设计点气动热力循环分析
热力学循环与热机实验设计

实验设备:制冷机、温度传感器、压力传感器、功率计等
实验步骤: a. 启动制冷机,使其达到稳定运行状态 b. 测量制冷机的输入功率、输出温度和压力 c. 计算制冷量、能效比等性能参数
汇报人:XX
验证热力学循环理论
热力学循环:包括四个主要过程:吸气、压缩、膨胀和排气
热机实验设计:根据热力学循环原理,设计出符合实际需求的热机
实验目的:验证热力学循环原理,提高热机效率
实验方法:通过改变热机参数,如温度、压力、体积等,观察热机性能的变化
确定实验目的和需求
设计实验方案和流程
准备实验设备和材料
进行实验操作和数据采集
热力学循环与热机的关系
热力学循环是热机工作的基础,其效率直接影响热机的性能
热力学循环包括四个主要过程:吸气、压缩、膨胀和排气
热力学循环的效率取决于压缩比、膨胀比、吸气温度和排气温度等参数
通过优化热力学循环,可以提高热机的效率和性能
添加标题
添加标题
添加标题
添加标题
热机在热力学循环中起到能量转换的作用,将高温热源的热能转化为低温热源的机械能
热力学循环的效率是衡量热机性能的重要指标,也是设计热机时需要考虑的关键因素。
提高热力学循环的效率可以降低能源消耗,提高热机的经济性和环保性。
热力学循环的效率受到多种因素的影响,包括热机的结构、材料、工作条件等。
热机实验设计
培养团队合作精神和解决问题的能力
提高实验技能和动手能力
掌握热机实验的基本操作和注意事项
应用领域:制冷机广泛应用于空调、冰箱、冷库等制冷设备中,为人们提供舒适的生活和工作环境。
工程热力学热力循环的热力学性能试验与数据分析
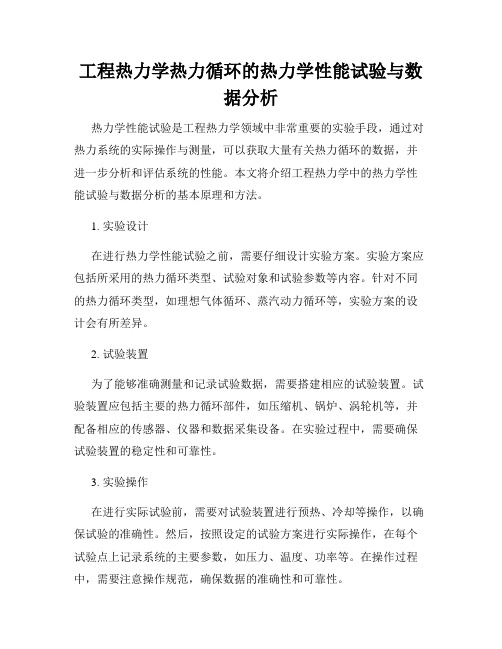
工程热力学热力循环的热力学性能试验与数据分析热力学性能试验是工程热力学领域中非常重要的实验手段,通过对热力系统的实际操作与测量,可以获取大量有关热力循环的数据,并进一步分析和评估系统的性能。
本文将介绍工程热力学中的热力学性能试验与数据分析的基本原理和方法。
1. 实验设计在进行热力学性能试验之前,需要仔细设计实验方案。
实验方案应包括所采用的热力循环类型、试验对象和试验参数等内容。
针对不同的热力循环类型,如理想气体循环、蒸汽动力循环等,实验方案的设计会有所差异。
2. 试验装置为了能够准确测量和记录试验数据,需要搭建相应的试验装置。
试验装置应包括主要的热力循环部件,如压缩机、锅炉、涡轮机等,并配备相应的传感器、仪器和数据采集设备。
在实验过程中,需要确保试验装置的稳定性和可靠性。
3. 实验操作在进行实际试验前,需要对试验装置进行预热、冷却等操作,以确保试验的准确性。
然后,按照设定的试验方案进行实际操作,在每个试验点上记录系统的主要参数,如压力、温度、功率等。
在操作过程中,需要注意操作规范,确保数据的准确性和可靠性。
4. 数据分析实验完成后,需要对所测得的大量数据进行整理和分析。
首先,对数据进行质量检查,排除异常值和错误数据。
然后,可以采用统计学方法对数据进行处理,计算平均值、标准差等,以获得更加准确的试验结果。
5. 热力学性能评价基于试验数据的分析结果,可以对热力循环的性能进行评价。
通过计算循环效率、功率输出等参数,可以评估热力系统的运行效果。
同时,还可以分析系统的能量损失情况,找出性能改进的方向。
总结:工程热力学热力循环的热力学性能试验与数据分析是一项重要的工作,可以为工程设计、运行和优化提供有力的依据。
通过合理的实验设计和仔细的数据分析,可以准确评估热力循环的性能,并提出改进措施。
