绿色莫来石晶须骨架多孔陶瓷的制备与性能
多孔莫来石陶瓷制备与性能研究

2019 年 第 53卷
10 月 第 5期
多孔莫来石陶瓷制备与性能研究
熊 洵 刘 浩 马 妍 王周福 王玺堂
武汉科技大学 省部共建耐火材料与冶金国家重点实验室 湖北武汉 430081
摘 要:为了改善多孔莫来石陶瓷结构与力学性能,以 d50 =11.48μm的氧化铝微粉和 d50 =26.84μm的分析 纯 SiO2为原料,分别添加 V2O5、含锆陶瓷纤维及炭黑,通过固相烧结法制得了莫来石多孔陶瓷。采用 XRD、 SEM等研究了温度、催化剂含量、陶瓷纤维以及炭黑的引入对莫来石多孔陶瓷结构与性能的影响。结果表明: V2O5的添加促进了莫来石的生长,降低了试样的体积密度;引入含锆陶瓷纤维,在 V2O5 液相的辅助作用下,形 成了陶瓷纤维-莫来石晶须多级结构,显著提高了试样的耐压强度;炭黑的氧化为莫来石晶须提供了生长空间, 有助于增大试样气孔率,降低体积密度。 关键词:多孔陶瓷;莫来石晶须;陶瓷纤维;多级结构
20%(w)无水乙醇湿混 12h,然后于 110℃干燥12h, 3h热处理。
国家自然科学基金(51474166,51672195);湖北省自然科学基
金创新群体项目(2017CFA004)。
熊洵:男,1995年生,硕士研究生。
Email:893887150@qq.com
通信作者:刘浩,男,1978年生,教授。
Email:wustlh@163.com
收稿日期:2019-02-17
研究者通过引入催化剂、助烧剂、陶瓷纤维等,在 调节显微结构、改善莫来石多孔陶瓷性能等方面开展 了大量工作;如 Rashad等[4]使用黏土和 AlF3·3H2O 制备出了针状多孔莫来石,其中,AlF3·3H2O降低了 莫来石形成温度,同时促进了莫来石生长,增大了莫 来石晶须尺寸。徐海等[5]的研究表明,Y2O3 与 SiO2 在 1100℃反应生成了 Y2Si2O7,并溶解到液相中,晶 须之间通过高温液相粘结,提高了试样的力学强度。 李和祯等[6]用共沉淀法制备了高纯莫来石前驱粉体, 并掺杂 CeO2制备莫来石陶瓷,形成了低黏度 Ce-Al- Si-O液相,促进了莫来石晶粒的发育,莫来石晶粒由 圆柱状 逐 渐 变 成 短 柱 状,增 大 了 晶 粒 尺 寸。 Vecchio 等[7]在铝钛金属化合物中添加氧化铝陶瓷纤维制备 了 Ti-Al3Ti-Al2O3复合材料,复合材料强度和断裂韧 性 的 提 高,归 结 于 氧 化 铝 陶 瓷 纤 维 的 连 接 作 用。 Hua等[8]采用冷压法制备了 ZrO2 纤维增强 NiFe2O4 陶瓷材料,ZrO2 与 NiFe2O4 具有良好的热力学和化 学 兼 容 性 ,通 过 纤 维 结 合 、纤 维 拔 出 、相 变 和 基 体 约 束等效应,有 效 提 高 了 材 料 的 力 学 性 能。 在 多 孔 陶 瓷孔隙 结 构 调 控 方 面,王 砚 军 等[9]分 别 以 TiH2 和
新型多孔陶瓷材料的制备与性能优化技术

新型多孔陶瓷材料的制备与性能优化技术多孔陶瓷材料是一种具有优异性能的功能性材料,它不仅具备了陶瓷材料的高温稳定性、耐腐蚀性和机械强度,还具有较大的比表面积、开放的孔隙结构和良好的吸附性能。
