陶瓷基板制造的技术
陶瓷基板的生产开发与应用方案(二)

陶瓷基板的生产开发与应用方案一、实施背景随着科技的不断发展和高精尖技术的广泛应用,电子行业对高性能、高可靠性和长寿命的电子基板的需求日益增长。
陶瓷基板作为一种具有优异性能的电子基板,在高温、高频率、高可靠性和高密度等方面具有显著优势。
因此,开发陶瓷基板的生产技术并推广其应用具有重要意义。
二、工作原理陶瓷基板是一种采用陶瓷材料制成的电子基板,其工作原理主要基于陶瓷材料的优异性能。
陶瓷材料具有高导热性、高绝缘性、低膨胀系数和优良的机械性能,能够满足各种极端环境下的电子设备需求。
通过将陶瓷材料与金属化层结合,可以制造出具有优良电性能和机械性能的陶瓷基板。
三、实施计划步骤1.研发阶段:进行市场调研,收集客户需求和技术资料,制定研发计划。
2.材料选择与制备:选择合适的陶瓷材料和金属化层材料,制备出合格的陶瓷基板样品。
3.工艺优化:通过不断试验和优化工艺参数,提高陶瓷基板的性能和生产效率。
4.中试生产:在小规模生产线上进行中试生产,验证工艺的可行性和稳定性。
5.批量生产:根据中试结果,调整生产线,进行批量生产。
6.质量检测与控制:对生产的陶瓷基板进行严格的质量检测和控制,确保产品符合要求。
7.应用推广:与相关行业合作,推广陶瓷基板的应用。
四、适用范围陶瓷基板适用于以下领域:1.航空航天:陶瓷基板能够满足航空航天领域的高温、高可靠性和长寿命需求。
2.汽车电子:汽车发动机控制单元、车载雷达等需要高导热性、高耐久性的基板材料。
3.电力电子:陶瓷基板可用于制造高频率、高功率的电力电子设备。
4.通信电子:通信基站、路由器等通信设备需要高性能、高稳定的基板材料。
5.工业控制:工业控制设备需要能够在恶劣环境下稳定工作的基板材料。
6.医疗设备:医疗设备需要具有高生物相容性和高稳定性的基板材料。
7.国防军工:陶瓷基板能够满足国防军工领域的高温、高可靠性和保密性需求。
五、创新要点1.采用新型陶瓷材料和金属化层材料,提高陶瓷基板的性能和稳定性。
陶瓷基板的种类特性和工艺
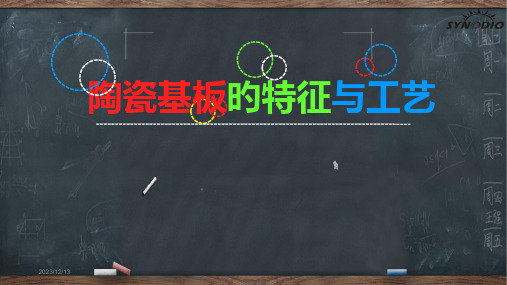
三、陶瓷基板旳特征
陶瓷散热基板特征比较中,主要选用散热基板旳:(1)热传导率、 (2)工艺温度、(3)线路制作措施、(4)线 径宽度,四项特征作进一步旳讨论:
2023/12/13
三、陶瓷基板旳特征——热传导率
热传导率又称为热导率,它代表了基板材料本身直接传导热能旳一种能力,数值愈高代表其散热能力愈 好。LED散热基板最主要旳作用就是在于,怎样有效旳将热能从LED芯片传导到系统散热,以降低 LED 芯片旳温度,增长发光效率与延长LED寿命,所以,散热基板热传导效果旳优劣就成为业界在选用 散热基板时,主要旳评估项目之一。
检视表一,由四种陶瓷散热基板旳比较可明看出,虽然Al2O3材料之热传导率约在20~24之间,LTCC为 降低其烧结温度而添加了30%~50%旳玻璃材料,使其热传导率降至2~3W/mK左右;而HTCC因其普遍 共烧温度略低于纯Al2O3基板之烧结温度,而使其因材料密度较低使得热传导系数低Al2O3基板约在 16~17W/mK之间。一般来说,LTCC与HTCC散热效果并不如DBC与DPC散热基板里想。
2023/12/13
二、陶瓷基板旳种类——DBC
直接敷铜陶瓷基板因为同步具有铜旳优良导电、 导热性能和陶瓷旳机械强度高、低介电损耗旳 优点,所以得到广泛旳应用。在过去旳几十年 里,敷铜基板在功率电子封装方面做出了很大 旳贡献,这主要归因于直接敷铜基板具有如下 性能特点:
