水泥稳定碎石土7天无侧限抗压强度测量方法
水泥稳定碎石无侧限抗压强度计算公式

水泥稳定碎石无侧限抗压强度计算公式水泥稳定碎石无侧限抗压强度是用于评估水泥稳定碎石材料的强度和稳定性的重要指标。
该指标常用于设计和施工过程中,以确保水泥稳定碎石材料能够满足工程要求并具备足够的承载能力。
本文将就水泥稳定碎石无侧限抗压强度的计算公式进行详细讨论,并探讨其在工程实践中的应用价值。
1. 水泥稳定碎石简介水泥稳定碎石是一种常用的路基材料,通过添加适量的水泥和充分的机械拌和作用,使岩石颗粒与水泥胶结,形成坚实的结构。
这种材料具有较高的强度和耐久性,在道路、机场、堤坝等工程中被广泛应用。
2. 无侧限抗压强度的意义无侧限抗压强度是评估水泥稳定碎石材料抗压能力的重要指标。
它表示材料在受到均匀的压力作用下,发生破坏或塑性变形的能力。
无侧限抗压强度的高低决定了材料的承载能力,直接影响工程的安全性和可靠性。
3. 水泥稳定碎石无侧限抗压强度计算公式水泥稳定碎石无侧限抗压强度的计算公式一般采用以下形式:UCS = K × P其中,UCS表示无侧限抗压强度,K为系数,P为试件的峰值荷载。
具体来说,在进行实验室强度试验时,首先需要制备一定规格的水泥稳定碎石试件。
试件在试验机上受到均匀的压力加载,通过观察试件的破裂模式和记录荷载-位移曲线,可以确定试件的峰值荷载。
接下来,根据相应的系数K,将试件的峰值荷载代入计算公式中,即可得到水泥稳定碎石的无侧限抗压强度。
4. 水泥稳定碎石无侧限抗压强度的影响因素水泥稳定碎石无侧限抗压强度受到多个因素的影响,主要包括材料性质和试验条件。
材料性质方面,颗粒组成、水泥掺量、拌和比以及固养时间等都会对无侧限抗压强度产生影响;试验条件方面,加载速率和湿度等因素也会对试验结果产生一定的影响。
5. 水泥稳定碎石无侧限抗压强度的应用价值水泥稳定碎石无侧限抗压强度的准确测定和合理应用对于工程设计和施工决策至关重要。
根据无侧限抗压强度的计算结果,可以评估水泥稳定碎石材料的承载能力,为工程提供依据;可以根据不同工程要求,选择合适的无侧限抗压强度作为设计参数,确保工程的安全性和经济性。
水泥稳定碎石基层施工技术指导和检验要点

水泥稳定碎石基层施工技术指导和检验要点一、设计要求:水泥稳定碎石基层设计宽度:全幅10m,厚度20cm,压实度98%,7天无侧限抗压强度达到3.5Mpa。
二、材料的要求:1.碎石级配必须符合规范要求,其颗粒组成和塑性指数应分别满足《公路路面基层施工技术规范》(JTJ034-2000)表3.2.2的有关规定,碎石最大粒径控制在31.5mm以内。
2、碎石料压碎值不大于30%。
3、配料要准确,拌合要均匀,没有粗细颗粒离析现象。
4、碎石含泥量不得超过3%,液限应小于28%,塑性指数应小于9%。
5、碎石材料级配问题采购碎石中的石屑含量过少,没有很好填充空隙,从而混合料很难压实。
根据规范规定,二级公路宜采用表1中的2号级配;一级公路宜采用表1中的3号级配,单个颗粒的最大粒径不应超过31.5mm。
各粒的通过量以接近级配范围的中高限为宜,4.75mm 以下的颗粒含量在40%左右较为合适,达不到的可以掺河砂或石屑补充,使级配碎石达到规范要求,这样比较容易压实。
三、施工要求:1、下承层(底基层)须经验收合格。