目前,多孔陶瓷材料已经广泛应用于过滤、分离、催化、吸附等领域。
本文将重点介绍新型多孔陶瓷材料的制备方法和性能优化技术。
一、制备方法1. 模板法模板法是一种较为常见的多孔陶瓷材料制备方法。
在此方法中,首先制备一种模板,如聚苯乙烯微球、有机胶体等,然后通过沉积、烧结等工艺,将模板与陶瓷材料有机地结合在一起,并最终通过高温处理将模板燃烧掉,留下孔隙。
这种方法制备的多孔陶瓷材料具有较为规则的孔隙结构和较高的孔隙率。
2. 泡沫法泡沫法是一种利用泡沫状原片作为模板制备多孔陶瓷材料的方法。
在此方法中,首先制备一种泡沫状原片,如聚苯乙烯泡沫,然后通过浸渍、烧结等工艺,将陶瓷材料沉积在泡沫状原片上,并最终通过高温处理将泡沫状原片燃烧掉,留下孔隙。
与模板法不同,泡沫法制备的多孔陶瓷材料具有较为复杂的孔隙结构和较低的孔隙率。
3. 化学法化学法是一种利用化学反应制备多孔陶瓷材料的方法。
在此方法中,通过合成陶瓷材料的前驱体,如溶胶-凝胶法、水热合成法等,然后通过调控反应条件和添加外部剂,如有机膨胀剂、表面活性剂等,在陶瓷材料中形成孔隙结构。
这种方法制备的多孔陶瓷材料具有较高的比表面积和较好的孔隙分布。
二、性能优化技术1. 改变孔隙结构多孔陶瓷材料的性能主要受其孔隙结构的影响。
通过调控制备工艺和添加外部剂等方法,可以改变多孔陶瓷材料的孔隙结构,如孔隙大小、孔隙形状、孔隙分布等。
例如,可以通过调节烧结温度和烧结时间,控制陶瓷材料的颗粒结合程度和孔隙大小;可以添加聚合物等外部剂,调节陶瓷材料的孔隙形状和孔隙分布。
2. 表面修饰多孔陶瓷材料的性能还可以通过表面修饰来进行优化。
表面修饰可以改变多孔陶瓷材料的表面性质,增强其化学反应活性和吸附能力。
多孔陶瓷材料的制备及性能研究
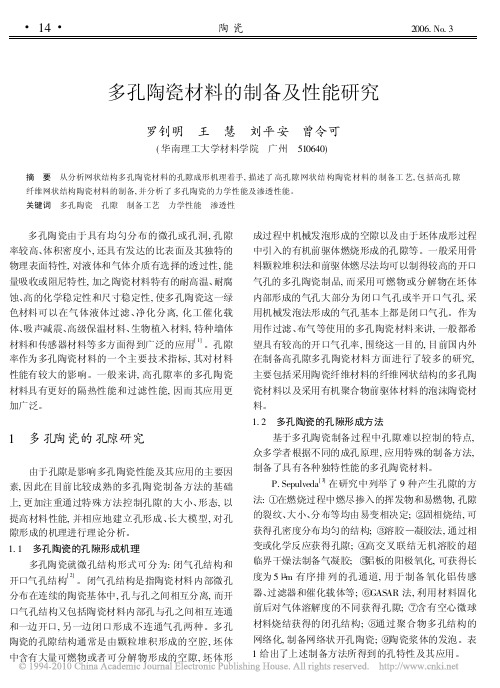
多孔陶瓷材料的制备及性能研究罗钊明 王 慧 刘平安 曾令可(华南理工大学材料学院 广州 510640)摘 要 从分析网状结构多孔陶瓷材料的孔隙成形机理着手,描述了高孔隙网状结构陶瓷材料的制备工艺,包括高孔隙纤维网状结构陶瓷材料的制备,并分析了多孔陶瓷的力学性能及渗透性能。
关键词 多孔陶瓷 孔隙 制备工艺 力学性能 渗透性多孔陶瓷由于具有均匀分布的微孔或孔洞,孔隙率较高、体积密度小,还具有发达的比表面及其独特的物理表面特性,对液体和气体介质有选择的透过性,能量吸收或阻尼特性,加之陶瓷材料特有的耐高温、耐腐蚀、高的化学稳定性和尺寸稳定性,使多孔陶瓷这一绿色材料可以在气体液体过滤、净化分离,化工催化载体、吸声减震、高级保温材料、生物植入材料,特种墙体材料和传感器材料等多方面得到广泛的应用[1]。
孔隙率作为多孔陶瓷材料的一个主要技术指标,其对材料性能有较大的影响。
一般来讲,高孔隙率的多孔陶瓷材料具有更好的隔热性能和过滤性能,因而其应用更加广泛。
1 多孔陶瓷的孔隙研究由于孔隙是影响多孔陶瓷性能及其应用的主要因素,因此在目前比较成熟的多孔陶瓷制备方法的基础上,更加注重通过特殊方法控制孔隙的大小、形态,以提高材料性能,并相应地建立孔形成、长大模型,对孔隙形成的机理进行理论分析。