热性能好;
电容性能;
直接敷铜陶瓷基板最初旳研究就是为了处理大电 流和散热而开发出来旳,后来又应用到AlN陶瓷旳 金属化。除上述特点外还具有如下特点使其在大 功率器件中得到广泛应用:
4.在工艺温度与裕度旳考量, DPC旳工艺温度仅需 250~350℃左右旳温度即可 完毕散热基板旳制作,完全 防止了高温对于材料所造成 旳破坏或尺寸变异旳现象, 也排除了制造成本费用高旳 问题。
dba陶瓷基板工艺

dba陶瓷基板工艺一、基板制备DBA陶瓷基板是一种以陶瓷为基材,通过微加工技术制造而成的基板。
其制备过程包括以下几个步骤:1.陶瓷基材制备:采用高纯度陶瓷材料,通过球磨、干燥、成型等工艺,制备成所需的陶瓷基材。
2.基材表面处理:对陶瓷基材进行抛光、清洗等处理,以去除表面杂质和缺陷。
3.微加工:采用微加工技术,将陶瓷基材加工成具有所需电路图案的基板。
4.基板清洗:清洗基板表面,去除微加工过程中留下的杂质和污染物。
二、铜箔制备铜箔是DBA陶瓷基板上的主要导电材料,其制备过程包括以下几个步骤:1.铜箔材料选择:选择高导电性能的铜箔材料,如纯铜或铜合金。
2.铜箔剪裁:根据实际需要,将铜箔剪裁成所需的尺寸和形状。
3.铜箔表面处理:对铜箔表面进行抛光、清洗等处理,以去除表面杂质和缺陷。
4.铜箔矫直:通过矫直机对铜箔进行矫直,以保证其在DBA陶瓷基板上的平整度。
三、键合键合是将DBA陶瓷基板与铜箔连接在一起的关键步骤,其主要包括以下几个环节:1.表面处理:对DBA陶瓷基板和铜箔进行表面处理,以增强它们之间的粘附性。
2.焊料选择:选择合适的焊料,如银铜合金、锡铅合金等,用于将DBA陶瓷基板与铜箔连接在一起。
3.键合工艺:采用超声波键合、热压键合等工艺,将DBA陶瓷基板与铜箔紧密连接在一起。
4.键合质量检测:对键合后的DBA陶瓷基板进行质量检测,如X 射线检测、超声波检测等,以确保键合质量和可靠性。
四、电路制作电路制作是DBA陶瓷基板工艺的核心环节之一,其主要包括以下几个步骤:1.光刻制版:采用光刻技术制作DBA陶瓷基板的电路图案模板。
2.电路印刷:使用印刷机将电路图案模板上的电路转移到DBA陶瓷基板上。
3.电路固化:通过加热等手段使电路图案模板上的电路材料固化在DBA陶瓷基板上。
4.电路质量检测:对制作完成的电路进行质量检测,如外观检测、电性能检测等,以确保电路的质量和可靠性。
详解陶瓷基电路板制作的重要工艺(钻孔、蚀刻、覆铜)
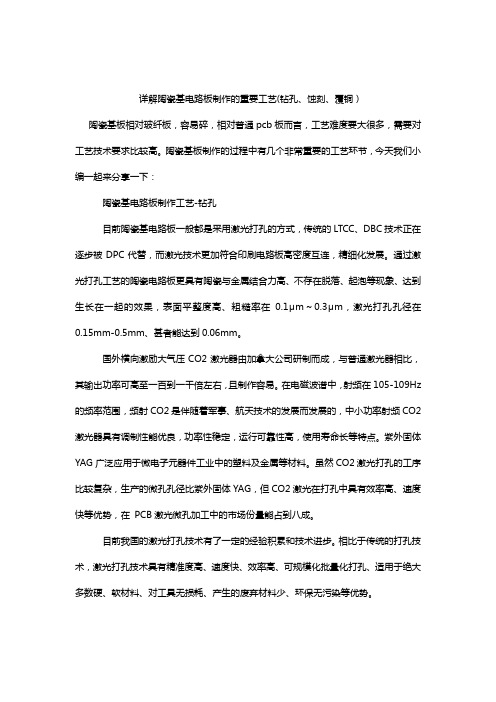
详解陶瓷基电路板制作的重要工艺(钻孔、蚀刻、覆铜)陶瓷基板相对玻纤板,容易碎,相对普通pcb板而言,工艺难度要大很多,需要对工艺技术要求比较高。
陶瓷基板制作的过程中有几个非常重要的工艺环节,今天我们小编一起来分享一下:陶瓷基电路板制作工艺-钻孔目前陶瓷基电路板一般都是采用激光打孔的方式,传统的LTCC、DBC技术正在逐步被DPC代替,而激光技术更加符合印刷电路板高密度互连,精细化发展。
通过激光打孔工艺的陶瓷电路板更具有陶瓷与金属结合力高、不存在脱落、起泡等现象、达到生长在一起的效果,表面平整度高、粗糙率在0.1μm~0.3μm,激光打孔孔径在0.15mm-0.5mm、甚者能达到0.06mm。
国外横向激励大气压CO2激光器由加拿大公司研制而成,与普通激光器相比,其输出功率可高至一百到一千倍左右,且制作容易。
