神,提高生产效率。
第九个工具是视觉管理。
视觉管理是指通过可视化的手段来传达信息和管理生产过程。
通过视觉管理,可以提高沟通效率,减少错误和浪费。
第十个工具是员工培训。
员工培训是指提供必要的培训和教育,使员工能够更好地理解和应用精益生产的方法。
精益生产十大工具

精益生产十大工具精益生产是一种旨在提高生产效率和减少浪费的管理方法。
它包含了许多工具和技术,旨在帮助组织更好地管理资源、提高产能和优化流程。
在这篇文章中,我将介绍精益生产的十大工具,以帮助读者更好地了解和应用这些工具。
1.5S法则:5S法则是一种用于组织工作环境和提高效率的方法。
它包括整理、整顿、清扫、标准化和自律五个步骤。
通过实施5S法则,组织可以改善工作环境,减少浪费和失误,并提高生产效率。
2.价值流图:价值流图是一种用于分析和改善生产流程的工具。
它可以帮助组织识别价值和非价值活动,并定位瓶颈和浪费。
通过分析价值流图,组织可以找到改进的机会,并优化流程以提高产出和客户满意度。
3.流程映射:流程映射是一种用于图形化表示和分析流程的工具。
它可以帮助组织识别和理解整个流程的各个步骤和关键决策点。
通过流程映射,组织可以更好地了解流程,并找出改进的机会。
4.持续改善:持续改善是精益生产的核心原则之一。
它强调从小改进开始,通过反复模拟和实验,逐步提高流程和产品的质量。
持续改进要求组织保持开放和灵活,不断追求更高的效率和产品质量。
5.单点故障:单点故障是指在生产过程中存在可能导致整个流程中断或崩溃的单一关键节点。
通过识别和消除单点故障,组织可以提高生产线的稳定性和可靠性,并降低因故障引起的停产和成本。
6.稳定性:稳定性是指生产流程的可靠性和一致性。
通过确保设备和工艺的稳定性,组织可以减少因工艺变异而导致的浪费和不良品,提高生产效率和质量。
7.柔性制造:柔性制造是指组织能够快速适应市场需求变化,并在不降低质量和效率的情况下生产不同类型的产品。
通过实施柔性制造,组织可以更好地利用资源、减少库存和满足客户需求。
8.精细化:精细化是指组织对生产过程中每一个环节和细节进行深入分析和控制。
通过精细化,组织可以更好地了解产品和生产线的性能,并找到改进的机会,以提高生产效率和质量。
9.标准化:标准化是指通过制定和执行标准,确保生产过程和产品的一致性和质量。
精益生产十大工具

精益生产的十大工具------施增虎一、精益生产的起源精益生产:不多不少,不迟不早,刚刚好,以最少的投入来满足顾客的需求,企业获得最大的回报,投入里面包括人力、物力、设备、时间、场地,通过你的加工、生产、制造变成了成品,成品质量要好,数量要准确,供货要及时,价格要具有竞争力。
生产资源投入5M:人员manpower,机器machine,材料materials,方法methods,测量measuremant.成品输出SQDCM:安全safety,质量quality,成本cost,交期delivery,士气morale.精益5大原则:寻找价值;认识价值流;让作业流动起来;按客户的需求拉动生产;持续生产,尽善尽美。
-丰田生产方式与精益生产-丰田生产方式产生背景及发展-精益生产的新发展二、精益生产两大支柱-核心理论:消除八大浪费,降低成本-两大支柱:准时化和自动化三、精益生产要领的应用精益案例:一、通用加工工厂从濒临破产到精益生产美国第一工厂。