1.1 多孔陶瓷的孔隙形成机理多孔陶瓷就微孔结构形式可分为:闭气孔结构和开口气孔结构[2]。
闭气孔结构是指陶瓷材料内部微孔分布在连续的陶瓷基体中,孔与孔之间相互分离,而开口气孔结构又包括陶瓷材料内部孔与孔之间相互连通和一边开口,另一边闭口形成不连通气孔两种。
多孔陶瓷的孔隙结构通常是由颗粒堆积形成的空腔,坯体中含有大量可燃物或者可分解物形成的空隙,坯体形成过程中机械发泡形成的空隙以及由于坯体成形过程中引入的有机前驱体燃烧形成的孔隙等。
一般采用骨料颗粒堆积法和前驱体燃尽法均可以制得较高的开口气孔的多孔陶瓷制品,而采用可燃物或分解物在坯体内部形成的气孔大部分为闭口气孔或半开口气孔,采用机械发泡法形成的气孔基本上都是闭口气孔。
多孔陶瓷的制备及性能分析

第一章综述1.1 多孔陶瓷的概述多孔陶瓷是一种经高温烧成、体内具有大量彼此相通或闭合气孔结构的陶瓷材料,是具有低密度、高渗透率、抗腐蚀、耐高温及良好隔热性能等优点的新型功能材料。
多孔陶瓷的种类繁多,几乎目前研制生产的所有陶瓷材料均可通过适当的工艺制成陶瓷多孔体。
根据成孔方法和孔隙结构的不同,多孔陶瓷可分为三类:粒状陶瓷烧结体、泡沫陶瓷和蜂窝陶瓷。
根据所选材质不同,可分为刚玉质、石英质、堇青石质、莫来石质、碳化硅质、硅藻土质、氧化锆质及氧化硅质等。
多孔陶瓷材料一般具有以下特性:化学稳定性好,可制成使用于各种腐蚀环境的多孔陶瓷;具有良好的机械强度和刚度,在气压、液压或其他应力载荷下,多孔陶瓷的孔道形状和尺寸不会发生变化;耐热性好,用耐高温陶瓷制成的多孔陶瓷可过滤熔融钢水和高温气体;具有高度开口、内连的气孔;几何表面积与体积比高;孔道分布较均匀,气孔尺寸可控,在0.05~600µm范围内可以制出所选定孔道尺寸的多孔陶瓷制品。
多孔陶瓷的优良性能,使其已被广泛应用于冶金、化工、环保、能源、生物等领域。
如利用多孔陶瓷比表面积高的特性,可制成各种多孔电极、催化剂载体、热交换器、气体传感器等;利用多孔陶瓷吸收能量的性能,可制成各种吸音材料、减震材料等;利用多孔陶瓷的低密度、低热传导性,可制成各种保温材料、轻质结构材料等;利用多孔陶瓷的均匀透过性,可制成各种过滤器、分离装置、流体分布元件、混合元件、渗出元件、节流元件等。
因此,多孔材料引起了材料科学工作者的极大兴趣并在世界范围内掀起了研究热潮。
1.2 多孔陶瓷的制备方法多孔陶瓷是由美国于1978年首先研制成功的。
他们利用氧化铝、高岭土等陶瓷材料制成多孔陶瓷用于铝合金铸造中的过滤,可以显著提高铸件质量,降低废品率,并在1980年4月美国铸造年会上发表了他们的研究成果。
此后,英、俄、德、日等国竞相开展了对多孔陶瓷的研究,已研制出多种材质、适合不同用途的多孔陶瓷,技术装备和生产工艺日益先进,产品已系列化和标准化,形成为一个新兴产业。
莫来石结合碳化硅多孔陶瓷的制备与性能研究的开题报告
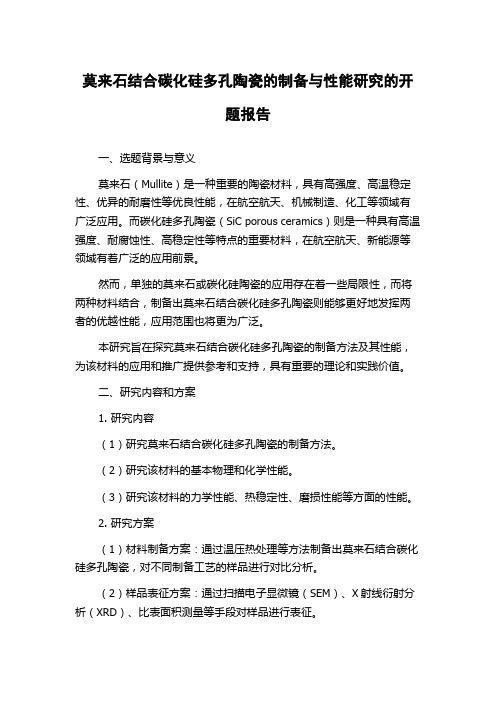
莫来石结合碳化硅多孔陶瓷的制备与性能研究的开题报告一、选题背景与意义莫来石(Mullite)是一种重要的陶瓷材料,具有高强度、高温稳定性、优异的耐磨性等优良性能,在航空航天、机械制造、化工等领域有广泛应用。