摊铺前,对原旧路底基层有松散现象及时清理,如发现表面过干,表面应适当洒水,如下承层过湿发生软弹现象,采取挖开晾或换填等措施处理,直至合格为止。
2.每10m放样出中、边桩,松铺系数按试验路段数据指导,用松铺系数计算碎石堆料距离,避免料不够或过多。
3.级配碎石必须提前24小时进行闷料湿润,碎石含水量应大于最佳含水量2%,以补偿摊铺及碾压过程中的水份损失。
要求使用强制式搅拌机(产能500t/h),主要是强制式搅拌机拌出的混合料比较均匀,容易成型,对保证质量起到关键作用,有效地避免了质量隐患,拌和时间保证在1~2min之间。
4.细料要达到40%左右(如果没有建议在原级配碎石基础上把石屑掺加到10%左右),所得到的密实状态是最佳密实状态,在施工过程中,水泥用量宜比设计配合比增加0.5~1.0%,5.拌和站离施工现场较远时,含水量的控制更为重要,主要施工员或试验员要作好灰、水的含量控制,同时要求做好水泥滴定和水量的测定等试验工作,并指导好施工,同时做好无侧限抗强度试验的抽样工作。
水泥稳定碎石土7天无侧限抗压强度测量方法

水泥稳定土击实实验一、目的适用范围目的测定水泥稳定混合料料样最大密度及最优含水率)。
适用范围最大粒径≤37mm。
二、实验仪器及击实筒天平(称量为2kg,感量为1g)、台秤(称量为10kg,感量为5g)、推土器、喷水设备、碾土设备、拌土设备、修土刀、小量筒、盛土盘、测含水率设备、平直尺及保湿设备等。
( 1 )轻型击实:锤底直径50mm,击锤质量为2.5kg ,落距为300mm,单位体积击实功为598.2kJ /m3(图I-25 ),分 3 层击实。
(2)重型击实:锤底直径50mm,击实筒内径为击锤质量为 4.5kg ,落距为450mm,单位体积击实功为2687和2677.2kJ /m3击实方法及击实筒规格粒径25mm颗粒<20%和含黏土多用甲、乙法;碎石土和粒径25mm颗粒>20%用丙法(本次实验选用丙法)三、试样制备1、按高速公路基层标准级配(标准级配已发到每个实验小组)用图解法对A、B、C、D 四种矿料(干集料)进行掺配。
2、每个实验小组分别按四分法至少准备 5 个试样(试样不重复使用),每个样重 5.5kg(集料总量 5.5kg ×5 个)。
3、按预估最佳含水率为4%,每个实验小组的 5 个试样分别加入不同水(以4%为中心按1%含水率级差递增减)。
按预定含水率制备试样方法:每个试样取 5.5kg ,试样加水量计算方法m w=5.5kg ×混合料预达含水率%,例:样1:m w1=5.5kg×2%;样2m w2=5.5kg×3%;样3m w3=5.5kg×4%;样4m w4=5.5kg× 5%;样5m w5=5.5kg×6%。
在调土盘上,每个样分别用喷水设备加预定水量,均匀搅拌后,装入保湿器或塑料袋内,浸润(闷土)备用。
浸润时间:拌匀后闷料碎石土2-4 小时备用(高塑性土不少于24h,低塑性土不少于12h)。
四、击实实验1、击实前加入水泥拌匀(按规范推荐水泥剂量值3%、4%、5%、6%、7%加水泥):水泥用量=水泥剂量×每个试样干集料质量。
水稳层7天无侧限抗压强度取样标准

水稳层7天无侧限抗压强度取样标准水稳层是指在道路基层上铺设的采用砂石、水泥等材料进行混合、碾压、固化形成的路面层,具有一定的抗压能力和稳定性。
