包埋铸造技术
固定义齿包埋铸造技术操作流程
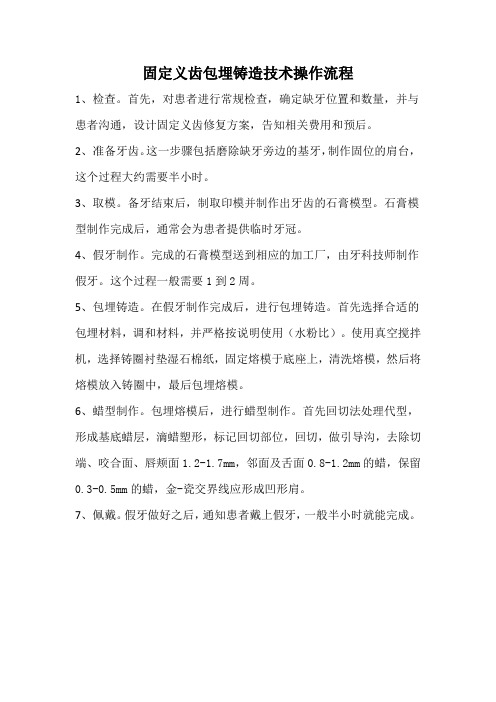
固定义齿包埋铸造技术操作流程
1、检查。
首先,对患者进行常规检查,确定缺牙位置和数量,并与患者沟通,设计固定义齿修复方案,告知相关费用和预后。
2、准备牙齿。
这一步骤包括磨除缺牙旁边的基牙,制作固位的肩台,这个过程大约需要半小时。
3、取模。
备牙结束后,制取印模并制作出牙齿的石膏模型。
石膏模型制作完成后,通常会为患者提供临时牙冠。
4、假牙制作。
完成的石膏模型送到相应的加工厂,由牙科技师制作假牙。
这个过程一般需要1到2周。
5、包埋铸造。
在假牙制作完成后,进行包埋铸造。
首先选择合适的包埋材料,调和材料,并严格按说明使用(水粉比)。
使用真空搅拌机,选择铸圈衬垫湿石棉纸,固定熔模于底座上,清洗熔模,然后将熔模放入铸圈中,最后包埋熔模。
6、蜡型制作。
包埋熔模后,进行蜡型制作。
首先回切法处理代型,形成基底蜡层,滴蜡塑形,标记回切部位,回切,做引导沟,去除切端、咬合面、唇颊面1.2-1.7mm,邻面及舌面0.8-1.2mm的蜡,保留0.3-0.5mm的蜡,金-瓷交界线应形成凹形肩。
7、佩戴。
假牙做好之后,通知患者戴上假牙,一般半小时就能完成。
固定义齿包埋铸造技术操作流程

固定义齿包埋铸造技术操作流程The investment casting process, also known as lost-wax casting, is a widely used technique for producing complex and intricate metal parts. This process involves creating a wax pattern, encasing it in a ceramic shell, and then melting the wax out to create a cavity that can be filled with molten metal. One specific variation of investment casting is the shell mold casting technique, which utilizes a pre-coated sand shell to create the mold. In this article, we will explore the step-by-step process of shell mold casting in detail.The first step in the shell mold casting process is to create a pattern. This pattern is typically made of wax and is an exact replica of the desired metal part. Skilled craftsmen use various tools and techniques to shape the wax pattern to the desired specifications. This step requires precision and attention to detail to ensure that the final product meets the required dimensions and specifications.Once the wax pattern is ready, it is then attached to a wax sprue, which is a wax rod that acts as a channel for the molten metal to flow into the mold. The sprue is carefully positioned to allow for proper filling