精益管理改善的十大原则!
精益改善十大原则精益生产专家们的十大改善工具
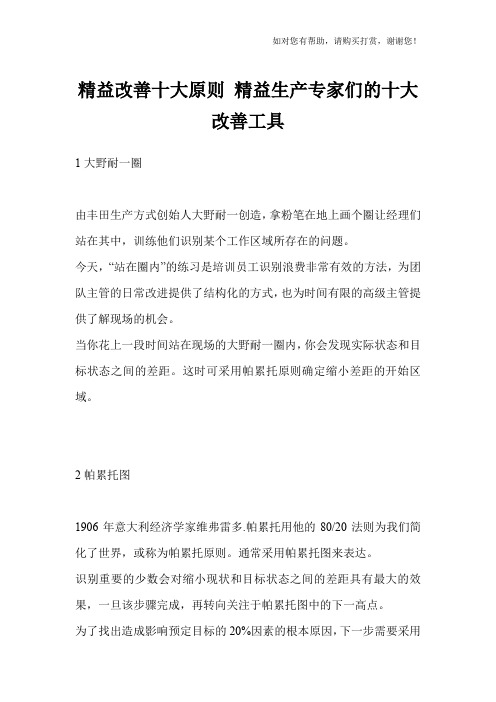
精益改善十大原则精益生产专家们的十大改善工具1大野耐一圈由丰田生产方式创始人大野耐一创造,拿粉笔在地上画个圈让经理们站在其中,训练他们识别某个工作区域所存在的问题。
今天,“站在圈内”的练习是培训员工识别浪费非常有效的方法,为团队主管的日常改进提供了结构化的方式,也为时间有限的高级主管提供了解现场的机会。
当你花上一段时间站在现场的大野耐一圈内,你会发现实际状态和目标状态之间的差距。
这时可采用帕累托原则确定缩小差距的开始区域。
2帕累托图1906年意大利经济学家维弗雷多.帕累托用他的80/20法则为我们简化了世界,或称为帕累托原则。
通常采用帕累托图来表达。
识别重要的少数会对缩小现状和目标状态之间的差距具有最大的效果,一旦该步骤完成,再转向关注于帕累托图中的下一高点。
为了找出造成影响预定目标的20%因素的根本原因,下一步需要采用石川图深挖其中的根本原因。
3石川图石川图(又称鱼骨图或因果图)用以识别造成特定事件或情况的原因。
这是一种相当灵活的工具。
即可以采用4M(人,材料,设备,方法)或6M(加上环境和测量方法)为制造或生产型流程的进行根原因分析,又可用4P(价格,促销,地点,产品)进行市场和销售的改善。
到目前为止,你已经识别出问题的根原因,下一步准备实施相应的措施。
所以你需要一个行动计划。
4甘特图亨利.甘特在1910期间创造了闻名于世的项目管理工具甘特图。
任何使用微软项目管理软件或使用这个经典项目管理工具的人都需要感谢甘特先生。
随着甘特图在全球范围传播,带来管理大型,复杂项目的革命。
甘特先生算是早期具有精益思维的专家,他为后来的发展奠定了基础,例如标准作业合并表,安排每日工作和作业平衡。
行动计划不能仅局限于“计划和实施”,也要注重“检查和纠正”。
这是根据PDCA环原则,通称戴明环。
5戴明环戴明环又称为PDCA环。
爱德华.戴明以其在日本教授和传播PDCA 的质量改进方式而闻名。
更准确的说,应归功于Walter Shewhart,他是统计学的先驱者同时也是戴明的老师, PDCA即源自于他的构想。
生产精益管理原则及技巧

生产精益管理的原则与技巧建立稳定的流程,运用不断改进的工具以找出导致缺乏效率的根本原因,并采取有效的对策,把最佳实务标准化,以促进学习,而不是在每个新计划及每位新经理人上台后,又重新发明新方法。
一、生产精益管理的原则1、建立无间断流程以使问题浮现。
要求重新设计流程,使流程不仅仅是工作过程的描述。
一定要建立快速输送材料与信息的流程,使流程与员工的行为动作紧密地联结在一起。
要使整个企业文化重视流程,这是促成真正的持续改进流程及员工发展的关键。
2、实施拉式生产制度以避免生产过剩在你生产流程下游的客户有需求的时候,供应给他们正确数量的正确东西。
使在制品及库存减至最少,每项产品只维持少量存货,根据向客户实际交付的数量,经常补充存货。
按客户的需求每天进行调整在制品和存货量,而不是依靠计算机的时间表与系统来追踪已经成为浪费的存货。
