第六章 材料的磨损
第6章 刀具磨损和刀具耐用度
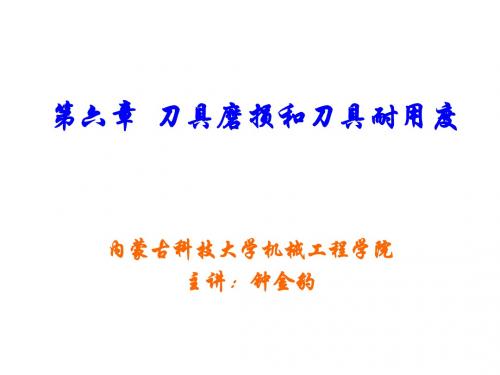
(vc3 、 T3)…各点。可发现,在一定切削速度范围内, 这
些点基本上在一条直线上。
c 1> c 2> c 3> c 4
VB
T1
T2 T
T3
T4
不同vc时的刀具磨损曲线
( ln ln ln ln
1 2 3 4
c 1,T1 )
(
c 2,T2 )
(
c 3,T3 )
ln
(
c 4,T4 )
lnT1
lnT2 lnT
14
切削速度对刀具磨损强度的影响
15 返回本章目录 返回本章目录
第三节 刀具磨损过程及磨钝标准
切削金属时,刀具一方面切下切屑,另一方面 刀具本身也要发生损坏。 刀具损坏的形式主要有磨损和破损两类。 前者是连续的逐渐磨损; 后者包括脆性破损(如崩刃、碎断、剥落、裂纹 破损等)和塑性破损两种。 刀具磨损后,使工件加工精度降低,表面粗糙 度增大,并导致切削力加大、切削温度升高, 甚至产生振动,不能继续正常切削。因此,刀 具磨损直接影响加工效率、质量和成本。
16
1.刀具的磨损过程
1)初期磨损阶段 2)正常磨损阶段 3)急剧磨损阶段
返回本章目录
17
1)初期磨损阶段
这一阶段磨损曲线的斜率较大。由于刃磨后的 新刀具,其后刀面与加工表面间的实际接触面 积很小,压强很大,故磨损很快。 新刃磨后的刀面上的微观粗糙度也加速了磨损。 初期磨损量的大小与刀具刃磨质量有很大关系, 通常在VB=0.05—0.1mm之间。 经过研磨的刀具,其初期磨损量小,而且要耐 用得多。
切削速度v(m/min)
800 600 500 400 300 200
陶瓷刀具 (VB=0.4mm) 硬质合金 (VB=0.4mm)
刀具磨损、破损和使用寿命(刀具耐用度

•
刀具与切屑、工件间的接触表面经常是新鲜表面;
• 接触压力非常大;
• 接触表面的温度很高;
磨料磨损
冷焊磨损 刀具磨损形式: 扩散磨损 氧化磨损 热电磨损(扩散磨损一种)
§ 6-2刀具磨损过程及磨钝标准
6.2.1刀具磨损过程(后刀面磨损值VB随时间延长而增大)
刀具磨损过程分为三个阶段:
①初期磨损阶段(OA段)
切削时间T
图6-11刀具磨损曲线
3)在双对数坐标上是一直线(在一定速度范围内)
lg vc = - m lg T + lg A
m = tg φ
A为当 T=1s (min)时纵坐标截距
泰勒公式 (6-4)
vc =A /Tm
或:
T= C1 /vcz
(z =1/m)
A— 与工件材料有关的系数 m— 切削速度对刀具使用寿命的影响程度
Cv T 1/ m 1/ n 1/ p vc f a p
※ 当用硬质合金车刀切削碳钢时,切削用 量与刀具的经验公式为
T
Cv v f
5 c 1.75 0.75 p Nhomakorabeaa
式中 C——与工件材料、刀具材料和其他条件 v 有关的常数。
※ 切削用量中切削速度对刀具使用寿命 T 影响最大;其次是进给量;切削深度影 响最小。
6.1.2后刀面磨损 6.1.3前、后刀面同时磨损
a)后刀面磨损
b)前刀面磨损 hd > 0.5mm
c)前、后刀面 同时磨损 0.1mm< hd <0.5mm
hd <0.1mm