二、从求医进程看医院办理四、杜绝浪费消除成本(一)精益生产的思想基础:消除浪费浪费:一切不为顾客创造价值但却消耗资源活动或行为。
区分增值活动与非增值活动增值活动:将原料或信息转换,改变形状,第一次来满足客户的需求;浪费:目前是不能取消的动作叫浪费增值的三个条件:改变形状或形态,第一次做对不返工,客户付钱。
五、杜绝浪费消除成本(二)七种浪费:过量生产浪费,纠正缺陷浪费,多余工序浪费,过渡库存浪费,物料运输浪费,多余动作浪费,等候时间浪费去除过量生产浪费技巧:小批量生产(或单件流),拉动式生产,均衡计划。
去除纠正缺陷浪费技巧:供应商质量保证,防错,减少变差,在线检验去除多余工序浪费技巧:对比现有工艺和顾客需求,产品设计改进,六、杜绝浪费消除成本(三)去除过渡库存浪费技巧:小批量生产,均衡计划,拉动系统,提升设备可利用率和一次合格率,及时处理过期物料,小批量采购,及时生产,缩小仓库面积。
精益生产管理的十大工具

精益生产管理的十大工具精益生产管理是一种通过优化生产过程,减少浪费和提高效率的方法。
在精益生产管理中,有许多工具和技术可用于帮助企业实现这些目标。
以下是精益生产管理的十大工具。
1. 价值流图:价值流图是一种可视化工具,用于展示产品或服务在整个价值流中的流动,包括所有的价值和非价值活动。
通过使用价值流图,企业可以识别出浪费和瓶颈,并制定改进计划。
2. 5S:5S是一个用于组织和维护工作场所的系统。
它包括整理、整顿、清扫、标准化和维持的步骤。
通过实施5S,企业可以改善工作环境,减少浪费和提高工作效率。
3. 高效供应链管理:高效供应链管理是通过优化供应链中的物流和信息流来降低成本和提高响应速度。
它包括减少库存、改善交付时间和优化供应链合作伙伴关系等方面。
4. 物料需求计划:物料需求计划是一种用于确定需要多少原材料和零部件的工具。
通过正确计划物料需求,企业可以避免库存积压和缺货的问题。
5. 单点作业:单点作业是一种通过减少从一台机器到另一台机器的传送时间来减少生产周期的方法。
这可以通过重新布局设备、改进工艺流程和优化工作站来实现。
6. 柔性生产:柔性生产是一种能够快速适应市场需求和变化的生产方式。
它包括灵活的工作组织、多功能的设备和高度培训的员工。
7. 持续改进:持续改进是一种通过不断寻找和消除浪费、改进工艺和提高质量来提升生产效率的方法。
它可以通过实施PDCA循环(计划、执行、检查、行动)和员工参与来实现。
8. 产能平衡:产能平衡是一种通过平衡生产线上的工作负荷来避免瓶颈和过度生产的方法。
这可以通过调整生产节奏、提高设备利用率和优化工艺来实现。
9. 供应商合作:供应商合作是一种与供应商建立长期合作关系,并与其共同努力改进质量、交付和成本的方法。
这可以通过共享信息、共同制定目标和进行持续改进活动来实现。
10. 质量管理工具:质量管理工具是一系列用于识别和解决质量问题的方法和技术。
其中包括流程图、因果图、直方图、散点图等。
精益生产培训之十大工具
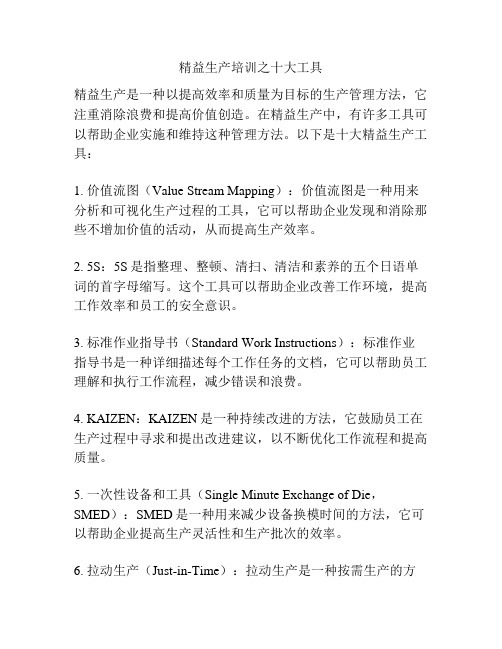
精益生产培训之十大工具精益生产是一种以提高效率和质量为目标的生产管理方法,它注重消除浪费和提高价值创造。
在精益生产中,有许多工具可以帮助企业实施和维持这种管理方法。