在电磁波谱中,射频在105-109Hz 的频率范围,频射CO2是伴随着军事、航天技术的发展而发展的,中小功率射频CO2激光器具有调制性能优良,功率性稳定,运行可靠性高,使用寿命长等特点。
紫外固体YAG广泛应用于微电子元器件工业中的塑料及金属等材料。
虽然CO2激光打孔的工序比较复杂,生产的微孔孔径比紫外固体YAG,但CO2激光在打孔中具有效率高、速度快等优势,在PCB激光微孔加工中的市场份量能占到八成。
目前我国的激光打孔技术有了一定的经验积累和技术进步。
相比于传统的打孔技术,激光打孔技术具有精准度高、速度快、效率高、可规模化批量化打孔、适用于绝大多数硬、软材料、对工具无损耗、产生的废弃材料少、环保无污染等优势。
陶瓷基电路板制作工艺-覆铜如何给陶瓷基板pcb覆铜?覆铜是指在电路板上没有布线的区域覆上铜箔,与地线相连,以增大地线面积,减小环路面积,降低压降,提高电源效率和抗干扰能力。
覆铜除了能减小地线阻抗,同时具有减小环路截面积,增强信号镜像环路等作用。
因此,覆铜工艺在陶瓷基板PCB工艺中起着非常关键的作用,不完整、截断镜像环路或者位置不正确的铜层经常会导致新的干扰,对电路板的使用产生消极影响。
电子封装用陶瓷基板材料及其制备工艺

泛。
陶瓷基片主要包括氧化铍(BeO)、氧化铝(Al2O3)和氮化铝(AlN)、氮化硅(Si3N4)。
与其他陶瓷材料相比,Si3N4陶瓷基片具有很高的电绝缘性能和化学稳定性,热稳定性好,机械强度大,可用于制造高集成度大规模集成电路板。
几种陶瓷基片材料性能比较从结构与制造工艺而言,陶瓷基板又可分为HTCC、LTCC、TFC、DBC、DPC等。
高温共烧多层陶瓷基板(HTCC)HTCC,又称高温共烧多层陶瓷基板。
制备过程中先将陶瓷粉(Al2O3或AlN)加入有机黏结剂,混合均匀后成为膏状浆料,接着利用刮刀将浆料刮成片状,再通过干燥工艺使片状浆料形成生坯;然后依据各层的设计钻导通孔,采用丝网印刷金属浆料进行布线和填孔,最后将各生坯层叠加,置于高温炉(1600℃)中烧结而成。
此制备过程因为烧结温度较高,导致金属导体材料的选择受限(主要为熔点较高但导电性较差的钨、钼、锰等金属),制作成本高,热导率一般在20~200W/(m·℃)。
低温共烧陶瓷基板(LTCC)LTCC,又称低温共烧陶瓷基板,其制备工艺与HTCC类似,只是在Al2O3粉中混入质量分数30%~50%的低熔点玻璃料,使烧结温度降低至850~900℃,因此可以采用导电率较好的金、银作为电极材料和布线材料。
因为LTCC采用丝网印刷技术制作金属线路,有可能因张网问题造成对位误差;而且多层陶瓷叠压烧结时还存在收缩比例差异问题,影响成品率。
为了提高LTCC导热性能,可在贴片区增加导热孔或导电孔,但成本增加。
厚膜陶瓷基板(TFC)相对于LTCC和HTCC,TFC为一种后烧陶瓷基板。
采用丝网印刷技术将金属浆料涂覆在陶瓷基片表面,经过干燥、高温烧结(700~800℃)后制备。
金属浆料一般由金属粉末、有机树脂和玻璃等组分。
经高温烧结,树脂粘合剂被燃烧掉,剩下的几乎都是纯金属,由于玻璃质粘合作用在陶瓷基板表面。
烧结后的金属层厚度为10~20μm,最小线宽为0.3mm。
氮化铝陶瓷基板生产制作流程和加工制造工艺

氮化铝陶瓷基板生产制作流程和加工制造工艺氮化铝陶瓷基板相对于氧化铝套基板而氧,机械强度和硬度增加,相应的导热率比氧化铝陶瓷基板更高。
氮化铝陶瓷基板生产制作难度增加,加工工艺也有所不同。
今天小编主要是讲述一下氮化铝陶瓷基板生产制作流程和加工制造工艺。