因此,在热力学性能试验中,严谨的实验操作和准确的数据分析是至关重要的。
通过不断地进行试验与数据分析,可以不断提升热力系统的工作效率和性能,进而为能源的合理利用和环境的保护做出贡献。
分析气体动力循环方法

10-1 10-2 10-3 10-4 10-5 10-6 10-7 10-8
分析动力循环的一般方法 活塞式内燃机实际循环的简化 活塞式内燃机的理想循环 活塞式内燃机各种理想循环的比较 斯特林循环 埃里克森循环 燃气轮机装置循环 燃气轮机装置的定压加热实际循环
课件目录
本章作业
10-1 分析动力循环的一般方法
(10-2)
当两个相同尺寸发动机比较时,MEP大的比MEP小的可 产生更多净输出功。
10-3 活塞式内燃机的理想循环
一、混合加热理想循环(Sabathe循环)
v1
p 3
4
T
4
v2
3
v4
2
v3
2 5
5
p3
p2
11
o
vo
s
图10-4 混合加热理想循环的p-v图和T-s图
混合加热循环的热效率为:
解: 由已知条件:p1 = 0.17 MPa,T1 = 333.15 K
点1:
v1
R gT1 p1
0.562
m3 / kg
点2:
v2
v1
0.0387
m 3 / kg
1 – 2 是定熵过程,有
p2
p
1
(
v v
1 2
)
p1
7.18
kPa
T2
p2v2 Rg
968
K
点3:p3 = 10.3 MPa,v3 = v2 = 0.038 7 m3/kg
1
O
V
图10-2 定压燃烧柴油机示功图
2 +
热力学循环在燃气轮机系统中的优化设计

热力学循环在燃气轮机系统中的优化设计燃气轮机是一种高效的能源转换设备,广泛应用于发电、航空和工业领域。
热力学循环是燃气轮机系统中的核心部分,对其进行优化设计可以提高系统的热效率和经济性。
燃气轮机系统的热力学循环主要包括压缩、燃烧和膨胀三个过程。
在压缩过程中,空气被压缩到高压状态,提高了燃烧效率。
在燃烧过程中,燃料与空气混合燃烧,释放出热能。
在膨胀过程中,高温高压的燃气通过涡轮机膨胀,驱动发电机产生电能。
为了优化燃气轮机系统的热力学循环,可以从以下几个方面进行设计。
首先,优化压缩过程。
压缩过程中的能量损失主要来自于压缩机的机械损耗和热损耗。
为了减小机械损耗,可以采用高效的压缩机,并减小压缩机的转速和摩擦损耗。
而为了减小热损耗,可以采用间冷和再热技术,将压缩过程分为多个级别,降低热损耗并提高压缩效率。
其次,优化燃烧过程。
燃烧过程中的能量损失主要来自于不完全燃烧和燃烧产物的热损耗。
为了提高燃烧效率,可以采用预混合燃烧技术,将燃料和空气充分混合,提高燃烧速度和燃烧效率。
同时,可以采用燃烧室再生技术,利用燃烧产生的高温废气对进气空气进行预热,提高燃烧效率和热能利用率。
最后,优化膨胀过程。
膨胀过程中的能量损失主要来自于涡轮机的机械损耗和热损耗。
为了减小机械损耗,可以采用高效的涡轮机,并减小涡轮机的转速和摩擦损耗。
而为了减小热损耗,可以采用废热回收技术,利用涡轮机排出的高温废气对进气空气进行预热,提高热能利用率。
除了上述的优化设计措施,还可以通过改进燃料供应系统、增加余热利用装置等方式进一步提高燃气轮机系统的热效率和经济性。
此外,燃气轮机系统的运行条件和负荷变化也会对其热力学循环产生影响,因此需要根据实际情况进行优化设计。
总而言之,热力学循环在燃气轮机系统中的优化设计是提高系统热效率和经济性的重要手段。
通过优化压缩、燃烧和膨胀过程,改进燃料供应系统和增加余热利用装置,可以进一步提高燃气轮机系统的性能。