而碳化硅多孔陶瓷(SiC porous ceramics)则是一种具有高温强度、耐腐蚀性、高稳定性等特点的重要材料,在航空航天、新能源等领域有着广泛的应用前景。
然而,单独的莫来石或碳化硅陶瓷的应用存在着一些局限性,而将两种材料结合,制备出莫来石结合碳化硅多孔陶瓷则能够更好地发挥两者的优越性能,应用范围也将更为广泛。
本研究旨在探究莫来石结合碳化硅多孔陶瓷的制备方法及其性能,为该材料的应用和推广提供参考和支持,具有重要的理论和实践价值。
二、研究内容和方案1. 研究内容(1)研究莫来石结合碳化硅多孔陶瓷的制备方法。
(2)研究该材料的基本物理和化学性能。
(3)研究该材料的力学性能、热稳定性、磨损性能等方面的性能。
2. 研究方案(1)材料制备方案:通过温压热处理等方法制备出莫来石结合碳化硅多孔陶瓷,对不同制备工艺的样品进行对比分析。
(2)样品表征方案:通过扫描电子显微镜(SEM)、X射线衍射分析(XRD)、比表面积测量等手段对样品进行表征。
(3)性能测试方案:对样品的力学性能、热稳定性、磨损性能等进行测试和分析,包括压缩强度、抗张强度、杨氏模量、热膨胀系数、热导率等方面。
三、预期成果本研究将在莫来石结合碳化硅多孔陶瓷的制备和性能研究方面取得以下预期成果:(1)制备出优异性能的莫来石结合碳化硅多孔陶瓷,并对其制备工艺进行优化;(2)对该材料的基本物理和化学性质进行系统研究;(3)对该材料的力学性能、热稳定性、磨损性能等方面的性能进行测试和分析,得出该材料的应用潜力和优化方向,为该材料的应用和推广提供参考。
四、研究工作计划本研究计划分为以下几个阶段:(1)文献调研和资料收集:搜集与莫来石结合碳化硅多孔陶瓷的制备和性能研究相关的文献和资料,对该材料的研究现状进行了解和分析;(2)材料制备和表征:根据文献调研的结果确定样品的制备工艺,利用SEM、XRD等手段对样品进行表征;(3)性能测试和分析:对样品的力学性能、热稳定性、磨损性能等方面的性能进行测试和分析,得出该材料的应用潜力和优化方向;(4)撰写论文和答辩准备:整理出实验结果和数据,提交论文并准备答辩。
莫来石晶须的特性及应用

图 6 用 莫来 石 晶 须制 备 的 多孔 基体 ( W- M B)
而出现气 孔率 比较高 的情况 。 所测 数据支 持 了这样 的
在制备 成本高 、 抗氧化 性差 等 问题 。要使 晶须 在材料
复合 中发挥 作用 , 须 考虑 的主要 因素包 括 : 必 晶须 与
由 S M 照 片可 以看 出 , 样 E E 试 D骨 料颗 粒 比较
基 体 的界面性 质 ( 面结合 力 、 界 物理 匹配 、 化学相 容 ) 、
晶须 的性能 ( 长径 比、 晶须 含量 、 晶须 强度 、 晶须排 布 )
圆润 , 孔 呈均匀分 布 , 气 骨料形 状 明显有别 于 另外 三
个 试样 。试 样 MW— B中 晶须 与 粘接 料 反 应 比较充
等。 基 于莫来 石 晶须所 具 备 的一 些 优异性 能 , 以预 可
见其在 如下领 域可望得 到 较好 的应用 :
分, 被包 裹且 略有 熔蚀 , 仍可 分辨 出所用 原料 的晶 但 须形 状 。试 样 M C中晶须 与粘 接料 结合 牢 固 , W— 晶
