高锰钢铸件验收标准
铸件质量检验标准

铸件质量检验标准铸件是一种常见的生产工艺,广泛用于各个行业和领域。
铸件质量的好坏直接影响产品的性能和可靠性,因此进行铸件质量检验至关重要。
本文将介绍铸件质量检验的标准和方法。
一、铸件质量检验的重要性铸件质量检验的目的是确保铸件的尺寸精度、表面质量和机械性能达到设计要求。
一方面,铸件的尺寸精度和表面质量直接影响产品的装配和使用;另一方面,对于承受重载或高温等极端工况的铸件来说,其机械性能的好坏关系到产品的安全可靠性。
二、铸件质量检验的标准铸件质量检验的标准包括国家标准、行业标准和企业自身标准。
国家标准是根据相关法律法规制定的,具有强制性,是衡量铸件质量的重要依据。
行业标准是在国家标准的基础上,由行业协会或行业组织制定的,作为行业内铸件质量的参考指南。
企业自身标准是企业根据生产情况和需求制定的,用于规范和管理内部质量控制。
在铸件质量检验中,常用的国家标准有《铸造铁件技术条件》、《铸铝合金件技术条件》等,而行业标准包括《汽车铝合金压铸铸件技术规范》、《船用铸铁件技术条件》等。
企业自身标准则根据企业具体的生产工艺和要求制定,例如《XX公司铸件质量检验标准》。
三、铸件质量检验的方法铸件质量检验的方法主要包括外观检查、尺寸检测和性能测试。
1. 外观检查外观检查是铸件质量检验中最简单直观的方法。
通过肉眼观察铸件的外观,检查是否有裂纹、砂眼、气孔、夹渣等缺陷。
外观检查可以用目视检查或借助放大镜进行观察。
2. 尺寸检测尺寸检测是铸件质量检验中最常见的方法。
主要是测量铸件的外形尺寸、孔径尺寸和壁厚尺寸等。
常用的尺寸测量工具有游标卡尺、内径卡尺、外径卡尺、深度尺等。
尺寸检测可以帮助判断铸件是否满足设计要求。
3. 性能测试性能测试是铸件质量检验中最关键的方法,主要包括力学性能测试、化学成分分析和金相组织分析。
力学性能测试主要是测试铸件的拉伸、弯曲、冲击等力学性能。
化学成分分析可以确定铸件的材料成分是否符合要求。
金相组织分析可以观察铸件的金相组织结构,评估其机械性能。
铸件表面质量提升验收技术条件

铸件表面质量提升验收技术条件1 范围本文件规定了铸件分类、目测铸件技术要求、检验规则.本标准适用于中国一拖集团有限公司内/外供方采用砂型铸造,金属型铸造方法获得的黑色、有色合金铸件产品。
2 规范性引用文件下列文件对于本文件的应用是必不可少的.凡是注日期的引用文件,仅所注日期的版本适用于本文件。
凡是不注日期的引用文件,其最新版本(包括所有的修改单)适用于本文件.GB/T 6060。
1—1997 表面粗糙度比较样块铸造表面GB/T 15056-1994 铸造表面粗糙度评定方法Q/YT 014.2—2009 图样通用技术要求Q/YT 022。
4—2011 砂型机器造型铸件尺寸公差Q/YT 022。
10—2011 铸铁件机械加工余量Q/YT 303。
1-2011 球墨铸铁件验收技术条件Q/YT 303.2—2011 灰铸铁件验收技术条件Q/YT 303.3—2011 铸造碳钢件验收技术条件Q/YT 303.5-2011 铝合金铸件验收技术条件Q/YT 303。
6-2011 高锰钢履带板验收技术条件Q/YT 303。
7-2011 铜合金铸件验收技术条件Q/YT 303.9-2011 硅锰钢履带板验收技术条件3 铸件分类铸件根据其所处安装位置、工作条件及表面是否加工分三类,其定义和检验项目见表1。
表1 铸件分类4 目测铸件技术要求4.1 一般要求4.1.1 砂型铸造全部外露件和部分外露件表面粗糙度要求Ra25~Ra50。
金属铸造和有色件表面粗糙度要求Ra25,待加工表面允许降低一级。
4.1.2 铸件表面不得有影响零件强度、密封性能及严重影响外观的缺陷。
4.1.3 铸件采购、质量检查和供方可在保证铸件满足铸件验收技术条件的前提下,鼓励三方协商建立铸件外观质量标杆样件(即合格的最低标准实物)库,便于铸件外观质量验收参照标杆样件执行,低于此实物标准时为不合格。