3、建立立即暂停以解决问题,从一开始就重视品质管理的文化为顾客提供的品质决定着你的定价。
你要想收益高,首先需要品质好。
为了提高品质,应该使用所有能够确保产品品质的现代方法。
想一想,我们的方法是不是能够确保产品品质?使生产设备具有发现问题及一发现问题就停止生产的能力。
在企业中设立支持快速解决问题的制度和监督检测。
在企业文化中融入发生问题时立即暂停或减缓速度、就地改进质量以提升长期生产力的概念。
4、工作的标准化是持续改进与授权员工的基础在工作场所中的任何地方都使用稳定、可重复的方法,以维持流程的可预测性、规律的运作时间,以及规律的产出。
到一定时间时,应该汲取对流程的累积学习心得,把“现在”的最佳实务进行标准化,让员工对于标准提出有创意的改进意见,把这些见解纳入新标准中。
5、使工作负荷水准稳定(生产均衡化),工作应象龟兔赛跑中的乌龟一样杜绝浪费只是实现精益所必须做的工作的1/3。
避免员工与设备的负荷过重,以避免生产安排的不均匀,也同等重要。
尽量使所有制造与服务流程的工作负荷平均化,以取代大多数公司实行的批量生产方法中经常启动、停止、启动的做法。
精益生产10个原则
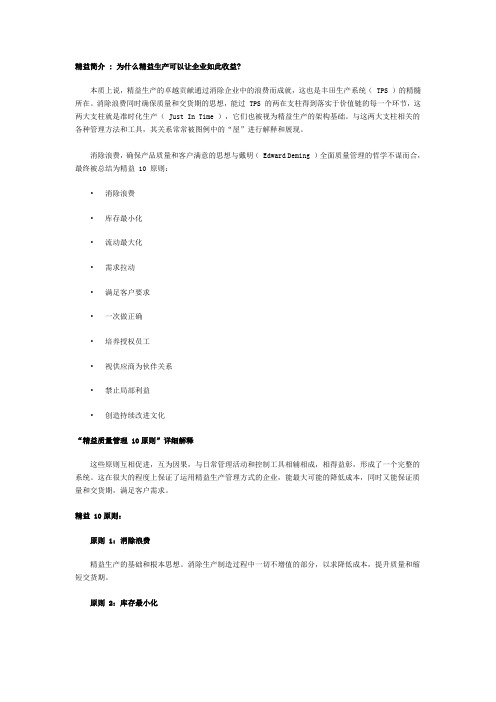
精益简介 : 为什么精益生产可以让企业如此收益?本质上说,精益生产的卓越贡献通过消除企业中的浪费而成就,这也是丰田生产系统( TPS )的精髓所在。
消除浪费同时确保质量和交货期的思想,能过 TPS 的两在支柱得到落实于价值链的每一个环节,这两大支柱就是准时化生产( Just In Time ),它们也被视为精益生产的架构基础。
与这两大支柱相关的各种管理方法和工具,其关系常常被图例中的“屋”进行解释和展现。
消除浪费,确保产品质量和客户满意的思想与戴明( Edward Deming )全面质量管理的哲学不谋而合,最终被总结为精益 10 原则:•消除浪费•库存最小化•流动最大化•需求拉动•满足客户要求•一次做正确•培养授权员工•视供应商为伙伴关系•禁止局部利益•创造持续改进文化“精益质量管理 10原则”详细解释这些原则互相促进,互为因果,与日常管理活动和控制工具相辅相成,相得益彰,形成了一个完整的系统。
这在很大的程度上保证了运用精益生产管理方式的企业,能最大可能的降低成本,同时又能保证质量和交货期,满足客户需求。
精益 10原则:原则 1:消除浪费精益生产的基础和根本思想。
消除生产制造过程中一切不增值的部分,以求降低成本,提升质量和缩短交货期。
原则 2:库存最小化库存是 7 大浪费之一。
库存占用资金和场地,并掩盖了企业经营管理中的大量问题,精益生通过不断降低库存,暴露问题,解决问题后再降低库存的循环不断降低库存量。
原则 3:流动最大化让物流和加工过程快速流动起来,以最短的生产周期应对市场变化。
原则 4:需求拉动不再依靠预测来生产,而根据客户的需求来生产,尽可能最迟将客户的需求导入生产环节以提升准确性。
当客户需求的时候才生产。
原则 5:满足客户要求了解客户的正真需求,满足顾客在质量、交货、服务、价格等方面的需求。