以下是十大精益生产工具:1. 价值流图(Value Stream Mapping):价值流图是一种用来分析和可视化生产过程的工具,它可以帮助企业发现和消除那些不增加价值的活动,从而提高生产效率。
2. 5S:5S是指整理、整顿、清扫、清洁和素养的五个日语单词的首字母缩写。
这个工具可以帮助企业改善工作环境,提高工作效率和员工的安全意识。
3. 标准作业指导书(Standard Work Instructions):标准作业指导书是一种详细描述每个工作任务的文档,它可以帮助员工理解和执行工作流程,减少错误和浪费。
4. KAIZEN:KAIZEN是一种持续改进的方法,它鼓励员工在生产过程中寻求和提出改进建议,以不断优化工作流程和提高质量。
5. 一次性设备和工具(Single Minute Exchange of Die,SMED):SMED是一种用来减少设备换模时间的方法,它可以帮助企业提高生产灵活性和生产批次的效率。
6. 拉动生产(Just-in-Time):拉动生产是一种按需生产的方法,它可以帮助企业减少库存和生产浪费,并且能够更好地满足顾客需求。
7. 故障模式与影响分析(Failure Mode and Effects Analysis,FMEA):FMEA是一种用来分析和评估潜在故障模式和其影响的方法,它可以帮助企业识别潜在风险,并采取措施进行预防和改进。
8. 委托管理(Gemba Walk):委托管理是一种通过实地走访生产现场来了解问题和挑战的方法,它可以帮助管理层与现场员工保持沟通,并及时解决问题。
9. PDCA循环:PDCA循环是指计划、实施、检查和行动的四个步骤,它是一种持续改进的管理方法,可以帮助企业不断优化工作流程和提高绩效。
精益生产常用工具
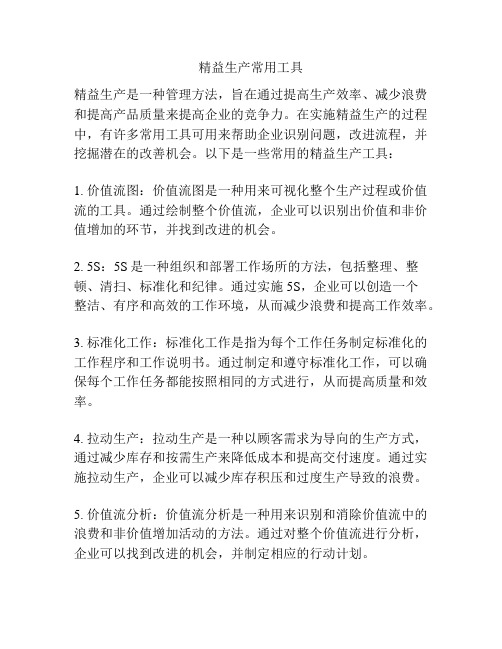
精益生产常用工具精益生产是一种管理方法,旨在通过提高生产效率、减少浪费和提高产品质量来提高企业的竞争力。
在实施精益生产的过程中,有许多常用工具可用来帮助企业识别问题,改进流程,并挖掘潜在的改善机会。
以下是一些常用的精益生产工具:1. 价值流图:价值流图是一种用来可视化整个生产过程或价值流的工具。
通过绘制整个价值流,企业可以识别出价值和非价值增加的环节,并找到改进的机会。
2. 5S:5S是一种组织和部署工作场所的方法,包括整理、整顿、清扫、标准化和纪律。
通过实施5S,企业可以创造一个整洁、有序和高效的工作环境,从而减少浪费和提高工作效率。
3. 标准化工作:标准化工作是指为每个工作任务制定标准化的工作程序和工作说明书。
通过制定和遵守标准化工作,可以确保每个工作任务都能按照相同的方式进行,从而提高质量和效率。
4. 拉动生产:拉动生产是一种以顾客需求为导向的生产方式,通过减少库存和按需生产来降低成本和提高交付速度。
通过实施拉动生产,企业可以减少库存积压和过度生产导致的浪费。
5. 价值流分析:价值流分析是一种用来识别和消除价值流中的浪费和非价值增加活动的方法。
通过对整个价值流进行分析,企业可以找到改进的机会,并制定相应的行动计划。
6. 周期时间分析:周期时间分析是一种用来测量和分析整个生产过程或价值流的时间的方法。
通过测量各个环节的时间,并分析其比例和关系,企业可以找到时间浪费和瓶颈,并采取相应的改进措施。