水稳层的7天无侧限抗压强度是指在水稳层构筑完成后,经过7天养护后,进行无侧限抗压强度测试的结果。
1.取样位置:从水稳层表面取样,应选择代表性好、无破损、新刷破面的试件。
2.取样数量:每个试验点应取3个试件,取样数量应根据设计要求进行确定。
3.取样方法:采用随机取样的方法,避免代表性不足。
每个试件应保持形状规则、边界清晰、表面光滑。
4. 取样尺寸:试件的直径应为150mm,高度应为300mm。
5.取样时间:在水稳层完成摊铺后,须养护3天以上,最长不超过7天后方可进行取样。
6.取样方式:采用环状剥离法进行取样,即从水稳层表面剥掉上、下两层,保留中间一层进行剥离。
剥离面积不应小于80%。
7.取样保存:取样完成后的试件应立即放入标有标识的密封包装袋中,并标明取样位置、时间等信息。
1.试件准备:将取样的试件放置在水浸砂浆中养护24小时以上,并保持试件的湿润状态。
2.压力机测试:将试件放置在压力机下,调整夹紧装置使其与试件表面平行,然后逐渐施加力,使试件承受垂直向下的压力。
3.抗压强度计算:根据试件的最大承载力和试件的几何尺寸,计算出试件的抗压强度。
一般来说,水稳层7天无侧限抗压强度的要求一般在2MPa以上。
总结起来,水稳层7天无侧限抗压强度的取样标准包括取样位置、数量、方法、尺寸、时间、保存等方面的要求。
测试方法采用压力机进行,通过计算试件的最大承载力来得出抗压强度。
这些标准和方法的严格执行可以确保水稳层的质量,保证道路的稳定性和耐久性。
5%水泥稳定碎石配合比设计说明
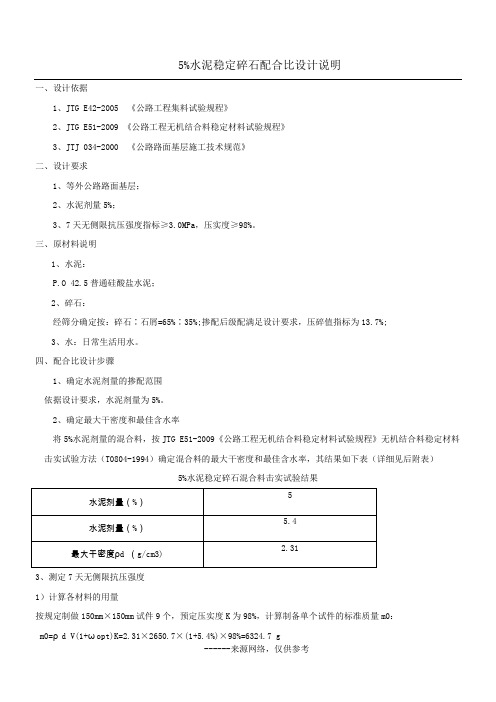
5%水泥稳定碎石配合比设计说明一、设计依据1、JTG E42-2005 《公路工程集料试验规程》2、JTG E51-2009 《公路工程无机结合料稳定材料试验规程》3、JTJ 034-2000 《公路路面基层施工技术规范》二、设计要求1、等外公路路面基层;3、测定7天无侧限抗压强度1)计算各材料的用量按规定制做150mm×150mm试件9个,预定压实度K为98%,计算制备单个试件的标准质量m0: m0=ρd V(1+ωopt)K=2.31×2650.7×(1+5.4%)×98%=6324.7 g考虑到试件成型过程中的质量损耗,实际操作过程中每个试件质量增加1%,即m0'=m0×(1+1%)=6324.7×(1+1%)=6387.9g每个试件的干料总质量:m1=m0'/(1+ωopt)= 6387.9/(1+5.4%)=6060.7 g 每个试件中水泥质量:m2=m1×α/(1+α)=6069.7×5%/(1+5%)=288.6 g 每个试件中干土质量:m3=m1-m2=6060.7-288.6=5772.1 g 每个试件中的加水量:mw=(m2+m3)×ωopt=(288.6+5772.1)×5.4%=327.3 g 故配制单个5%水泥剂量的试件各材料的用量为:水泥:m2= 288.6 gZa参五、确定试验室配合比经试验7天无侧限抗压强度满足设计要求。
故按上述击实结果计算每立方米各材料用量。