and solidification of the metal. Additional wax components, such as gates and vents, may also be added to facilitate the flow of metal and the escape of gases during the casting process.After the wax pattern and sprue assembly is complete,it is time to create the ceramic shell mold. The wax pattern is dipped into a ceramic slurry, which coats the pattern with a thin layer of ceramic material. This process is repeated multiple times, allowing each layer to dry before the next one is applied. The repeated dipping and drying process helps to build up a strong and durable shell around the wax pattern.Once the ceramic shell has been built up to the desired thickness, it is then placed in a drying oven. The oven gradually heats up, causing the wax inside the shell to melt and drain out through the sprue and vents. This stepis crucial, as it eliminates the wax pattern and creates a hollow cavity in the shape of the desired part.After the wax has been completely melted out, the ceramic shell is fired in a high-temperature furnace. This firing process helps to strengthen the shell and remove any remaining traces of wax. The shell is then cooled and ready for the final step in the casting process.The final step in shell mold casting is the pouring of the molten metal into the ceramic shell. The shell is preheated to a specific temperature to prevent thermal shock and ensure proper metal flow. The molten metal is poured into the sprue, and gravity pulls it down into the mold cavity. Once the metal has solidified, the shell is broken away, revealing the cast metal part.In conclusion, the shell mold casting process is a complex and intricate technique used to produce high-quality metal parts. It involves creating