中小型锅炉烟气脱硫常用脱硫技术
锅炉烟气脱硫 钠碱法

锅炉烟气脱硫钠碱法一、钠碱法原理钠碱法是一种有效的烟气脱硫技术,其原理是利用钠碱(如氢氧化钠、碳酸钠等)与烟气中的二氧化硫反应,生成硫酸钠和亚硫酸钠等物质,从而达到脱硫的目的。
二、钠碱法工艺流程钠碱法工艺流程一般包括以下几个步骤:.吸收剂制备:将所需钠碱制成溶液或浆液。
.吸收剂供应:将吸收剂送入吸收塔。
.烟气洗涤:在吸收塔内,烟气与吸收剂进行充分接触,使二氧化硫被吸收剂吸收。
.脱硫产物分离:从吸收剂中分离出硫酸钠和亚硫酸钠等脱硫产物。
.吸收剂循环使用:将分离出的脱硫产物处理后,再循环使用。
三、钠碱法设备组成钠碱法设备一般由以下几个部分组成:.吸收塔:用于烟气洗涤和脱硫反应的主要设备。
.供料系统:包括吸收剂制备、供应和循环系统。
.分离系统:用于从吸收剂中分离出脱硫产物。
.控制系统:用于控制整个工艺流程的运行。
四、钠碱法操作要点钠碱法操作要点包括以下几点:.合理控制吸收剂的浓度和流量,确保与烟气中的二氧化硫充分反应。
.保持设备的运行状态良好,定期检查和维护设备。
.严格控制工艺参数,如温度、压力等,以确保最佳的脱硫效果。
.及时处理脱硫产物,避免对环境造成二次污染。
五、钠碱法优缺点钠碱法的优点包括:.脱硫效率高,可达到90%以上的脱硫效率。
.吸收剂循环使用,降低了运行成本。
.设备组成简单,操作方便。
.在一定程度上可以适应不同的烟气条件。
钠碱法的缺点包括:.需要对设备进行定期维护和检查,增加了运行成本。
.脱硫产物可能含有重金属等有害物质,需要妥善处理,否则会对环境造成污染。
.钠碱法需要使用大量的钠碱,因此原料成本较高。
.在高浓度二氧化硫的烟气中,钠碱法的脱硫效率较低。
锅炉烟气脱硫技术方案及案例分析

锅炉烟气脱硫技术方案及案例分析随着环保意识的不断提高,锅炉烟气脱硫技术成为了重点关注的领域。
本文将介绍基于不同生产需求的锅炉烟气脱硫技术方案及其案例分析,以期帮助企业在选择和使用脱硫技术方案时有所依据。
一、海藻酸锌膜法生产需求:对流量小、效果好、成本低的脱硫技术有需求。
海藻酸锌膜法是一种通过将锌离子与海藻酸分子结合形成膜,在烟气中吸收二氧化硫的技术。
该技术具有处理流量小、效果好、成本低的优点。
案例分析:某热电厂以该技术制定了脱硫技术方案,采用了海藻酸锌膜法,将海藻酸、锌离子、钙离子等添加到烟气中,形成对二氧化硫具有吸收能力的膜。
该技术不仅处理效果好,还大大降低了脱硫成本。
二、喷射吸收脱硫技术生产需求:对处理高浓度二氧化硫的需求。
喷射吸收脱硫技术是一种通过将喷嘴喷出的乳化液喷入烟气中,将其中的二氧化硫与乳化液中的氧化剂反应而被吸收的技术。
案例分析:某钢铁生产企业在使用锅炉时发现,烟气中二氧化硫浓度较高,无法满足环保要求。
经过对多种脱硫技术的比较,企业选择了喷射吸收脱硫技术,并设计了相应的脱硫方案。
采用该技术后,企业二氧化硫排放浓度降低了90%以上,达到了严格的环保要求。
三、氨水脱硫技术生产需求:对处理大气浓度二氧化硫浓度较低的需求。
氨水脱硫技术是一种通过将氨水与烟气中的二氧化硫反应而使其减少的技术。
该技术相对比较成熟,处理二氧化硫效果显著,也相对容易实现。
案例分析:某燃煤发电企业选择了氨水脱硫技术,并制定了脱硫方案。