随着科学技术的不断发展,燃气轮机系统的优化设计将会得到更多的突破,为能源转换领域的可持续发展做出更大的贡献。
气体动力循环

§10–4 活塞式内燃机各种理想循环的热力学比较
一.压缩比相同,吸热量相同时的比较
q1v q1m q1 p
q2 v q2 m q2 p
得 T5 T1
把T2、T3、T4和T5代入
1 t 1 1 1 1
讨论:
a) t
b) t
c) t
v1 二、定压加热理想循环 —Diesel cycle v2 v1 v3 v2 v2
二. 实际工作循环的抽象与简化
简化原则为:
(1)不计吸气和排气过程,将内燃机的工作过程看作是 气缸内工 质进行状态变化的封闭循环。 (2)把燃烧过程看作是外界对工质的加热过程,
并认为2-3是定容加热过程,3-4是定压加热过程。
(3)略去压缩过程和膨胀过程中工质与气缸壁之间的热量 交换,近似地认为是绝热过程。
——不可逆过程中实际作功量和循环加热量之比。
§10–2 活塞式内燃机实际循环的简化
分类: 按燃料:煤气机(gas engine)
汽油机(gasoline engine; petrol engine)
柴油机(diesel engine) 按点火方式:点燃式(spark ignition engine) 压燃式(compression ignition engine) 按冲程:二冲程(two-stroke ) 四冲程(four-stroke )
气体而增大。
三.定容加热理想循环—Otto cycle
v1 v2
p3 p2
热效率
q1 cV T3 T2
v1 v2
q2 cV T4 T1
工业用汽轮机中热力循环系统的优化设计
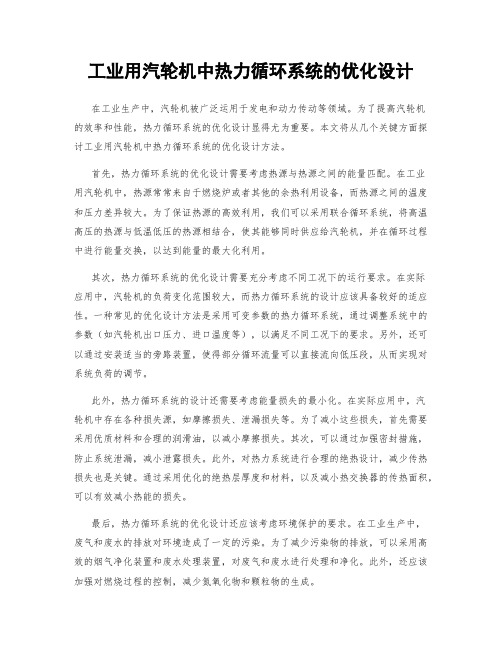
工业用汽轮机中热力循环系统的优化设计在工业生产中,汽轮机被广泛运用于发电和动力传动等领域。
为了提高汽轮机的效率和性能,热力循环系统的优化设计显得尤为重要。
本文将从几个关键方面探讨工业用汽轮机中热力循环系统的优化设计方法。
首先,热力循环系统的优化设计需要考虑热源与热源之间的能量匹配。
在工业用汽轮机中,热源常常来自于燃烧炉或者其他的余热利用设备,而热源之间的温度和压力差异较大。
为了保证热源的高效利用,我们可以采用联合循环系统,将高温高压的热源与低温低压的热源相结合,使其能够同时供应给汽轮机,并在循环过程中进行能量交换,以达到能量的最大化利用。
其次,热力循环系统的优化设计需要充分考虑不同工况下的运行要求。
在实际应用中,汽轮机的负荷变化范围较大,而热力循环系统的设计应该具备较好的适应性。
一种常见的优化设计方法是采用可变参数的热力循环系统,通过调整系统中的参数(如汽轮机出口压力、进口温度等),以满足不同工况下的要求。
另外,还可以通过安装适当的旁路装置,使得部分循环流量可以直接流向低压段,从而实现对系统负荷的调节。
此外,热力循环系统的设计还需要考虑能量损失的最小化。
在实际应用中,汽轮机中存在各种损失源,如摩擦损失、泄漏损失等。
为了减小这些损失,首先需要采用优质材料和合理的润滑油,以减小摩擦损失。
其次,可以通过加强密封措施,防止系统泄漏,减小泄露损失。
此外,对热力系统进行合理的绝热设计,减少传热损失也是关键。
通过采用优化的绝热层厚度和材料,以及减小热交换器的传热面积,可以有效减小热能的损失。
最后,热力循环系统的优化设计还应该考虑环境保护的要求。
在工业生产中,废气和废水的排放对环境造成了一定的污染。
为了减少污染物的排放,可以采用高效的烟气净化装置和废水处理装置,对废气和废水进行处理和净化。