由击实得最大干密度为2310kg/m3,每立方米材料的干料质量为2310kg,故每立方米水泥质量为2310×5%÷(1+5%)=110kg,每立方米干土质量为 2310-110=2200kg每立方米大碎石质量为2200×65%=1430kg每立方米石屑质量为2200×35%=770kg每立方米水质量为2310×5.4%=124.7kg故确定试验室配合比为水泥∶碎石∶石屑∶水=110∶1430∶770∶793∶124.7。
水泥稳定碎石无侧限抗压强度影响因素的探究

水泥稳定碎石无侧限抗压强度影响因素的探究摘要:随着交通基础建设投资力度的加大,我国公路通车里程逐年快速增长。
水泥稳定碎石经过拌和、摊铺、压实、养护成型的形式,具有强度高、稳定性好、扩散应力强、抗冻性好、造价低廉等特点,是基层和底基层的主要材料类型之一。
水泥稳定碎石强度满足与否直接影响着工程质量的好坏。
本文首先介绍了水泥稳定碎石的检测内容,并从延时时间、水泥掺量、养护条件三方面,对水泥稳定碎石强度检测结果影响因素展开了探究。
本文旨在为相关应用与研究提供参考。
关键词:水泥稳定碎石强度;影响因素;水泥掺量;养护时间;延时时间前言:因为近些年来路面交通量增大,路面超载现象日趋严重,普通的级配碎石和级配砾石已经很难满足交通负荷的需要,水泥稳定碎石基层底基层整体性强,承载力高、稳定性强且随着时间推移强度不断增强,所以目前在我国的道路建设中得到普遍的应用。
其性能参数是否符合要求,这就需要我们对其性能用正确的试验方法进行检测,提供最真实有效的强度数据给使用方,从而保证工程的质量。
水泥稳定碎石试验配合比设计步骤和内容对水泥进行检测,宜采用强度等级为32.5或42.5的水泥,初凝时间应大于3h,终凝时间大于6h。
对几档碎石进行筛分,得到碎石不同粒径含量,根据碎石含量计算混合含量,混合筛分后确认混合比例。
掺配不同水泥剂量,对混合料进行击实试验,得到最佳含水率和最大干密度。
用最佳含水率、最大干密度、压实度、损耗率对无机结合料进行成型。
成型试件的高度和质量损失满足规范要求。
在标准养护室对试件进行养生。
且质量损失满足规范要求。
进行无侧限抗压强度,标准差、变异系数应满足规范要求。
根据设计要求选择最优的水泥掺量。
水泥稳定碎石配合比设计的影响因素2.1不同水泥掺量对水泥稳定碎石配合比设计强度的影响2.1.1试验步骤如下:在同一批样品中,按照四分法取(0-5)mm、(5-16)mm、(16-31.5)mm三种规格的碎石,将其合成规范要求级配中值进行掺配。
7天无侧限

收、取样日期:2013-10-29
制件日期:
2013-10-29
要求龄期(d): 7试验日期:
2013-11-5
报告日期:结论: 依据《JTJ 034-2000》标准,符合设计要求。
.
1、未经许可不得部分复制本报告
2、本报告无试验报告专用章无效
3、本结果仅指来样而言 .
安徽启程工程质量检测有限责任公司 无机结合料稳定材料无侧限抗压强度试验报告
试验编号:13061029
工程名称:合肥市高新区柏堰湾路(石莲南路~永和路)道排及附属工程 委托单位:广西建工集团第四建筑工程有限责任公司
2013年11月5日
试验室专用章: .
结合料品种: 水泥 厂牌: / 品质等级: / 出厂日期: / .试件收到日期: / 试件数量: 13 混合料用水量: / .稳定材料种类: 5.0%水泥稳定碎石 .