江苏陶瓷
Ja guCea is in s rm c
20 0 7年 6月 第 4 0卷 第 3期
表 2 三种 多孔基 体 的 主 要特 性
从 上 表 中多 孔基 体 的物 理性 能 的对 比可 以 明显
看出, 样 E 试 D的烧 成 收 缩最 小 , 是 显 气 孔率 却 也 但
圈 5 用奠 来石 晶 须 制备 的 多 孔基体 ( - MW A)
多孔莫来石陶瓷的制备和性能研究

的条件 下采用 传统 的粉 末处 理技 术 制 成 , 这 些 形 成
剂 包括 锯屑 、 淀粉 、 石 墨和一 些有 机材 料 。这 种 方法 可 以通 过调 整孔 隙形成 剂 的加入 量 、 颗 粒大 小 、 形状
时, 制 备 了 气孔 率 为 6 1 % 的 多 孔莫 来 石 陶瓷 , 其 具有 相 当高 的比 表 面 积 ( 1 2 . 4 m ・ ) , 能很好的阻止裂纹扩展 , 具 有
很好的抗热震性 。
关 键 词 :反应合成 ; 机械特性 ; 显微结构 ; 莫来石
中图分 类号 :T Q 1 7 5 . 7 1 2 . 1
器 。更 简单 的是 , 多孔 材 料 可 以在使 用 孔 隙形 成 剂
方形 试 样 。通过 几何 方 法 , 得 到生 坯 的相 对 密 度 约
等于 3 7 %。反应 结合 实验 是在 空气 气 氛下 , 在 1 4 5 0~1 6 5 0 q c的箱 式 炉 中 进 行 , 升 温 和 降温 速 率 为 5 ℃・ ai r n ~。 在 1 1 0 0 c 【 = 下保温 5 h确 保 S i C完 全 氧
以及分 布来 直接 改变气孔 特 性 。 同时 , 多孔莫 来石 陶瓷 材料具 有 低热 膨胀 系数 、 良好 的抗热 震性 以及 在高 温条件 下非 常好 的机 械性
能和化 学稳 定性 , 所 以近年 来其 发展 受到 广泛关 注 。
研究表 明 , 高致 密性莫 来 石 可 以用 A 1 O 和 s i 或者 S i C混合 粉反应 合成 制得 。s i 和S i C在 空 气 中加 热
莫来石晶须纤维多孔材料的制备及性能研究

第1章绪论1.1前言随着工业的发展和人口数量的不断增加,能源储量不断降低。
进入21世纪后,全球一体化程度进一步提高,能源危机也逐渐成为全世界范围内面临的重大议题。
面临能源危机,除了加大力度开发新能源及可再生能源外,如何实现对资源的合理利用,通过科技减少资源浪费也同样重要。
在工业生产中,每年都有大量的热能由于隔热系统不够完善而遭到浪费,最终导致能源利用率降低。
比如在金属冶炼、建材等需要高温条件进行生产的行业,大多是耗能高、污染重。
因此在工业生产领域,通过研发先进生产工艺及技术制备出隔热性能更好的隔热材料,以完善隔热系统来提高能源利用率,避免过多的资源浪费显得尤为重要。
隔热材料不仅在工业生产领域有着广泛的应用,它在飞行器的热防护系统也是不可缺少的一部分。
随着科技的发展尤其是航空航天技术的发展,飞行器的运行速度不断提高,在飞行过程中,飞行器外表与空气摩擦产生大量热量,导致飞行器表面温度高达2000o C,为了确保飞行器内部仪器、仪表的正常运行,保障飞行安全,就必须配备绝热性能良好的热防护系统。