7. 柔性生产:柔性生产是一种以快速响应市场需求为导向的生产方式,通过灵活地调整生产线和生产能力,以适应需求的变化。
通过实施柔性生产,企业可以降低库存、提高交付速度和灵活性。
8. 产能平衡:产能平衡是指在不同工序间平衡产能,以避免过剩和瓶颈的发生,从而提高效率和质量。
通过进行产能平衡,企业可以合理安排生产能力,以满足顾客需求并避免资源浪费。
综上所述,以上提到的工具是精益生产中常用的工具,通过使用这些工具,企业可以识别问题,改进流程,并发现潜在的改善机会,从而提高生产效率和产品质量,降低成本,提高竞争力。
精益生产十大工具
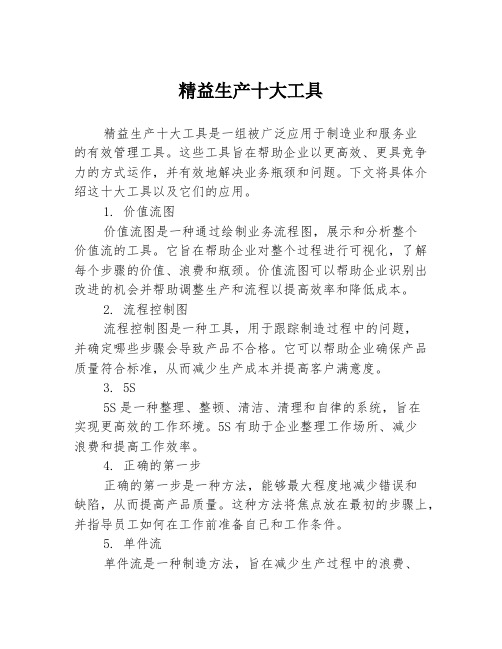
精益生产十大工具精益生产十大工具是一组被广泛应用于制造业和服务业的有效管理工具。
这些工具旨在帮助企业以更高效、更具竞争力的方式运作,并有效地解决业务瓶颈和问题。
下文将具体介绍这十大工具以及它们的应用。
1. 价值流图价值流图是一种通过绘制业务流程图,展示和分析整个价值流的工具。
它旨在帮助企业对整个过程进行可视化,了解每个步骤的价值、浪费和瓶颈。
价值流图可以帮助企业识别出改进的机会并帮助调整生产和流程以提高效率和降低成本。
2. 流程控制图流程控制图是一种工具,用于跟踪制造过程中的问题,并确定哪些步骤会导致产品不合格。
它可以帮助企业确保产品质量符合标准,从而减少生产成本并提高客户满意度。
3. 5S5S是一种整理、整顿、清洁、清理和自律的系统,旨在实现更高效的工作环境。
5S有助于企业整理工作场所、减少浪费和提高工作效率。
4. 正确的第一步正确的第一步是一种方法,能够最大程度地减少错误和缺陷,从而提高产品质量。
这种方法将焦点放在最初的步骤上,并指导员工如何在工作前准备自己和工作条件。
5. 单件流单件流是一种制造方法,旨在减少生产过程中的浪费、减少库存和减少制造时间。
它可以帮助企业以更高效的方式生产各种产品,并根据客户的需求提供服务。
6. 智能制造智能制造是一种制造技术,旨在将传统的制造过程与先进的计算机技术结合起来,以实现更高效、更可靠且更精确的生产。
智能制造的目标是提高质量、降低成本并增强企业的竞争力。
7. 按需制造按需制造是一种生产模式,在该模式下,生产和服务是根据客户需求实时产生的。
按需制造可以大大减少库存,避免过剩的库存和减少过时产品,从而提高效率和降低成本。
8. JidokaJidoka是一种制造方法,旨在通过自动化控制制造过程和机器上的检测,实现实时可视化生产过程。
Jidoka可帮助企业有效地识别和纠正制造过程中的错误,并最大限度地减少损失和产品缺陷。
9. KaizenKaizen是一种改进方法,旨在不断优化生产过程。
- 1、下载文档前请自行甄别文档内容的完整性,平台不提供额外的编辑、内容补充、找答案等附加服务。
- 2、"仅部分预览"的文档,不可在线预览部分如存在完整性等问题,可反馈申请退款(可完整预览的文档不适用该条件!)。
- 3、如文档侵犯您的权益,请联系客服反馈,我们会尽快为您处理(人工客服工作时间:9:00-18:30)。
Check, Do, Verify
Check - The previous operators work. Do - Your work. Verify - That you did your work correctly.