批准: 审核: 报告: .。
无侧限抗压强度试验步骤
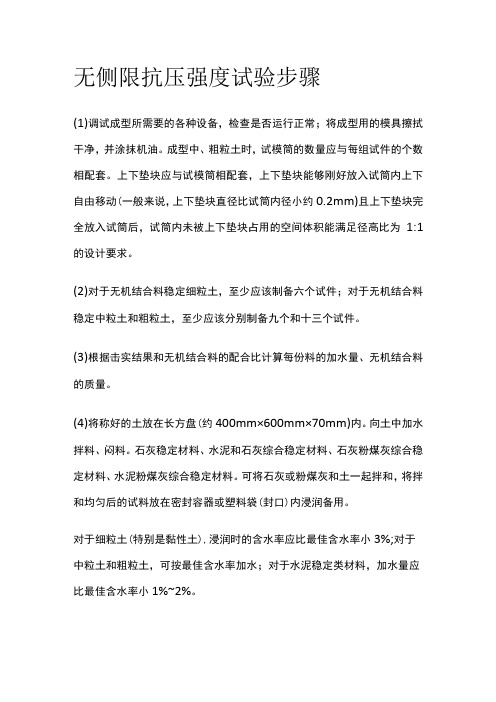
无侧限抗压强度试验步骤(1)调试成型所需要的各种设备,检查是否运行正常;将成型用的模具擦拭干净,并涂抹机油。
成型中、粗粒土时,试模筒的数量应与每组试件的个数相配套。
上下垫块应与试模筒相配套,上下垫块能够刚好放入试筒内上下自由移动(一般来说,上下垫块直径比试筒内径小约0.2mm)且上下垫块完全放入试筒后,试筒内未被上下垫块占用的空间体积能满足径高比为1:1的设计要求。
(2)对于无机结合料稳定细粒土,至少应该制备六个试件;对于无机结合料稳定中粒土和粗粒土,至少应该分别制备九个和十三个试件。
(3)根据击实结果和无机结合料的配合比计算每份料的加水量、无机结合料的质量。
(4)将称好的土放在长方盘(约400mm×600mm×70mm)内。
向土中加水拌料、闷料。
石灰稳定材料、水泥和石灰综合稳定材料、石灰粉煤灰综合稳定材料、水泥粉煤灰综合稳定材料。
可将石灰或粉煤灰和土一起拌和,将拌和均匀后的试料放在密封容器或塑料袋(封口)内浸润备用。
对于细粒土(特别是黏性土),浸润时的含水率应比最佳含水率小3%;对于中粒土和粗粒土,可按最佳含水率加水;对于水泥稳定类材料,加水量应比最佳含水率小1%~2%。
浸润时间要求:黏质土12~24h,粉质土6~8h,砂类土、砂砾土、红土砂砾、级配砂砾等可以缩短到4h左右;含土很少的未筛分碎石、砂砾及砂石可以缩短到2h。
浸润时间一般不超过24h。
(5)在试件成型前Ih内,加入预定数量的水泥并拌和均匀。
在拌和过程中应将预留的水(对于细粒土为3%对于水泥稳定类为1%~2%)加入土中,使混合料达到最佳含水率。
拌和均匀的加有水泥的混合料应在Ih内按下述方法制成试件,超过Ih的混合料应该作废。
其他结合料稳定材料,混合料虽不受此限,但也应尽快制成试件。
(6)用反力架和液压千斤顶,或采用压力试验机之间。
将试模配套的下压块放入试模的下部,但外露2cm左右。
将称量的规定数量的稳定材料混合料分2~3次灌入试模中,每次灌入后用夯棒轻轻均匀插实。
- 1、下载文档前请自行甄别文档内容的完整性,平台不提供额外的编辑、内容补充、找答案等附加服务。
- 2、"仅部分预览"的文档,不可在线预览部分如存在完整性等问题,可反馈申请退款(可完整预览的文档不适用该条件!)。
- 3、如文档侵犯您的权益,请联系客服反馈,我们会尽快为您处理(人工客服工作时间:9:00-18:30)。
水泥稳定土击实实验
一、目的适用范围
目的测定水泥稳定混合料料样最大密度及最优含水率)。
适用范围最大粒径≤37mm。
二、实验仪器及击实筒
天平(称量为2kg,感量为1g)、台秤(称量为10kg,感量为5g)、推土器、喷水设备、碾土设备、拌土设备、修土刀、小量筒、盛土盘、测含水率设备、平直尺及保湿设备等。
(1)轻型击实:锤底直径50mm,击锤质量为2.5kg,落距为300mm,单位体积击实功为598.2kJ/m3(图I-25),分3层击实。
(2)重型击实:锤底直径50mm,击实筒内径为击锤质量为4.5kg,落距为450mm,单位体积击实功为2687和2677.2kJ/m3
击实方法及击实筒规格
粒径25mm颗粒<20%和含黏土多用甲、乙法;碎石土和粒径25mm颗粒>20%用丙法(本次实验选用丙法)。
三、试样制备