4.2 灰铸铁件及碳钢铸件4.2.1 表面缺陷4.2.1.1 铸件表面不允许有冷隔、裂纹、孔洞贯穿内外表面的缺陷及机械加工不能去除的其它缺陷.4.2.1.2 铸件上的型砂、芯砂、披缝必须清理干净;其中,披缝非加工面不大于 2 mm,加工面不大于 3 mm;4.2.1.3 灰铸铁件表面允许存在的孔洞类缺陷见表 2;表 2 砂型铸造灰铸铁件表面允许存在的孔洞类缺陷4.2.1.4 碳钢铸件表面允许存在的孔洞类缺陷见表 3表 3 碳钢铸件表面允许存在的孔洞类缺陷4.2.1.5 铸件内、外表面应清理干净,不应有浮砂、粘砂、氧化皮。
高锰钢检测项目和标准
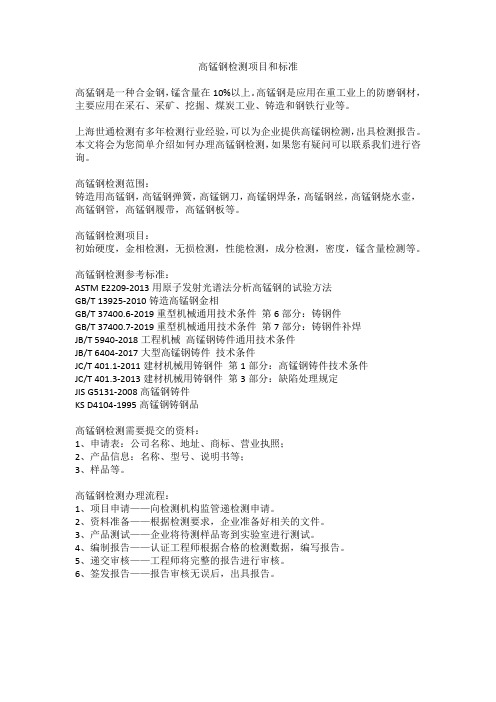
高锰钢检测项目和标准高猛钢是一种合金钢,锰含量在10%以上。
高锰钢是应用在重工业上的防磨钢材,主要应用在采石、采矿、挖掘、煤炭工业、铸造和钢铁行业等。
上海世通检测有多年检测行业经验,可以为企业提供高锰钢检测,出具检测报告。
本文将会为您简单介绍如何办理高锰钢检测,如果您有疑问可以联系我们进行咨询。
高锰钢检测范围:铸造用高锰钢,高锰钢弹簧,高锰钢刀,高锰钢焊条,高锰钢丝,高锰钢烧水壶,高锰钢管,高锰钢履带,高锰钢板等。
高锰钢检测项目:初始硬度,金相检测,无损检测,性能检测,成分检测,密度,锰含量检测等。
高锰钢检测参考标准:ASTM E2209-2013用原子发射光谱法分析高锰钢的试验方法GB/T 13925-2010铸造高锰钢金相GB/T 37400.6-2019重型机械通用技术条件第6部分:铸钢件GB/T 37400.7-2019重型机械通用技术条件第7部分:铸钢件补焊JB/T 5940-2018工程机械高锰钢铸件通用技术条件JB/T 6404-2017大型高锰钢铸件技术条件JC/T 401.1-2011建材机械用铸钢件第1部分:高锰钢铸件技术条件JC/T 401.3-2013建材机械用铸钢件第3部分:缺陷处理规定JIS G5131-2008高锰钢铸件KS D4104-1995高锰钢铸钢品高锰钢检测需要提交的资料:1、申请表:公司名称、地址、商标、营业执照;2、产品信息:名称、型号、说明书等;3、样品等。
高锰钢检测办理流程:1、项目申请——向检测机构监管递检测申请。
2、资料准备——根据检测要求,企业准备好相关的文件。
3、产品测试——企业将待测样品寄到实验室进行测试。
4、编制报告——认证工程师根据合格的检测数据,编写报告。
5、递交审核——工程师将完整的报告进行审核。
6、签发报告——报告审核无误后,出具报告。
建材机械用高锰钢铸件技术条件

建材机械用高锰钢铸件技术条件1主题内容与适用范围1.1本标准规定了高锰钢铸件的材料牌号、技术要求和检验规则等。
1.2本标准适用于建材机械中的高锰钢铸件。
2引用标准GB223钢铁及合金化学分析方法GB228金属拉力试验法GB231金属布氏硬度试验方法GB2106金属夏比(V型缺口)冲击试验方法YB3210高锰钢铸件技术条件JC40l.3建材机械用铸钢件缺陷处理规定Jc10l.4建材机械用铸钢件交货技术条件3材料牌号高锰钢铸件的材料牌号见表1表1材料牌号用途ZGMn13-A强烈冲击高负荷磨损铸件ZGMn13-B一般冲击磨损铸件ZGMn13Cr2高屈服耐磨铸件4技术要求4.1化学成份高锰钢的化学成份应符合表2的规定。
表2材料牌号元素含量% C Mn Si P S Cr ZGMn13-A 1.10-1.30 11.00-13.00 0.40-0.70≤0.07≤0.04 - ZGMn13-B 1.00-1.40 11.00-14.00 0.30-0.80≤0.09≤0.05 - ZGMn13cr20.90-1.30 11.00-14.00 0.30-0.80≤0.08≤0.04 1.50-2.50 4.2机械性能高锰钢铸件必须进行水韧处理,处理后试样的机械性能应符合表3的规定。
表3材料牌号机械性能最小值屈服强度抗拉强度延伸率冲击吸收功硬度σsσbδ5Akv HB N/mm[2] N/mm[2] % J ZGMn13-A - 680 25 92≤229 ZGMn13-B - 640 20 -≤229 ZGMn13Cr2380 710 20 -≤2434. 3金相组织4.3.1高锰钢铸件水韧处理后试样的金相组织应为奥氏体,允许晶粒内残存少量分散的碳化物,晶界存在断续网状碳化物。