一,氮化铝陶瓷基板生产制作流程1,氮化铝陶瓷基板生产制作过程氮化铝陶瓷基板生产制作流程,大致和陶瓷基板的制作流程接近,需要做烧结工艺,厚膜工艺,薄膜工艺因此具的制作流程和细节有所不同。
氮化铝陶瓷基板制作流程详见文章“关于氧化铝陶瓷基板这个八个方面你知道几个?”2,氮化铝陶瓷基板研磨氮化铝陶瓷电路板的制作流程是非常复杂的,第一步就是氮化铝陶瓷电路板的表面处理,也叫作研磨,其作用是去除其表面的附着物以及平整度的改善。
众所周知,氮化铝陶瓷基板会比氧化铝陶瓷电路板的硬度高很多,遇到比较薄的板厚要求的时候,研磨就是一个非常难得事情了,要保证氮化铝陶瓷电路板不会碎裂,还要达到尺寸精度和表面粗糙度的要求,需要专业的人操作。
不同的研磨方式对氮化铝陶瓷电路板的平整度、生产率、成品率的影响都是很大的,而且后续的工序是没办法提高基材的几何形状的精度。
所以氮化铝陶瓷电路板的制作选用的都是离散磨料双面研磨,对于生产企业来讲整个工序的成本会提升很多,但是为了使客户得到比较完美的氮化铝陶瓷电路板。
另外研磨液是一种溶于水的研磨剂,能够很好的做到去油污,防锈,清洁和增光效果,所以可以让氮化铝陶瓷电路板超过原本的光泽。
然而如今国内市场上的一些氮化铝陶瓷电路板仍旧不够完美,例如产品的流痕问题,是困扰氮化铝陶瓷电路板加工行业的难题。
主要还是没有办法达到比较好的成本控制和生产工艺。
3,氮化铝陶瓷基板切割打孔金瑞欣特种电路采用是激光切割打孔,采用激光切割打孔的优点:●采用皮秒或者飞秒激光器,超短脉冲加工无热传导,适于任意有机&无机材料的高速切割与钻孔,小10μm的崩边和热影响区。
●采用单激光器双光路分光技术,双激光头加工,效率提升一倍。
多层陶瓷基板及其制造方法

多层陶瓷基板及其制造方法多层陶瓷基板是一种用于集成电路及其他电子器件的基板材料。
它由多层陶瓷层和导电金属层交替叠加而成,具有优良的电绝缘性能、高强度和优异的热导率。
本文将介绍多层陶瓷基板的制造方法及其相关技术。
一、多层陶瓷基板的制造方法1. 原料准备:多层陶瓷基板的主要材料是陶瓷粉末和有机粘结剂。
通常使用的陶瓷粉末包括氧化铝、氮化铝和氧化锆等,有机粘结剂主要是聚合物树脂。
这些原料经过混合和筛分后,制成可用于制造基板的坯料。
2. 基板成型:将坯料通过压制、挤出或注射成型工艺,制成带有导电通孔的原始基板。
这些通孔将用于连接多层陶瓷层和导电金属层。
3. 陶瓷层烧结:将多个陶瓷层叠加在一起,并在高温下进行烧结,以实现层间结合。
在烧结过程中,有机粘结剂将分解和燃烧,使陶瓷层之间形成坚固的结合。
烧结后的陶瓷层具有较高的密度和强度。
4. 金属层制备:在陶瓷层之间涂覆金属浆料,并通过烧结的方式使其与陶瓷层牢固结合。
金属浆料通常是由导电金属粉末和有机粘结剂组成。
烧结后的金属层在多层陶瓷基板中起到导电和连接功能。
5. 电连接:通过钻孔和镀铜等工艺在金属层上形成电连接,以实现电子器件的连接和信号传输。
二、多层陶瓷基板的相关技术1. 高可靠性技术:多层陶瓷基板在高温、高湿和恶劣环境下应用广泛,因此需要具备高可靠性。
相关的技术包括优化材料配方、提高烧结质量和优化金属层的制备工艺等。
2. 高频应用技术:多层陶瓷基板在高频电路中具有较好的性能,但需要考虑电磁波的传播特性和导热性能。
相关技术包括优化金属层的导电性能和设计合适的电连接结构。
3. 低温烧结技术:传统的多层陶瓷基板制备过程中需要高温烧结,但这可能导致一些敏感电子器件的失效。
因此,发展低温烧结技术具有重要意义。