原则 6:一次做正确生产的每个环节确保提供的都是合格品,每一步骤都作工确,而不是最后校正。
在制造过程中坚持“不制造、不传递、不接受”不合格品的“三不”原则。
精益十项原则
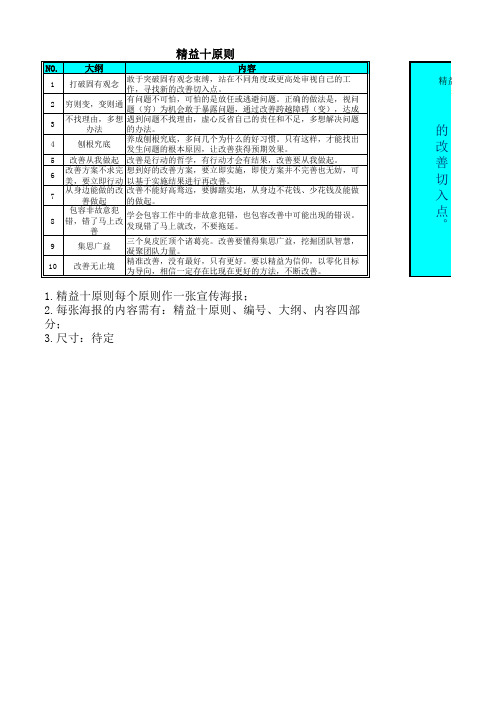
的 改 善 切 入 点 。
己 的 工 作 , 寻 找 新
1.精益十原则每个原则作一张宣传海报; 2.每张海报的内容需有:精益十原则、编号、大纲、内容四部 分; 3.尺寸:待定
精益十原则(一) 打破固有观念
内容要 求
的 改 善 切 入 点 。
己度束敢 的或缚于 工更,突 作高站破 ,处在固 寻审不有 找视同观 新自角念
精益十原则
NO.
1 2 3 4 5
大纲打破固有观念 Fra bibliotek则变,变则通 不找理由,多想 办法 刨根究底
内容
敢于突破固有观念束缚,站在不同角度或更高处审视自己的工 作,寻找新的改善切入点。 有问题不可怕,可怕的是放任或逃避问题。正确的做法是,视问 题(穷)为机会敢于暴露问题,通过改善跨越障碍(变),达成 遇到问题不找理由,虚心反省自己的责任和不足,多想解决问题 的办法。 养成刨根究底,多问几个为什么的好习惯。只有这样,才能找出 发生问题的根本原因,让改善获得预期效果。 改善是行动的哲学,有行动才会有结果,改善要从我做起。 想到好的改善方案,要立即实施,即使方案并不完善也无妨,可 以基于实施结果进行再改善。 改善不能好高骛远,要脚踏实地,从身边不花钱、少花钱及能做 的做起。
精益十原则 打破固有观
改善从我做起 改善方案不求完 6 美,要立即行动 从身边能做的改 7 善做起 包容非故意犯 学会包容工作中的非故意犯错,也包容改善中可能出现的错误。 8 错,错了马上改 发现错了马上就改,不要拖延。 善 三个臭皮匠顶个诸葛亮。改善要懂得集思广益,挖掘团队智慧, 9 集思广益 凝聚团队力量。 精准改善,没有最好,只有更好。要以精益为信仰,以零化目标 10 改善无止境 为导向,相信一定存在比现在更好的方法,不断改善。
精益管理改善方案

精益管理改善方案随着市场的竞争越来越激烈,企业的生产效率和产品品质成为各行各业的关注点。
精益管理作为一种改进生产流程和管理方式的方法,成为企业实现高效生产和优化管理的有效手段。
本文将从精益管理的基本原则、实施步骤和案例应用等方面进行论述,探讨精益管理改善方案。
一、精益管理的基本原则精益管理最初源于日本汽车工业,在不断的实践中形成了一系列基本原则,其中最重要的有以下几点:1、价值流观点。
使用价值流图来分析整个生产过程,找到非价值增加的环节,尽可能消除浪费。
2、一次加工能力。
通过有效的生产布局和加工工艺优化,实现一次性加工符合顾客要求的产品。
3、流动式生产方式。
采用流水线的生产方式,实现工序无停顿的连续运作。
4、拉式生产方式。
基于顾客需求进行生产,避免过度生产和库存积压。
5、质量控制。
从源头上就控制产生不良品的环节,保证产品质量。
二、精益管理的实施步骤精益管理的实施需要系统性的方法和长期的思考,以下是具体的步骤:1、组建工作团队。