4.3.2 ZGMn13-A、ZGMn13-B的金相组织应符合下列规定:a.碳化物不超过YB 3210第一评级图的3级、3A级或3B级;b.非金属夹杂物总和(氧化物+硫化物)不超过YB 3210第二评级图的3A级或4A级。
astm a128标准

astm a128标准ASTM A128标准。
ASTM A128标准是一种用于高锰钢铸件的标准规范,它适用于制造各种类型的高锰钢铸件,包括碎石机的衬板、颚式破碎机的颚板、锤式破碎机的锤头等。
这些铸件通常需要具备耐磨、耐冲击和耐磨损的特性,以满足在采矿、建筑和其他工业领域中的使用要求。
ASTM A128标准对高锰钢铸件的化学成分、机械性能、金相组织、硬度和冲击性能等方面进行了详细的规定。
其中,化学成分是保证高锰钢铸件具有良好的耐磨性和抗冲击性的重要因素之一。
根据标准规定,高锰钢铸件的主要化学成分包括碳(C)、锰(Mn)、硅(Si)、磷(P)、硫(S)和铬(Cr),其中锰的含量通常在11%至14%之间。
此外,标准还要求对铸件的金相组织和晶粒度进行检验,以确保其具有良好的耐磨性和抗冲击性。
在机械性能方面,ASTM A128标准要求对高锰钢铸件进行拉伸试验、硬度测试和冲击试验。
通过这些试验,可以评估铸件的抗拉强度、屈服强度、延伸率、硬度和冲击韧性等性能指标,以确保其在使用过程中能够承受较大的冲击和磨损。
除了化学成分和机械性能外,ASTM A128标准还对高锰钢铸件的热处理工艺和表面质量提出了要求。
热处理工艺可以改善铸件的组织结构和性能,提高其耐磨性和抗冲击性。
而对表面质量的要求则包括表面粗糙度、缺陷和氧化层等方面,以确保铸件在使用过程中能够保持良好的表面状态。
总的来说,ASTM A128标准对高锰钢铸件的各项性能和质量都进行了严格的规定和检验,以确保其能够满足在采矿、建筑和其他工业领域中的使用要求。
通过遵循这一标准,可以生产出具有良好耐磨性和抗冲击性能的高锰钢铸件,为相关行业的发展和应用提供可靠的保障。
铸件表面质量验收标准
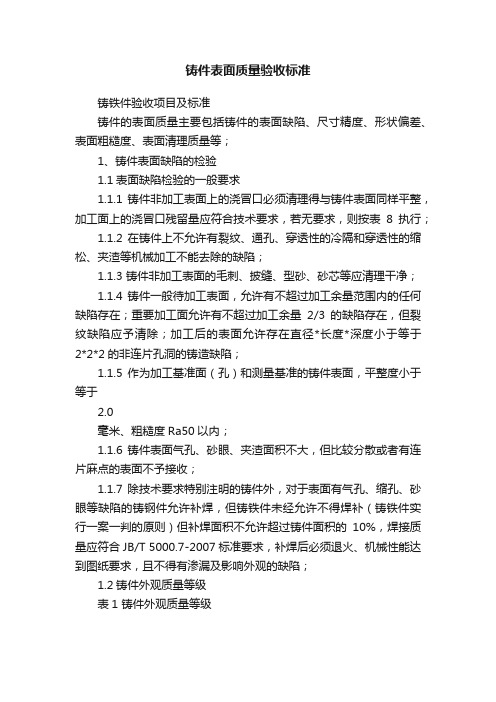
铸件表面质量验收标准铸铁件验收项目及标准铸件的表面质量主要包括铸件的表面缺陷、尺寸精度、形状偏差、表面粗糙度、表面清理质量等;1、铸件表面缺陷的检验1.1表面缺陷检验的一般要求1.1.1 铸件非加工表面上的浇冒口必须清理得与铸件表面同样平整,加工面上的浇冒口残留量应符合技术要求,若无要求,则按表8执行;1.1.2 在铸件上不允许有裂纹、通孔、穿透性的冷隔和穿透性的缩松、夹渣等机械加工不能去除的缺陷;1.1.3 铸件非加工表面的毛刺、披缝、型砂、砂芯等应清理干净;1.1.4 铸件一般待加工表面,允许有不超过加工余量范围内的任何缺陷存在;重要加工面允许有不超过加工余量2/3的缺陷存在,但裂纹缺陷应予清除;加工后的表面允许存在直径*长度*深度小于等于2*2*2的非连片孔洞的铸造缺陷;1.1.5 作为加工基准面(孔)和测量基准的铸件表面,平整度小于等于2.0毫米、粗糙度Ra50以内;1.1.6 铸件表面气孔、砂眼、夹渣面积不大,但比较分散或者有连片麻点的表面不予接收;1.1.7 除技术要求特别注明的铸件外,对于表面有气孔、缩孔、砂眼等缺陷的铸钢件允许补焊,但铸铁件未经允许不得焊补(铸铁件实行一案一判的原则)但补焊面积不允许超过铸件面积的10%,焊接质量应符合JB/T 5000.7-2007标准要求,补焊后必须退火、机械性能达到图纸要求,且不得有渗漏及影响外观的缺陷;1.2铸件外观质量等级表1 铸件外观质量等级2、铸件尺寸的检验2.1铸件毛坯尺寸公差铸件尺寸公差应按毛坯图或技术条件规定的尺寸公差等级执行,当技术文件未规定尺寸公差时,则应以GB6414-1999为依据,并按照表2选定公差值(粗线框内为推荐使用公差等级);(单位:mm)表2铸件尺寸公差2.2铸件分型面处最大错型值应不得超过表2所示公差值,当需进一步限制错型量时,应从表3中选取;表3 错型值(GB6414-1999)2.3铸件加工余量应符合表4的规定,有特殊要求的表面应在技术要求中单独标注加工余量;表4 加工余量(单位:mm)3、表面粗糙度检测表面粗糙度总体检测原则依据图纸要求,当图纸无要求是执行国标GB/T15056-1994;3.1一般情况下,表面粗糙度要求Ra50,铸件难以清理的部位,局部允许Ra100,待加工表面允许降低1级;3.2.