a wax pattern, building a ceramic shell around it, melting out the wax, and pouring molten metal into the resulting cavity. Thisprocess requires skilled craftsmanship, precision, and attention to detail to achieve the desired results. Shell mold casting offers several advantages, including the ability to produce intricate and complex parts, excellent surface finish, and dimensional accuracy.。
金属全冠包埋铸造操作流程

谢谢
浇铸
铸造的时机 铜基合金:熔化时先为分散块状,逐渐熔成
球状,表面有膜呈不太光亮的橘红色时即可 铸造。 金合金:熔化时分散的合金块向坩埚底聚集 ,随着温度上升,合金熔成球面,呈淡黄色 ,光亮如镜,此时为铸造时机。 高熔合金:铸造时机为当合金熔化呈球面状 ,其表面的氧化膜即将破开时。
浇铸
浇铸
高频离心铸造机步骤: 1. 检查各部件是否完好,根据铸圈调换合适
的“ V” 形铸造托架。 2. 启动电源,预热 5 - 10 分钟。 3. 将经过焙烧的铸圈放在托架上,浇注口与
坩埚托架口一致。 4. 坩埚置于托架上,放入按
钮,观察合金合金熔化过程。
浇铸
6. 到达铸造时机,进行离心铸造, 5 - 10S 。
7. 待离心机停止转动,打开盖子,取出铸圈 并轻放于冷却台上。
8. 将工作线圈调整到冷风口处冷却。 9. 清洁坩埚。
若有多个铸圈,可连续铸造,重复 上述步骤。
浇铸
真空压力铸造机 首先对铸型的
容器抽真空,然后在第 二阶段利用压缩空气把 液态合金压入铸模腔中 。
浇铸
Tri-Caster 铸造机 使 用火焰熔化合金。通过 一个透明管接于真空泵 ,一个红管接于压缩空 气源。优点:熔化的金 属正好等于充满铸腔和 铸道所需金属。
合金放入坩埚内, 火焰加热,开始熔 化时加入保护粉, 10S 后浇铸。
浇铸
浇铸
把机器上的一个杠杆 向下压,底座上的一 个阀会打开,真空泵 把空气抽出。同时, 0.3 - 0.4 巴的初始压 力把液态金属压入铸 道和铸腔中,压力不 断升高,直到 1.5 巴 。
焙烧
浇铸
(三)铸造的方法 1. 离心铸造法(纵型、横型离心铸造
铸造包埋材料的主要成分

铸造包埋材料的主要成分
铸造包埋材料的主要成分是粘土、沙子、砂以及其它粉末物质。
粘土是一种碱性的非金属矿物,具有较强的吸水能力,可增加铸造包埋材料的弹性和耐久性,并且可以帮助减少铸件表面的缺陷。
沙子是一种硬度较大的矿物,具有较高的热传导率,可以加快铸件消除热应力和收缩的过程。
砂是由自然界中的石英、长石、铁矿物等构成,具有较好的密度和较强的耐磨性,可以有效地避免铸件表面的裂纹。
此外,还可以添加一些其它粉末物质,如碳酸钙、碳酸镁、铝粉以及多种粘结剂,可以改善材料的流动性和耐久性。
包埋与铸造技术

包埋与铸造技术嘿,朋友!今天咱们来聊聊包埋与铸造技术。
这俩词儿听起来是不是有点专业,有点神秘?别担心,听我慢慢给您说道说道。
先来说说包埋。
您知道吗,有一次我去一个小工厂参观,就亲眼目睹了一次包埋的过程。
那是一家做金属饰品的小厂,工人们正在制作一批精美的项链坠子。
他们把一个个小小的金属部件放进一种特殊的粉末里,然后用工具轻轻地压实。
那个粉末就像是给金属部件穿上了一层厚厚的“棉衣”。
当时我就好奇地问工人师傅,这是在干啥呀?师傅笑着跟我说:“这就是包埋呀!这层粉末能在后续的加工中起到保护和支撑的作用。
”我凑过去仔细看,发现那粉末颗粒还挺细腻的,就像冬天的雪花一样。
再讲讲铸造。
我想起之前在一个车间里看到的铸造场景,那场面真是壮观!巨大的熔炉里,金属液红彤彤的,像流动的火焰。