选择合适的人员参与精益管理改进,提高整个团队的意识和素质。
2、制定改进计划。
将改进目标设置在价值流程上,明确改进的目的和方向。
3、识别流程中的浪费。
通过价值流图体现出整个流程中的各种浪费,包括时间浪费、物料浪费、人员浪费等等。
4、寻找改善机会。
分析流程中的各个环节,找到浪费的原因和改善的机会。
5、确定改进方案。
根据寻找到的改善机会,制定相应的改进方案,采取合适的工具和技术进行改善。
6、测试改进效果。
在改变生产流程之前进行试验,进一步完善改进方案。
7、推广改进成果。
有效宣传并推广改进成果,形成学习和借鉴的机制。
三、案例应用以某制造业企业为例,其采用精益管理方法优化了生产流程和管理方式,显著提升了效率和品质:1、价值流程分析。
通过价值流图分析整个生产流程,找到物料浪费、人员浪费、生产停滞等问题。
2、改进方案制定。
采用排程软件优化生产计划,提高工作效率。
同时,修正文档流程,减少重复劳动和人为错误。
精益思维“十大”原则
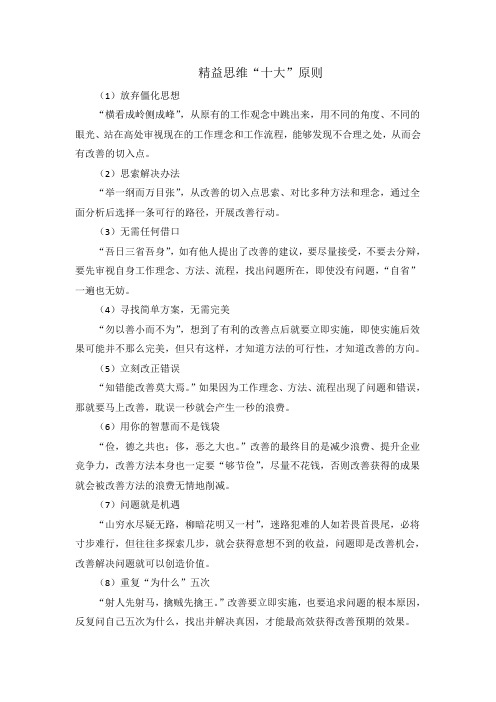
精益思维“十大”原则(1)放弃僵化思想“横看成岭侧成峰”,从原有的工作观念中跳出来,用不同的角度、不同的眼光、站在高处审视现在的工作理念和工作流程,能够发现不合理之处,从而会有改善的切入点。
(2)思索解决办法“举一纲而万目张”,从改善的切入点思索、对比多种方法和理念,通过全面分析后选择一条可行的路径,开展改善行动。
(3)无需任何借口“吾日三省吾身”,如有他人提出了改善的建议,要尽量接受,不要去分辩,要先审视自身工作理念、方法、流程,找出问题所在,即使没有问题,“自省”一遍也无妨。
(4)寻找简单方案,无需完美“勿以善小而不为”,想到了有利的改善点后就要立即实施,即使实施后效果可能并不那么完美,但只有这样,才知道方法的可行性,才知道改善的方向。
(5)立刻改正错误“知错能改善莫大焉。
”如果因为工作理念、方法、流程出现了问题和错误,那就要马上改善,耽误一秒就会产生一秒的浪费。
(6)用你的智慧而不是钱袋“俭,德之共也;侈,恶之大也。
”改善的最终目的是减少浪费、提升企业竞争力,改善方法本身也一定要“够节俭”,尽量不花钱,否则改善获得的成果就会被改善方法的浪费无情地削减。
(7)问题就是机遇“山穷水尽疑无路,柳暗花明又一村”,迷路犯难的人如若畏首畏尾,必将寸步难行,但往往多探索几步,就会获得意想不到的收益,问题即是改善机会,改善解决问题就可以创造价值。
(8)重复“为什么”五次“射人先射马,擒贼先擒王。
”改善要立即实施,也要追求问题的根本原因,反复问自己五次为什么,找出并解决真因,才能最高效获得改善预期的效果。
(9)让每个员工寻找答案“三个臭皮匠,顶个诸葛亮。
”改善周是团体活动,改善点的发现、改善方法的发掘与实施,都需要多人配合,也包括领导与员工的配合。
(10)改进无止境“没有最好,只有更好”。
工作的改善亦是无限的,只有持续不断地“打破固有观念”,“寻找可行的方法”,一直改善实施下去,才能最终满足客户不断上升的需求。
改善与自主改善.