在实施过程中,企业对脱硫反应的控制和稳定性进行了优化,确保了脱硫效果的稳定、可靠,并满足了国家环保要求。
结语:本文介绍了针对不同生产需求的三种锅炉烟气脱硫技术方案及其案例分析。
对于企业在选择和使用锅炉烟气脱硫技术方案时,应根据企业自身生产情况和环保要求进行选择和合理规划,以达到最佳效果。
几种最常用烟气脱硫技术的优缺点
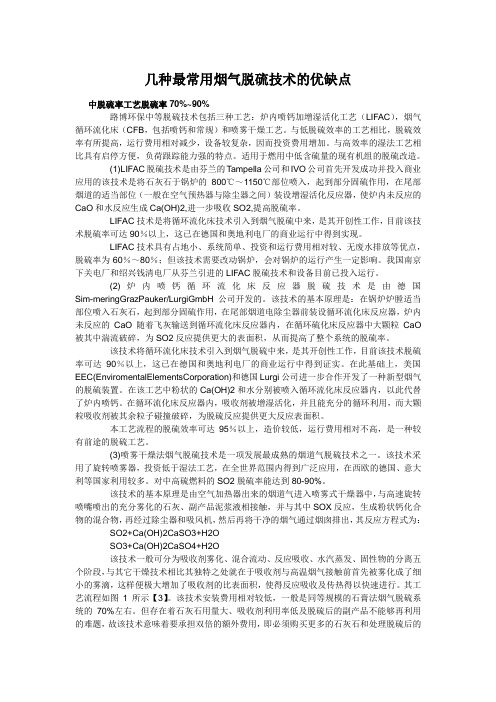
几种最常用烟气脱硫技术的优缺点中脱硫率工艺脱硫率70%~90%路博环保中等脱硫技术包括三种工艺:炉内喷钙加增湿活化工艺(LIFAC),烟气循环流化床(CFB,包括喷钙和常规)和喷雾干燥工艺。
与低脱硫效率的工艺相比,脱硫效率有所提高,运行费用相对减少,设备较复杂,因而投资费用增加。
与高效率的湿法工艺相比具有启停方便,负荷跟踪能力强的特点。
适用于燃用中低含硫量的现有机组的脱硫改造。
(1)LIFAC脱硫技术是由芬兰的Tampella公司和IVO公司首先开发成功并投入商业应用的该技术是将石灰石于锅炉的800℃~1150℃部位喷入,起到部分固硫作用,在尾部烟道的适当部位(一般在空气预热器与除尘器之间)装设增湿活化反应器,使炉内未反应的CaO和水反应生成Ca(OH)2,进一步吸收SO2,提高脱硫率。
LIFAC技术是将循环流化床技术引入到烟气脱硫中来,是其开创性工作,目前该技术脱硫率可达90%以上,这已在德国和奥地利电厂的商业运行中得到实现。
LIFAC技术具有占地小、系统简单、投资和运行费用相对较、无废水排放等优点,脱硫率为60%~80%;但该技术需要改动锅炉,会对锅炉的运行产生一定影响。
我国南京下关电厂和绍兴钱清电厂从芬兰引进的LIFAC脱硫技术和设备目前已投入运行。
(2)炉内喷钙循环流化床反应器脱硫技术是由德国Sim-meringGrazPauker/LurgiGmbH公司开发的。
该技术的基本原理是:在锅炉炉膛适当部位喷入石灰石,起到部分固硫作用,在尾部烟道电除尘器前装设循环流化床反应器,炉内未反应的CaO随着飞灰输送到循环流化床反应器内,在循环硫化床反应器中大颗粒CaO 被其中湍流破碎,为SO2反应提供更大的表面积,从而提高了整个系统的脱硫率。
该技术将循环流化床技术引入到烟气脱硫中来,是其开创性工作,目前该技术脱硫率可达90%以上,这已在德国和奥地利电厂的商业运行中得到证实。
在此基础上,美国EEC(EnviromentalElementsCorporation)和德国Lurgi公司进一步合作开发了一种新型烟气的脱硫装置。
锅炉烟气脱硫技术方案

锅炉烟气脱硫技术方案锅炉烟气脱硫技术是指通过一系列化学反应或物理吸附作用,将烟气中的SO2转化为可排放的形式,从而达到减少环境污染的目的。
下面是一份锅炉烟气脱硫技术方案。
1. 工艺流程锅炉烟气脱硫工艺主要包括前处理、吸收反应、释放反应、过滤、水洗和降温等程序。
前处理:对烟气进行处理,主要包括除尘、脱酸和脱氧等。
吸收反应:采用干法吸收或湿法吸收等技术,将烟气中的SO2和吸收剂产生化学反应,形成硫酸。
释放反应:通过加热、稀释等方式,将硫酸分解为SO2和H2O,其中SO2可以与碱性物质反应,生成稳定的硫化物,如CaSO3、CaSO4等。
过滤:通过布袋过滤器等装置,去除烟气中的颗粒物和异味物质等。