使用面积法作为验收依据面积法常用的比较样块评定铸件表面粗糙度;方法如下:3.2.1 铸造表面粗糙度比较样块应符合GB6060.1-1997标准;3.2.2 按照国标BWZ001-88评定铸件表面粗糙度的等级;3.2.3 铸件的浇道、冒口、修补的残余表面及铸造表面缺陷(如粘砂、结疤等)不列为被检表面;3.2.4 以铸造表面粗糙度比较样块为对照标准,对被检铸件的铸造表面用视觉或触觉的方法进行对比;3.2.5 用样块对比时,应选用适于铸造合金材料和工艺方法的样块进行对比;3.2.6 被检的铸造表面必须清理干净,样块表面和被检表面均不得有锈蚀处;3.2.7 用样块对比时,砂型铸造表面被检点数应符合表7的规定;特种铸造表面被检点数应按表8的规定加倍;被检点应平均分布,每点的被检面积不得小于与之对比面的面积;表7 被检铸造表面最低检测数3.2.8 当被检铸造表面的粗糙度介于比较样块两级参数值之间者,所确定的被检铸造表面的粗糙度等级为粗的一级;3.2.9 对被检铸造表面,以其80%的表面所达到的最粗表面粗糙度等级,为该铸造表面粗糙度等级;3.3铸件表面清理检测3.3.1 铸件几何形状必须完整,非加工面上的清理损伤不应大于该处的尺寸偏差,加工面上的损伤不应大于该处加工余量的1/2;3.3.2允许铸件表面有少量的局部低凹或打磨痕迹,在直径不大于8mm,并能保证铸件规定的最小的壁厚;3.3.3为去除铸造缺陷而打磨后的铸件表面粗糙度应与一般铸件表面粗糙度基本一致;3.3.4除特殊情况外,铸件表面允许残留的浇冒口、毛刺,多肉残余量应按表8的要求进行;表8 浇冒口、毛刺、多肉等允许残留量值3.3.5铸件表面须经过防锈处理,保证在铸件进入面加工时不得有任何的锈蚀;3.3.6铸件表面如有油漆要求的,必须按有关涂装规定执行;4、铸件重量检测对于没有特殊要求的铸件,重量偏差可以不作为验收依据;如果技术条件有要求,供需双方协商后,铸件的重量偏差也应作为验收依据,一般应符合表6的规定;表6 铸件重量偏差。
高锰钢国标
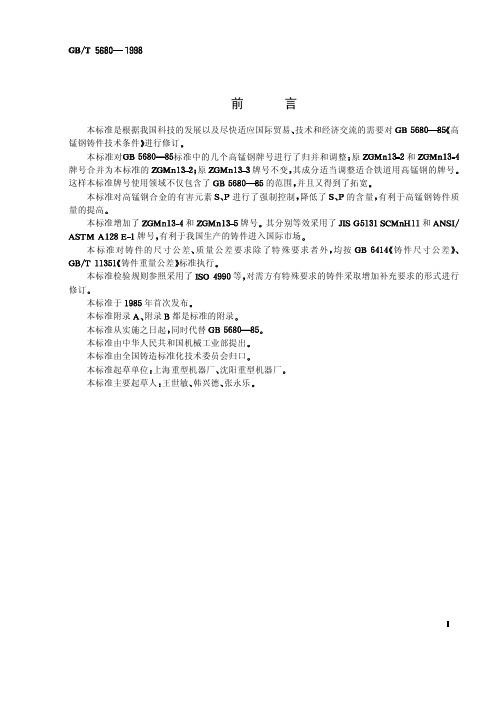
块 表面有裂痕 仍保持在一块上 同样视为合格 当规定进行弯曲试验时 每一炉钢应进行一次这样
试验
弯曲试样 块 应以和它们所代表的铸件同样的方式进行水韧处理 并需考虑到金属断面的差
异 除需方另有规定外 试样 块 的热处理方式一般由制造厂自行选定 可单独热处理 也可与其代表的
铸件一起热处理
如果试样 块 因缺陷而试验不合格 视试验无效 并对同炉的另一块试样 块 进行试验 如果某
收级别
非金属夹杂物按
中规定评级 不大于 和 级应为合格
金相检验用试样可在力学性能用试块中制取 金相试样的制取应距铸造表面不少于
试验
方法按
规定进行
力学性能检验
力学性能和检验规则 力学性能试验 每一批量取一个水韧处理后的试样 试验结果应符合表
中规定性能数值不能满足需方要求 在订货时可经双方协商另定验收数值 表
未溶碳化物级别不大于 级为合格
析出碳化物级别不大于 级为合格
过热碳化物级别不大于 级为合格
试样上碳化物超过
和
规定时 可在铸件上取样复查 或在重新水韧
处理的试块上取样复查 其复试结果若过热碳化物超过规定者应判废 未溶和析出碳化物超过规定者允
许按 处理
如需方认为
和
的规定不能满足其要求 可在订货时经双方协商另定验
前
言
本标准是根据我国科技的发展以及尽快适应国际贸易 技术和经济交流的需要对
高
锰钢铸件技术条件 进行修订
本标准对
标准中的几个高锰钢牌号进行了归并和调整 原
和
牌号合并为本标准的
原
牌号不变 其分适当调整适合铁道用高锰钢的牌号
这样本标准牌号使用领域不仅包含了
的范围 并且又得到了拓宽
高锰钢铸件技术条件