图1 – 24 刀具磨损的形式
★刀具磨损原因 刀具磨损经常是机械的、热的、化学的三种作用 的综合结果。 ★刀具磨损特点(状态)
粘着磨损ppt课件

粘着磨损杜永平
粘着磨损杜永平
粘着磨损杜永平
粘着磨损杜永平
粘着磨损杜永平
二、粘着磨损的机理 实际接触面积:表观面积的0. 01~0. 1%; 表面压力:5000Mpa; 瞬时温度:1000℃,持续几毫秒。 润滑油膜、吸附膜或其他膜都将发生破裂, 使接触峰顶产生粘着,随后,在滑动中粘着点 又被破坏。就形成粘着——破坏——再粘着的 交替过程。
粘着磨损杜永平
通常高速重载和润滑不良的摩擦副易发生胶 合磨损,目前提出的各种胶合计算准则尚属半 经验计算,缺少足够而准确的数据,因此还不 能有效地普遍应用。
1. pmaxvs≤c 准则
pmax—Hertz最大应力;
1953年,美国Almen提v出s—的相准对则滑动速度;
pm avxs c c—实验常数。
粘着磨损杜永平
三、胶合计算准则
判断胶合发生的观点 表面形貌; 摩擦温度达到临界值作为判据; 摩擦系数突然增大并大幅度变化。
胶合磨损的发生不仅取决于润滑油膜的破裂, 而且与摩擦表面上化学反应膜的形成情况有关。 樊瑜瑾等人通过测量摩擦过程中表面温度、摩擦 力和油膜的变化以及表面反应膜的形成情况,探 讨了油润滑下GCr15与45号钢发生胶合的条件。 实验表明:滑动速度对胶合的发生有很大影响。
摩擦类型;
摩擦温度;
润滑情况;
滑动距离。
Archard计算模型的不足之处在于: 完全忽略了金属变形的物理特性及有关材 料学的变化; 在数学表达式中使用了一些假设,有些过 于粗糙,不尽合理; 对不同条件下的金属磨损过程没能提供确 切的说明。
第六章 水轮机的泥砂磨损(new)
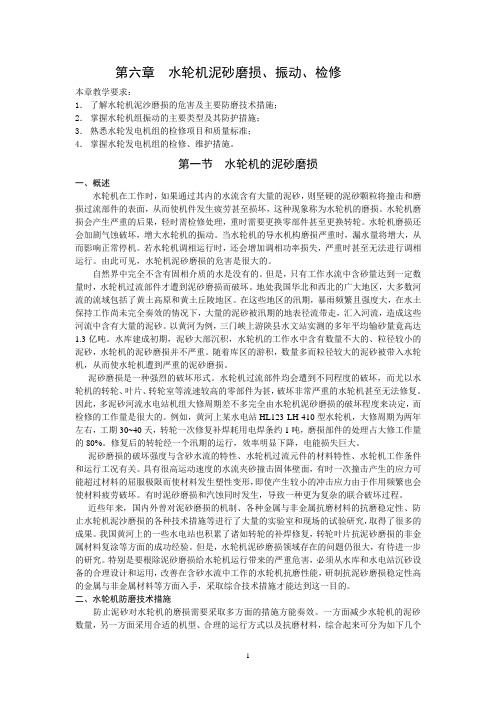
第六章水轮机泥砂磨损、振动、检修本章教学要求:1.了解水轮机泥沙磨损的危害及主要防磨技术措施;2.掌握水轮机组振动的主要类型及其防护措施;3.熟悉水轮发电机组的检修项目和质量标准;4.掌握水轮发电机组的检修、维护措施。
第一节水轮机的泥砂磨损一、概述水轮机在工作时,如果通过其内的水流含有大量的泥砂,则坚硬的泥砂颗粒将撞击和磨损过流部件的表面,从而使机件发生疲劳甚至损坏,这种现象称为水轮机的磨损。
水轮机磨损会产生严重的后果,轻时需检修处理,重时需要更换零部件甚至更换转轮。
水轮机磨损还会加剧气蚀破坏,增大水轮机的振动。
当水轮机的导水机构磨损严重时,漏水量将增大,从而影响正常停机。
若水轮机调相运行时,还会增加调相功率损失,严重时甚至无法进行调相运行。
由此可见,水轮机泥砂磨损的危害是很大的。
自然界中完全不含有固相介质的水是没有的。
但是,只有工作水流中含砂量达到一定数量时,水轮机过流部件才遭到泥砂磨损而破坏。
地处我国华北和西北的广大地区,大多数河流的流域包括了黄土高原和黄土丘陵地区。
在这些地区的汛期,暴雨频繁且强度大,在水土保持工作尚未完全奏效的情况下,大量的泥砂被汛期的地表径流带走,汇入河流,造成这些河流中含有大量的泥砂。
以黄河为例,三门峡上游陕县水文站实测的多年平均输砂量竟高达1.3亿吨。
水库建成初期,泥砂大部沉积,水轮机的工作水中含有数量不大的、粒径较小的泥砂,水轮机的泥砂磨损并不严重。