Process
Building Quality into the Process 2 ways to perform SPF
精益生产工具(1)
2020/11/30
精益生产工具(1)
Batch
Building Quality into the Process Single Piece Flow
Single Piece Flow
From: The Toyota Production System
Sample Inspect catches Defect too Late • When you Finally Find a Defect
Ref Material Presentation training for explanation on Supermarket definition and use
精益生产工具(1)
Pull Production Methodology & Sequence
Legend
8 Parts
7 6
5
10 9
process of any problem. - an obligation to stop the process until any
problem has been resolved.
Single piece or one piece flow is a means to primarily build Quality into the process. This is achieved by establishing a takt Time, developing std work, and swip. The premise is that an Operator can only work on one piece at a time, and performs a Quick quality check on the CTQs of the process before moving The part to the following process. If a defect is detected, Jidoka Is enacted…the line is stopped, and immediate action is taken To remediate the situation and take countermeasures to prevent reoccurence
1. Takt time 2. Std work
Flow: work (process) that is done in conjunction with or simultaneous to transportation
精益生产工具(1)
One Piece Flow
• The production is organized into a synchronous chain where each person has a balanced amount of work relative to his/her supplier and customer in the chain.
flaw in 100 parts. The next person checks your work and can catch 1/100 so that’s 1/10,000. Then that person Verifies their work and can catch 1/100. That’s 1/1,000,000 errors that can get through.
# Lots of
Total Manual & Travel Time
Standard Work-in-Process
Operator
Man/Travel Time
27 - avg lot = 6
Turns
Takt/Rate Time
100/Day
DPU's
The next process is the customer … never send defects !
Check, Do, Verify
精益生产工具(1)
One Piece Flow
Your customer is the next step in the process. Give to your customer, exactly what they need ( 1 item), exactly when they need it, done perfect every time.
• As one person finishes their element, so do all. Work is then moved down the line synchronously.
• Every person is empowered to stop the production process if a reject is spotted.
Inspect
Process
Inspect
Transport
The next process is the customer … never send defects ! 精益生产工具(1)
Check, Do, Verify
Gets you into Parts Per Million qualityWhen you verify your work, you catch 1
Supplier
Supermarket
Material Information Empty container Full container 1 Sequence / Timing
3
4
Cell or Chaku-Chaku line
2
1
Assembly Line
精益生产工具(1)
JIT Jidoka
Tenants of 1 pcs Flow
• Do Not Make Defects • Do Not Pass Along Defects • Do Not Accept Defect
Quality, Quality, Quality…Defects are the Worst Kind of Waste
Average by total volume
Average by
model
In general, the more fluctuations you in the production flow, the more muda you
end up having. That is because the capacity and capability of a line tends to be set
精益生产工具(1)
Leveled Production
roducts that can be sold
lowering the peaks among the daily production volumes
HEIJUNKA
as much as possible and making the production flow smooth and unflucuating.
Production Line Cell 6
Part Number All Parts
Part Name
All Tubes
Operator
Orbital Weld
Flex
Weld
End Finish
Weld
End Finish
Torch Braze
Mech. Clean
Mech. Clean
Mark
GEMS Global Production System
g ACTION WORKOUT
New / Rev Organization
Tubing
Area
CFM Cell
Page 1 of 1
Supervisor
Fern Bissonnette
Date 2nd Qtr. ‘01
Standard Work Sheet
• You only have one • You know where it occurred • You Can find/Resolve the Root Cause immediately
The next process is the customer … never send defects !
Hydro Test
Outside Cell FPI X-Ray EDM
Weld
End Finish
Scope of Operations
From: Raw material To: Finished Goods
Quality Check
Safety Precaution
Standard Work-in-Process
Check, Do, Verify
Every Customer in a Process has:
- a right to expect perfect material - an obligation to inspect the material before use. - an obligation to inform the previous step in the
Transportation is integrated into the production process via human conveyance e.g., Chaku-Chaku