此外,还应该加强对燃烧过程的控制,减少氮氧化物和颗粒物的生成。
综上所述,工业用汽轮机中热力循环系统的优化设计是提高汽轮机效率和性能不可或缺的一环。
航空器的气动热分析与优化
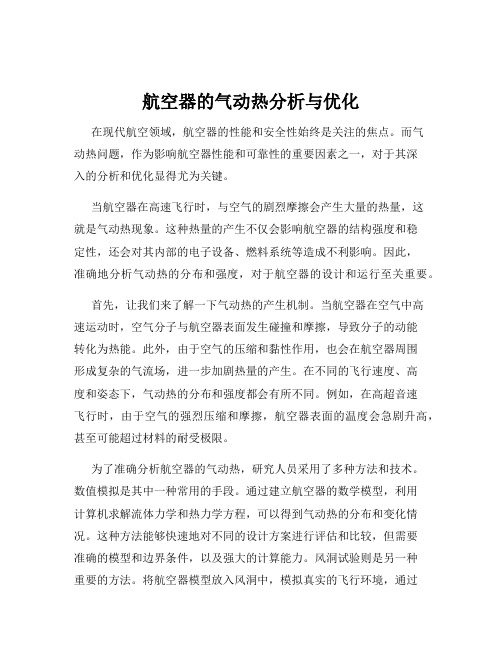
航空器的气动热分析与优化在现代航空领域,航空器的性能和安全性始终是关注的焦点。
而气动热问题,作为影响航空器性能和可靠性的重要因素之一,对于其深入的分析和优化显得尤为关键。
当航空器在高速飞行时,与空气的剧烈摩擦会产生大量的热量,这就是气动热现象。
这种热量的产生不仅会影响航空器的结构强度和稳定性,还会对其内部的电子设备、燃料系统等造成不利影响。
因此,准确地分析气动热的分布和强度,对于航空器的设计和运行至关重要。
首先,让我们来了解一下气动热的产生机制。
当航空器在空气中高速运动时,空气分子与航空器表面发生碰撞和摩擦,导致分子的动能转化为热能。
此外,由于空气的压缩和黏性作用,也会在航空器周围形成复杂的气流场,进一步加剧热量的产生。
在不同的飞行速度、高度和姿态下,气动热的分布和强度都会有所不同。
例如,在高超音速飞行时,由于空气的强烈压缩和摩擦,航空器表面的温度会急剧升高,甚至可能超过材料的耐受极限。
为了准确分析航空器的气动热,研究人员采用了多种方法和技术。
数值模拟是其中一种常用的手段。
通过建立航空器的数学模型,利用计算机求解流体力学和热力学方程,可以得到气动热的分布和变化情况。
这种方法能够快速地对不同的设计方案进行评估和比较,但需要准确的模型和边界条件,以及强大的计算能力。
风洞试验则是另一种重要的方法。
将航空器模型放入风洞中,模拟真实的飞行环境,通过测量表面的温度和热流,可以直接获取气动热的数据。
然而,风洞试验成本较高,而且难以完全模拟复杂的飞行条件。
在实际的气动热分析中,需要考虑众多因素。
航空器的外形和表面粗糙度是影响气动热的重要因素之一。
流线型的外形能够减少空气的阻力和摩擦,从而降低热量的产生。
而表面的粗糙度则会增加气流的扰动,导致热量增加。
飞行速度和高度也是不可忽视的因素。
随着飞行速度的增加,气动热会呈指数级增长;而飞行高度的变化则会影响空气的密度和温度,进而影响气动热的分布。
基于对气动热的分析,优化工作就显得尤为重要。
气体热循环

气体热循环一、气体热循环的概述气体热循环是指通过燃烧可燃物质,使工作物质(通常为空气或其他气体)经历一系列的压缩、加热、膨胀和冷却等过程,从而产生功和热量的循环过程。
气体热循环广泛应用于发电、空调、制冷等领域。
二、理想气体热循环1. 布朗运动理论布朗运动理论是描述分子运动的理论,它认为分子在空气中以高速随机运动,碰撞时会传递能量。
这种分子运动形成了气体的压力和温度等性质。
2. 卡诺循环卡诺循环是一种理想化的气体热循环模型,它由四个步骤组成:等温膨胀、绝热膨胀、等温压缩和绝热压缩。
卡诺循环具有最高效率,但无法实现。
3. 理想化布朗运动理论将布朗运动理论应用于卡诺循环中,可以得到理想化布朗运动理论,它是一种简化的气体热循环模型。
理想化布朗运动理论由两个等温过程和两个绝热过程组成,可以用于实际气体热循环系统的设计。
三、实际气体热循环1. 常用气体热循环常用的气体热循环包括:布雷顿循环、奥托循环、迈克耳森-布雷顿循环、斯特林循环等。
这些气体热循环都有各自的优点和适用范围。
2. 布雷顿循环布雷顿循环是一种基于蒸汽机原理的气体热循环,它由四个步骤组成:加热、膨胀、冷却和压缩。
布雷顿循环广泛应用于发电领域。