随着库区的游积,数量多而粒径较大的泥砂被带入水轮机,从而使水轮机遭到严重的泥砂磨损。
泥砂磨损是一种强烈的破坏形式。
水轮机过流部件均会遭到不同程度的破坏,而尤以水轮机的转轮、叶片、转轮室等流速较高的零部件为甚,破坏非常严重的水轮机甚至无法修复。
因此,多泥砂河流水电站机组大修周期差不多完全由水轮机泥砂磨损的破坏程度来决定,而检修的工作量是很大的。
例如,黄河上某水电站HL123-LH-410型水轮机,大修周期为两年左右,工期30~40天,转轮一次修复补焊耗用电焊条约1吨,磨损部件的处理占大修工作量的80%。
第6章 磨损与腐蚀失效分析汇总

金属表面 发生局部 塑性变形
磨粒嵌入金属 表面,切割金 属表面
表面被 划伤
特点 • 普遍存在于机件中; • 磨损速度较大,0.5~5 μm/h 防止措施 • 提高表面硬度(从选材方面); • 减少磨粒数量(从工作状况方面)。
(3)疲劳磨损的特征及判断。 它会引起表面金属小片状脱落,在金属表 面形成一个个麻坑,麻坑的深度多在几微 米到几十微米之间。 特点 产生接触疲劳的零件表面上出现许多针状 或痘状的凹坑,称麻点,故得名麻点磨损, 亦称疲劳磨损。 接触疲劳是裂纹形成和扩展的过程。
• 在化工、石油化工、轻工、能源、交通等 行业中,约60%的失效与腐蚀有关。化工与 石油化工行业腐蚀失效所占比例更高一些。 如近年来(1995 ~ 2000年)国内先后四次对石 化企业的压力容器使用情况进行调查,其中 对失效原因调查统计认为,在使用中因腐蚀 产生严重缺陷及材质劣化,是近年来引起容 器报废的主要原因。
6.2 腐蚀失效分析
6.2.1 腐蚀及腐蚀失效 1. 腐蚀的概念
腐 蚀 介 质
耐 蚀 金 属
(1)腐蚀的定义。 • 金属与环境介质发生化学或电化学作用,导致金 属的损坏或变质。OR在一定环境中,金属表面或界 面上进行的化学或电化学多相反应,结果使金属转 入氧化或离子状态。 (2)腐蚀介质。 • 通常不把所有的介质都称为腐蚀介质。例如,空 气、淡水、油脂等虽然对金属材料均有一定的腐蚀 作用,但并不称为腐蚀介质。一般仅把腐蚀性较强 的酸、碱、盐的溶液称为腐蚀介质。
• 腐蚀不仅损耗了地球的资源,而且因腐蚀而造成 的生产停顿、产品质量下降,甚至人身事故等损 失,更是无法估量。分析、材料腐蚀及控制的研究 给予了前所未有的关注。 (2)腐蚀介质。 • 通常不把所有的介质都称为腐蚀介质。例如,空 气、淡水、油脂等虽然对金属材料均有一定的腐蚀 作用,但并不称为腐蚀介质。一般仅把腐蚀性较强 的酸、碱、盐的溶液称为腐蚀介质。
第六章 疲劳与磨损

若应力变化幅度为常值,称为等幅交变应 等幅交变应 力。若应力变化幅度也是周期性变化的(图 a),或应力变化幅度具有偶然性(图b), 称为变幅交变应力 变幅交变应力。图b所示的也称随机交变 变幅交变应力 随机交变 应力。 应力
变动应力示意图: 变动应力示意图:
+ -
+ -
+ -