高锰钢铸件技术条件
高锰钢铸件是一种常用于制造高强度、高韧性、高耐磨性的零部件的材料。
为了保证高锰钢铸件的质量和性能,需要遵循一些技术条件。
1. 原材料选用:高锰钢铸件的原材料应选用高品质的高锰钢材料,且必须符合国家标准或行业标准。
2. 熔炼工艺:高锰钢铸件的熔炼应采用电弧炉或感应炉进行,必须严格控制熔炼温度和保持时间,以确保熔体的均匀性和稳定性。
3. 浇注工艺:高锰钢铸件的浇注应采用真空浇铸或低压浇铸技术,以避免氧化和杂质的混入,保证铸件表面的光洁度和内部的致密性。
4. 热处理工艺:高锰钢铸件的热处理应根据不同的材料和工艺要求,采用正火、淬火、回火等多种方式进行,以保证铸件的硬度、韧性、强度等性能指标符合要求。
5. 检测和质量控制:高锰钢铸件应进行严格的检测和质量控制,包括外观检验、尺寸测量、化学成分分析、金相检查、硬度测量、非破坏性检测等多项指标,以确保铸件的质量和性能。
综上所述,高锰钢铸件的制造需要遵循一系列技术条件,包括原材料选用、熔炼工艺、浇注工艺、热处理工艺、检测和质量控制等方面,以保证铸件的质量和性能符合要求。
- 1 -。
- 1、下载文档前请自行甄别文档内容的完整性,平台不提供额外的编辑、内容补充、找答案等附加服务。
- 2、"仅部分预览"的文档,不可在线预览部分如存在完整性等问题,可反馈申请退款(可完整预览的文档不适用该条件!)。
- 3、如文档侵犯您的权益,请联系客服反馈,我们会尽快为您处理(人工客服工作时间:9:00-18:30)。
MY高锰钢铸件验收标准1.成分:该系列产品包含了2种成分,各元素的含量范围如下:Grade C Si P S Mn Cr SANS 4007:2008 Type 6 1.00-1.35 1.00 max0.05 max0.04max 16.0-19. 1.5-2.5For consistent quality purposes, CAB Incorporated recommends that P to be 0.05 max, S to be 0.04 max, Al to be 0.03-0.06, for all grades. This will help reduce foundry scrap and improveproduct usable life.2.铸件内部质量: 请提供铸造工艺图, 并提高你们的模具结果. 铸造工艺图中需提供浇注系统和浇注温度,熔炉温度等信息.3.标识:铸字包括产品名称,材料种类、供应商代码、炉号。
各项之间用空格分开。
采用凹面突字,突字不能高出铸件表面。
字体大小为:字高〉25mm,字宽〉16mm。
铸字位置,图纸上已经分别注明。
铸字需清晰可见,干净整洁。
关于产品名称:分别是MP1000BL和MP1000 Mantle, 图纸上有.关于材料种类:用A-6代替TYPE6 。
供应商代码:MY炉号: 按照工厂内部的炉号规定. 炉号需要和成分, 热处理, 性能, 尺寸对应。
4.加工尺寸公差图纸上有,未注公差按照CT11级。
5.模具完成后,需要在模具上用油漆笔在三个方向上注明以下字符。
“PROPERTY OF CAB INC, OAKWOOD GA, USA”6.热处理:产品需要在1000度以上进行水韧处理。
产品之间的间隙至少在25MM以上。
热处理完成后,需提交以下报告:(1)热处理炉温曲线,需要反映出保温时间,温度等信息。
(2)淬火后的水温和铸件温度(3)装炉信息:每炉装的产品名称,数量和炉号。
(4) 所有记录需要有操作人员的签字和日期。
7.微观组织:一个75X75X125 mm的试块将和铸件一同浇注,做附铸试块. 一同热处理,进行微观组织检测。
在试块的中心取样。
避开缩的区域.基体组织为100%的奥氏体, 只允许在晶界上分别不连续的,孤立的碳化物,奥氏体晶粒的大小按照ASTM E112标准的1级~3级之间,碳化物的标准按照国标GB/T 13925执行,其中:1)for undissolved carbides, Grades W1 to W3 or better are acceptable未溶解碳化物W1~W3级合格2)for precipitated carbides, Grades X1 to X3 or better are acceptable沉淀碳化物X1~X3级合格3)for overheated carbides, Grades G1 to G2 or better are acceptable过热碳化物G1~G2 合格。