3. 奥托循环奥托循环是一种基于内燃机原理的气体热循环,它由四个步骤组成:吸入、压缩、爆发和排出。
奥托循环广泛应用于汽车发动机领域。
4. 迈克耳森-布雷顿循环迈克耳森-布雷顿循环是一种基于热泵原理的气体热循环,它由四个步骤组成:压缩、冷却、膨胀和加热。
迈克耳森-布雷顿循环广泛应用于制冷和空调领域。
5. 斯特林循环斯特林循环是一种基于热机原理的气体热循环,它由两个等温过程和两个绝热过程组成。
斯特林循环具有高效率和低噪音等优点,但适用范围较窄。
四、气体热循环的应用1. 发电气体热循环广泛应用于发电领域,包括火力发电、核能发电等。
其中,火力发电主要采用布雷顿循环和废气余热回收技术,提高能源利用效率。
2. 汽车发动机奥托循环作为汽车发动机的基本工作原理,已成为现代交通工具不可或缺的部分。
- 1、下载文档前请自行甄别文档内容的完整性,平台不提供额外的编辑、内容补充、找答案等附加服务。
- 2、"仅部分预览"的文档,不可在线预览部分如存在完整性等问题,可反馈申请退款(可完整预览的文档不适用该条件!)。
- 3、如文档侵犯您的权益,请联系客服反馈,我们会尽快为您处理(人工客服工作时间:9:00-18:30)。
部件效率和部件损失
部件效率和部件损失依据当前的发动机部件设计水平而定,下表给出了发动机 各部件效率和部件损失的范围。 风扇效率 压气机效率 燃烧室效率 高压涡轮效率 低压涡轮效率 0.88 ~ 0.90 0.85 ~ 0.87 0.97 ~ 0.99 0.88 ~ 0.89 0.90 ~ 0.91 中间机匣总压损失 燃烧室总压损失 外涵道总压损失 混合室总压损失 喷管速度系数 0.01 ~ 0.02 0.02 ~ 0.03 0.03 ~ 0.04 0.02 ~ 0.03 0.98 ~ 0.99 根据飞机要求确定
出口流量: 油气比的推导 (忽略燃油温度) : W3 = W22 (1 − δ HP − δ LP − β ) 高压压气机的单位 气流压缩功:
LC = c p (Tt 3 − Tt 22 )
风扇的单位气流压缩功:
LF = c p (Tt 22 − Tt 2 )
燃烧室能量平衡
f =
c pg Tt 4 − c p Tt 3 H f η b − c pg Tt 4
混合室掺混模型
混合室
内涵进口面积和静压:
A5 = W5 Tt 5 pt 5 K g q g (λ5 )
− kg k g −1
出口总温: c pgW6Tt 6 = c pgW5Tt 5 + c pW5 II Tt 5 II 冲量定理与流量方程联立,求解出口静压和马赫数:
p6 A6 1 + k g M 62 = p5 A5 1 + k g M 52 + p5 II A5 II 1 + kM 52II ⎛ k − 1 2 ⎞ k g −1 K g q g (λ6 ) p6 ⎜1 + M6 ⎟ K g q g (λ6 ) pt 6 2 ⎝ ⎠ = W6 = Tt 6 Tt 6
⎛ kg −1 2 ⎞ T9 = Tt 9 ⎜1 + M9 ⎟ ⎜ ⎟ 2 ⎝ ⎠ a9 = k g RT9
−1
出口(排气)速度:v9 = a9 M 9
性能参数
净推力: FN = v9W9 − v0Wa 单位推力:
FS = FN W9 β ⎞ ⎛ = v9 − v0 = ⎜1 + f 0 − ⎟v9 − v0 Wa Wa 1+ B ⎠ ⎝
kg
(
)
(
)
(
)
⎛ kg −1 2 ⎞ p5 = pt 5 ⎜1 + M5 ⎟ ⎜ ⎟ 2 ⎝ ⎠