飞行器的隔热系统主要是隔热瓦组成的隔热层。
这些隔热瓦除了具有耐高温的性能外还需要具有较好的抗热震性能,能够承受住热冲击和热梯度,同时具有低密度、高比强度的特点。
总之,隔热材料不仅在工业生产提高能源利用率方面有着广泛应用,也在航空航天等国防领域的热防护系统方面也不可缺少,因此,研制低密度、高比强度、低成本、高重复利用率的隔热材料有着重要意义。
1.2 隔热材料的定义及分类隔热材料,即为能阻滞热流传递的材料,又称绝热材料,它具有低密度、高气孔率、低热导率等特点[1,2]。
根据所组成材料的不同,隔热材料主要可以分为以下几类:金属隔热材料、陶瓷隔热材料、碳基复合隔热材料、纤维隔热材料。
金属隔热材料具有韧性大、强度高、热匹配好等优点,但是由于金属材料耐高温性能较差,密度较大,不能应用在航空航天领域。
陶瓷隔热材料主要由高温陶瓷及其复合材料组成,耐高温性能较好,可以在2000o C条件下保持稳定,但陶瓷隔热材料的抗热震性较差。
- 1、下载文档前请自行甄别文档内容的完整性,平台不提供额外的编辑、内容补充、找答案等附加服务。
- 2、"仅部分预览"的文档,不可在线预览部分如存在完整性等问题,可反馈申请退款(可完整预览的文档不适用该条件!)。
- 3、如文档侵犯您的权益,请联系客服反馈,我们会尽快为您处理(人工客服工作时间:9:00-18:30)。
绿色莫来石晶须骨架多孔陶瓷的制备与性能建筑废弃物排放量大,资源化利用率低,其大量堆积、填埋不仅挤占良田,污染水土资源、空气环境,甚至会造成严重的二次灾害。
建筑废弃物主要化学成分是SiO<sub>2</sub>、Al<sub>2</sub>O<sub>3</sub>、CaO等,属于有用矿产资源。
莫来石是大气压下Al<sub>2</sub>O<sub>3</sub>-SiO<sub>2</sub>系中稳定的化合物,以此为基体的多孔陶瓷具有密度低、导热系数小、抗热震性好、热膨胀系数低、高温力学性能好、耐腐蚀等优点,广泛用于隔热、过滤、吸音、催化剂载体等领域。
但是,其作为多孔材料,不可避免孔隙率高而机械强度低的缺点,且其传统制备原料主要源于高岭土等不可再生资源。
因此,本文以建筑废弃物的精细化利用、莫来石多孔陶瓷的制备、原位晶须增强多孔陶瓷为契机,利用建筑废弃物低温制备莫来石晶须骨架多孔陶瓷,详细研究工艺、配方、结构、性能之间的关系,并探讨相关的机理。
本文首先研究了建筑废弃物的物理化学性质和莫来石晶须的烧成过程与机理。
采用红外光谱分析、热重分析、硅酸盐快速测定、晶相分析等手段,研究了建筑废弃物主要化学成分为SiO<sub>2</sub>、Al<sub>2</sub>O<sub>3</sub>和CaO。
然后,以其为主要原料,氧化铝做补充铝源(按莫来石经典组成
3Al<sub>2</sub>O<sub>3</sub>.2SiO<sub>2</sub>配比),综合采用莫来石晶须生成工艺中的气相法和氧化物掺杂法,制备原位莫来石晶须增强的晶须骨架多孔陶瓷。
详细研究烧成温度、保温时间、升温速率、成型压力、球磨时间等工艺参数对烧结样品晶相组成、断面微观结构、吸水率、开口孔隙率、孔径分布、体积密