每个产品出一个金相样的报告。
8. 表面缺陷按照标准MSS SP-55执行,允许的缺陷等级见下表。
Classification MSS SP-55 Acceptance Level SCRATA Comparator Equivalent Type I: Hot Tears and Cracks None Acceptable None Acceptable Type II: Shrinkage Level “B” or better Use MSS SP-55 Type III: Sand Inclusions Level “B” or better Comparator B2 or better Type IV: Gas Porosity Level “B” or better Comparator C2 or better Type V: Veining Level “B” or better Use MSS SP-55Type VI: Rat Tails Level “B” or better Use MSS SP-55Type VII: Wrinkles, Laps, ColdShutsLevel “B” or better Comparator D2 or betterType VIII: Cutting Marks Level “B” or better Comparator G2 or better Comparator H4 or betterType IX: Sand Scabs Level “B” or better Comparator E1 or better Type X: Chaplets Level “B” or better Comparator F2 or better Type XI: Weld Repairs Level “B” or better Comparator J3 or better Type XII: Surface Roughness Level “B” or better Comparator A3 or better 9.焊补:仅允许修饰性的焊补。
工作面不允许焊补。
具体按照附件的焊接规程。
10. 出货提交报告报告需要在出货前以邮件的形式提交,包括:A 每炉的成分报告B 产品的全尺寸报告C 每炉的金相报告。
附照片及倍数。
D 热处理炉温记录,装炉记录,扫描发给我们。
11 包装:托盘包装. 包装带扎紧。
加工面和毛坯面都喷下面色卡RAL5023防锈漆.4.6 Weld4.6.1No weld repair is permitted to solely improve the casting visual appearance. Reasonablegrinding is preferred to remove surface or subsurface defects when castings do not meet Section 4.5.3. Castings with cracks or hot tears that cannot be removed by grinding are to4.6.2For castings with defects larger than 4 square inches (25 square centimeters) or, deeper than 1 inch (25.4 mm) or a 20% of through section thickness at the defect region a request for weld repair is to be submitted to CAB