水洗:采用水雾冲洗或水浴冷凝等方式,将烟气中的微量颗粒和一部分SO2洗净。
降温:将烟气降温至环境标准,通过冷凝、燃烧余热等方式回收能量。
2. 工艺特点(1)适用广泛:该工艺适用于燃煤、燃油和燃气等不同种类的锅炉烟气。
(2)效果显著:该工艺可以将烟气中的SO2去除率达到90%以上,满足国家相关标准。
(3)投资低:该工艺设备采用常规材料和技术,成本相对较低。
(4)运行费用低:该工艺采用高效吸收剂,可降低吸收剂的用量及维护费用。
(5)环保安全:该工艺在脱硫过程中不会产生二氧化碳等有害物质,且操作简单,对工人的伤害小。
3. 工艺设备(1)烟气处理系统:包括前处理、吸收、排放和过滤等装置。
(2)吸收液循环系统:包括吸收液储罐、泵、管道和冷却器等组成。
(3)SO2释放系统:包括加热器、分离器、冷却器和泵等。
(4)废弃物处理系统:包括废水处理系统和废渣处理系统等。
(5)控制系统:包括机电自动控制系统和PLC控制系统等。
4. 工艺布局工艺布局应尽量紧凑,设备间的距离要短,不仅方便操作、检修,还能节约场地,降低工程费用。
设备的高度要考虑到操作、维护和安全等因素,同时也要注意烟道的结构和通风情况,以便保证烟气流畅,工艺效果和安全性能达到最佳。
烟气脱硫技术简介

国内烟气脱硫技术我国目前的经济条件和技术条件还不允许象发术达国家那样投入大量的人力和财力,并且在对二氧化硫的治理方面起步很晚,至今还处于摸索阶段,国内一些电厂的烟气脱硫装置大部分欧洲、美国、日本引进的技术,或者是试验性的,且设备处理的烟气量很小,还不成熟。
不过由于近几年国家环保要求的严格,脱硫工程是所有新建电厂必须的建设的。
因此我国开始逐步以国外的技术为基础研制适合自己国家的脱硫技术。
以下是国内在用的脱硫技术中较为成熟的一些,由于资料有限只能列举其中的一些供读者阅读。
石灰石——石膏法烟气脱硫工艺石灰石——石膏法脱硫工艺是世界上应用最广泛的一种脱硫技术,日本、德国、美国的火力发电厂采用的烟气脱硫装置约90%采用此工艺。
它的工作原理是:将石灰石粉加水制成浆液作为吸收剂泵入吸收塔与烟气充分接触混合,烟气中的二氧化硫与浆液中的碳酸钙以及从塔下部鼓入的空气进行氧化反应生成硫酸钙,硫酸钙达到一定饱和度后,结晶形成二水石膏。
经吸收塔排出的石膏浆液经浓缩、脱水,使其含水量小于10%,然后用输送机送至石膏贮仓堆放,脱硫后的烟气经过除雾器除去雾滴,再经过换热器加热升温后,由烟囱排入大气。
由于吸收塔内吸收剂浆液通过循环泵反复循环与烟气接触,吸收剂利用率很高,钙硫比较低,脱硫效率可大于95% 。
注意:锅炉出来的烟气经过除尘之后温度还是很高,而进入脱硫系统,温度是不能太高,温度过高,则吸收塔内的石膏结晶受到很大影响,而且设备的腐蚀和磨蚀会非常严重。
一般在原烟气和净烟气之间加设GGH(气气换热器),一方面对原烟气进行降温,以利于后面处理。
一方面对净烟气进行升温,有利于排烟的抬升,减少烟囱雨的形成,也在直观上减少烟囱排烟的量。
而且如果净烟气不升温的话,SO3会形成酸露,对烟囱的腐蚀非常严重。
脱硫过程的温度一般控制在40-60之间,不是需要太高的温度进行的。
旋转喷雾干燥烟气脱硫工艺喷雾干燥法脱硫工艺以石灰为脱硫吸收剂,石灰经消化并加水制成消石灰乳,消石灰乳由泵打入位于吸收塔内的雾化装置,在吸收塔内,被雾化成细小液滴的吸收剂与烟气混合接触,与烟气中的SO2发生化学反应生成CaSO3,烟气中的SO2被脱除。