1、按高速公路基层标准级配(标准级配已发到每个实验小组)用图解法对A、B、C、D四种矿料(干集料)进行掺配。
2、每个实验小组分别按四分法至少准备5个试样(试样不重复使用),每个样重5.5kg(集料总量5.5kg×5个)。
3、按预估最佳含水率为4%,每个实验小组的5个试样分别加入不同水(以4%为中心按1%含水率级差递增减)。
按预定含水率制备试样方法:每个试样取5.5kg,试样加水量计算方法m w=5.5kg×混合料预达含水率%,例:样1:m w1=5.5kg×2%;样2m w2=5.5kg×3%;
样3m w3=5.5kg×4%;样4m w4=5.5kg×5%;样5m w5=5.5kg×6%。
在调土盘上,每个样分别用喷水设备加预定水量,均匀搅拌后,装入保湿器或塑料袋内,浸润(闷土)备用。
浸润时间:拌匀后闷料碎石土2-4小时备用(高塑性土不少于24h,低塑性土不少于12h)。
四、击实实验
1、击实前加入水泥拌匀(按规范推荐水泥剂量值3%、4%、5%、6%、7%加水泥):水泥用量=水泥剂量×每个试样干集料质量。
(各实验小组加水泥剂量值:一组
3%、二组4%、三组5%、四组6%、五组7%水泥)。
2、将击实筒固定在刚性底面上,装好护筒、垫块,在击实筒内壁涂薄层凡士林油,并在筒底(小试筒)或垫块(大试筒)上放置蜡纸或塑料薄膜。
3、取制备好的试样分层倒入有垫块筒内,分三层击实,每次倒入土为5.5kg /3大约1800g;击实后样等于或略高于筒高(高于筒顶小于6mm);每次加土后整平表面,并稍加压紧,然后按规定的击数(98次)进行第一层土击实,击实时,落锤应铅直自由落下,锤迹必须均匀分布于土面上,每一层击实完成后,将试样表面“拉毛”再上上一层土,并按要求击实各层土。
4、称筒加土的质量:
用修土刀沿套环内壁削挖后,扭动,取下垫块、套环,齐筒顶削平土样,拆除底板,擦净筒外壁,称量,准确至1g。
5、测击实试样含水率(含水率实验):
(1)从击实筒中用推土器推出筒内试样,在样中心处按规定重量取两个含水率试样测含水率(粒径2mm取50g样;粒径5mm取100g样;粒径大于25mm 取500g样),测平行含水率,分别称两试样湿土重(m1)。
(2)烘干湿土称干土重(m s)。
(3)计算含水率(W)
1100s s
m m w m -=⨯ (4)计算至0.1%,平行误差<1%,应符合规定。
6、每实验小组依次将不同含水率的几个试样进行分层击实和测定其他几个试样含水率:按上述2)、3)、4)、
5)步骤进行。
7、其他实验小组按以上步骤进行本组击实和测定试样含水率。
五、实验数据计算整理
1、计算每次击实后试样的湿密度(ρ)
12m m V
ρ-= m 1-湿样+试筒合重;m 2-试筒重;V-试筒体积,V=2177cm 3;ρ-试样湿密度,计算至(0.01g/cm 3
)。
2、计算每次击实后试样的干密度(ρd ) 10.01d w ρ
ρ=+
w-试样含水率,不带%号;ρ-试样湿密度;ρd -干密度,计算至(0.01g/cm3)。
3、绘W-ρd 关系曲线图。
4、确定最大干密度(ρdmax)和最优含水率W op
以干密度ρd为纵坐标,以含水率W为横坐标,绘制击实曲线。
曲线上峰值点所对应的数值即分别为该土的最大干密度(ρdmax)和最优含水率W op(图I-26)。
如曲线不能给出峰值点,应进行补点试验。