Incorporated for review and approve. The request is to clearly state the defect size and position with pictures and how the factory is to perform and inspect the weld repair. A unique casting identification (ID) number is to be included in the request.Once approved by CAB Incorporated, the factory is to follow guidelines in Section 4.6.3 and the factory proposed welding procedure to repair the defect.Re-heat treatment maybe required after welding, per section 4.3, and if so, castings can only be re-heat treated once.The unique casting ID is to be either stamped or tagged properly to the repaired casting.The factory is expected to conduct manufacturing process change to improve thecasting quality if the defect is repetitive and consistent with the current process.4.6.3 The following guidelines are to be followed to perform any weld repair for casting defectsexcept for those stated in Section 4.6.1:1)it shall be done using a filler metal with similar chemical composition as in Section2.3.1. The electrode size is to be as small as practical.2)the defect must be fully removed by minimum grinding or arc air to ensure the properweld penetration to the side walls. The casting shall be rejected if a cavity shrinkage orcore shift is discovered during the excavation. Spotting weld over the top of defects isnot acceptable.3)the base metal temperature is to be controlled to lower than 450F (232C) throughoutwelding. Peen welds immediately after each pass. Alternate weld repair among severalcastings are recommended to keep the casting temperature as low as possible4)At CAB Incorporated’s discretion, an X-ray inspection to the weld repair area mightbe required to verify that no significant cracks are present due to the weld repair.。