出口流量:W6 = W5 + W5 II 出口面积: A6 = A5 + A5 II
内外涵进口马赫数预先给定 0.3 ~ 0.5 。 内外涵进口面积是特征截面尺寸之一。
加力燃烧室
出口总温和总压:
Tt 7 pt 7 = pt 6σ ab
− kg k g −1
低压涡轮
出口流量:
W5 = W4 c = W45 + W22δ LP
π HP
出口总温和总压:
导向器出口总温和总压:
c pgW4 cTt 4 c = c pgW45Tt 45 + c pW22δ LPTt 3 pt 4 c = pt 45
c pgW5 (Tt 4 c − Tt 5 ) = Wa LF + Lext ⎡ 1 − Tt 5 / Tt 4 c ⎤ p = t 4 c = ⎢1 − ⎥ η LP p5 ⎣ ⎦
第四章 设计点气动热力循环分析
第一节 综述
通常,飞机设计的典型任 务剖面中存在着若干个关键性 能点,典型任务剖面和关键性 能点对应着飞机设计任务书中 的具体性能考核指标。相应地, 飞机设计师也会在关键性能点 上提出对发动机性能的要求, 如起飞状态的推力要求、给定 某些巡航状态的小时耗油量要 求、给定某些高空高速状态的 机动性要求等。上述性能要求 就是最初的发动机设计指标。
加力燃烧室总压损失 0.02 ~ 0.04
加力燃烧室效率 0.85 ~ 0.95 飞机引气量
涡轮冷却空气量 根据涡轮前温度确定 根据飞机要求确定 飞机功率提取
在设计点选择、热力循环参数初选、部件效率和部件损失确定完成之后,就可 以开始进行设计点性能计算和热力循环分析了。
第三节
设计点性能计算
本节主要以混排涡扇发动机作为研究对象,介绍如何进行设计点性能计算。在 此阶段,发动机的空气流量可任意选定。相应地,设计点计算的最终结果仅输出单 位推力和耗油率等不依赖于发动机流量和尺寸的性能参数。
高压涡轮
出口流量:
W45 = W4 a = W4 + W22δ HP
导向器出口总温和总压: c pgW4 aTt 4 a = c pgW4Tt 4 + c pW22δ HPTt 3
pt 4 a = pt 4
出口总温和总压:
转子的冷却与功率提取
c pgW45 (Tt 4 a − Tt 45 ) = W22 LC ⎡ 1 − Tt 45 / Tt 4 a ⎤ p = t 4 a = ⎢1 − ⎥ η HP p45 ⎣ ⎦
某战斗机的典型任务剖面
某长航时无人机典型任务剖面
本章主要内容
本章主要讨论根据关键性能点的推力、耗油率等指标需求如何完成发动机的初 步总体气动设计。包括设计点的选择、热力循环参数选择、部件效率和部件损失的 确定、发动机空气流量和特征截面尺寸的确定。 设计点的选择包括:确定发动机设计点的飞行高度、飞行马赫数、环境温度和 环境压力。 热力循环参数的选择包括:确定总增压比、涡轮前温度、加力出口温度、风扇 (低压压气机)压比和涵道比。 部件效率和部件损失的确定包括:确定风扇(低压压气机)效率、高压压气机 效率、燃烧室效率、加力燃烧室效率、高压涡轮效率、低压涡轮效率、中间机 匣总压损失、燃烧室总压损失、外涵道总压损失、混合室总压损失、加力燃烧 室总压损失、尾喷管速度系数、涡轮冷却空气量、飞机引气量、飞机功率提取 等。 最终确定的参数包括:发动机空气流量、混合室内涵进口面积、混合室外涵进 口面积、尾喷管喉部面积、尾喷管出口面积。
− kg k g −1
π LP
外涵道
出口流量、总温 和总压:
W5 II = W2 II Tt 5 II = Tt 2 II pt 5 II = pt 2 II σ d
出口面积和静压:
A5 II = W5 II Tt 5 II pt 5 II Kq (λ5 II )
− k k −1
⎛ k −1 2 ⎞ p5 II = pt 2 II ⎜1 + M 5 II ⎟ 2 ⎝ ⎠
热力循环参数
初步给定满足设计要求的热力循环参数范围。范围划分太窄,可能遗漏满足设 计要求的循环参数;范围划分太宽,将增加设计点计算的工作量。 涡轮前温度的上限要综合考虑发动机热端部件的材料和冷却技术,下限要保证 燃烧室至少达到 600K 以上的温升。 总增压比的范围应涵盖发动机的最佳增压比。 战斗机和攻击机的发动机通常选择小涵道比(<1.0)或涡喷发动机;民用客机 或运输机的发动机通常选择中高涵道比(>3.0)。 混排涡扇发动机的风扇增压比选择应满足混合室最小掺混损失条件,即:混合 室内外涵进口马赫数相等、进口静压相等。 分排涡扇发动机的增压比选择应与涵道比匹配,保证耗油率最小。 在热力循环参数范围内,分别取不同的涡轮前温度、总增压比和涵道比加以组 合,形成一系列的橡皮发动机(rubber engine)。再分别对每个橡皮发动机进行设 计点计算和热力循环分析。
出口马赫数:
M9 =
k g −1 ⎡ ⎤ ⎛ pt 9 ⎞ k g 2 ⎢ ⎜ ⎟ − 1⎥ ⎥ k g − 1 ⎢⎜ p0 ⎟ ⎝ ⎠ ⎢ ⎥ ⎣ ⎦
加力油气比:
f ab = W6 (1 − f ) Wf W fab
出口静温和声速:
= + f ab
总油气比:
f0 = W f + W fab W6 (1 − f ) W6 (1 − f )
进气道
总温和总压:
Tt 2 = Tt 0 p t 2 = p t 0σ i
总压恢复系数:
⎧σ i = 0.97 (M 0 ≤ 1.0 ) ⎪ ⎨ ⎪σ i = 0.97 1 − 0.075(M 0 − 1)1.35 ⎩
速度: v0 = a0 M 0
[
]
(M
> 1 .0 )
风扇
出口总温和总压:
Tt 22 = Tt 2 II
k −1 ⎛ ⎞ ⎜ π Fk − 1 ⎟ = Tt 2 ⎜1 + ⎟ ηF ⎟ ⎜ ⎝ ⎠
高压压气机
出口总温和总压:
k −1 ⎛ ⎞ ⎜ π Ck − 1 ⎟ Tt 3 = Tt 22 ⎜1 + ⎟ ηC ⎟ ⎜ ⎝ ⎠ pt 3 = pt 22π C
主燃烧室
出口总温和总压:
Tt 4 pt 4 = pt 3σ b
3600(W f + Wab ) FN
若为双轴涡喷发动机,则令涵道比为零 计算内涵至低压涡轮出口,再令低压涡 轮出口截面参数等于加力燃烧室进口截 面参数完成剩余计算。 若为单轴涡喷发动机,则令进气道出口 截面参数等于压气机进口截面参数,并 将飞机功率提取计入高压涡轮能量平衡 方程,计算至高压涡轮出口,再令高压 涡轮出口截面参数等于加力燃烧室进口 截面参数完成剩余计算。
耗油率:
sfc =
=
3600 f 0 FS
推演
若不存在加力燃烧室,则令混合 室出口截面参数等于尾喷管进口 截面参数完成剩余计算。 若为分排涡扇发动机,则外涵道 出口和低压涡轮出口气流分别按 完全膨胀计算推力。
发动机各截面定义
第四节
混排涡扇发动机气动热力循环分析
在第二节的设计准备工作阶段,选定了热力循环参数的范围,并在范围内选择 了不同热力循环参数的组合,形成了一系列的橡皮发动机。通过第三节的设计点性 能计算,可以得到这些橡皮发动机的单位推力和耗油率。 本节的目的在于分析总增压比、涡轮前温度、涵道比和风扇压比对单位推力和 耗油率的影响,在此基础上,进一步探讨如何选择更加合理的热力循环参数组合来 满足设计指标要求。