+ -交变应力的描述:交变应力的描述:上图所示的齿轮传动副,观察其中一个齿, 上图所示的齿轮传动副,观察其中一个齿,该齿参与啮合就承 否则就不承载。由于该齿承受着随时间循环变化的载荷, 载,否则就不承载。由于该齿承受着随时间循环变化的载荷, 因而齿根上任一点A的弯曲正应力也随时间循环变化 的弯曲正应力也随时间循环变化。 因而齿根上任一点 的弯曲正应力也随时间循环变化。像这样 随时间而循环变化的应力称为交变应力。 随时间而循环变化的应力称为交变应力。交变应力随时间变化 的历程称为应力谱(应力-时间曲线)。 的历程称为应力谱(应力-时间曲线)。
摩擦副真实接触面积ar只有表现接触面积a的百分之一和万分之一产生塑性流动接触面积增加接触面上压力很大很容易达到材料的压缩屈服极限sy接触点塑性变形后接触面容易产生粘合现象产生结点滑动时先将结点切开设结点的剪切强度极限为则摩擦则摩擦系数sy则摩擦系数显然此时摩擦系数取决于材料的剪切强度和抗压强度材料的剪切强度越低滑动时先将粘结点切开的强度抗压强度越高摩擦系数越小
2. 疲劳破坏的基本概念
疲劳:工程构件在服役过程中, 疲劳:工程构件在服役过程中,由于承受变动载 荷或反复承受应力和应变, 荷或反复承受应力和应变,即使所受的应力低于 断裂强度或屈服强度,也会导致裂纹萌生和扩展, 断裂强度或屈服强度,也会导致裂纹萌生和扩展, 以至构件材料断裂而失效,或使其力学性质变坏, 以至构件材料断裂而失效,或使其力学性质变坏, 这一过程,或这一现象称为疲劳。 这一过程,或这一现象称为疲劳。 疲劳是一个过程, 疲劳是一个过程,疲劳破坏过程是材料内部薄 弱区域组织在变动应力作用下, 弱区域组织在变动应力作用下,逐渐发生变化和 损伤累积、开裂,当裂纹扩展达到一定程度后发 损伤累积、开裂, 生突然断裂的过程, 生突然断裂的过程,是一个从局部区域开始的损 伤累积,最终引起整理破坏的过程。 疲劳破坏过 伤累积,最终引起整理破坏的过程。(疲劳破坏过 程可以明显地分成裂纹萌生、 程可以明显地分成裂纹萌生、裂纹扩展和最终断 裂三个部分) 裂三个部分
第六章刀具磨损和刀具使用寿命
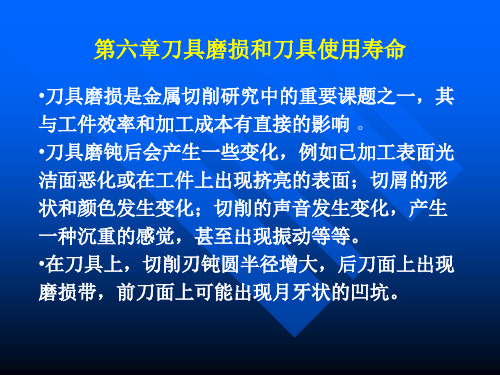
• 6.3.2刀具磨钝标准 刀具磨钝达一定限度就不能继续作用,而应进行重磨,这
个磨损限度成为刀具的磨钝标准。一般以后刀面磨损值 VB达到一定数值作为磨钝标准。磨钝标准的具体数值可 从切削用量手册中查得。 • 规定磨钝标准的两点标准: • ①一般将粗加工的磨钝标准定在正常磨损阶段的后期 临近剧烈磨损阶段以前。随着后刀面磨损值的加大,切 削力将增大,尤以Fx与Fy增大得更为显著,所以当机床、 刀具、工件系统刚度差时,刀具磨钝标准应适当减小。
6.4刀具使用寿命与切削用量的关系
• 6.4.1刀具使用寿命 • 1.刀具的使用寿命:刀具刃磨后,从开始投入切削至达到 磨钝标准的净切削时间称为刀具使用寿命,记为 T。
• 2.刀具总寿命:新刀从开始切削至报废的总切削时间,包括 多次重磨。等于刀具使用寿命与刃磨次数的乘积。
• 刀具寿命可以作为衡量材料的可加工性的标准;衡量刀具 材料切削性能的标准;衡量刀具几何参数合理性的标准。
6.2刀具的磨损原因