工人们穿着厚厚的防护服,小心翼翼地操作着设备,将那炽热的金属液倒进事先准备好的模具里。
随着“滋滋”的声响和一阵热气升腾,金属液慢慢填满了模具的每一个角落。
等到冷却之后,打开模具,一个成型的铸件就出现在眼前啦。
包埋和铸造技术在很多领域都有着广泛的应用。
比如说在珠宝制造中,通过包埋和铸造,可以制作出各种精美的首饰;在机械制造里,能生产出复杂的零部件;在牙科领域,还能为患者打造出合适的牙冠和假牙呢。
您想想,要是没有包埋与铸造技术,咱们生活中的很多东西可能就不会像现在这么精致和好用啦。
就拿咱们每天用的锅碗瓢盆来说,如果没有先进的铸造技术,可能就没有那么光滑的表面,用起来也不会那么顺手。
包埋和铸造技术可不是随随便便就能做好的,这需要非常精细的操作和严格的工艺控制。
从材料的选择,到温度的掌握,再到模具的设计,每一个环节都不能出错。
哪怕是一点点的偏差,都可能导致最终的产品出现瑕疵或者不合格。
比如说,在包埋的时候,如果粉末的比例不对,或者压实的程度不够,在后续的加工过程中,就可能出现变形或者破裂的情况。
而在铸造的时候,如果金属液的温度过高或者过低,倒进模具的速度太快或者太慢,都会影响铸件的质量和性能。
高熔合金铸造包埋材料

包埋材料膨胀特性的ADA标准
种类 压缩强度 固化膨胀系数(%) 热胀系数 综合热胀系数 Mpa
Ⅰ型(嵌体 >2.46 用热膨胀型)
Ⅱ型(嵌体用 >2.46 吸水膨胀型) Ⅲ型(局部 义齿用热膨 胀型)
空气中
0.0-0.5 — 0.0-0.4
水中 (×10-6· K-1) (×10-6· K-1)
— 1.2-2.2 — 1.0-2.0(700℃) 0.0-0.6(500℃) 1.0-1.5(700℃) 1.3-2.0 1.3-2.7 1.2-2.9
3. 应用:一般用作内层包埋材料,用氨气处 理后,可加速固化。外层包埋用少量硬质
石膏(10%)与粗石英粉配制的石膏包埋
材料与水调和,可以缩短包埋时间、节约
材料。
四、铸钛包埋材料
纯钛: 生物相容性好 耐腐蚀 重量轻 弹性模量低 熔点高 化学活性大 铸造收缩1.8%~2.0%
性能要求
① 原料对钛成惰性,属于高熔点物质
在750℃时,可出现显著的收缩倾向
所以石膏类包埋材料的加热温度必须在700℃以下。
蜡型被熔除后,有些碳元素残留在铸型
中,可有与石膏发生以下反应:
CaSO4+4C→CaS+4CO
3CaSO4+CaS→4CaO+4SO2 4CaSO4+CaS→4CaO+4CO↑+4SO2↑
(三)用法 可用于中熔和低熔合金的包埋 使用时,按一定比例与水调和,将蜡型包 埋,避免产生气泡 用粗石英砂(40目)与石膏按3:1的比例 配制的石膏包埋材料,可以用于高温包埋 材料的外层包埋,减低成本,方便开圈
2. 性能
⑴ 固化反应和固化时间 正硅酸乙脂包埋材料
铸造包埋材料castinginvestmentmaterials

机械强度:石膏越多强度越大
透气性:粉末粒度越大,越均匀,水粉比 越大,透气性越高 耐热性:二氧化硅熔点1713℃,石膏分解 温度1000℃,大于700℃时,铸型中的残留 碳(蜡)会将石膏还原生成二氧化硫,污染 金属。 表面光洁度:粉末粒度小( > 200目)
(三)用法
适用合金:金合金(1000-850 ℃ )、银合金
(1100-875 ℃ )、铜合金(700-950 ℃ ) 、锡锑合金(1100-875 ℃ )
使用:
1)包埋料与水按比例调和(30-40% ),再包埋 蜡型。 2)铸造温度必须在700℃以下(方石英和石英的热 膨胀在600-700℃ 最大;石膏的分解)。
5.1 铸圈和衬纸
Casting ring and ring liner
5.2 蜡型的位置
the location of wax pattern
5-6mm
3-5mm
3-5mm
5.3 润 湿 wet
5.4 调拌和包埋 mixing and investing
操作性:硅溶胶浓度越高调拌越困难,操作 多采用真空搅拌机。
结固时间:初凝时间(同石膏) 7-10min, 终凝时间40-120min。
综合膨胀率1.3-2.0%