最优含水率W op≥12%,取整数;6%<W op <12%,取一位小数,取0或0.5,精确到0.5%;W op≤6%时取一位小数,用偶数表示,精确到0.2%。
5、最优含水率校正:超大颗粒(粒径大于38mm)含量大于>5%要校正,小于5%不校正。
水泥稳定碎石土7天无侧限抗压强度制件
1、按现场压实度规定(高速公路基层规定压实度
K=98%)计算干密度;
制件干密度=最大干密度×98%(K=98%)
2、每个试验小组按本组最佳含水率、最大干密度和本组的水泥剂量制一个试件的实际混合料总数量(m)。
()()2
max 0max 015.1.1514d d m V w K w K πρρ⨯=+=⨯⨯⨯+⨯
ρd -最大干密度;w 0-最佳含水率;K-工地压实度(K=98%)。
3、配制某一水泥剂量试件各种材料总毛用量,一般干集料要5700-7000g (稳定细粒土6500g 、稳定碎石7000g ),试样体积V=2651cm 3。
4、制一个样各种材料用量:
(1)当集料不含水时
水泥=7000×水泥剂量/(100+水泥剂量)
集料=7000×100/(100+水泥剂量)
水=7000×w 0(本组最佳含水率)
(2)若集料中含a%水
水泥=7000×水泥剂量/(100+水泥剂量)
集料=7000×100/(100+水泥剂量)×(1+ a%) 水=7000×(w 0-100/(100+水泥剂量)×a%)
5、集料中各种粒径粒料称料(M=x+y+z+…)加水闷料2-4小时。
制样前再加水泥,制9个7天无侧限抗压
强度试件(制件数量为6、9、13)。
6、试模装料前在内涂机油,装料后压块上下各留1cm ,将装好料试模置于压力机上,开动压力机将上下压块压人试模并与试模齐平。
7、脱模(6-8小时后),对试样标准条件(南方养生温度25±2℃,北方温度20±2℃)养生6 d ,浸水1d 。
量测试件浸水前后高度和重量(直径×高:50mm ×50mm 试件重量差<1g ;100mm ×100mm 试件重量差<4g ;150mm ×150mm 试件重量差<10g )。
8、无侧限抗压强度试验及计算(R=P/A (Mpa)) 试件为直径×高:
50mm ×50mm 试件:R=0.00051P
100mm ×100mm 试件: R=0.000127P
150mm ×150mm 试件: R=0.000057P
式中:P-破坏荷载,单位N ;A-受力面积,单位mm 2;R-无侧限抗压强度,单位Mpa 。
9、试验计算 (1)计算强度平均值: (2)计算标准差: (3)计算偏差系数:
10、选用水泥剂量 0
100
Cv R
=⨯0σ=123........n R R R R R n
++++=
此剂量试件的的室内试验结果平均抗压强度应符合下式的要求:
:平均抗压强度;
Rd-设计抗压强度,取Rd=3.5 Mpa ;Za-保证率系数,保证率P 为95% ,则Za=1.645;Cv-试验结果的偏差系数;σ0-标准差。
11、确定实验室稳定土配合比:
强度满足上式要求的最小水泥剂量(水泥经济剂量)为配合比用水泥用量,此水泥用量实验小组击实试验获得的最大干密度(ρdmax )和最优含水率Wop 为稳定土配合比干密度、
含水率。
12、稳定材料施工配合比
满足以上条件时的最佳用水量和水泥剂量为设计合格的配合比。
工地实际采用的水泥剂量应比室内确定的剂量多0.5%-1.0%。
1d R R ZaCv ≥-R。