刀具的磨损过程和机理非常复杂,有机械负荷和硬质点 造成的机械磨损;切屑粘附造成的粘附磨损;周期性交变 载荷造成的疲劳磨损;化学效应造成的氧化和扩散磨损及 刀尖区高温塑性变形、热应力造成的磨损等。其特点可归 纳为: ⑴摩擦接触表面是活性很高的新鲜表面; ⑵摩擦接触的温度很高,可达800oC~1000oC; ⑶摩擦接触面之间的接触压应力很大,可达2GPa以上; ⑷磨损速度很快。刀具的磨损通常是机械、化学和热效应 综合作用的结果。
• 2.后刀面磨损 • 切削过程中,刀具后刀面与已加工表面之间存在着强烈的摩擦, 在后刀面上毗邻切削刃的地方磨出了沟痕,这种磨损形式称之为 后刀面磨损。 • 在切削脆性及以较低速度及较小进给量切削塑性材料时,均会发 生后刀面磨损。一般以后刀面的磨损量作为衡量刀具磨损的主要 参数。 • 后刀面磨损分为三个区,由刀尖向刀身方向分别为C、B、N,相 应的磨损量为VC、VB、VN。 • VC:磨损较大,因为刀尖强度差,散热条件差;VB:磨损均匀, 与刀尖相比,强度、散热相对较好。VN:磨损大,因其靠近前 一道工序加工后产生的加工硬化层,或毛坯表面的硬层。
第六章 材料的磨损解读

6.5.1 实验室试验的原理
1)
2)
3)
4)
5) 6)
耐磨试验在摩擦磨损试验机上进行,种类很多,代表性的: 销盘式磨损试验机,是将试样加上载荷压紧在旋转圆盘上,该 法试验速度可调,精度较高; 环块式磨损试验机,试样在圆环外表面做摩擦运动; 往复运动式磨损试验机,试样在静止平面上往复运动,可评定 导轨、缸套与活塞环等摩擦副的耐磨性; 滚子式磨损试验机,可测定材料在滑动、滚动、滚动和滑动复 合摩擦及间歇接触摩擦情况下的磨损; 砂纸磨损试验机,对磨材料为砂纸,简单易行; 快速磨损试验机,旋转圆轮用硬质合金制造,能较快测定材料 的耐磨性,也可测定润滑剂的摩擦及磨损性能。
6.1.1 摩擦 定义:两个相互接触的物体或物体与介质之 间在外力作用下,发生相对运动,或者具有 相对运动的趋势时,在接触表面上所产生的 阻碍作用称为摩擦。这种阻碍相对运动的阻 力称为摩擦力。
6.1.1.1 摩擦力
摩擦力的方向总是沿着接触面的切线方向,跟物体
相对运动方向相反,阻碍物体间的相对运动。 摩擦力(F)与施加在摩擦面上的法向压力(P)之比称
*减小零件使用时的磨损是我们学习材料磨损性能的最终目的。
薛群基院士
从事润滑失效研究,现为兰州化学物理研究所所 长,固体润滑国家重点实验室学术委员会主任,亚洲 摩擦学理事会主席,是我国材料摩擦学和摩擦化学领 域的主要学术带头人之一
6.1.2 摩损 定义:磨损是在摩擦的作用下,发生在材料 表面的局部反复进行的变形与断裂。
为摩擦系数,以μ表示,即μ=F/P。
μ静 μ μ动
μ静 >μ动
6.1.1.2 摩擦的分类 按照两接触面运动方式的不同,可以将摩擦 分为: ①滑动摩擦:指的是一个物体在另一个物 体上滑动时产生的摩擦。 ②滚动摩擦:指的是物体在力矩作用下, 沿接触表面滚动时的摩擦。
- 1、下载文档前请自行甄别文档内容的完整性,平台不提供额外的编辑、内容补充、找答案等附加服务。
- 2、"仅部分预览"的文档,不可在线预览部分如存在完整性等问题,可反馈申请退款(可完整预览的文档不适用该条件!)。
- 3、如文档侵犯您的权益,请联系客服反馈,我们会尽快为您处理(人工客服工作时间:9:00-18:30)。
6.2 磨损的基本类型
按照磨损的失效机制,磨损一般分为四类:
粘着磨损 磨粒磨损 腐蚀磨损 接触疲劳(麻点疲劳磨损)