目前,人们通过添加适当的添加剂,改变烧结工艺参数等方式,实现多层陶瓷基板的低温烧结。
4. 高密度互连技术:随着电子器件的微小化和集成化,多层陶瓷基板上的导电通孔需要更高的密度和更小的尺寸。
陶瓷基板工艺技术

陶瓷基板工艺技术陶瓷基板工艺技术是一项重要的制造技术,广泛应用于电子、电器、通信等行业。
它是指将陶瓷原料通过加工工艺加工成所需形状和尺寸的基板产品的一系列工艺过程和技术。
首先,陶瓷基板的制备工艺包括原料选择和配比。
陶瓷基板一般由氧化铝和氮化硼等陶瓷粉末经过高温烧结和压制等工艺制成。
在原料选择中,需要选择纯度高、颗粒均匀的原料,以确保基板的物理性能和电化学性能。
其次,陶瓷基板的成型工艺。
常见的成型工艺有压制、注浆和挤出等。
压制工艺是将陶瓷粉末放入模具中,通过压力使其成型。
注浆工艺是将陶瓷粉末与稀释剂混合,通过注射器注入模具中。
挤出工艺是将陶瓷糊料挤出成型,然后经过干燥和烧结等工艺。
再次,陶瓷基板的烧结工艺。
烧结是将成型的陶瓷基板放入炉中进行高温处理,使其颗粒间发生结合,形成致密的基板。
烧结过程中需要控制好温度和时间,以及气氛的控制。
烧结温度过低,基板不能充分结合;烧结温度过高,基板易变形、开裂。
同时,气氛控制也非常重要,不同材料对氧化还原气氛的要求不同。
最后,陶瓷基板的加工工艺。
加工工艺包括切割、打孔、修整等。
切割是将烧结成型后的陶瓷基板切割成所需的尺寸。
打孔是根据设计要求,在基板上钻孔,以便之后的组装和安装。
修整是处理基板表面的不平整、毛刺和划痕,使其达到平整、光滑的要求。
通过以上工艺技术的整合与应用,可以制备出各种形状、尺寸和性能优良的陶瓷基板产品。
陶瓷基板具有优良的绝缘性能、机械强度和耐温性能,广泛应用于电路板、电子器件、高频器件等领域。
随着科技的不断发展,陶瓷基板工艺技术也在不断创新和改进,以满足不同行业对于高性能陶瓷基板的需求。
- 1、下载文档前请自行甄别文档内容的完整性,平台不提供额外的编辑、内容补充、找答案等附加服务。
- 2、"仅部分预览"的文档,不可在线预览部分如存在完整性等问题,可反馈申请退款(可完整预览的文档不适用该条件!)。
- 3、如文档侵犯您的权益,请联系客服反馈,我们会尽快为您处理(人工客服工作时间:9:00-18:30)。
9
粘结剂:
PVB(聚乙烯醇聚丁醛树脂)
分散剂:
DBP(邻苯二甲酸二丁酯)、鱼油、合成油
烧成温度:
1500-1600 º C
气氛:
加湿H2、H2-N2、NH3的分解混合气
10
(b) Al2O3陶瓷金属化
共烧法 厚膜法 薄膜法 难熔金属法
难熔金属法
厚膜法
薄膜法
共烧法
11
(c) Al2O3基板表面金属化 — 难熔金属法
4
a-Al2O3
Al3+与O2-之间为强固的离子键; O2-阴离子近似于密排六方排列; Al3+阳离子占据了2/3的八面体空 隙位置,即每个Al3+位于6个O2-构 成的八面体的中心; a-Al2O3结构的填充极为密实,其 物理性能,化学性能稳定, 具有 密度高、机械强度大等特性。
②热导率/(W/m· K) ③绝缘耐压/(kV/mm)
④r
⑤莫氏硬度 ⑥表观密度/(103kg/m3)
⑦弹性模量/105MPa
⑧比热容/(10-1kcal/kg· º C) Al2O3% ⑨tan/10-4
16
厚膜混合IC用基板 表面粗糙度,价格 、与布线导体结合力; 常用96wt%的Al2O3基板。
薄厚膜混合IC用基板
厚度几百nm以下,薄膜的物理性能、电气性能受表面 粗糙度影响很大; 保证表面平滑,表面被覆玻璃釉(几十微米)。