2.3 机械强度
抗压强度高,随温度增加而增加 调和后24h,压缩强度为9-30MPa,加
热冷却后为2-14MPa。
强度与结合剂含量、粉液比成正比。
2.4 透气性
透气性与粒度、粒度分布、粉液比有关。 粉末粒度200-350目,透气性及表面光洁 度稍差于石膏包埋材料。
包埋与铸造技术课件

(1)衬垫要求
在铸圈的上下端形成3~5mm空白区 采取在一端(上端或下端)形成一3~5mm空白区 无圈铸型技术,用普通铸圈替代时,则不需形成空白区
(2)衬垫方法
(1)湿衬法 (2)干衬法
3. 清洗熔模
在熔模制作完成后,需要将插有铸道针的熔模固定在成形座上进行清洗
(1)清洗熔模的目的
二、包埋前的准备
1. 包埋材料的选择
不同的铸造合金有不同的铸造收缩率,所以必须选用与之相适应的包埋材。 中熔合金多采用石膏系包埋料 高熔合金采用磷酸盐系或硅酸盐系包埋料 钛合金采用二氧化锆耐高温包埋料
2. 选择铸圈
铸圈是包在铸型外围,使包埋料成型的工具。
衬里铸圈
在铸圈的内壁四周,衬垫厚度均匀一致的石棉纸或代用品,以缓冲铸圈对包埋材料加热膨胀的限制
八、缩陷
定义 防止措施 延长加压时间,使铸造压力持续时间长于合金凝固时间 改善包埋料的透气性,在熔摸的边缘安放排气孔。
九、砂眼
定义 防治措施 制作熔模时,特别在安插铸道时,避免铸型腔内产生内尖角。 掌握好包埋料的使用方法和配方,提高铸型的强度和韧性。 使用规范的铸圈底座,保证铸道口的质量。 在烘烤和焙烧过程中防止外界砂粒落入铸型腔内。
第五节 钛铸造技术
一、钛及钛合金铸造的条件
(一)抽真空 1、高真空排除空气 2、”转换“排气 (二)惰性气体保护 1、氩气 2、氦气
二、溶解方法
(一)高频感应溶解 (二)弧溶解
三、铸造法
(一)差压式铸造法 (二)加压铸造法 (三)离心铸造法
(三)烘烤焙烧中的问题
1、过早烘烤或升温过快 2、温度低或时间短
(四)熔铸过程中的问题
1、合金投放量不足 2、合金熔化不全 3、铸造压力不足 4、非贵金属高熔合金熔化时粘性大, 流动性差
- 1、下载文档前请自行甄别文档内容的完整性,平台不提供额外的编辑、内容补充、找答案等附加服务。
- 2、"仅部分预览"的文档,不可在线预览部分如存在完整性等问题,可反馈申请退款(可完整预览的文档不适用该条件!)。
- 3、如文档侵犯您的权益,请联系客服反馈,我们会尽快为您处理(人工客服工作时间:9:00-18:30)。
6.瓷粉熔点必须低于合金熔点170℃~270℃。 7.合金与瓷粉相匹配。瓷的热膨胀系数应略小于烤瓷合金。两者
之间的匹配是烤瓷熔附金属修复体成功的关键因素之一(图84)。 8.金属基底要求有一定的厚度0.3~0.5mm。 9.烤瓷粉的颜色应具有可匹配性,色泽稳定。 10.烤瓷粉应能经受反复烘烤而不发生过大的物理性质变化,能保 持其热膨胀系数的相对稳定性,以确保瓷粉具有良好的透明度、 色泽以及光亮度。
烤瓷修复技术
一、熔附原理
1.化学结合 2.机械结合 3.压缩结合 4.范德华力结合
1.化学结合:最主要
金属基底通过表面预氧化形成的氧化物与烤瓷材料中的 氧化物发生化学反应,能产生很强的结合力。
这种结合力在合金与烤瓷材料的结合中起着重要的作用。
2.机械结合
瓷熔融后流入到凹凸不平的金属表面所形成的机械锁结 作用而使瓷与金属保持结合。
一般金属表面用80目左右的氧化铝进行喷砂处理,即可 形成较为合适的金属表面凹凸不平的界面
3.压缩结合
当烤瓷热膨胀率稍小于合金热膨胀率时,瓷 熔附合金表面冷却后,合金与瓷界面所产生 的张应力和压应力基本达到平衡,有促进金瓷结合的作用。
4.范德华力结合
范德华力是指两种物质紧密贴合时分子之间形 成的引力,可使熔融的瓷黏附到金属表面。
方法:压力要轻,顺一个方向,避免打磨的碎屑嵌入划痕,或空隙 内的空气烧结时形成气泡。选用钨钢磨头。
(1)前牙金-瓷衔接线的位置
1)咬合关系正常:可设计全瓷覆盖。 2)咬合紧:覆盖小、覆合深、牙体唇舌径小,舌侧采用金属板,