杭州信多达电机事业部
自主改善与合理化建议
1 2 3 4 5 6 7
合理化建议 提出建议 宏观措施 积极倡导 流程较长 奖励可观 难度较大 倡导开展
自主改善 自主实施 日常工作 数量指标 流程较短 积少成多 难度不定 全员参与
杭州信多达电机事业部
活动意义
杭州信多达电机事业部
改善内容
杭州信多达电机事业部
小改善 小改善 小改善 小改善 小改善
小改善的 积累
大的效果
杭州信多达电机事业部
改善的着眼点-3
从“4M”的角度
人 勉 强 勉强姿势 勉强的能力知识 人数 >工作量 等待的时间多 能力 >工作难度 有的忙,有的闲 两人作业时,一 人操作一人等待 物 品质、性能等 交货期的勉强 扔掉可用的东西 油、水、气的泄 漏 同一产品品质、 形状、材质同 交货期不一致
杭州信多达电机事业部
定义
改善
为了更好而改变; 在企业经营理念中,用以持续不断地改进工作方法和人员的效 率等; 精益生产方式的基础是改善活动。
自主改善:
是指员工自己通过手段与方法的变更,使工作或结果变得更 好,从而获得制度化的嘉奖,并使改善后的工作标准化的过程。
杭州信多达电机事业部
定义
杭州信多达电机事业部
还有很多很多
。。。。。。
杭州信多达电机事业部
精益提案
等待你的参与!
杭州信多达电机事业部
为什么 我们要大力推广 自主改善活动? 因为。。。。。。
杭州信多达电机事业部
杭州信多达电机事业部
杭州信多达电机事业部
杭州信多达电机事业部
杭州信多达电机事业部
杭州信多达电机事业部
杭州信多达电机事业部
精益改善十大原则解析
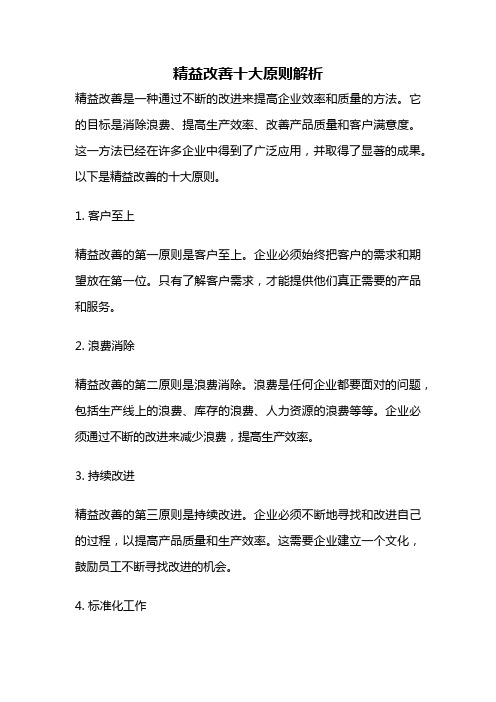
精益改善十大原则解析精益改善是一种通过不断的改进来提高企业效率和质量的方法。
它的目标是消除浪费、提高生产效率、改善产品质量和客户满意度。
这一方法已经在许多企业中得到了广泛应用,并取得了显著的成果。
以下是精益改善的十大原则。
1. 客户至上精益改善的第一原则是客户至上。
企业必须始终把客户的需求和期望放在第一位。
只有了解客户需求,才能提供他们真正需要的产品和服务。
2. 浪费消除精益改善的第二原则是浪费消除。
浪费是任何企业都要面对的问题,包括生产线上的浪费、库存的浪费、人力资源的浪费等等。
企业必须通过不断的改进来减少浪费,提高生产效率。
3. 持续改进精益改善的第三原则是持续改进。
企业必须不断地寻找和改进自己的过程,以提高产品质量和生产效率。
这需要企业建立一个文化,鼓励员工不断寻找改进的机会。
4. 标准化工作精益改善的第四原则是标准化工作。
标准化工作是为了减少差异性,提高生产效率和产品质量。
企业必须确保每个员工都能够按照标准程序完成工作。
5. 建立流程精益改善的第五原则是建立流程。
企业必须建立一个清晰的流程,确保从供应链到生产线,从物流到销售,每个环节都是协调一致的。
6. 建立团队精益改善的第六原则是建立团队。
企业必须建立一个团队文化,鼓励员工之间的合作和协作。
只有团队配合默契,才能实现精益改善的目标。
7. 建立信任精益改善的第七原则是建立信任。
企业必须建立信任的关系,包括员工之间的信任、企业与客户之间的信任。
只有建立信任的关系,才能实现持续改进。