薄膜混合IC用基板
纯度99%以上,表面粗糙度小
17
(b) LSI用基板
同时烧成技术制作的LSI封装,气密性好、可靠性高;
机械强度高、热导率高,在多端子、细引脚节距、高
38
液相的流动性要好,烧结后期在AlN晶粒生长过程的 驱动下向三角晶界处流动,而不致于在AIN晶粒间形 成热阻层。
进一步的在烧结的过程中能够从三角晶界处流向基板 表面,从而净化AlN的晶界;
助烧剂最好不与AlN发生反应,否则产生晶格缺陷,
难以形成AlN完整晶形。
助烧剂:碱土金属或稀土金属的氧化物、氟化物等, 如Y2O3、CaO、CaF2等。
25
AlN的热导率理论值:320 W/(m· K);实际值:< 200 W/(m· K);
AlN主要靠声子传热,在热传输过程中,晶体中的缺 陷、晶界、气孔、电子以及声子本身都会产生声子散 射,从而影响A1N基板的热导率;
声子散射对热导率K的影响关系式为:
K =1/3cvl
c: 比热容;v = 声子运动速度; l: 声子平均自由程
一;
机械强度、热导率比Al2O3低;
介电常数比Al2O3低,有利提高传输速度;
制造、金属化方法与Al2O3基本相同;
21
日立公司开发莫来石用于多层电路板;
导体层:W,44层
22
3、氮化铝基板
(1) AlN 陶瓷性质
热导率高(> Al2O3)
热膨胀系数与Si匹配 (适用高密度封装、MCM)
第三章 陶瓷基板制造技术
第一节 陶瓷基板概论
1、陶瓷基板具备条件 2、陶瓷基板的制造方法 3、流延成型工艺 4、陶瓷基板的金属化 第二节 各类陶瓷基板
1、氧化铝基板2、莫来石基板
3、氮化铝基板4、碳化硅基板 5、氧化铍基板
1
1、氧化铝基板
(1)Al2O3陶瓷的基本性质
优良的机械强度;
26
为了提高AlN的热导率:
必须对陶瓷的微结构进行控制,排除点阵畸变、位
错、层错、非平衡点缺陷等晶体缺陷,尽量保证晶
体的完整性; 减少气孔、第二相析出。
27
(3) AlN 粉的制备
电子级AlN粉要求纯度高、烧结性活性好; AlN粉中的杂质特别是氧的含量,对陶瓷基板的性能 有显著影响;氧含量提高会严重降低基板的热导率;
34
(4) AlN 基板的制造
AlN自扩散系数小 常压下2440℃升华
常规烧结
35
(a) 使用超细粉制备基板:
纳米尺度的颗粒,在比该材料的熔化温度低的条件下 熔融。颗粒的尺度越小,熔化温度越低。在超细状态 下的AlN粉可以在比它的升华温度低得多的时候完成
烧结。
受粉体的性能影响较大,如果小粒径的AlN粉没有达
此外,在表面电镀Ni、Au、Ag等,改善导体膜的 焊接性能。
12
MnO -Al2O3系相图
13
经Mo-Mn法处理的Al2O3基板焊接截面结构
焊料 Ni电镀层 Mo-Mn 中间层(MnO · Al2O3) Al2O3基板
14
(6)Al2O3 陶瓷基板的应用
(a) 混合集成电路用基板
15
①抗弯强度/10M
散热性等高密度封装中,Al2O3基板作用重大。
18
(c) 多层电路基板
IBM308X, TCM,
基板:90mm × 90mm,
布线:共烧Mo; L:120 m
19
NEC, 100 mm 100mm, PI布线; PI介电常数低,提高信号传输速度。
20
2、莫来石基板
3Al2O3 · 2SiO2, 是Al2O3-SiO2体系最稳定晶相之
30
(b) Al2O3碳热还原法:
Al2O3 + N2 + 3C → 2AlN + 3CO
两步完成:
第一步由C还原生成气相中间产物Al(g)、