瓷层只覆盖至舌侧切缘2~3mm。 3)正中颌在切1/3处,将金-瓷衔接布设计在舌1/2处。 4)邻面金-瓷结合设计在邻接点舌侧至少1mm处。
(2)后牙金-瓷衔接线的位置
(三)金属烤瓷用合金与瓷粉的要求
• 1.合金和瓷粉应具有良好的生物相容性。 • 2.合金必须具有较高的强度、硬度及弹性模量。 • 4.合金铸造性能好,收缩变形小,并具有良好的
润湿性。 • 5.合金和瓷粉应各含有一种或一种以上相同的元
素,以便在高温熔融时发生化学反应,使两种材料 紧密结合产生化学结合力。
合金表面被融化的瓷润湿得越好,黏结能力就 越强,因此合金表面在涂瓷前清洁处理很重要。
范德华力是瓷-金结合中力量最弱的一种力。
二、金属烤瓷材料
(一)金属烤瓷用合金的种类 (二)金属烤瓷用瓷粉的种类 (三)金属烤瓷用合金与瓷粉的要求
(一)金属烤瓷用合金的种类
1.贵金属合金: 金基合金系列:金-铂-钯,金-银-钯 钯基合金系列:银-钯,高钯合金 2.非贵金属合金:目前应用较多的是镍铬合金 3. 钛基合金:难铸造,需专门设备与瓷粉,崩瓷率高。
三、烤瓷熔附金属修复工艺流程
牙体制备 → 取印模、灌注模型 → 制作可卸式代型 → 涂 布间隙涂料、上颌架 → 金属基底蜡型制作 → 包埋、焙 烧、铸造 → 金属基底处理 → 瓷筑塑、烧结与完成
四、金属基底的制作
(一)金属基底的设计 (二)蜡型制作 (三)包埋、焙烧及铸造 (四)金属基底的处理
唇面的回切
邻面的回切
舌侧的回切
修整金瓷交界
检查咬合情况
安插夹持柄
安插铸道
(四)金属基底上瓷前的处理 ※
(1)金属表面的打磨调整 (2)喷砂 (3)清洁 (4)排气和预氧化 (5)基底冠表面颈缘的处理
金属基底冠烤瓷前处理
(1) 打磨调整
目的:去除包埋材料的细小颗粒、金属小瘤子以及过厚的氧化膜; 调整金属基底的形态、厚度。
图8-23 弯卡尺 (A 尖头金属卡尺 B 钝头蜡用卡尺)
2、PFM基底冠蜡型制作方法:
a) 滴蜡法 b) 回切法 c) 压接法 d) 浸蜡法
3)蜡型制作步骤:
a) 回切法 b) 滴蜡法
PFM基底熔模的制作标志
金瓷交界及舌侧回切标志
切端的回切
(一)金属基底的设计
1.金属基底的设计形式 2.金属基底的基本要求 3.瓷-金的衔接线设计 4.颈缘设计
1.金属基底的设计形式
(1)全瓷覆盖型 (2)部分瓷覆盖型
2.金属基底的基本要求 ※ ※
(1)金属基底表面要形成光滑曲面,不能有锐角、锐边 (图)。
(2)尽可能设计成全瓷覆盖形式(图) (3)保证瓷层厚度均匀一致,瓷层过厚易发生裂纹
1.蜡型制作的要求
(1)蜡型的厚度应均匀一致,防止过薄或过厚。蜡型厚度可用钝头蜡 用卡尺测量(图)。
(2)蜡型表面应光滑圆钝,尖锐的棱角、尖嵴会造成应力集中,导致 瓷层断裂。
(3)在金属与瓷衔接处应有明显的凹形肩台,肩台位置的设计应避开 咬合接触区,以防瓷裂。
(4)如果牙体有较大缺损,应注意在设计与制作蜡型时,恢复缺损部 分的外形,并预留出瓷层1.0~1.5mm的均匀厚度。注意不宜使瓷层局部 过厚,否则会因瓷体中心区排气差而产生气泡。
(图)。 (4)金-瓷交界线应保证金属具有合适的支撑面积,使
金瓷呈对接形式,即可保证强度,防止遮色瓷暴露 (图)。 (5)金-瓷衔接处应避开咬合功能区(图)。 (6)金属基底应保持一定的厚度(图)。
3.瓷-金的衔接线设计
(1)前牙金-瓷衔接线的位置 (2)后牙金-瓷衔接线的位置
(二)金属烤瓷用瓷粉的种类 瓷粉按其作用不同可分为:
不透明瓷(遮色瓷) 颈部瓷、肩台瓷 遮色牙本质瓷 牙本质瓷(体瓷):主体部分 釉质瓷(切端瓷):半透明性,位于切端2/3或颌2/3 透明瓷 修饰瓷、着色剂 光釉 调拌液:基本成分为水和氧化锌,有的还有甘油
金属烤瓷粉及调拌液
1)全瓷覆盖:避免瓷层过厚。 2)部分瓷覆盖:避开咬合接触区。 3)邻接面一般用瓷来恢复:金瓷交界放在邻接区以下1mm。
4.颈缘设计
(1)金属边缘型 (2)金-瓷边缘型 (3)瓷边缘型
图8-20 金属边缘型
图8-21 金-瓷边缘型
图8-22瓷边缘型
(二)蜡型制作
1.蜡型制作的要求 2.蜡型的制作方法 3.蜡型制作的步骤