6.2.1 磨损类型的转化
磨损类型并非固定不变,在不同的外部条件和材料特 性下,损伤机制会发生转化,由一种损伤机制变成另 一种损伤机制。
6.2.1 影响磨损的条件
外部条件比如:滑动速度、温度、润滑剂 类型等。 材料特性比如:材料与氧的化学亲和力以 及形成的氧化膜性质、材料的力学性能、 材料的耐热性等。
6.6.2 减轻磨粒磨损的主要措施
6.6.3提高接触疲劳抗力的措施 6.6.4 非金属材料的磨损特性
尺寸法:用摩擦表面法向尺寸减少量来表示,称为 线磨损量;也可用体积来表示,称为体积磨损量; 称重法:用精密天平分析试样试验前后质量的变化, 称为重量磨损量。
由于上述磨损量是摩擦行程或时间的函数, 因此,也可用比磨损量表示其磨损特性,单 位为mg/m,或mg/s。 为与习惯概念一致,还常用磨损量的倒数或 相对耐磨性表征。
6.6.1 减轻粘着磨损的主要措施
合理选择摩擦副的材质保证充分的润滑条件 等都是非常重要的,边界润滑膜与氧化膜都 能限制金属微凸体的直接接触、抑制接点的 生长。在摩擦表面上,一两个分子层的润滑 剂可使磨损急剧下降。
固体润滑是降低粘着作用的有效手段尤其在 真空条件下石墨、二硫化钼及铟等表面膜对 粘着磨损的抑制作用是很有效的。 同时可利用各种表面处理改善摩擦副的抗粘 附作用。近年来,应用广泛的有表面热处理、 表面化学处理、表面化学热处理、电镀、渗 镀、喷镀、离子镀、离子注入等。
深层剥落: 这类剥落坑较深(>0.4mm)、块大。一 般发生在表面强化的材料中,如渗碳钢中。
6.3.4.3 接触应力一般出现如下两种情况:
线接触应力:两接触物体在加载前为线接触 (如圆柱与圆柱、圆柱与平面接触)。 点接触应力:两接触物体在加载前为点接触
(如滚珠轴承)。
线接触应力
z z max 1 y / b
6.5.1 实验室试验的原理
1)
2)
3)
4)
5) 6)
耐磨试验在摩擦磨损试验机上进行,种类很多,代表性的: 销盘式磨损试验机,是将试样加上载荷压紧在旋转圆盘上,该 法试验速度可调,精度较高; 环块式磨损试验机,试样在圆环外表面做摩擦运动; 往复运动式磨损试验机,试样在静止平面上往复运动,可评定 导轨、缸套与活塞环等摩擦副的耐磨性; 滚子式磨损试验机,可测定材料在滑动、滚动、滚动和滑动复 合摩擦及间歇接触摩擦情况下的磨损; 砂纸磨损试验机,对磨材料为砂纸,简单易行; 快速磨损试验机,旋转圆轮用硬质合金制造,能较快测定材料 的耐磨性,也可测定润滑剂的摩擦及磨损性能。
6.5.2 磨损试验机示意图
6.5.3 接触疲劳磨损试验机示意图
6.6 提高材料耐磨性的途径
磨损是造成材料损耗的主要原因,也是机件3种 主要失效形式(磨损、腐蚀、断裂)之一,为 此提高机件的耐磨性越来越引起人们的重视。 粘着磨损是一种最常见的的磨损形式,它在摩 擦学的研究和应用中有非常重要的地位和作用。 世界上技术先进的国家都为粘着磨损的研究及 对策投入了大量的财力和人力。
第六章 材料的磨损性能
任何机器运转时,相互接触的零件之间都将因相对 运动而产生摩擦,而磨损正是由于摩擦产生的结果。 由于磨损,将造成表层材料的损耗,零件尺寸发生 变化,直接影响了零件的使用寿命。
同学们 知道吗?