度、线收缩率、抗弯强度等性能的影响,得出莫来石晶须制备的较佳工艺参数。
在此较佳工艺参数基础上,详细研究了晶须催化剂和烧结助剂对莫来石晶须形貌及多孔陶瓷结构和性能的影响。
实验结果表明,当向坯料中引入一定量的氟化物(AlF<sub>3</sub>、
CaF<sub>2</sub>)和氧化物(MoO<sub>3</sub>、B<sub>2</sub>O<sub>3</sub>、V<sub>2</sub>O<sub>5</sub>、CeO<sub>2</sub>)分别用作晶须催化剂和烧结助剂时,均能有效促进样品莫来石化反应的发生和莫来石晶须的生成,从而有效提高多孔陶瓷性能。
当向原料中引入12 wt%含量的AlF<sub>3</sub>和3 wt%含量的MoO<sub>3</sub>时,样品显示出优异特性,开口孔隙率67.4±0.5%,抗弯强度24.0±0.8 MPa,莫来石晶须分布均匀,晶须直径0.05<sup>0</sup>.5μm,长度8<sup>1</sup>0μm,长径比20<sup>3</sup>0。
此外,研究了铝源对晶须骨架多孔陶瓷结构和性能的影响。
实验结果表明,氧化铝含量、粒径、晶型对莫来石晶须生成及多孔陶瓷性能均有显著影响。
当氧化铝添加量为50 wt%时,能够制备出形貌较好的莫来石晶须;采用沉淀法制备出的不同晶型的过渡态氧化铝,因其表面缺陷大、活性高,用作铝源时,促进了坯料低温下发生莫来石化反应;纳米氧化铝以其粒径较小、表面活化能较大的优势,促进了莫来石的低温制备,但原料易团聚,致使晶须细小,分布不均匀。
其中,沉淀法850℃煅烧制备出的δ-Al<sub>2</sub>O<sub>3</sub>,用作制备多孔陶瓷的补充铝源时,在烧成温度1250℃即可制得莫来石晶须,此时,多孔陶瓷样品开口孔隙率65.9±0.8%,体积密度1.28 g.cm<sup>-3</sup>。
最后,研究了烧结助剂对晶须骨架多孔陶瓷低温烧成及烧成样品结构和性能的影响。
实验结果发现,烧结助剂的单掺、共掺均能有效促进莫来石晶须及晶须
骨架多孔陶瓷的低温烧成。
单元烧结助剂中,B<sub>2</sub>O<sub>3</sub>的助熔效果最好,烧成温度1100℃即可制备出莫来石晶须,同时又能生成一定量的硼酸铝晶须,烧成温度1150℃制得的多孔陶瓷具有较好性能,开口孔隙率79.9±0.9%,抗弯强度15.6±0.7 MPa,体积密度0.85g.cm<sup>-3</sup>,导热系数0.24
W.mK<sup>-1</sup>,1000<sup>2</sup>000 Hz平均吸声系数0.80。
双元烧结助剂中,3 wt%含量MoO<sub>3</sub>和3 wt%含量V<sub>2</sub>O<sub>5</sub>共掺,1300℃烧成温度下的莫来石晶须长度较长,长径比较大,多孔陶瓷性能更优,开口孔隙率73.4±0.7%,抗弯强度28.9±0.6 MPa,体积密度0.93
g.cm<sup>-3</sup>,导热系数0.36 W.mK<sup>-1</sup>,1000<sup>2</sup>000 Hz平均吸声系数0.60。