目前广泛使用的5种脱硫工艺技术方案简介

目前广泛使用的5种脱硫工艺技术方案简介目录目前广泛使用的5种脱硫工艺技术方案简介 (1)1、湿法烟气脱硫工艺 (1)2、半干法烟气脱硫工艺 (3)3、烟气循环流化床脱硫工艺 (4)4、干法脱硫工艺 (5)5、NID半干法烟气脱硫 (6)目前世界上燃煤电厂烟气脱硫工艺方法很多,这些方法的应用主要取决于锅炉容量和调峰要求、燃烧设备的类型、燃料的种类和含硫量的多少、脱硫率、脱硫剂的供应条件及电厂的地理条件、副产品的利用等因素。
近年来,我国电力工业部门在烟气脱硫技术引进工作方面加大了力度,对目前世界上电厂锅炉较广泛采用的脱硫工艺都有成功运行工程,主要有湿法烟气脱硫、干法烟气脱硫和半干法烟气脱硫。
现将目前应用较为广泛的几种脱硫工艺原理、特点及其应用状况简要说明如下:1、湿法烟气脱硫工艺湿法烟气脱硫包括石灰石/石灰-石膏法烟气脱硫、海水烟气脱硫和用钠基、镁基、氨作吸收剂,一般用于小型电厂和工业锅炉。
氨洗涤法可达很高的脱硫效率,副产物硫酸铵和硝酸铵是可出售的化肥。
以海水为吸收剂的工艺具有结构简单、不用投加化学品、投资小和运行费用低等特点。
而以石灰石/石灰-石膏法湿法烟气脱硫应用最广。
《石灰石/石灰-石膏法烟气脱硫工程设计规范》中关于湿法烟气脱硫工艺的选择原则为:燃用含硫量Sar≥2%煤的机组或大容量机组(200MW及以上)的电厂锅炉建设烟气脱硫装置时,宜优先采用石灰石-石膏湿法脱硫工艺,脱硫率应保证在96%以上。
湿法烟气脱硫工艺采用碱性浆液或溶液作吸收剂,其中石灰石/石灰-石膏湿法脱硫是目前世界上技术最成熟、应用最广,运行最可靠的脱硫工艺方法,石灰石经破碎磨细成粉状与水混合搅拌制成吸收剂浆液;也可以将石灰石直接湿磨成石灰石浆液。
石灰石或石灰浆液在吸收塔内,与烟气接触混合,烟气中的SO2与浆液中的碳酸钙以及鼓入的氧化空气进行化学反应,最终反应产物为石膏,经脱水装置脱水后可抛弃,也可以石膏形式回收。
由于吸收剂浆液的循环利用,脱硫吸收剂的利用率很高。
烟气锅炉脱硫脱硝 工艺

烟气锅炉脱硫脱硝工艺
烟气锅炉脱硫脱硝工艺主要包括以下步骤:
1.烟气预处理:将烟气通过除尘器去除固体颗粒物和粉尘,以减少后续处理的干扰和防止设备堵塞。
2.烟气脱硫:将石灰石或氨水等脱硫剂喷入烟气中。
与烟气中的二氧化硫反应生成硫酸钙或硫酸铵,从而达到脱除烟气中二氧化硫的目的。
常用的脱硫工艺包括湿法脱硫和干法脱硫。
其中。
干法脱硫如SDS 干法脱硫则利用粉末的活性高的钙基或者钠基脱硫剂,吸收烟气中的二氧化硫。
3.烟气脱硝:将氨水或尿素等脱硝剂喷入烟气中,在催化剂的作用下与烟气中的氮氧化物反应生成氮和水,从而达到脱除烟气中氮氧化物的目的。
脱硝工艺用于去除烟气中的氮氧化物。
4.烟气后处理:将处理后的烟气通过除臭器等设备去除异味等杂质,使烟气达到排放标准。
其中。
烟气脱硫脱硝技术有多种,包括scr脱硝+半干法脱硫+布袋除尘(+升温热备)、半干法脱硫+布袋除尘+升温+低温scr脱硝、升温+scr 脱硝+ (余热回收+ )湿法脱硫+湿式电除尘+加热空气热备、干法脱硫脱硝一体化技术等。
这些技术各有特点,可以根据实际情况选择适合的工艺。