8. 管理风险精益改善的第八原则是管理风险。
企业必须识别和管理风险,以确保生产线的稳定和产品质量的可靠性。
只有管理好风险,才能确保企业的可持续发展。
9. 培训员工精益改善的第九原则是培训员工。
企业必须为员工提供培训和学习机会,以提高他们的技能和知识水平。
只有具备足够的技能和知识,才能实现精益改善的目标。
10. 持续改进精益改善的第十原则是持续改进。
企业必须始终保持改进的状态,不断寻找和解决问题,以提高生产效率和产品质量。
- 1、下载文档前请自行甄别文档内容的完整性,平台不提供额外的编辑、内容补充、找答案等附加服务。
- 2、"仅部分预览"的文档,不可在线预览部分如存在完整性等问题,可反馈申请退款(可完整预览的文档不适用该条件!)。
- 3、如文档侵犯您的权益,请联系客服反馈,我们会尽快为您处理(人工客服工作时间:9:00-18:30)。
精益管理改善的十大原则!
1打破固有观念
以前正确的,现在未必正确;现在正确的,未来未必正确。
所谓“当局者迷,旁观者清”,从原有的工作观念中跳出来,用旁观者的眼光、站在高处审视自己的工作理念和工作流程,也许就会发现不合理之处,也就有了改善的切入点。
2寻找可行的方法
有了改善的切入点后,接下来就是如何开展改善活动。
在自己面前也许有多种方法和理念,但是通过全面分析以后要选择一条可行的路径,开展改善。
3不要分辨,要否定现状
“吾日三省吾身”,没有人提建议,也要每日自省。
如果有他人给自己提出了改善的建议,更要尽量接受,不要去分辨,要先审视自身工作理念、方法、流程,找出问题所在,即使没有问题,对自己做一次全面检查也无害。
4不要力求完美,50分也好,立即实施
想到了对自身工作有利的改善点后就要立即实施,哪怕实施后效果并不那么完美,但是只有实施了,才知道方法是否可行,才知道向何方改善。
5错了马上改善
如果确实是自身工作理念、方法、流程出现了问题和错误,那就要马上改善,耽误一秒钟就要产生一秒钟的浪费。
6先从不花钱的改善做起
改善的最终目的是减少浪费、提升企业竞争力,毋庸置疑,改善方法本身也一定要“够节俭”,尽量不花钱,否则改善获得的成果就会被改善方法的浪费无情地削减。
7穷则变,变则通
“山穷水尽疑无路,柳暗花明又一村”,当我们面前只有两条路:死亡或者改变,无疑,聪明的人会毫无迟疑地选择改变,因为改变了才有生存下去的希望和可能。
当我们在谷底时,无论往哪一个方向走,只要走,我们的高度都比谷底要高,只要改变了,往往就会获得意想不到的收益。
8追求根源,反复五次为什么
改善要立即实施,也要追求问题的根本原因,正所谓“有的放矢”,排除假因获得真因,才能够以最高的效率获得改善预期的效果。
那如何获得真因呢?答案就是反复问自己五次为什么,每问一次,就向真因靠近一点。
9十个人的智慧比一个人的智慧高明
“三个臭皮匠,顶个诸葛亮。
”改善是一个团体活动,改善点的发现、改善方法的发掘与实施,都需要多人配合,也包括领导与员工的配合。
10改善是无限的
有一句著名的广告语道“没有最好,只有更好”。
在生产过程中,我们需要随时关注顾客,满足甚至超越顾客的需求,而顾客的需求是在不断增长的,因此,对自身工作的改善也是无限的,我们需要持续不断地“打破固有观念”,“寻找可行的方法”,改善下去。