因机件间摩擦磨损要多消耗总能源的 1/3-1/2,并引起不少机件失效。磨 损每年给人类带来上千亿美元的巨额 浪费。
剧烈磨损阶段
6.1.2.2 磨损过程的三个阶段:
表面被磨平, 实际接触面 积不断增大, 表面应变硬 化,形成氧 化膜,磨损 速率减小。
随磨损的增长,磨 耗增加,表面间隙 增大,表面质量恶 化,机件快速失 效。
斜率就是磨损速率,唯一稳定值; 大多数机件在稳定磨损阶段(AB 段)服役; 磨损性能是根据机件在此阶段 的表现来评价。
6.3 磨损的机制
6.3.1 粘着磨损
粘着磨损又称咬合磨损。由于零件 表面某些接触点在高的局部压力下 发生粘合,在相互滑动时,粘着点 又被剪切分开,接触面上有金属磨 屑被拉拽出来,这种过程反复进行 很多次,便导致了表面的损伤。
粘着磨损
6.3.1.1 粘着磨损表面特征
机 件 表 面 有 大 小 不 等 的 结 疤 。
为摩擦系数,以μ表示,即μ=F/P。
μ静 μ μ动
μ静 >μ动
6.1.1.2 摩擦的分类 按照两接触面运动方式的不同,可以将摩擦 分为: ①滑动摩擦:指的是一个物体在另一个物 体上滑动时产生的摩擦。 ②滚动摩擦:指的是物体在力矩作用下, 沿接触表面滚动时的摩擦。
6.1.1.3 摩擦的防护与运用
汽车制动器
零件的磨损让我们付出了很多时间和金钱。
衣物的磨损
同学们知道F1赛车的磨损现象吗?
轮胎压痕(SEM 5000X)
摩擦痕迹(350X)
同学们的手机外壳有没有磨损的情况? 你是怎么防护的啊?