烟气脱硫脱硝技术是应用于多氮氧化物、硫氧化物生成化工工业的一项锅炉烟气净化技术。
氮氧化物、硫氧化物是空气污染的主要来源之一,因此,应用此项技术对环境空气净化益处颇多。
请注意,烟气锅炉脱硫脱硝工艺的具体实施可能因设备、环境、排放标准等因素而有所不同。
因此,在实际操作中,应根据具体情况进行选择和调整。
中小型锅炉烟气湿法脱硫系统的优化设计
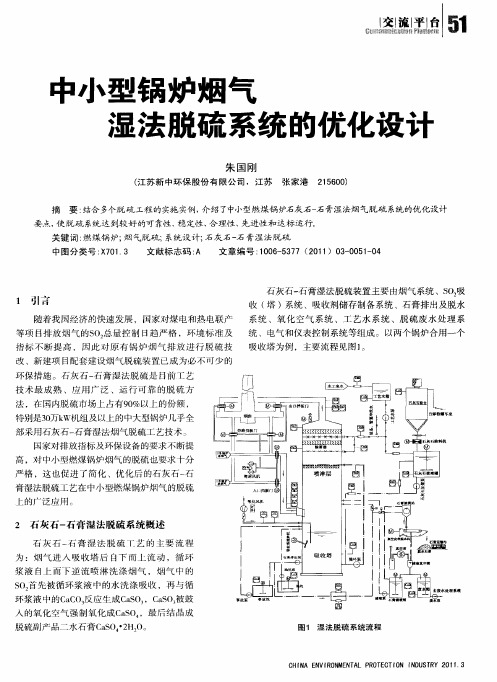
净 烟 气 s 放 浓 度 (g m ) O排 m / 钙 硫 比 ( 定 品质 ) ( aS) 规 C/ 脱 硫 系 统 运 行 阻 力 (a) P脱硫 系统 达到较好 的可靠性 、 使 稳定性、 合理性 、 先进性和达标运行。
关键 词 : 燃煤锅 炉; 烟气脱硫; 系统设计; 石灰石一 膏湿法脱硫 石
中 图 分 类号 :7 13 X 0 . 文 献标 志 码 : A 文 章 编 号 :0 65 7 (0 1 30 5 — 4 10 - 3 7 2 1 )0 — 0 10
脱硫效率 高 、脱 硫系统实 际运行 阻力 小 、负荷适 应性强 和可调节 范同广等性能 ,可最 大程度减少
脱硫系统材料和能源消耗 ,合理控制投资规模。
321 系统 的 优 化 -. ( 1)烟 气 系统
由 于 脱 硫 系 统 的 实 际 运 行 阻 力 较 小 ( 20 a ≤10 P ),炯气 系 统 简 化 了 大 湿 法 配 置 的增 压 风机 系 统 ,运行 阻力 【锅 炉 引风机 调 节 、克 服 , } 1
燃煤含硫量 ( %) 烟 气温 度 ( ) ℃
( 4)仪 用压 缩 空气 系统
因用气量不 大 ( . ~1 m / i 05 . n),脱 硫系统不单 5 m
独设置压缩空气制备系统 ,仅在脱硫装置现场设置一个
参 数 、 指 标
压缩空气储罐 和一套过滤器 ,仪用压缩空气 由电厂主系
对 简洁 、先进 、可靠 、经济实用的中小型燃煤锅炉烟气
度 ,能 实 现 长 期 、稳 定 、可 靠 达 标 运 行 ,且 具 有
污泥处 理l艺 流程 :澄清器排泥一 污泥输送泵一板 l
- 1、下载文档前请自行甄别文档内容的完整性,平台不提供额外的编辑、内容补充、找答案等附加服务。
- 2、"仅部分预览"的文档,不可在线预览部分如存在完整性等问题,可反馈申请退款(可完整预览的文档不适用该条件!)。
- 3、如文档侵犯您的权益,请联系客服反馈,我们会尽快为您处理(人工客服工作时间:9:00-18:30)。
中小型锅炉烟气脱硫常用脱硫技术山东省热电设计院环保工程中心脱硫技术按脱硫工艺与燃烧的结合点可分为:燃烧前脱硫(如洗煤,微生物脱硫);燃烧中脱硫(工业型煤固硫、炉内喷钙);燃烧后脱硫,即烟气脱硫(Flue Gas Desulfurization,简称FGD)。
FGD是目前世界上唯一大规模商业化应用的脱硫方式,是控制酸雨和二氧化硫污染的最主要技术手段。
烟气脱硫技术主要利用各种碱性的吸收剂或吸附剂捕集烟气中的SO2,并将其转化为较为稳定且易机械分离的硫化合物或单质硫,从而达到脱硫目的。
FGD的方法按脱硫剂和脱硫产物干湿状态可分为三类:(1)湿法FGD技术是用含有吸收剂的溶液或浆液在湿状态下脱硫和处理脱硫产物。