Al2O (g);第二步氮化生成AlN;
常加入CaO、CaF2、Y2O3等作为催化剂;有效地降低
活化能,提高反应速率;
加适当过量的碳,既能加快反应速率,提高转换率,
也有助于控制粉末团聚,获得理想的粒径分布;
AlN粉的纯度较高,成型和烧结性能都比较好; 缺点:合成温度高,反应时间长,颗粒度比较大。
31
Al2O3碳热还原机理:
C还原Al2O3 Al2O3(s) + 3C(s) 2Al(g) + 3CO(g) Al2O3(s) + 2C(s) Al2O(g) + 2CO(g) 2Al(g) + N2(g) 2AlN(s) [或 Al2O(g) + N2(g) + C(s) 2AlN(s) + CO(g) ]
通过点阵或晶格振动,即借助晶格波或热波进行 热传递; 载热声子通过结构基元(原子、离子或分子)间进行 相互制约、相互协调的振动来实现热的传递; 如果晶体为具有完全理想结构的非弹性体,则热 可以自由地由晶体的热端不受任何干扰和散射向 冷端传递,热导率可以达到很高的数值; 热导率主要由晶体缺陷和声子自身对声子散射控 制。
23
AlN晶体结构
a = 0.31 nm; c = 0.498 nm;
属六方晶系,是以【AlN4】四方体 为结构单元的纤维矿型; 共价键化合物; AIN晶体呈白色或灰色; 常压下分解温度为2 200~2 450℃; 理论密度为3.26 g/cm3。
24
(2) AlN 的导热机理
良好导热特性,适用于高温环境;
具有耐抗侵蚀和磨耗性;
高电气绝缘特性。
2
良好表面特性,提供优异平面度与平坦度; 抗震效果佳; 低曲翘度; 高温环境下稳定性佳; 可加工成各种复杂形状。
3
(2)Al2O3晶体结构
具有多种同质异晶体; a(三方)、b(六方)、g(四方)、h(ቤተ መጻሕፍቲ ባይዱ轴)、r(晶系 未定)、χ (六方)、κ(六方)、δ(四方)、θ(单斜)Al2O3等10多种变体; 主要有a(三方)、b(六方)、g(四方)相; a-Al2O3为高温稳定相,工业上使用最多。
到一定的含量,是无法在设定的温度下完成烧结;
生产大量的纳米状态的AlN粉会提高生产成本; 需要解决超细粉的团聚问题,(给后续工艺带来一定 的困难,比如流延成型等)。
36
(b) 热压(或热等静压)烧结法:
用于制造高性能的块体AlN陶瓷材料的制备;
工艺条件复杂,不适合进行批量生产;
只能制作简单形状的瓷体,并且共烧基板采用这种工
直接键合铜金属化;
AlN-W共烧金属化。
42
(6) AlN 基板的应用 (a) LSI封装
43
(b) 超高频(VHF)频带功率放大器模块
散热基板结构剖面
(c) 大功率器件、激光二极管基板
44
4、碳化硅(SiC)基板
(1) SiC基板的特性
热扩散系数大(> 铜1.1cm2/s); 热膨胀系数与Si更加接近; 缺点:
Al2O3分解 2Al2O3(s) 4Al(g) + 3O2(g) 2C(s) + O2(g) 2CO(g) 2Al(g) + N2(g) 2AlN(s)
CO还原氧化铝 Al2O3(s) + 2CO(g) Al2O(g) + 2CO(g) Al2O(g) + 2CO(g) + N2(g) 2AlN(s) + CO(g)
艺会受到很大的局限性,无法用于电子封装基板的生 产。
37
(c) 常压烧结法:
助烧剂
选择原则:
在较低的温度与AlN颗粒表层的A12O3发生共溶,形
成液相,这样才能降低烧结温度;
产生的液相对AlN颗粒能够具有良好润湿性,有效起 到烧结作用;