防护
第一节 磨损的基本概念及类型
1、摩擦与磨损的概念 2、磨损的基本类型 △
6.1 摩擦与磨损的概念
6.3.2.1 磨粒磨损表面特征
表 面 有 擦 伤 或 因 明 显 犁 皱 形 成 的 沟 槽
6.3.2.2 磨粒磨损模型
此模型可得出:磨粒磨损量与接触压力、滑动距离成正 比,与材料硬度成反比,与硬材料凸出部分或磨粒形状 θ 有关。
6.3.2.3 磨粒磨损影响因素
基体材料力学性能、 基体显微组织、 磨粒硬度
在摩擦过程中,零件表面还将发生一系列物理、 化学和力学状态的变化:
1、因材料塑性变形而引起表层硬化和应力状态的变化 2、因摩擦热和其它外部热源作用下而发生的相变、淬火、 回火以及再结晶等 3、因与外部介质相互作用而产生的吸附作用
6.1.2.1 磨损过程分为以下三个阶段:
跑合(磨合)阶段
稳定磨损阶段
2 浅层剥落
条件:纯滚动或 摩擦力较小 次表层受循环切 应力,裂纹垂直 扩展 深度为0.2-0.4mm
3 深层剥落
条件:表面硬化层 深度不足 裂纹位于硬化层与 心部交界处 深度>0.4mm
6.4 耐磨性评价
耐磨性:是指材料抵抗磨损的性能,迄今还没有一 个明确的统一标准,通常用磨损量表示:磨损量越 小,耐磨性越高。 表示磨损量的方法分为尺寸法和称重法。
6.3.4.1 接触疲劳的表面特征
痘 状 贝 壳 状 凹 坑
6.3.4.2 接触疲劳类型
根据裂纹起始位置和形态的差异,分为麻点剥落 (点蚀)、浅层剥落、深层剥落三种主要类型。
麻点剥落: 是指深度在0.1-0.2mm以下的小块剥落, 裂纹一般起源于表面,剥落坑呈针状或痘状。 浅层剥落: 其剥落深度一般为0.2-0.4 mm。
6.3.1.2 粘着磨损模型示意图
此模型反映配对材料粘着力大小,决定于摩擦条件和 摩擦副材料。
阿查得估算法:
pn
d
4
2
3 sc
pL W K 3Hv
W为磨损量,K粘着磨损系数,L为滑动距离, Hv为软材料硬度
6.3.1.2 影响粘着磨损的因素
脆性材料的抗粘着能力比塑性材料高
金属性质越是相近,构成摩擦副时磨损 也越严重 摩擦速度一定时粘着磨损量随法相力 增大而增大 法相力一定时粘着磨损量随摩擦速度 的增加先增后减 表面粗糙度影响
2
2
R1 R2 pE b 1.52 ( ) L R1 R2
z max
pE R1 R2 0.418 ( ) L R1 R2
点接触应力 z z max 1 x 2
a
3
2
z max 0.388
pE 2 R
2
6.3.4.4 接触疲劳的过程
1 麻点剥落
条件:滚动加 滑动 最大综合切应 力在表层反复 作用表层产生 裂纹,扩展方 向小于45o 深度0.1-0.2mm
粘着磨损多发生在摩擦副相对滑动速度小、 接触面氧化膜脆弱、润滑较差、接触应力大 的滑动摩擦条件下. 相对运动中相互作用的 当粘着点的结合强度低于两侧材料时,则沿 表面间的摩擦、磨损、 接触面剪断,磨损量小;润滑等物理现象 当粘着点的结合强度高于两侧材料时,剪断 面发生在强度小的材料上,被剪断的材料转 移到强度高的材料上,软材料表面形成凹坑 而硬材料表面形成凸起,磨损加剧。
*减小零件使用时的磨损是我们学习材料磨损性能的最终目的。
薛群基院士
从事润滑失效研究,现为兰州化学物理研究所所 长,固体润滑国家重点实验室学术委员会主任,亚洲 摩擦学理事会主席,是我国材料摩擦学和摩擦化学领 域的主要学术带头人之一
6.1.2 摩损 定义:磨损是在摩擦的作用下,发生在材料 表面的局部反复进行的变形与断裂。
ε表示所研究材料的耐磨性。
标准试样的磨损量 被测试样的磨损量
6.5 磨损试验方法
磨损实验方法分为实物试验与实验室试验两 类。
实物试验的条件与实际情 况一致或者接近,结果可 靠性高,但实验周期长, 且结果是诸多因素的综合 反映。 周期短、成本低、易于控制 各种影响因素,科研就单个 因素的影响规律及探讨磨损 机制。
6.3.2 磨粒磨损
磨粒磨损是指硬的磨粒或凸出物在零件表面的摩 擦过程中,使材料表面发生磨耗的现象。这种磨 粒或凸出物一般指石英,砂土,矿石等非金属磨 料,也包括零件本身磨损产物随润滑油进入摩擦 面而形成的磨粒。 根据磨粒或凸出物的来源,磨粒磨损分为两体磨 粒磨损和三体磨粒磨损。前者如挫削过程,后者 如抛光过程。
6.3.3 腐蚀磨损