该法具有脱硫反应速度快、设备简单、脱硫效率高等优点,但普遍存在腐蚀严重、运行维护费用高及易造成二次污染等问题。
(2)干法FGD技术的脱硫吸收和产物处理均在干状态下进行。
该法具有无污水废酸排出、设备腐蚀程度较轻,烟气在净化过程中无明显温降、净化后烟温高、利于烟囱排气扩散等优点,但存在脱硫效率低,反应速度较慢、设备庞大现场布置困难等问题。
(3)半干法FGD技术兼有干法与湿法的一些特点,指脱硫剂在干燥状态下脱硫、在湿状态下再生(如水洗活性炭在省流程),或者在湿状态下脱硫、在干状态下处理脱硫产物(如喷雾干燥法)的烟气脱硫技术。
特别是在湿状态下脱硫、在干状态下处理脱硫产物的半干法,以其既有湿法脱硫反应速度快、脱硫效率高的优点,又有干法无污水废酸排出、脱硫后产物易于处理的优势而受到人们广泛的关注。
目前,国内外燃煤或燃油电厂所采用的烟气脱硫工艺多达百余种。
在这些脱硫工艺中,有的技术较为成熟,已经达到商业化应用的水平,有的尚处于研究阶段。
业主在选择脱硫工艺时,要选择工艺成熟、有大量相同规模运用业绩的技术,尤其要选择运用具有国外技术背景,且在国内有常年运行业绩的脱硫技术。
由于中小型电站规模小,难以对脱硫技术进行深入研究,所以最好选择常用成熟技术,避免投资风险。
以下是几种常用的、主要适用于中小型锅炉烟气脱硫的工艺说明与比较。
1 半干法/干法脱硫技术半干法脱硫工艺的特点是脱硫剂以液浆形态喷入反应吸收区,被烟气加热,液体蒸发,产生干态的副产品。
干法脱硫技术的特点是脱硫剂以干态喷入反应器,产生干态的副产品。
已有成熟应用业绩的半干法/干法工艺主要有喷雾干燥法、炉内喷钙尾部增湿活化法、循环流化床法(CFB)等,其它半干法/干法脱硫技术由于脱硫效率、磨损、脱硫剂利用率等问题而较少采用。
1.1 喷雾干燥法喷雾干燥法是20世纪70年代开发的一种FGD技术,80年代开始成功地用于燃用低硫煤的锅炉。
该工艺的优点是脱硫渣为干燥固体,便于处理,工艺能耗低,无废水,无腐蚀,投资与运行费用均较低,常用于燃用含硫量小于2 %的低硫煤的电站锅炉,可以达到70-90 %的脱硫效率。
其工艺流程为脱硫剂预先浆化后用泵送至雾化器,脱硫剂浆液在雾化器中被雾化成细滴并进入喷雾干燥吸收器的烟气中,边蒸发边和SO2气体进行反应,生成干态的反应产物。
一般烟气进入喷雾干燥吸收器的温度为120-160°C,经过脱硫剂的雾化、蒸发和吸收SO2等过程,烟气被冷却至60-80°C,但应控制干燥吸收器出口处的烟温高于露点10°C以上。
随烟气进入除尘器的飞灰和干态反应产物被分离出来以后,一部分被再循环送回制浆系统,和脱硫剂浆混合成固体浓度为30-50 %的浆液。
为保证良好的雾化,可采用离心式雾化轮或者双流体雾化喷嘴,将浆液破碎成滴径为20-400µm的液滴,以利于液滴的分布、蒸发及SO2的反应。
反应步骤及方程式如下:①生石灰制浆:CaO + H2O → Ca(OH)2②SO2被液滴吸收:SO2 + H2O → H2SO3③吸收的SO2同溶解的吸收剂反应生成CaSO3:H2SO3 + Ca(OH)2 → CaSO3 + 2H2O④液滴中CaSO3达到饱和后,即开始结晶析出:CaSO3 (aq) → CaSO3 (s)⑤部分溶液中的CaSO3与溶于液滴中的O2反应,氧化成硫酸钙:CaSO3 (aq) + 1/2O2 → CaSO4 (aq)⑥CaSO4饱和结晶析出:C aSO4 (aq) → CaSO4 (s)该工艺系统很关键的一个参数就是吸收塔出口温度。
一方面要求有足够低的温度,以满足脱硫化学反应的需要,另一方面又要保证高于露点,以防止设备和烟道的腐蚀。
因此在烟气中二氧化硫浓度、钙硫比不变的情况下,就只能通过水量的变化来控制吸收塔出口温度。
一般根据不同含硫量的烟气,这一温度又有一定的范围,一般用吸收塔出口温度高于相同状态下的绝热饱和温度∆t来表示,∆t一般为10-18°C,最高的∆t不超过30°C,仅在含量低且脱硫要求不高的装置上,才采用较高的近绝热饱和温度,而对含硫量高且脱硫要求也高的装置上,近绝热饱和温度一般为∆t=10-15°C。
在设计中考虑烟气在塔内的停留时间一般为8-12 s,吸收塔的高径比(吸收塔圆柱部分高与其直径的比值)一般为0.7-0.9。
山东省热电设计院与加拿大Turbosonic公司签订技术合作协议,引进其先进的喷雾干燥脱硫技术以及先进的Turbotak双流体雾化喷嘴,并对其进行优化设计及国产化,降低FGD系统的投资和运行维护费用,以最小的投入和消耗来很好的满足环保要求。
1.2 循环流化床烟气脱硫方法循环流化床烟气脱硫工艺的反应机理是:以循环流化床原理为基础,通过吸收剂的多次再循环,延长吸收剂与烟气的接触时间,以达到高效脱硫的目的。
在塔内回流烟气循环流化床反应器内,飞灰、Ca(OH)2粉末、烟气及喷入的水分,在流化状态下充分混合,强化了传热、传质过程,加上Ca(OH)2粉末多次再循环,使实际反应的Ca/S比远远大于表观Ca/S比,从而实现高效脱硫。
循环流化床烟气脱硫不但具有干法脱硫工艺的许多优点,如流程简单、占地少、投资小以及副产品可以综合利用等,而且能在较低的钙硫比(1.1-1.2)情况下接近或达到湿法工艺的脱硫效率,即90 %以上。
我院与无锡华光锅炉股份有限公司签订了技术合作协议,自2007年4月11日至2012年4月10日,华光授权山东院在山东省内推广及销售华光循环流化床烟气脱硫产品,华光锅炉的CFB技术源自奥地利AE E。
CFB脱硫工艺由吸收剂添加系统、吸收塔、再循环系统以及自动控制系统组成。
烟气从流化床下部布风板进入吸收塔,与消石灰颗粒充分混合,SO2、SO3及其他有害气体如HCl和HF等被吸收。
工艺水用喷嘴喷入吸收塔下部,以增加烟气湿度降低烟温,使反应温度尽可能接近水露点温度,从而提高脱硫效率。
反应产物由烟气从吸收塔上部携带出去,经除尘器分离,分离下来的固体灰渣经输送设备送回循环床吸收塔,灰渣循环量可以根据负荷进行调节。
在文丘里缩径处形成的高速烟气流与循环灰和脱硫剂固体颗粒及液体雾滴迅速混合,在反应器中形成气-固-液三相流。
吸收剂的再循环延长了脱硫反应时间,提高了脱硫剂的利用率。
该工艺的吸收剂为生石灰在现场干消化所得到的氢氧化钙细粉末。
该工艺的副产品呈干粉状,含水率只有2 %左右,流动性好,适宜采用气力输送装置外送。
其化学组成与喷雾干燥工艺的副产品类似,主要成分有飞灰、CaSO3、CaSO4、CaCl2、CaF2以及未反应的吸收剂等,加水后会发生固化反应,固化后的屈服强度可达15-18 N/mm2,渗透率约为3×10-11,压实密度为1.28 g/cm3,强度与混凝土接近,渗透率与黏土相当,因此适合用于矿井回填、道路基础等方面。
该工艺的特点是系统较简单:其Ca/S比较其它半干法低,脱硫效率可达85 %以上;设计紧凑,节省空间,易用于改造项目;吸收剂,脱硫灰均为干态,生产过程中不产生废水,不易形成二次污染;固体颗粒停留时间长,提高了石灰利用率,降低了石灰耗量;排烟温度高,烟囱、烟道无需做防腐处理。
该工艺脱硫效率相对湿法较低,不适用于含硫率太高的烟气脱硫;对锅炉负荷变化的适应性差,运行控制要求较高,比较适合于负荷变化不大的中小型锅炉,焚烧炉和工业窑炉。
2 湿法脱硫技术湿法工艺是指脱硫剂以液浆形式喷入反应器,而脱硫产品也以液浆形式排出的系统。
适用于中小型锅炉烟气脱硫的湿法脱硫技术有很多,依采用的脱硫剂不同,主要有石灰(石)法、氧化镁法、钠法、双碱法、氨法等几类。
湿法脱硫因其脱硫效率高、适应范围广而得到广泛运用,市场占有率为85 %以上。
中小型脱硫产物的处理国内外多采用抛弃法处理。
2.1 石灰(石)—石膏湿法脱硫工艺石灰(石)—石膏湿法脱硫工艺是采用石灰石CaCO3或石灰CaO作为脱硫吸收剂原料,经消化处理后加水搅拌制成石灰石浆液或者氢氧化钙浆液作为脱硫吸收浆。
石灰或吸收剂浆液喷入吸收塔,吸附其中的S O2气体,产生亚硫酸钙,并经强制曝气氧化为硫酸钙,再经旋流、压渣等过程制成石膏。
该工艺的优点主要是:1、脱硫效率高,在Ca/S比小于1.1的时候,脱硫效率可高达95 %以上;2、吸收剂利用率高,可达到90 %;3、吸收剂资源广泛,价格低廉;4、适用于高硫燃料,尤其适用于大容量电站锅炉的烟气处理;5、废液排放量少,副产品为石膏,高品位石膏可用于建筑材料。
该工艺的缺点是:1、系统复杂,占地面积较大;2、造价高,一次性投资大;在美国,一般单位造价在$150-200/kW;在中国,重庆珞璜电厂一期烟气脱硫工程2×360MW脱硫装置占电厂总投资的11.15%,太原第一热电厂高速平流简易湿式300MW机组的6 00000m3/h脱硫装置的单位造价约为RMB650元/kW,杭州半山电厂2×125 MW和北京第一热电厂2×4 10 t/h锅炉脱硫装置单位造价更高达RMB 1600/KW;3、运行问题较多。
由于副产品CaSO4易沉积和粘结,所以,容易造成系统积垢,堵塞和磨损;4、高液/气比所带来的电、水循环和耗量非常大;5、副产品处理问题。
目前,世界上对该副产品处理,主要采用抛弃和再利用两种方法:西欧和日本因缺乏石膏资源,所以用此副产品做建筑用石膏板,与此同时,当地建筑规范也为该产品的推广使用提供了方便。
但对副产品石膏的成分要求严格(CaSO4>96%)。
在美国,因天然石膏资源丰富,空地较多,过去一般采用抛弃处理。
在中国,天然石膏资源丰富,而石灰石的成分却很难保证,因此脱硫石膏的成分不稳定,建筑行业很难采用;对于建在城市近郊或工业区的需要脱硫的电厂,又很难容纳大量石膏渣液的抛弃,即使有空闲场地抛弃,从长远来讲,仍然可能造成固体废弃物的二次污染。
因而副产物处理存在问题。
之前由于石灰-石膏法传统工艺系统占地面积大,一次性投资高,且有其潜在的缺陷,如设备的积垢、堵塞、腐蚀和磨损等,该法主要被新建电厂,特别是大型电站锅炉烟气脱硫所采用,而中小型锅炉烟气脱硫采用石灰(石)法并回收石膏存在规模不经济问题,由于规模较小,出售脱硫石膏的收入往往不能补偿回收石膏的设备投资费用。